Remember the first time you saw a 3D printer in action? That was mind-blowing, right? Well, wire cutting technology is doing something similar for injection mold manufacturing.
Wire Electrical Discharge Machining revolutionizes injection mold manufacturing by allowing precision crafting of intricate shapes, streamlining processes, and enhancing mold quality and production efficiency.
While the snippet offers a quick peek into Wire EDM‘s potential, there’s so much more to explore. From shaping mold cavities to crafting precise inserts, this technology is reshaping the industry in ways I couldn’t have imagined. Let’s dive deeper into these exciting facets and uncover the full spectrum of Wire EDM‘s capabilities.
Wire EDM enhances precision in mold manufacturing.True
Wire EDM allows for precise cuts, crucial for complex mold shapes.
Wire cutting technology is outdated in mold manufacturing.False
Wire EDM is a modern technology revolutionizing precision and efficiency.
- 1. How Does Wire EDM Revolutionize Mold Cavity and Core Processing?
- 2. How Does Wire Cutting Enhance Mold Insert Manufacturing?
- 3. Why is Wire EDM the Best Choice for Ejector and Cooling Hole Processing?
- 4. How does wire cutting enhance electrode processing?
- 5. How does Wire EDM boost efficiency in mold manufacturing?
- 6. Conclusion
How Does Wire EDM Revolutionize Mold Cavity and Core Processing?
When I first discovered Wire EDM, it felt like unlocking a secret weapon in mold making.
Wire EDM revolutionizes mold processing with unmatched precision, enabling complex designs and operations irrespective of material hardness, ensuring exceptional accuracy, enhanced efficiency, and mold durability.
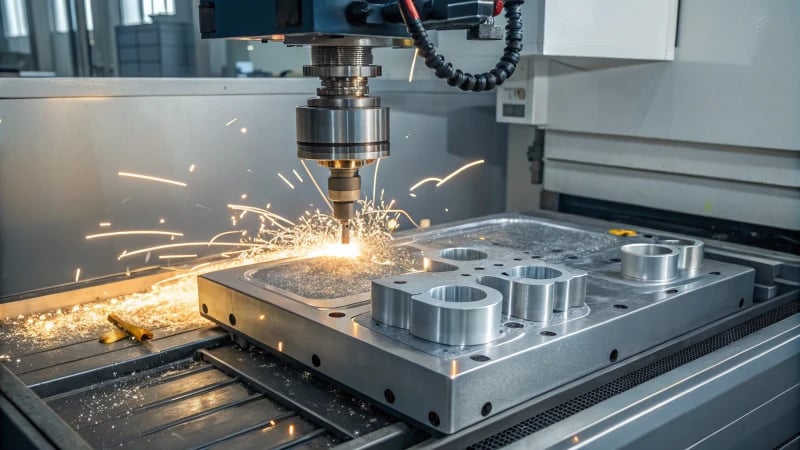
Precision and Complex Shape Processing
I remember tackling a particularly challenging mold design with curves so intricate, it felt like solving a 3D puzzle. That’s when Wire EDM became my go-to solution. This technique allows for precise control of the cutting path, perfect for those complex geometric shapes that once seemed impossible. Whether I’m working on delicate watch parts1 or any other high-precision piece, Wire EDM‘s micron-level accuracy ensures that every detail is spot on.
Feature | Benefit |
---|---|
Precision | Micron-level accuracy |
Complexity | Handles intricate curves and special-shaped holes |
Post-Quenching Operations
One of the most mind-blowing aspects of Wire EDM is its ability to handle post-quenching operations. Traditional methods would buckle under the pressure of hardened materials, but not Wire EDM. I can maintain the dimensional and shape accuracy of molds with hardened cores—an absolute game-changer for creating high-precision plastic molds with complex structures like fine reinforcing ribs.
- Example: In my work, I’ve seen how Wire EDM processes mold cores into intricate internal structures post-quenching, solving issues traditional methods couldn’t handle.
High-Precision Insert Manufacturing
Inserts have always been critical for durability and maintenance in molds. Wire EDM‘s precision—up to ±0.005mm—means I can manufacture inserts that fit perfectly with other mold components. The control over dimensions like outer and inner diameters ensures everything aligns seamlessly.
Inserts2 of various shapes can be crafted to meet specific assembly needs with remarkable accuracy, which has been crucial in my projects.
Insert Type | Shape Options | Precision |
---|---|---|
Square | Various | High |
Round | Various | High |
Ejector and Cooling Hole Processing
Processing ejector holes used to be tedious until I started using Wire EDM. It effortlessly ensures precise location and dimension accuracy, which is vital for smooth operation in molds. Plus, forming varied shapes for cooling holes has never been easier, greatly enhancing temperature control during injection molding.
- Example: For large injection molds, I can batch process dozens of ejector holes simultaneously, maintaining strict diameter accuracy.
Whether it’s spirals or other complex shapes, Wire EDM makes sure molds stay cool and efficient.
Electrode Processing for EDM
In shaping electrodes needed for EDM processes, Wire EDM is indispensable. It crafts electrodes with complex contours precisely, optimizing material use without sacrificing quality.
- Example: When dealing with intricate electrode shapes, Wire EDM guarantees they match design specs exactly, supporting accurate subsequent EDM operations.
Electrode contour processing3 benefits from adjustable wire tension and cutting speeds, producing top-notch surface finishes and dimensional accuracy.
Wire EDM has truly redefined my approach to mold cavity and core processing by merging precision with versatility across various manufacturing phases. It’s fascinating to see how this technology transforms modern machining techniques—offering solutions that were once out of reach.
Wire EDM achieves micron-level accuracy in mold processing.True
Wire EDM offers precise control, achieving micron-level accuracy in molds.
Wire EDM cannot process hardened materials post-quenching.False
Wire EDM excels in processing hardened materials after quenching, maintaining accuracy.
How Does Wire Cutting Enhance Mold Insert Manufacturing?
Ever tried to solve a puzzle with pieces that just won’t fit? That’s what mold making can feel like without the right tools.
Wire cutting, especially Wire EDM, revolutionizes mold insert manufacturing by allowing precise crafting of complex shapes and processing post-quenching, maintaining dimensional accuracy regardless of material hardness.
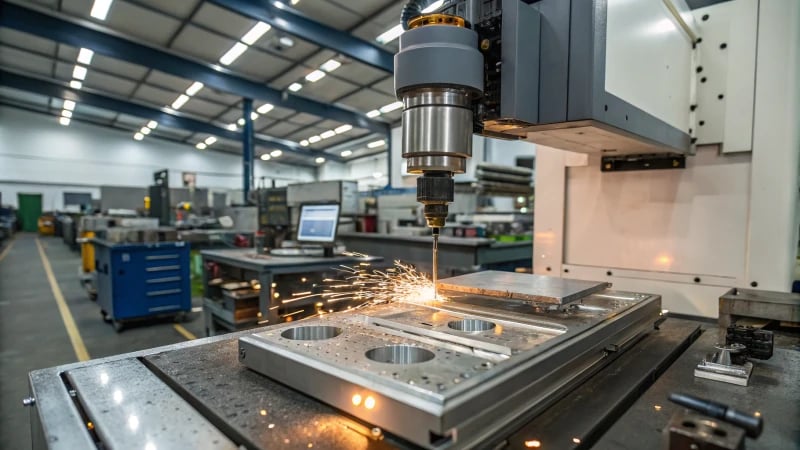
Precision in Mold Insert Manufacturing
Have you ever had to assemble something complex and wished for a magic wand to make everything fit perfectly? That’s what wire cutting feels like in mold insert manufacturing. Picture this: precision so fine that we’re talking about cutting with an accuracy of ±0.005mm or better. This isn’t just about getting a job done; it’s about crafting inserts that slot in like they were born to fit—whether they’re square, round, or have some funky shape you’ve dreamed up.
Insert Type | Precision Level |
---|---|
Square | ±0.005mm |
Round | ±0.005mm |
Special | ±0.005mm |
Post-Quenching Processing
Imagine trying to carve a statue out of granite with a butter knife—sounds impossible, right? That’s what traditional machining feels like post-quenching. But wire cutting? It’s like having a laser-focused chisel that cuts through, regardless of how hard the material has become. It’s this power that maintains the mold’s shape and size, even allowing us to craft intricate structures like those fine reinforcing ribs that hold everything together.
Wire cutting excels here as it’s unaffected by the material’s hardness, preserving the dimensional and shape accuracy of molds, maintaining the structural integrity required for high-precision tasks.
Complex Shape Processing
Remember the first time you saw a magician pull off an unbelievable trick? That’s the level of awe wire cutting brings to complex mold shapes. By programming precise paths, it carves out the most intricate cores and cavities, even those with narrow slits or unique holes, with high-precision contours4. Think of it as creating art out of metal, especially in those delicate molds for watch parts where every detail counts.
Cutting Off Large Inserts
When it comes to big or split-required inserts, wire cutting is like having the perfect tool for the job every time. It delivers unmatched cross-sectional accuracy and flatness, crucial for those parts that need to fit together without a hair out of place.
By embracing wire cutting in these facets of mold insert manufacturing, we achieve precision and efficiency that elevate our work to meet the rigorous standards of today’s production demands.
Wire cutting achieves precision of ±0.005mm in mold inserts.True
Wire cutting provides high precision, ensuring mold inserts meet assembly requirements.
Wire cutting struggles with post-quenching hardened materials.False
Wire cutting excels in processing hardened materials without losing precision.
Why is Wire EDM the Best Choice for Ejector and Cooling Hole Processing?
Ever wondered why Wire EDM is the unsung hero in mold-making? Let me walk you through its magic, especially when it comes to crafting those intricate ejector and cooling holes.
Wire EDM is ideal for ejector and cooling hole processing due to its precision in cutting complex shapes and maintaining tight tolerances, enhancing accuracy and efficiency in mold applications.
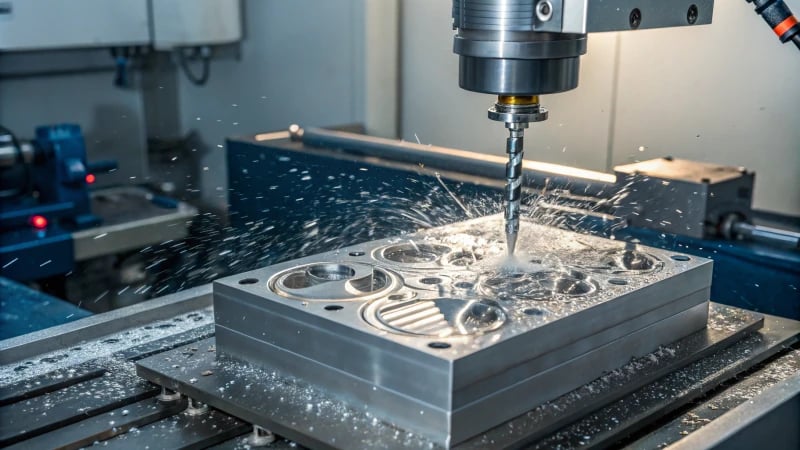
The Precision of Wire EDM in Ejector Hole Processing
I remember the first time I encountered the need for precision in ejector holes—it felt like threading a needle, but on a much larger scale. With Wire EDM, I could program precise paths that allowed me to accurately locate5 and create multiple ejector holes in one go. This capability not only reduced errors but significantly boosted my efficiency in mold manufacturing.
Picture this: producing large injection molds with countless ejector holes. Wire EDM came to my rescue, handling multiple holes simultaneously, speeding up production, and ensuring each hole was consistently accurate in diameter—a must for flawless ejector installation.
Feature | Wire EDM Benefits |
---|---|
Ejector Holes | Accurate positioning and batch processing |
Cooling Hole Innovations with Wire EDM
Cooling holes are like the unsung heroes of mold temperature control during injection molding. I was once tasked with creating a cooling system that demanded intricate designs, and Wire EDM proved invaluable. It allowed me to produce complex shapes, such as spirals, which enhanced heat dissipation.
In high-precision applications where temperature control is crucial, Wire EDM enabled me to craft spiral cooling channels6 that efficiently removed heat, improving the product quality remarkably. This method is vital for molds requiring meticulous temperature management.
Feature | Wire EDM Benefits |
---|---|
Cooling Holes | Complex shapes and precise temperature control |
Versatility in Mold Cavity and Core Processing
The versatility of Wire EDM extends beyond just holes—it’s my go-to for complex mold cavity and core processing. Even when working with post-quenching materials that have hardened, Wire EDM shines by maintaining dimensional and shape accuracy. I find this particularly useful when producing detailed mold parts like reinforcing ribs or intricate internal structures.
Whether it’s creating cavities or cores7 with high-precision contours, even in hardened materials, Wire EDM stands out from traditional methods. This ensures that the final products meet the stringent demands of modern manufacturing, keeping them as precise as the designs intended.
Wire EDM can create multiple ejector holes in one operation.True
Wire EDM is programmed for precision, reducing error margins in mold manufacturing.
Cooling holes made by Wire EDM cannot handle complex shapes.False
Wire EDM excels at creating complex cooling channels, enhancing heat dissipation.
How does wire cutting enhance electrode processing?
Wire cutting is like the magic wand in electrode processing, creating precise shapes and maximizing efficiency for mold manufacturing.
Wire cutting enhances electrode processing by providing precise contour shaping and efficient material use, ensuring high-precision mold manufacturing and accurate adherence to design specifications.
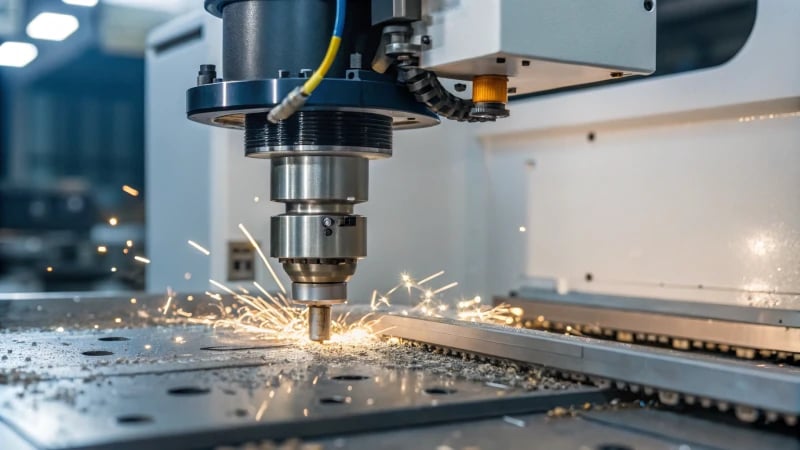
Precision Contour Creation
Wire cutting plays a critical role in creating precise electrode contours. This process is integral in Electrical Discharge Machining (EDM), where electrodes are crafted to exact specifications to ensure accurate mold creation.
By controlling parameters such as the tension and speed of the electrode wire, manufacturers can achieve electrodes with high dimensional accuracy and excellent surface quality. This is particularly important when dealing with complex geometries that require meticulous attention to detail.
For example, when producing electrodes for intricate curved surfaces8 in mold cavities, wire cutting ensures the contour aligns perfectly with design requirements.
Parameters | Importance |
---|---|
Wire Tension | Ensures stability and precision |
Cutting Speed | Influences surface finish and dimensional accuracy |
Material Utilization and Efficiency
Another significant advantage of wire cutting in electrode processing is its ability to maximize material use. By precisely cutting electrode materials into specific shapes as per design needs, it minimizes waste and optimizes resource use.
This is particularly beneficial when manufacturing a set of electrodes needed for various parts of a mold core. Each electrode can be efficiently shaped using wire cutting techniques, ready for subsequent EDM operations.
Consider a scenario where a manufacturer needs electrodes with varying shapes for different mold sections. Wire cutting allows the material to be segmented accurately, ensuring each piece meets precise shape requirements without excess waste.
Explore efficient material usage9 strategies to enhance productivity in electrode processing.
Advanced Applications in Mold Manufacturing
In high-precision industries like mold manufacturing, wire cutting is invaluable. It ensures that every aspect of electrode design is replicated with high fidelity, supporting the production of complex molds. This includes handling intricate designs such as narrow slits or special-shaped holes, which are often challenging with conventional methods.
Moreover, wire cutting is unaffected by material hardness, making it ideal for post-quenching processing tasks where traditional methods might falter. This flexibility allows for maintaining dimensional and shape accuracy after hardening processes without risking deformation.
For instance, when creating cooling holes or ejector holes in molds, wire cutting enables precise positioning and dimensional accuracy, critical for effective mold function and longevity.
Investigate post-quenching processing10 solutions that leverage wire cutting for optimal results.
By employing these capabilities, manufacturers not only enhance the quality of their products but also improve overall production efficiency, meeting high industry standards and customer expectations efficiently.
Wire cutting ensures precise electrode contours in EDM.True
Wire cutting achieves high dimensional accuracy and surface quality for electrodes.
Wire cutting is ineffective for post-quenching processing.False
Wire cutting remains effective after quenching, maintaining shape accuracy.
How does Wire EDM boost efficiency in mold manufacturing?
Have you ever watched a master artist at work, creating something breathtaking with just a few strokes? That’s what Wire EDM is doing for mold manufacturing today.
Wire EDM enhances mold manufacturing efficiency by allowing precise shaping, supporting post-quenching processing, and improving insert and electrode production, which reduces lead times and material waste.
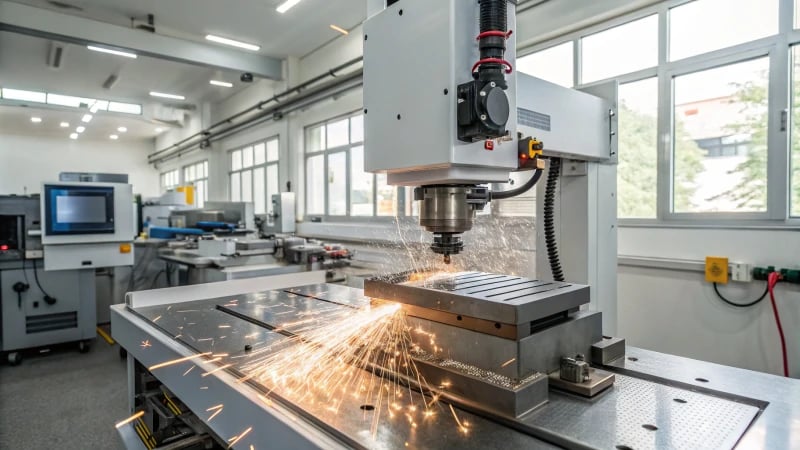
Precision in Mold Cavity and Core Processing
Imagine trying to carve intricate details into a tiny, delicate piece—like crafting a watch part. That’s where Wire EDM shines. With its ability to follow programmable cutting paths, it allows us to create molds with stunning precision, achieving micron-level accuracy. I remember working on a project where the tiniest misalignment could have thrown everything off, but thanks to Wire EDM, we nailed it.
Moreover, wire EDM excels in post-quenching processing. After quenching, mold cavities become tough nuts to crack with traditional methods. But Wire EDM? It’s like a hot knife through butter, slicing through hardened materials without losing an ounce of dimensional accuracy. It’s been a game-changer for high-precision plastic molds, especially when crafting those intricate reinforcing ribs.
Enhancing Mold Insert Processing
Inserts can be tricky little fellows, requiring perfect fit and tight tolerances. I’ve spent hours ensuring every dimension was spot on. With Wire EDM, achieving an accuracy of ±0.005mm is not just possible—it’s practically guaranteed. This tool ensures inserts fit like a glove within the mold assembly, enhancing durability and maintenance efficiency.
A common challenge is cutting large or split inserts while maintaining shape integrity. With wire EDM, the cross-sectional accuracy is maintained even for slender inserts11 that require careful handling during the cutting process.
Streamlined Mold Hole Processing
Ejector and cooling holes are the unsung heroes of mold manufacturing. They need to be just right for everything to function smoothly. Wire EDM allows for precise hole positioning and creation with minimal error margins. I’ve tackled large molds with dozens of ejector holes, and Wire EDM made batch processing them feel like a breeze.
Creating complex cooling channels12 with Wire EDM also means better temperature control during injection molding, resulting in superior product quality.
Efficient Electrode Production
Electrodes are pivotal in shaping mold cavities. Wire EDM crafts these with remarkable precision and high surface quality, adhering to even the most stringent design specs. It optimizes material usage by efficiently cutting electrodes into multiple shapes.
For electrodes with complex designs, Wire EDM is an indispensable asset in modern mold-making13, ensuring every contour is precisely as intended.
Process | Benefits |
---|---|
Mold Cavity Processing | High precision for complex shapes |
Post-Quenching | Maintains accuracy in hard materials |
Insert Manufacturing | Tight tolerance and fit |
Hole Processing | Precise multi-hole batch processing |
Electrode Production | Optimized material usage and precision |
In my experience, integrating Wire EDM into our processes has been like adding a fine-tipped brush to an artist’s palette—allowing for detail, precision, and efficiency that seemed out of reach before.
Wire EDM achieves ±0.005mm accuracy in mold insert processing.True
Wire EDM provides high precision, crucial for tight tolerance in inserts.
Wire EDM cannot process hardened materials after quenching.False
Wire EDM effectively processes hardened materials without affecting accuracy.
Conclusion
Wire cutting technology, specifically Wire EDM, revolutionizes injection mold manufacturing by enhancing precision, enabling complex shapes, and improving efficiency in post-quenching processing and insert production.
-
Discover real-world applications of Wire EDM in creating high-precision watch parts molds. ↩
-
Learn about advanced techniques for manufacturing high-precision inserts using Wire EDM. ↩
-
Understand how Wire EDM enhances electrode contour processing with superior accuracy. ↩
-
Learn how wire cutting achieves intricate designs to enhance the quality and functionality of molds. ↩
-
Explore how Wire EDM enhances positional accuracy in creating multiple ejector holes efficiently. ↩
-
Discover how Wire EDM crafts intricate cooling channels that improve mold temperature control. ↩
-
Find out how Wire EDM produces high-precision contours in mold cavities and cores. ↩
-
Learn how wire cutting achieves precise contours essential for crafting intricate curved surfaces. ↩
-
Discover strategies to optimize resource use during electrode production, enhancing efficiency. ↩
-
Find solutions for maintaining shape accuracy in hardened materials through wire cutting. ↩
-
Learn about techniques to maintain accuracy when cutting slender inserts with wire EDM. ↩
-
Understand the advantages of using wire EDM to create efficient cooling channels. ↩
-
Discover how wire EDM optimizes electrode production for modern mold manufacturing. ↩