Let me take you into the intricate world of injection molding, where every detail counts.
Waterway design is crucial in injection molds because it ensures effective cooling, which directly affects the dimensional accuracy, mechanical properties, and surface quality of the molded parts. Proper design reduces cycle times, enhances production efficiency, and stabilizes production processes.
But there’s so much more to explore beyond the surface. Join me as we dive deeper into how waterway design intricately weaves into the fabric of product quality and manufacturing efficiency.
Water channel diameter affects mold cooling efficiency.True
Optimal diameters ensure balanced cooling and maintain mold integrity.
How Does Water Channel Diameter Affect Cooling Efficiency?
Water channel diameter is pivotal in dictating the cooling efficiency of injection molds, impacting both product quality and manufacturing speed.
The diameter of water channels in injection molds is crucial for cooling efficiency. Smaller diameters can restrict water flow, leading to poor cooling, while excessively large diameters might compromise mold strength. Optimal diameters, typically between Ø6 – Ø12mm, ensure balanced cooling and maintain mold integrity.
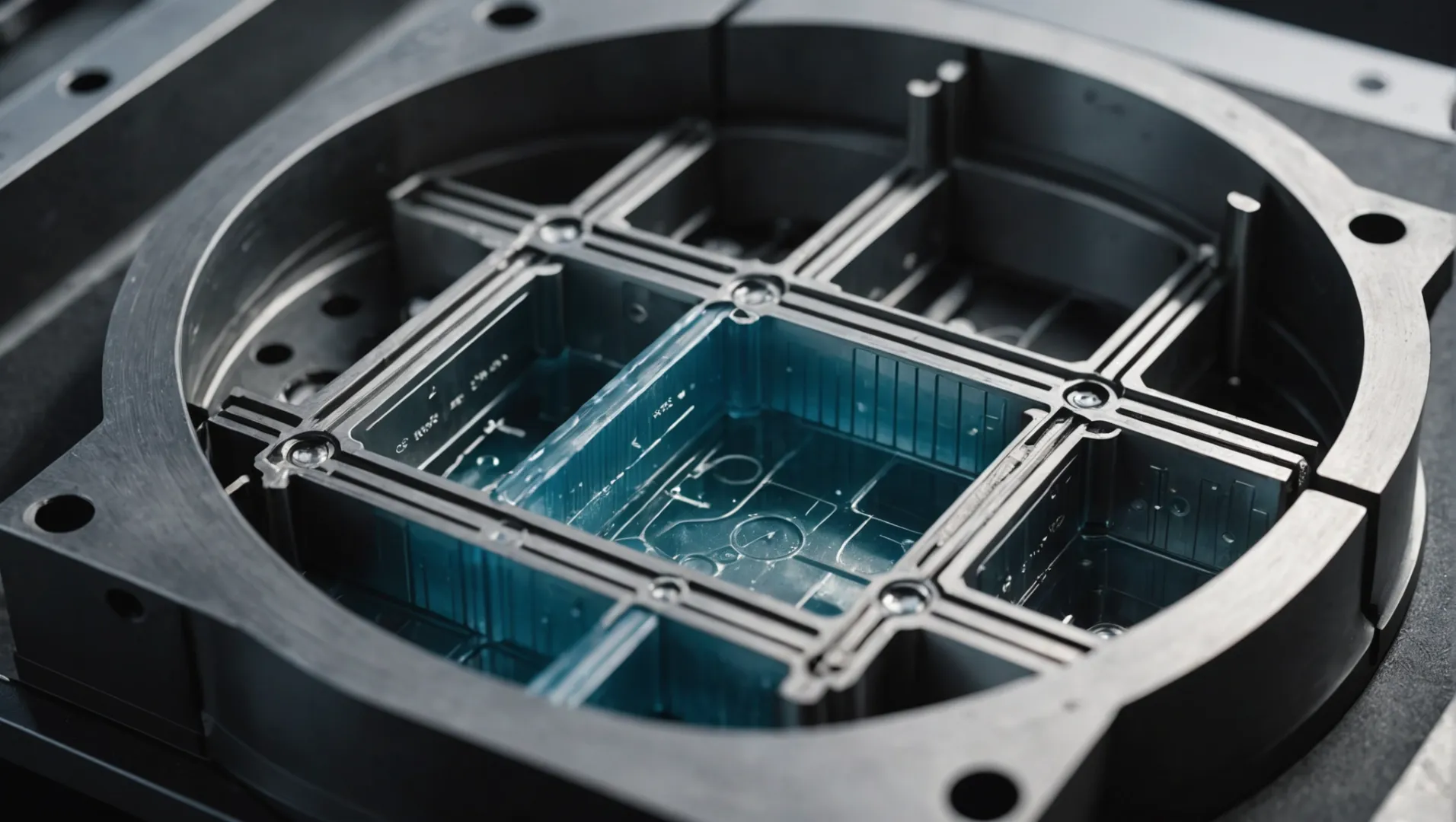
The Role of Water Channel Diameter in Cooling
In the realm of injection molding, the diameter of water channels significantly influences cooling performance. Cooling efficiency not only affects the dimensional accuracy and mechanical properties of the final product but also determines the overall cycle time of the molding process.
Optimal Diameter Selection
The choice of water channel diameter typically ranges from Ø6mm to Ø12mm, based on the size and complexity of the mold. For smaller components or molds with less demanding cooling needs, a diameter of Ø6 – Ø8mm is often sufficient. Conversely, larger parts or those requiring rapid heat dissipation might benefit from diameters closer to Ø10 – Ø12mm. This selection ensures an adequate flow rate and prevents overheating or uneven cooling, which can lead to defects such as warping or internal stresses.
Table 1: Recommended Water Channel Diameters
Mold Size | Recommended Diameter |
---|---|
Small Injection Parts | Ø6 – Ø8mm |
Large Injection Parts | Ø10 – Ø12mm |
Balancing Flow Rate and Structural Integrity
While a larger diameter can increase the flow rate and enhance cooling efficiency, it also poses challenges. An overly large channel may weaken the mold’s structural integrity or complicate manufacturing processes. On the other hand, smaller diameters might restrict water flow, leading to insufficient cooling and longer cycle times. Therefore, striking a balance between these factors is crucial for optimizing both the performance and durability of injection molds.
Practical Implications
Consider a complex automotive part1 requiring consistent cooling across varied geometric profiles. Here, a strategic combination of different channel diameters might be employed to ensure uniform temperature distribution without compromising mold strength.
Interaction with Other Design Elements
Water channel diameter is intricately linked with other design factors, such as the distance from the cavity surface2 and channel arrangement. Ideally, the distance should be 1.5 – 2 times the channel diameter to maximize cooling effectiveness without risking mold damage or inefficient heat transfer.
By carefully selecting the diameter and considering its interaction with other design parameters, manufacturers can achieve significant improvements in cooling efficiency, product quality, and production rates.
Smaller water channels improve cooling efficiency.False
Smaller diameters restrict flow, leading to poor cooling efficiency.
Larger channel diameters can weaken mold structure.True
Excessively large diameters may compromise the mold's strength.
What Role Does Water Channel Arrangement Play in Mold Performance?
Understanding the impact of water channel arrangement in molds is crucial for optimizing injection molding performance.
Water channel arrangement significantly influences mold performance by ensuring uniform cooling, which affects product quality and production efficiency. Proper arrangement can prevent defects, maintain structural integrity, and reduce cycle times.
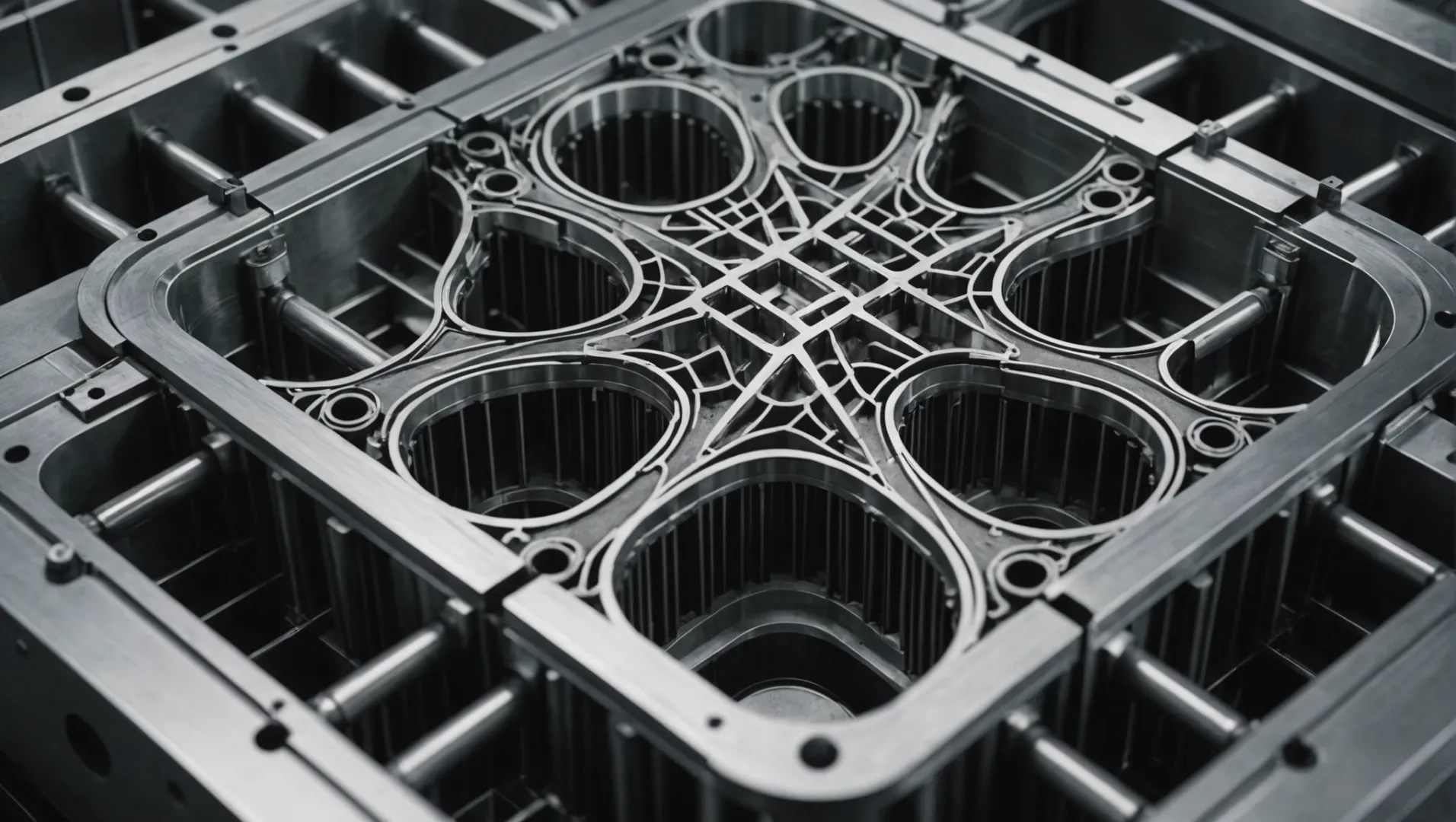
The Science Behind Water Channel Arrangement
In injection molding, the arrangement of water channels determines how efficiently heat is dissipated from the mold. By strategically placing water channels, mold designers can achieve consistent temperature control, which is vital for maintaining the integrity of the molded part.
-
Plane Arrangement: This method is typically used for flat or simply shaped parts. By arranging channels parallel to the part’s contour, uniform cooling is ensured, preventing warping or shrinkage issues. For example, plane arrangement techniques3 are highly effective for creating flawless flat panels.
-
Surrounding Arrangement: Ideal for circular parts like plastic cups, surrounding arrangements help maintain even cooling around the circumference. This prevents any one side from cooling faster than another, which could lead to deformation.
-
Three-Dimensional Arrangement: Complex parts demand a more intricate water channel setup. By incorporating channels in various planes and directions, molds can be cooled evenly despite their complexity. For instance, three-dimensional designs4 are essential in automotive component manufacturing.
Balancing Structural Integrity with Cooling Efficiency
The distance between the water channel and the cavity surface also plays a pivotal role. An optimal distance ensures effective cooling without compromising mold strength. Typically, this distance is 1.5 to 2 times the diameter of the channel, ensuring balance between cooling efficiency and mold durability.
Additionally, the diameter of these channels must be chosen carefully. Smaller diameters might lead to insufficient water flow, whereas larger diameters can weaken the mold’s structure. For larger molds or those with stringent cooling needs, a diameter range of Ø10 – Ø12mm is recommended.
Enhancing Production Through Optimized Water Channel Design
A well-conceived water channel layout not only improves product quality but also boosts production efficiency. By reducing cooling times—an aspect that constitutes up to 80% of the molding cycle—manufacturers can significantly increase throughput. In practice, enhancing water channel design can decrease cooling time by approximately 10%, leading to substantial cost savings in mass production settings.
To summarize, the strategic arrangement of water channels in molds is a multifaceted process that influences both product quality and manufacturing efficiency. By carefully considering factors such as channel placement, diameter, and proximity to the mold cavity, manufacturers can achieve superior results in injection molding.
Plane arrangements prevent warping in flat parts.True
Plane arrangements ensure uniform cooling, preventing warping issues.
Larger water channel diameters always improve cooling.False
Larger diameters can weaken mold structure, affecting efficiency.
How Does Cooling Influence Product Quality in Injection Molding?
Cooling in injection molding is critical, impacting the dimensional accuracy, mechanical properties, and surface quality of products.
Cooling determines product quality in injection molding by affecting shrinkage, internal stress, and surface finish. Proper cooling ensures uniform shrinkage, enhancing dimensional accuracy and mechanical properties while preventing defects such as weld marks and air marks.
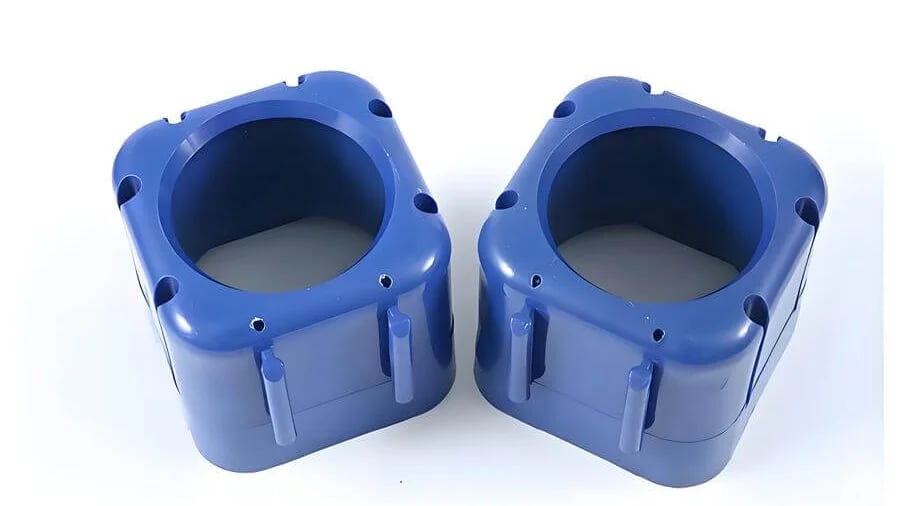
The Science of Cooling in Injection Molding
Cooling is a vital phase in the injection molding process. It begins right after the molten plastic fills the mold cavity, and its importance cannot be overstated. The cooling phase affects not only how quickly a part can be ejected from the mold but also how well it performs in its intended application.
The primary goal of cooling is to solidify the molten plastic to a temperature where it can withstand demolding forces without distortion. This requires precise control over cooling rates and temperatures. Variations can lead to discrepancies in the final product’s dimensions and structural integrity.
Impact on Dimensional Accuracy
Uniform cooling is crucial for maintaining dimensional accuracy5. If some areas of the part cool faster than others, it can result in uneven shrinkage. For instance, if a part is thicker at one end, it will cool slower there, leading to possible warping or misalignment. A well-designed water channel system ensures even heat dissipation across the mold, maintaining tight tolerances essential for applications like precision components in electronics.
Enhancing Mechanical Properties
The cooling rate influences the crystallinity and molecular orientation of polymers, which directly affect mechanical properties such as strength and toughness. Faster cooling rates typically result in less crystalline structures, which might be advantageous for certain polymers that benefit from amorphous phases.
For example, in the production of automotive components requiring high impact resistance, controlling the cooling rate helps achieve the necessary balance between toughness and rigidity.
Surface Quality Considerations
Surface defects like weld marks and air marks are common challenges when cooling is not optimized. These defects occur when cooling is uneven, leading to incomplete fusion of different flow fronts within the mold cavity. A thoughtful water channel arrangement6 minimizes these issues by providing consistent cooling rates.
Furthermore, rapid or uneven cooling can cause surface tensions that manifest as visible defects or reduce the surface finish quality. By managing these factors through effective cooling strategies, manufacturers can improve both the aesthetics and functionality of their products.
Cooling’s role in injection molding extends far beyond solidification. Its influence on product quality makes it a cornerstone of successful manufacturing, affecting everything from appearance to performance.
Cooling affects dimensional accuracy in injection molding.True
Uniform cooling prevents uneven shrinkage, maintaining tight tolerances.
Faster cooling rates increase crystallinity in polymers.False
Faster cooling generally results in less crystalline, more amorphous structures.
Can Optimized Waterways Improve Production Efficiency?
Harnessing the power of optimized waterways can drastically enhance production efficiency in injection molding processes.
Optimized waterways improve production efficiency by reducing cooling times, enhancing product quality, and stabilizing manufacturing processes. Proper design and arrangement of water channels ensure uniform cooling, leading to shorter cycle times and fewer defects.
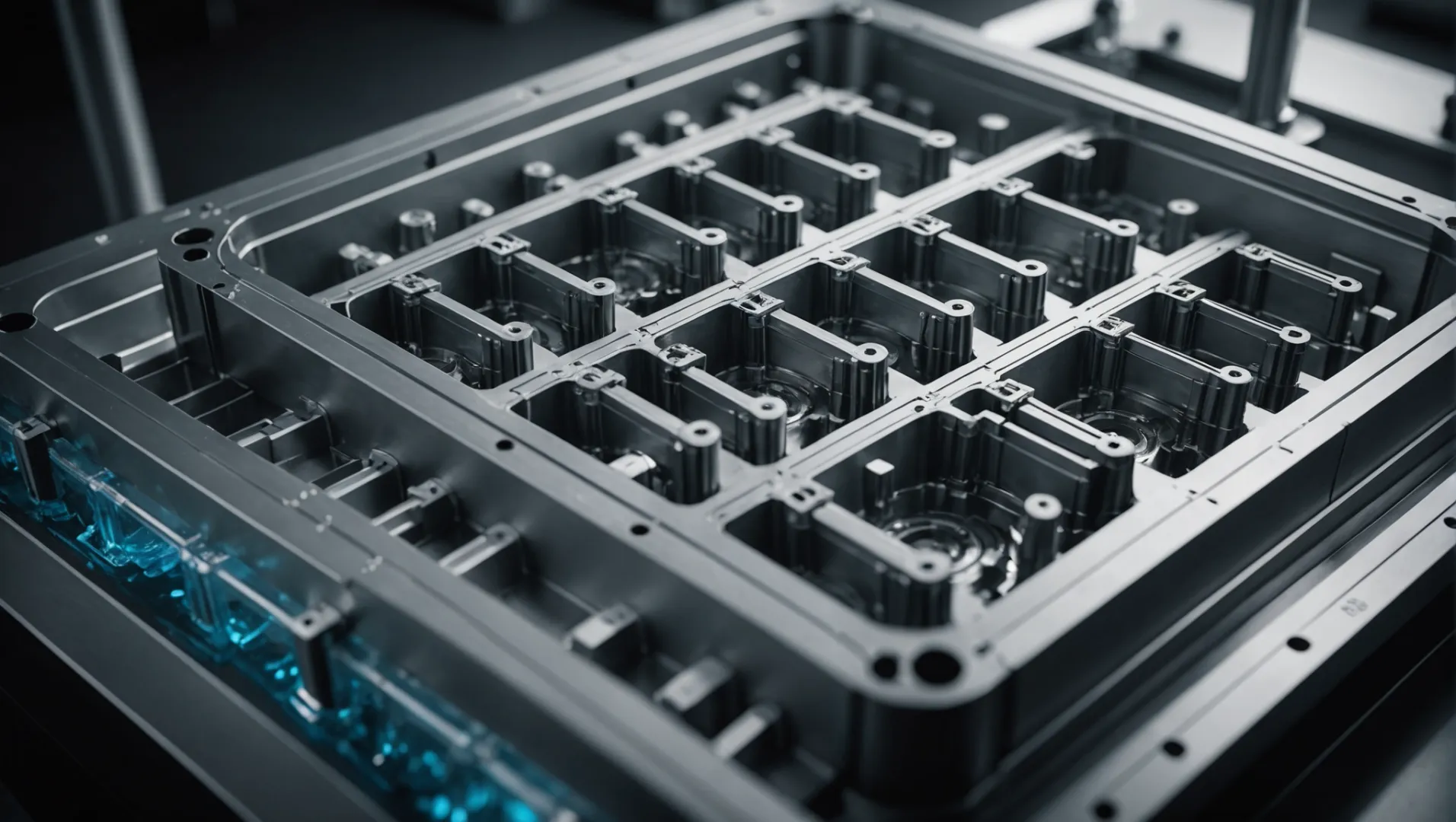
Understanding Waterway Optimization
In injection molding, optimizing waterways involves selecting the right water channel diameter7, maintaining proper distances from the cavity, and arranging channels strategically. These elements work together to ensure effective cooling, which is essential for enhancing production efficiency. Cooling accounts for a significant portion of the molding cycle, making its efficiency crucial.
Water Channel Diameter
Choosing the correct diameter for water channels is critical. For smaller injection parts, a diameter of Ø6 – Ø8mm is optimal, while larger parts may require Ø10 – Ø12mm. A too-small diameter can lead to insufficient cooling, whereas a too-large diameter may compromise mold strength.
Distance from Cavity
The distance between water channels and the cavity is equally important. Ideally, this should be 1.5 to 2 times the diameter of the water channel. This ensures adequate cooling without compromising mold integrity or allowing plastic melt infiltration.
Impact on Production Efficiency
Shortened Molding Cycles
Efficient waterway designs can reduce cooling times by up to 10%, significantly shortening overall molding cycles. This reduction translates directly into increased production capacity, especially vital for high-volume manufacturing environments.
Parameter | Standard Measurement | Impact on Efficiency |
---|---|---|
Water Channel Diameter | Ø6 – Ø12mm | Affects cooling rate and mold integrity |
Distance from Cavity | 1.5 – 2 times diameter | Ensures balanced cooling |
Enhanced Product Quality
Uniform cooling facilitated by well-optimized waterways leads to consistent dimensional accuracy and surface quality. This minimizes defects like air marks or weld lines, reducing scrap rates and enhancing product reliability.
Stable Production Processes
An optimized cooling system maintains consistent mold temperatures, minimizing fluctuations that can lead to product defects. This stability supports continuous production with fewer interruptions and lower scrap rates.
Conclusion: A Strategic Approach
Implementing an optimized waterway design is not just about reducing cycle times or improving quality—it’s about creating a robust production environment8 that can meet high demands efficiently. By focusing on channel diameter, placement, and arrangement, manufacturers can achieve a competitive edge in both quality and efficiency.
Optimized waterways reduce cooling times by up to 10%.True
Efficient waterway designs shorten cooling, boosting production speed.
Water channels should always be 3 times their diameter from the cavity.False
Ideal distance is 1.5 to 2 times the channel's diameter.
Conclusion
In short, effective waterway design is pivotal in enhancing injection molding outcomes. Reflect on your current designs and consider improvements for better quality and efficiency.
-
Learn how varied diameters ensure uniform cooling for complex parts.: Cooling channels are a critical component of mold design that helps parts cool at the same rate throughout the part. ↩
-
Discover ideal spacing for maximizing cooling efficiency.: The center distance between adjacent channel can be 1.7 to 2 times diameter of the channel. This is also governed by the strength of mould steel. The difference … ↩
-
Discover methods to achieve uniform cooling in flat panel molding.: Discover strategies and best practices in design for injection molding, a method for producing cost-effective plastic and metal parts. ↩
-
Learn how complex designs ensure even cooling for intricate parts.: By utilizing metal 3D printers, you can greatly reduce the number of machining processes while having a high degree of flexibility in design. This means that … ↩
-
Learn how uniform cooling affects precision in molded parts.: Uneven cooling causes differences in the crystallinity of each part of the molded product, resulting in dimensional defects such as warpage and … ↩
-
Explore water channel strategies that enhance surface finish quality.: The channel design/modification tools in HEC-RAS allow the user to perform a series of trapezoidal cuts into the existing channel geometry or to create new … ↩
-
Learn about ideal diameters for efficient cooling in molds.: The right mold components can help improve mold cooling and thereby produce higher-quality parts. ↩
-
Discover how strategic planning enhances molding efficiency.: Making injection molding more sustainable aims to minimize material waste through efficient designs, optimized mold layouts, and the reduction … ↩