Have you ever wondered why injection molding is the go-to method for manufacturers?
Injection molding is fast and cost-effective due to its high degree of automation, short production cycles, low raw material costs, shared mold expenses, and reduced energy consumption. This process allows for mass production of complex shapes with high precision.
Let’s dive deeper into the intricacies of injection molding and uncover how it revolutionizes manufacturing efficiency.
Injection molding is highly automated.True
Automation minimizes human intervention, enhancing efficiency and reducing errors.
How Does Automation Enhance Injection Molding Efficiency?
Automation is revolutionizing injection molding, driving efficiency and reducing costs.
Automation in injection molding enhances efficiency by minimizing manual intervention, reducing human error, and optimizing cycle times. Automated control systems manage operations from material handling to product ejection, ensuring consistent quality and reduced scrap rates.
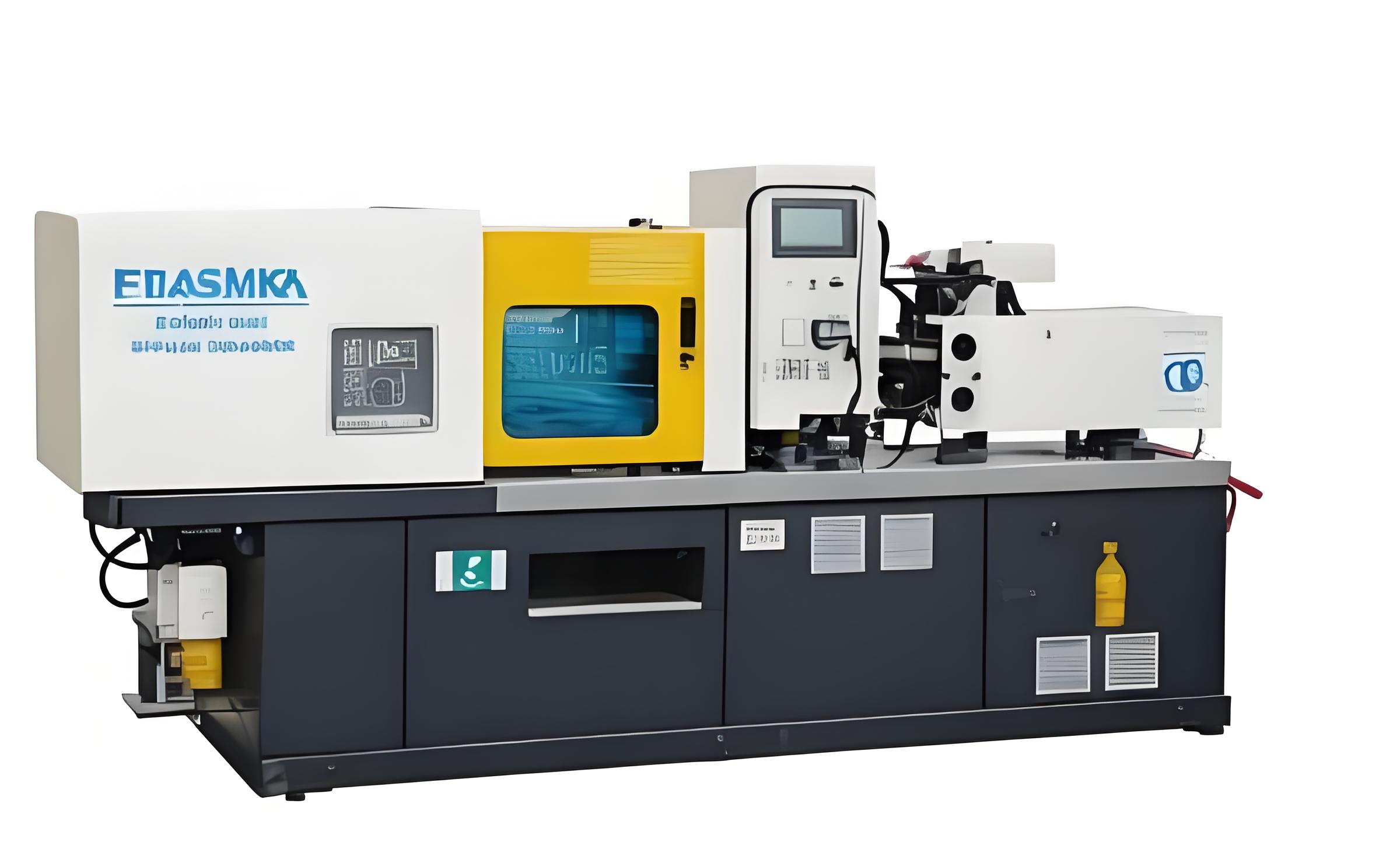
The Role of Automation in Streamlining Production
Automation is the backbone of modern injection molding, transforming it into a highly efficient process. Automated control systems in injection molding machines manage every stage, from raw material delivery to mold ejection. This minimizes the need for human intervention, thereby reducing the likelihood of errors and inconsistencies. By maintaining precise control over process variables, these systems ensure consistent product quality and significantly lower scrap rates.
For instance, automated control systems1 can precisely regulate temperature and pressure conditions, essential for the optimal flow of plastic into molds. This precision is crucial for maintaining tight tolerances and high-quality finishes.
Optimizing Production Cycles Through Automation
One of the standout features of injection molding is its rapid production cycle. Automation plays a pivotal role here by optimizing each phase of the process. Once a mold is set up and debugged, automated systems manage the swift filling, cooling, and ejection of the product with remarkable speed.
A typical cycle might involve seconds for the injection phase and mere minutes for cooling, depending on material properties and product complexity. Automation ensures these cycles are repeatable with minimal variation, maximizing throughput while maintaining quality.
Reducing Costs Through Automated Systems
While initial investments in automation technology can be substantial, the long-term cost benefits are significant. Automated systems contribute to cost reduction by minimizing labor expenses and lowering defect rates. They also enable the efficient use of raw materials through precise dosing and minimize waste through optimized processes.
Moreover, with modern advancements in CAD/CAM2, automated systems can even assist in designing molds that are easier to manufacture and maintain, further reducing downtime and associated costs.
Enhancing Flexibility and Adaptability
Automation doesn’t just boost efficiency—it also enhances flexibility. With programmable systems, manufacturers can quickly adjust parameters to accommodate different materials or design changes without extensive downtime. This adaptability is crucial in today’s fast-paced market where consumer demands shift rapidly.
For example, flexible manufacturing systems3 allow for quick switching between different product lines or custom runs with minimal setup time.
In conclusion, while automation in injection molding primarily enhances efficiency by streamlining processes and reducing errors, its benefits extend beyond production speed to include significant cost savings and increased adaptability in manufacturing.
Automation reduces scrap rates in injection molding.True
Automated systems ensure precise control, minimizing errors and scrap.
Manual intervention is essential in automated injection molding.False
Automation minimizes manual intervention, enhancing efficiency and consistency.
What Role Do Raw Materials Play in Cost Reduction?
Raw materials significantly influence the cost-effectiveness of injection molding, directly impacting overall production expenses.
In injection molding, raw materials like plastics are cost-effective due to their low base cost, recyclability, and reduced energy consumption during processing. This makes them crucial in minimizing production costs while maintaining high-quality outputs.
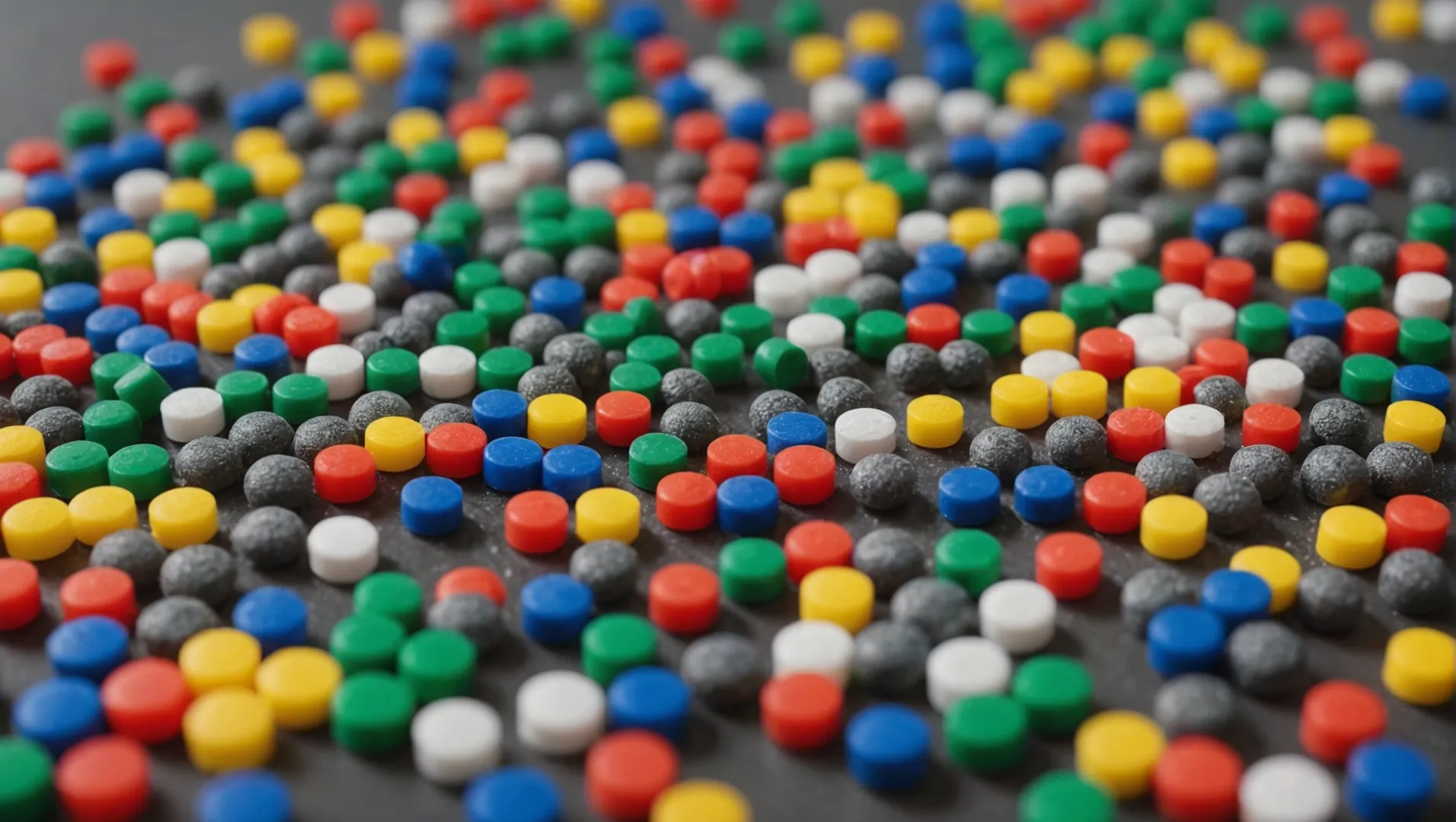
Understanding the Cost of Raw Materials in Injection Molding
Injection molding primarily uses plastic raw materials, which are inherently less expensive compared to other materials like metals or ceramics. Plastics, derived from petrochemicals, benefit from continuous advancements in petrochemical technology, which have driven down production costs. Additionally, plastics offer versatility in terms of material properties4, allowing manufacturers to select the most cost-effective option that meets performance requirements.
The Recyclability Advantage
One of the significant benefits of using plastic raw materials is their recyclability. Recycled plastics can be reintroduced into the production cycle, effectively reducing the demand for new raw materials and, consequently, lowering production costs. This practice not only supports environmental sustainability but also aligns with economic strategies by cutting down on waste and resource consumption.
Raw Materials and Energy Efficiency
Plastics require less energy to process in injection molding compared to other materials. This energy efficiency is a direct result of the properties of plastics that allow for quick heating and cooling cycles. Moreover, innovative heating technologies5 such as electromagnetic heating used in injection molding machines further optimize energy consumption. By minimizing energy usage, manufacturers can significantly reduce operational costs.
Comparing Costs with Other Materials
Material | Base Cost | Recyclability | Energy Efficiency |
---|---|---|---|
Plastics | Low | High | High |
Metals | High | Moderate | Low |
Ceramics | High | Low | Moderate |
The table above illustrates how plastics stand out in terms of cost-effectiveness compared to metals and ceramics. Their low base cost, high recyclability, and superior energy efficiency make them an ideal choice for injection molding processes aimed at cost reduction.
By leveraging these characteristics, manufacturers can produce high-quality products efficiently and economically, ensuring competitiveness in various industries like automotive, electronics, and consumer goods.
Plastics have a lower base cost than metals in molding.True
Plastics are derived from petrochemicals, making them cheaper than metals.
Recyclability increases the cost of using plastics in molding.False
Recyclability reduces the need for new materials, lowering costs.
How is Energy Consumption Minimized in Injection Molding?
Discover how modern injection molding processes minimize energy usage while enhancing efficiency.
Energy consumption in injection molding is minimized through efficient heating systems, optimized motor power, and advanced technologies that streamline production processes.
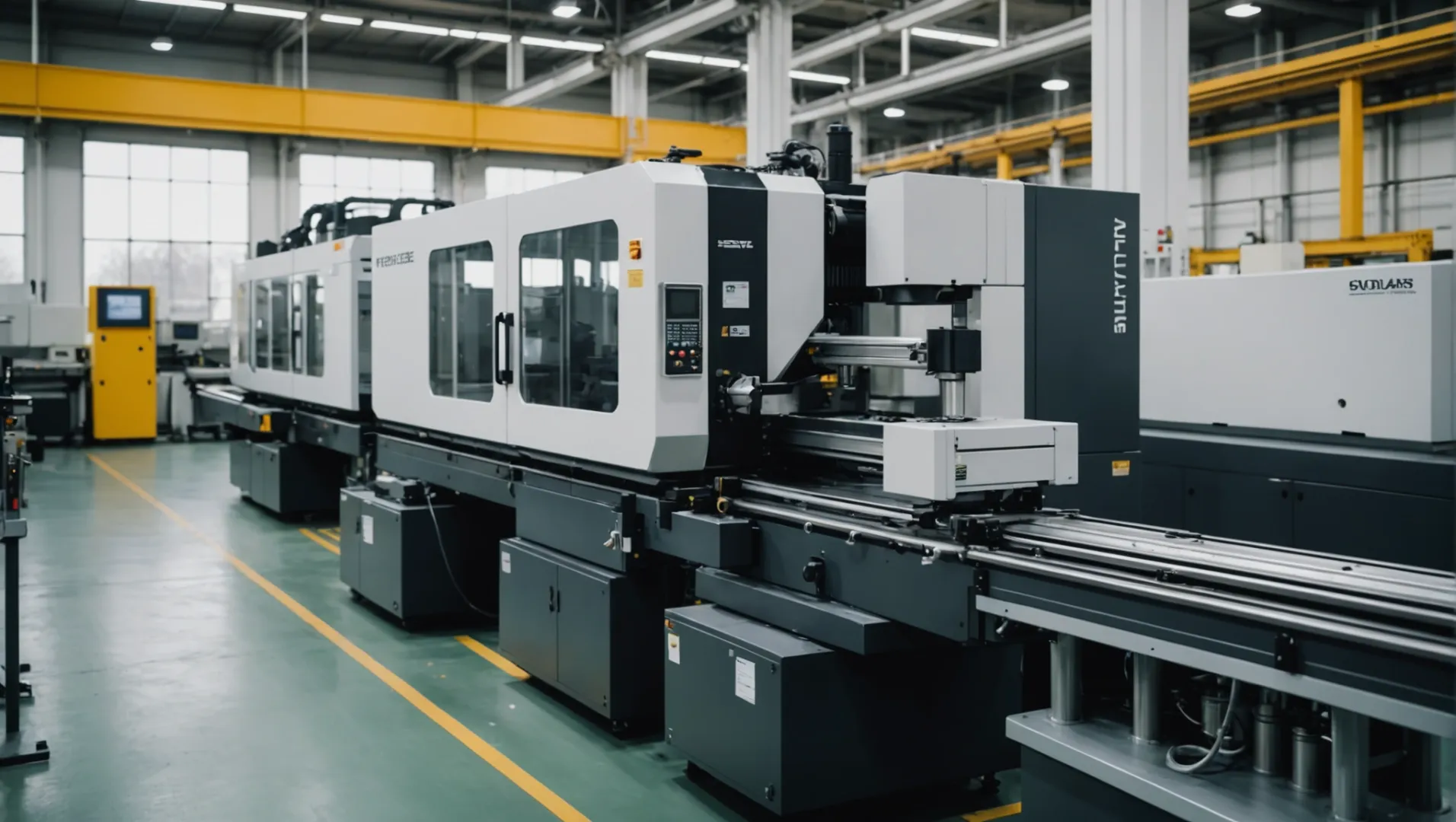
Understanding the Energy Dynamics in Injection Molding
Injection molding is recognized for its energy efficiency compared to other manufacturing processes. This efficiency stems from the ability to produce large volumes of parts with minimal energy wastage. By understanding the key areas where energy consumption occurs, manufacturers can implement strategies to further reduce energy use.
Efficient Heating Systems
One of the primary energy-consuming stages in injection molding is the heating of plastic materials. To address this, modern machines employ advanced heating technologies such as electric or electromagnetic heating. These systems quickly bring materials to the required temperature with minimal waste. Energy-efficient heating methods6 not only reduce energy use but also shorten cycle times, enhancing overall productivity.
Optimizing Motor Power
Injection molding machines are equipped with motors that can adjust their power output based on production needs. This adaptability ensures that machines do not consume more energy than necessary. Variable frequency drives (VFDs) and servo motors are examples of technologies that allow precise control over motor functions, thus reducing unnecessary energy expenditure. Motor efficiency in injection molding7 is a critical factor in minimizing energy costs.
Automation and Energy Management
Automation plays a pivotal role in managing energy consumption. Automated systems can adjust operations dynamically, ensuring that each step of the injection process runs at optimal efficiency. By reducing human error and maintaining consistent quality, automation minimizes both energy use and material waste. Furthermore, integrating energy management systems allows manufacturers to monitor and control energy usage across operations. Role of automation in reducing energy consumption8 is increasingly prominent in modern facilities.
Conclusion
Through a combination of efficient heating, adaptable motor technology, and automation, injection molding stands as a benchmark for energy-efficient manufacturing. These advancements not only contribute to cost savings but also support sustainable production practices.
Efficient heating reduces energy use in injection molding.True
Advanced heating systems minimize waste, lowering energy consumption.
Automation increases energy consumption in injection molding.False
Automation optimizes processes, reducing both energy and material waste.
What Makes Injection Molding Suitable for Complex Shapes?
Injection molding enables the creation of intricate designs with precision and efficiency, ideal for complex manufacturing needs.
Injection molding’s suitability for complex shapes stems from its ability to produce high-precision parts with intricate geometries in a single process. By utilizing advanced mold designs and diverse plastic materials, this method allows for the efficient production of detailed components without the need for additional machining or assembly.

Advanced Mold Design Capabilities
Injection molding stands out in manufacturing due to its ability to produce complex shapes with remarkable precision. One of the primary reasons is the use of advanced mold design9 technologies. With modern techniques like computer-aided design (CAD) and computer-aided manufacturing (CAM), intricate mold designs can be developed and fine-tuned to ensure that each component is produced accurately.
These sophisticated molds allow for the creation of parts with undercuts, complex cavities, and tight tolerances, which would be challenging to achieve with other manufacturing processes. For example, the automotive industry often utilizes injection molding to produce components with complex geometries that fit precisely within larger assemblies.
Diverse Material Compatibility
The versatility of injection molding extends to its compatibility with a wide range of plastic materials. This flexibility is crucial for creating products that require specific material properties, such as strength, flexibility, or resistance to environmental factors.
By selecting the appropriate material, manufacturers can ensure that the final product meets the necessary performance standards without compromising on design complexity. The ability to use various materials also facilitates innovation, allowing designers to experiment with different formulations to achieve unique outcomes.
Single-Process Manufacturing
A significant advantage of injection molding is its capability to produce fully formed products in a single operation. This efficiency reduces the need for secondary processes such as machining, drilling, or assembly, which can add time and cost.
By eliminating these additional steps, injection molding not only speeds up production but also minimizes potential errors and inconsistencies that may arise during manual assembly. This feature is particularly beneficial in industries where precision and reliability are paramount, such as electronics and medical devices.
Precision and Repeatability
Injection molding excels in delivering consistent results across large production runs. Once a mold is created and validated, it can be used to produce thousands or even millions of identical parts with minimal variation. This repeatability ensures that every piece maintains the same quality and precision as the first, which is essential for maintaining product integrity in competitive markets.
In summary, the ability of injection molding to efficiently produce complex shapes with high precision, material diversity, and single-process manufacturing makes it an ideal choice for industries requiring intricate component designs.
Injection molding uses CAD for mold design.True
CAD enhances precision in creating intricate mold designs.
Injection molding requires multiple processes for complex shapes.False
It produces complex shapes in a single process, reducing extra steps.
Conclusion
In summary, injection molding’s combination of advanced technology and strategic cost factors makes it a powerhouse in manufacturing. Embracing these principles can help businesses stay competitive.
-
Learn how automated controls optimize precision and reduce errors.: Better machine utilization. Automated plastic injection molding systems are interconnected. · Quicker production · Lower labor costs · Improved fabrication … ↩
-
Discover how CAD/CAM improves mold design and efficiency.: Advanced CAD/CAM software with dedicated electrode design capabilities greatly reduces electrode design, modeling and manufacturing time. Read … ↩
-
Explore how flexible systems enhance adaptability in production.: A flexible manufacturing system (FMS) is an integrated manufacturing setup that allows for the efficient production of a variety of products … ↩
-
Explore diverse plastic types for optimal material selection.: There are three main classes of TPU materials: polyester, polyether, and polycaprolactone. Trademarked products are available from manufacturers such as Lanxess … ↩
-
Learn about advanced heating technologies that reduce energy costs.: Insulating the Barrel · 100% Electric Machines · Use a Variable Speed Drive · Calculating Life Cycle Costs · Use the Correct Machine for the Product. ↩
-
Learn about advanced heating technologies that cut energy use.: Injection molds are heated using electric heating or hot runner systems. Different heating methods have different heating rates and control capabilities. ↩
-
Understand how motor control reduces unnecessary energy consumption.: Here are six different energy saving methods that can be used to help reduce the amount of energy needed. ↩
-
Explore how automation enhances energy efficiency in manufacturing.: Intelligently designed home automation systems can help lower your home’s energy consumption, thus reducing your household expenses and your carbon footprint. ↩
-
Explore how advanced mold design enhances precision and complexity in manufacturing.: Manufacturing complex injection-molded parts often requires more advanced molding techniques like side-action cams, pickout inserts, … ↩