Short shots in injection molding1 occur when the molten plastic fails to completely fill the mold cavity, resulting in incomplete or partially formed parts. This defect is a common challenge in industries like automotive, medical, and consumer goods, especially for parts with complex geometries or thin walls. Addressing short shots2 is critical to maintaining product quality, minimizing waste, and ensuring efficient production processes.
Short shots happen when the mold doesn’t fully fill, often due to low pressure, temperature issues, or poor mold design3, leading to incomplete parts that can disrupt manufacturing.
This article explores the causes of short shots, debunk common misconceptions, and provide actionable solutions to prevent and troubleshoot this issue, ensuring high-quality injection-molded parts.
Short shots are always caused by low injection pressure.False
While low injection pressure is a frequent cause, short shots can also stem from inadequate temperatures, material flow issues, or suboptimal mold design.
Short shots only affect the appearance of the part.False
Beyond aesthetics, short shots can undermine the functionality and structural integrity of parts, particularly in precision-driven applications.
What Are Short Shots in Injection Molding?
Short shots refer to a defect where the plastic material does not fully occupy the mold cavity during the injection molding process4, producing incomplete parts. This issue is especially prevalent in high-precision sectors like medical device manufacturing, where even minor imperfections can lead to significant consequences.
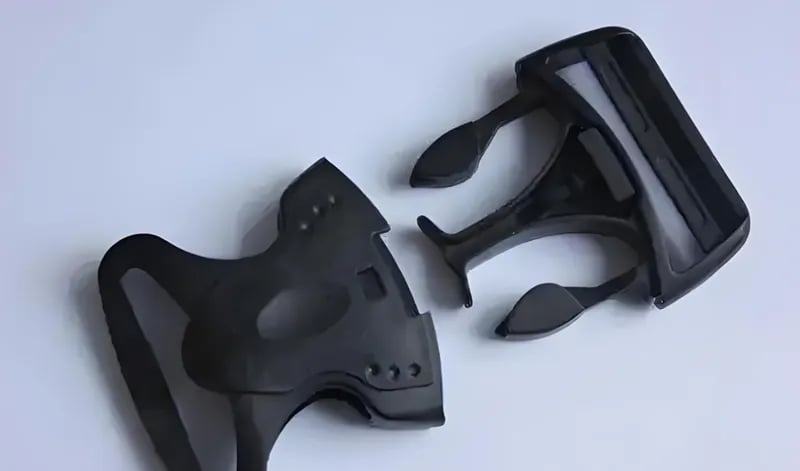
Short shots occur when molten plastic fails to fill the mold completely, often due to insufficient pressure, temperature, or poor mold design, resulting in defective parts.
Cause of Short Shot | Solution |
---|---|
Low Injection Pressure | Increase pressure to ensure complete filling. |
Inadequate Melt Temperature | Raise melt temperature for better flowability. |
Poor Mold Design | Enhance venting and optimize gate placement. |
Insufficient Material Supply | Verify material availability and clear blockages. |
High Material Viscosity | Use materials with better flow or adjust settings. |
Causes of Short Shots
Several factors contribute to short shots, including:
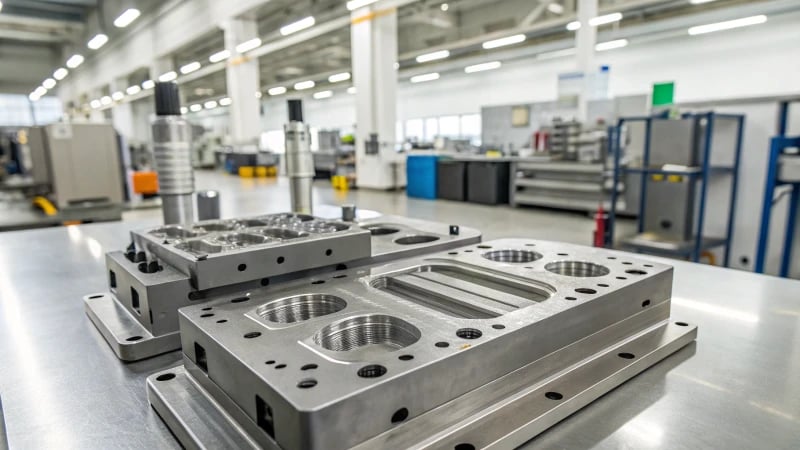
-
Low Injection Pressure: Insufficient force prevents the plastic from reaching all areas of the mold.
-
Temperature Issues: Low melt or mold temperatures can cause the plastic to solidify prematurely.
-
Mold Design Flaws: Inadequate venting, small gates, or poorly designed runners can impede material flow.
-
Material Properties: High-viscosity plastics with poor flow characteristics can struggle to fill intricate molds.
Impact of Short Shots
Short shots compromise both the visual appeal and functional performance of parts. In critical applications, such as medical devices or automotive components, this defect can lead to costly recalls or safety hazards.
Short shots can be prevented by simply increasing injection pressure.False
While higher pressure may help, it doesn’t address other root causes like temperature or mold design, which also require attention.
Short shots are more common in thin-walled parts.True
Thin-walled parts demand precise pressure and temperature control, increasing their susceptibility to short shots.
What Are the Common Causes of Short Shots?
Identifying the root causes of short shots is the first step toward effective resolution. Here are the primary contributors:
Common causes include low injection pressure, inadequate temperature, poor mold design, and material flow issues, each necessitating targeted adjustments.
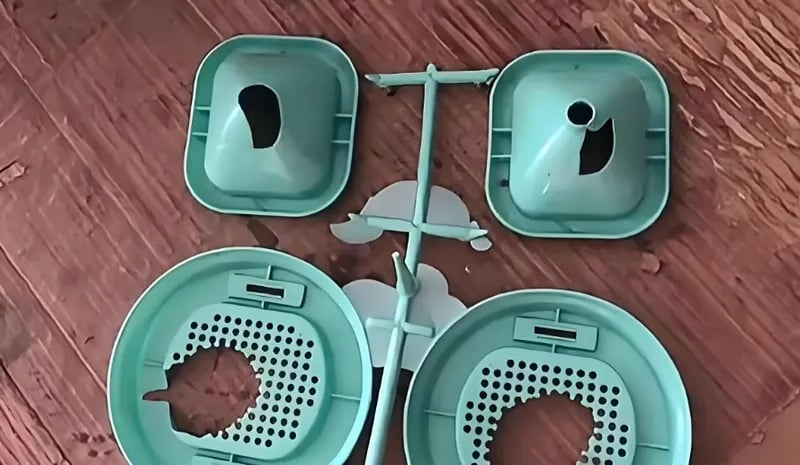
Injection Pressure and Speed
Low pressure or slow injection speed can prevent the plastic from fully penetrating the mold, particularly in complex or long-flow-path designs.
Temperature Control
Proper melt and mold temperatures are vital. If the melt is too cool, it may not flow adequately, and a cold mold can cause early solidification.
Mold Design
Design elements like insufficient venting, undersized gates, or suboptimal runner placement can restrict plastic flow, leading to incomplete filling. Effective venting is crucial to release trapped air.
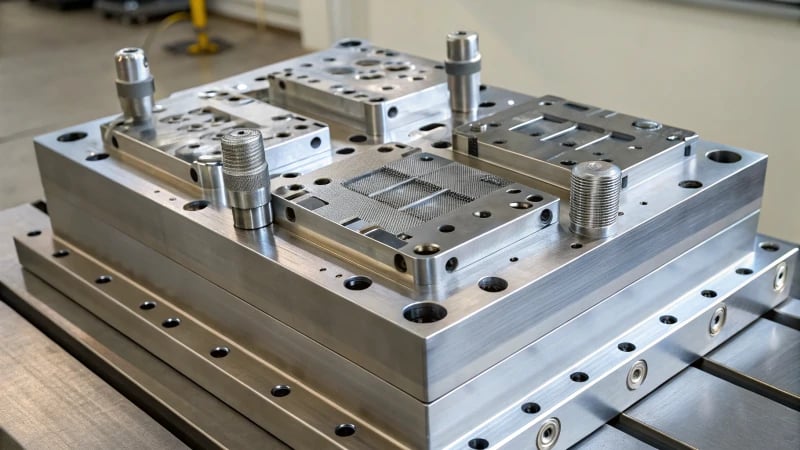
Material Properties
The melt flow index (MFI)5 of the plastic determines its flowability. Materials with low MFI (high viscosity) are more prone to short shots, especially in detailed or thin-walled parts.
Increasing injection speed always prevents short shots.False
Higher speed can help but may introduce defects like flash or burn marks if not balanced with pressure and temperature.
Proper mold venting is crucial to prevent short shots.True
Adequate venting allows air to escape, reducing flow resistance and ensuring complete mold filling.
How Can Short Shots Be Prevented?
Preventing short shots requires a proactive strategy that optimizes equipment, materials, and processes.
Prevention involves fine-tuning injection parameters, enhancing mold design, selecting suitable materials, and leveraging simulation tools.
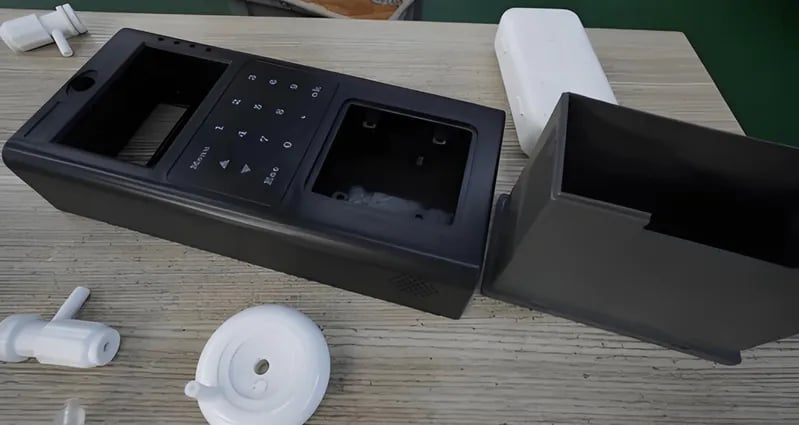
Optimizing Injection Parameters
-
Pressure: Adjust injection pressure to ensure full mold filling, tailoring it to the part’s complexity.
-
Speed: Balance injection speed to avoid premature solidification without causing overpacking.
-
Temperature: Maintain optimal melt and mold temperatures to keep the plastic fluid throughout the process.
Improving Mold Design
-
Venting: Add vent grooves (0.02-0.04 mm deep, 5-10 mm wide) to release trapped air (First Mold).
-
Gates and Runners: Optimize gate size and placement for even material distribution, using multiple gates for intricate parts.
Material Selection
Choose plastics with appropriate flow properties (higher MFI) for complex or thin-walled designs to facilitate complete filling.
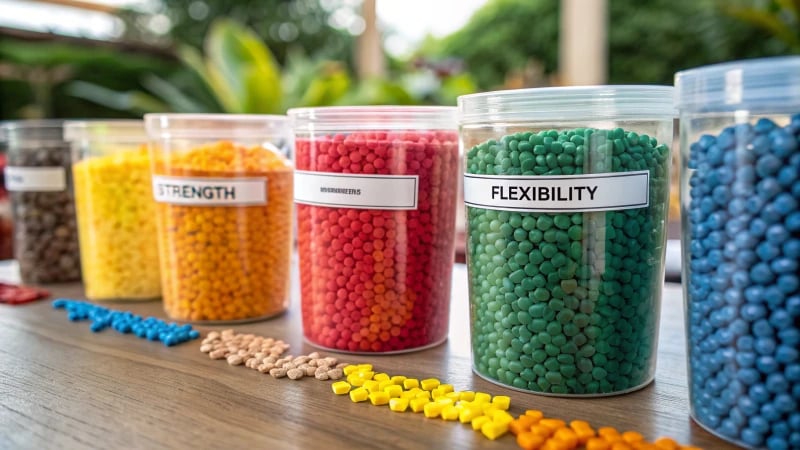
Simulation Tools
Employ mold flow simulation software6 to predict and mitigate short shot risks by refining process parameters before production starts.
Simulation tools can completely eliminate short shots.False
While highly useful, simulations can’t account for all real-world variables like machine wear or material variations.
Proper material selection is key to preventing short shots.True
Materials with suitable flow properties reduce the risk of incomplete filling, especially in demanding designs.
How to Troubleshoot Short Shots?
When short shots occur, a structured troubleshooting process can quickly pinpoint and resolve the issue.
Troubleshooting entails verifying injection settings, temperature, mold design, and material compatibility.
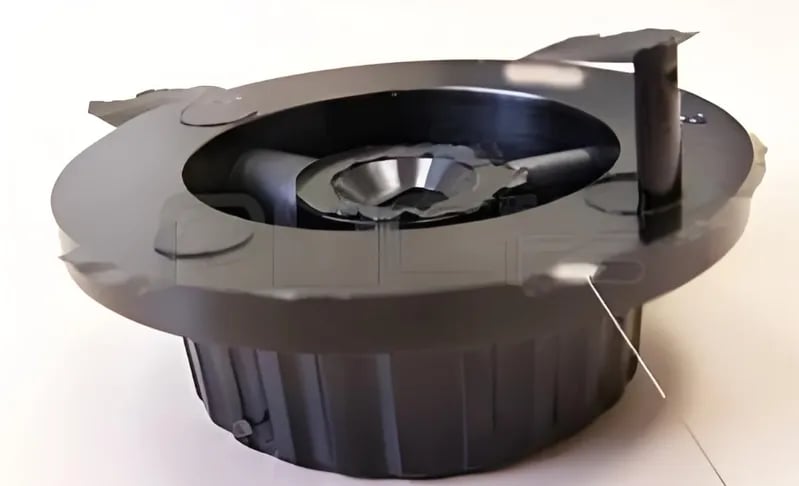
Step-by-Step Troubleshooting Guide
-
Check Pressure and Speed: Confirm settings are adequate; increase pressure or adjust speed as needed.
-
Inspect Temperatures: Ensure melt and mold temperatures align with material specifications; adjust if off-range.
-
Examine Mold Design: Look for venting issues (e.g., burn marks) or gate/runner inadequacies; modify if necessary.
-
Verify Material Supply: Check for sufficient material and clear any feed system blockages.
-
Assess Material: Ensure the plastic’s flow properties match the part requirements; switch materials if needed.
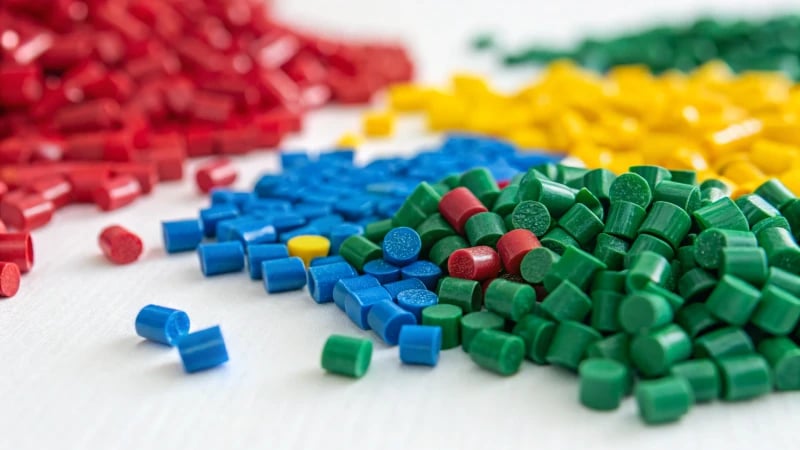
Advanced Techniques
-
Pressure Transducers: Monitor cavity pressure to locate filling deficiencies.
-
Thermal Imaging: Detect temperature inconsistencies in the mold that may cause premature cooling.
Troubleshooting short shots always requires changing the mold design.False
Many cases can be resolved by adjusting settings or materials without altering the mold.
Pressure transducers can help identify the exact location of short shots.True
Transducers reveal pressure drops, pinpointing where filling fails for precise fixes.
What Are the Differences Between Short Shots and Other Injection Molding Defects?
Distinguishing short shots from other defects aids in accurate diagnosis and correction.
Short shots result from incomplete filling, unlike flash (overfilling) or sink marks (cooling issues).
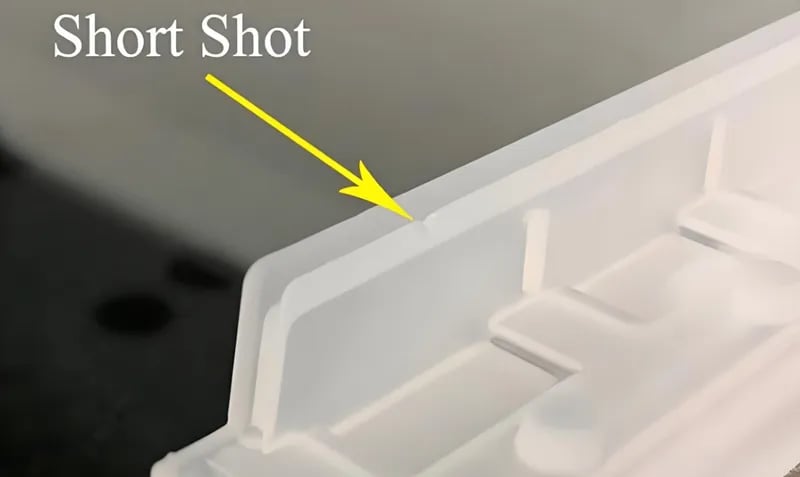
Short Shots vs. Flash
-
Short Shots: Incomplete mold filling, missing sections.
-
Flash: Excess material escapes the mold, forming thin protrusions.
Short Shots vs. Sink Marks
- Short Shots: Missing material due to poor filling.
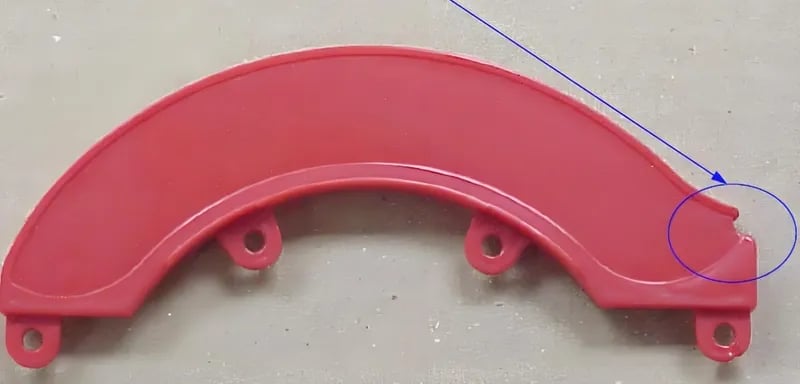
- Sink Marks: Surface depressions from uneven cooling or packing.
Short Shots vs. Warping
-
Short Shots: Incomplete parts from filling issues.
-
Warping: Shape distortion due to cooling stresses.
Short shots and flash can occur simultaneously in the same part.False
Short shots indicate underfilling, while flash indicates overfilling, making them generally incompatible.
Sink marks can sometimes be mistaken for short shots.True
Both may appear as imperfections, but sink marks are depressions, while short shots are absences.
Conclusion
Short shots in injection molding pose a significant challenge, affecting part quality and production efficiency. By addressing causes like low pressure, temperature inconsistencies7, and mold design] flaws, manufacturers can implement robust prevention and troubleshooting strategies. Optimizing settings, enhancing molds, selecting appropriate materials, and using simulation tools are essential steps toward eliminating this defect.
-
Learn about best practices in injection molding to enhance product quality and reduce defects. This resource is invaluable for manufacturers. ↩
-
Understanding short shots is crucial for improving manufacturing quality and efficiency. Explore this link for in-depth insights. ↩
-
Discover how effective mold design can prevent defects like short shots and improve overall production quality. A must-read for engineers. ↩
-
Exploring the injection molding process helps in identifying defects and enhancing production efficiency. ↩
-
The MFI is key to selecting materials for injection molding. Learn how it impacts flowability and part quality by checking this resource. ↩
-
Mold flow simulation software can significantly enhance production efficiency and reduce defects. Discover its advantages through this link. ↩
-
Temperature control is key to successful injection molding. Learn how to manage temperature for optimal results. ↩