Let’s take a deep dive into how injection molding is transforming the toy industry!
Injection molding technology allows for efficient mass production, complex shape formation, and diverse material applications, making it essential in the toy industry for creating intricate and high-quality designs.
While this technology enables fast and precise production, its unique capabilities extend far beyond basic manufacturing. From innovative design possibilities to personalized customization, the following sections delve into how injection molding is reshaping toy production. Stay with us as we explore these fascinating applications.
Injection molding enables rapid toy mass production.True
Injection molding machines produce toys quickly, meeting high market demands.
How Does Injection Molding Enable Innovative Toy Designs?
Injection molding technology has revolutionized toy design by enabling complex structures and allowing for rapid, high-quality production of innovative toys.
Injection molding enables innovative toy designs through precise molding of complex shapes, integration of multiple components, and use of diverse materials, facilitating creativity and efficiency in toy production.
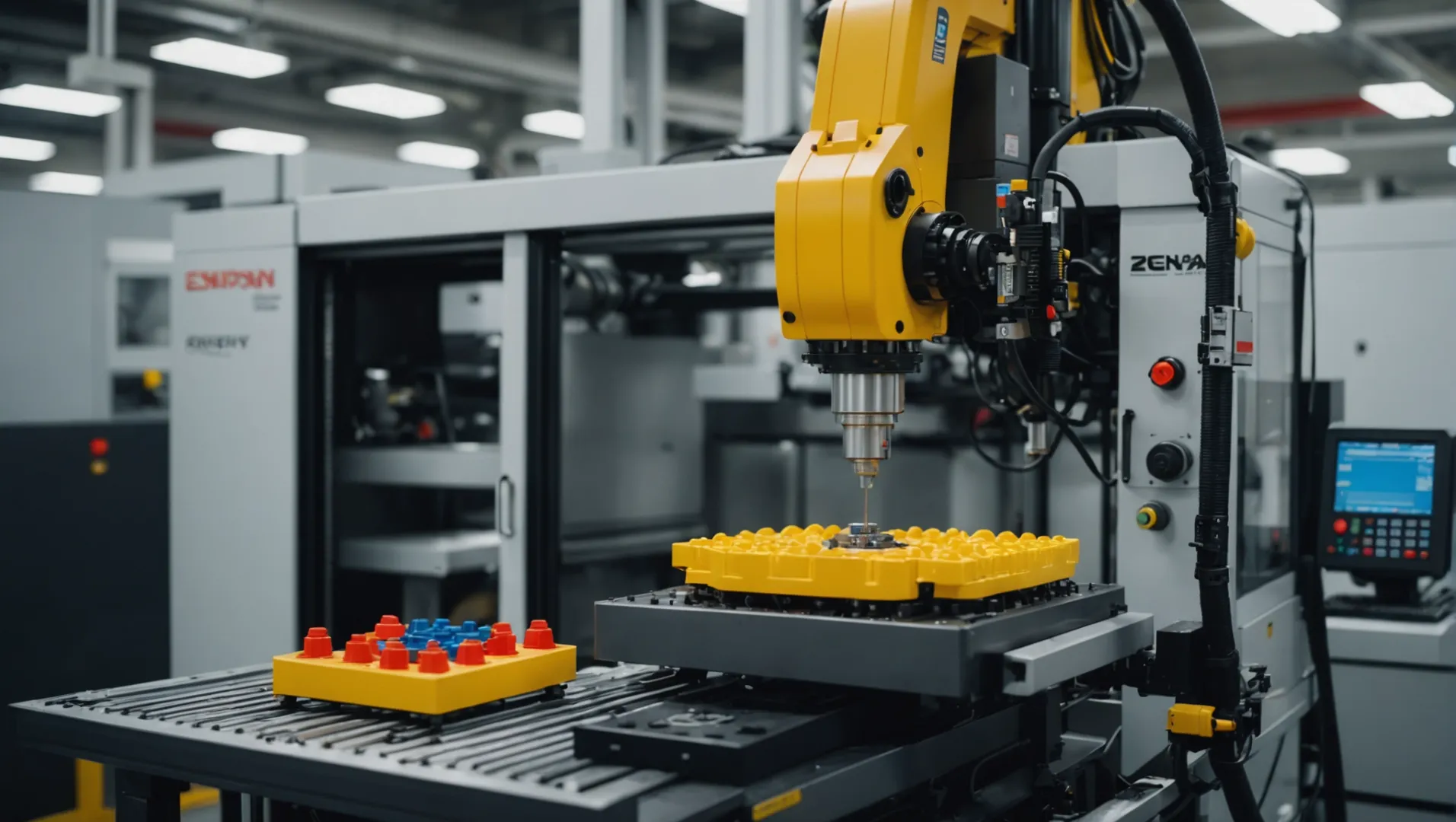
Efficient Mass Production for Creative Designs
Injection molding technology stands out in the toy industry for its ability to produce toys at remarkable speeds. This efficiency is crucial during peak demand periods, such as holidays, where the market demands rapid production. For instance, building blocks and doll accessories can be molded within minutes, ensuring that manufacturers meet market demands quickly.
Moreover, the high degree of automation in modern injection molding machines reduces manual intervention, enhancing both production efficiency and product quality. Automated systems manage tasks like feeding, molding, and demolding, which not only improves productivity but also ensures consistency in the quality of toys produced.
Complex Shape Molding and Design Innovation
One of the most significant advantages of injection molding is its capability to create complex and precise shapes. This precision is vital for toy models like cars or airplanes, where intricate details matter. The technology allows for the accurate control of plastic flow and filling, resulting in toy parts that meet high dimensional accuracy and design requirements.
Additionally, injection molding facilitates multi-component integrated molding. Special mold designs enable multiple parts to be molded simultaneously, reducing assembly time and increasing the reliability of toys with movable parts, such as rotatable joints and foldable structures. This capability streamlines production processes and enhances the durability of toys.
Material Versatility in Toy Design
The versatility of materials available for injection molding is another factor that enables innovation. Toy manufacturers can select from a wide range of plastics like polyethylene (PE), polypropylene (PP), and polycarbonate (PC), each offering different physical and chemical properties to meet specific design needs. For example, thermoplastic elastomers (TPE) can be used to create toys with a soft feel, while polymethyl methacrylate (PMMA) offers high transparency for toys requiring clear components.
Special additives can also be incorporated to give toys unique properties such as color vibrancy, antibacterial qualities, or antistatic features. This diversity in material selection allows toy designers to experiment with new ideas and create products that stand out in the market.
Personalized Customization and Small Batch Production
The ability to quickly replace molds makes injection molding ideal for personalized toy production. Companies can swiftly respond to customer demands by designing custom molds based on client specifications. This flexibility supports small-batch production, aligning with current consumer trends towards personalized products.
By optimizing injection processes and mold designs, manufacturers can keep costs low while meeting the demand for diverse, customized toy designs. This capability encourages experimentation with novel designs without incurring prohibitive costs.
Realizing Innovative Design Concepts
Injection molding facilitates special structural designs such as hollow, thin-walled, or multi-layer structures. This flexibility opens up new possibilities for toy innovation. For example, hollow plastic toys like inflatable rings can be made lighter and cheaper using injection molding techniques.
Furthermore, combining injection molding with other processes like printing or electroplating can enhance the appearance and functionality of toys. Printing adds decorative patterns, spraying increases glossiness, and electroplating provides a metallic finish. These processes allow for an array of aesthetically pleasing and functional toy designs that captivate consumers.
In summary, injection molding is not just about mass production; it’s a catalyst for innovation in toy design. By leveraging its capabilities, manufacturers can push the boundaries of creativity while maintaining efficiency and cost-effectiveness in production.
Injection molding enables rapid toy production.True
Injection molding allows fast production, meeting high demand quickly.
Injection molding restricts toy design creativity.False
It enhances creativity by enabling complex shapes and material versatility.
What Role Does Material Selection Play in Toy Injection Molding?
Choosing the right material is crucial in toy injection molding, influencing quality, safety, and functionality.
Material selection in toy injection molding determines the durability, safety, and aesthetic appeal of toys, playing a pivotal role in meeting industry standards and consumer expectations.

The Importance of Material Selection in Toy Production
Selecting the right material for toy injection molding is more than just a technical decision; it’s integral to achieving the desired characteristics of the final product. Materials like polyethylene (PE) and polypropylene (PP) offer excellent strength and flexibility, which are ideal for robust toys that need to endure rough play.
For toys requiring transparency or vivid colors, materials such as polycarbonate (PC) or polystyrene (PS) are preferred. These materials allow for the incorporation of pigments and additives that enhance visual appeal without compromising safety.
Safety Considerations
Safety is paramount when selecting materials for toy production. Non-toxic, BPA-free plastics are critical to ensuring that toys are safe for children. Additionally, materials should comply with safety regulations like ASTM F963 and EN71, which specify requirements for toy safety.
A practical example is the use of thermoplastic elastomer (TPE), known for its soft texture and flexibility, making it suitable for teething toys. This material not only meets safety standards but also offers a pleasant tactile experience.
Enhancing Durability and Functionality
Material selection directly affects a toy’s durability and functionality. For instance, using polycarbonate (PC) in building blocks ensures high impact resistance and long-term durability. Meanwhile, multi-component integrated molding1 allows for complex functional parts like moving joints to be produced efficiently.
Additionally, adding specific additives can impart special properties such as UV resistance or antibacterial features. This not only prolongs the lifespan of toys but also enhances their usability in diverse environments.
Aesthetic Versatility
The choice of material also plays a significant role in the aesthetic versatility of toys. For instance, polymethyl methacrylate (PMMA) can be used to achieve high transparency for clear parts or window sections in toys like cars or planes.
Moreover, special additives can create unique textures or finishes, such as matte or glossy surfaces, broadening design possibilities and consumer appeal.
By understanding the diverse applications and benefits of different materials in toy injection molding, manufacturers can create products that not only meet but exceed market expectations. This strategic selection process ensures toys are safe, durable, and visually appealing, thus enhancing their market competitiveness.
Polyethylene is used for transparent toys.False
Polyethylene is not typically used for transparency; polycarbonate is preferred.
Polycarbonate offers high impact resistance.True
Polycarbonate is known for its excellent impact resistance, ideal for durable toys.
How Can Injection Molding Support Sustainable Toy Production?
As environmental concerns rise, sustainable practices in toy manufacturing are gaining momentum. Injection molding plays a pivotal role in this shift.
Injection molding supports sustainable toy production by minimizing waste, optimizing material usage, and facilitating the use of recycled plastics, which reduces the environmental footprint of toy manufacturing.
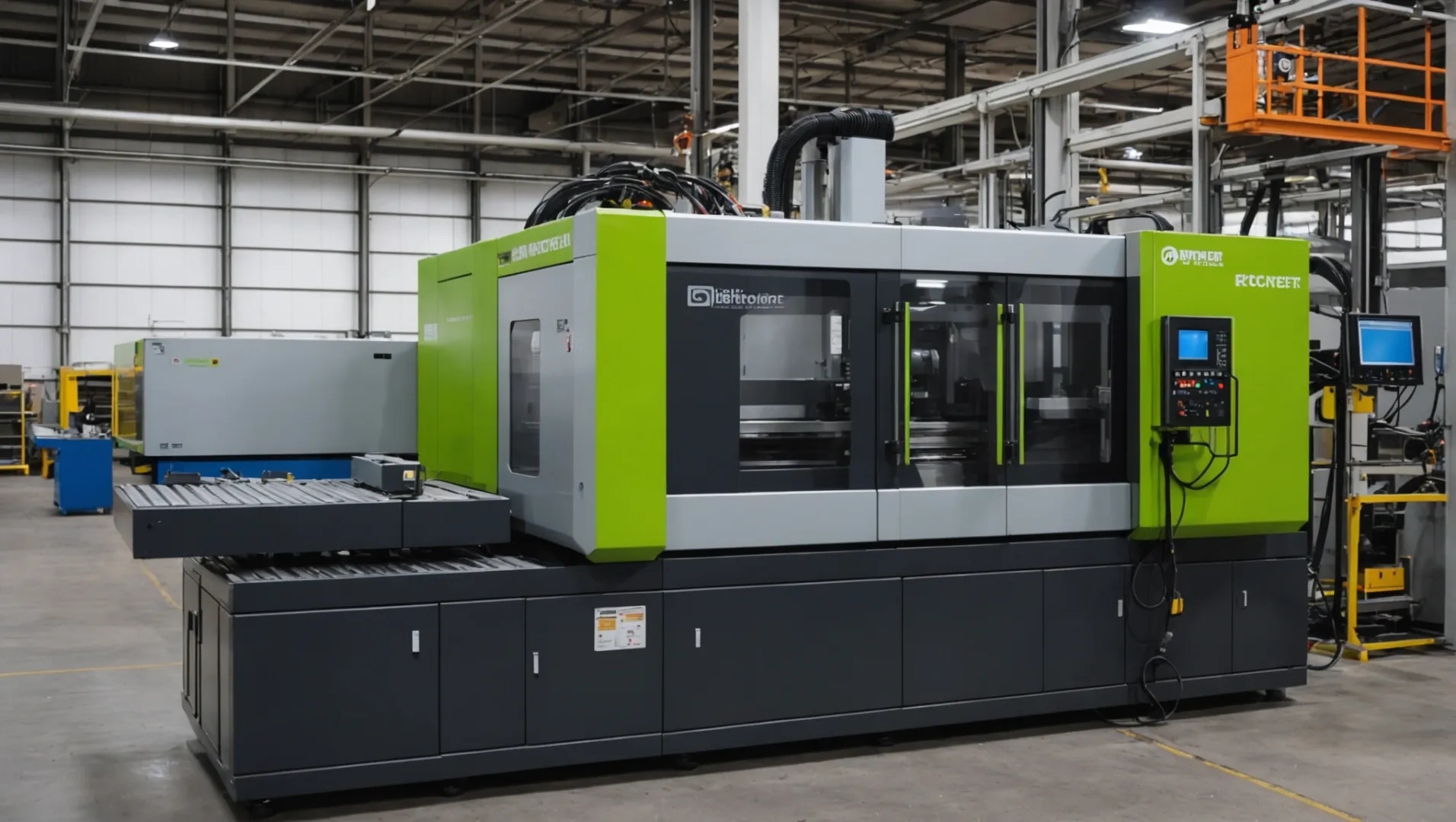
Reducing Material Waste
One of the key advantages of injection molding2 in sustainable toy production is its efficiency in material usage. The precision of this technology ensures that each mold is filled with the exact amount of plastic needed, significantly reducing excess and minimizing waste. This precision helps manufacturers avoid overproduction and the subsequent disposal of unused materials.
Moreover, any plastic waste generated during the process can often be recycled and reintroduced into the production cycle, further diminishing the need for virgin materials. This recycling capability not only conserves resources but also aligns with environmental policies aiming to reduce plastic waste.
Utilizing Recycled Materials
Injection molding is well-suited for using recycled plastics, a practice that is becoming increasingly prevalent in the toy industry. By incorporating post-consumer plastics, manufacturers can reduce reliance on new plastic production, thereby cutting down on energy consumption and greenhouse gas emissions associated with producing new materials.
The use of recycled materials does not compromise the quality of toys. Advances in recycling processes have ensured that recycled plastics meet the same safety and durability standards as new materials. For example, toys made from recycled polyethylene (rPE) or recycled polypropylene (rPP) can maintain their structural integrity and aesthetic appeal.
Energy Efficiency in Production
Modern injection molding machines are designed to be energy-efficient. They consume less power compared to older models, thanks to advances in machine design and technology. Features such as servo-driven hydraulic systems and improved insulation reduce energy requirements, making production more environmentally friendly.
Additionally, the high degree of automation in injection molding minimizes the need for human intervention, which can lead to further energy savings. Automated processes ensure that machines run optimally without unnecessary idling or power wastage.
Biodegradable Plastics and Additives
Another promising avenue for sustainable toy production is the use of biodegradable plastics and eco-friendly additives in injection molding. These materials break down more easily in natural environments compared to traditional plastics, offering an eco-friendly alternative for toy manufacturing.
Manufacturers are experimenting with bioplastics derived from renewable resources like corn starch or sugarcane, which can be used in injection molding. These materials not only reduce dependency on fossil fuels but also contribute to lowering the carbon footprint of toys. Furthermore, additives that enhance biodegradability can be incorporated into the molding process without compromising product quality.
Supporting a Circular Economy
Injection molding facilitates a circular economy model in toy production by enabling product designs that are easier to disassemble and recycle at the end of their life cycle. By focusing on design for disassembly, manufacturers can ensure that toy components are easily separated and recycled, rather than being discarded as waste.
This approach not only supports sustainability but also aligns with consumer demands for more environmentally responsible products. As awareness grows about environmental impacts, consumers are increasingly favoring brands that prioritize sustainable practices.
In conclusion, injection molding technology3 has the potential to significantly enhance sustainability in toy production by minimizing waste, embracing recycled and biodegradable materials, and improving energy efficiency. These initiatives are vital steps towards a more sustainable future for the toy industry.
Injection molding reduces toy production waste.True
Precision mold filling minimizes excess material, reducing waste.
Recycled plastics compromise toy quality in molding.False
Recycled plastics meet safety and durability standards in toys.
What Are the Cost Benefits of Using Injection Molding in Toy Manufacturing?
Injection molding offers significant cost savings in toy manufacturing through efficient mass production and reduced labor costs.
Injection molding provides cost benefits by enabling rapid production cycles, reducing material wastage, and minimizing labor expenses, making it a financially viable option for toy manufacturers.
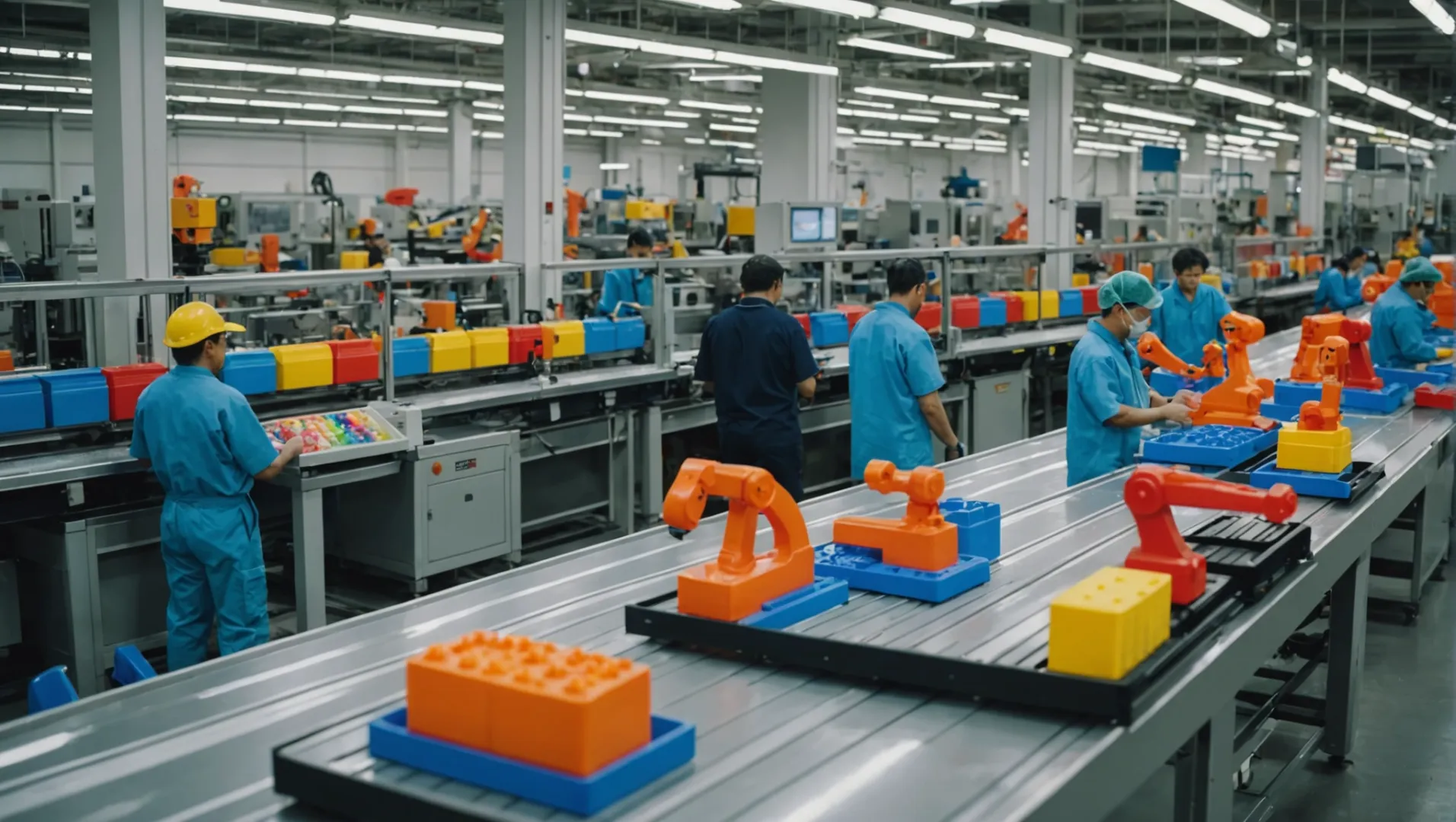
Efficient Mass Production
Injection molding stands out for its ability to produce large volumes of toys quickly and efficiently. This speed is crucial during peak sales seasons, where demand can skyrocket. For instance, injection molding machines can churn out simple toys like building blocks or doll accessories in just a few minutes. This rapid production rate not only meets market demands but also lowers per-unit production costs, which is critical for maintaining competitive pricing.
Automation and Labor Cost Reduction
Modern injection molding machines are equipped with automated systems that handle everything from feeding to demolding. This high degree of automation reduces the need for manual labor, thereby cutting down on labor costs significantly. For large-scale toy producers, this automation translates to substantial savings in operational expenses and boosts overall productivity.
Material Efficiency
Injection molding is also cost-effective due to its efficient use of materials. The precision of the process minimizes waste, ensuring that almost every bit of raw material contributes to the final product. This is particularly beneficial when working with expensive materials, as it maximizes the return on investment for each batch produced. In addition, injection molding allows for diversified material application4, which means manufacturers can choose cost-effective materials without compromising on quality.
Reduced Assembly Costs
One of the standout advantages of injection molding is its ability to create complex parts in a single cycle. This feature reduces or eliminates the need for additional assembly processes, which can be both time-consuming and costly. For example, toys with intricate designs or movable parts can be produced as integrated pieces, enhancing durability and reliability while lowering assembly labor costs.
Flexible and Scalable Production
The flexibility of injection molding also supports cost-effective scalability. Manufacturers can swiftly switch molds to produce different toy designs without significant downtime, enabling them to respond to market trends and customer preferences efficiently. This adaptability ensures that companies can offer a wide variety of products without incurring hefty retooling expenses.
In conclusion, injection molding offers numerous cost benefits in toy manufacturing by streamlining production processes, reducing waste, and minimizing labor expenses. These advantages make it an attractive choice for companies looking to maximize efficiency and profitability.
Injection molding reduces labor costs in toy manufacturing.True
Automation in injection molding cuts down on manual labor needs.
Injection molding increases material wastage in toy production.False
The precision of injection molding minimizes material waste.
Conclusion
Injection molding technology empowers the toy industry with efficient production, innovative design, and material versatility. Embrace these insights to leverage injection molding in creative toy development.
-
Discover how multi-component molding enhances toy design efficiency.: The process involves adding another set of plastic pellets to add another color that would be integrated into the same plastic mold. Some of these multi-color … ↩
-
Explore how precise mold filling minimizes material waste.: In this article, we will explore effective strategies to help you reduce all types of waste in your injection molding business and achieve long-term success. ↩
-
Learn about its impact on eco-friendly production practices.: Plastic molding offers techniques to produce high-quality products while being environmentally conscious. The closed industrial loop is highly efficient. ↩
-
Learn how diverse materials enhance cost-efficiency in injection molding.: Diversified Plastics offers several different injection molding processes for molding engineered industrial resins into virtually any shape. ↩