Do you often struggle with headaches from uneven wall thickness in injection molding? I definitely have faced this issue before. It really feels overwhelming sometimes.
Uneven wall thickness in injection molding leads to challenges like uneven melt flow, fusion marks, and warping, affecting product quality and performance. Understanding these effects is crucial for enhancing design and manufacturing processes.
I want to tell you about my journey in the complex world of design and manufacturing. Many people do not realize how important wall thickness is for projects. I did not expect how much wall thickness would affect my work. At first, I felt confused when I saw problems with melt flow and strange marks appearing without warning. Every mistake taught me something important. I also want to support you in dealing with these issues. We should explore the details of uneven wall thickness. We will find simple solutions to really improve your injection molding techniques.
Uneven wall thickness causes imbalanced melt flow in molding.True
Imbalanced melt flow occurs due to uneven wall thickness, affecting the quality of molded products.
Warping deformation is not affected by wall thickness variations.False
Warping deformation is indeed influenced by uneven wall thickness during the injection molding process.
- 1. What are the common defects caused by uneven wall thickness?
- 2. How can design choices mitigate the effects of uneven wall thickness?
- 3. What best practices should I implement during the injection molding process?
- 4. How does material selection influence the outcomes of varying wall thickness?
- 5. Conclusion
What are the common defects caused by uneven wall thickness?
Have you ever faced problems with uneven wall thickness in your projects? I have struggled with this too. Understanding defects from uneven walls is very important. Quality of products in manufacturing processes really depends on this, especially in injection molding.
Uneven wall thickness can lead to unbalanced melt flow, fusion marks, warped shapes, and internal stress, all affecting product quality and functionality. Understanding these defects aids in developing durable designs and processes.
Effects of the Filling Phase
During the filling phase of injection molding, uneven wall thickness causes trouble. One major issue is unbalanced melt flow. For example, in a product with 2mm thin walls and 6mm thick walls, the melt flows into thicker areas first. These thicker areas give less resistance. In one project, the thin sections were underfilled. Short shots weaken the whole product. Very often.
Another problem comes as fusion marks. These marks form when melt from different thicknesses meet at different times. This leads to poor connection. When injecting a shell product, these marks appear at the junctions between thin and thick areas. They ruin the look and strength of your product.
Also, you face complex injection adjustments to fix this. Methods like segmental or variable speed injection help. I spent countless hours mastering these techniques for different thicknesses. It’s a very delicate process!
Effects of Cooling Stages
Cooling stages suffer greatly from uneven thickness. The main defect is uneven cooling and warping. Thick parts cool slowly, while thin parts cool fast. This difference causes warping. I once molded a flat plate with a thick center. During cooling, it twisted towards the thicker area. Not ideal for precision.
Also, internal stress concentration is a big issue. Stress often builds up at the junction of thick and thin sections. For instance, a product with a thick base and thin handle may crack at the joint. This happens when it’s removed from the mold. Seeing your work break apart is really heartbreaking.
Effects of Holding Pressure Stage
In the holding pressure stage, uneven wall thickness causes chaos. Uneven holding pressure and shrink marks are common problems. Thick sections need more melt for shrinkage, while thin sections risk overpressure. Once, we molded a plastic container. The bottom developed ugly shrink marks due to under-pressure. At the same time, edges on the thin sides lifted due to overpressure.
Controlling holding pressure becomes very tough. Adjusting pressure and timing for different thicknesses is like juggling torches. I have conducted many mold trials to improve these settings. This helps reduce defects like shrink marks and flying edges.
Summary Table of Common Defects Due to Uneven Wall Thickness
Uneven Holding Pressure | Uneven Wall Thickness |
---|---|
Thick areas require more melt; thin areas risk overpressure, causing defects. | Shrink marks on thick bottoms; flying edges on thin walls. |
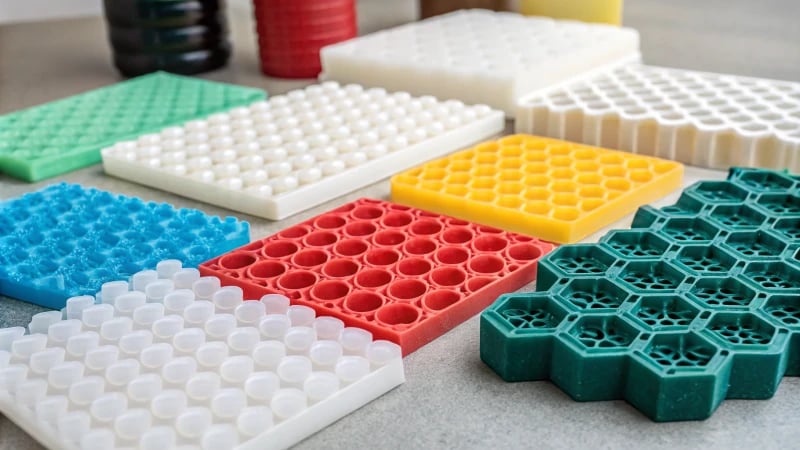
Effects of the Filling Phase
Different wall thickness during production leads to many puzzling issues. I recall a project where we had uneven melt flow and fusion marks. Many frustrating problems surfaced. These defects affect how the product looks. They also impact how it functions. Common defects result from such issues. They may impact your designs significantly.
One of the most significant issues is imbalanced melt flow. When the melt flows into a cavity with varying thickness, it tends to fill the thicker areas first due to reduced flow resistance. For instance, consider a product with thin-walled sections of 2mm and thick-walled areas of 6mm; the melt will rush into the thicker sections, potentially leaving thin-walled areas underfilled or even resulting in short shots. This scenario can compromise the integrity of the entire product.
Another concern is the generation of fusion marks. These marks occur when the melt converges from different wall thickness areas that have been filled asynchronously. Differences in temperature, pressure, and flow rates can cause incomplete integration at junctions, leading to unsightly marks that affect both appearance and strength. For example, in a shell product, if the melt flows around a thin reinforcement and thick body portion, fusion marks may appear at their junction.
Moreover, complicated injection parameter adjustments are often necessary to ensure uniform filling. Techniques such as segmental injection or variable speed injection may be required to manage the differences in thickness effectively. This increases the complexity of the injection molding process significantly.
Effects of Cooling Stages
Cooling is another critical phase affected by uneven wall thickness. The primary defect associated with this stage is uneven cooling and warping deformation. Thick-walled areas cool more slowly than thin-walled ones, leading to warping as different sections shrink at different rates.
Consider an injection-molded flat plate with a thick center and thin edges; it may warp towards the thicker area during cooling, compromising its dimensional accuracy and aesthetic appeal.
Furthermore, internal stress concentration is a notable concern. When cooling occurs unevenly, stress can build up at transitions between thick and thin sections. For example, a product featuring a thick base and a thin handle may experience cracks at the joint due to these concentrated stresses upon demolding.
Effects of Holding Pressure Stage
The holding pressure stage can also present challenges due to uneven wall thickness. Problems of uneven holding pressure and shrink marks are common defects that arise from this scenario. Thick-walled areas need additional melt to compensate for shrinkage, while thin-walled sections might suffer from over-pressurization.
For example, in a plastic container with varying thicknesses, under-pressurization could lead to shrink marks on the thick bottom while over-pressurization might cause flying edges on thin sidewalls. This variability significantly affects product quality.
Moreover, achieving a controlled holding pressure effect becomes challenging due to complexities introduced by uneven wall thickness. Accurately adjusting holding pressure and time for different wall thickness areas requires meticulous optimization; for intricate designs, mold trials may be necessary to refine these parameters to minimize defects like shrink marks and flying edges.
Summary Table of Common Defects Due to Uneven Wall Thickness
Defect Type | Description | Example |
---|---|---|
Imbalanced Melt Flow | Thicker areas fill first leaving thin areas underfilled | Short shots in thin-walled sections |
Fusion Marks | Marks formed at junctions due to asynchronous filling and differences in flow rates | Marks on shell product junctions |
Warping Deformation | Differential cooling causes warping as different areas shrink at different rates | Flat plate warping towards thick area |
Internal Stress Concentration | Stress builds up at transitions between thick and thin walls leading to cracks upon demolding | Cracking at base-handle joint |
Uneven Holding Pressure | Thick areas need more melt; thin areas may become over-pressurized leading to defects | Shrink marks on thick bottoms; flying edges on thin walls. |
Uneven wall thickness causes imbalanced melt flow in molding.True
Imbalanced melt flow occurs when thicker areas fill first, leaving thin sections underfilled, compromising product integrity during the injection molding process.
Fusion marks are unrelated to uneven wall thickness in products.False
Fusion marks result from asynchronous filling due to varying wall thickness, affecting appearance and strength of molded products.
How can design choices mitigate the effects of uneven wall thickness?
Have you ever dealt with the annoying problem of uneven wall thickness in your designs? I have definitely been there! We should explore ways to transform those design troubles into successes. Strategic choices help improve product quality and reduce flaws.
Designers can mitigate uneven wall thickness by optimizing wall distribution, strategically placing gates to control melt flow, using simulations, adjusting cooling strategies for even heat distribution, and modifying holding pressures according to section thicknesses.
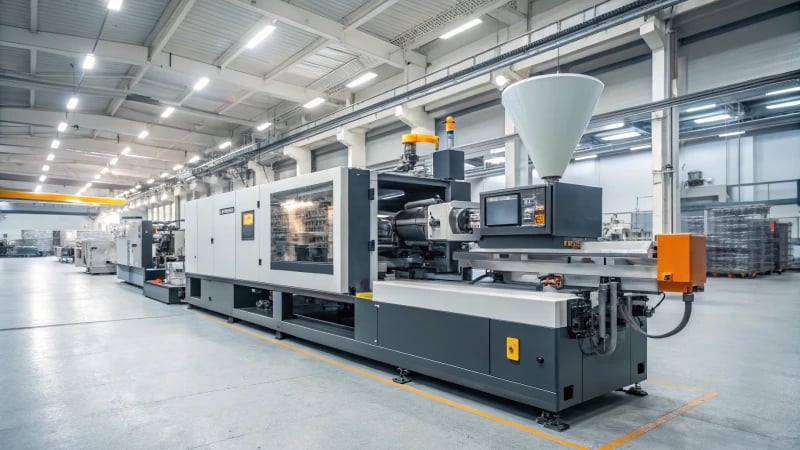
Understanding Design Choice Effects
When I began in product design, I faced a tough problem with uneven wall thickness in injection molding. This challenge changed everything for me. I saw how important design choices are to solve these issues. Experience taught me that careful planning really improves product quality and performance. Over the years, I have adopted some useful strategies:
Optimize Wall Thickness Distribution
A very effective method in my design work has been adjusting wall thickness distribution. It’s amazing how little adjustments lead to big improvements. For instance, I used gradual shifts between thick and thin parts to lower stress spots. This simple change not only strengthened my designs but also helped avoid expensive mistakes.
I remember a tough project where I used ribbing. It was a big revelation for me. The ribbing gave the strength needed and saved material. When dealing with similar tasks, think about using a design tool1 for simulating different wall thicknesses. It really reveals new ideas!
Control Melt Flow Behavior
Controlling melt flow during filling was also an important lesson for me. I dealt with uneven melt flow. Thicker parts filled faster, leaving thin parts empty. Seeing fusion marks from uneven flow taught me a memorable lesson.
To solve this, I put gates wisely for balanced filling in complex shapes:
Table 1: Flow Control Techniques
Technique | Description |
---|---|
Gate Placement | Position gates to promote even melt distribution. |
Simulation Software | Utilize CAD tools for predicting melt behavior. |
Adjusting Injection Speed | Vary speed based on wall thickness during filling. |
Flow simulation software also provided great help; it shows how melt acts based on wall thickness changes.
Adjust Cooling Strategies
Cooling speed directly affects product quality. Uneven cooling causes warping. I designed cooling channels that spread heat evenly over different wall thicknesses:
- Design cooling channels to ensure uniform heat dissipation across different wall thicknesses.
- Implement cooling time adjustments based on the geometry of the part, allowing thicker areas to cool more effectively without warping.
This step not only stopped warping but also kept dimensions accurate.
For advanced cooling ideas, explore cooling strategies2.
Fine-Tune Holding Pressure Settings
Managing holding pressure with uneven wall thickness was tricky. Early on, I struggled with shrink marks on thick parts and flying edges on thin ones from wrong pressure settings.
I started using different holding pressures for each section’s thickness:
- Thick parts needed more pressure for shrinkage.
- Thin sections needed careful watching to prevent too much pressure.
Mold trials were crucial in my work to find the best holding pressures and times for designs:
Table 2: Holding Pressure Recommendations
Section Type | Recommended Holding Pressure |
---|---|
Thick-Walled Areas | Higher holding pressure |
Thin-Walled Areas | Lower holding pressure |
Conclusion Note
Reflecting on my journey, I see how vital these design choices have been to lessen uneven wall thickness effects. By focusing on wall thickness distribution, controlling melt flow, adjusting cooling plans and fine-tuning holding pressure, I improved product quality and reduced flaws. If you’re eager to learn more about injection molding design, check out best practices3. Together, we can face these challenges and improve our designs!
Optimizing wall thickness distribution improves product strength.True
By using gradual transitions and ribbing, designers can enhance structural integrity while minimizing stress concentrations in uneven wall thickness designs.
Strategic gate placement ensures balanced melt flow during molding.True
Proper gate positioning is crucial for achieving even melt distribution, which is vital for managing uneven wall thickness in injection molding processes.
What best practices should I implement during the injection molding process?
I explore the world of injection molding and discover the importance of following best practices. This is really crucial for achieving great results. What are the main strategies? How to succeed in this complex process?
Optimize injection molding by adjusting injection speeds for wall thickness, managing cooling rates to prevent warping, and tweaking holding pressure to ensure consistent product quality.
Understanding the Effects of the Filling Phase
The filling phase of injection molding is where everything starts. This is when hot plastic fills the mold. Getting this right is really important.
-
Imbalanced Melt Flow: I remember facing imbalanced melt flow for the first time. I worked on a part with both thin (2mm) and thick (6mm) sections. The melt filled the thicker areas too fast, leaving thin areas underfilled. The result? Defects that I fixed later. It was quite a lesson!
-
Generation of Fusion Marks: Fusion marks can also be tricky. When the melt comes together at different wall thickness points, it can cause visible defects. For example, if a thin reinforcement meets a thicker part, improper convergence may create marks that harm appearance and strength.
-
Complex Injection Parameter Adjustment: Handling uneven wall thickness needs careful changes in injection settings. In my experience, strategies like segmental injection or variable speed injection have been very useful. Starting fast for thick sections and slowing down for thin ones improves filling uniformity a lot.
Optimizing Cooling Stages
Cooling is another phase that really affects product quality.
-
Uneven Cooling and Warping Deformation: Have you ever faced warping because of uneven cooling? I have! Thick sections cool slowly, while thin ones cool fast. One time, I molded a flat plate with a thicker center and thinner edges. It warped as it cooled, affecting accuracy. I learned to watch cooling rates closely to prevent this.
-
Internal Stress Concentration: Another worry is internal stress concentration. Transitions between thick and thin parts can build stress and cause cracks. I once worked on a product with a thick base and a thin handle. The stress at their junction led to a failure. Being aware of these risks is vital!
Managing Holding Pressure Stage
The holding pressure stage is where I focus on keeping product integrity after filling.
-
Uneven Holding Pressure and Shrink Marks: Thick-walled areas need more material for shrinkage, while thin areas risk too much pressure. I’ve seen shrink marks on thick areas when under-pressurized and flying edges on thin walls due to over-pressure. It’s a delicate balance!
-
Control Challenges for Holding Pressure: Uneven wall thickness complicates holding pressure management. I often go through many trials to minimize shrink marks and flying edges. Fine-tuning the parameters is really key!
Summary Table of Best Practices in Injection Molding
Using these best practices during injection molding has helped me produce high-quality products. It has also improved my production efficiency. If you seek deeper insights into molding processes, explore further here.
And for a full guide on injection molding techniques, check out this resource.
With these experiences and insights, I’m excited to continue my journey in injection molding, sharing what I’ve learned along the way.
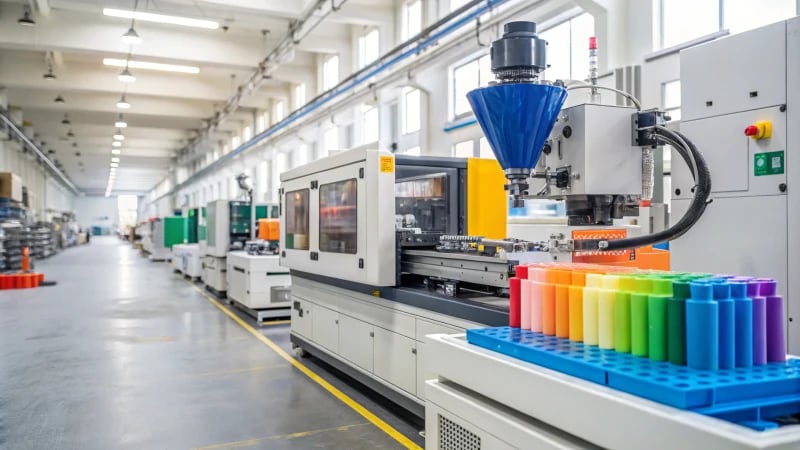
Best Practices in Injection Molding
Injection molding works best when following a few important practices. Adjusting injection speeds based on wall thickness is critical. Managing cooling rates effectively probably prevents warping. Fine-tuning holding pressure is important to maintain consistent quality. These practices are very helpful!
Summary Table of Best Practices in Injection Molding
Phase | Best Practice | Example |
---|---|---|
Filling Phase | Adjust injection speed based on wall thickness | Start fast for thick walls, slow for thin ones |
Cooling Stage | Monitor cooling rates to prevent warping | Ensure uniform cooling times across parts |
Holding Pressure | Fine-tune holding pressure based on thickness | Test adjustments through trial runs |
Implementing these best practices during the injection molding process not only ensures higher quality products but also optimizes production efficiency. For deeper insights into optimizing your molding processes, explore further here4.
For a comprehensive guide on injection molding techniques, visit this resource.
Adjusting injection speed prevents defects in thin sections.True
Properly adjusting injection speed based on wall thickness helps avoid underfilling and ensures uniform melt flow, reducing defects like short-shooting.
Uneven cooling does not affect product quality in injection molding.False
Uneven cooling can lead to warping and dimensional inaccuracies, negatively impacting the quality of the final product during injection molding.
How does material selection influence the outcomes of varying wall thickness?
Did you ever think about how the materials we pick affect the final design, particularly the wall thickness? I have thought about this too. It is a very interesting journey to explore together!
Material selection significantly influences wall thickness outcomes by affecting melting, cooling, and stress handling during production, reducing defects, and enhancing product performance.
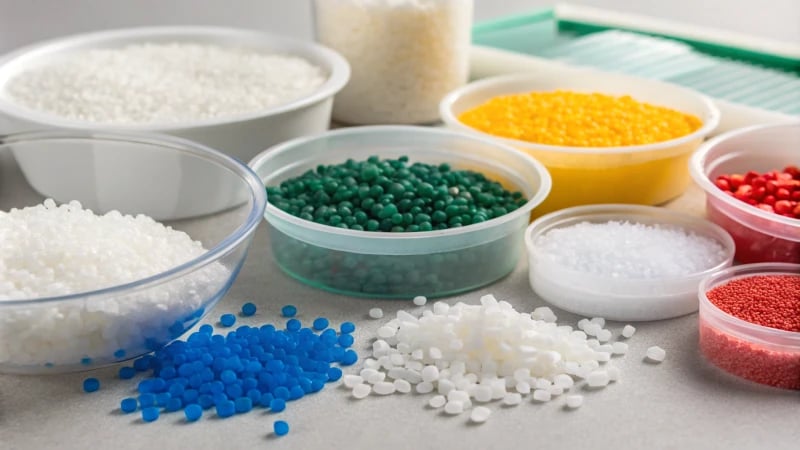
Understanding Material Selection
Choosing the right material is very important in product design, especially with different wall thicknesses. The chosen material can significantly impact the manufacturing process and the final product’s performance.
For instance, when selecting a material for injection molding, its viscosity and flow characteristics are crucial. A material that flows easily can fill thinner sections of a mold more effectively, preventing issues like underfilling or short-shooting. In contrast, a viscous material may struggle to fill thin-walled areas, leading to defects.
Effects of Filling Phase
- Imbalanced Melt Flow: An uneven wall thickness can cause an imbalanced melt flow. Thicker areas receive more melt due to reduced flow resistance. This is particularly evident in products with a mix of thin (2mm) and thick (6mm) walls, where thicker areas fill faster.
- Fusion Marks Formation: When melts converge from varying thicknesses, fusion marks can arise. The temperature and pressure differences can lead to incomplete integration at junctions, negatively affecting the product’s appearance and mechanical strength.
To mitigate these issues, consider materials with better flow properties or employ techniques like variable speed injection5 for more controlled filling across varying wall sections.
Effects of Cooling Stages
- Uneven Cooling: Materials also behave differently during cooling. For example, thicker walls cool slower than thinner ones, potentially causing warping. A plastic plate with a thick middle and thin edges may warp due to differing shrinkage rates.
- Internal Stress Concentration: Different cooling rates can create internal stresses that may lead to cracks post-demolding. For example, in a product with a thick base and thin handle, the stress at the joint might cause failures when subjected to external forces.
Utilizing materials with lower shrinkage rates can help mitigate such risks while ensuring dimensional accuracy.
Effects of Holding Pressure Stage
- Uneven Holding Pressure: The holding pressure process can become complicated with varying wall thicknesses. Thick sections need more melt to address shrinkage, while thinner sections risk over-pressurization.
- Control Challenges: Achieving uniform holding pressure is challenging. It requires precise adjustments according to wall thickness, often necessitating extensive testing. For instance, a plastic container with varying wall thickness may develop shrink marks if not monitored closely.
For best practices, always test different materials under varied holding pressures to identify optimal settings for your specific product design.
Conclusion
In the end, choosing materials affects how products perform with different thicknesses. Understanding how material properties work with design is vital for better performance and quality in projects. It’s an ongoing learning journey.
Material selection affects melt flow in injection molding processes.True
Choosing the right material is crucial for effective melt flow, impacting product quality during injection molding.
Thicker walls cool faster than thinner walls in manufacturing.False
In manufacturing, thicker walls typically cool slower than thinner ones, leading to potential warping and internal stress issues.
Conclusion
This article explores the impact of uneven wall thickness on injection molding, detailing challenges such as melt flow imbalance, cooling issues, and holding pressure complications.
-
Discover effective strategies and best practices to address challenges in product design with uneven wall thickness. ↩
-
Explore advanced techniques for cooling strategies that minimize defects related to uneven wall thickness. ↩
-
Learn about best practices for managing holding pressure in injection molded products with uneven wall thickness. ↩
-
Clicking this link provides access to detailed guidelines that can enhance your injection molding techniques and improve product quality. ↩
-
Explore advanced material selection techniques for achieving optimal results in varying wall thickness designs. ↩