Imagine standing before a machine that can create precision parts, yet knowing that a slight temperature variation could ruin everything. That’s the challenge in injection molding!
Uneven mold temperature affects injection molded parts by causing dimensional inaccuracies, inconsistent surface quality, and variable mechanical properties. Higher temperature areas allow for better material flow, while lower temperature areas may lead to shrinkage and defects, impacting overall product quality.
Understanding how uneven mold temperature affects your parts is just the beginning. Read on to explore how these issues manifest in your products and discover strategies to mitigate them for enhanced manufacturing efficiency and product quality.
Uneven mold temperature causes injection parts to warp.True
Uneven cooling rates from temperature variations lead to warping.
What Causes Uneven Mold Temperature in Injection Molding?
Uneven mold temperatures can significantly affect the quality of injection molded parts. But what causes these temperature disparities?
Uneven mold temperature in injection molding is primarily caused by inconsistent cooling channel design, irregular heat distribution, and equipment malfunctions. Addressing these issues requires meticulous mold design and regular equipment maintenance to ensure consistent quality in molded parts.

Inconsistent Cooling Channel Design
One of the primary culprits behind uneven mold temperature is poorly designed cooling channels. These channels are responsible for maintaining consistent temperatures across the mold surface. When channels are improperly placed or unevenly distributed, certain areas of the mold may cool faster or slower than others. This disparity can lead to inconsistent surface qualities, such as flow marks1, and impact the overall dimensional accuracy of parts.
The design of cooling channels should facilitate even cooling by ensuring uniform distribution across the mold’s critical areas. Computational fluid dynamics (CFD) simulations can help engineers assess and optimize these designs before they are implemented.
Irregular Heat Distribution
Apart from cooling channels, irregular heat distribution can also arise from variations in material properties or thicknesses within the mold. Areas with thicker sections may retain heat longer, leading to uneven cooling. This can result in warping deformations2 as different sections of a part shrink at varying rates.
Using uniform wall thickness throughout the design can mitigate these temperature variations. Additionally, employing materials with consistent thermal conductivities can further enhance even heat distribution.
Equipment Malfunctions
Equipment-related issues, such as malfunctioning heating elements or inadequate thermal insulation, can also contribute to uneven mold temperatures. Such problems may lead to hotspots or cold spots on the mold surface, affecting the mechanical properties of the final product.
Regular maintenance and inspection of molding machines are crucial to identify and rectify these issues promptly. Replacing worn-out components and ensuring proper insulation around heaters can prevent significant temperature disparities.
Environmental Factors
Finally, external environmental conditions, such as ambient temperature fluctuations or drafts in the production area, can influence mold temperatures. Ensuring that the injection molding environment is controlled and stable helps maintain consistent mold temperatures.
By understanding and addressing these factors, manufacturers can improve the reliability and quality of their injection molded parts.
Inconsistent cooling channels cause uneven mold temperature.True
Poorly designed channels lead to uneven cooling, affecting part quality.
Environmental factors have no effect on mold temperature.False
Ambient conditions can influence mold temperatures, causing disparities.
How Can Temperature Control Enhance Molded Part Quality?
In injection molding, precise temperature control is key to producing high-quality parts efficiently.
Temperature control in molding ensures consistent material flow, reducing defects like warping and flow marks. By maintaining optimal temperature, parts achieve better dimensional accuracy, improved surface finish, and enhanced mechanical properties.
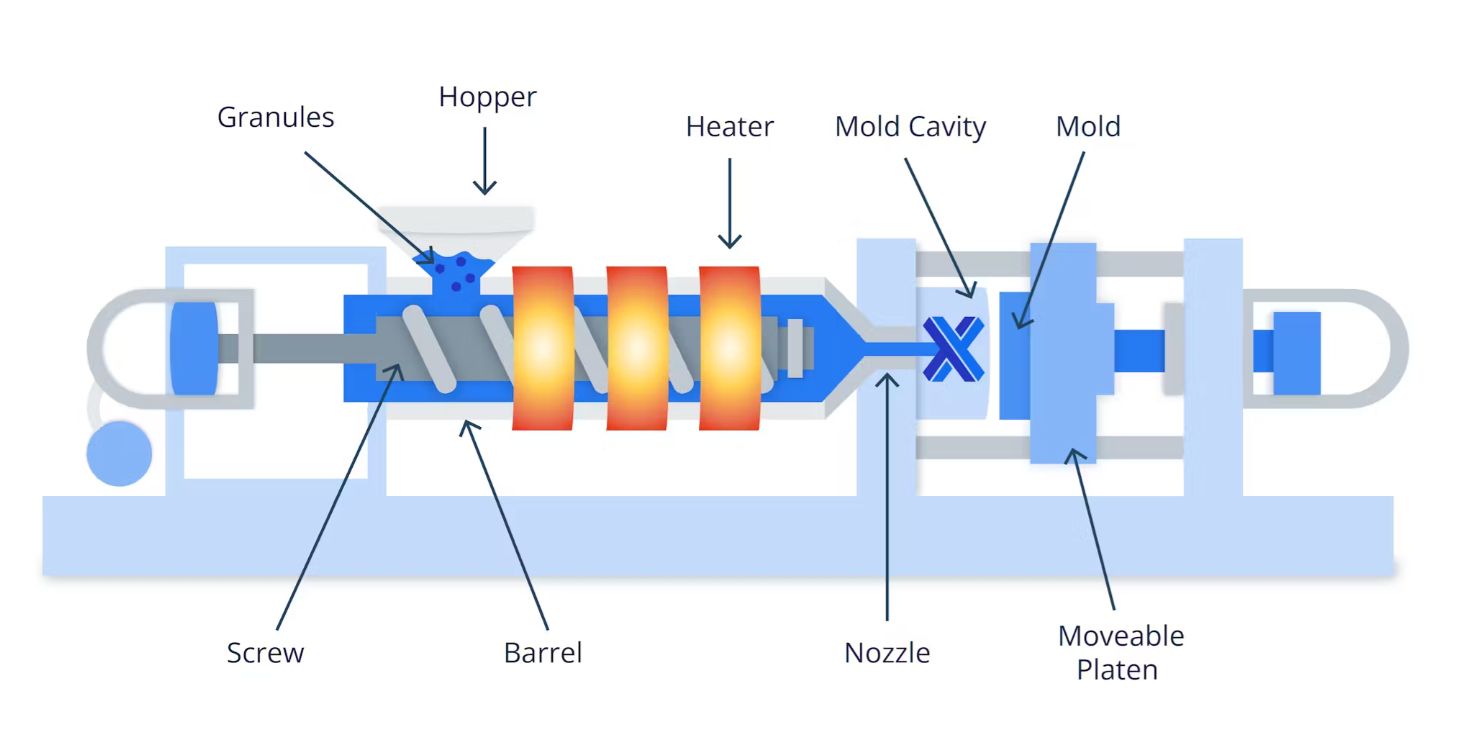
The Importance of Uniform Temperature Distribution
Achieving uniform temperature distribution within the mold is crucial for maintaining the integrity of molded parts. When temperature is controlled precisely, it allows for consistent material flow across the entire mold. This consistency prevents flow marks and weld lines3 that typically occur when temperature variations cause uneven flow rates.
Maintaining uniformity also aids in achieving the desired dimensional accuracy. Variations in mold temperature can lead to differential cooling rates, which in turn cause parts to shrink unevenly. By controlling the mold temperature, manufacturers can ensure that each part cools at a consistent rate, preserving its intended dimensions and improving fit and assembly precision.
Enhancing Surface Quality
Surface finish is an essential aspect of molded part quality. Temperature control plays a pivotal role here by ensuring that the molten material replicates the fine details of the mold surface. A well-regulated mold temperature allows for a smooth finish by preventing premature solidification of the material.
For instance, in high-temperature areas, the plastic melt flows more smoothly, allowing for a higher gloss finish. Conversely, cooler areas can result in dull surfaces or incomplete filling of the mold’s fine features. Thus, consistent temperature management is key to avoiding these issues and achieving superior surface aesthetics.
Optimizing Mechanical Properties
The mechanical properties of a molded part—such as strength and toughness—are significantly influenced by the temperature at which it is processed. In regions of the mold where temperature is higher, polymer chains have more time to crystallize and align properly, resulting in stronger and tougher components.
Lower temperatures may lead to inadequate molecular alignment, causing weak spots within the material. By carefully managing mold temperatures, manufacturers can ensure that the mechanical properties are uniform throughout the part, enhancing its reliability and performance.
Strategies for Effective Temperature Control
Implementing efficient temperature control involves utilizing advanced technologies such as:
- Thermal sensors: These are used to monitor and adjust mold temperatures in real-time.
- Heating and cooling systems: Integrating these systems can help maintain optimal temperatures throughout the molding process.
- Simulation tools: These tools predict how different temperatures affect material flow and cooling, allowing for adjustments before production begins.
By employing these strategies, manufacturers can significantly enhance part quality, leading to better performance and reduced manufacturing defects.
Uniform temperature prevents flow marks in molded parts.True
Consistent mold temperature ensures even material flow, reducing defects.
High mold temperatures lead to weaker mechanical properties.False
Higher temperatures allow better polymer alignment, enhancing strength.
What Are the Common Defects Due to Temperature Variations?
Temperature fluctuations during manufacturing can lead to various defects in products. Understanding these issues is crucial for quality control.
Common defects due to temperature variations include warping, dimensional inaccuracy, and inconsistent surface quality. These defects arise from uneven cooling and heating, affecting the material’s properties and the final product’s performance.
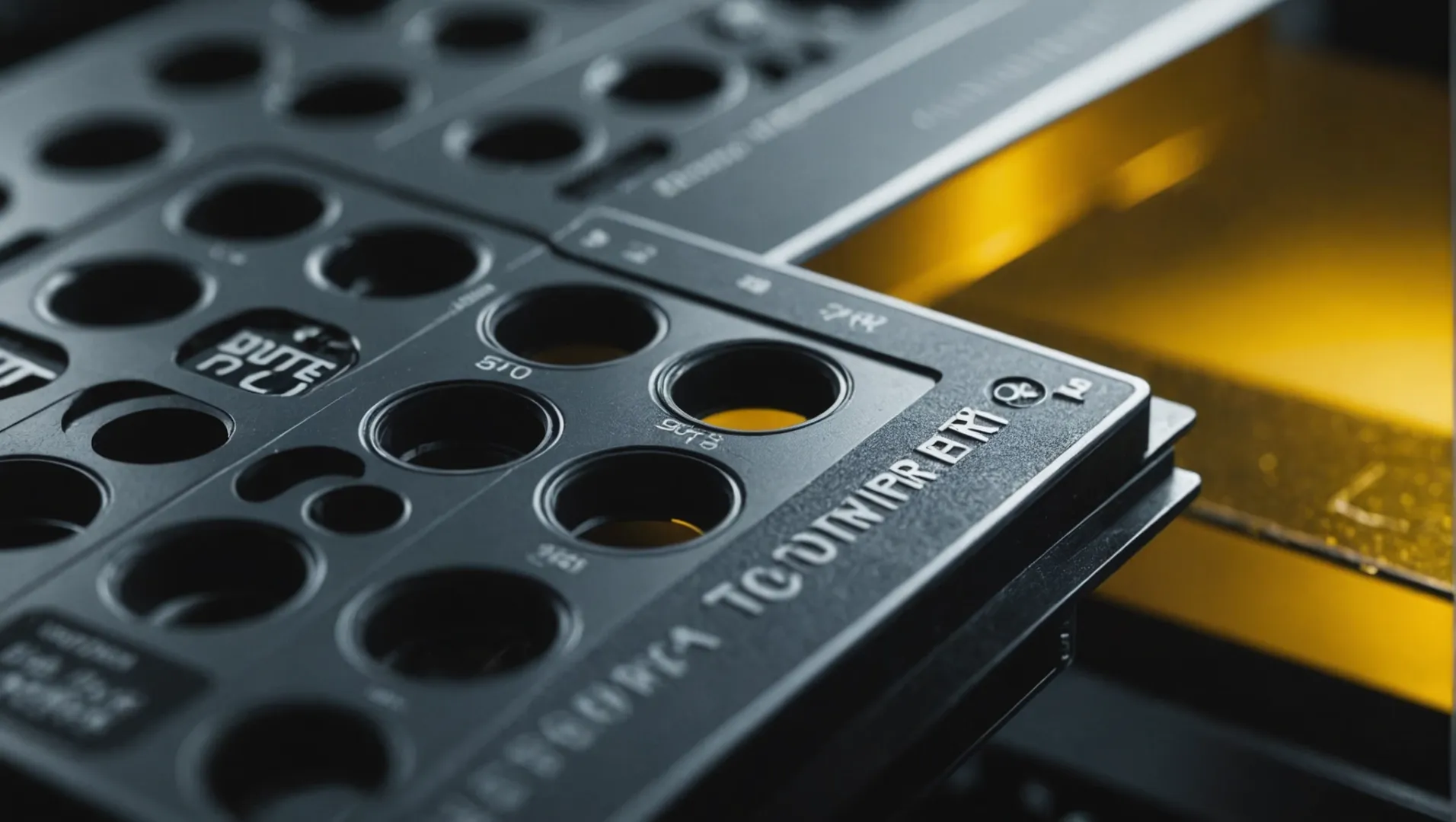
Dimensional Inaccuracy
Temperature variations often lead to dimensional inaccuracies in molded parts. When the mold temperature is uneven, certain areas of the plastic melt may have better fluidity due to higher temperatures. This results in a more complete filling of the cavity and less cooling shrinkage, causing the dimensions in these areas to be larger. Conversely, cooler areas may exhibit reduced melt flow, leading to insufficient filling and greater shrinkage, ultimately resulting in smaller dimensions.
The following table illustrates how temperature variations can affect dimensional accuracy:
Temperature Zone | Fluidity | Shrinkage | Dimensional Outcome |
---|---|---|---|
Higher | Better | Less | Larger Size |
Lower | Worse | More | Smaller Size |
This inconsistency is particularly problematic for high-precision assembly requirements, where even minor dimensional variations can lead to significant issues.
Appearance Quality Issues
Surface Gloss Inconsistency
Inconsistent surface gloss is a visible defect caused by uneven mold temperatures. Higher temperatures allow the plastic melt to replicate the mold’s finish more effectively, resulting in a glossy surface. Conversely, cooler areas may not achieve full replication, leading to dull or rough surfaces.
Flow and Weld Marks
Flow marks occur when the plastic melt moves at different speeds across the mold due to temperature differences. Areas with lower temperatures slow down the flow, creating visible marks. Weld marks form when multiple melt strands converge in temperature-variant zones, leaving noticeable lines on the finished part.
Warping Deformation
Uneven cooling leads to differential stress distribution within the part, causing warping. As different temperature zones shrink unevenly, parts may warp, affecting both appearance and functionality.
Mechanical Property Variations
Strength Differences
Temperature variations influence molecular arrangement and crystallinity. In hotter zones, plastic molecules have more time for orderly crystallization, enhancing strength. Cooler zones result in lower crystallinity and weaker structural integrity.
Toughness Variations
The toughness of molded parts can vary due to uneven temperatures. Generally, plastics exhibit better toughness at higher temperatures, whereas cooler areas may compromise impact resistance and durability.
By addressing these common defects through precise temperature control, manufacturers can ensure consistent quality and performance in their molded products. For further insights into how temperature control enhances molded part quality4 or to learn about optimizing mold temperature5 for better performance, continue exploring this topic.
Temperature variations cause warping in molded parts.True
Uneven cooling leads to differential stress, causing warping.
Higher mold temperatures result in duller surfaces.False
Higher temperatures enhance surface gloss by better mold finish replication.
How to Optimize Mold Temperature for Better Performance?
Optimizing mold temperature is key to ensuring high-quality injection molded parts. But how can you achieve the perfect balance?
To optimize mold temperature for better performance, maintain uniform heating across the mold surface, use advanced temperature control systems, and regularly monitor and adjust settings to suit material specifications. These practices help prevent defects, enhance product quality, and ensure manufacturing efficiency.
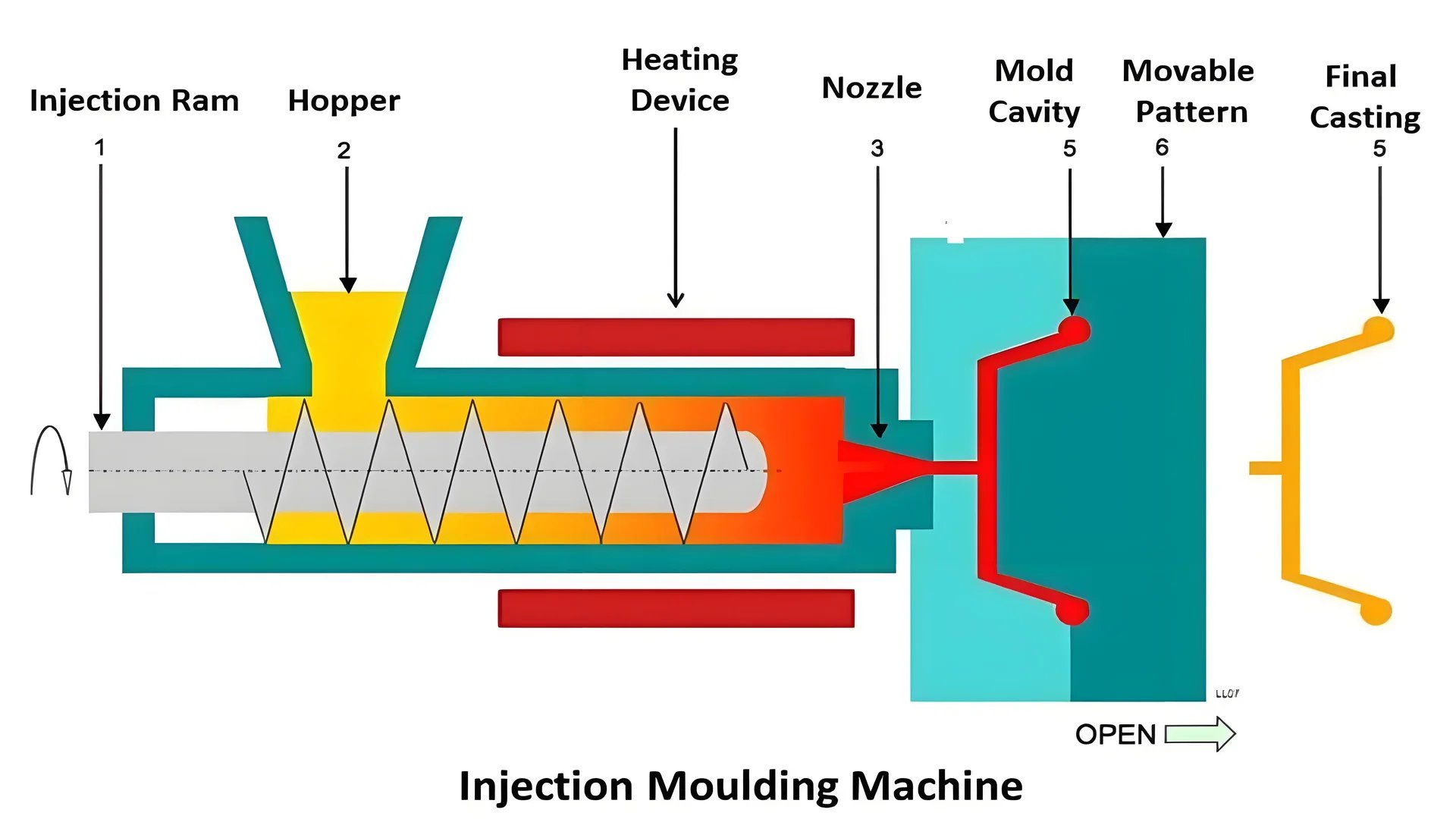
Importance of Uniform Mold Temperature
Maintaining a consistent mold temperature is crucial for achieving high-quality injection molded parts. Uneven temperatures can lead to issues like dimensional inaccuracies6 and surface defects. By ensuring even heating, the material flows uniformly, filling the mold completely and cooling evenly to avoid shrinkage and warping.
Advanced Temperature Control Systems
Investing in advanced temperature control systems can dramatically improve mold temperature consistency. These systems often include features like multi-zone heating7 and real-time monitoring, allowing for precise adjustments tailored to specific materials. This leads to enhanced mechanical properties and aesthetic quality of molded parts.
Monitoring and Adjustments
Regular monitoring and timely adjustments are essential in optimizing mold temperature. Using sensors to track temperature variations allows for immediate corrections, preventing defects before they occur.
For example, if a sensor detects a drop in temperature in one area of the mold, the system can automatically increase heat to maintain uniformity. This proactive approach not only ensures better performance but also reduces waste and improves efficiency.
Material-Specific Temperature Settings
Different materials require unique temperature settings to perform optimally. Understanding the specific requirements of your material is key to setting the correct mold temperature. For instance, materials like ABS may need higher temperatures compared to polypropylene to prevent defects such as flow marks or weld lines.
Consulting with material suppliers or referring to material datasheets8 can provide insights into the ideal temperature range for your chosen material, ensuring better product performance and quality.
Uniform mold temperature prevents surface defects.True
Consistent temperatures ensure even material flow, reducing defects.
ABS requires lower mold temperatures than polypropylene.False
ABS typically needs higher temperatures to avoid flow marks.
Conclusion
By addressing temperature variations effectively, manufacturers can significantly enhance the dimensional accuracy, appearance, and mechanical properties of their injection molded parts.
-
Understand how flow marks form and affect part quality.: Flow marks, also referred to as flow lines, appear as wavy patterns or ripples on a molded part’s surface. Flow marks commonly occur as lines or circles and … ↩
-
Learn about factors contributing to warping deformations.: Material shrinkage during and after manufacturing plays an important role in why injection molded plastic parts warp. ↩
-
Learn about how flow marks impact product aesthetics and functionality.: Flow marks commonly occur as lines or circles and they indicate an uneven material flow. Find out where they come from and how to prevent it? ↩
-
Learn techniques for improving product quality through temperature control.: Let’s break the mold down into two simple parts, the heat exchanger and the pressure vessel, and review how they can impact overall part quality and dimensions. ↩
-
Discover strategies for optimizing mold temperatures to enhance performance.: Need to figure out your mold-cooling energy requirements for the various polymers you run? What about sizing cooling circuits so they … ↩
-
Learn how temperature impacts dimensional stability and precision in molding.: For softer plastics, low mold temperature during molding favors dimensional stability. Regardless of the material, consistent mold temperature … ↩
-
Explore how multi-zone heating improves mold temperature consistency.: Energy Efficiency: Optimizing energy consumption by minimizing heat loss and ensuring uniform temperature distribution throughout the mold. ↩
-
Find detailed temperature settings for different molding materials.: The Standard Material Data Sheet. The standard material data sheet consists almost entirely of performance characteristics measured at room temperature. In … ↩