Do you ever think about how plastic changes into different forms during extrusion? It’s really interesting!
The extrusion process produces continuous profiles with consistent cross-sections, such as pipes, rods, and custom profiles. The final shape depends on the die design and material properties, tailored for specific applications.
I remember the first time I saw extrusion at work. Watching a simple plastic pellet change into a long, sleek pipe felt like magic. This moment sparked my curiosity about the whole process. Extrusion mostly creates profiles with the same cross-section. We notice this in sturdy pipes that carry water. Strong rods also use extrusion; they become important supports in machinery. There are special profiles too. These are often complex and designed for specific uses. They include elegant frames for doors and windows. Each shape reveals a story of purpose. Each one shows how functional it is.
Extrusion primarily produces continuous profiles with constant cross-sections.True
This claim highlights the main outcome of the extrusion process, which is to create uniform shapes like pipes and rods.
The final shape of extruded products is solely determined by material type.False
This claim is false as the die design also significantly influences the final shape of extruded products.
- 1. What really influences the shapes we extrude?
- 2. Join me on a trip through extrusion, an intriguing plastic technology.
- 3. How does die design truly shape the dimensions of the final product?
- 4. What are common applications for different extruded profiles?
- 5. What advancements are being made in extrusion technology?
- 6. Conclusion
What really influences the shapes we extrude?
Did you ever think about how those perfectly shaped plastic pipes or shiny aluminum profiles are created? Understanding the main points of extruded shapes fascinates many. It’s very important for designers like us. We try to create products that really satisfy our clients’ needs.
Material properties, extrusion process parameters, cooling methods and application requirements are important factors for extruded shapes. These elements together determine the quality and functionality of extruded products. Designers create high-quality items tailored to specific applications. Products are really made for specific needs.
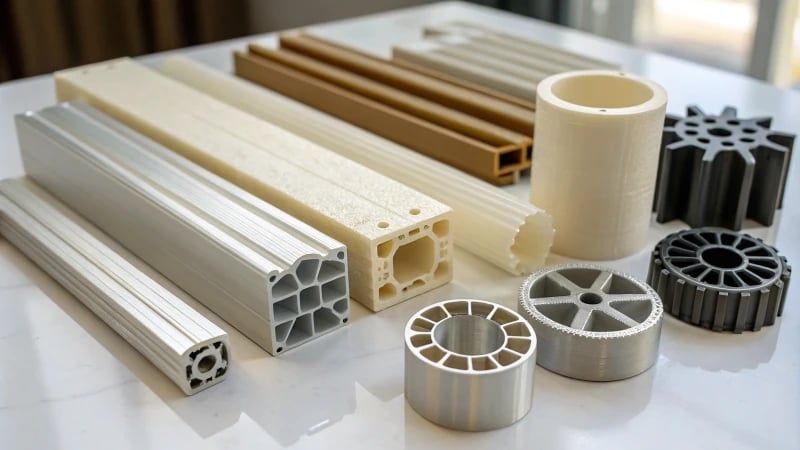
Join me on a trip through extrusion, an intriguing plastic technology.
It turns raw materials into long shapes with consistent forms. Years in product design taught me that every detail counts. Material type and extrusion details all matter. These choices help our designs work well and connect with users.
Material Properties
Material choice is essential. Picture a design meeting debating PVC, aluminum or polyethylene. Each material has unique traits. These traits decide their usage and placement.
Material | Characteristics | Applications |
---|---|---|
PVC | Lightweight, durable | Pipes, fittings |
Aluminum | High strength-to-weight ratio | Structural components, automotive parts |
Polyethylene | Excellent chemical resistance | Packaging, containers |
I recall my first aluminum project. The strength-to-weight balance amazed me. It suited structural parts in consumer electronics. Yet, melting points and flow nature mattered. These characteristics affected extrusion quality. Picking the right one felt like finding a perfect puzzle piece. This couldn’t be more crucial.
For more on material selection1 in extrusion, see here.
Extrusion Process Parameters
Exploring deeper, I learned that extrusion demands precise adjustment of multiple factors:
- Temperature: Finding the ideal temperature is tricky. Higher heat helps flow but can risk material integrity.
- Pressure: Pressure seems simple. Yet, low pressure might produce incomplete profiles – something I experienced during a tight deadline.
- Die Design: Creating die designs is a true art! Complex shapes call for precise engineering, both exciting and stressful.
Understanding these parameters helps optimize production and ensures that extruded shapes meet specific design criteria. For detailed insights on extrusion parameters2, check this out.
Knowing these factors improved our production. Our extruded shapes always meet design needs without losing quality.
Cooling and Solidification
Here’s where it gets fascinating. Cooling impacts the final shape greatly:
- Air Cooling: This method works well for thermoplastics; it allows fast solidification without issues.
- Water Bath: More traditional but ensures even cooling; this method is crucial for bigger profiles to avoid warping or shape changes.
Choosing the right cooling changed the game for me. It involved both functionality and looks. Perfect decorative trims needed precision; aesthetic quality is equally critical. To explore more about cooling methods3, click here.
Application Requirements
Projects forced me to adapt designs based on their goals:
- Load-Bearing Capacity: Managing internal pressures in pipes meant adjusting wall thickness and diameter properly.
- Aesthetic Considerations: In architecture, surface look and color were vital; these factors could make or ruin a design. It opened my mind to more than extrusion and expanded to post-treatment processes.
Tailoring designs based on application requirements ensures that extruded shapes fulfill both functional and aesthetic needs. To learn more about application-driven design4, see this link.
Material choice affects the properties of extruded shapes.True
Different materials have unique characteristics that influence the final product's performance in extrusion processes.
Higher extrusion temperatures always improve material quality.False
While higher temperatures can enhance flow, they may also degrade material properties if not controlled properly.
How does die design truly shape the dimensions of the final product?
Do you ever think about how a die’s design might affect a product’s size? I have explored the complex world of extrusion processes. The design of a die is very important. It is more important than you probably imagine!
The design of the die very significantly affects the size of extruded products. It guides how the material flows. It also keeps the profiles consistent. A well-made die results in exact size and shape. Precise dimensions are crucial for the best product performance.
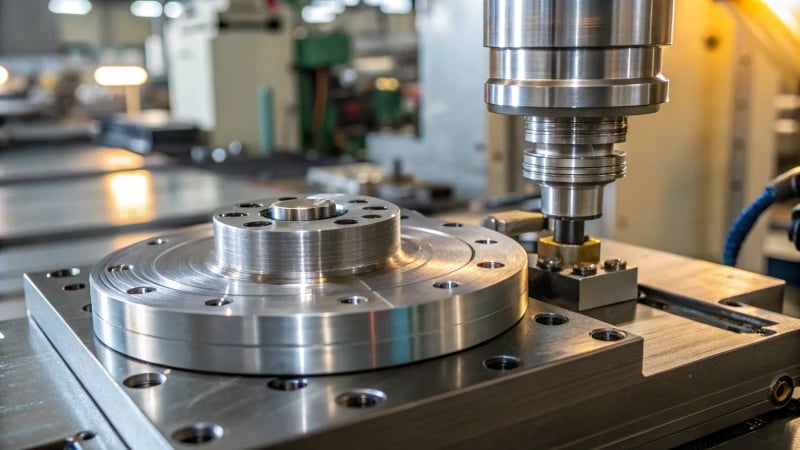
Understanding Die Design in Extrusion
Die design is a critical factor in determining the final dimensions of extruded products. The die shapes the molten material as it passes through, defining not just the cross-sectional profile but also influencing the consistency and quality of the product.
For example, consider pipes:
- The die must be engineered to ensure a uniform circular cross-section that can vary in wall thickness or diameter based on application requirements.
- If the die is poorly designed, it can lead to defects such as uneven walls or dimensional inaccuracies, which can adversely affect the product’s performance.
Types of Dies and Their Impact on Dimensions
Different types of dies will yield distinct impacts on the dimensions of the final product:
Die Type | Application Example | Impact on Dimensions |
---|---|---|
Circular Die | Water pipes | Uniform circular cross-section |
Square Die | Rods for machining | Consistent square cross-section |
Special Shape | Frame profiles for windows | Complex shapes tailored to specific functions |
The design of special profiles requires intricate die designs to accommodate unique cross-sectional shapes, which can include polygons and other complex geometries. The die’s precision affects not only the dimensions but also how well these profiles fit in their intended applications.
Material Flow and Its Effect on Dimensions
The flow characteristics of the material through the die significantly influence the final product dimensions.
- For instance, in pipe extrusion, if the material flows unevenly due to poor die design, it can result in variations in wall thickness or diameter.
- Achieving a steady flow is essential for maintaining uniformity in dimensions. Inconsistent flow can cause defects that may require costly rework or lead to product failure.
Conclusion
Understanding how die design affects product dimensions is essential for optimizing extrusion processes. By tailoring the die to meet specific requirements, manufacturers can enhance product quality and ensure that dimensions align with specifications. If you’re keen to learn more about die design, check out this resource5. It might save you from the pitfalls I faced!
Poor die design can cause uneven wall thickness in pipes.True
If the die is not properly designed, it can lead to defects like uneven walls, affecting product performance.
Die design has no impact on the quality of extruded products.False
This statement is false; die design is crucial for ensuring product quality and dimensional accuracy.
What are common applications for different extruded profiles?
Extruded profiles surround us in daily life. Have you wondered about their origin or uses? Let’s explore the intriguing world of these adaptable shapes. We will uncover their applications in everyday situations together!
Extruded profiles are useful in many industries. They are common in plumbing for water, drainage and gas pipes. Industries use them for structural support, like rods. Architectural designs also use special profiles. Their unique properties help meet specific needs in different areas. These profiles are very versatile.
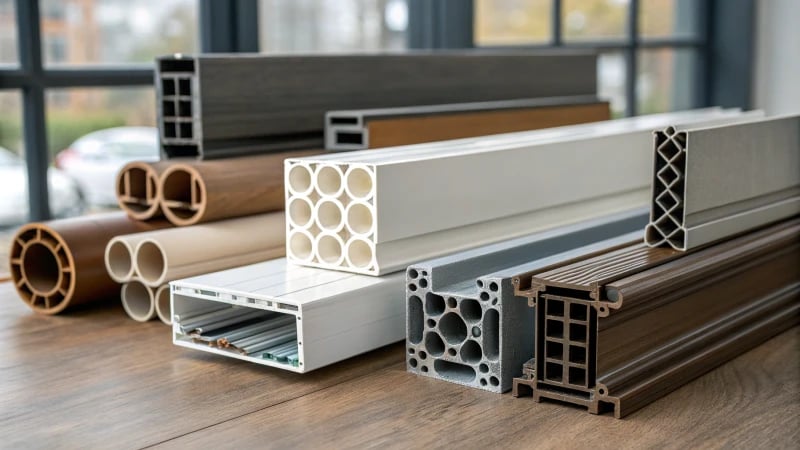
Understanding Extruded Profiles
When I first learned about extrusion technology, I felt amazed at how it creates endless shapes with the same cross-section. It’s like magic! This process allows many uses in different industries, turning raw materials into important parts that support our daily lives.
Common Applications of Extruded Profiles
1. Pipes
I remember my first plumbing project, a DIY renovation of my bathroom. I had to choose the right pipes and that’s when I learned how vital extruded pipes are in construction and plumbing. They come in many types, including:
- Water Supply Pipes: Carry fresh, clean water to our homes.
- Drainage Pipes: The unsung heroes of waste management.
- Gas Pipes: Provide fuel for heating and cooking in homes and businesses.
Type of Pipe | Applications | Typical Cross-Section |
---|---|---|
Water Supply Pipe | Residential, Industrial | Circular |
Drainage Pipe | Waste Management | Circular |
Gas Pipe | Utility Lines | Circular |
The design of these pipes changes based on their roles, adjusting wall thickness and diameter to work perfectly for their tasks.
2. Rods
I find it intriguing that extrusion also produces rods with regular shapes, like circular or square cross-sections. These rods are very useful in different places:
- Machining Blanks: Act as raw material for further work.
- Support Structures: Add stability and strength to simple designs.
Shape | Use Cases | Length Customization |
---|---|---|
Circular | Blank for machining | Cut to requirement |
Square | Supporting parts | Cut to requirement |
The adaptability of these rods is impressive; they are crafted to match the exact needs of a project. They are truly versatile.
3. Special Profiles
Now, let’s talk about special profiles! These are the intricately designed shapes for specialized applications. They include:
- Frame Profiles: Crucial for plastic doors and windows, with detailed features like card slots and sealing grooves.
- Architectural Profiles: Used for decoration, improving ceilings and corners with style.
Profile Type | Application | Cross-Section Shape |
---|---|---|
Frame Profile | Doors and Windows | Polygonal |
Architectural Profile | Interior Design | Complex shapes |
Each of these special profiles is created with care. They meet specific installation and usability needs.
Conclusion
From plumbing to architecture, the wide applications of extruded profiles show the incredible versatility and functionality of this technology. I really appreciate how much they contribute to our everyday experiences. If you’re curious to learn more about using aluminum extrusions, check out the advantages of aluminum extrusions6. It’s probably a journey worth taking!
Extruded pipes are exclusively used for gas distribution.False
This claim is false as extruded pipes are also used for water supply and drainage, not just gas.
Rods produced through extrusion can be customized in length.True
True, extruded rods can be cut to specific lengths based on user requirements, enhancing their adaptability.
What advancements are being made in extrusion technology?
Extrusion technology changes rapidly. This progress transforms manufacturing and sustainable materials. Many exciting innovations shape this field. Have you ever thought about them?
Recent improvements in extrusion technology involve co-extrusion for multi-layered products. Automation increases efficiency. New sustainable materials improve product quality. The new materials really help in reducing the environmental impact.
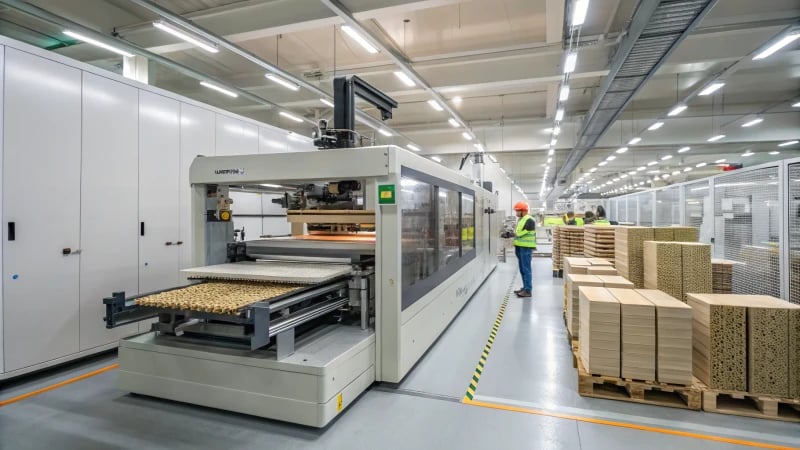
Innovations in Extrusion Processes
I have been watching extrusion technology grow, and it is very impressive! One fascinating advancement is the development of co-extrusion, which creates multi-layered products all at once. This technique optimizes efficiency and innovation. Picture a pipe with an inner layer resisting chemicals and an outer layer tough against environmental conditions. It is like a superhero pipe! It resists elements and performs its job perfectly!
Another breakthrough is combining 3D printing with extrusion. This new approach allows for more design options and less material waste. When I first saw such a product, I was amazed by its complex shapes. Truly, this is the future of manufacturing, where tailored solutions come to life, meeting very specific needs.
Materials Advancements
Materials in extrusion are also evolving. We now use bio-based plastics and recycled materials. These changes support sustainability in amazing ways. As someone who cares for our planet, it is great to see eco-friendly choices. Using recycled plastic in pipes prevents landfill waste while keeping high quality; it benefits everyone!
Automation and Smart Technology
Automation sees remarkable progress too. Incorporating smart sensors and data analytics in extrusion lines are changing the game. These machines seem to think! Real-time monitoring and adjustments keep quality steady and predict maintenance needs, reducing downtime which is crucial for efficiency.
Moreover, machine learning algorithms use past data to refine processes. It fascinates me to see how tech transforms traditional methods into effective and smooth operations.
Technology Type | Benefits |
---|---|
Co-extrusion | Multi-layer products with tailored properties |
3D Printing Integration | Customization and reduced material waste |
Use of Bio-based Plastics | Eco-friendly solutions |
Automation & Smart Tech | Enhanced efficiency and predictive maintenance |
Special Applications
Advancements in extrusion lead to exciting specialized uses. Creating special profiles has become more precise with better design tools. Manufacturers craft complex shapes for specific functions; for example, sealing grooves in window frames improve energy efficiency directly impacting daily life!
Additionally, micro-extrusion also gains attention as this method makes tiny products with perfect precision—important in fields like medical device manufacturing.
In summary, the extrusion industry adapts and flourishes despite market and environmental challenges. Staying updated is important for anyone in this field; curious minds should explore advanced extrusion technologies7 or sustainable materials in manufacturing8. It is a thrilling time to participate in this industry!
Co-extrusion allows for multi-layered product creation.True
Co-extrusion enables the simultaneous production of products with different material properties, enhancing functionality and application suitability.
3D printing reduces material waste in extrusion processes.True
Integrating 3D printing with extrusion minimizes material waste while allowing complex designs and faster production times.
Conclusion
Extrusion technology creates various continuous profiles such as pipes and rods. Factors like material choice and die design significantly influence the final product’s shape and quality.
-
Discover how different materials affect extrusion quality and performance. This link provides insights into choosing the right material for your project. ↩
-
Learn about how process parameters influence extrusion outcomes. This link will guide you through critical extrusion settings. ↩
-
Explore different cooling techniques used in extrusion processes. This resource will enhance your understanding of solidification effects on shapes. ↩
-
Understand how application requirements drive design decisions in extrusion. This link offers valuable perspectives for optimizing your designs. ↩
-
Discover how die design influences product dimensions and enhances production efficiency in extrusion processes. ↩
-
Explore this link to discover the various industries utilizing aluminum extrusions and their specific applications. Gain insights that could enhance your projects. ↩
-
Explore cutting-edge technologies in extrusion that enhance efficiency and sustainability in manufacturing processes. ↩
-
Learn about sustainable practices in manufacturing, particularly related to materials used in extrusion processes. ↩