When embarking on a manufacturing journey, understanding the lead-time for plastic injection molds becomes essential. It’s not just about waiting; it’s about planning and strategizing your next steps.
The typical lead-time for a plastic injection mold ranges from a few weeks to several months, depending on factors such as mold complexity, size, precision requirements, and the supplier’s production capacity.
But wait—there’s more! Let’s dive deeper into the specific factors that influence these timelines and explore how we can optimize them.
Mold complexity affects lead-time significantly.True
Complex molds require intricate designs and precision, extending lead-time.
How Does Mold Complexity Impact Lead-Time?
Mold complexity plays a pivotal role in determining the lead-time for plastic injection molds.
The complexity of a mold directly impacts its lead-time, with simpler molds typically requiring a few weeks and complex molds needing several months. Key factors include the intricacy of the design, precision requirements, and the number of moving parts involved.
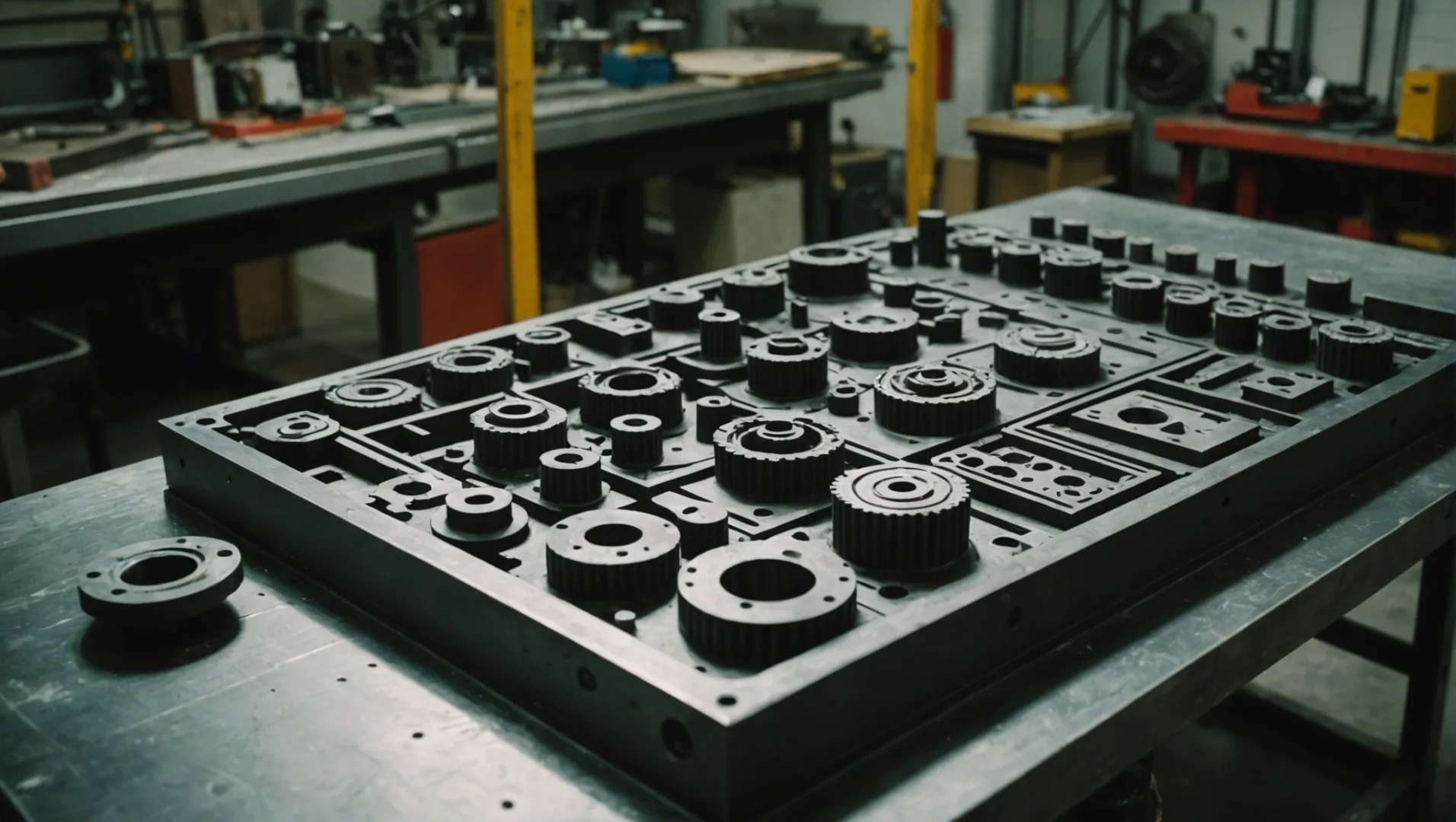
Understanding Mold Complexity
Mold complexity encompasses several aspects, including the structural intricacy, the number of components, precision specifications, and any special functionalities. Each of these factors contributes uniquely to extending or shortening lead-time.
Simple vs. Complex Molds
-
Simple Molds: These molds are straightforward in design, often small, and lack specialized features. Their production is generally faster, taking only a few weeks to a month. For instance, molds used for basic household items are less demanding in terms of design and manufacturing processes.
-
Complex Molds: These molds feature intricate designs, high precision requirements, and multiple moving parts. They require detailed planning and involve complex manufacturing processes like CNC and EDM machining. An example would be molds used for automotive parts, which can extend lead-time to several months due to their complexity and precision demands.
Design and Precision Requirements
The level of precision required significantly affects lead-time. Molds with high precision1 require meticulous control during manufacturing, extending the preparation cycle. Larger molds with high precision also demand more extensive processing and assembly efforts, further impacting timelines.
Mold Type | Precision Requirement | Lead-Time Estimate |
---|---|---|
Small & Simple | Low | 2-4 weeks |
Large & Complex | High | 2-4 months |
Influence of Design Changes
Frequent design changes or modifications during the mold development phase can significantly prolong lead-time. Each change necessitates a cycle of redesign, reprocessing, and additional testing. Moreover, the approval process for these changes can delay progress if not managed efficiently.
Strategies for Managing Complexity
- Advance Planning: Engage with suppliers early in the process to understand requirements and plan for potential challenges.
- Optimized Design Tools: Utilize advanced software to enhance design efficiency, reducing unnecessary complexities.
- Concurrent Engineering: Implement simultaneous design and manufacturing processes to streamline lead-times.
By addressing these complexity factors effectively, manufacturers can better manage timelines and optimize project outcomes.
Simple molds are completed in 2-4 weeks.True
Simple molds, with straightforward designs, typically take 2-4 weeks.
Complex molds never require design changes.False
Complex molds often undergo design changes, extending lead-times.
What Role Does Supplier Capacity Play in Mold Preparation?
Supplier capacity is crucial in determining the efficiency and speed of mold preparation.
Supplier capacity directly influences mold preparation by dictating the pace of production, resource allocation, and the ability to manage concurrent projects effectively. Strong supplier capacity can significantly reduce lead-times, whereas limited capacity can cause delays and extend preparation cycles.
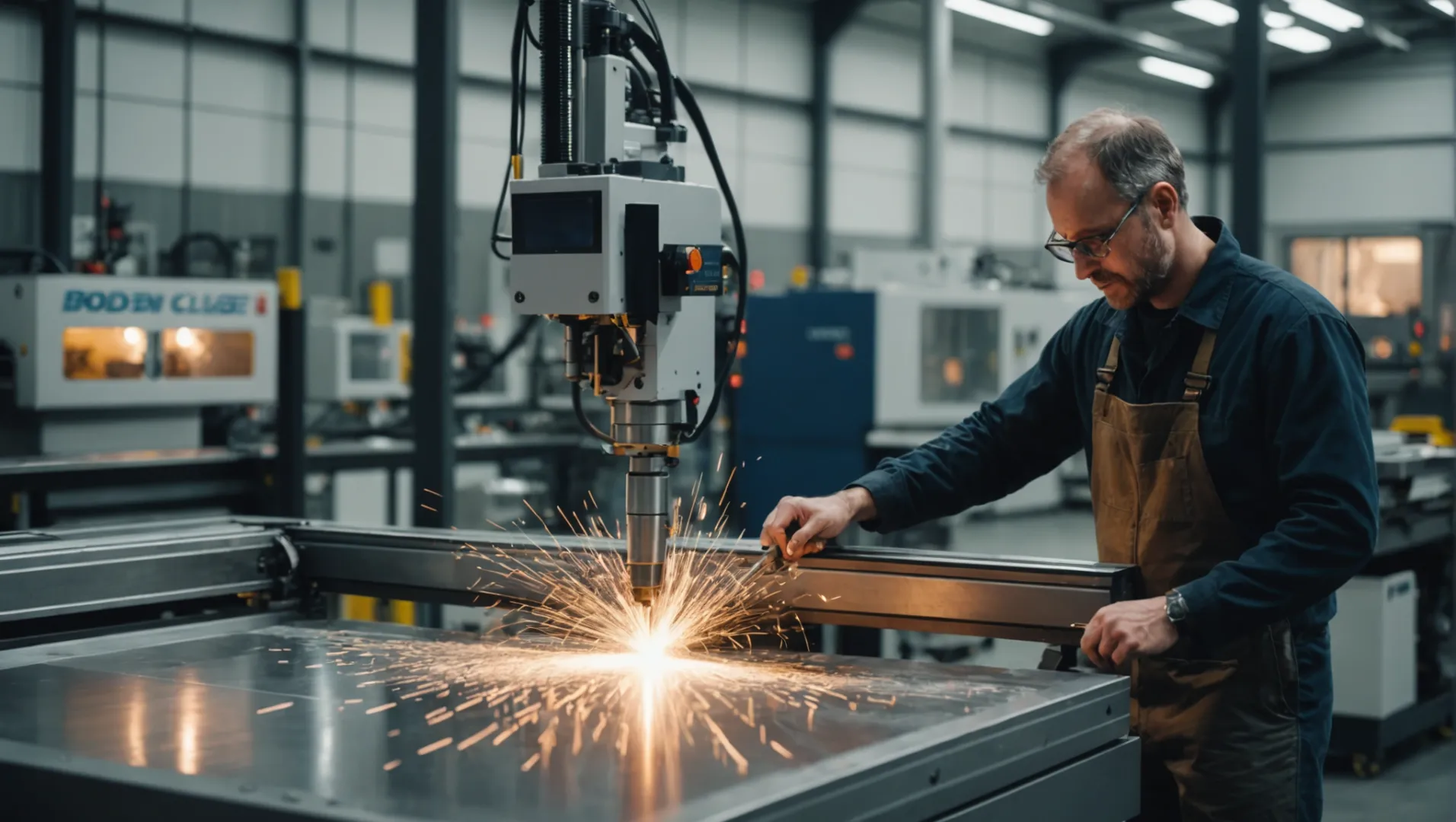
Understanding Supplier Capacity
Supplier capacity refers to a manufacturer’s ability to handle production demands efficiently, encompassing aspects such as equipment availability, workforce expertise, and resource management. A supplier with high capacity can accelerate mold preparation by optimizing production schedules and reducing bottlenecks.
- Advanced Equipment and Technology: Suppliers equipped with cutting-edge technology like high-speed CNC machines and automated processes can streamline operations. This reduces manual interventions, minimizes errors, and enhances precision.
- Skilled Workforce: An experienced team capable of handling complex tasks ensures that each stage of mold preparation is conducted smoothly, maintaining quality while adhering to timelines.
Impact on Lead-Times
The capacity of a supplier plays a pivotal role in determining the lead-time of mold preparation.
- Efficient Scheduling: High-capacity suppliers often employ sophisticated scheduling systems that allow for optimal resource allocation. This means projects are less likely to experience downtime or delays due to resource shortages.
- Concurrent Project Management: With robust capacity, suppliers can manage multiple projects simultaneously without compromising on quality or delivery times. This flexibility is particularly beneficial for clients requiring multiple molds or facing tight deadlines.
Challenges with Limited Capacity
Suppliers with constrained capacity face several challenges that can adversely affect mold preparation timelines.
- Overloading: Taking on too many projects without adequate resources leads to stretched timelines and increased chances of errors. This can further delay production as issues need rectifying.
- Resource Shortages: Limited capacity often means insufficient access to necessary materials or equipment, causing stoppages and extending lead-times.
Real-World Examples
Consider a large automotive parts manufacturer2 that requires intricate molds for various components. A supplier with strong capacity could deliver multiple molds concurrently, ensuring the manufacturer meets its production schedules without delays. In contrast, a supplier with limited resources might struggle to meet deadlines, leading to potential production slowdowns.
By understanding these dynamics, businesses can make informed decisions when selecting suppliers, ensuring their projects remain on track.
High supplier capacity reduces mold preparation lead-times.True
Strong capacity allows efficient scheduling and resource allocation.
Limited supplier capacity enhances production speed.False
Limited capacity often causes delays due to resource shortages.
Can Design Changes Affect Mold Lead-Times?
Design changes during mold preparation can significantly impact lead-times, often leading to delays.
Yes, design changes can greatly affect mold lead-times. Frequent modifications necessitate redesign, reprocessing, and extended approval processes, often prolonging the preparation cycle.
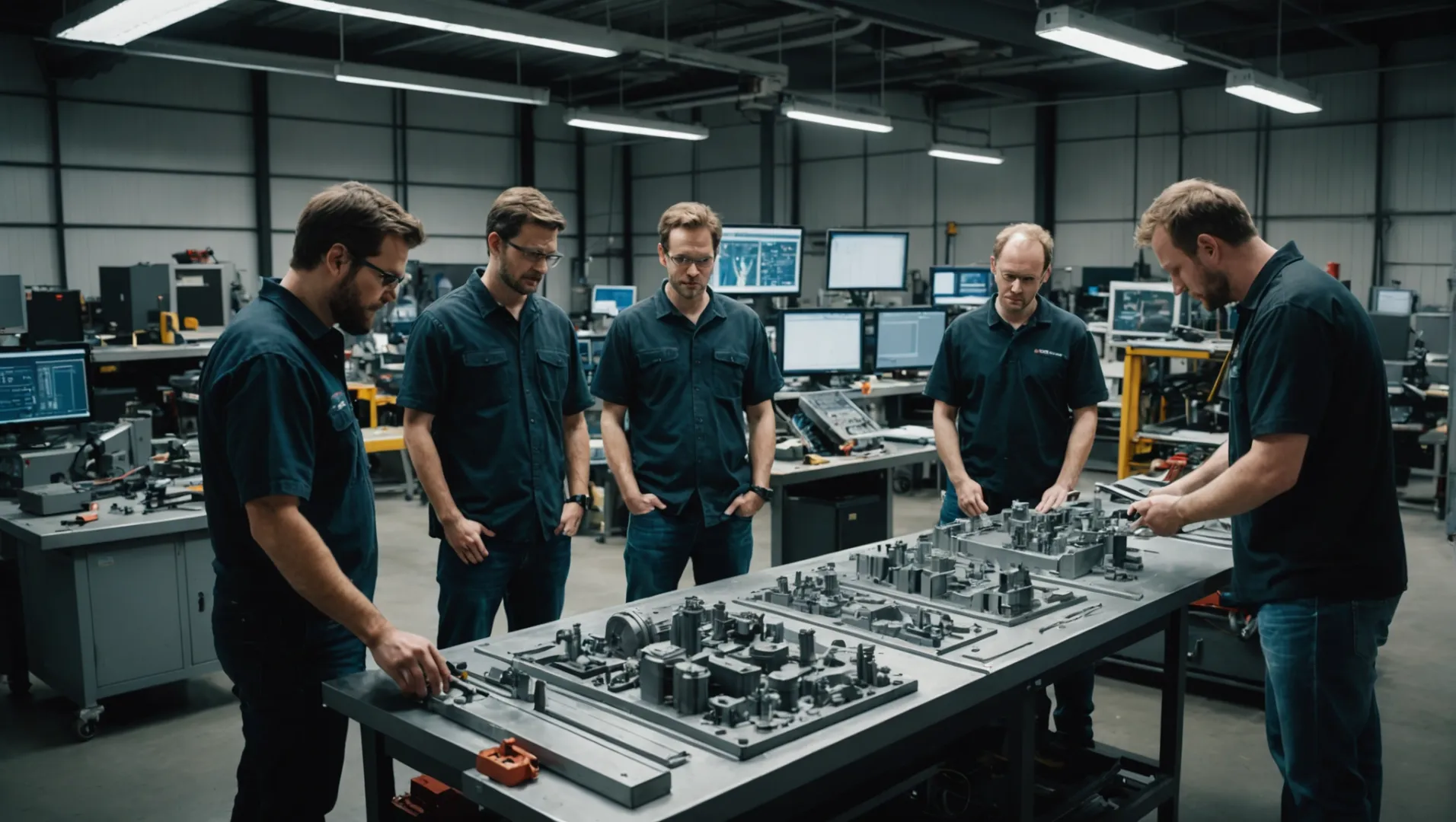
The Impact of Design Complexity on Lead-Times
Design changes can dramatically alter the timeline for mold preparation. When a design is complex, it inherently requires more time and precision. A minor change in such designs can result in extensive revisions to the mold’s architecture, impacting the lead-time significantly.
Simple vs. Complex Designs:
- Simple Designs: A straightforward design with minimal components may only require slight adjustments if changes are made, thus having a minimal effect on lead-times. For instance, altering the shape of a simple plastic box mold might be quick and require minimal processing changes.
- Complex Designs: In contrast, a complex design, such as those used in automotive parts, could require complete redesigns of multiple interconnected components. This complexity means that even a small change could cascade into significant delays due to increased precision requirements and additional testing phases.
Approval Processes and Their Role in Delays
The approval process is another critical factor where design changes can slow down mold preparation. A complex approval chain can lead to significant delays as each department or individual involved might need to reassess and approve the new design changes.
Streamlined vs. Complex Approval Processes:
- Streamlined Processes: Companies with efficient, straightforward approval processes experience fewer delays as decisions are made rapidly and communicated effectively. Effective communication3 within teams ensures that all stakeholders are informed and aligned.
- Complex Processes: In organizations with complex bureaucratic structures, changes might need approval from multiple levels, each adding its own review time to the overall process.
Strategies to Minimize Impact of Design Changes
- Advance Planning:
- Proactively planning for potential design changes by considering all aspects in the initial design stage helps mitigate future changes. Thorough initial discussions with suppliers about possible adjustments can prepare both parties for quicker transitions.
- Concurrent Engineering:
- Implementing concurrent engineering allows for parallel processes where design, manufacturing, and testing occur simultaneously. This approach can significantly reduce waiting times when changes are needed.
- Efficient Communication:
- Establishing clear and open communication channels between all parties involved ensures that any required changes are quickly understood and acted upon. This reduces the lag time between recognizing a need for change and implementing it.
By adopting these strategies, manufacturers can better manage the impact of design changes on mold lead-times, thereby optimizing their project timelines and reducing potential delays.
Complex designs lead to longer mold lead-times.True
Complex designs require more precision and revisions, extending lead-times.
Simple designs always cause significant mold delays.False
Simple designs usually need minimal adjustments, causing fewer delays.
What Strategies Can Reduce Mold Preparation Time?
Reducing mold preparation time is crucial for accelerating product launches and improving manufacturing efficiency.
To reduce mold preparation time, employ strategies like advance planning, design optimization, efficient communication, and concurrent engineering. These approaches streamline processes, minimize delays, and enhance collaboration, resulting in faster project completion.
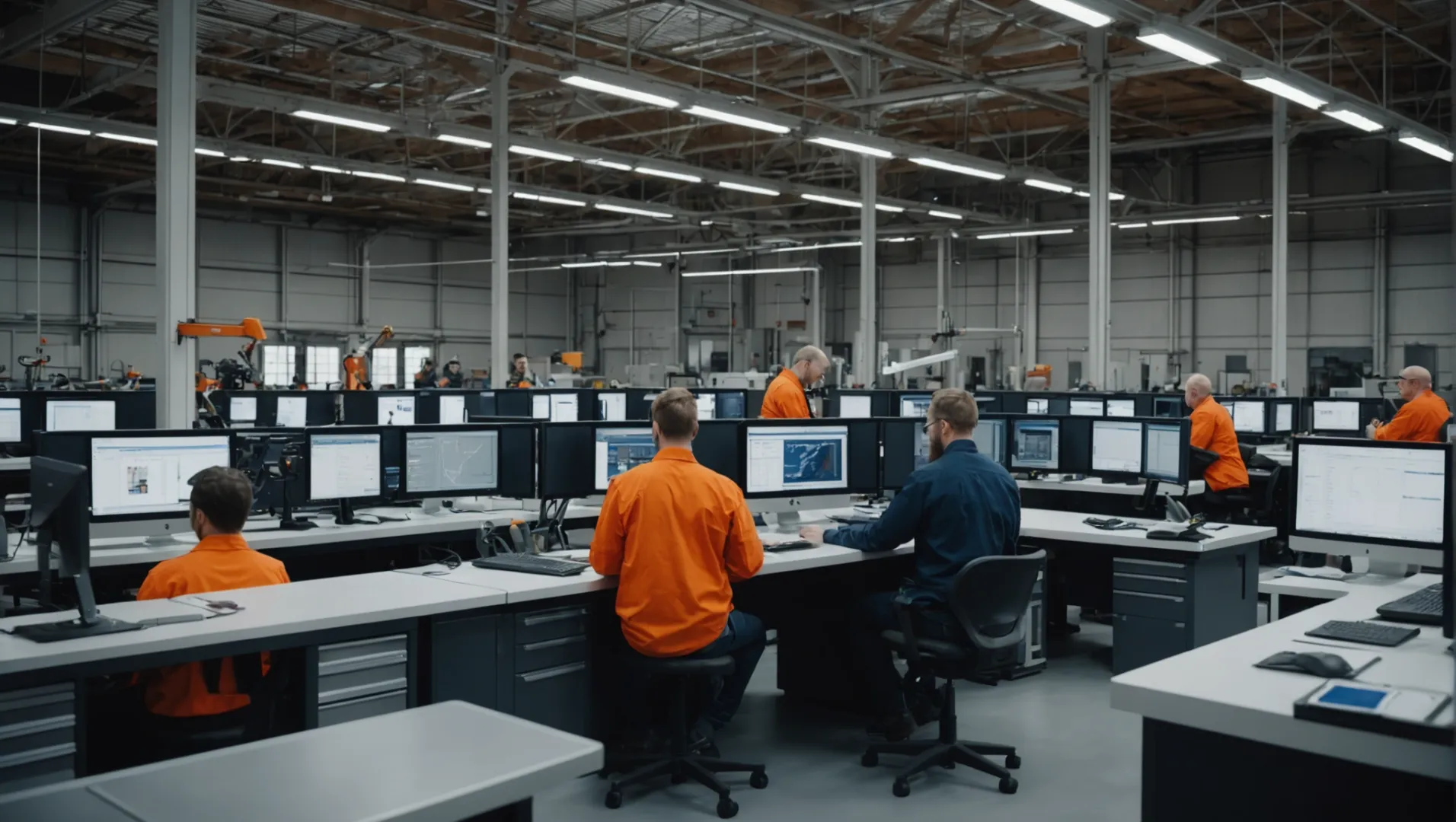
Advance Planning and Preparation
Advance planning is a cornerstone in minimizing mold preparation time. By thoroughly communicating with the mold supplier from the outset, you ensure that all requirements and specifications are clear. Preparing necessary design data and technical documents ahead of time allows the supplier to start work promptly. For instance, if a project requires specialized raw materials or processing technologies, planning and arranging these elements in advance secures their availability when needed.
Optimize Design and Manufacturing Process
Optimization at the design stage can significantly impact preparation speed. Utilizing advanced design software helps reduce unnecessary structures, enhancing the manufacturability and efficiency of the mold. During manufacturing, employing high-speed cutting and EDM technologies can drastically cut down processing time. Moreover, a strategic arrangement of processing sequences prevents redundant actions, saving valuable time.
Strengthen Communication and Coordination
Effective communication is key to keeping a project on track. Establishing a robust communication mechanism with your mold supplier enables you to stay updated on production progress and swiftly address any issues that arise. Within your team, fostering strong coordination between departments like design, production, and quality control ensures each phase proceeds smoothly, mitigating potential bottlenecks.
Conduct Concurrent Engineering
Concurrent engineering is a revolutionary approach that involves overlapping phases of design, manufacturing, and debugging rather than following them sequentially. This method significantly shortens the preparation cycle and boosts overall project efficiency. For example, while molds are being designed, procurement of materials and preparation of processing equipment can simultaneously occur, ensuring a seamless workflow.
Embracing these strategies not only reduces lead-time but also enhances the overall quality and efficiency of the manufacturing process. For more information on advanced mold design techniques4 or effective supplier management5, explore our recommended resources.
Advance planning reduces mold preparation time.True
Planning ensures all materials and documents are ready, speeding up the process.
Concurrent engineering delays mold preparation.False
Concurrent engineering shortens preparation time by overlapping project phases.
Conclusion
By understanding the complexities and planning strategically, you can effectively navigate the timelines associated with mold preparation.
-
Explore how high precision requirements extend mold lead-times.: Typical lead time could take 3 to 4 weeks for a single cavity prototype mold. This estimate is suited for low production volume of about 450 to 1000 samples. ↩
-
Explore how supplier capacity affects automotive parts manufacturing timelines.: We are a high-capacity automotive plastic parts manufacturer with a team of qualified injection mold engineers with experience spanning over 15 years. ↩
-
Learn how streamlined communication enhances project efficiency and reduces delays.: Here are 12 ways you can enhance effective communication in manufacturing between your organization and frontline employees and ultimately, boost your returns. ↩
-
Discover tools and methods to streamline mold design for efficiency.: Advanced casting methods include vacuum casting, centrifugal casting, and investment casting. These methods allow for better control over the … ↩
-
Learn how to manage suppliers for timely mold production.: 10 supplier management best practices and strategies · 1. Set strategic objectives and establish KPIs · 2. Adopt a centralized supplier … ↩