Navigating the world of plastics can feel overwhelming. But understanding the right materials can pave the way for your project’s success!
Several types of plastics are commonly used in injection molding, including polyethylene (PE), polypropylene (PP), polyvinyl chloride (PVC), polystyrene (PS), ABS plastic, polycarbonate (PC), and polyamide (PA). Each type offers unique properties suitable for different applications.
Let’s dive deeper into these materials! By exploring their distinct features and applications, you can select the most appropriate plastic for your specific needs.
Polyethylene is the most commonly used plastic for injection molding.True
Polyethylene's versatility, cost-effectiveness, and chemical resistance make it a popular choice.
What Are the Advantages of Using Polyethylene in Injection Molding?
Polyethylene (PE) is a versatile material widely used in injection molding due to its unique properties.
Polyethylene offers several advantages for injection molding, including excellent chemical resistance, low moisture absorption, and superior electrical insulation. It’s a cost-effective choice for creating durable products like containers, pipes, and household items.
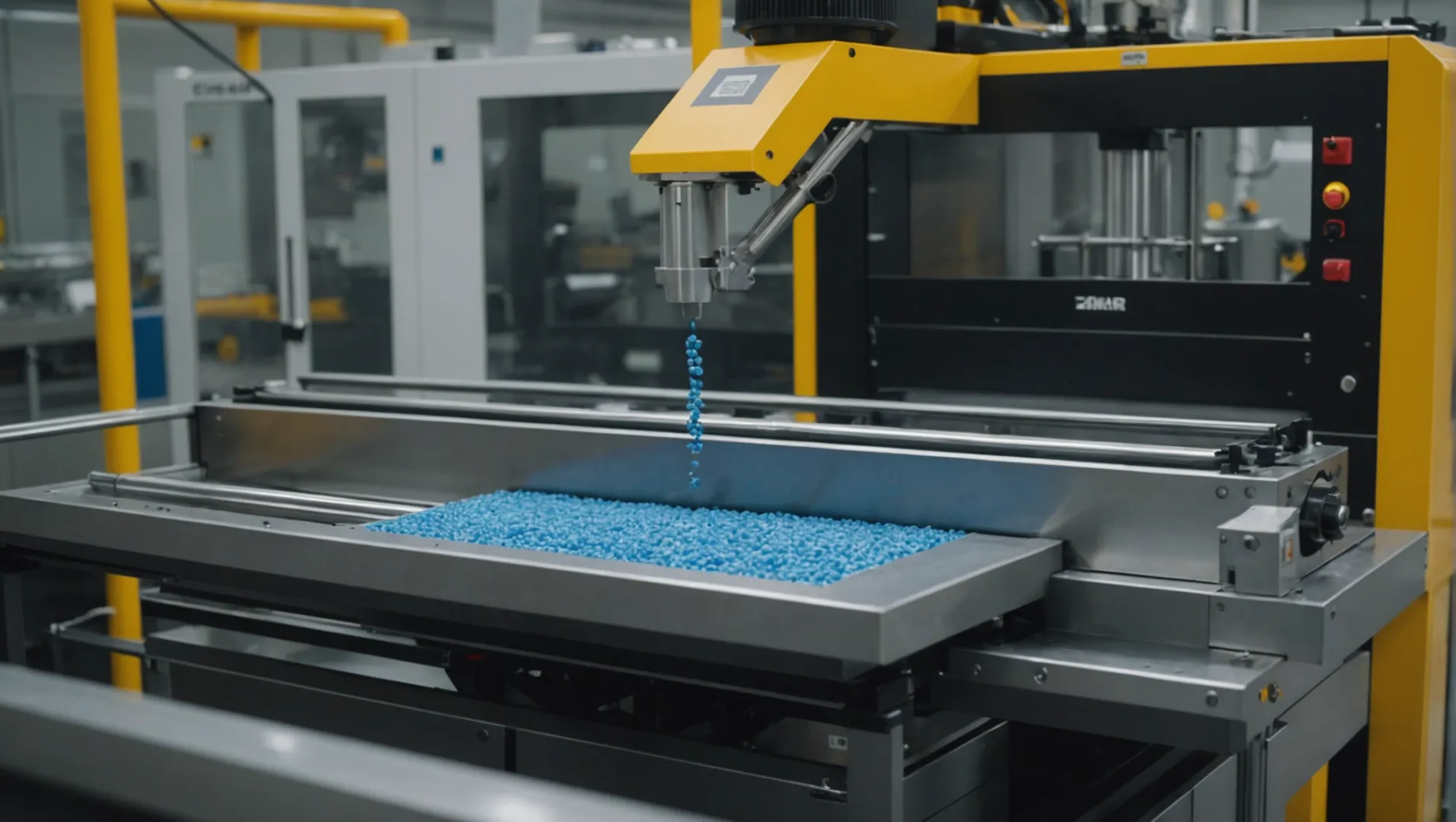
Polyethylene’s Unique Properties
Polyethylene stands out as an injection molding material due to its excellent chemical resistance1, which allows it to withstand most acids and alkalis. This characteristic makes it ideal for applications in chemical storage and packaging. Additionally, polyethylene has low water absorption, ensuring that molded products maintain their integrity and stability in moist environments.
Another significant advantage is its superior electrical insulation properties. This makes polyethylene a preferred choice for manufacturing electrical components and housings, where insulating capabilities are crucial.
Property | Description |
---|---|
Chemical Resistance | Withstands acids and alkalis, ideal for chemical storage. |
Low Water Absorption | Maintains integrity in humid conditions. |
Electrical Insulation | Suitable for electrical components. |
Application Scenarios of Polyethylene
The versatility of polyethylene extends to a variety of applications. It’s commonly used in making plastic films for packaging due to its flexibility and strength. In injection molding, polyethylene can be crafted into various daily necessities such as plastic basins and buckets.
Moreover, the production of pipes and containers benefits from polyethylene’s durability and resistance to environmental stress cracking. This ensures long-lasting performance even in challenging conditions.
Economic Benefits of Using Polyethylene
Cost-effectiveness is another reason why manufacturers prefer polyethylene. Its relatively low production cost compared to other plastics like polycarbonate or ABS makes it an attractive option for large-scale manufacturing processes.
Furthermore, its recyclability contributes to sustainable manufacturing practices. By choosing polyethylene, companies can reduce material waste and lower production expenses, aligning with eco-friendly goals.
In conclusion, the advantages of using polyethylene in injection molding are extensive, offering practical solutions for numerous industrial and consumer applications. Its unique properties not only enhance product quality but also support efficient and sustainable manufacturing processes. For further insights into how polyethylene compares with other plastics, exploring industry case studies can be beneficial.
Polyethylene is highly resistant to acids and alkalis.True
Polyethylene withstands most acids and alkalis, ideal for chemical storage.
Polyethylene absorbs high amounts of moisture.False
Polyethylene has low water absorption, maintaining integrity in moist environments.
How Does Polypropylene Compare to Other Plastics for Injection Molding?
Polypropylene’s unique properties make it a standout choice in the world of injection molding.
Polypropylene (PP) is favored for its low density, excellent heat resistance, and superior strength compared to other plastics, making it ideal for automotive, home appliances, and consumer goods.
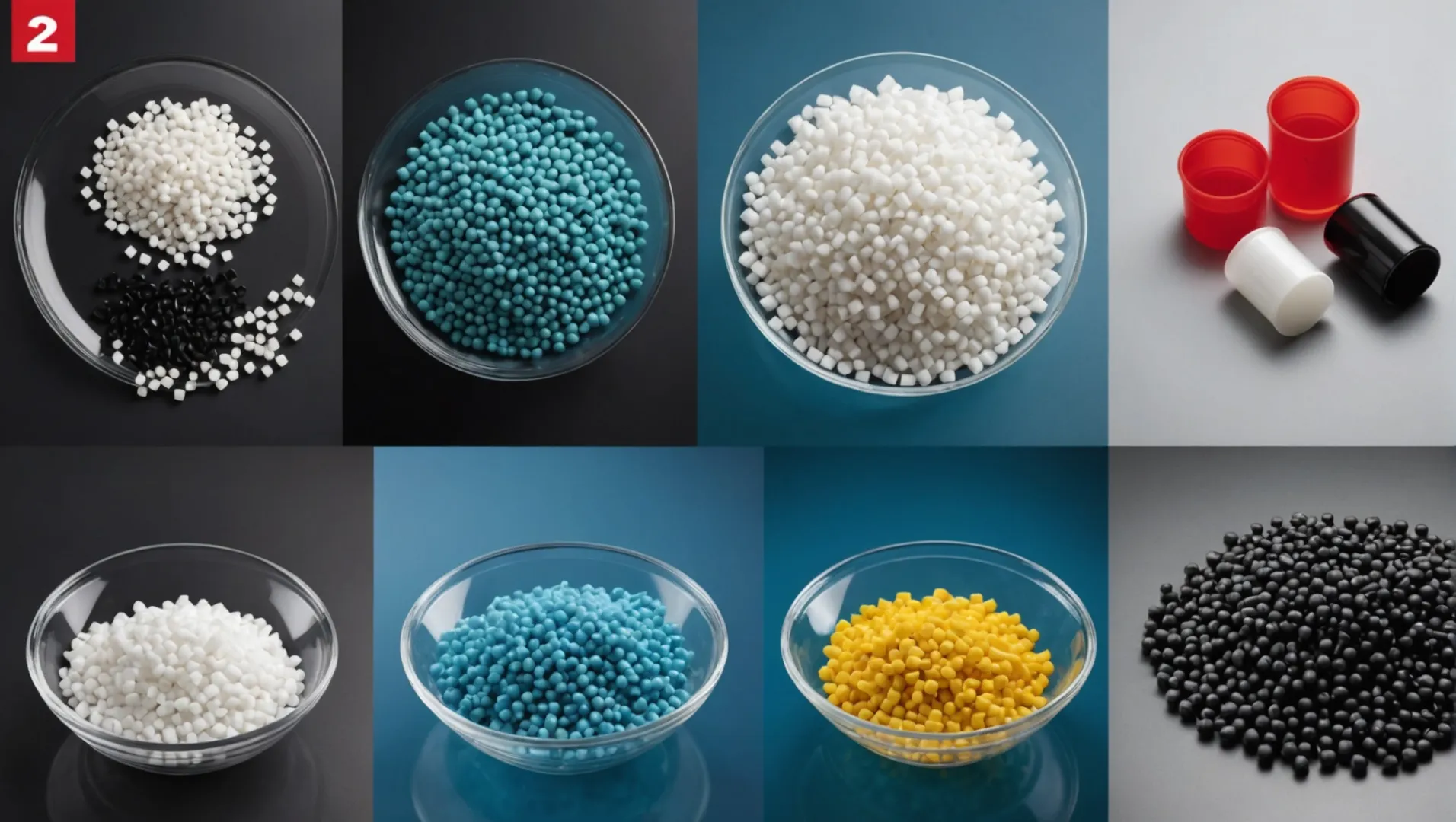
Comparing Polypropylene to Polyethylene
Polypropylene (PP) stands out for its low relative density, making it one of the lightest plastics available. It boasts impressive heat resistance, maintaining its form at temperatures up to 150°C. This makes PP particularly suitable for products exposed to high heat environments, such as automotive components and kitchenware.
In contrast, Polyethylene (PE) is valued for its excellent chemical stability and resistance to low temperatures. Its versatility makes it suitable for items like containers and films, but it lacks the heat resistance and strength of polypropylene.
Polypropylene Versus Polyvinyl Chloride
While Polyvinyl Chloride (PVC) is known for its cost-effectiveness and flame retardancy, it releases harmful substances at high temperatures, limiting its application in certain industries. Polypropylene, however, does not have these limitations and is often preferred in scenarios where higher temperatures and environmental safety are concerns.
Comparing with Polystyrene and ABS Plastic
Polystyrene (PS) is appreciated for its clarity and insulating properties. However, its brittleness limits its use in more durable applications. Polypropylene, with its superior strength and rigidity, is chosen over PS for products requiring a longer lifecycle or more robust performance.
ABS plastic, renowned for its toughness and heat resistance, competes closely with PP in sectors like automotive and electronics. Yet, the lightweight nature of polypropylene often gives it an edge in applications where weight reduction is crucial.
Polycarbonate and Polyamide Considerations
Polycarbonate (PC) offers high impact resistance and transparency, ideal for optical instruments and helmets. However, PP remains a more cost-effective choice for many consumer goods due to its adequate strength and lower price point.
Polyamide (PA), or nylon, is highly durable with excellent wear resistance. While suitable for mechanical parts like gears, polypropylene’s lower cost and ease of processing often make it more attractive for consumer goods.
Plastic Type | Key Features | Common Uses |
---|---|---|
Polyethylene | Chemical stability, low temperature resistance | Containers, films |
Polyvinyl Chloride | Cost-effective, flame retardant | Building materials |
Polystyrene | Clarity, insulation | Toys, packaging |
ABS Plastic | Toughness, heat resistance | Automotive parts |
Polycarbonate | Impact resistance | Helmets, optics |
Polyamide | Durability, wear resistance | Mechanical parts |
By understanding these differences, manufacturers can make informed decisions on whether polypropylene or another plastic better suits their specific application needs2.
Polypropylene is lighter than polyethylene.True
Polypropylene has a lower relative density than polyethylene.
Polyvinyl chloride is safer at high temperatures than polypropylene.False
PVC releases harmful substances at high temperatures, unlike polypropylene.
Why Is ABS Plastic Popular in the Automotive Industry?
ABS plastic is a top choice in automotive manufacturing due to its superior qualities.
ABS plastic is favored in the automotive industry for its high strength, toughness, and heat resistance, making it ideal for components like car dashboards and trims. Its easy processing and surface hardness further enhance its suitability for various applications.
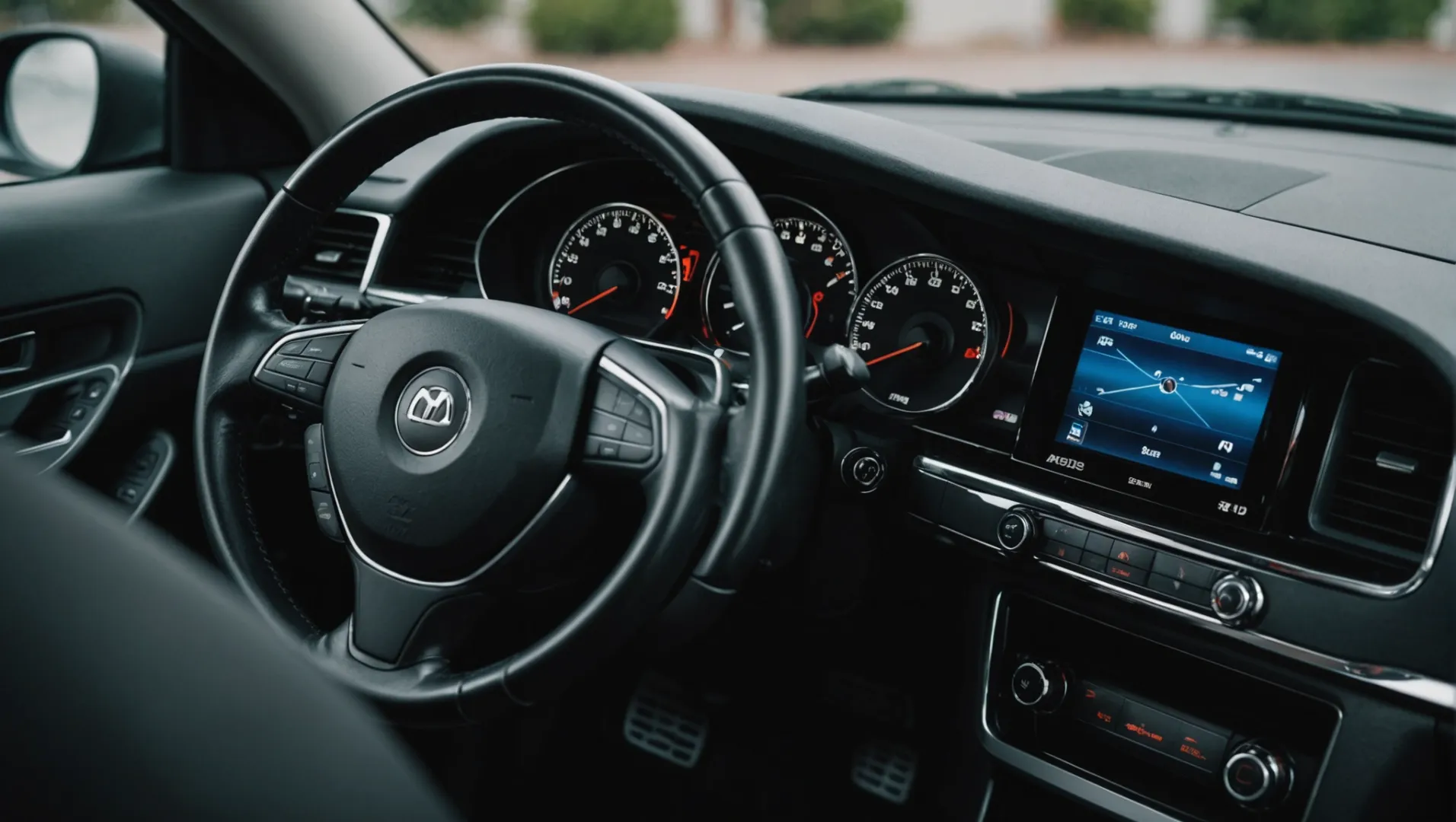
The Versatile Nature of ABS Plastic
ABS (Acrylonitrile Butadiene Styrene) is celebrated in the automotive sector for its exceptional combination of properties3. It balances strength and flexibility, ensuring that automotive components can withstand regular wear and tear while maintaining their structural integrity. Additionally, its high surface hardness makes it resistant to scratches and dents, a crucial factor for parts frequently in contact with drivers and passengers.
Resistance to Heat and Chemicals
In the automotive environment, components must endure temperature fluctuations and exposure to various chemicals. ABS plastic excels here due to its inherent heat resistance, preventing deformation or damage even under extreme conditions. This property ensures reliability and longevity for car interiors exposed to sunlight or heat emanating from engines.
Ease of Processing and Finishing
ABS plastic is straightforward to mold and shape, allowing manufacturers to produce complex components efficiently. Its ability to be painted easily means it can seamlessly blend with other materials or match specific interior designs. This flexibility in design and finishing is pivotal in the ever-evolving automotive industry where aesthetics play a significant role.
Comparative Analysis with Other Plastics
Plastic Type | Heat Resistance | Toughness | Ease of Processing |
---|---|---|---|
Polypropylene (PP) | Good | Moderate | Moderate |
Polycarbonate (PC) | Excellent | High | Difficult |
ABS | Very Good | High | Easy |
Compared to other plastics like polypropylene4 and polycarbonate, ABS stands out for its balance of desirable attributes without compromising on processing ease or cost-effectiveness.
Application Scenarios
ABS plastic is utilized extensively in the automotive industry, notably for components such as car dashboards, trims, and interior panels5. Its ability to mimic more expensive materials while providing excellent durability makes it a cost-effective solution for high-quality vehicle interiors.
ABS plastic is highly resistant to heat.True
ABS's heat resistance makes it ideal for automotive components exposed to high temperatures.
ABS plastic is difficult to process and shape.False
ABS is easy to mold and shape, facilitating the production of complex automotive parts.
What Should Be Considered When Choosing Plastic for Injection Molding?
Selecting the optimal plastic for injection molding is crucial to ensure product performance and cost efficiency.
When choosing plastic for injection molding, consider factors like mechanical properties, thermal stability, chemical resistance, and cost. These elements determine the suitability of plastics like PE, PP, PVC, PS, ABS, PC, and PA for different applications.

Mechanical Properties
The mechanical properties of plastic significantly influence its applicability in injection molding. For instance, Polycarbonate6 (PC) is favored for its high strength and impact resistance, making it ideal for protective gear. Conversely, Polystyrene7 (PS) offers excellent rigidity but is brittle, restricting its use to non-load-bearing applications.
Thermal Stability
Thermal stability determines a plastic’s ability to withstand heat without deforming. Polypropylene8 (PP) stands out with its capability to endure temperatures up to 150°C, making it suitable for automotive and kitchenware applications.
Chemical Resistance
Chemical resistance is vital in environments exposed to corrosive substances. Polyethylene9 (PE) is known for its resistance to acids and alkalis, commonly used in containers and piping systems.
Cost Considerations
Budget constraints often guide material selection. Polyvinyl Chloride10 (PVC) offers a cost-effective solution with good processing performance and flame retardancy but comes with limitations in food-related applications due to potential harmful emissions.
Plastic Type | Key Features | Common Applications |
---|---|---|
PE | Low water absorption, chemical stable | Films, containers, pipes |
PP | Low density, heat resistant | Automotive interiors, electrical housings |
PVC | Corrosion resistant, affordable | Building materials, cable ducts |
PS | Transparent, good insulation | Electrical housings, toys |
ABS | High strength, easy to process | Automotive parts, electronics housings |
PC | High impact resistance, transparent | Optical instruments, helmets |
PA | Wear resistant, good mechanical properties | Machinery parts, textiles |
Evaluating these factors ensures a strategic approach to selecting the most suitable plastic for your injection molding needs.
Polycarbonate is ideal for protective gear due to high strength.True
Polycarbonate's high impact resistance makes it suitable for safety equipment.
PVC is commonly used in food-related applications.False
PVC can emit harmful substances, limiting its use in food applications.
Conclusion
Understanding the unique properties of each plastic helps you make informed choices in injection molding, ensuring optimal performance and cost-effectiveness.
-
Discover how polyethylene resists acids and alkalis effectively.: Certain types of chemicals are absorbed to varying degrees by poly- ethylene causing swelling, weight-gain, softening and some loss of yield strength. These … ↩
-
Discover how polypropylene’s properties enhance injection molding efficiency.: Key Benefits: PP is resistant to moisture absorption, and has a very slippery surface that makes it a good substitute for other plastics in a variety of low- … ↩
-
Learn how ABS’s properties benefit automotive design.: ABS can be easily moulded, sanded and shaped, while its glossy surface finish is highly compatible with a wider range of paints and glues. ABS plastics takes … ↩
-
Compare polypropylene and ABS for automotive uses.: The PP bumpers are more soft and better at impacts, but will not match up. There are ABS bumpers that are made in China that use recycled … ↩
-
Explore how ABS is used in car interiors.: It’s used to make temporary signs, and for panels by trimmers. Lighter than solid panels, nearly as rigid, but you can form it cold if needed. ↩
-
Explore how polycarbonate enhances product durability.: Some of the benefits of this technology include lower tool cost, lower material cost as well as more part consolidation. Water assist molding polycarbonate also … ↩
-
Learn about the advantages and limitations of polystyrene.: Polystyrene is used in a wide range of applications because this injection molding material is lightweight, relatively inexpensive, and moisture resistant. ↩
-
Discover why polypropylene suits high-temperature environments.: This thermoplastic has a melting point that typically ranges between 160°C to 170°C, although this can vary based on the specific type of … ↩
-
Understand how polyethylene withstands harsh chemicals.: These raw materials have out- standing resistance to both physical and chemical attack. The following chart should be used as a guide for evaluating the … ↩
-
Find out how PVC offers budget-friendly solutions.: It can produce highly efficient, durable and complex parts with high precision and cost-effectiveness. Due to its massive benefits, PVC plastic injection … ↩