Choosing the right plastic for injection molding is not just a technical decision; it’s an opportunity to enhance your product’s success!
Common plastics suitable for injection molding include Polyethylene (PE), Polypropylene (PP), Polyvinyl Chloride (PVC), Polystyrene (PS), ABS, and Polycarbonate (PC). Each offers unique properties like strength, heat resistance, and flexibility, making them ideal for specific applications.
Let’s delve deeper into each type of plastic to uncover their distinct characteristics and see which aligns best with your project needs.
Polycarbonate is used for optical lenses.True
Polycarbonate's high strength and transparency make it ideal for lenses.
- 1. What Are the Key Properties to Consider When Selecting Plastics for Injection Molding?
- 2. How Do Different Plastics Impact the Cost-Effectiveness of Injection Molding?
- 3. Which Industries Benefit Most from Specific Plastics in Injection Molding?
- 4. How Can Material Selection Influence Product Longevity and Sustainability?
- 5. Conclusion
What Are the Key Properties to Consider When Selecting Plastics for Injection Molding?
Selecting the right plastic for injection molding is essential to meet specific product requirements and enhance performance.
Key properties to consider include strength, thermal stability, chemical resistance, and electrical insulation. These factors influence the performance and suitability of plastics like PE, PP, PVC, PS, ABS, and PC for various applications.
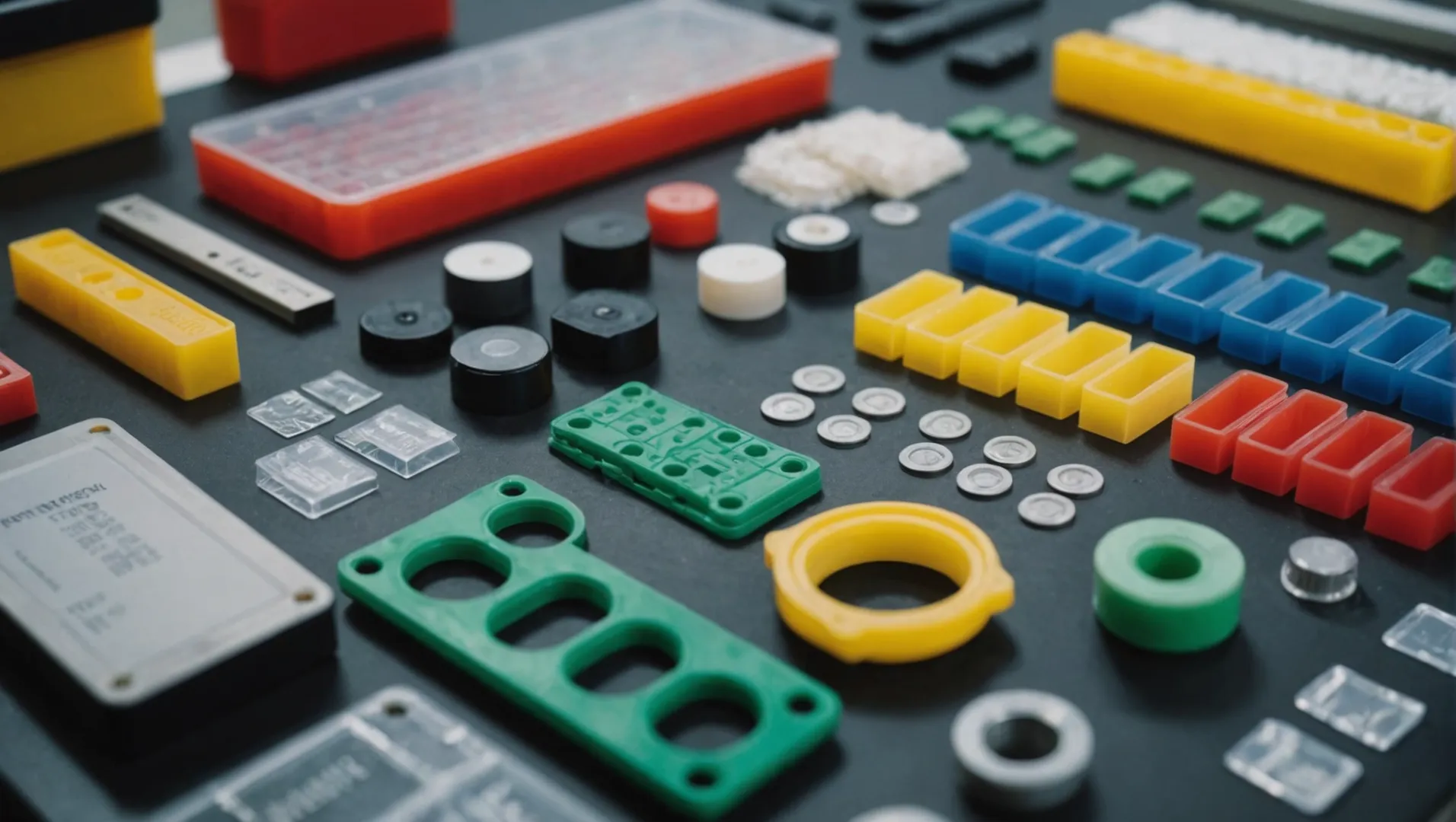
Understanding Plastic Properties
When choosing a plastic for injection molding, understanding the inherent properties of each material is crucial. These properties dictate how the plastic will perform under different conditions and ultimately influence the choice of material for your specific application.
-
Strength and Durability: Evaluate the mechanical strength required for your product. For instance, Polycarbonate’s high strength1 makes it ideal for optical lenses and bulletproof glass. Conversely, Polystyrene’s brittleness2 limits its use to less demanding applications like toys and packaging.
-
Thermal Stability: Consider how temperature fluctuations might affect the material. Polypropylene (PP)3 offers excellent heat resistance, making it suitable for car parts exposed to heat. In contrast, PVC‘s poor thermal stability4 requires careful temperature management during processing.
-
Chemical Resistance: Some environments expose products to chemicals. Polyethylene’s chemical stability5 makes it resistant to acids and alkalis, ideal for containers and pipes. However, ensure your material choice matches the specific chemicals it will encounter.
-
Electrical Insulation: If the product will carry electricity or be near electrical sources, choose materials like ABS6, known for their excellent electrical insulation properties.
Analyzing Application Scenarios
Different plastics are better suited for specific applications due to their unique properties:
Plastic Type | Application Examples |
---|---|
PE | Plastic bags, bottles, barrels |
PP | Automotive parts, appliance housings |
PVC | Pipes, wire insulation |
PS | Electrical housings, toys |
ABS | Electronic casings, automotive interiors |
PC | Optical lenses, bulletproof glass |
Understanding how these materials function in real-world scenarios helps in aligning them with your project’s needs.
- Flexibility and Processing Ease: Consider the flexibility and ease of processing required. ABS‘s ease of shaping7 makes it versatile for various manufacturing processes like electroplating.
Exploring these factors ensures that you select the most suitable plastic for your injection molding project, balancing performance, cost-effectiveness, and sustainability.
Polycarbonate is ideal for optical lenses due to strength.True
Polycarbonate's high strength and durability make it suitable for optical lenses.
PVC has excellent thermal stability for high-heat applications.False
PVC has poor thermal stability, needing careful temperature management.
How Do Different Plastics Impact the Cost-Effectiveness of Injection Molding?
Selecting the right plastic can dramatically influence the cost-effectiveness of injection molding.
The cost-effectiveness of injection molding is heavily influenced by the type of plastic used. Each plastic—like PE, PP, PVC, PS, ABS, and PC—has distinct properties affecting material costs, processing time, and waste. Choosing the right plastic can optimize manufacturing efficiency and reduce overall costs.
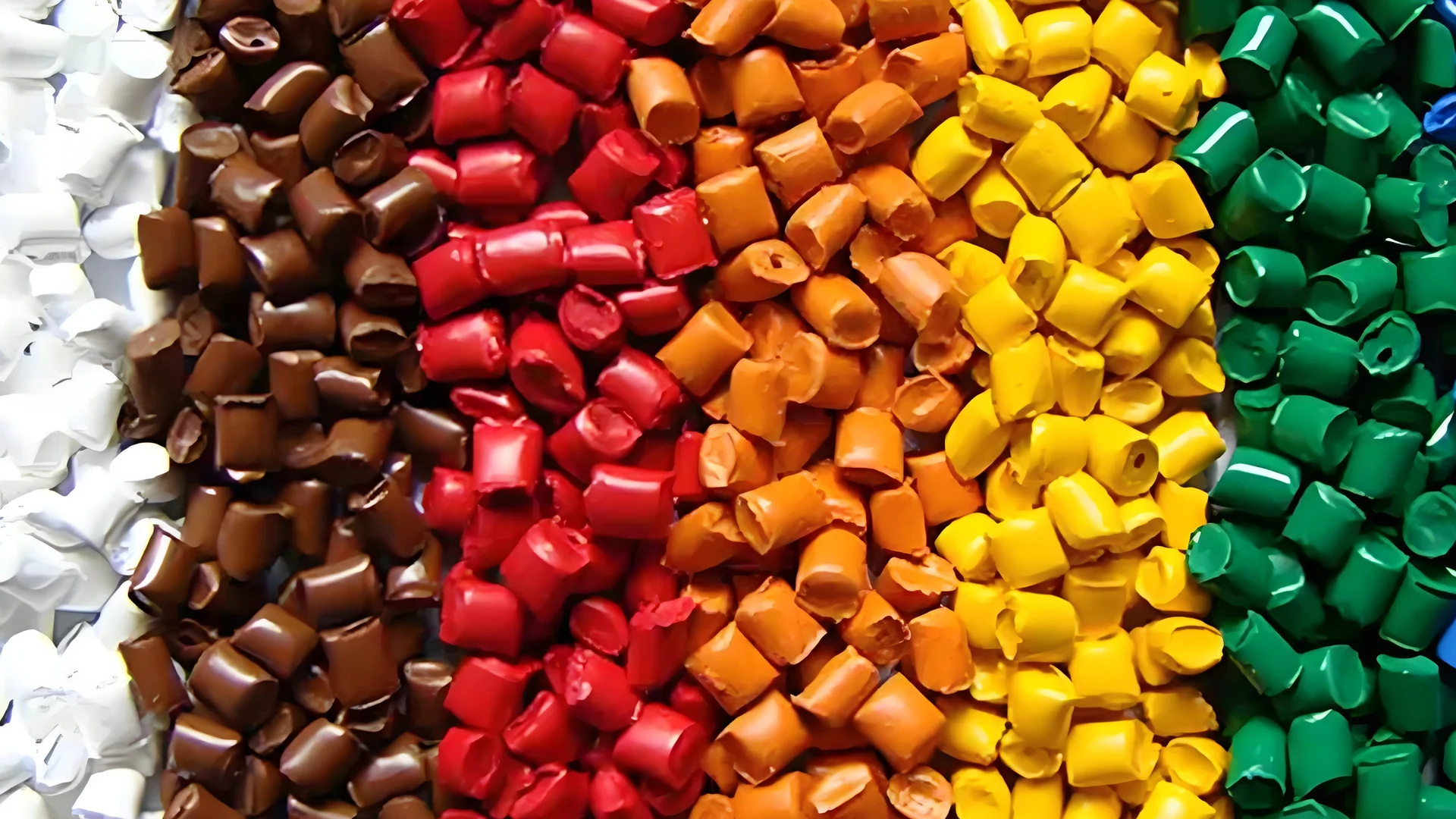
Understanding Material Costs
The choice of plastic significantly affects the material costs in injection molding.
- Polyethylene (PE) is generally affordable and offers low water absorption, reducing drying time and costs.
- Polypropylene (PP) provides a balance of cost and performance, with better strength and stiffness than PE, making it cost-effective for applications requiring durability.
Comparing Material Costs
Plastic Type | Average Cost (per kg) | Key Benefits |
---|---|---|
PE | $1.20 – $1.50 | Low cost, flexible |
PP | $1.50 – $1.80 | Durable, lightweight |
PVC | $1.00 – $1.20 | Strong, corrosion-resistant |
PS | $1.50 – $2.00 | Transparent, rigid |
ABS | $1.80 – $2.20 | Tough, versatile |
PC | $2.50 – $3.00 | High impact resistance |
Processing Efficiency
Processing efficiency involves cycle times and energy consumption.
- PVC has a longer cycle time due to its poor thermal stability, which might increase costs.
- PS, being brittle, requires careful handling but offers good optical properties.
Waste Management and Sustainability
The choice of plastic impacts waste generation and recycling opportunities.
- ABS is recyclable but generates more waste during the trimming process.
- PC is less prone to waste due to its high strength and dimensional stability.
For detailed comparisons of these plastics’ characteristics, consider exploring various plastic properties for injection molding8 to ensure optimal material selection.
Industry-Specific Impacts
Different industries benefit from specific plastics:
- Automotive industry: Prefers PP and PC for lightweight yet durable components.
- Consumer goods: Often utilize ABS for its toughness and gloss finish.
Understanding these specific applications helps in aligning material choice with industry needs and reducing costs through targeted material use.
PVC has the lowest average cost per kg among listed plastics.True
PVC costs $1.00 - $1.20 per kg, lower than other plastics.
ABS is less recyclable than other plastics used in injection molding.False
ABS is recyclable but generates more waste during trimming.
Which Industries Benefit Most from Specific Plastics in Injection Molding?
Industries thrive on the versatility of plastics in injection molding to optimize their production processes.
Industries like automotive, electronics, packaging, and healthcare benefit immensely from specific plastics used in injection molding due to their tailored properties that enhance product performance and cost-efficiency.

Automotive Industry
The automotive industry extensively uses Polypropylene (PP)9 for its lightweight and durable properties. PP is integral in manufacturing car bumpers, dashboards, and interior components due to its heat resistance and insulation properties. Similarly, ABS plastic10 offers high impact resistance and toughness, making it suitable for both exterior and interior automotive parts.
Electronics Sector
In the electronics sector, Polycarbonate (PC)11 is favored for its high strength and excellent electrical insulation. These properties are crucial for the safe housing of electronic components. Similarly, Polystyrene (PS)12, with its good optical properties, is used in producing clear casings for electronic devices.
Packaging Industry
The packaging industry benefits greatly from Polyethylene (PE)13 due to its low water absorption and chemical stability. These features make PE ideal for creating films, bags, and containers that protect products from moisture and contaminants.
Plastic Type | Key Properties | Common Applications |
---|---|---|
PE | Low water absorption, chemical stability | Films, bags, containers |
PP | Low density, high heat resistance | Car parts, appliance housings |
PVC | Mechanical strength, chemical resistance | Pipes, cable insulation |
PS | Optical clarity, electrical insulation | Casings, toys |
ABS | Impact resistance, high gloss finish | Automotive interiors, electronic housings |
PC | High toughness, dimensional stability | Optical lenses, safety equipment |
Healthcare Applications
In healthcare, Polyvinyl Chloride (PVC)14 is widely used due to its chemical resistance and flexibility. It’s a material of choice for making medical tubing and containers. The ability of PVC to withstand sterilization processes without degradation is a significant advantage.
Industries selecting the right plastic enhance product longevity while optimizing manufacturing efficiency. The distinct characteristics of each plastic type drive innovations across sectors by providing tailored solutions for specific needs.
Polypropylene is used in car dashboards for heat resistance.True
PP's heat resistance and insulation make it ideal for dashboards.
Polystyrene is commonly used for medical tubing due to flexibility.False
PVC, not PS, is used for medical tubing due to flexibility.
How Can Material Selection Influence Product Longevity and Sustainability?
Selecting the right materials is crucial for enhancing product durability and reducing environmental impact.
Material selection directly influences both the longevity and sustainability of products by determining their durability, recyclability, and overall environmental footprint. Choosing materials with high resistance to wear and tear extends product life, while sustainable options like biodegradable or recyclable plastics reduce ecological impact.
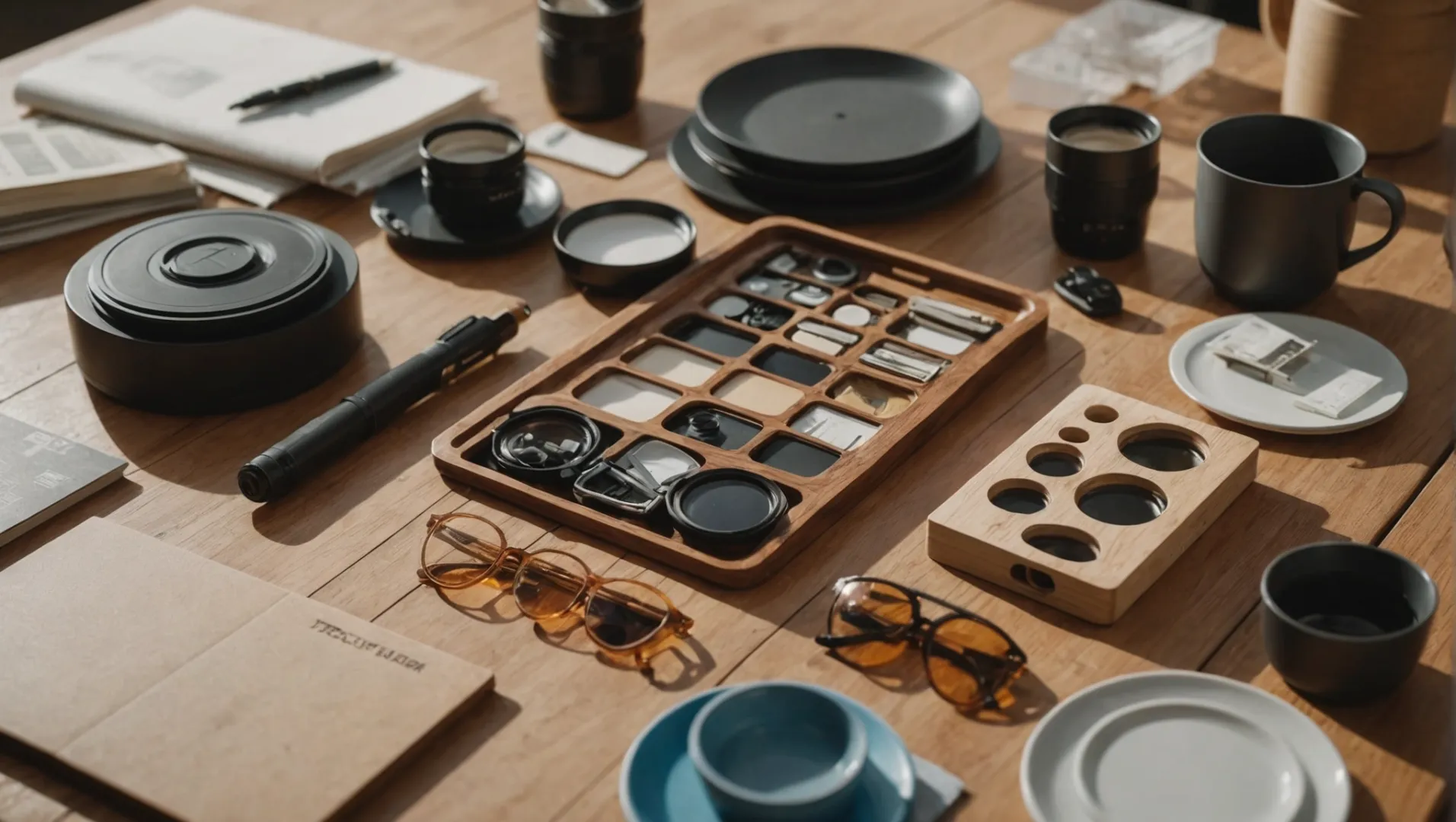
The Role of Material Durability in Product Longevity
When choosing materials for product design, particularly in injection molding processes15, durability is a key consideration. For instance, Polyethylene (PE) is known for its excellent chemical stability and low water absorption, which contribute to its longevity in applications like containers and pipes. Similarly, Polycarbonate (PC) offers high strength and toughness, making it ideal for products that require long-lasting resilience such as optical lenses and bulletproof glass.
Sustainability Through Recyclability and Biodegradability
Sustainability in material selection is not solely about reducing environmental footprint but also ensuring the materials can either be recycled or are biodegradable. Polypropylene (PP) and ABS plastic, for example, can be recycled, which reduces waste and supports a circular economy. This makes them suitable for industries that prioritize sustainability without compromising on performance.
Balancing Cost and Environmental Impact
While opting for sustainable materials can sometimes lead to higher initial costs, the long-term benefits of reduced environmental impact and potential regulatory incentives can offset these expenses. Industries are increasingly opting for materials like bio-based plastics or those with lower carbon footprints to align with sustainability goals16. The automotive industry, for instance, benefits from using materials like PP due to its light weight and recyclability, which improves fuel efficiency and reduces emissions.
Case Studies: Industry Applications
In the electronics industry, ABS plastic is favored due to its comprehensive performance features, such as high strength and ease of processing. Its ability to be electroplated also enhances product aesthetics without sacrificing environmental considerations. On the other hand, the use of PVC in plumbing showcases its excellent mechanical properties and chemical resistance, crucial for long-lasting installations. However, care must be taken due to PVC‘s potential for toxic emissions when improperly disposed of.
Understanding these aspects can guide manufacturers in selecting materials that not only meet their design specifications but also contribute positively to sustainability efforts. By prioritizing durability and recyclability, companies can create products that support longer lifespans and align with eco-friendly practices.
Polyethylene has low water absorption properties.True
Polyethylene's low water absorption enhances its longevity in applications.
PVC is fully biodegradable and environmentally safe.False
PVC is not biodegradable and can emit toxins if improperly disposed.
Conclusion
Selecting the right plastic is key to maximizing performance and efficiency in injection molding. Evaluate your project’s requirements to choose the ideal material and enhance your manufacturing outcomes.
-
Learn about Polycarbonate’s high strength and durability features.: The main reason for polycarbonate’s high strength is its robust and solid chemical structure. For one, its molecules possess strong bonds in high numbers, … ↩
-
Understand Polystyrene’s brittleness and its impact on applications.: Steric hindrance is the short answer. But it depends on a property of polymer chain architecture called tacticity. ↩
-
Explore how Polypropylene withstands high temperatures effectively.: Its unique properties, such as its impressive polypropylene heat resistance, durability, and mechanical strength, make it a favorite in various … ↩
-
Discover why PVC has poor thermal stability.: According to López et al. (2011), the main mass loss of PVC was between 250 and 320 °C, depending on the material and the stabilizers and additives. ↩
-
Find out how Polyethylene resists acids and alkalis.: These raw materials have out- standing resistance to both physical and chemical attack. The following chart should be used as a guide for evaluating the … ↩
-
See why ABS is great for electrical applications.: Electrical Properties of ABS ; Arc Resistance, 60 – 120 sec ; Dielectric Constant, 2.7 – 3.2 ; Dielectric Strength, 15.7 – 34 kV/mm ; Dissipation Factor, 50 – 190 x … ↩
-
Learn why ABS is favored for its processing versatility.: 99% of people can get there abs showing – it just takes dedication and alot of discipline. It’s not a quick ride. ↩
-
Explore detailed properties of each plastic for informed material choices.: These are the most common plastic materials for injection molding: acrylic (PMMA); acrylonitrile butadiene styrene (ABS); nylon (polyamide, PA) … ↩
-
Discover how PP enhances durability and safety in car manufacturing.: In the automotive industry, PP’s commonly used for bumpers, chemical tanks, cable insulation, and gas cans. Polypropylene is also often utilized … ↩
-
Learn why ABS is crucial for robust automotive components.: Advantages of ABS. Impact resistance: ABS plastic is known for its excellent impact resistance, making it suitable for applications that require durability … ↩
-
Understand PC’s role in ensuring electronics’ safety and efficiency.: Polycarbonate plastic is widely used for its transparency and impact-resistance, making it a great lightweight choice for key industries. ↩
-
Explore PS’s effectiveness in clear electronic casings.: Polystyrene is used in different forms, including as foam, film, and rigid plastic, for applications from food packaging to electronics protection. ↩
-
See how PE revolutionizes moisture-resistant packaging solutions.: One of the most common uses for polyethylene bundling film is for wrapping water bottles and canned goods. The polyethylene bundling film is … ↩
-
Uncover PVC’s importance in safe and flexible medical tools.: For example, within a hospital it may be used in water and drainage pipes and in fire resistant cabling in electrical and telecommunications equipment. Vinyl in … ↩
-
Explore how injection molding enhances material strength and product lifespan.: The material from which a mold is made is a key factor influencing its durability. Different materials offer varying degrees of hardness, wear … ↩
-
Discover standards that guide eco-friendly material selection in industries.: ASTM standards on sustainability and sustainable development address environmental and economic concerns in buildings and construction. ↩