Have you ever felt confused by the different types of injection molding machines? You’re not alone. Many people share this feeling. Let’s explore these interesting machines together.
Injection molding machines fall into groups based on how they look, their power source, how they melt plastic and how they clamp molds. Understanding these categories is very important. This knowledge helps you pick the right machine for your manufacturing needs.
While exploring the world of product design, I quickly saw that knowing injection molding machines is very important. Each type has a unique charm and quirks. They meet different manufacturing needs. Choosing the right one really improves efficiency and product quality. This choice is crucial. Designing sleek consumer electronics or robust components requires understanding these machines’ details. This knowledge strengthens confidence in decisions during the design process. Let’s look closer at each category and see how they match our creative visions.
Injection molding machines can be categorized by appearance.True
Injection molding machines are classified based on various factors, including their appearance, which affects their design and functionality.
All injection molding machines use the same power source.False
Injection molding machines can differ in power sources, including hydraulic, electric, and hybrid options, catering to different manufacturing needs.
- 1. What makes hydraulic injection molding machines so advantageous?
- 2. How do electric injection molding machines compare to hydraulic ones?
- 3. What should I consider when choosing an injection molding machine?
- 4. How Do Plasticization Methods Influence Injection Molding?
- 5. How does the mold clamping method truly influence production efficiency?
- 6. Conclusion
What makes hydraulic injection molding machines so advantageous?
Have you ever thought about what makes hydraulic injection molding machines unique in manufacturing? I did too. I discovered that they play a very important role in creating our daily products. They shape items we use every day.
Hydraulic injection molding machines offer important benefits. They provide strong clamping force for better product quality. Each cycle is precise, allowing for complex designs. These machines work well with different materials. They save money due to energy efficiency. Production is very fast. These features are ideal for many manufacturing purposes.
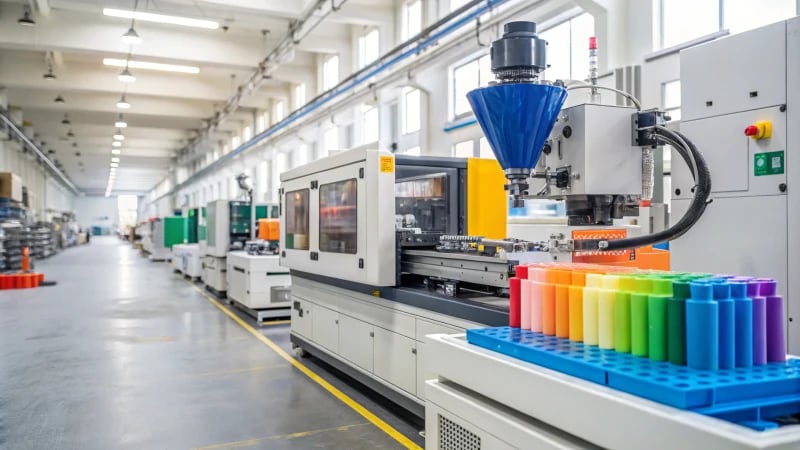
Hydraulic injection molding machines really fascinate me. They interest me not just for their mechanics but because they deeply impact production speed and product quality. When I entered the manufacturing industry, I was amazed. These machines transform raw materials into complex shapes with precision and speed. Let’s look into some key advantages that make hydraulic machines unique.
High Clamping Force
First thing I noticed about hydraulic machines was their incredible clamping force. Imagine holding a mold together while injecting material under high pressure. That’s when hydraulic systems excel. This force is crucial for keeping mold integrity. It affects the quality of the final product.
- Pressure Control: Hydraulic systems easily manage pressure. They keep output consistent, like a steady hand guiding a delicate brush.
- Product Quality: Clamping force impacts surface finish and dimensional accuracy. It’s like creating fine art; every detail matters!
For more insights, check out this article on clamping force benefits1.
Precision and Repeatability
I value accuracy in design, so precision in manufacturing is crucial. Hydraulic injection molding offers very precise results in every cycle. Control over speed and pressure allows for accurate injections. This is especially important for complex designs.
Feature | Hydraulic Injection Molding | Other Types |
---|---|---|
Precision | High | Moderate to Low |
Repeatability | Excellent | Varies |
Setup Complexity | Moderate | High |
Versatility
I work on many projects needing different materials and designs. Hydraulic machines excel here. They tackle various materials, especially high-viscosity ones needing strong pressure.
- Material Compatibility: Machines handle diverse thermoplastics and elastomers really well.
- Mold Design Flexibility: Complex geometries or multi-cavity molds fit effortlessly in hydraulic machines.
For a deeper dive into material handling, visit material compatibility insights2.
Cost-Effectiveness
Let’s discuss costs. I thought hydraulic injection molding machines were pricey. But I realized they save money in the long run. Initial investment might be higher; however, they lead to lower operational costs over time because of:
- Energy Efficiency: Modern hydraulic systems use less energy impressively.
- Long Lifespan: Strong construction means fewer replacements and repairs. This is probably a good deal.
Speed of Production
Speed is vital in our fast-paced world. Hydraulic machines offer quick operation cycles. Quick injection and cooling times mean more productivity. When facing deadlines, I am grateful for their ability to keep pace with high demand.
- Cycle Times: Typically faster than electric machines, hydraulics ensure high throughput.
- Automation Potential: Including hydraulic machines in automated production lines boosts overall efficiency.
To understand more about speed advantages, refer to production speed analysis3.
Hydraulic machines provide high clamping force for better quality.True
The significant clamping force ensures mold integrity, enhancing product quality through better control during injection.
Hydraulic injection molding is less precise than electric machines.False
Hydraulic systems deliver high precision and repeatability, outperforming electric machines in accuracy during the injection process.
How do electric injection molding machines compare to hydraulic ones?
Do you ever ask how electric injection molding machines compare to hydraulic ones? Many people in manufacturing think about this. Production technology can be really complex.
Electric injection molding machines usually provide greater precision and energy efficiency compared to hydraulic machines. Hydraulic machines might have lower starting costs. However, electric models likely save more money over time due to lower operating expenses. Electric machines really contribute to long-term savings.
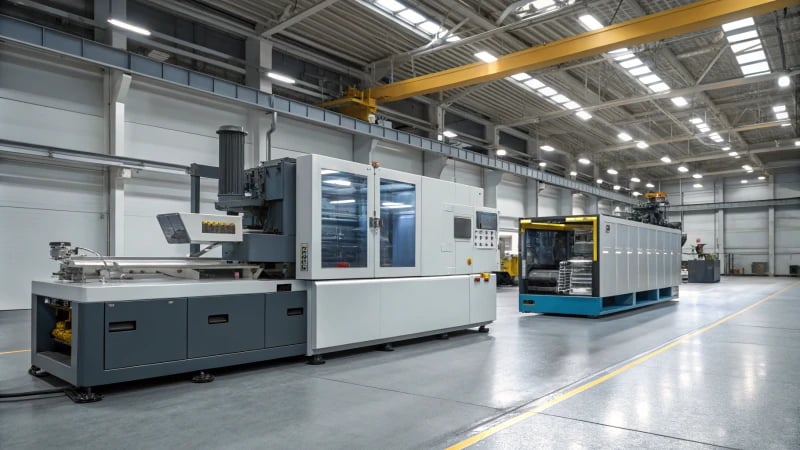
Efficiency and Energy Consumption
When I first joined the industry, I felt amazed by the different worlds of electric and hydraulic injection molding machines. Each type has unique strengths and challenges that influence the manufacturing process. Let’s explore this interesting comparison!
Electric injection molding machines utilize servo motors for operation, which leads to significant energy savings compared to hydraulic machines. The efficiency of electric machines can reach up to 70% higher energy savings, as they only draw power when needed. This can drastically lower operational costs in the long run.
In contrast, hydraulic machines are less efficient because they constantly consume energy, even when idle. This continuous operation can lead to higher electricity bills, especially in high-production environments. You can learn more about the impact of energy consumption on overall manufacturing costs in this detailed guide4.
Precision and Control
Now, let’s talk about precision. Electric machines shine here! One of the standout features of electric injection molding machines is their superior precision. The servo motors allow for accurate positioning and control of the injection process, leading to better part quality and reduced scrap rates. This is particularly advantageous in industries where tolerances are critical, such as in consumer electronics.
Hydraulic machines, while powerful, can exhibit variations in speed and pressure due to their reliance on hydraulic fluid. This can sometimes result in less consistent part quality. For a deeper dive into how precision affects product quality, check out this resource.
Cost Considerations
Cost is a big factor in making decisions. When it comes to initial investment, hydraulic injection molding machines generally have a lower upfront cost compared to their electric counterparts. However, it’s essential to consider the total cost of ownership. While electric machines may be pricier initially, their energy efficiency and lower maintenance costs can lead to significant savings over time.
To give you a clearer picture, here’s a comparison table:
Feature | Electric Machines | Hydraulic Machines |
---|---|---|
Initial Cost | Higher | Lower |
Energy Efficiency | High (up to 70% savings) | Low (constant energy draw) |
Precision Control | Very precise | Moderate |
Maintenance Costs | Lower | Higher |
Ideal Applications | High precision needs | Large-scale production |
Environmental Impact
I care about sustainability, so the smaller environmental impact of electric machines really impresses me. Their energy use is lower, leading to less noise pollution and a smaller carbon footprint. It feels great to know that my choices help the environment.
Electric injection molding machines are often praised for their lower environmental footprint. With reduced energy consumption and less noise pollution during operation, they align well with sustainability goals.
In contrast, hydraulic systems often leak fluids if not maintained correctly; this poses environmental hazards if not maintained correctly. Additionally, their higher energy consumption contributes to a larger carbon footprint.
Summary of Key Differences
To sum up, choosing between electric or hydraulic machines depends on your specific needs. It’s important to consider efficiency, precision, cost and environmental impact before deciding.
In summary: while both electric and hydraulic injection molding machines have their advantages and disadvantages; factors such as efficiency,
costs,
and environmental impacts should be carefully weighed before making a decision.
If you’re interested in more detailed comparisons between different types of injection molding machines visit this comprehensive comparison page.
Electric injection molding machines are more energy efficient than hydraulic ones.True
Electric machines can save up to 70% energy compared to hydraulic machines, making them more efficient for operations.
Hydraulic injection molding machines have lower initial costs than electric models.True
Hydraulic machines typically require a lower upfront investment compared to electric injection molding machines, appealing for budget-conscious buyers.
What should I consider when choosing an injection molding machine?
Choosing the right injection molding machine involves more than numbers. Understanding production needs and securing quality is essential. Key factors play a significant role in your manufacturing journey.
Selecting an injection molding machine requires considering several factors. Start by looking at the shot size and tonnage. Platen size is also crucial. Decide between horizontal or vertical machines. Choose the type based on power source꞉ hydraulic, electric or pneumatic. Mold design must fit the machine. Think about production volume needs. Budget constraints are important too.
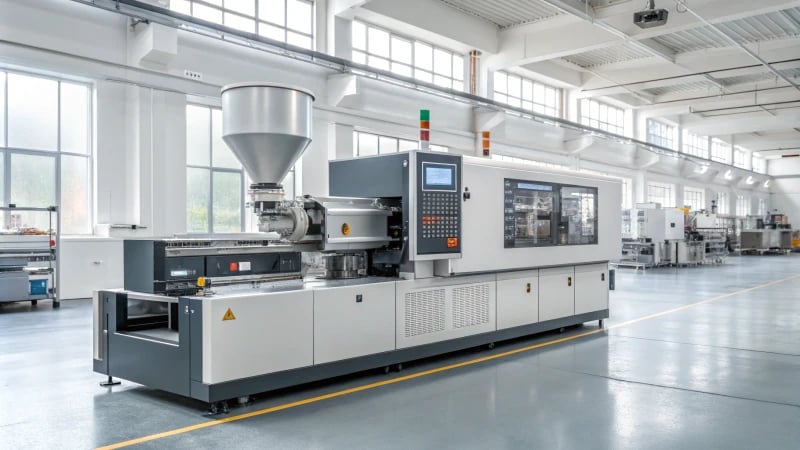
Understanding Injection Molding Machine Specifications
When selecting an injection molding machine, it is essential to understand the specifications that align with your production needs. Key specifications include:
- Shot Size: This is how much plastic the machine injects into a mold in one cycle. The right shot size really means the difference between a well-made product and a bad one. For instance, on a big consumer project, we chose a machine with a bigger shot size for better quality.
- Tonnage: This refers to the clamping force of the machine. Insufficient tonnage leads to poor-quality parts with issues like flash. In one of my projects, we did not consider this well and wasted a lot of material because the molds were not tight enough.
- Platen Size: It is crucial to match the platen size with your mold dimensions. I remember once we did not check this detail and misalignment caused costly damage and wasted time.
Machine Type Considerations
The type of injection molding machine significantly influences production capability and operational costs. Consider these types:
Type | Advantages | Disadvantages |
---|---|---|
Horizontal Injection | Easy operation, low center of gravity, suitable for automation | Takes up more space, mold installation can be tricky |
Vertical Injection | Smaller footprint, good for insert molding | Limited by gravity effects on mold alignment |
Electric Injection | Precise control, energy-efficient | Higher cost and limited for large machines |
Hydraulic Injection | Reliable and powerful clamping pressure | More maintenance required and energy-consuming |
Choosing between these types should align with your specific production goals and space availability.
Power Source Options
Another critical factor is the power source of the injection molding machine:
- Hydraulic Machines: These are popular for their strong clamping power. They are good for different applications but may increase operational costs due to high energy use.
- Electric Machines: Ideal for precision and energy saving. I often suggest them for tasks needing high accuracy. However, they might not work for applications needing stronger clamping forces.
- Pneumatic Machines: Ideal for lightweight items and low energy use. However, they might lack power for heavier manufacturing needs.
Other Factors to Consider
Apart from specifications and machine types, consider additional factors:
- Mold Design Compatibility: The machine must suit your mold design without lowering quality. I have faced problems when this was not considered, leading to design changes later.
- Production Volume Needs: It is really crucial to evaluate how many parts you need per cycle. In high-volume production, faster cycle times are very important.
- Budget Constraints: Include both initial cost and ongoing expenses. Sometimes, investing in advanced machines saves money in the long run, as I have learned from experience.
By considering these essential factors when choosing an injection molding machine, you prepare for success in increasing production efficiency and product quality.
Shot size is irrelevant when selecting an injection molding machine.False
The shot size is crucial as it determines the plastic volume per cycle, impacting product quality.
Electric injection machines are more energy-efficient than hydraulic ones.True
Electric machines offer superior energy efficiency compared to hydraulic machines, making them ideal for precision tasks.
How Do Plasticization Methods Influence Injection Molding?
Have you ever thought about how those detailed plastic parts we use each day are created? It all begins with the magical process of plasticization in injection molding. Let’s explore this exciting world together!
Plasticization methods in injection molding play a key role. These determine how raw plastics melt and get ready for shaping. This process directly influences the quality of production. It also impacts efficiency. Knowing these methods is very important for successful manufacturing. Understanding really matters!
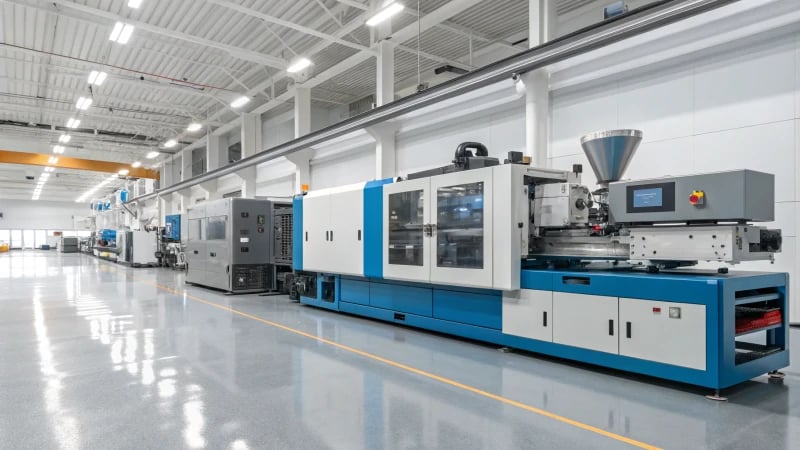
Understanding Plasticization in Injection Molding
Plasticization is a critical process in injection molding that transforms raw plastic materials into a molten state, making them suitable for shaping into complex designs. The effectiveness of this process largely depends on the chosen plasticization method, which directly influences the quality of the final product.
Types of Plasticization Methods
-
Plunger Plastic Injection Molding Machine
- Description: This method relies on a plunger to inject material but has poor mixing and plasticizing properties.
- Current Use: Rarely utilized in modern manufacturing due to its limitations.
- Advantages: Simple mechanism.
- Disadvantages: Requires additional devices for effective operation, leading to inefficiency.
-
Reciprocating Screw Plastic Injection Molding Machine
- Description: Utilizes a screw for both plasticization and injection, allowing for excellent mixing and plasticizing characteristics.
- Current Use: This is the most common method in the industry today due to its efficiency and effectiveness.
- Advantages: High control over the material’s properties and consistent quality.
- Disadvantages: Initial investment and maintenance can be high.
-
Screw-Plunger Plastic Injection Molding Machine
- Description: Combines the use of a screw for plasticization and a plunger for injection, separating the two processes.
- Advantages: Provides flexibility in processing various materials with different properties.
- Disadvantages: Complexity in design can lead to increased costs.
Importance of Choosing the Right Method
Choosing the right plasticization method can significantly impact production efficiency, cost-effectiveness, and product quality. Here’s a table summarizing the differences:
Method | Mixing Quality | Usage | Complexity | Cost |
---|---|---|---|---|
Plunger | Poor | Rare | Low | Low |
Reciprocating Screw | Excellent | Common | Moderate | High |
Screw-Plunger | Moderate | Specialized | High | Moderate |
Impact on Material Properties
The choice of plasticization method also affects the final material properties, such as:
- Viscosity: Higher viscosity can lead to difficulties in filling molds, affecting detail and finish.
- Temperature Control: Precise temperature management ensures that materials are adequately melted without degradation.
- Mixing Homogeneity: A well-mixed material leads to consistent quality, reducing defects.
For further insights into how these methods influence manufacturing processes, check out detailed analysis5.
Conclusion
Understanding the role of plasticization methods is vital for product designers and manufacturers alike. The implications of choosing the right plasticization technique can resonate throughout the entire production lifecycle, influencing everything from cost to final product quality. For those looking to delve deeper into specific methods and their applications, consider exploring resources that discuss best practices in injection molding6.
Reciprocating screw method is the most common in injection molding.True
The reciprocating screw method is widely used due to its efficiency and excellent mixing properties, making it the preferred choice in modern manufacturing.
Plunger plastic injection is frequently used in modern manufacturing.False
Plunger plastic injection molding is rarely used today because of its poor mixing capabilities and inefficiency compared to other methods.
How does the mold clamping method truly influence production efficiency?
Have you ever thought about how choosing the right mold clamping method affects production efficiency? This choice is very important. Let’s explore why every manufacturer should really think about this.
The mold clamping method greatly affects production efficiency. It influences cycle times, product quality and energy use in injection molding. Choosing the right method is important. Manufacturers should understand their options. Good decisions in mold clamping probably increase efficiency.
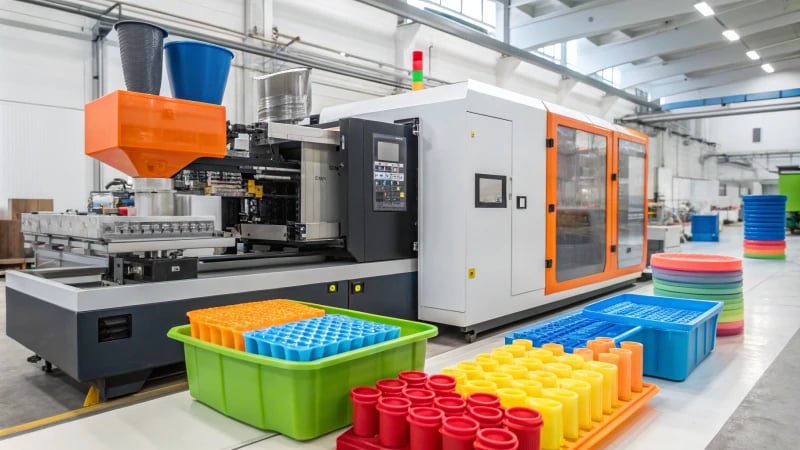
Understanding the Mold Clamping Method
The mold clamping method deeply influences production efficiency. It affects cycle times, product quality, and energy use in injection molding. I have seen how these methods impact project outcomes. Choosing the right method is like picking a perfect tool. It can simplify your work or make it more difficult.
The mold clamping method is crucial in the injection molding process. It’s more than just a technicality; there is real potential for increased efficiency. I remember learning about the toggle type clamping method. It was like finding a hidden gem. This method is reliable and cost-effective, allowing for quicker mold opening and closing cycles, which can reduce overall cycle times by up to 10%. A small change can smooth production lines and raise throughput.
Another method is direct pressure. It has precise control over clamping force, which is useful for complex molds needing strict tolerances. I recall when uneven pressure caused defects in a project that troubled us for weeks; direct pressure would have prevented it. Although it uses more energy, the benefits were clear: reduced scrap rates were worth it.
Cycle Time Implications
Cycle times are crucial as the mold clamping method chosen affects how fast molds open and close, impacting production output.
Clamping Method | Average Cycle Time Reduction | Cost Impact |
---|---|---|
Toggle Type | 10% | Low |
Direct Pressure | 5% | Medium |
Two-Plate Type | 15% | High |
The two-plate type clamping mechanism fits larger molds and can significantly speed up cycle time. However, with high initial costs, I reconsidered for smaller tasks unless producing large quantities where such efficiencies justify the investment.
Quality Control and Consistency
Quality control is always a top priority. A good clamping system ensures even pressure on the mold surface, leading to better product quality. Uneven clamping can cause serious issues such as:
- Fluctuating product dimensions
- More defects
- Higher rates of rework
Inconsistent pressure led to a product batch that failed standards. Using hydraulic injection molding machines with direct pressure improved clamping control; each cycle offered consistent results and transformed component production with tight tolerances.
Energy Consumption Considerations
Energy consumption needs attention as different clamping methods have varying energy needs:
- Toggle Type: Generally uses less energy due to mechanical advantage.
- Direct Pressure: Consumes more energy through hydraulic systems.
- Full Electric Systems: They save energy and offer precise control.
Understanding these factors helped me choose machinery aligned with production and sustainability goals. For energy-efficient molding techniques, explore more energy saving practices7.
Conclusion of Insights
The mold clamping method influences production efficiency, including cycle times and energy use. Picking the correct clamping method helps manufacturers like us optimize production, improve product quality, and increase profits. This journey requires learning and adaptation; but every step leads to results we want to achieve.
Toggle type clamping reduces cycle times by up to 10%.True
The toggle type clamping method is known for its efficiency, allowing quicker mold cycles that can reduce overall production time significantly.
Direct pressure methods guarantee lower energy consumption than toggle type.False
Direct pressure methods typically consume more energy due to hydraulic systems compared to the mechanically advantageous toggle type.
Conclusion
Explore common types of injection molding machines categorized by appearance, power source, plasticization methods, and clamping techniques to enhance manufacturing efficiency.
-
This link provides detailed insights into the operational efficiency of hydraulic machines, helping you understand their competitive edge. ↩
-
Explore material compatibility options with hydraulic systems to see if they fit your production needs. ↩
-
Learn how hydraulic systems can enhance production speed and efficiency in your manufacturing process. ↩
-
Discover insights on operational differences and efficiency to make informed purchasing decisions. ↩
-
Explore various plasticization methods and their impact on injection molding efficiency and product quality. ↩
-
Learn about the best practices and techniques for optimizing the plasticization process in injection molding. ↩
-
This link provides insights into enhancing productivity through optimal clamping techniques. ↩