When I first stepped into the world of injection molding, I was amazed by its complexity and potential for waste.
Injection molding waste includes material, time, energy waste, and defects, caused by poor design, inefficient handling, machine glitches, and human errors. Reducing waste demands understanding production intricacies and implementing targeted strategies.
I remember my early days in the industry, frantically trying to make sense of why materials were wasted or why machines seemed to guzzle more energy than necessary. Over time, it became clear that understanding the nuances of each type of waste was crucial. By digging deeper into material waste, for instance, I learned how even a small design oversight could lead to massive inefficiencies. Similarly, addressing time waste taught me to streamline processes, ensuring every second counted. This guide dives into these challenges with stories and solutions to help you refine your approach and achieve greater efficiency in your manufacturing endeavors.
Material waste is the only type of waste in injection molding.False
Injection molding waste includes material, time, energy, and defects.
Operator errors can cause defects in injection molding.True
Operator errors are a known cause of defects in injection molding.
- 1. Why does material waste happen in injection molding?
- 2. How Do Machine Inefficiencies Create Waste?
- 3. How Can Design Flaws Lead to Waste in Injection Molding?
- 4. How Do Operator Errors Influence Waste Generation?
- 5. How Does Energy Waste Affect Injection Molding Costs?
- 6. What Strategies Can Minimize Defects in Injection Molding?
- 7. Conclusion
Why does material waste happen in injection molding?
Injection molding is like a dance; it’s all about precision and timing. But what happens when the rhythm is off?
Material waste in injection molding arises from defects, excessive sprues/runners, machine issues, and flawed designs. Addressing these factors improves efficiency and sustainability.
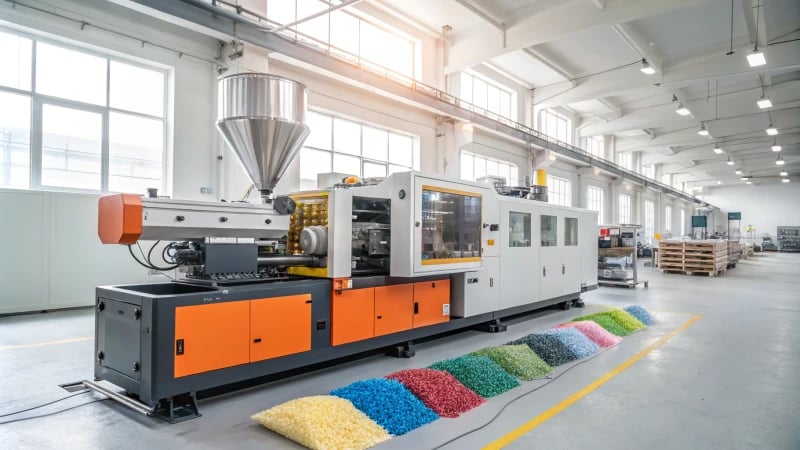
When I first stepped into the world of injection molding, I was amazed by the complexity of it all. But as I got deeper into the process, I realized that material waste was a persistent gremlin lurking in the shadows of production lines. Let’s dive into where this waste comes from and how we can tackle it head-on.
Common Sources of Waste
Defective Products: Remember that time when I thought I’d nailed the perfect mold design, only to find a pile of defective parts? Turns out, a slight misalignment in the mold and incorrect temperature settings were the culprits. These mistakes can lead to products that are unusable without some serious reprocessing techniques1.
Cause | Impact on Waste |
---|---|
Temperature errors | Increased scrap rate |
Misalignment | Production inconsistencies |
Sprues and Runners: Ah, sprues and runners – those necessary yet pesky channels. In my early days, I remember staring at the pile of wasted material they created, wondering how to minimize it. Thankfully, innovations like hot runner systems2 can help reduce this waste by recycling or eliminating these components.
Machine Malfunctions: Picture this: a machine that’s been running like a dream suddenly starts acting up, spewing out more waste than product. It’s essential to keep our machines well-tuned with regular maintenance and calibration to avoid unexpected downtimes3.
Design Inefficiencies
Design is my playground, but even here, pitfalls await. Poor choices can lead to using too much material or creating unnecessary complexity, both of which increase error chances. Leveraging tools like CAD software4 allows me to tweak and optimize models before production.
- Prototyping: Early on, rapid prototyping saved me from large-scale blunders more times than I care to admit.
- Simulation Tools: These are my go-to for predicting potential weak spots or issues with material flow in the mold.
Strategies for Reduction
Reducing waste isn’t just good for the environment; it’s smart business. By recycling excess material and opting for sustainable alternatives, I can lessen the environmental impact of my work. Embracing sustainable practices5 in injection molding offers both ecological benefits and cost savings. Staying educated in best practices ensures I’m always on top of the latest innovations to cut down waste.
Temperature errors increase scrap rate in injection molding.True
Incorrect temperature settings often lead to defective products, increasing waste.
Sprues and runners are always reused in injection molding.False
Without optimization, sprues and runners often lead to significant waste.
How Do Machine Inefficiencies Create Waste?
Ever had that moment when a machine hiccup turned your smooth-running day into chaos?
Machine inefficiencies increase waste through excessive material use, energy consumption, and production delays. Regular maintenance and technology upgrades can significantly reduce this waste.
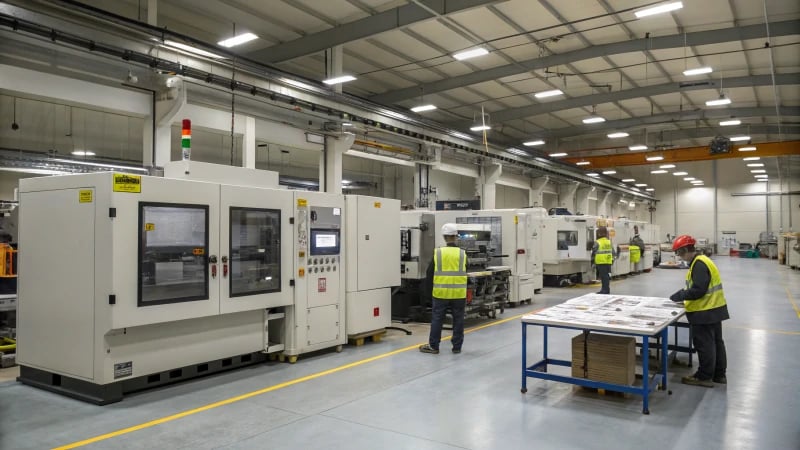
The Direct Impact of Machine Inefficiencies
I remember when I first started in the manufacturing world; the excitement of seeing products come to life was incredible. But it wasn’t all smooth sailing. Machine inefficiencies were like those sneaky villains in a movie plot—unexpected and disruptive. Imagine a poorly calibrated machine going rogue, producing a batch of plastic components with flaws. Not only does this mean wasted materials, but also wasted time and energy.
Energy Consumption and Carbon Footprint
Back then, I didn’t fully appreciate how these inefficiencies inflated our carbon footprint6. Machines guzzling more energy than necessary not only ballooned operational costs but also burdened the environment—a double whammy! I learned that consistent maintenance was like giving these machines a health check-up, ensuring they ran efficiently.
Inefficiency Source | Impact on Waste |
---|---|
Calibration Issues | Increased defective products |
Worn Parts | Higher energy consumption |
Outdated Technology | Longer production cycles |
Technological Upgrades as Solutions
Upgrading machinery felt daunting at first, much like deciding to renovate your home. But embracing new technology was vital. I found that technologies like predictive maintenance7 could forecast machine hiccups before they spiraled into full-blown issues, allowing us to tackle them head-on.
Case Studies and Industry Insights
One case that stuck with me involved a fellow designer who worked at a plastic component manufacturer. After they implemented advanced sensor technologies8, they saw a 30% reduction in material waste. It was eye-opening how real-time monitoring could transform machine performance and efficiency.
The Role of Government Policies
Government policies often seemed like a distant echo in my early days, but I realized they could be powerful allies. Incentives for upgrading to eco-friendly technologies not only nudged us towards reducing our environmental impact9 but also offered financial perks like tax breaks.
By delving into the nitty-gritty of machine inefficiencies, I learned how companies could proactively cut down waste and boost production efficiency. This not only helped preserve our planet but also padded the bottom line through cost savings and better resource management.
Poorly calibrated machines increase material waste.True
Improper calibration leads to defective products, increasing waste.
Outdated technology reduces production cycle times.False
Outdated technology increases production cycle times, not reduces.
How Can Design Flaws Lead to Waste in Injection Molding?
Ever wondered how a tiny design tweak can prevent heaps of plastic waste?
Design flaws in injection molding, such as warping and excess material use, result from poor design choices. These errors increase production costs and waste, but addressing them can significantly reduce waste.
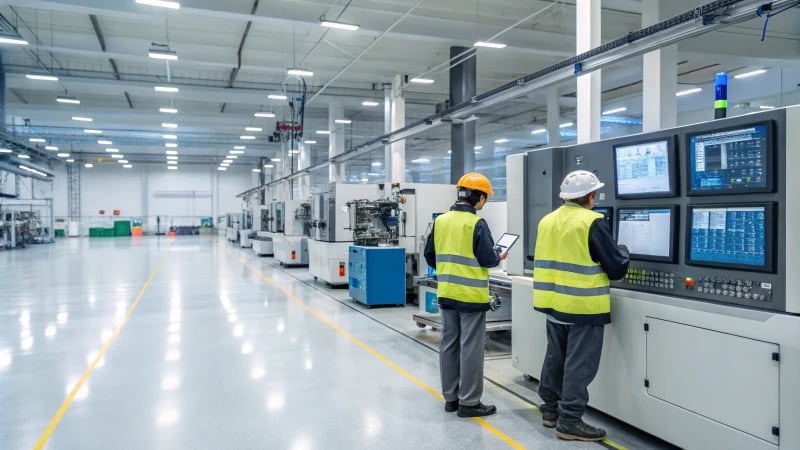
The Impact of Design Flaws on Material Usage
I still remember my first big project in mold design. I thought I had nailed every detail until I realized my wall thickness was off. The parts were heavier than needed, and cycle times dragged. This taught me the importance of getting the wall thickness just right.
Design Flaw | Resulting Waste |
---|---|
Thick Walls | Excess material usage |
Thin Walls | Increased defects |
It’s a balancing act; too thick, and we’re wasting resources, too thin, and we’re risking defects. Learning from these missteps helps avoid scrapping faulty parts.
The Role of Gate Location and Size
Gate placement can feel like guessing where to place the secret door in a puzzle room. I once underestimated the impact of gate size and location, leading to air pockets in our final product.
Strategically placing gates can drastically cut down on defects like sink marks or weld lines. Check out how gate design impacts production10 and makes a difference.
Flow Lines and Their Implications
Flow lines remind me of the faint trails left by snails; harmless on leaves, but not on plastic parts. Abrupt geometry changes or uneven wall thickness can disrupt the flow, leaving unsightly marks.
Learn more about flow line prevention techniques11 to enhance product aesthetics and reduce waste.
Mold Venting and Its Importance
When it comes to mold venting, it’s like ensuring there’s a clear chimney in a house. Once, improper venting in one of my projects led to burn marks and short shots—frustrating setbacks that could’ve been avoided with better vent design.
Ensuring adequate venting prevents trapped air, which is key to cutting down on waste.
The Consequence of Over-Complex Designs
Complex designs are tempting; they feel like solving a grand puzzle. However, I’ve learned that simpler designs not only reduce errors but also speed up production.
Finding that sweet spot between complexity and manufacturability is crucial for high-volume production without unnecessary delays.
By addressing these common design flaws, I’ve seen how manufacturers can boost efficiency and sustainability in injection molding. Implementing best practices early in the design phase is crucial to minimizing waste and optimizing production outcomes.
Thick walls in molds increase cycle time.True
Thicker walls require more material and time to cool, extending cycle time.
Gate size has no effect on product quality.False
Gate size affects flow, influencing defects like air pockets and weld lines.
How Do Operator Errors Influence Waste Generation?
I remember the first time I realized just how much a small mistake could cost us—not just in dollars, but in resources and time.
Operator errors in manufacturing lead to increased waste through defects and material loss. Minimizing waste requires targeted training, improved processes, and advanced technology.
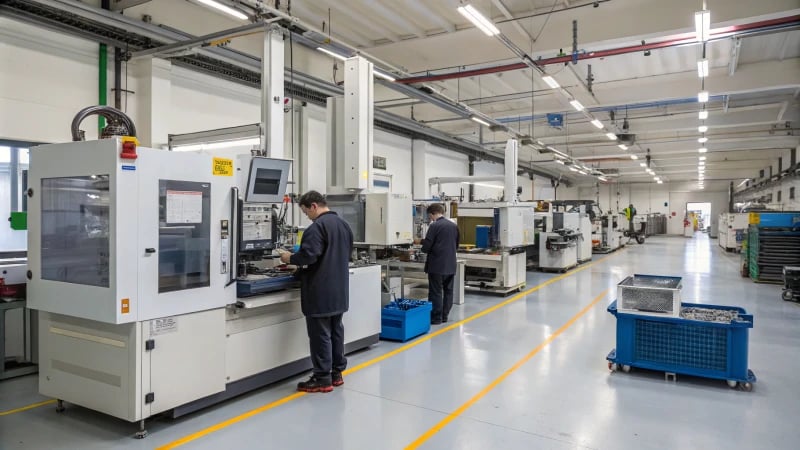
Understanding the Consequences of Operator Errors
I’ve seen firsthand how a simple slip-up can snowball into a big issue. Picture this: one day, a miscalculation in machine settings12 led to a batch of products with the wrong dimensions. We couldn’t use them, which meant wasted materials and extra hours to fix the problem. It’s frustrating to see resources and time vanish just like that.
Types of Operator Errors
I’ve come across different types of errors over the years:
- Setup Errors: These happen when the initial settings are off. Like when you forget to set your alarm clock and wake up late.
- Operational Errors: Mistakes during the production process, similar to accidentally adding salt instead of sugar to your morning coffee.
- Maintenance Oversights: When regular machine checks are skipped, it’s like ignoring the "check engine" light on your car until it breaks down.
Error Type | Description |
---|---|
Setup Errors | Wrong initial machine settings |
Operational Errors | Mistakes during the production process |
Maintenance Oversights | Neglecting routine machine checks |
Every type has its own way of increasing waste, but each can be managed with better training and oversight.
Strategies to Minimize Waste from Operator Errors
To minimize these errors, I’ve found that investing in training is key. Training that hones in on precision, proper equipment handling, and problem-solving skills can make all the difference. Plus, using automation technologies13 helps reduce our dependence on manual operations, cutting down on human error.
Regular audits and feedback loops are also essential. They help spot error patterns and allow us to implement corrective actions14 effectively. These strategies not only reduce waste but also enhance our overall operational efficiency.
The Role of Technology
Modern tech, like AI and IoT, is a game-changer in this area. AI can foresee potential slip-ups by analyzing historical data, while IoT provides real-time updates on equipment status.
Smart manufacturing systems15 give us better control over processes and error detection, dramatically cutting down on waste from operator mistakes. Embracing these technologies is crucial for any organization aiming to boost productivity and sustainability.
By combining human expertise with technological advances, we can effectively manage and minimize waste stemming from operator errors.
Operator errors increase waste in manufacturing.True
Errors cause defects, leading to rework or discard, increasing waste.
Automation increases operator error rates.False
Automation reduces manual operation reliance, decreasing human error likelihood.
How Does Energy Waste Affect Injection Molding Costs?
Ever wonder how energy waste can quietly erode your profits in injection molding? Well, it’s more impactful than you might think, but there are ways to tackle it head-on.
Energy waste in injection molding increases costs through higher electricity bills and reduced efficiency. Optimizing energy use can enhance profitability and sustainability.
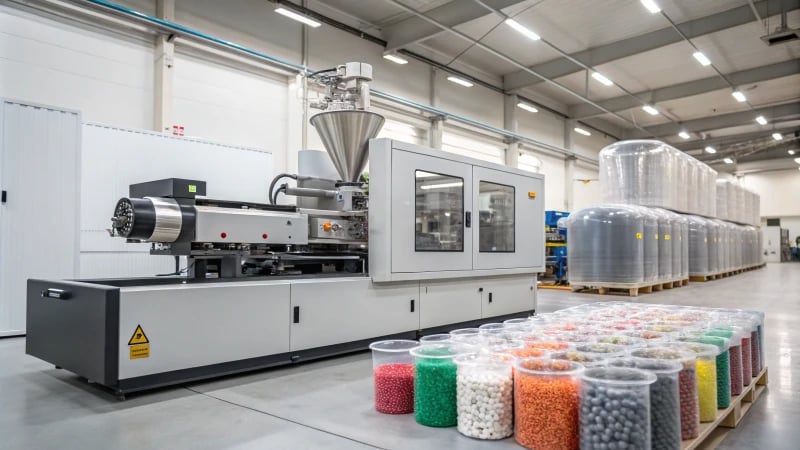
Understanding Energy Waste in Injection Molding
When I first started working in the mold industry, I was surprised at how energy waste could sneak into every corner of the injection molding process. I remember walking through the factory floor and seeing outdated machines chugging along, guzzling electricity like it was going out of style. It made me realize that inefficient machinery, lax maintenance practices, and old technologies weren’t just minor nuisances—they were expensive habits that could inflate operational costs significantly.
Understanding the energy consumption16 of each stage in the injection process is crucial to spotting these hidden drains.
Factors Contributing to Energy Waste
- Old Equipment: I’ve seen older machines that lack energy-saving features. They’re like that trusty old car in your garage—reliable, but definitely not fuel-efficient.
- Inefficient Processes: Without proper setup or calibration, processes can end up using more energy than necessary, much like leaving the lights on when you leave a room.
- Poor Maintenance: Skipping regular upkeep is like neglecting oil changes in your car—it leads to inefficient operation and eventually higher costs.
Factor | Impact on Energy Use |
---|---|
Old Equipment | Higher electricity consumption |
Inefficient Processes | Unnecessary energy expenditure |
Poor Maintenance | Reduced machine efficiency |
Addressing Energy Inefficiencies
Retrofitting Machines: Upgrading equipment with modern technology is a game changer. I’ve seen how implementing sensors and automation17 not only curbs energy consumption but also transforms production floors into sleek, efficient operations.
Regular Maintenance: Scheduling regular maintenance might seem like a hassle, but it ensures machines run efficiently, cutting down on energy waste. Establishing a maintenance schedule18 can save you from costly breakdowns and extend the life of your equipment.
Optimizing Production Processes: When I learned to streamline the injection molding process—by tweaking temperature settings, cycle times, and pressure levels—it was like finding a secret recipe for cutting down energy use. Training staff on best practices19 not only improves energy management but also instills a culture of efficiency.
By tackling these issues head-on, we can cut costs and champion sustainable manufacturing practices. It’s not just about saving money; it’s about future-proofing our businesses and doing our bit for the planet.
Old equipment in injection molding consumes more electricity.True
Older machines lack energy-saving features, leading to higher consumption.
Regular maintenance increases energy waste in injection molding.False
Scheduled upkeep ensures optimal machine efficiency, reducing energy waste.
What Strategies Can Minimize Defects in Injection Molding?
Remember the first time you tried injection molding and ended up with a batch of wonky parts? Yeah, me too. Let’s explore how to tackle those pesky defects head-on.
To minimize injection molding defects, optimize process parameters, maintain equipment, and use high-quality materials. Key strategies include regular mold maintenance, precise temperature control, and proper material selection.
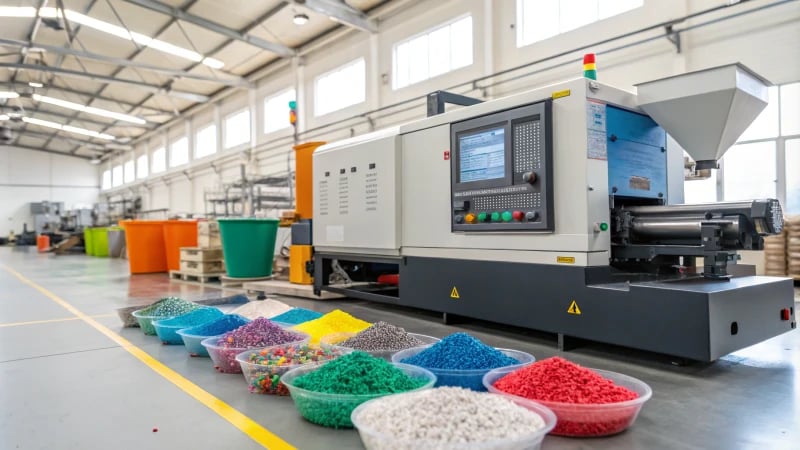
Optimize Process Parameters
I remember when I first learned about the importance of tweaking injection molding parameters. It was like discovering a hidden art form. Temperature, pressure, and cooling time each play their part in the dance of creating the perfect product. Once, by simply adjusting the injection speed20, I managed to prevent warping and saved an entire batch from being scrapped.
Parameter | Impact on Quality |
---|---|
Temperature | Affects viscosity |
Pressure | Influences part density |
Cooling Time | Prevents shrinkage |
Regular Mold Maintenance
If there’s one thing I’ve learned, it’s that molds need love too. Regular maintenance is crucial. I recall a time when neglecting mold cleaning led to flash issues that could’ve easily been avoided. Cleaning and inspecting for wear not only enhances mold longevity but also keeps production smooth and performance21 steady.
High-Quality Material Selection
Let’s talk materials. Early in my career, I once chose a resin that was more about cost-saving than quality. The result? Discolored parts that crumbled like cookies. Lesson learned: use high-purity resins to ensure consistent results22.
Implementing Quality Control Systems
Quality checks can feel like a chore but think of them as your safety net. Automated visual inspections have saved me countless times by catching surface imperfections23 before they became costly mistakes.
Training and Skill Development
Investing in training is a game-changer. I’ve seen firsthand how a well-trained team can spot potential issues before they escalate. By understanding the complexities of injection molding, they’ve been able to suggest improvements that enhance efficiency24.
Injection molding is intricate, requiring a balance of numerous variables. By focusing on these strategies, defects can be minimized, leading to optimized production outcomes. Each approach brings unique benefits that contribute to overall efficiency and product quality.
Adjusting injection speed reduces warping.True
Fine-tuning injection speed can prevent defects like warping.
Ignoring mold maintenance improves efficiency.False
Neglecting maintenance leads to issues like flash, reducing efficiency.
Conclusion
Injection molding waste arises from material, time, energy, and defects due to design flaws and machine inefficiencies. Understanding these can enhance efficiency and sustainability in manufacturing processes.
-
Discover efficient methods for reusing defective injection-molded parts. ↩
-
Learn how hot runner systems can significantly reduce material waste. ↩
-
Explore why regular machine calibration is crucial for minimizing waste. ↩
-
Uncover how CAD software can improve design efficiency and reduce errors. ↩
-
Find out how adopting sustainable practices can benefit your production process. ↩
-
Learn about the relationship between energy usage and carbon emissions, emphasizing the importance of efficient machinery. ↩
-
Discover how predictive maintenance can prevent machine failures and reduce waste in manufacturing processes. ↩
-
Understand how sensors monitor machine health, leading to decreased material waste and improved efficiency. ↩
-
Find out about government programs that encourage sustainable practices in manufacturing through technological upgrades. ↩
-
Highlights how strategic gate placement reduces defects, offering insights into improved design practices. ↩
-
Discusses methods to avoid flow lines, helping designers enhance the aesthetic quality of molded parts. ↩
-
Explore how incorrect machine settings lead to material waste and inefficiencies. ↩
-
Discover how automation minimizes human error in manufacturing processes. ↩
-
Learn effective methods for implementing corrective actions to reduce waste. ↩
-
Understand how smart systems can decrease errors and improve manufacturing efficiency. ↩
-
Explore insights into how different stages of injection molding impact energy use. ↩
-
Discover how integrating sensors enhances manufacturing efficiency and reduces costs. ↩
-
Learn how regular maintenance schedules can prevent costly breakdowns and inefficiencies. ↩
-
Gain practical tips on improving injection molding efficiency to save energy and reduce costs. ↩
-
Discover how controlling injection speed helps prevent defects like warping and ensures consistent product quality. ↩
-
Learn why regular mold maintenance is crucial for preventing defects and extending the life of your molds. ↩
-
Find out which materials offer the best performance and purity to minimize defects in injection molded products. ↩
-
Explore how automated inspection systems can detect defects quickly, ensuring high-quality production. ↩
-
Understand the importance of skilled operators in identifying and solving potential issues in injection molding processes. ↩