Are you struggling with the choice between two-shot injection molding and overmolding for your next project? I understand that feeling. I am really here to help you solve this manufacturing puzzle!
Two-shot injection molding combines two materials in one cycle, creating seamless multi-material parts, while overmolding adds a second layer of material onto an existing product. Both methods enhance plastic products, but each offers distinct benefits depending on design needs.
When I first entered the world of product design, I faced this same choice. It was like standing at a crossroads. I felt unsure which path would lead to the best result for my project. Two-shot injection molding and overmolding both have unique qualities. Understanding their details is crucial for success in design work.
This article takes a close look at these techniques. It explores their processes, benefits and best uses. You might be an experienced designer or a beginner. Either way, the insights here will probably help you with your projects.
Two-shot injection molding uses a single molding cycle.True
This method combines two materials in one cycle, streamlining production.
Overmolding adds material to an already molded part.True
This process enhances an existing substrate with new material for improved functionality.
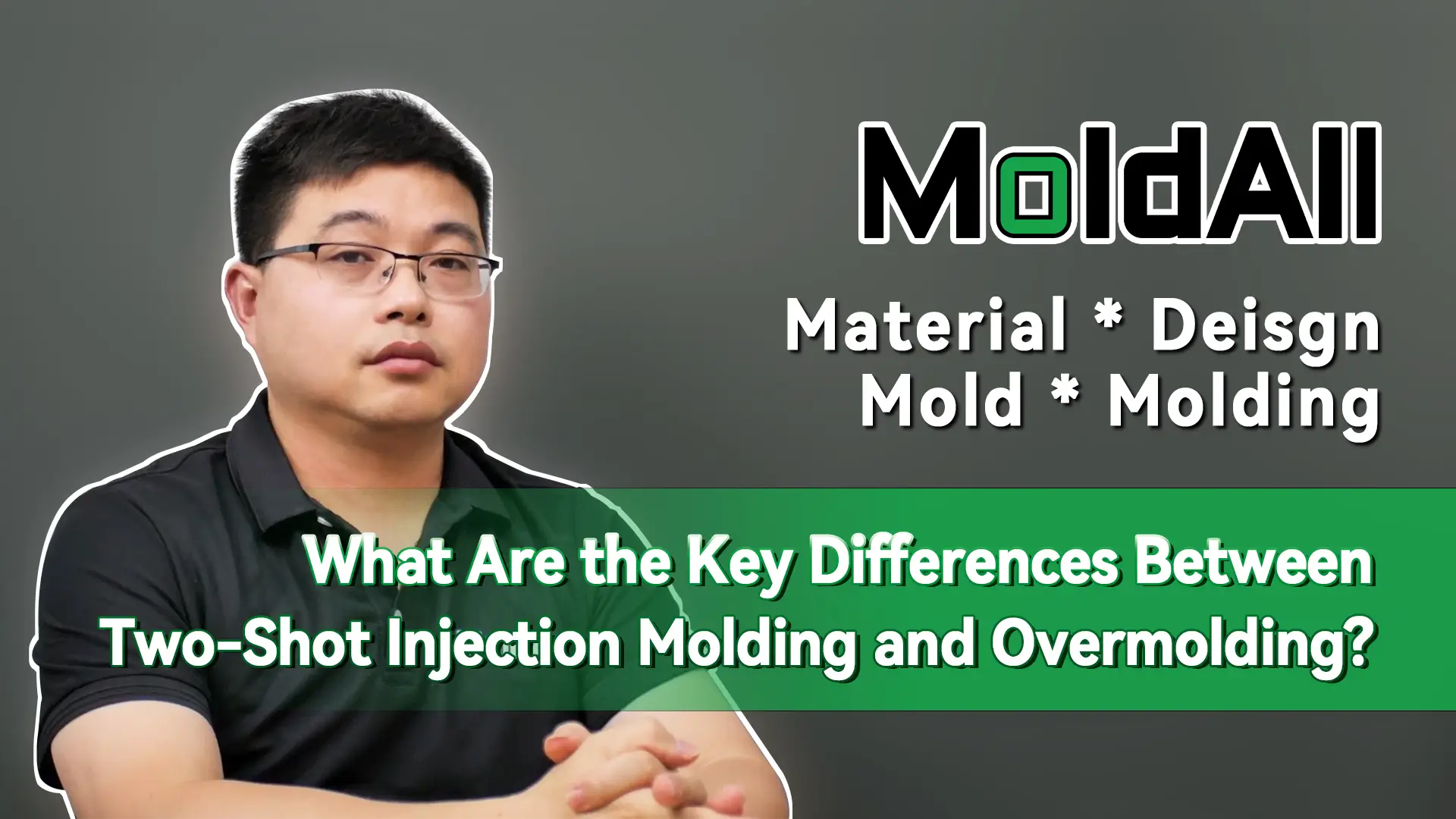
- 1. What Are the Benefits of Two-Shot Injection Molding?
- 2. How Does Overmolding Enhance Product Functionality?
- 3. What Are the Cost Implications of Each Molding Technique?
- 4. In What Applications Are Two-Shot Injection Molding and Overmolding Most Suitable?
- 5. What Should Designers Consider When Choosing Between These Processes?
- 6. Conclusion
What Are the Benefits of Two-Shot Injection Molding?
Have you ever thought about how intricate plastic items are produced in just one molding process? Let’s explore the amazing world of two-shot injection molding. This method has truly remarkable benefits!
Two-shot injection molding changes production methods. It allows two different materials to get injected in one cycle. This process improves product strength. Products have more versatile designs. It reduces costs significantly. It is very important for modern manufacturing.
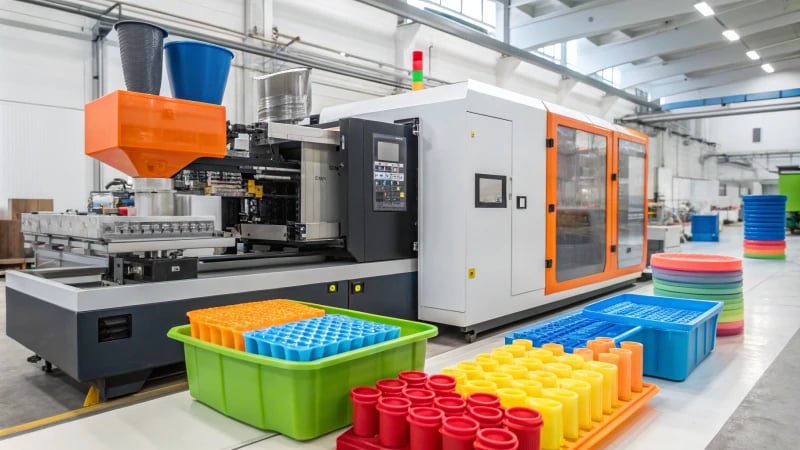
Overview of Two-Shot Injection Molding
I recall my first experience with two-shot injection molding during my design journey. It seemed like magic! This creative process lets us create complex plastic items with different material qualities in one molding cycle. People also call it double-shot or two-color injection molding.
The principle of the process involves using an injection molding machine equipped with two injection units. The first material is injected to form the base structure, while the second material, often differing in color or texture, is injected to create the outer structure or functional parts. This integration not only enhances the product’s functionality but also its aesthetic appeal.
Advantages of Double-Shot Injection Molding
- High Production Efficiency
This technique saves a lot of time! By completing both injections in a single molding cycle, manufacturers can achieve significant time savings. This means higher output rates compared to traditional methods that take extra time with several processes.
Metric | Traditional Methods | Two-Shot Injection Molding |
---|---|---|
Cycle Time (minutes) | 2-5 | 1-3 |
Output Rate (units/hour) | 100-200 | 300-500 |
-
Improved Product Integrity
The joining of materials amazed me when I first watched it happen. The products are strong and long-lasting due to the seamless combination of materials, minimizing the risk of defects that are common in assembly processes. -
Design Versatility
Creativity really shines here! Different sections of the product can have varying hardness, colors, and gloss levels. When crafting a tool with a soft grip, I start with a hard plastic body, then add a soft grip – all at once! This flexibility helps me explore design limits while fulfilling both look and functionality needs effectively. -
Cost Savings
Buying a double-shot injection molding machine may seem overwhelming initially; however, long-term savings are really beneficial! Although the initial investment may be higher, less material waste and fewer assembly steps lower production costs, making it an attractive option for large-scale manufacturing.
Comparison with Other Molding Processes
When comparing two-shot injection molding with techniques like secondary molding or overmolding, its benefits become very clear:
Feature | Two-Shot Injection Molding | Secondary Molding | Overmolding |
---|---|---|---|
Cycle Efficiency | High | Moderate | Moderate |
Material Variety | Two simultaneous materials | Multiple steps needed | One additional layer |
Product Complexity | High | Moderate | Moderate |
Assembly Requirement | None | Required | Minimal |
Conclusion
To sum up, two-shot injection molding brings many perks – high production efficiency, improved product strength, design flexibility and cost savings. Understanding these benefits has been vital in refining my production methods and making wise decisions about manufacturing choices.
If you’re eager to learn about specific uses and case studies of two-shot injection molding, I suggest exploring our resources on advanced molding techniques1. You really won’t want to miss them!
Two-shot injection molding increases production efficiency.True
This method allows for two materials to be injected in one cycle, saving time and boosting output rates significantly compared to traditional methods.
Two-shot injection molding requires more assembly steps than traditional methods.False
In fact, this process eliminates the need for additional assembly by combining materials in a single molding cycle, enhancing product integrity.
How Does Overmolding Enhance Product Functionality?
Have you ever held a tool that felt just right in your hand? The perfect grip and solid feel happen because of a fascinating process named overmolding. But what exactly makes this technique so unique and interesting?
Overmolding really helps products work better by letting manufacturers mix different materials. These materials improve how durable, attractive and effective products are. This method allows for intricate designs and productive manufacturing processes. Products feel nice to hold and probably last a longer time.

Understanding Overmolding
Overmolding combines layers of different materials to create something unique. I remember holding a tool crafted with this technique. The soft rubber grip felt comfortable, while the hard plastic body felt strong. This mix of materials improves user experience and extends the life of a product. It’s really special.
Benefits of Overmolding
-
Greater Longevity: Overmolding often helps a product last much longer. I once joined a project to create shock-absorbing handles for power tools. A softer outer layer protected the inner parts from damage. This approach helped the tool survive longer and work better.
-
Better Looks: First impressions are so important in consumer products. Overmolding allows designers to craft vibrant products with striking colors and textures. It gives devices a personality. Smartphones look sleek and have non-slip surfaces. They really catch the eye and feel wonderful to hold.
-
More Uses: Picture a product serving many roles without needing extra parts. This really shows the wonder of techniques like double-shot injection molding2. This method fosters innovative designs that are easy to produce and simple to use.
Techniques Used in Overmolding
- Double-shot Injection Molding: This process uses two injection units to bring different materials together in one mold during a single cycle. This method can form products with complex features. For instance, in tool manufacturing, hard plastic shapes the body, while soft plastic forms the grip. Both materials connect seamlessly.
Process | Description |
---|---|
Double-shot Injection Molding | Combines two different plastics into one part for complex designs. |
Secondary Molding | Utilizes an existing molded part to add additional features or materials. |
- Secondary Molding: This method takes earlier molded components and builds on them. I recall a project where we added a textured film over a plastic shell. This addition brought both function and style.
Real-World Applications of Overmolding
Overmolding improves products across many industries. For instance:
- In smartphones, overmolding is used to create durable yet lightweight cases that also provide a non-slip surface.
- In cars, overmolding integrates rubber seals for water resistance while keeping structural strength intact.
Techniques like secondary molding3 have shown me that designers can elevate product appearance and performance effectively.
Overmolding improves product durability through material combinations.True
By layering materials, overmolding enhances durability, allowing products to absorb shocks and resist wear, ultimately extending their lifespan.
Overmolding is only used in consumer electronics manufacturing.False
This claim is false; overmolding is utilized across various industries, including automotive and healthcare, for diverse applications beyond consumer electronics.
What Are the Cost Implications of Each Molding Technique?
I am a designer. I really understand how important it is to know the costs of different molding methods. We should explore how tooling, choosing materials and the number of items produced affect our expenses. This is crucial. Our bottom line is really impacted.
Understanding the costs of molding techniques is very important for budgeting. Tooling complexity, material choice and production volume are essential factors. Double-shot injection molding usually has higher initial costs. However, it can become more efficient for complex products over a long period. Secondary molding provides flexibility. It probably lowers expenses in the long run.
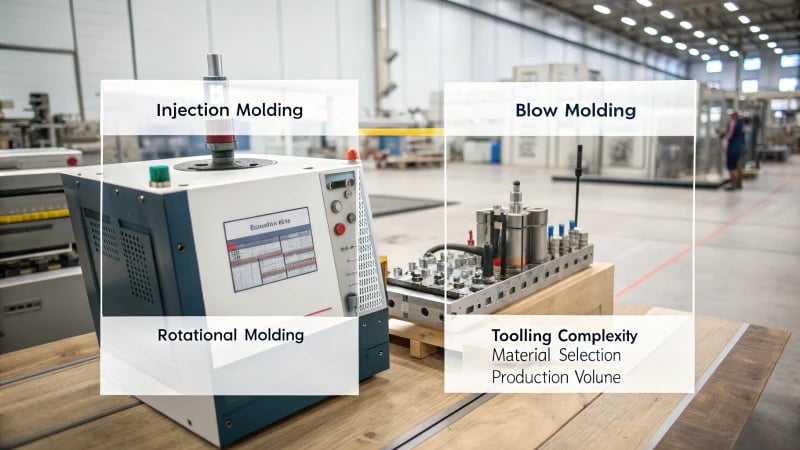
Understanding Cost Implications of Molding Techniques
When evaluating the cost implications of various molding techniques, it’s essential to consider multiple factors including tooling, material selection, and production volume. These elements can significantly influence the overall cost of production, and understanding them can help manufacturers make informed decisions.
Tooling Costs
Tooling costs refer to the expenses associated with creating the molds used in the manufacturing process. Different molding techniques have varying tooling requirements:
Molding Technique | Tooling Complexity | Initial Investment | Long-term Cost Efficiency |
---|---|---|---|
Double-shot Injection Molding | High | High | Medium |
Secondary Molding Process | Medium | Medium | High |
Double-shot injection molding requires complex molds with mechanisms for rotating or sliding, which increases initial investment but can offer better long-term efficiency for products requiring multiple materials.
In contrast, secondary molding may have a lower initial tooling cost but can involve multiple processes that might increase time and labor costs in the long run.
Material Selection
The choice of materials plays a critical role in determining production costs. Different molding techniques allow for different material types, which can affect not only the cost but also the quality and functionality of the product:
- Double-shot Injection Molding: This method enables the use of two different materials within one product. For instance, using a hard plastic for the body and a soft rubber for grips can enhance product usability but may increase material costs due to the need for specialized materials.
- Secondary Molding Process: It allows for the integration of additional materials onto an existing substrate, often improving product features without the need for completely new molds. For example, adding a soft-touch coating to a hard plastic shell can enhance user experience without substantially raising costs.
Production Volume Impact
Production volume has a significant impact on cost per unit in any molding process:
- Low Volume Production: Higher costs per unit due to setup times and tooling amortization spread over fewer units.
- High Volume Production: Lower costs per unit as fixed costs are distributed over a larger number of units, making high-volume production more cost-effective.
For manufacturers like Jacky, understanding these dynamics is crucial for budgeting and project planning. Utilizing cost calculators can provide insights into how varying production volumes affect pricing. Explore cost calculators4 that can aid in these calculations.
Conclusion on Cost Implications (For Further Reading)
In summary, each molding technique presents unique cost implications that must be considered during the design and manufacturing process. Further research into specific techniques can provide deeper insights into making optimal decisions for production costs. Learn more about injection molding costs5.
By understanding these factors, designers like Jacky can better strategize their projects, ensuring that they meet both functional and aesthetic requirements while managing costs effectively.
Double-shot injection molding has high initial tooling costs.True
This technique requires complex molds, leading to a significant initial investment, impacting overall production costs.
Secondary molding always results in lower long-term costs.False
While secondary molding may have lower initial costs, it can incur higher labor and time expenses, affecting long-term cost efficiency.
In What Applications Are Two-Shot Injection Molding and Overmolding Most Suitable?
When I started exploring product design, learning the uses of two-shot injection molding and overmolding felt like opening a treasure chest. These techniques can change how we create products. They really can improve the way we manufacture. Let’s explore these interesting methods together.
If you want to improve product design, two-shot injection molding is excellent. This process creates items with different material properties. Overmolding adds new functions to existing parts. It improves components like grips or moisture protection.
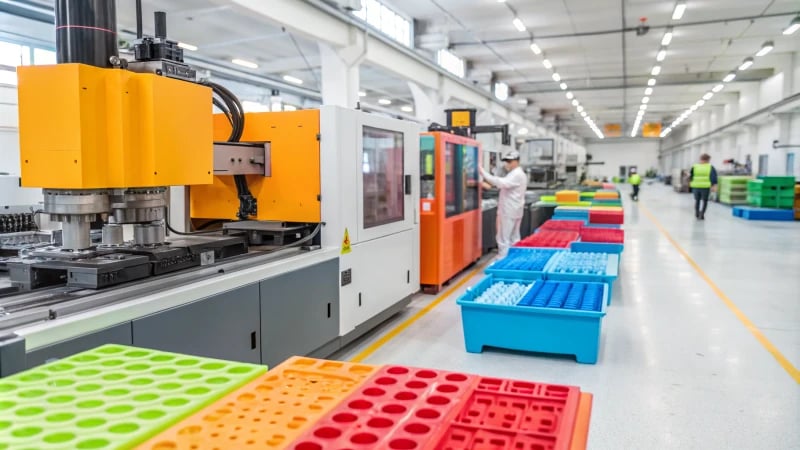
Applications of Two-Shot Injection Molding
Two-shot injection molding is particularly suitable for products that require multiple material properties. This technique is commonly employed in the following applications:
- Consumer Electronics: Many gadgets use this method. Devices often need both hard and soft materials. For example, your smartphone might have a tough outer shell and soft areas for a better grip. That comfort comes from two-shot molding.
- Automotive Parts: The automotive industry is a field full of opportunities for two-shot molding. Control knobs and switches frequently use this technique, where a hard base blends with a soft layer to provide great feedback for drivers.
- Medical Devices: Comfort is key in medical tools. Two-shot molding helps create surgical tools with comfy grips. These ergonomic designs help doctors during critical moments.
For more insights on applications of two-shot molding6, visit our detailed guide.
Applications of Overmolding
Now, let’s explore overmolding. This technique transforms existing parts by adding function and style. Common applications include:
- Grip Enhancements: Hand tools become more user-friendly with overmolding. A rubber or silicone layer over a plastic handle provides a non-slip surface that feels excellent in your hands.
- Electronic Housings: Use overmolding for electronic items, where it involves a rigid case combined with an outer layer for protection and better ergonomics—like a cozy cover for your devices.
- Insert Molding: This method is great for mixing metal or other materials into plastic parts, especially useful for strong automotive components where the way materials blend to improve function is fascinating.
Learn more about overmolding techniques in our comprehensive article.
Comparative Analysis of Both Techniques
When comparing two-shot injection molding and overmolding, both provide unique benefits depending on project requirements. Below is a comparison table summarizing their suitability based on various factors:
Factor | Two-Shot Injection Molding | Overmolding |
---|---|---|
Material Compatibility | High – can combine different plastic types | Moderate – typically one substrate material |
Design Complexity | Suitable for complex geometries | Good for adding features to existing parts |
Production Volume | High efficiency for mass production | Lower efficiency; best for smaller batches |
Cost Considerations | Higher initial setup costs | Lower setup costs but may increase per unit cost |
By understanding these applications, designers like Jacky can make informed decisions regarding which process to utilize for optimal product development. For an in-depth analysis on selecting the right molding process, refer to our resource page.
Two-shot injection molding is ideal for consumer electronics.True
This technique allows combining hard and soft materials, enhancing functionality and comfort in devices like smartphones.
Overmolding is primarily used for mass production.False
Overmolding is better suited for smaller batches, enhancing existing parts rather than large-scale manufacturing.
What Should Designers Consider When Choosing Between These Processes?
Picking the best design process often feels difficult. It’s essential for crafting products that work well and satisfy users. I will share some thoughts that have helped me decide.
When choosing between double-shot injection molding and secondary molding, designers should consider factors like process principles, mold complexity, material compatibility and project goals. This careful thinking helps match the chosen process with the desired product function and appearance. Product aesthetics and functionality matter.
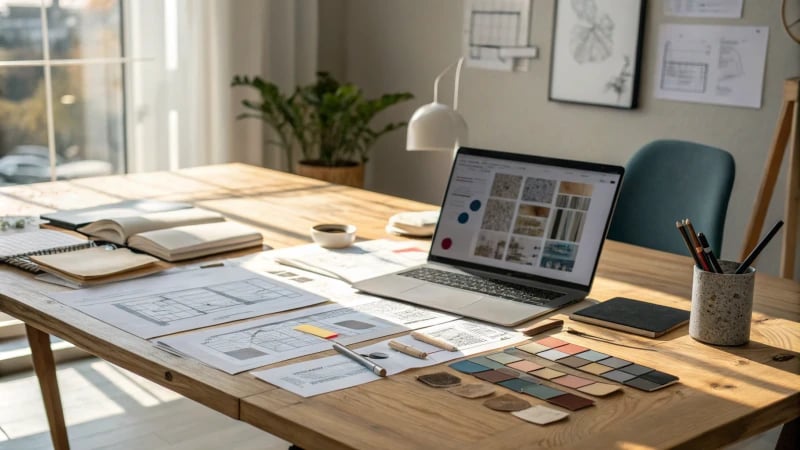
Understanding the Core Processes
When designers are faced with the choice between double-shot injection molding and secondary molding, several key considerations must be made. Understanding the principles and features of each process is crucial in determining which one fits best for a particular project.
- Process Principles
- Double-shot injection molding involves injecting two different materials into the same mold to create complex products in one cycle. Imagine creating a tool with a hard plastic body and a soft, comfy grip – this is where double-shot stands out!
- Secondary molding, on the other hand, uses pre-molded parts as substrates, allowing for additional materials or shape alterations through subsequent processes. I remember using secondary molding to add a rubber coating to a product – what a change it brought to its look and function!
Evaluating Mold Features
The complexity of the molds used in these processes can significantly impact production efficiency and product quality. Here’s how they compare:
Feature | Double-shot Injection Molding | Secondary Molding |
---|---|---|
Mold Complexity | High, due to rotating/sliding mechanisms | Variable, often simpler than double-shot |
Runner System Design | Requires precise runner systems for material flow | Less critical, but depends on process used |
Material Compatibility | High compatibility with different materials | Depends on second process and materials |
Assessing Process Advantages
Understanding the advantages of each process can guide designers in making informed decisions:
- Double-shot injection molding offers:
- High production efficiency with complex material combinations. Parts stay strongly joined, making it perfect for durable items!
- Strong integrity between joined parts, ideal for products requiring durability.
- Secondary molding provides:
- Flexibility to enhance existing products with additional features or aesthetics. This process lets me improve existing designs without starting over. Combining techniques can lead to really innovative products.
- Combines benefits from various molding techniques, such as the precision of injection molding with the adaptability of thermoforming.
Considerations for Material Properties
Designers should also consider how material properties affect product functionality:
- In double-shot injection molding, different hardness levels and colors can be achieved in one part, which is beneficial for ergonomic designs like tools with soft grips. I’ve used this technique to create comfortable products.
- Secondary molding allows for enhancements like metal reinforcements or special coatings that can improve durability and appearance. Each layer gives the product a new dimension!
Project Requirements and Goals
Finally, aligning the choice of process with project goals is essential:
- For projects needing high integration and good looks, I often choose double-shot molding. It meets all the needs for complex designs.
- If flexibility or post-molding function is needed, secondary molding might be my usual choice depending on what best fits the project’s needs.
For further insights into these processes, you can explore detailed articles about double-shot injection molding7 and secondary molding techniques8. These resources have helped me throughout my career!
Double-shot molding allows for complex product designs in one cycle.True
This process enables the creation of intricate products by injecting two materials simultaneously, enhancing design capabilities.
Secondary molding is always simpler than double-shot molding.False
While secondary molding often uses simpler molds, it can vary based on the specific processes and requirements involved.
Conclusion
Learn about the differences between two-shot injection molding and overmolding, including their processes, benefits, applications, and cost considerations for effective product design.
-
Explore this link for a deeper understanding of advanced techniques in two-shot injection molding and how they can optimize your production. ↩
-
This link provides deeper insights into the overmolding process and its advantages, essential for any designer looking to innovate. ↩
-
Learn more about secondary molding techniques and how they can enhance existing products, adding value and functionality. ↩
-
Clicking this link will help you find detailed calculators tailored to assess molding costs accurately based on your specific parameters. ↩
-
This link provides deeper insights into injection molding costs, allowing you to understand the financial impact better. ↩
-
Discover expert insights on selecting the right molding process to enhance your product designs effectively. ↩
-
This link will provide you with a deeper understanding of design processes and help refine your decision-making skills. ↩
-
Explore this resource to learn more about secondary molding processes and their applications. ↩