Imagine a world where you can double your output without doubling your effort. Welcome to the realm of injection molding where producing two parts in one mold is not just a dream—it’s a reality!
Yes, it is possible to produce two distinct parts in one mold using injection molding. This approach leverages multi-cavity or family molds to enhance production efficiency, reduce costs, and streamline processes by simultaneously molding two parts within the same cycle.
But hold on! While this technique sounds enticing, it comes with its own set of challenges. Let’s dive into the details that can make or break your production success.
Two parts can be produced in one mold using injection molding.True
Multi-cavity or family molds allow simultaneous production of two parts.
What Are Multi-Cavity and Family Molds?
In the world of injection molding, multi-cavity and family molds offer innovative solutions for efficient production.
Multi-cavity molds feature multiple identical cavities for producing the same part, while family molds contain cavities for different parts. Both aim to increase efficiency by manufacturing multiple components in a single molding cycle, but each serves different needs in production.
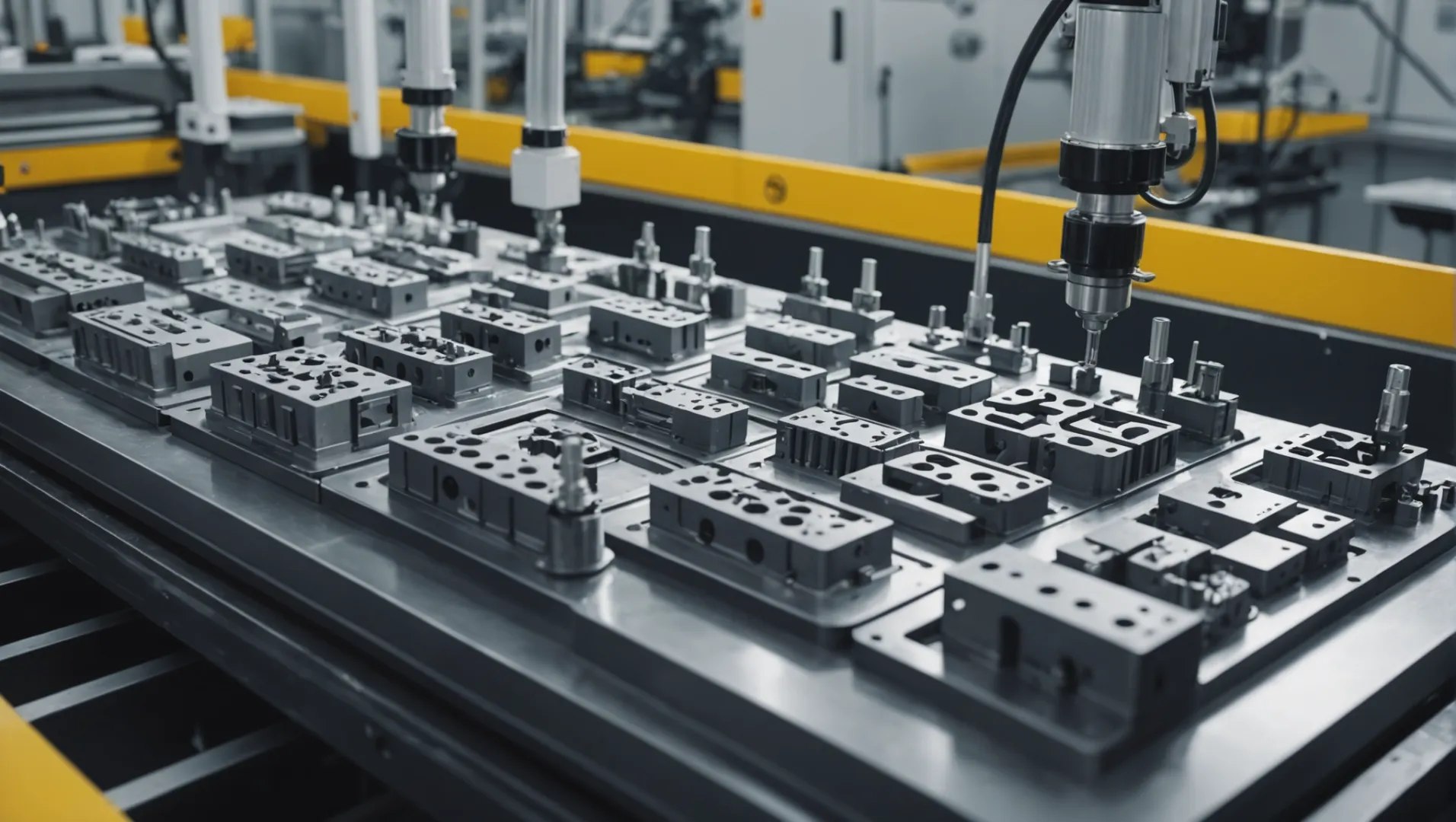
Understanding Multi-Cavity Molds
Multi-cavity molds are designed with several identical cavities, allowing manufacturers to produce multiple copies of the same part in one injection cycle. This method is ideal for high-volume production, as it significantly boosts efficiency and reduces per-unit costs. By optimizing the cycle time, it ensures consistent quality across all parts.
Advantages of Multi-Cavity Molds:
- Increased Productivity: Producing multiple parts simultaneously reduces cycle time and increases output.
- Cost Efficiency: The cost per part decreases as production volume increases, making it economically viable for large-scale operations.
- Uniform Quality: With identical cavities, multi-cavity molds maintain consistent quality across all units.
Exploring Family Molds
Family molds take a different approach by featuring cavities that produce different parts in a single cycle. This technique is particularly beneficial for products that require multiple components to be manufactured together, such as parts of an assembly or product line.
Benefits of Family Molds:
- Versatile Production: Ideal for producing sets of related components, reducing the need for multiple molds.
- Material Savings: Allows for the efficient use of materials by reducing waste during the molding process.
- Simplified Logistics: Reduces the complexity of coordinating the production of separate components.
Choosing Between Multi-Cavity and Family Molds
Selecting between multi-cavity and family molds depends on several factors, including production volume, part design, and material use. For instance, understanding mold design principles1 is crucial when deciding which mold type aligns with your manufacturing goals.
Both mold types require careful consideration of design intricacies and process optimization to achieve the desired efficiency and quality. Balancing these elements is essential to capitalize on the benefits each mold type offers.
Multi-cavity molds increase production efficiency.True
Multi-cavity molds produce multiple parts simultaneously, reducing cycle time.
Family molds are best for identical part production.False
Family molds produce different parts in one cycle, not identical ones.
How Does Mold Design Affect Two-Part Production?
Mold design is a pivotal factor in efficiently producing two parts simultaneously using injection molding technology.
Mold design significantly impacts the quality, efficiency, and cost-effectiveness of producing two parts in a single cycle. A well-designed mold enables simultaneous production while ensuring precision, dimensional accuracy, and structural integrity.
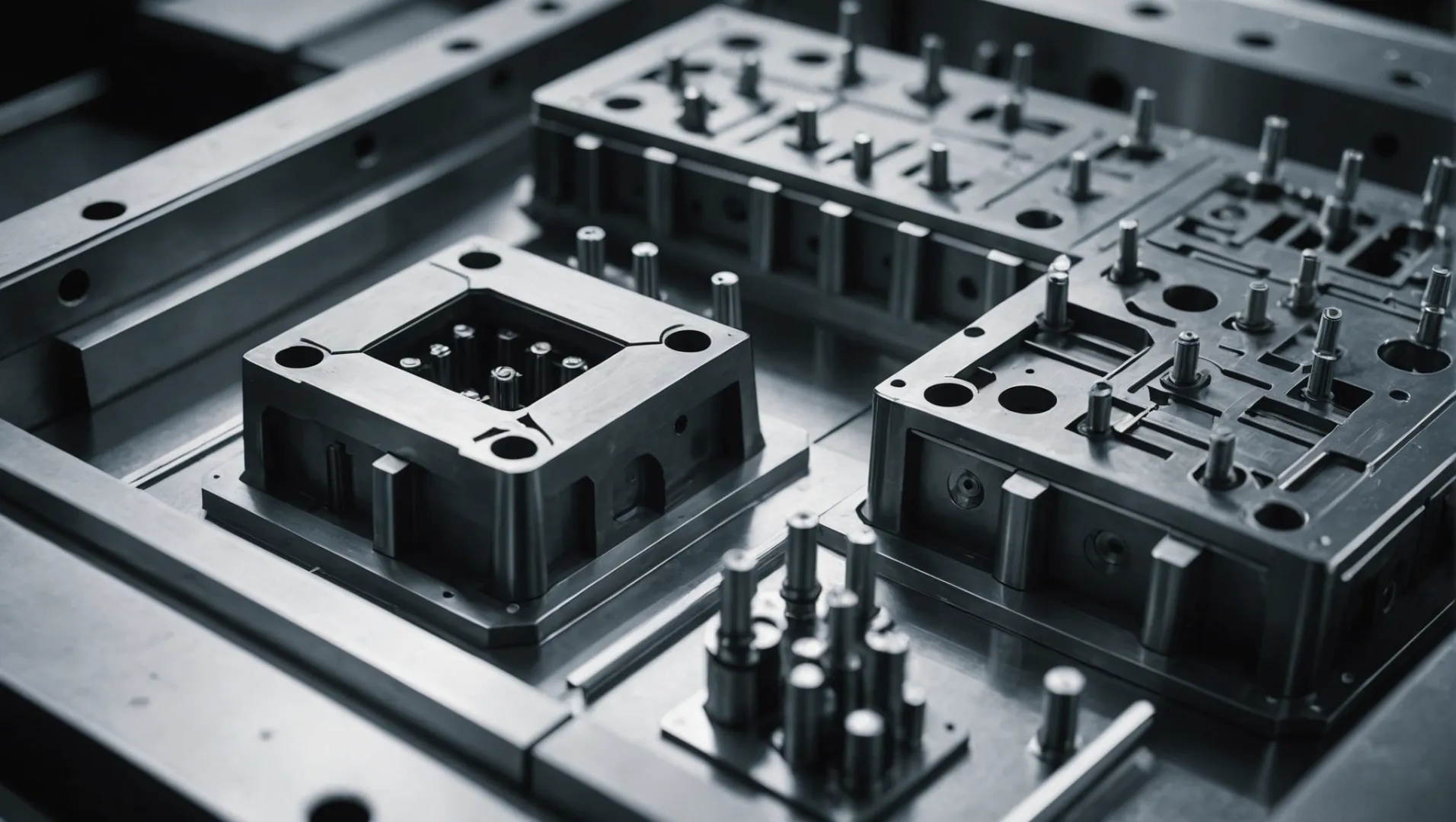
The Role of Mold Design in Two-Part Production
In the realm of injection molding2, mold design stands as a cornerstone. A thoughtfully designed mold can house multiple cavities, known as multi-cavity molds, or it can facilitate the creation of two different parts simultaneously, termed family molds. This design choice influences how efficiently the production line operates and the quality of the final products.
Efficiency and Cost Reduction
A properly designed mold can yield two parts within a single injection cycle. This dual production capability streamlines operations, leading to notable reductions in production time and costs. Manufacturers can increase throughput and optimize resource use by minimizing machine downtime and labor efforts.
Aspect | Single-Part Mold | Two-Part Mold |
---|---|---|
Production Cycle | Single part per cycle | Two parts per cycle |
Time Efficiency | Standard | Improved |
Cost Efficiency | Moderate | Enhanced |
Simplification Through Symmetry
For parts that are similar or symmetrical, mold design can be simplified by sharing sections of the mold structure. This not only decreases the complexity involved in creating multiple distinct molds but also ensures consistent quality across products due to shared design features.
Challenges in Mold Design for Two-Part Production
While advantageous, designing molds for two-part production is not without its hurdles. One primary concern is ensuring that both parts meet stringent quality and dimensional accuracy standards. This requires meticulous attention to detail during the mold design phase and subsequent manufacturing.
Another challenge lies in optimizing injection molding process parameters, such as temperature, pressure, and cooling times, to accommodate two different parts. This complexity can require significant trial and error, demanding expertise and precision to achieve optimal results.
Moreover, any defect in one part can potentially disrupt the production of the other, necessitating rigorous quality control measures to mitigate risks. Thus, comprehensive planning and execution are crucial to successful two-part production using injection molding.
Mold design affects injection molding efficiency.True
A well-designed mold can produce two parts simultaneously, enhancing efficiency.
Family molds produce only one part per cycle.False
Family molds are designed to produce two different parts in one cycle.
What Are the Challenges of Simultaneous Molding?
Simultaneous molding offers efficiency but comes with unique challenges that must be navigated carefully.
Simultaneous molding can increase production efficiency but presents challenges in mold design, process parameter adjustment, and quality control.
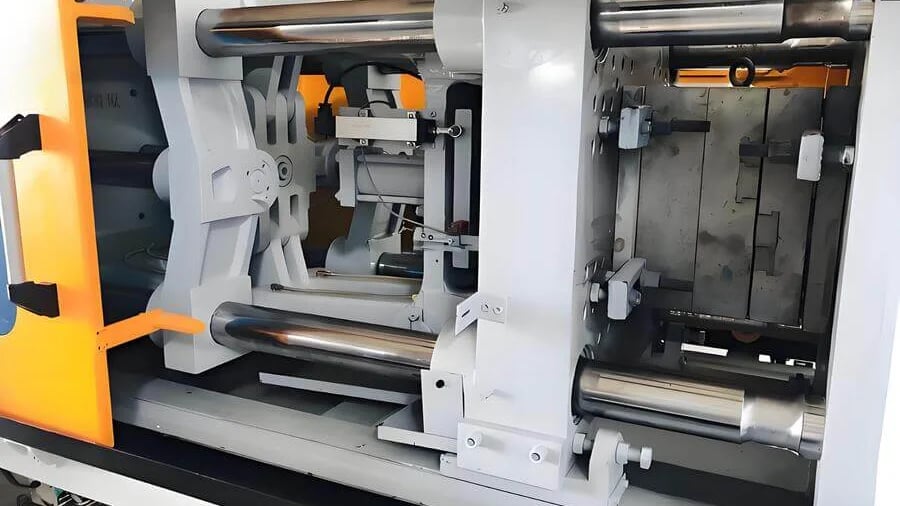
Complexity in Mold Design
Simultaneously molding two parts requires precise mold design3. The shared mold cavity must accommodate the specific geometry of both parts, maintaining structural integrity while allowing efficient material flow. Engineers often face increased complexity as they aim to balance the structural demands with production efficiency.
- Dimensional Accuracy: Achieving high accuracy is crucial, as any deviation can affect both parts’ functionality.
- Material Flow: Proper gating and venting are essential to ensure uniform distribution of molten plastic.
The intricacies of mold design demand expertise and innovative approaches to mitigate these challenges.
Process Parameter Optimization
Adjusting injection molding parameters4 is another critical area. The parameters must be fine-tuned to cater to the unique requirements of each part, which may differ significantly.
- Temperature Control: Consistent temperature is vital for uniform cooling and solidification.
- Pressure Adjustments: Different parts may require varied pressures for optimal molding.
These adjustments ensure that neither part suffers in quality or performance due to incompatible settings.
Quality Control Concerns
Maintaining strict quality control is imperative in simultaneous molding. If one part exhibits defects, it could affect the entire production batch. Thus, robust quality checks must be integrated into the process.
- Inspection Techniques: Utilize advanced inspection methods to identify defects early.
- Feedback Systems: Implement feedback loops to continuously monitor and adjust production parameters.
Simultaneous molding presents a nuanced balance of efficiency and complexity, requiring careful planning and execution to overcome its challenges. Understanding these complexities5 is essential for successful implementation.
Simultaneous molding always improves production efficiency.False
While it can improve efficiency, challenges in design and control may negate benefits.
Mold design complexity increases with simultaneous molding.True
Designing for two parts requires precise geometry and material flow management.
How Can Quality Control Be Ensured in Two-Part Molding?
Ensuring high-quality outcomes in two-part molding requires meticulous attention to various quality control measures.
Quality control in two-part molding can be ensured through precise mold design, stringent process parameter monitoring, and regular inspection. Implementing these measures helps maintain dimensional accuracy and prevent defects, thereby ensuring the reliability and consistency of the molded parts.
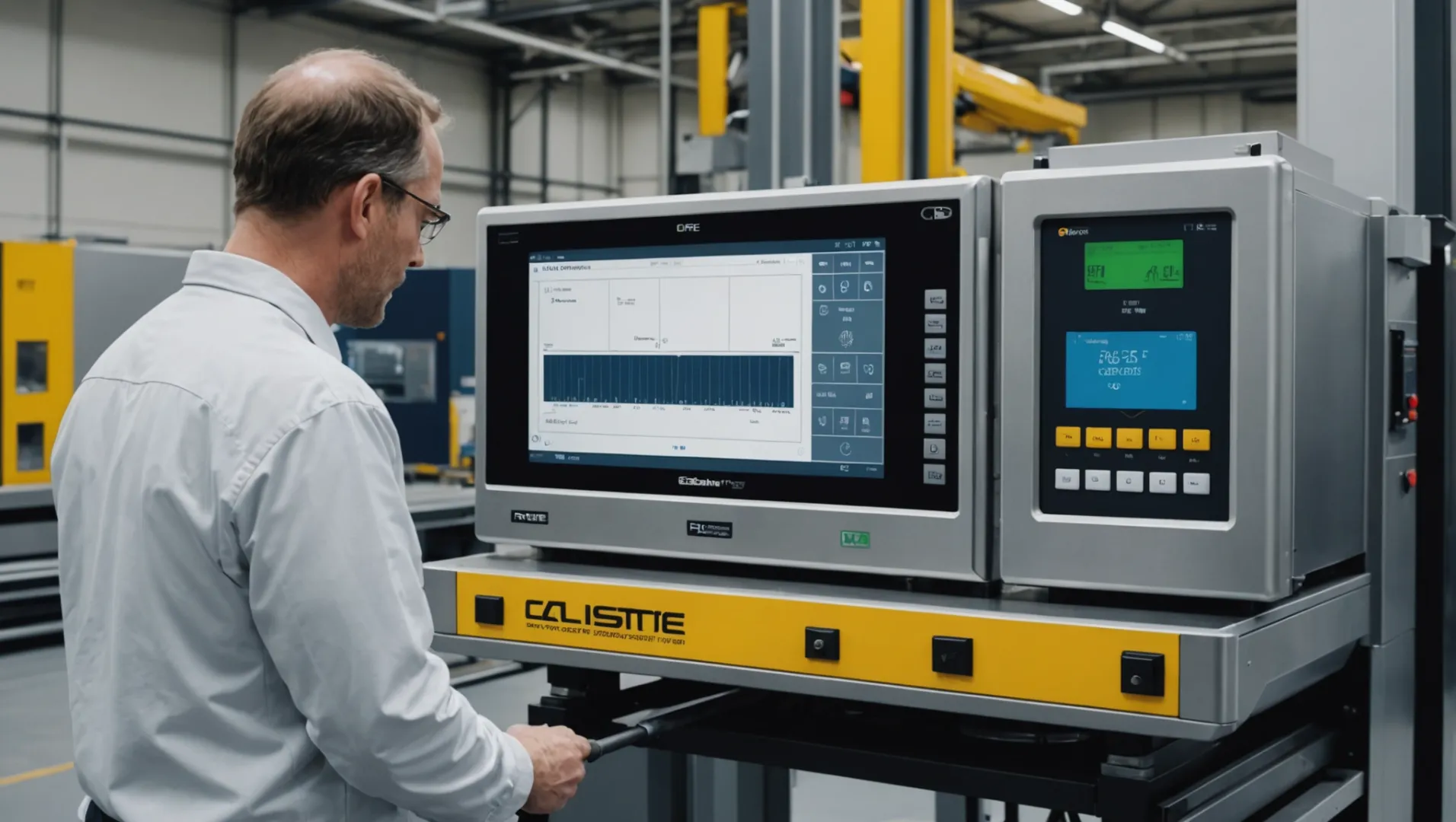
Importance of Precise Mold Design
The foundation of quality control in two-part molding6 lies in meticulous mold design. A well-designed mold must account for the shape and size of both parts, ensuring they align perfectly. This includes detailed attention to the gate location, runner system, and cooling channels, which are critical for achieving uniformity and minimizing defects.
Careful planning during the design phase reduces the likelihood of common issues such as warping or incomplete filling. Using CAD software to simulate the mold design can help anticipate potential problems and make necessary adjustments before production begins.
Monitoring Process Parameters
Once the mold is designed, maintaining strict control over the injection molding process parameters is crucial. Key parameters include:
- Temperature: Both the mold temperature and the melting temperature of the plastic need to be optimized.
- Pressure: Injection and holding pressures must be accurately calibrated to ensure complete filling and minimize flash.
- Cycle Time: Proper cycle timing prevents overheating and ensures adequate cooling.
Regular monitoring of these parameters helps in identifying deviations that could lead to defects. Automated systems can assist by providing real-time data, allowing for quick adjustments.
Parameter | Ideal Range | Impact on Quality |
---|---|---|
Temperature | Depends on material used | Affects flow and solidification |
Pressure | Varies with material and part | Influences dimensional accuracy |
Cycle Time | Based on part size and material | Ensures proper cooling |
Regular Inspection and Testing
Incorporating a robust inspection regimen is essential for ensuring quality in two-part molding. This involves:
- Visual Inspection: Checking for visible defects such as flash, burn marks, or sink marks.
- Dimensional Checks: Using tools like calipers or coordinate measuring machines (CMMs) to verify that parts meet specified tolerances.
- Functional Testing: For parts intended to perform specific functions, testing under simulated conditions is necessary.
These inspections should be conducted at regular intervals throughout production to catch any discrepancies early. Maintaining detailed records helps in tracing back any issues to their source, facilitating corrective actions.
Implementing these quality control strategies not only enhances product reliability but also streamlines production by reducing waste and rework.
Precise mold design prevents warping.True
Accurate mold design ensures uniformity, reducing warping risks.
Cycle time doesn't affect cooling.False
Proper cycle timing is crucial for ensuring adequate cooling.
Conclusion
Producing two parts in one mold is a viable strategy in injection molding, offering efficiency and cost benefits. However, careful consideration of design and process parameters is essential for success.
-
Gain insights into choosing the right mold type for your needs.: Unlike multi-cavity molds, family molds don’t produce identical parts. They instead allow for the production of multiple related parts within a … ↩
-
Understand the basics of injection molding and its industrial applications.: With injection molding, molten plastic is injected into a mold cavity under high pressure, creating a part all at once. Both processes are … ↩
-
Discover mold design strategies for efficient simultaneous production.: The same general guidelines used for developing a single-cavity co-injection mold cannot be fully applied to the design of a multi-cavity co- … ↩
-
Learn how to adjust parameters for dual-part injection molding.: The third optimized process parameter is the packing pressure, which is mainly used to avoid shrinkage or overpacking of the parts. ↩
-
Explore methods to ensure quality in simultaneous molding.: In this study, we investigated the suitability of in-mold pressure sensors to control the injection molding process in multi-cavity molds. ↩
-
Discover how precise mold design ensures quality in two-part molding.: The quality and make of the mold allows injection molders to ensure high tolerance, identify defects, maintain precision, choose the right raw materials, as … ↩