Creating transparent products with injection molding feels like crafting a masterpiece, blending skill with precision.
To produce transparent injection-molded products, select quality materials like polycarbonate or acrylic, ensure precise mold design with smooth finishes, and control molding temperatures and pressures to enhance clarity and reduce defects.
Having dabbled in the world of injection molding myself, I remember the first time I tackled a transparent product. It was a mixture of excitement and nervous anticipation. You see, understanding the basics is just the tip of the iceberg. Each material behaves differently under pressure and heat, and the devil is truly in the details. By diving deeper into each step—like selecting the right material or mastering mold design—I’ve been able to refine my process significantly. Stick around as I share detailed insights and a few hard-earned tips that could make your transparent products shine.
Polycarbonate is ideal for transparent injection molding.True
Polycarbonate is often used for its clarity and strength in molding.
High temperatures reduce clarity in injection molding.True
Excessive heat can cause discoloration and defects in the material.

What Materials Are Best for Transparent Injection Molding?
You know that feeling when you finally find the perfect material for your project? That’s what transparent injection molding can do for you!
The best materials for transparent injection molding include polycarbonate, acrylic, and PMMA, each providing excellent clarity and durability for diverse applications.
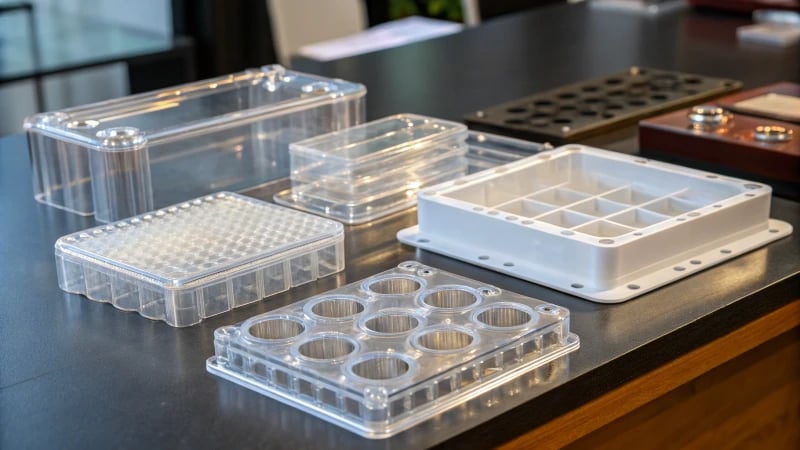
Polycarbonate: A Balance of Clarity and Strength
Remember the time when I dropped my phone, and it survived without a scratch? That’s because of its polycarbonate cover. Polycarbonate is not just tough—it’s practically unbreakable. Whether you’re designing safety glasses1 or LED light covers, this material offers the perfect mix of transparency and resilience. However, a word of caution: it can scratch easily if not coated.
Property | Polycarbonate |
---|---|
Clarity | High |
Impact Resistance | Excellent |
UV Stability | Moderate |
Acrylic: The Clear Choice for Aesthetics
I remember crafting a display case with acrylic for my daughter’s science fair project. It looked so sleek and professional! Acrylic, or PMMA, shines with its high-gloss finish and crystal-clear transparency, making it ideal for visually striking items. But keep in mind, its lower impact resistance means it’s best suited for less demanding applications.
Property | Acrylic |
---|---|
Clarity | Very High |
Impact Resistance | Moderate |
UV Stability | Good |
PMMA: A Versatile and Cost-Effective Option
I’ve always appreciated how PMMA combines cost-effectiveness with outstanding optical properties. Think about those stunning automotive lenses2 that you can’t help but admire—PMMA makes them possible. While not as impact-resistant as polycarbonate, its weatherability makes it a solid choice for applications exposed to the elements.
When selecting the right material for your project, it’s crucial to consider clarity, strength, and cost. Polycarbonate offers unmatched durability; acrylic provides superior aesthetics; and PMMA balances affordability with excellent performance. Dive into material properties3 to understand how each option fits your specific needs.
By diving deeper into these materials and understanding their unique benefits, you can enhance both the performance and appeal of your products. Don’t hesitate to reach out to industry experts or explore comprehensive material databases4 for more insights.
Choosing the right material significantly impacts your final product’s appearance and longevity. Make informed decisions by considering all factors involved.
Always stay updated with new advancements in material science to keep your designs innovative and competitive.
For personalized guidance, connect with suppliers or industry experts who can offer advice tailored to your project’s unique requirements. Industry forums5 are also excellent resources for shared experiences and insights.
Continue exploring these materials to ensure your design process remains efficient and aligned with modern manufacturing demands.
Happy designing! Stay curious, stay inspired!
Polycarbonate is prone to scratching without coating.True
Polycarbonate has excellent clarity and impact resistance but scratches easily.
Acrylic has higher impact resistance than polycarbonate.False
Acrylic offers superior aesthetics but lower impact resistance than polycarbonate.
How does mold design impact product transparency?
Have you ever wondered why some plastic products are crystal clear while others aren’t? The secret often lies in the mold design.
Mold design affects product transparency by managing material flow, surface finish, and cooling rate, ensuring even spread, reducing flow lines, and enhancing clarity in transparent items.
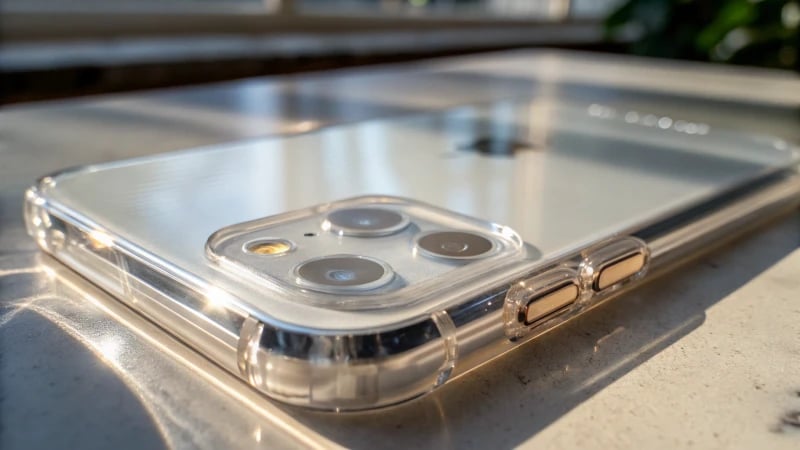
Material Flow and Uniformity
I remember the first time I held a perfectly clear plastic casing in my hands. It was mesmerizing, almost like holding a piece of glass. That’s when I realized how crucial mold design is in achieving such transparency. The way material flows through a mold can make or break the clarity of a product. An efficient mold design ensures smooth material flow6 throughout the cavity, minimizing those pesky flow and weld lines that can mess with the product’s optical clarity.
Example: Gate Location
One of my early mentors taught me about the magic of gate location. By strategically placing gates where they promote even filling, we can avoid excessive shear stress that might cloud the material. It’s like orchestrating a symphony where every note needs to hit perfectly for that flawless clarity and surface finish7.
Design Aspect | Impact on Transparency |
---|---|
Gate Location | Reduces shear, improves clarity |
Flow Channels | Ensures uniform distribution |
Surface Finish Considerations
Then there’s the surface finish. Imagine polishing a mold until it shines like a mirror. A polished mold surface reduces friction during injection, leading to a smoother finish on the final product. I’ve found that maintaining a high-quality mold surface8 is absolutely essential when you’re aiming for crystal-clear products.
Cooling Rate Management
Cooling is another beast altogether. During one of my projects, we struggled with maintaining clarity due to uneven cooling rates. It’s all about balance—cooling too fast or too slow can lead to defects. A well-designed cooling system prevents warping and opacity issues by managing crystallization in materials like polycarbonate.
- Uniform Cooling: Achieves consistent clarity across the product.
- Controlled Crystallization: Maintains optical properties by managing material structure.
Understanding cooling dynamics9 became my go-to strategy for refining transparent products.
Advanced Design Techniques
In today’s tech-savvy world, I can’t imagine designing molds without computer-aided engineering (CAE). These tools simulate material flow and cooling processes, allowing us to predict transparency issues before they become real-world headaches. This proactive approach has saved me countless hours and resources, ensuring transparency isn’t just an afterthought but a core element of the design process.
Utilizing CAE tools not only enhances efficiency but also ensures that transparency remains uncompromised throughout the manufacturing process.
Conclusion
Mold design is like an art form—it demands attention to detail in material flow, surface finish, and cooling rates to influence product transparency. By leveraging advanced design techniques and tools, we can optimize these factors to achieve products that are not just clear but strikingly beautiful.
Gate location affects material clarity in mold design.True
Strategic gate placement reduces shear stress, improving clarity.
Cooling rates have no impact on product transparency.False
Uneven cooling can cause warping, affecting transparency.
How Can You Ensure Crystal Clarity in Injection-Molded Products?
Ever wondered how to make injection-molded products crystal clear? Dive into techniques that bring transparency to life and see how small tweaks can lead to big results.
To ensure clarity in injection-molded products, select appropriate materials, design precise molds, and carefully control temperature and pressure during production to minimize defects and enhance transparency.
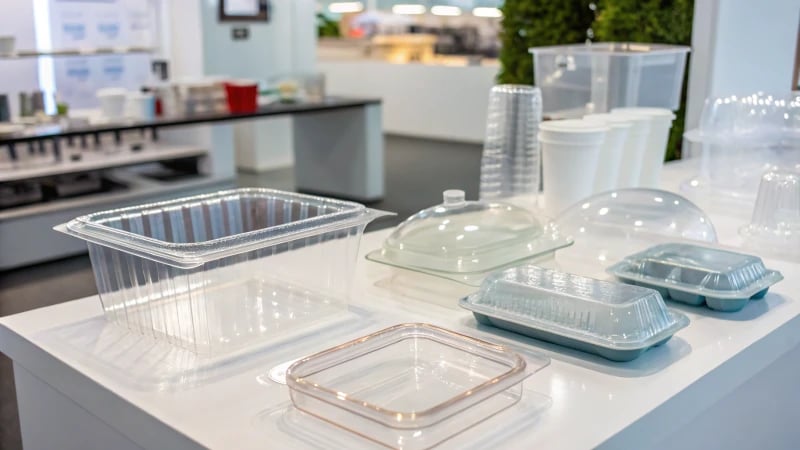
Material Selection for Transparency
I remember the first time I had to choose materials for a project that demanded perfect clarity. It was daunting! But then, I discovered the wonders of clear thermoplastics like polycarbonate and acrylic. These materials are renowned for their superior light transmission, which is a game-changer for anyone needing that glass-like finish.
Material | Clarity | Impact Resistance |
---|---|---|
Polycarbonate | Excellent | High |
Acrylic | Good | Moderate |
When you’re looking at options, it’s worth reviewing material properties10 to see which will meet your needs best.
Mold Design Considerations
Once, while working late on a mold design, I realized the importance of smooth mold surfaces. A tiny scratch can ruin the clarity we’ve worked so hard for. Since then, I’ve always emphasized polished molds and effective venting systems to avoid air traps. Utilizing CAD tools early on can help simulate potential issues before they become costly mistakes. I recommend diving into advanced mold design techniques11 to improve product clarity.
Process Parameter Optimization
I’ve learned that controlling temperature and pressure is like balancing on a tightrope. High temperatures can enhance material flow but push too far, and you risk degradation. It’s all about finding that sweet spot, and using process simulation software12 can be invaluable in tweaking these parameters for optimal clarity.
Testing and Quality Control
Testing isn’t just about ticking boxes; it’s our assurance that we’ve hit our clarity targets. I remember feeling a huge relief when my first batch passed visual inspections and light transmission tests without a hitch. It’s these rigorous standards that help maintain quality. For anyone in the field, following guidelines on quality testing13 is a must to ensure your production line consistently delivers top-notch results.
Polycarbonate has higher clarity than acrylic.True
Polycarbonate is known for its excellent clarity, surpassing acrylic.
High temperatures always improve material flow in molding.False
While high temperatures can improve flow, excessive heat may cause degradation.
Which Industries Thrive on Transparent Injection Molding?
Ever wondered how transparent injection molding can transform industries from mundane to extraordinary? Let me share some insights on which sectors are revolutionized by this technology.
Transparent injection molding benefits medical devices, consumer electronics, and automotive industries by providing essential clarity, precision, and durability for both aesthetic and functional applications.
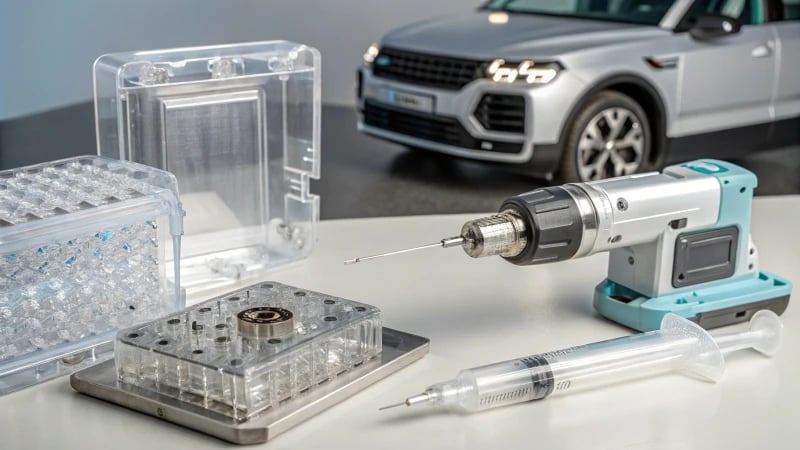
Medical Devices
I remember visiting a friend’s lab where they were working on cutting-edge medical devices14. They showed me a prototype of a syringe with a perfectly clear body, enabling nurses to easily monitor medication flow. It was fascinating to see how transparency wasn’t just about aesthetics but crucial for safety and efficiency.
Key Benefits:
- Clarity: Helps with visual inspections.
- Biocompatibility: Ensures safe interaction with biological systems.
Consumer Electronics
When I was working on a project in consumer electronics15, the team was obsessed with creating sleek yet durable smartphone cases. Transparent injection molding came to our rescue, allowing us to maintain a modern look without compromising strength. Products like LED screens also benefit, as this process enhances light transmission, making screens more vibrant.
Product Type | Benefit |
---|---|
Smartphone Cases | Aesthetic appeal, durability |
LED Screens | Enhanced light transmission |
Automotive Industry
In my discussions with colleagues in the automotive sector16, transparent parts were often highlighted. I was intrigued by how light covers made through this process improved visibility and safety. Dashboards crafted this way offered not just a sleek design but also ensured all components fit seamlessly.
- Light Covers: Improved visibility and safety.
- Dashboards: Sleek design with integral functionality.
Packaging Industry
My visit to a packaging expo opened my eyes to how transparent injection molding is transforming the packaging industry. Imagine picking up a beautifully clear cosmetics jar that instantly boosts the product’s appeal. In food packaging, clear materials like PET help consumers easily identify products, enhancing trust and buying decisions.
- Food Packaging: Visibility aids in product identification.
- Cosmetics: Aesthetic packaging boosts brand image.
Transparent injection molding isn’t just a technique; it’s a bridge to innovation across industries. It allows us to push boundaries by enhancing both form and function. I find it exciting to see how each sector uniquely utilizes this technology to stay competitive and deliver better products.
Transparent injection molding is essential for medical devices.True
It ensures clarity and biocompatibility, crucial for safe medical tools.
Automotive industry rarely uses transparent injection molding.False
It is used for light covers and dashboards, enhancing visibility and design.
Conclusion
Learn how to produce transparent products using injection molding by selecting the right materials, optimizing mold design, and controlling process parameters for clarity and durability.
-
Discover how polycarbonate enhances safety glasses with impact resistance. ↩
-
Learn why PMMA is preferred for automotive lenses due to its optical properties. ↩
-
Access comprehensive databases detailing various materials’ properties. ↩
-
Find expert advice on selecting materials tailored to project needs. ↩
-
Join forums for shared experiences and insights from industry professionals. ↩
-
This link explains how smooth material flow in molds reduces defects that impair transparency. ↩
-
Learn how proper gate placement improves clarity by reducing shear stress. ↩
-
Discover how maintaining a polished mold surface enhances product clarity. ↩
-
Understand how managing cooling rates can prevent opacity issues in plastics. ↩
-
This link provides an overview of material properties, helping you choose the right one for clarity. ↩
-
Explore advanced techniques that can enhance clarity through improved mold design. ↩
-
Simulation software helps optimize process parameters to enhance product clarity. ↩
-
These guidelines ensure your products meet clarity and quality standards consistently. ↩
-
Explore how medical devices benefit from transparent materials for better performance and safety. ↩
-
Discover how transparency enhances design and functionality in consumer electronics. ↩
-
Learn how automotive manufacturers use transparency for both aesthetic and practical purposes. ↩