Have you ever wondered how a seemingly simple plastic part comes to life? The answer lies in a fascinating process called injection molding, where each step counts—especially at the transfer position.
The transfer position in injection molding refers to the mold cavity point where the plastic melt transitions from the injection nozzle through the runner system into the mold. It plays a crucial role in switching from filling to packing stages, affecting the product’s quality.
While this provides a fundamental understanding, exploring the intricate details of the transfer position offers insights into process optimization and troubleshooting common issues. Dive deeper to enhance your knowledge of this essential aspect of injection molding.
Transfer position marks the transition from filling to packing.True
In injection molding, it signals the shift between these stages.
What is the Role of Transfer Position in Injection Molding?
The transfer position in injection molding is a critical point that influences the entire manufacturing process.
In injection molding, the transfer position marks where the plastic melt moves from filling to packing within the mold cavity, crucial for quality control.
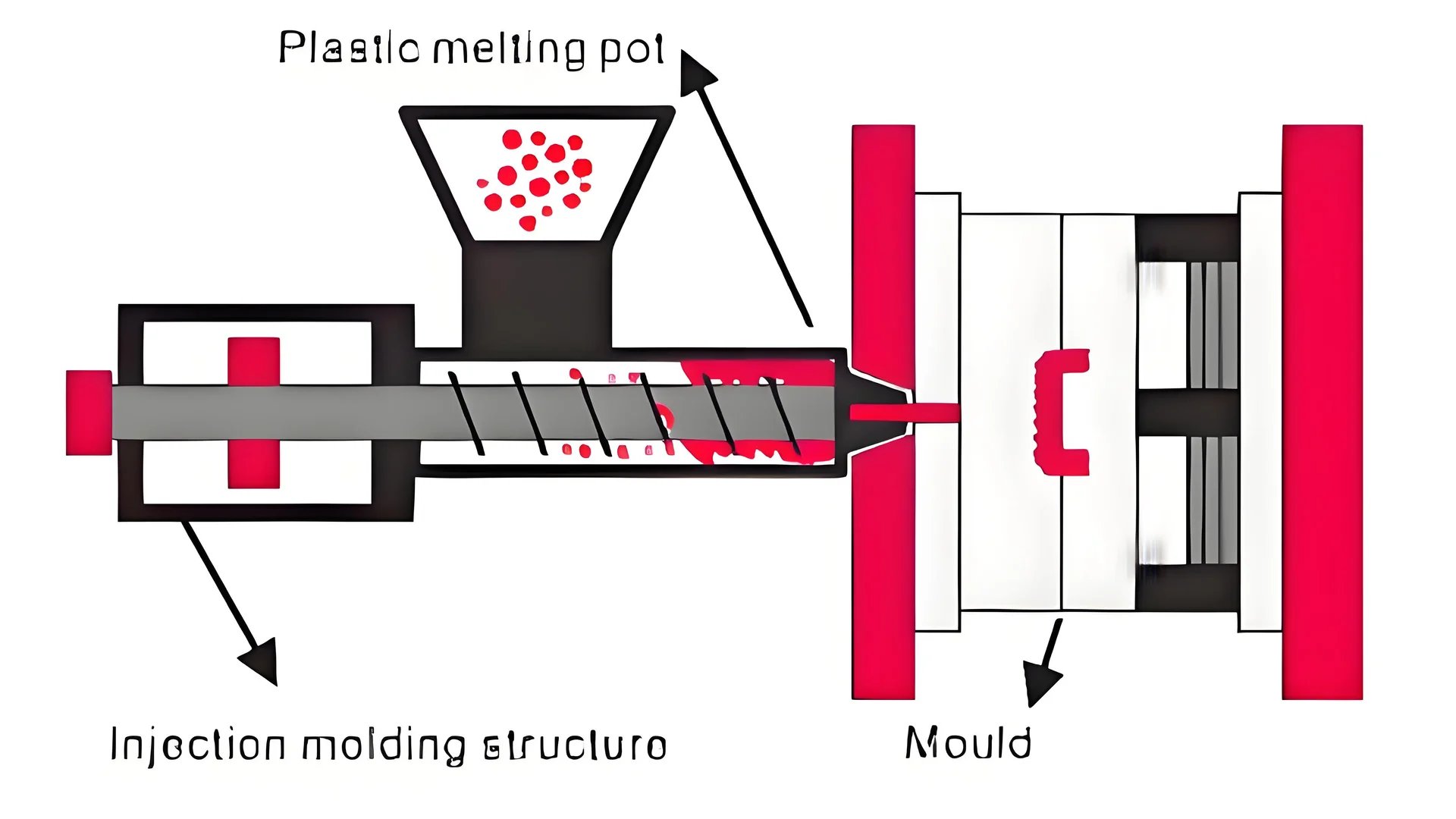
Understanding the Transfer Position’s Importance
In the complex landscape of injection molding, the transfer position1 is not just a procedural checkpoint but a linchpin of the process. It refers to the precise location in the mold cavity where the molten plastic transitions from the injection nozzle, traversing through the runner system and finally entering the mold cavity. This position is pivotal as it signifies when the injection phase transitions to the packing phase, ensuring the right amount of material fills the mold before cooling and solidifying.
Monitoring Process Parameters
The role of the transfer position extends to controlling key parameters in injection molding. Once the melt reaches this point, it signals a shift from high-speed injection to a more controlled packing stage. This transition is essential for adjusting parameters such as injection pressure, speed, and timing.
- Injection Pressure: Adjusting pressure at this stage ensures that any residual material is compacted correctly, reducing defects.
- Injection Speed: A reduction in speed helps in managing the flow and prevents overshooting beyond the desired volume.
Enhancing Product Quality
The transfer position’s impact on quality cannot be overstated. By facilitating a smooth transition between stages, it plays a crucial role in maintaining dimensional accuracy and preventing common defects such as short shots or flash.
Parameter | Impact on Quality |
---|---|
Pressure | Ensures full cavity fill |
Speed | Prevents overshoot |
Time | Manages solidification rate |
Troubleshooting with Transfer Position
Engineers leverage insights from observing how and when the melt reaches this position to troubleshoot issues like bubbles and voids. If problems are detected at this stage, it can indicate whether there’s a need for system adjustments or optimizations. For instance, if the melt does not reach the transfer position smoothly, it may lead to inconsistencies that affect final product quality.
Through comprehensive monitoring and adjustment at this critical juncture, engineers can enhance production efficiency and ensure high-quality output in injection molding.
Transfer position marks transition to packing phase.True
The transfer position indicates the shift from injection to packing.
Transfer position has no impact on product quality.False
It is crucial for maintaining dimensional accuracy and reducing defects.
How Does Transfer Position Affect Product Quality?
Understanding transfer position is crucial for ensuring quality in injection molding processes.
Transfer position in injection molding affects product quality by determining the transition from the filling to packing stage, influencing factors like dimensional accuracy and defect rates.
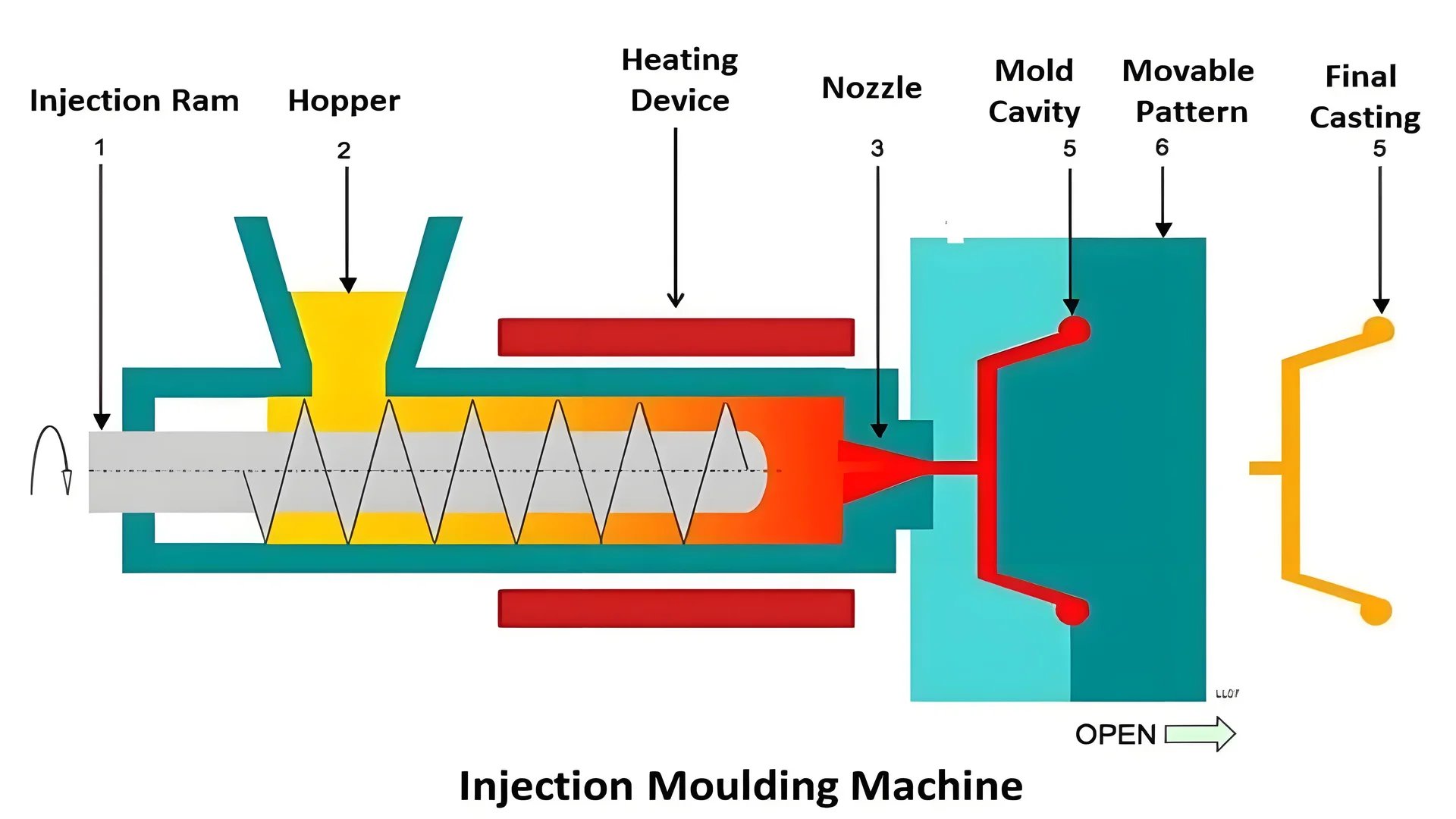
Understanding Transfer Position in Injection Molding
The transfer position refers to a critical point in the injection molding cycle where the plastic melt moves through the runner system to enter the mold cavity. It is not merely a physical location but a pivotal stage in the molding process that determines how well the material fills the cavity and transitions into the packing stage.
Impact on Product Quality
The quality of a molded product is significantly influenced by how effectively the transfer position is managed. The precise control of this transition can affect:
- Dimensional Accuracy: Proper management ensures that the melt fills the mold completely, reducing shrinkage and warping.
- Surface Finish: A well-handled transfer can minimize defects such as flash or surface blemishes.
- Structural Integrity: Ensures that parts are solidified without internal stresses or voids.
Factors Influencing Transfer Position
Several parameters must be fine-tuned to optimize the transfer position:
- Injection Pressure and Speed: These must be adjusted to ensure the melt reaches the transfer position smoothly, without causing defects like short shots or overpacking.
- Timing: Correct timing in switching from filling to packing is crucial. Delays can result in improper cooling and potential defects.
Parameter | Impact on Quality |
---|---|
Injection Pressure | Controls flow and fill rate, impacting strength and finish. |
Speed | Affects material distribution and cooling time. |
Timing | Influences shrinkage rates and dimensional stability. |
Troubleshooting Transfer Position Issues
Common issues such as short shots, flashes, or bubbles often arise at this stage. Engineers use monitoring systems to observe how the melt reaches and behaves at the transfer position. By analyzing these patterns, adjustments can be made to optimize performance.
For instance, if a part displays shrinkage issues2, engineers might adjust pressure settings to ensure even material distribution. Observations during this phase are instrumental in diagnosing and solving production challenges, ensuring a higher quality end product.
Transfer position affects injection molding product quality.True
It determines the transition from filling to packing, impacting quality.
Timing in transfer position doesn't impact shrinkage rates.False
Correct timing influences shrinkage rates and dimensional stability.
What Common Issues Arise at the Transfer Position?
Understanding issues at the transfer position is key to optimizing the injection molding process and ensuring high-quality outputs.
Common issues at the transfer position include short shots, flash, and bubbles, often caused by improper parameter settings or mold design errors.
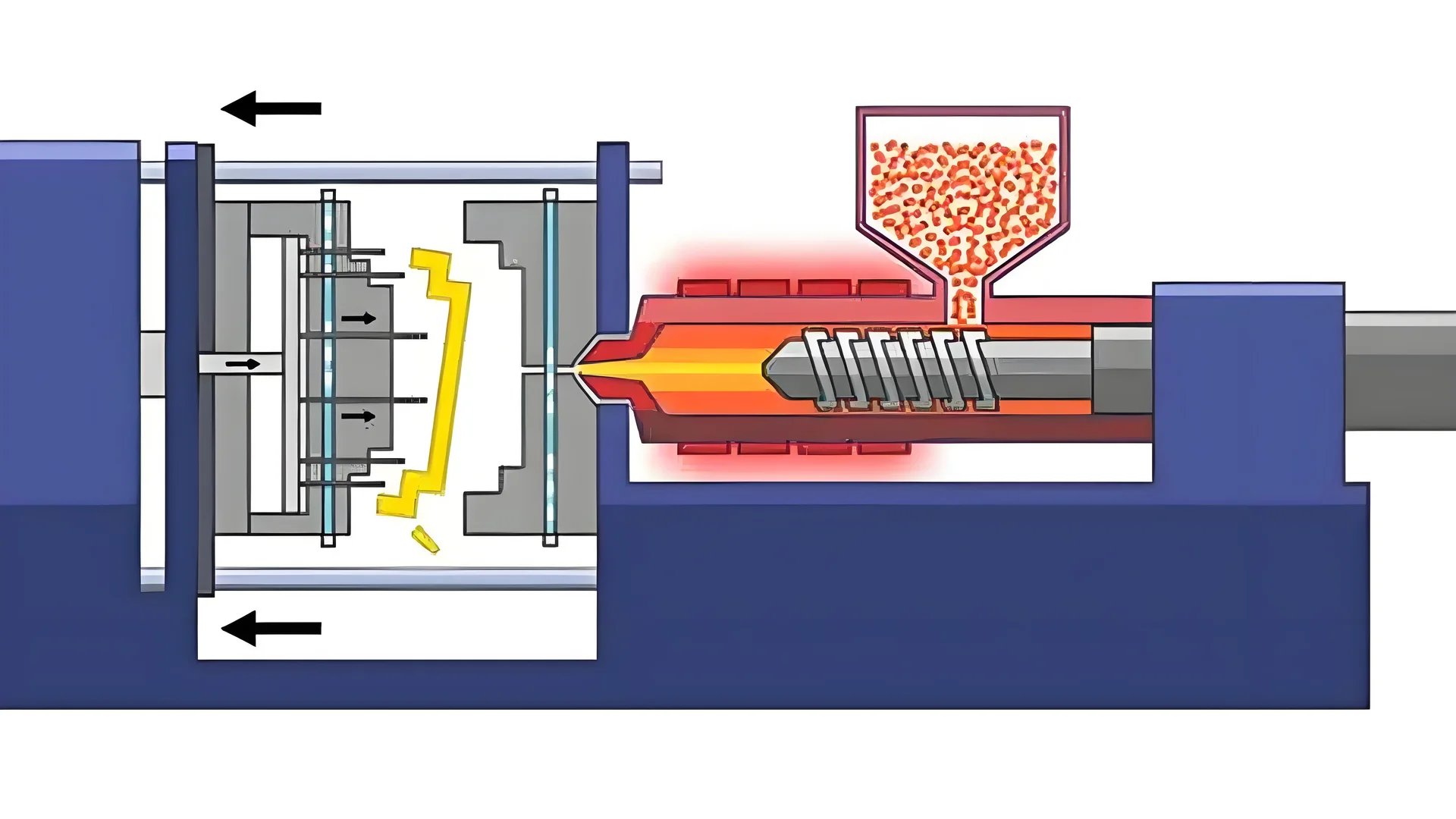
Short Shots
A short shot occurs when the mold cavity is not completely filled. This can result from insufficient injection pressure or speed. Monitoring the melt’s arrival time at the transfer position3 is crucial. If it reaches too late, it indicates a need for adjustments in injection speed or nozzle temperature.
Flash
Flash refers to excess material seeping out of the mold cavity, creating an unwanted thin layer on the part. It often occurs when the injection pressure is too high or due to poor mold clamping. By analyzing data at the transfer position, engineers can adjust parameters to prevent flash formation.
Bubbles
Bubbles can form within the plastic component due to trapped air or gas during molding. This is often due to rapid changes in pressure or temperature at the transfer position. Adjusting these parameters can help mitigate bubble formation and ensure a smoother finish.
Inconsistent Dimensions
Variability in dimensions can stem from fluctuations in temperature or pressure as the melt moves past the transfer position. Implementing real-time monitoring4 systems can help identify and correct these inconsistencies, leading to more precise and consistent part production.
Understanding these common issues and their solutions at the transfer position not only enhances product quality but also optimizes the overall efficiency of the injection molding process. With careful monitoring and parameter adjustment, these challenges can be effectively addressed.
Short shots occur due to insufficient injection pressure.True
Short shots happen when the mold cavity isn't fully filled.
Flash is caused by low injection pressure.False
Flash occurs due to high injection pressure or poor clamping.
How Can Engineers Optimize the Transfer Position?
Optimizing the transfer position in injection molding is critical for enhancing product quality and process efficiency.
Engineers can optimize the transfer position by adjusting parameters like injection pressure and speed, using real-time monitoring and simulation tools to ensure precise control over the molding process.

Understanding the Transfer Position’s Impact
The transfer position is crucial as it marks the transition between the filling and packing stages of injection molding. This transition directly influences the quality of the final product5. By optimizing this point, engineers can mitigate defects such as short shots and flashes.
Adjusting Process Parameters
Engineers should focus on fine-tuning parameters such as injection speed, pressure, and holding time. These adjustments help achieve a balanced flow of the melt, ensuring it reaches the transfer position smoothly. Using sensors to monitor these parameters in real time allows for immediate corrections, enhancing process stability.
Utilizing Advanced Simulation Tools
Leveraging software tools like mold flow analysis can provide insights into the flow dynamics within the mold. Such simulations help predict how changes in the transfer position might affect overall product integrity. Engineers can simulate different scenarios to determine the optimal settings before actual production.
Implementing Real-Time Monitoring
Real-time monitoring systems enable engineers to observe the process closely as it unfolds. By tracking variables such as temperature and pressure at critical points, adjustments can be made on-the-fly to optimize performance. This proactive approach minimizes downtime and reduces waste.
Addressing Common Issues
Common issues at the transfer position include bubbles, weld lines, and inconsistent part density. By employing preventative measures6 such as adjusting gate locations or modifying the cooling rate, engineers can overcome these challenges.
Ultimately, by combining analytical tools with real-time monitoring and adjustment capabilities, engineers can ensure the transfer position is optimized for maximum efficiency and quality in injection molding.
Adjusting injection speed improves transfer position.True
Fine-tuning injection speed ensures balanced melt flow, optimizing transfer.
Real-time monitoring has no impact on process stability.False
Monitoring allows immediate corrections, enhancing process stability.
Conclusion
Understanding and optimizing the transfer position can significantly elevate your production capabilities and ensure high-quality outputs.
-
Understand how transfer positions influence quality and efficiency in molding.: This is the distance on the injection molding machine controller that the screw travels in order to reach the part’s desired transfer … ↩
-
Learn strategies to reduce shrinkage and improve dimensional accuracy.: Controlling the mold temperature can control shrinkage. Using a cold mold allows the outer edges of a part to dry before it can fill and compress the entire … ↩
-
Gain a detailed understanding of transfer positions’ significance in molding.: This is the distance on the injection molding machine controller that the screw travels in order to reach the part’s desired transfer position. … ↩
-
Explore how real-time systems improve precision in injection molding.: Mold-Masters SmartMOLD is a cloud-based software platform dedicated to the plastics industry providing real-time data to drive injection molding … ↩
-
Learn how transfer positions influence product integrity and defect prevention.: The best position for mold transfer is to be able to take out the products smoothly. If the mold opening distance is too large, the molding … ↩
-
Explore solutions for common defects occurring at the transfer point.: The transfer position marks the switchover from filling to packing. Here’s why it’s so important: During filling, plastic flows into the mold at … ↩