Have you ever felt like a detective, trying to solve the mystery of the perfect plastic part? I certainly have. The right tools really change your injection molding tasks into smooth, efficient work.
Adjust injection molding process settings using tools like machine controllers, mold temperature controllers and sensors for pressure and flow. These tools offer real-time monitoring and changes. Quality and efficiency improve significantly.
I stood next to the injection molding machine, feeling both excited and overwhelmed by the endless dials and settings. Understanding everything depended on advanced controllers on modern machines. They allowed me to change injection speed, pressure and even screw speed with just a few easy taps. This meant adapting to each product’s unique structure and achieving a perfect fill every time. Perfect fill, every time.
The mold temperature controller is a real lifesaver. It helps when dealing with tricky materials like polycarbonate. Sometimes, I need to raise the heat to improve fluidity or lower it to speed up production. These controllers always keep the mold temperature just right.
Pressure and flow sensors are also my best friends in this process. They watch real-time changes, preventing issues like flash or overflow due to high pressure or weak filling from low pressure. Flow sensors, in particular, guide me in adjusting injection and screw speeds to keep product quality high. Product quality remains high.
In the end, I embraced data analysis software in my workflow. It gathers parameter data during operations. Statistical analysis helps me discover where adjustments are needed. Like a silent partner, it constantly optimizes our process, offering insights I never knew I needed.
Mold temperature controllers adjust injection molding parameters.True
Mold temperature controllers are used to maintain optimal mold temperatures, crucial for quality.
Data analysis software is unnecessary in injection molding.False
Data analysis software is vital for monitoring and optimizing the injection molding process.
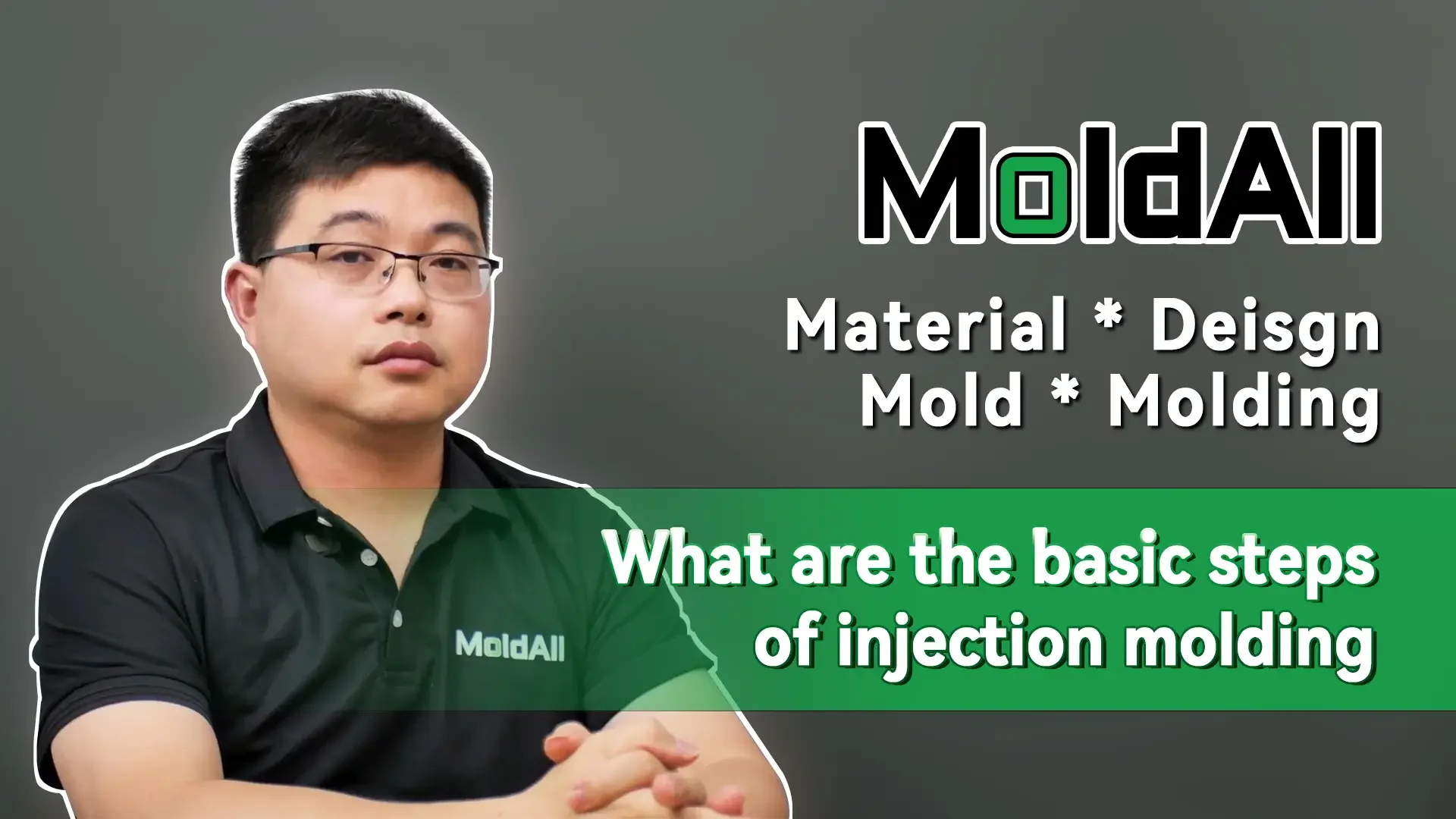
- 1. How Do Injection Molding Machine Controllers Enhance Efficiency?
- 2. Why is mold temperature control critical in injection molding?
- 3. How Do Pressure Sensors Ensure Quality in Manufacturing?
- 4. How Can Flow Sensors Optimize Material Usage?
- 5. What Insights Can Data Analysis Software Provide for Process Improvement?
- 6. Conclusion
How Do Injection Molding Machine Controllers Enhance Efficiency?
Visualize turning messy production lines into well-organized and smooth operations. Injection molding machine controllers act as conductors directing this impressive change.
Injection molding machine controllers improve efficiency by precisely adjusting settings such as injection speed, pressure and mold temperature. They reduce cycle time and cut down on defects. Controllers give precise control over production.
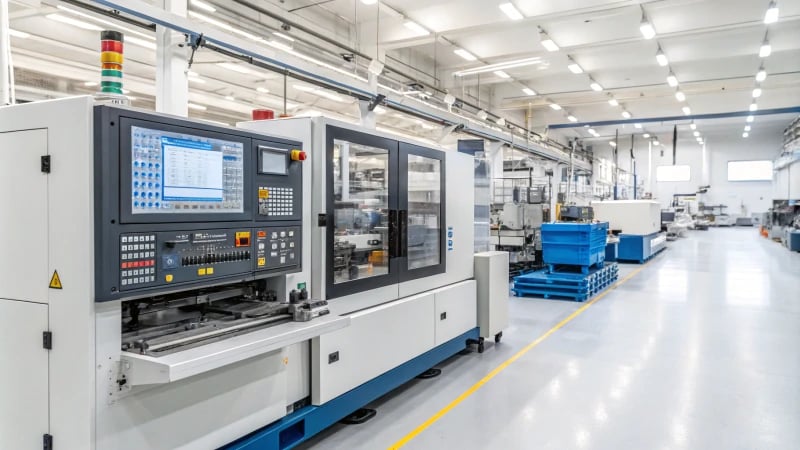
The Role of Advanced Controllers
Years ago, I discovered advanced injection molding machines1. These devices seemed like a leap into tomorrow. They were more than just machines; they felt like smart partners. Modern controllers allow operators like me to adjust settings for things like injection speed and pressure easily through a simple interface. Imagine changing speeds at different stages to fit each product’s needs. Like picking the right songs for a party, you achieve the perfect atmosphere every time.
Importance of Mold Temperature Control
Recognizing the value of a mold temperature controller2 was a big moment for me. When dealing with materials like polycarbonate, mold temperature controllers become very important allies. This clever tool manages heating and cooling to keep temperatures just right, helping the plastic melt glide smoothly.
Function | Benefits |
---|---|
Heating | Improves melt fluidity |
Cooling | Enhances production efficiency |
It’s as if you’re getting that ideal water temperature in your shower – not too hot, not too cold, just right.
Pressure and Flow Monitoring
Pressure sensors are quiet champions in our work. I once avoided an expensive error thanks to one of these sensors. It gives instant feedback, letting me fine-tune injection pressure and prevent problems like flash or incomplete filling. Similarly, flow sensors3 help by tracking melt flow rate. They act like a GPS for the injection process, making sure you stay on course.
Leveraging Data Analysis Software
To achieve excellence, we depend on data analysis software4. This software gathers crucial data like temperature and pressure during operations, similar to a fitness tracker for machines. Studying this information lets us refine settings, improve cycles and uphold excellent quality.
Utilizing statistical and process capability analyses reveals insights into parameter adjustments needed for optimal efficiency. For example, linking weight changes with parameter shifts can truly transform achieving consistent quality.
Advanced controllers are vital in today’s injection molding, allowing accurate control and insight from data. Manufacturers use these tools to produce high-quality items effectively while cutting down on cycle times and errors. The outcome is evident – better productivity and cost savings for the whole industry.
Advanced controllers optimize injection speed stages.True
Controllers adjust speeds at different stages, improving filling efficiency.
Mold temperature control is irrelevant in injection molding.False
Temperature control is crucial for fluidity and quick mold cooling.
Why is mold temperature control critical in injection molding?
Have you ever thought about why it’s so important to control mold temperature in injection molding?
Mold temperature control in injection molding is crucial. Proper temperature helps material move smoothly. This reduces mistakes. It improves product consistency. The process increases production efficiency. The final product quality rises. It’s really important.
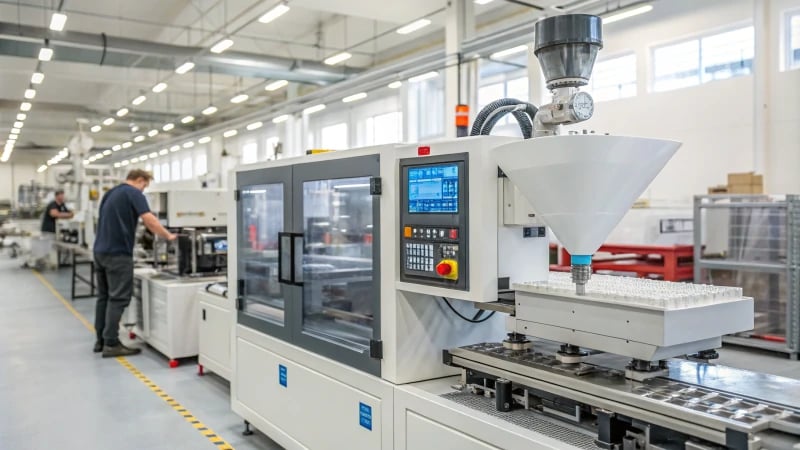
The Role of Mold Temperature in Injection Molding
I remember the first time I saw a perfect part come out of the machine. It felt magical, like a magician pulling a rabbit from a hat. But later, I realized the true magic was in controlling the mold’s temperature. High temperatures greatly improve the surface and shape of parts, while lower temperatures help speed up the process, reducing cycle times.
Temperature Setting | Effect on Parts |
---|---|
High | Better surface finish |
Low | Faster cycle times |
Heating and Cooling Mechanisms
Modern temperature controllers in molding are like silent heroes. They handle both heating and cooling to keep things smooth. For example, when working with plastics like polycarbonate, heating is crucial for proper melt flow. After injection, cooling starts quickly to lower the temperature, maintaining high productivity.
Interaction with Injection Molding Machine Controllers
The interaction between injection molding machine controllers5 and mold temperature controllers is like a perfect dance. Machine controllers change speeds and pressures for smooth operation. This teamwork shapes our products’ features.
Sensors’ Contribution to Temperature Control
Sensors are crucial in my job. Pressure and flow sensors give current data for adjustments, helping avoid flaws.
- Pressure Sensor: Watches pressure changes to prevent flash or overflow.
- Flow Sensor: Tracks melt flow for correct filling.
Data Analysis for Process Optimization
Data analysis has really changed our methods. Gathering information like temperature and pressure helps us find patterns and adjust well. This approach helps us improve process efficiency6 and quality of what we make by connecting weight changes in products with shifts in processing, setting the base for enhancing every work aspect.
High mold temperatures improve surface finish.True
High mold temperatures enhance the surface quality of molded parts.
Low mold temperatures increase cycle times.False
Low mold temperatures decrease cycle times, speeding up production.
How Do Pressure Sensors Ensure Quality in Manufacturing?
Do you ever think about how your favorite gadgets keep their perfect look and work well? Pressure sensors play a big role in this! They’re the hidden stars working hard to achieve it.
Pressure sensors in quality assurance watch and change important settings like injection pressure. This stops problems like flash or overflow. It keeps the products consistent and efficient. Products remain good and efficient.
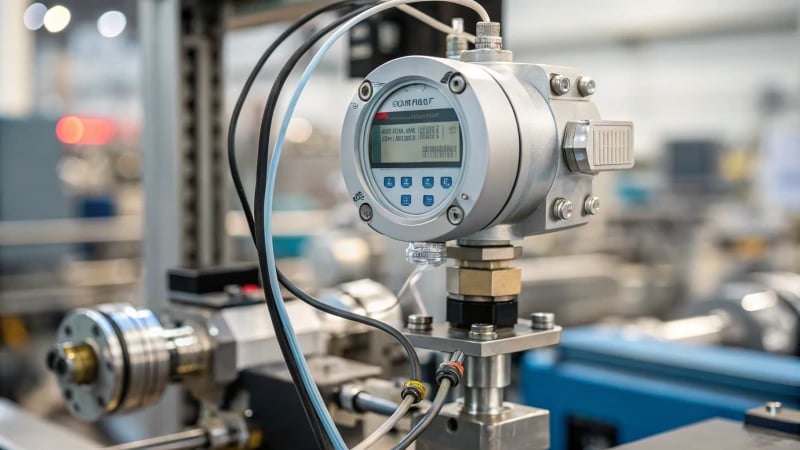
Watching Important Details
I remember seeing pressure sensors work for the first time during an injection molding process. It felt like watching a conductor lead a symphony – every part needed to be perfect in timing and note. These sensors are very important because they watch and adjust the injection pressure in real-time. They catch problems like flash or overflow before turning into expensive defects. Installed in both the injection system and mold, they keep the right amount of pressure throughout, which is crucial for achieving the perfect fill.
Parameter | Function |
---|---|
Injection Pressure | Ensures optimal filling of mold cavities |
Holding Pressure | Maintains product integrity during solidification |
Improving Production Speed
I once worked on a project where production speed was a huge issue until we used pressure sensors. During the holding stage, these sensors kept pressure within necessary limits, directly affecting the quality of the final product7. By combining pressure sensor data with flow sensor readings, I could finally understand the melt flow rate better. This allowed for precise changes to injection and screw speed settings. It felt like having a compass guiding us through difficult production challenges.
Role in Smart Choices
In my experience, using data software with pressure sensors changed how we worked. Advanced workshops use this software to analyze sensor data, revealing insights usually missed. By studying trends in pressure changes8 over time, we could adjust early, catching issues long before they appeared. Injection molding machine controllers9 help by allowing easy changes of key settings through an interface, adapting to specific product needs for best results.
Practical Uses and Gains
I remember a manufacturer troubled by product rejects because of uneven filling – a common fear. Using pressure sensors to change injection pressure on the go reduced defects significantly. This improved both product quality and customer satisfaction while saving money.
Additionally, for situations needing high mold temperatures, like with polycarbonate, pressure sensors with mold temperature controllers10 are vital. They apply just the right amount of pressure during molding, keeping plastic melt flow right for smooth production.
Pressure sensors aren’t just devices; they’re very important partners in our pursuit of quality in manufacturing.
Pressure sensors prevent defects in injection molding.True
They monitor and adjust parameters to avoid issues like flash or overflow.
Data from pressure sensors is irrelevant for decision making.False
The data aids in statistical analysis and process capability studies for consistency.
How Can Flow Sensors Optimize Material Usage?
Do you ever think about how flow sensors greatly reduce material waste in factories?
Flow sensors track the flow rate of materials during manufacturing to use resources better. This exact observation allows quick adjustments. These quick changes reduce waste. It really makes production more efficient.
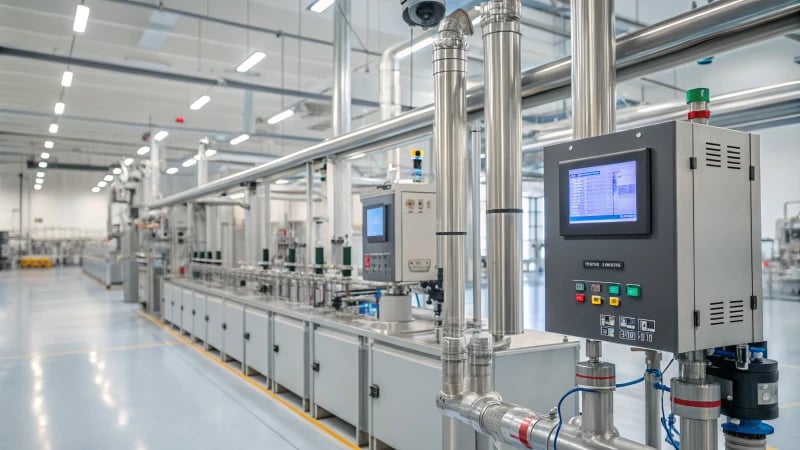
Understanding Flow Sensors
When I entered the busy world of manufacturing, flow sensors amazed me. These small tools work like hidden stagehands in a theater, quietly keeping everything smooth. In injection molding11, they watch the flow of plastic melt closely. Think about baking without measuring ingredients – chaos would follow. Flow sensors help the exact amount of material enter the mold, maintaining quality and avoiding waste.
Benefits in Injection Molding
Flow sensors in injection molding greatly improve the process. They act like a chef who adjusts the heat and ingredients based on taste. Sensors transmit live updates to the injection molding machine controller12, allowing operators to adjust injection speed and pressure. Every product stays consistent in quality, and machines work better.
Feature | Benefit |
---|---|
Real-time monitoring | Immediate process adjustments |
Precise control | Reduced material waste |
Data feedback | Improved product consistency |
Integration with Other Technologies
Excitement grows when flow sensors join with things like mold temperature controllers and pressure sensors. While the mold temperature controller13 keeps the heat just right, flow sensors manage the melt flow. This balance increases efficiency and lowers waste.
Advanced Data Analysis
Modern data analysis software elevates flow sensor data. The software, like a clever detective, links sensor data with things like temperature and pressure. Predicting changes in product weight becomes possible through data analysis software14. Manufacturers can set parameters ahead of time, using resources more wisely than ever before.
Flow sensors reduce material waste in injection molding.True
Flow sensors provide precise control, minimizing excess material use.
Data analysis software is unnecessary for flow sensor optimization.False
Data analysis helps interpret sensor data, enhancing optimization strategies.
What Insights Can Data Analysis Software Provide for Process Improvement?
Have you ever thought about improving your business processes using data?
Data analysis software changes how things work by finding weak points, proposing new ways to do tasks and giving instant information for better choices. It uses predictive calculations to fine-tune settings for smooth upgrades.
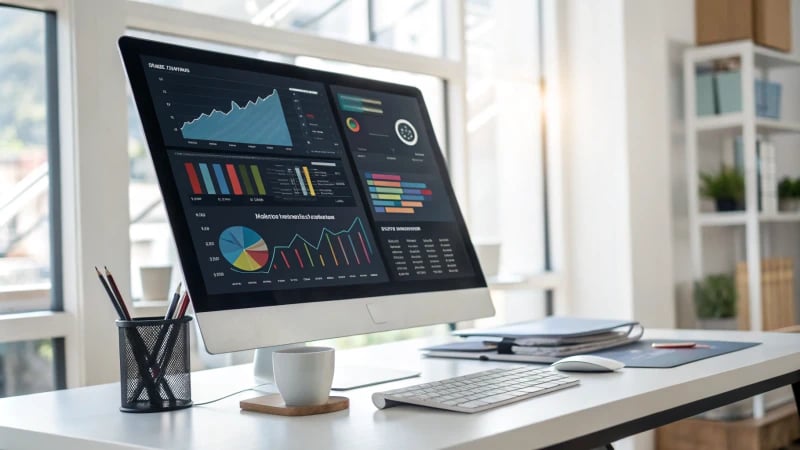
Unveiling Hidden Inefficiencies
I recall the first moment I realized the power of data analysis in manufacturing. The production line faced problems that seemed impossible to find. It felt like looking for a tiny needle in lots of hay. Then, we tried using data analysis tools. It was like someone suddenly lit up the room. The software gathered data from everywhere, like pressure sensors15 and temperature controls. Suddenly, those problems were clear and obvious.
Improving Decision-Making
Having real-time data is very empowering. Early in my injection molding career, I often doubted every choice. But data analysis software merged readings from different sensors, such as a flow sensor16. Finally, I saw the complete picture. It felt like having a smart co-pilot, helping me adjust things to keep product quality really high.
Predictive Analytics and Optimization
Magic happens with predictive analytics. Imagine looking at past data and spotting patterns. These patterns forecast future happenings. It’s like a magic crystal ball for manufacturing. With this knowledge, I could change machine settings to stop issues before they started, using insights from an injection molding machine controller17. Production stayed smooth and very efficient.
Gathering Comprehensive Data
In practice, we track important parameters that guide us in optimizing processes:
Parameter | Source |
---|---|
Temperature | Mold temperature controller |
Pressure | Pressure sensor |
Flow rate | Flow sensor |
Injection speed | Machine controller |
Process Capability Analysis
Understanding the link between process settings and output quality is important. Data analysis showed me how mold temperature changes affect product weight consistency. This insight provides a solid foundation for process improvements.
Using these tools smartly is essential for anyone eager to change their manufacturing methods. If interested in learning more about how data analytics18 reshaped my operations, lots of information awaits you.
Data analysis software highlights production line inefficiencies.True
It identifies anomalies using sensor data, prompting corrective actions.
Predictive analytics cannot suggest optimal machine settings.False
Predictive analytics uses historical data to recommend settings, preventing issues.
Conclusion
Explore essential tools for optimizing injection molding processes, including machine controllers, mold temperature controllers, pressure sensors, flow sensors, and data analysis software to enhance efficiency and product quality.
-
This link explores cutting-edge features of modern injection molding machines, offering insights into their capabilities and benefits. ↩
-
Learn about the functionality and significance of mold temperature controllers in improving injection molding processes. ↩
-
Understand how flow sensors help optimize injection molding by monitoring melt flow rates. ↩
-
Discover how data analysis software enhances injection molding efficiency through parameter optimization. ↩
-
Exploring machine controllers offers insights into automation and precision in molding. ↩
-
Data analysis enhances decision-making, leading to improved efficiency and quality. ↩
-
Explore this link to understand how holding pressure ensures product integrity during solidification. ↩
-
Learn about how analyzing pressure variations can prevent quality issues proactively. ↩
-
Discover how controllers enable precise parameter settings for optimal production outcomes. ↩
-
Find out how mold temperature controllers contribute to maintaining plastic fluidity during production. ↩
-
Explore how flow sensors contribute to efficient injection molding processes, focusing on their role in optimizing material usage. ↩
-
Learn about the critical functions of injection molding machine controllers and their interaction with flow sensors for process optimization. ↩
-
Discover how mold temperature controllers work in conjunction with flow sensors to ensure optimal manufacturing conditions. ↩
-
Find out how data analysis software enhances manufacturing efficiency by processing sensor data for better resource management. ↩
-
Understanding how pressure sensors enhance manufacturing processes can help optimize production efficiency and quality control. ↩
-
Flow sensors are crucial for maintaining consistent product quality by monitoring and adjusting material flow rates. ↩
-
Learning about advanced machine controllers helps enhance precision and efficiency in molding processes. ↩
-
Exploring how data analytics improves manufacturing efficiency offers insights into strategic process enhancements. ↩