Have you ever thought about how the size of your injection molding machine impacts the final product? The tonnage size plays a crucial role. It really affects quality in surprising ways.
Tonnage size in injection molding decides the clamping force. This force keeps the mold shut while injecting. Large tonnage usually results in accurate dimensions. It also gives better surface quality and reduces stress. If tonnage is too low, defects may appear. These include flying edges and uneven density. Such issues affect product quality.
I remember the first time I had trouble with injection molding. I realized how important the right tonnage size was. High-tonnage machines keep the mold closed tightly. This keeps the shape perfect for electronic housings. On the other hand, low-tonnage machines cause flying edges or fusion marks. These issues can be ugly.
Higher tonnage machines are great for surface quality. They copy the mold’s surface very well. This is crucial for shiny finishes on lenses or cosmetic packaging. Tonnage also impacts internal quality. Sufficient tonnage controls stress inside and keeps density even. This is very important for strong pipes or car parts. My experience showed me that choosing the correct tonnage is essential. It’s really about making products that meet all precision and quality standards.
High tonnage machines ensure dimensional accuracy.True
High clamping force prevents mold expansion, ensuring precise dimensions.
Low tonnage machines improve product appearance quality.False
Insufficient clamping force can cause defects like flying edges and fusion marks.
What Are the Advantages of High Tonnage Injection Molding Machines?
Have you ever thought about how powerful high tonnage injection molding machines transform manufacturing?
High tonnage injection molding machines offer precise size control. They deliver excellent surface quality. These machines handle internal stress well. Their strong clamping force guarantees exact product sizes. This strong force also improves surface looks and cuts down on mistakes like flying edges. Many sectors need this high accuracy. Quality is key for these industries.
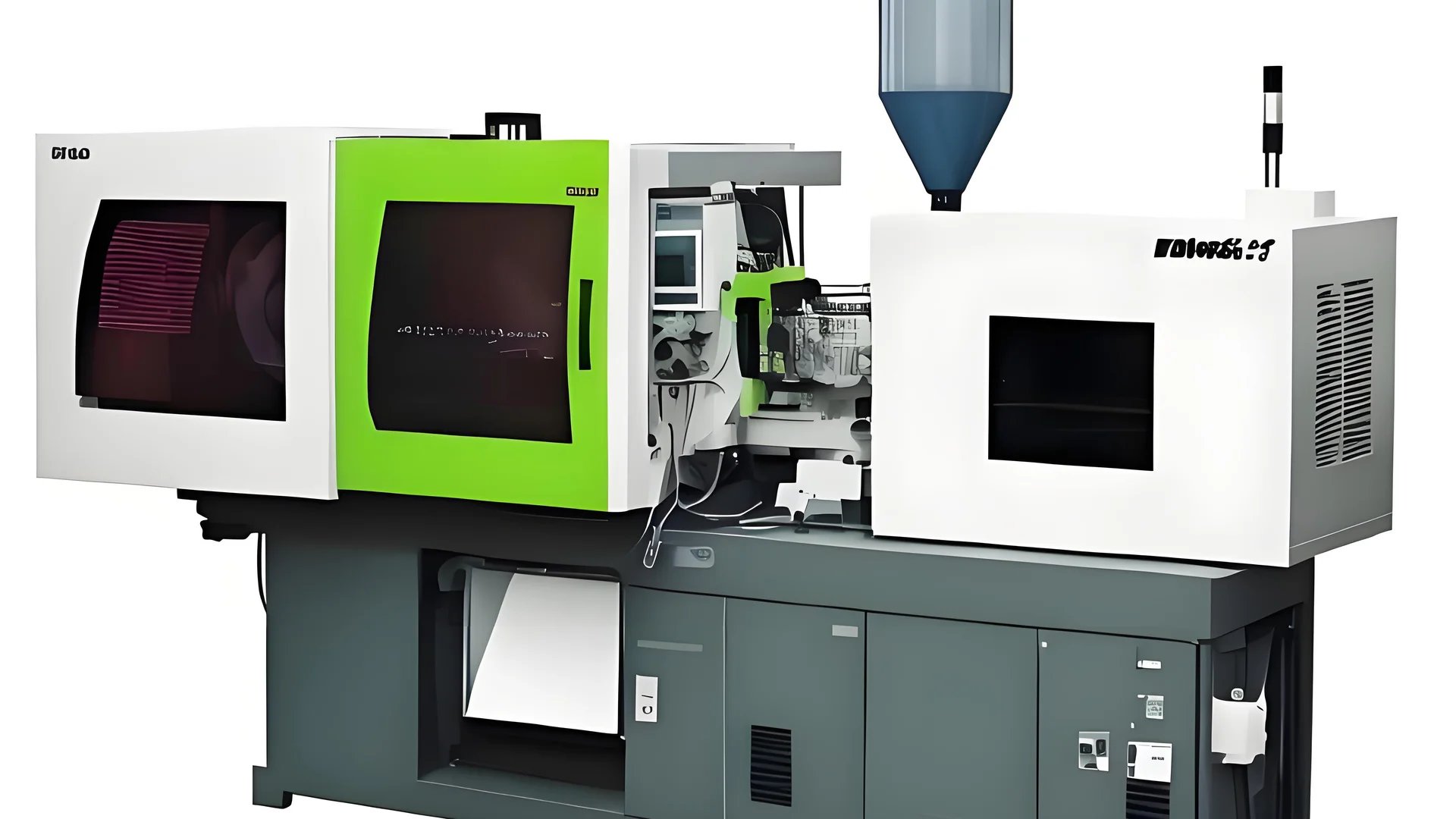
Dimensional Precision
High-power injection molding machines excel in delivering exceptional dimensional precision1. The first time I saw one, it was fascinating. These machines press the mold shut with great force while pouring in hot plastic, ensuring each millimeter counts. This precision is crucial for products like electronic parts, where exact sizes are necessary. Weaker machines may fail and leave extra plastic bits, leading to size deviations and compromised product aesthetics.
Surface Finish
The look of a product is very important for its success. High tonnage machines have the ability to replicate mold cavity surfaces effectively onto the product. I once held a plastic lens made by such a machine; its clarity and smoothness were perfect, like glass. The strong clamping force captures every detail of the mold, which is vital for items like beauty products and glasses. On the contrary, weaker machines often create products with defects like dents or flow marks.
Inside Quality
Internally, these machines contribute significantly to stress control and density uniformity. Strong machines keep consistent pressure and reduce stress inside the product. This stability is essential for car parts where strength is vital. I remember working with strong plastic pipes; their even density from the right force made them dependable under pressure. A high tonnage allows for even melt distribution, enhancing material distribution2 consistency.
Overall, high-power injection molding machines provide the necessary strength and steadiness to meet tough industry needs. They greatly reduce errors and improve accuracy, making them indispensable in fields focused on high-quality production outcomes where quality is not just a goal—it is everything.
High tonnage machines ensure better dimensional accuracy.True
They provide stronger clamping force, preventing mold expansion.
Low tonnage machines improve surface quality of products.False
Insufficient clamping force leads to defects like flying edges.
How Can Low Tonnage Lead to Product Defects?
Have you ever thought about how a basic machine adjustment might impact your product’s quality?
Low tonnage in injection molding leads to problems. Dimensional errors and poor surface finish often occur. Internal stress problems might also develop. These problems happen because the clamping force is not enough. This weak force lets the mold expand too much. Unstable melt flow results as well. It damages appearance. It harms structural integrity. The product’s quality probably suffers.
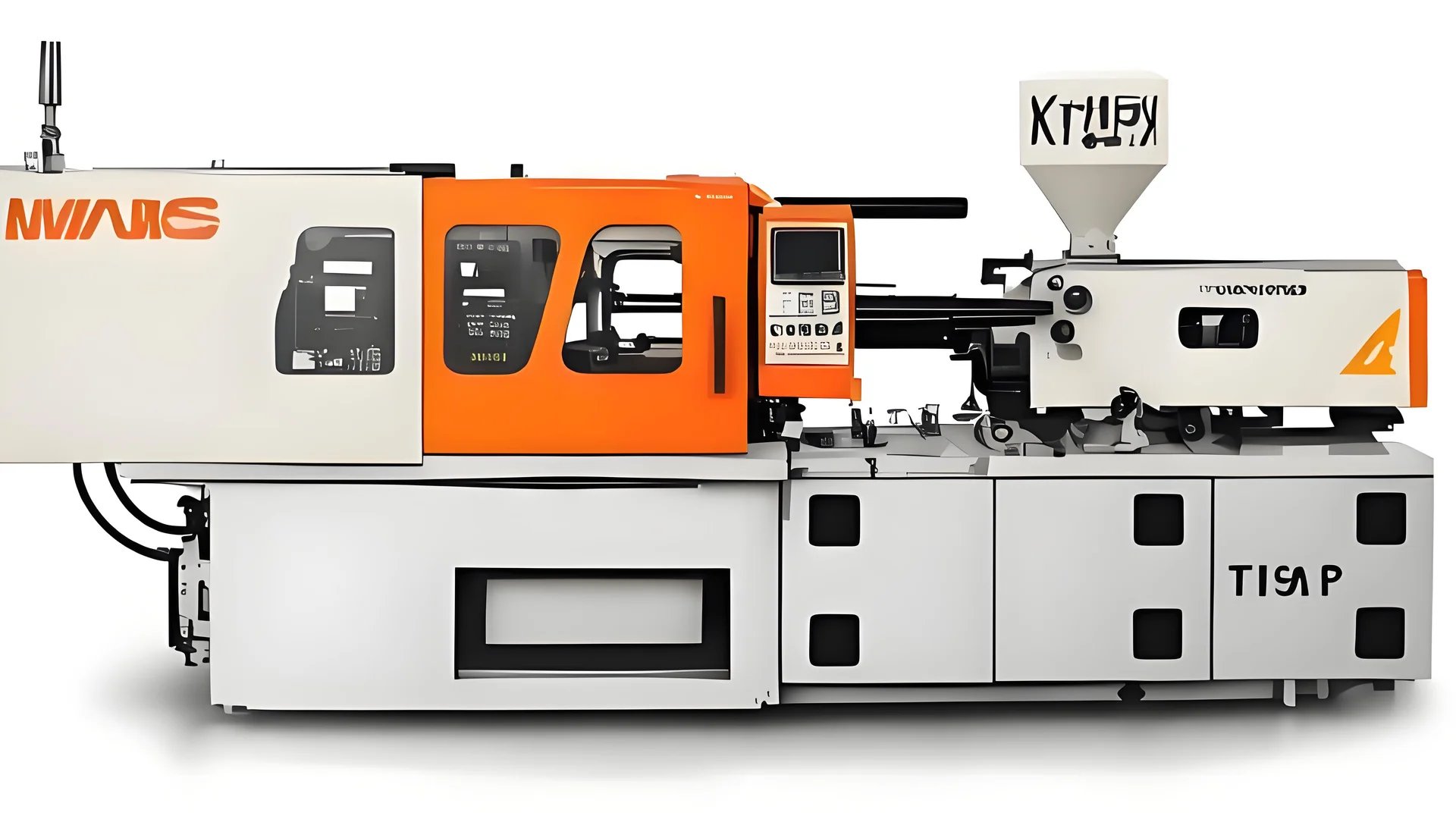
Dimensional Accuracy Challenges
I remember when I first faced the complexities of injection molding. Fresh out of engineering school, I managed a batch of electronic casings. At first, it seemed straightforward. But soon, the products had slight thickness differences. Low tonnage machines were the problem. These machines lacked the clamping force needed to keep molds tightly shut, leading to unwanted expansion and changes. Larger tonnage machines solved this by keeping uniform wall thickness and tight tolerances.
Low tonnage machines often struggle with maintaining dimensional accuracy3. This is because they lack the clamping force needed to counteract the expansion force of plastic melt within the mold cavity.
Appearance Quality Concerns
I won’t forget a project for crafting luxury cosmetic packaging. We started with low tonnage machines and the results disappointed us—lots of rough edges and ugly marks appeared. It was a big lesson: proper clamping force must replicate mold details on products’ surfaces.
A significant issue with low tonnage is its effect on the product’s appearance quality. Sufficient clamping force ensures a smooth transfer of mold details onto the product surface. Without it, defects like flying edges and fusion marks can appear.
Once we switched to a higher tonnage machine, everything changed—our glossy packages became perfect, truly flawless.
Internal Quality Issues
We focused on product quality during a high-strength pipe project. Low tonnage machines gave us uneven pressure, causing internal stresses that weakened the pipes—a big wake-up call.
The internal quality aspects4 of products can also be compromised by low tonnage. Insufficient clamping can lead to uneven pressure distribution during molding, creating internal stresses that weaken mechanical properties.
High tonnage machines controlled pressure better; they really improved density uniformity and made our products stronger. This taught us an important lesson: for durable items like car parts, high tonnage is key—it prevents stress cracks and keeps strength intact.
High tonnage machines ensure dimensional accuracy.True
High clamping force prevents mold expansion, maintaining size precision.
Low tonnage machines improve surface quality.False
Insufficient clamping force causes defects like flying edges and fusion marks.
Why Does Surface Quality Matter for Injection Molded Products?
Some plastic products look high-quality. Surface quality plays a crucial role!
Surface quality in injection molded products is very important. It ensures accurate dimensions, attractive looks and strong structure. This is crucial for meeting high-performance standards.
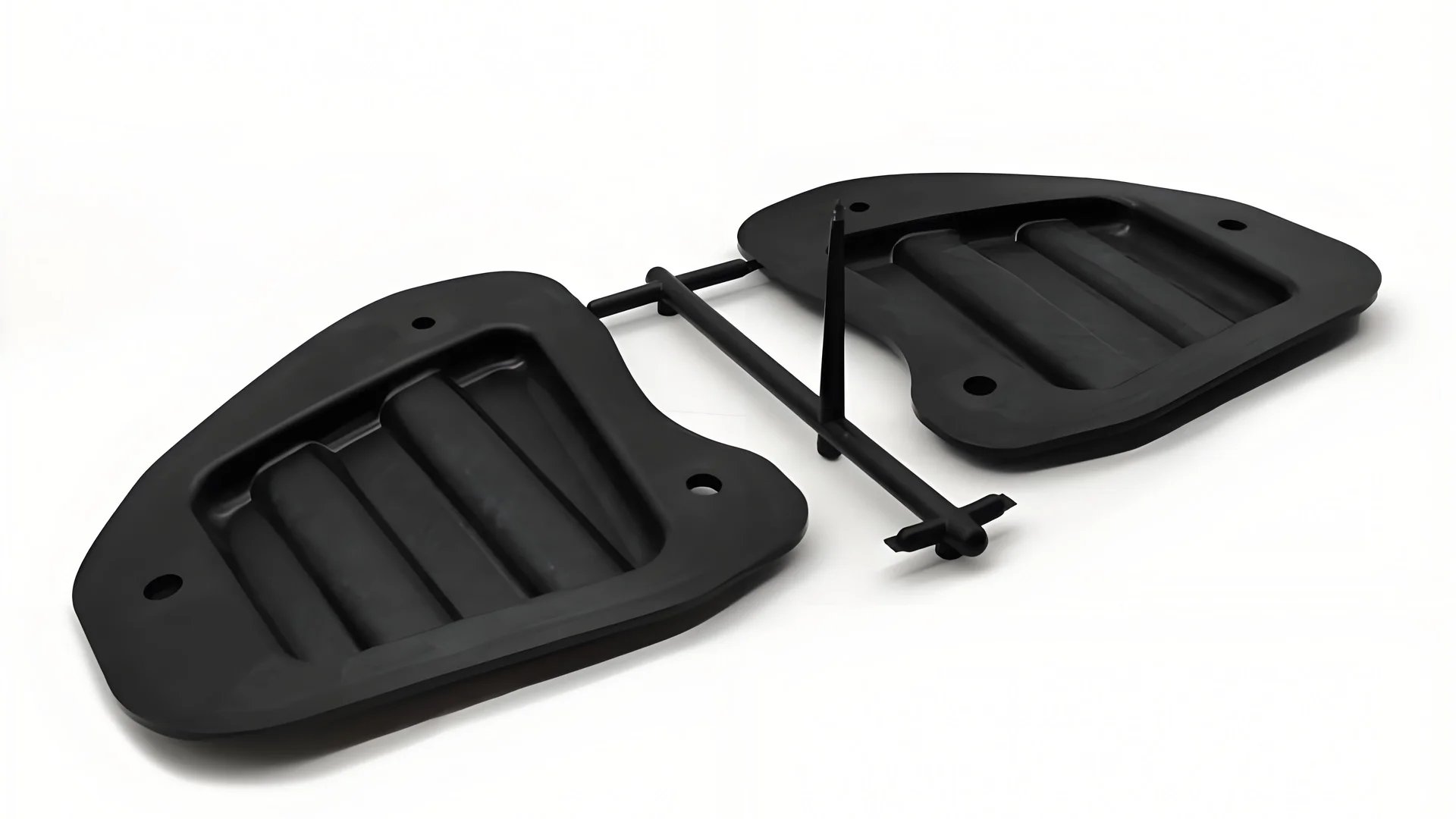
Dimensional Accuracy and Its Impact
I started learning about injection molding and quickly saw how small details change everything. Dimensional accuracy matters a lot. It’s like baking a cake; you need the right amounts, otherwise, the cake won’t rise properly. Injection molding requires high-tonnage machines. These machines hold the mold tightly closed, ensuring each piece comes out perfectly. This is very important for precision items like electronic component cases, where even a small mistake can cause many problems.
A friend in electronics shared a scary story. They used low-tonnage machines, which caused "flying edges" or extra plastic around the product edges. The entire batch was ruined—a costly lesson indeed.
For example, using a high-tonnage injection molding machine can ensure uniform wall thickness and control dimensional tolerances within tight limits. This is particularly important in applications demanding high precision, like precision electronic components5.
Improving Appearance Quality
Seeing a perfectly glossy product brings real satisfaction—it’s like the cherry on a sundae. The secret involves high-quality surface replication; strong clamping force helps achieve this perfection. Visual perfection is key for products like sleek lenses or luxury packaging—cutting corners is not an option.
A colleague saved a product line by choosing a machine with the right tonnage to avoid ugly fusion marks. These marks occur where plastic flows meet unevenly—imagine trying to sell luxury packaging with visible seams—not attractive!
Insufficient tonnage not only causes flying edges but also leads to fusion marks—visible lines formed when plastic flows converge unevenly. These marks are detrimental to the product’s appearance, especially when visual aesthetics are paramount.
Internal Quality Considerations
Internal quality is important too—it reminds me of learning about internal stress in engineering: you can’t see it, but it exists and affects everything. High-tonnage machines help control this by keeping pressure stable, resulting in stronger products essential for automotive parts.
Moreover, sufficient clamping force ensures uniform density distribution of the plastic melt within the cavity. During a factory visit, I learned about high-strength plastic pipes—the engineer explained how even density helped achieve amazing pressure resistance.
Understanding these elements enhances my appreciation for injection molding: surface quality isn’t just about looking nice; it’s about creating products that last and perform well under stress conditions.
See more about internal stress management6 in injection molding processes.
High tonnage machines improve surface quality.True
Strong clamping force ensures smooth, defect-free surfaces.
Low tonnage machines enhance dimensional accuracy.False
Insufficient clamping force leads to dimensional deviations.
How Does Tonnage Affect Internal Stress and Density in Molded Products?
Have you ever thought about how the correct tonnage in injection molding changes your products?
Tonnage in injection molding influences internal stress and density. It sets the best clamping force. This reduces stress. It also helps keep density even. These actions lead to very high-quality products. The products are strong and have exact measurements. They also have a really excellent finish.
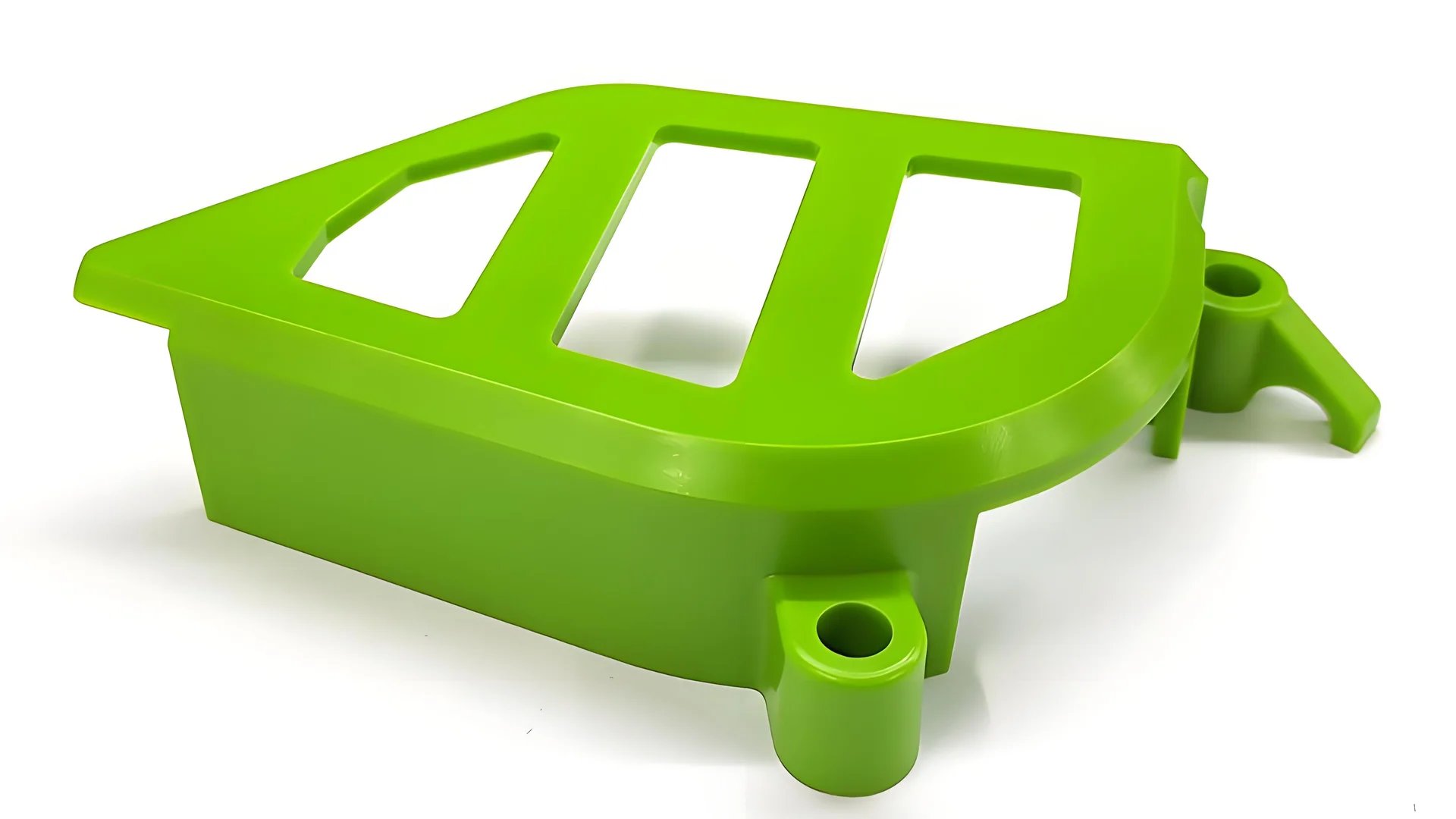
Impact on Dimensional Accuracy
Let’s discuss how tonnage affects the accuracy of dimensions. Larger tonnage injection molding machines provide the strong force required to hold things tightly during the injection process. Without enough clamping power, molds may expand, causing measurement errors. High-tonnage machines are crucial for parts needing exact measurements, like electronic housings, where every tiny bit matters. Conversely, low-power machines can cause defects like extra plastic bits due to inadequate clamping force, impacting both size and appearance quality. Therefore, selecting an appropriate tonnage is essential for achieving precise dimensional accuracy in injection molding processes7.
Influence on Surface and Appearance Quality
Tonnage also affects surface quality significantly. Large machines help achieve smooth, shiny finishes crucial for products like luxury cosmetic packaging. Adequate clamping ensures the mold cavity surface is accurately replicated. Lack of power could lead to marks where the plastic didn’t blend well, harming a product’s appearance—like wearing clean clothes with dirty shoes. Understanding how tonnage affects surface quality is crucial for industries focused on producing visually appealing products.
Internal Stress Management
Controlling stress inside molded items also relates to tonnage. High-power machines keep molds stable, allowing plastic to flow under even pressure conditions. This reduces stress—a big issue in components like car parts—and enhances strength and toughness by preventing future cracks. Using the right tonnage helps toughen products and is a key consideration for manufacturers aiming to enhance product durability.
Enhancing Density Uniformity
Finally, let’s cover density uniformity. Enough tonnage ensures even distribution of plastic melt within molds, which is vital for products under heavy pressure or needing special traits like strong pipes. Consistent density was my top focus when handling such projects as it improved structural strength and pressure-handling ability. Proper tonnage ensures consistent material density, enhancing the structural integrity and pressure resilience of these products.
By weighing these elements, I learned how to pick the right tonnage for various tasks—balancing internal stress and density helps create top-notch molded items.
High tonnage ensures dimensional accuracy.True
High tonnage machines provide strong clamping force, preventing mold expansion.
Low tonnage machines improve surface quality.False
Insufficient clamping in low tonnage machines can cause surface defects.
Conclusion
Tonnage size in injection molding significantly affects product quality, influencing dimensional accuracy, surface finish, internal stress control, and density uniformity, crucial for high-performance applications.
-
Understand how these machines maintain precise product dimensions. ↩
-
Learn why uniform material distribution enhances product durability. ↩
-
Explore how clamping force impacts precision in injection molding processes. ↩
-
Learn about managing internal stress for stronger, more durable molded products. ↩
-
Explore how precise dimensions enhance electronic component functionality. ↩
-
Learn about reducing internal stress for stronger molded products. ↩
-
Explore how precision affects product quality and performance. ↩