Have you ever thought about how a machine’s strength alters plastic into a flawless component?
The weight of an injection molding machine influences the clamping force. This force keeps the mold shut during injection. Greater weight permits larger molds. It maybe leads to more injection volume. The screw’s thickness and injection pressure are important as well.
I remember the first time I stood before a huge injection molding machine. It felt like meeting a friendly giant. This machine quietly turned raw plastic into something useful and precise. Knowing how tonnage – like the machine’s muscle – affects injection volume was a big reveal for me.
I dived into the details. Higher tonnage handles bigger molds. Think of it like fitting a larger pan in your oven. But it’s not just about strength. The screw diameter and injection pressure are crucial. They need to be just right, like seasoning and temperature in cooking. Adjusting these parts really matters. It can change a part from perfect to flawed. This process is a very delicate dance of power and precision.
Larger tonnage machines have larger injection volumes.True
Larger tonnage machines can hold larger molds, leading to larger volumes.
Injection pressure always increases injection volume.False
Higher pressure can improve filling but doesn't always increase volume.
How Does Clamping Force Impact Injection Molding?
Have you ever thought about how a simple force might really change your injection molding process?
Clamping force in injection molding keeps the mold tightly closed. This action stops defects such as flash. Precise product dimensions depend on it. Very important. It decides the size of molds. This force affects injection volume. It also allows higher pressures.
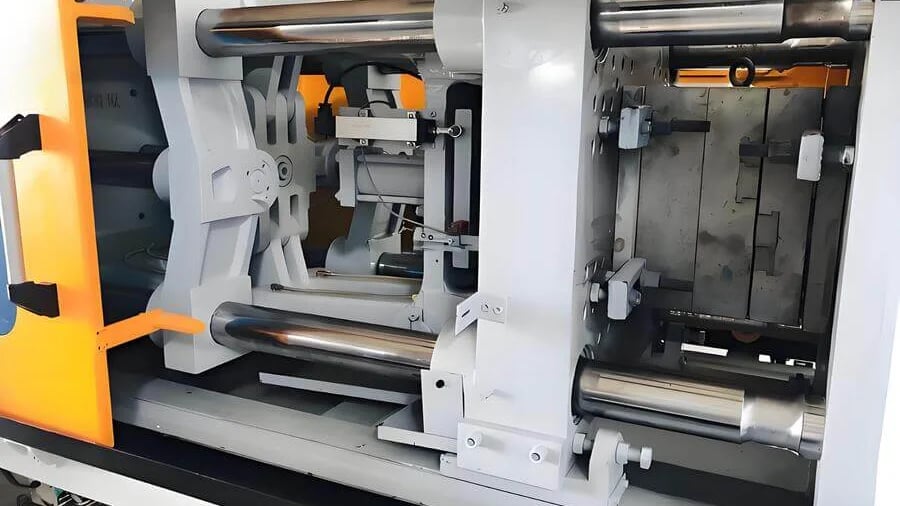
Understanding Clamping Force
I recall my first experience with clamping force during an internship at a plastic factory. The supervisor said clamping force is like a strong handshake, keeping the mold halves together during injection. Without enough of this force, plastic would leak out, causing a defect known as "flash." Measured in tons, the force holds the mold shut, especially when hot plastic is injected with high pressure. I discovered that the machine’s tonnage1 shows its clamping strength and must resist the plastic’s pressure to avoid leaks.
Indirect Influences on Injection Volume
There exists a complex relationship between clamping force and injection volume. More clamping force allows for bigger molds and more plastic injection. It was like finding a secret formula – our 500-ton machines accommodated larger molds compared to the 100-ton machines. We then produced bigger or more complicated products easily.
Machines with greater clamping forces also support higher injection pressures. I remember a project needing intricate mold fills. The increased pressure helped achieve complete fills, but we needed caution. Excess pressure2 might cause problems like flying edges or internal stress, ruining the perfect product.
The Complexity of Injection Molding Machine Dynamics
In a project review, I discovered not all machines are identical, even with the same tonnage. Features like screw diameter and injection stroke are important. For example, we examined two machines – both 300 tons – but one had a 50mm screw diameter and a 300mm stroke, while the other had a 40mm diameter and 250mm stroke. The first machine delivered more injection volume. This taught me to consider more than just numbers when selecting the right machine.
This complexity3 underscores the importance of considering all aspects of an injection molding machine when determining its suitability for a given project.
Clamping force prevents plastic melt overflow.True
Clamping force keeps the mold closed, preventing overflow during injection.
Higher tonnage machines always have higher injection volumes.False
Injection volume depends on factors like screw diameter, not just tonnage.
How Does Mold Size Affect Injection Volume?
Have you ever thought about why mold size is so important in injection molding? Let’s explore how it can really improve or harm your production process.
Mold size affects how much material is injected. It decides the space in the mold. Bigger molds often let more material in. However, it’s not just about size. Factors like injection pressure also play a role. Machine details are really important, too.
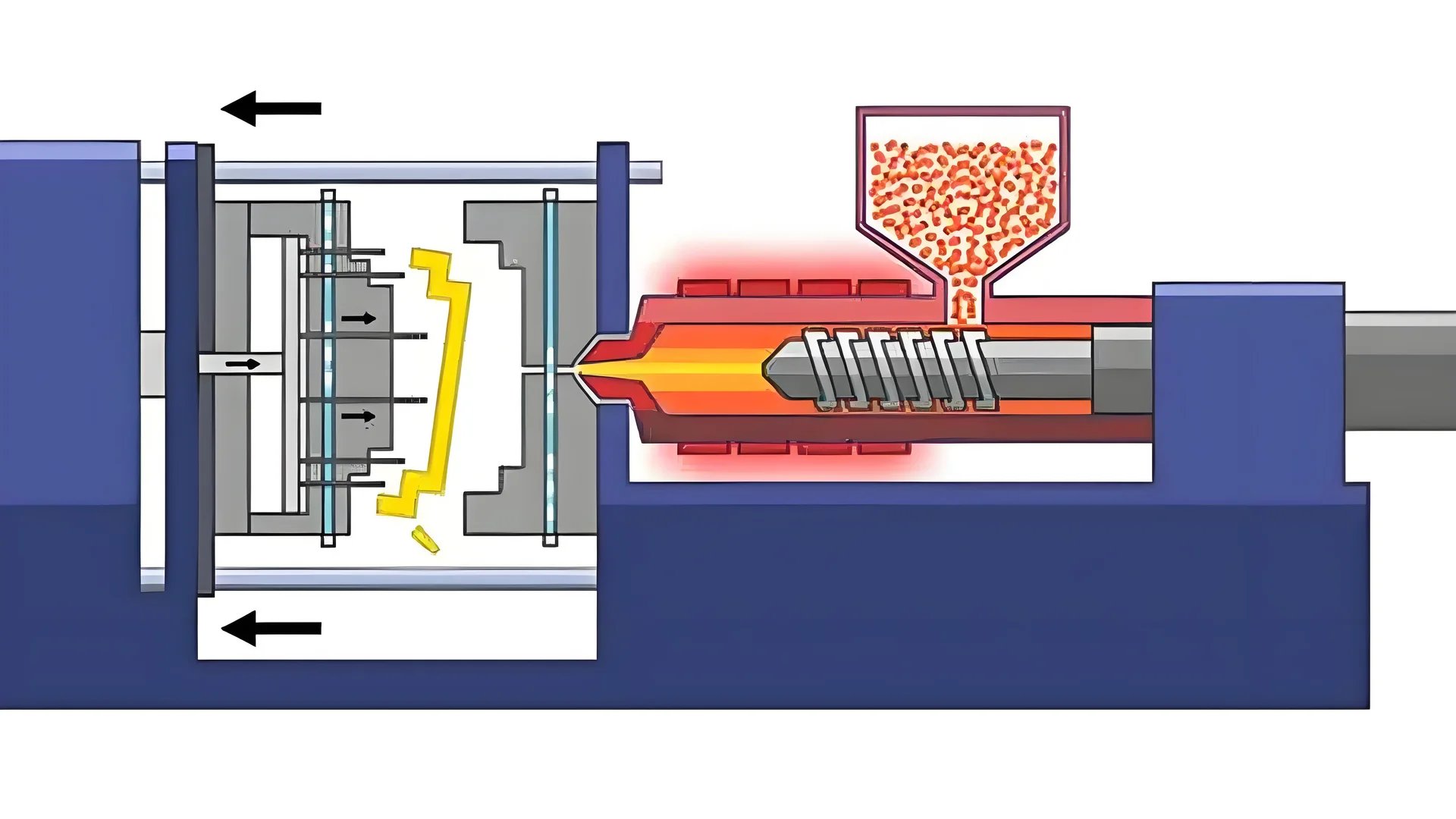
Understanding the Basics
I remember my first visit to an injection molding factory. The size of the machines and molds amazed me! I quickly learned that the mold size is crucial because it dictates the cavity’s capacity. Larger molds typically have larger cavities, allowing for more plastic melt to be injected, resulting in a higher injection volume4. However, this isn’t the sole factor at play.
Machine Tonnage and Mold Size
Later, I saw that a machine’s tonnage often controls the mold size it can manage. Think of a 500-ton machine as a heavyweight champion; it can handle much bigger molds than a 100-ton machine. This means the cavity volume5 in larger machines tends to be significantly greater, directly impacting the amount of material injected.
The Role of Injection Pressure
Then, I learned about injection pressure. An experienced engineer compared it to squeezing toothpaste—too much pressure creates a mess! High-tonnage machines apply more force, which might allow for more complete filling of big or complex molds. However, excessive pressure can lead to issues like flashing or internal stresses. Balancing these factors is crucial for optimizing injection volume6.
Non-Proportional Relationships
Once, while looking at machine specifications with a coworker, I noticed something interesting: there’s no absolute proportional relationship between mold size and injection volume. Machines with the same tonnage might differ in injection volumes due to variations in screw diameter and injection stroke. Imagine two machines, both 300 tons; one with a 50mm screw provides more volume than one with a 40mm screw.
Practical Considerations
Designing or selecting molds feels like solving a complex puzzle. You must think about mold size and machine specifications. This includes understanding how different factors like machine tonnage, screw diameter, and injection pressure interact to influence production outcomes7. Knowing these details helps improve efficiency and product quality—very important!
Higher tonnage machines always inject more plastic.False
Injection volume depends on factors like screw diameter and stroke, not just tonnage.
Larger molds generally require higher injection pressure.True
Higher injection pressure helps fill larger cavities effectively, ensuring complete filling.
Why Is Injection Pressure Crucial for Mold Filling?
I have always been curious about how a tiny change in injection pressure affects the quality of a molded product. It is not only about filling the mold. It really involves precision and perfection.
Injection pressure is vital for mold filling. It helps molten plastic flow smoothly. The pressure fills the mold cavity completely. This process lowers defects. Production quality increases.
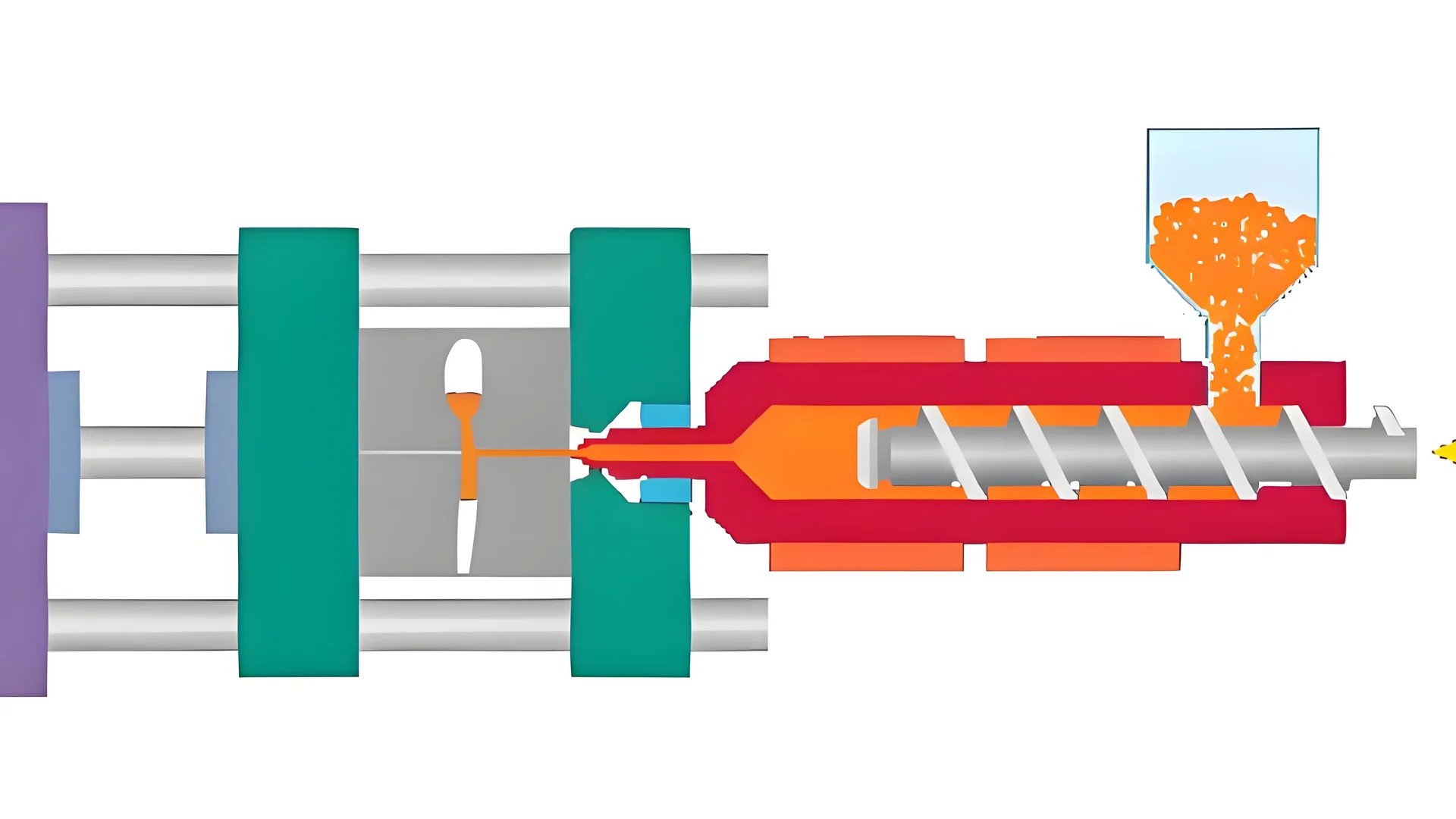
The Role of Injection Pressure in Mold Filling
I remember my first visit to a busy factory floor. Machines hummed, transforming molten plastic into useful items. There, I learned how important injection pressure is in the injection molding process8. This pressure drives molten plastic into every part of a mold. It’s like baking – too little pressure leaves holes, too much causes spills.
Higher injection pressures help fill complex molds. They push plastic into detailed designs that need it. It feels like icing a cake where the pressure must be perfect to reach all edges without overflow.
Balancing Pressure with Machine Tonnage
An early mentor told me that balancing pressure and machine tonnage is like mixing flavors when cooking. Higher tonnage machines exert more pressure, but results depend on mold size, complexity, and material. Machine tonnage9 mostly keeps molds closed while also influencing how much plastic enters.
Influences on Production Quality
Adjusting pressure is like tuning an instrument to achieve harmonious production. High pressure can improve consistency, reducing flaws. However, too much pressure may cause internal stresses—over-tightening guitar strings does the same—they break.
Finding a perfect injection pressure spot is key for optimizing production efficiency10 and reducing waste. Adjusting screw speed and back pressure might really help find this balance. It’s a careful art to learn in injection molding.
Higher tonnage means higher injection volume.False
Tonnage and injection volume aren't directly proportional; other factors affect volume.
Injection pressure affects mold filling quality.True
Higher injection pressure can improve mold filling, reducing defects.
Are There Limitations to Increasing Injection Pressure?
Have you ever thought about what occurs when injection pressure goes too high?
High injection pressure helps mold filling in injection molding. Yet, it might cause flying edges and stress inside, especially in complex shapes. The machine’s ability and the material’s traits must match the pressure. This balance stops flaws and keeps the process smooth.
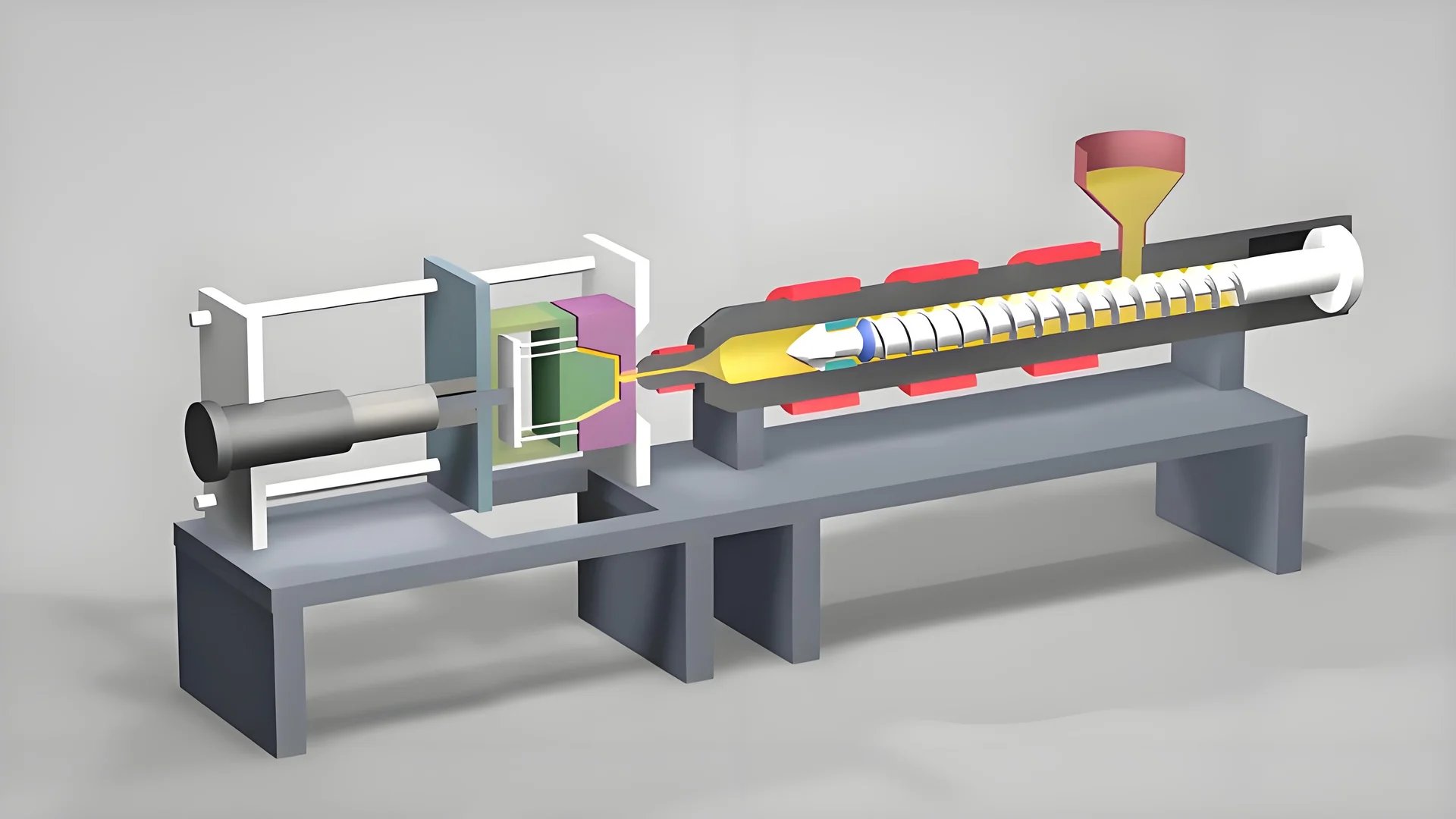
Understanding Injection Pressure
Injection pressure has always intrigued me. It plays a crucial role in things like injection molding11 and diesel engines. This pressure works like the system’s heartbeat, helping material or fuel enter a mold or combustion chamber. However, increasing injection pressure isn’t always the right answer.
The Role of Machine Tonnage
I once watched an injection molding machine do its job. Tonnage, or the clamping force, holds the mold closed while plastic flows inside. Larger machines handle bigger molds, which means injecting more plastic melt. But size alone isn’t enough; factors like screw diameter12 and stroke length matter too.
Indirect Influences of Higher Pressure
Higher pressure is tricky. It helps fill molds, especially when designs are complex. But too much pressure causes problems such as flying edges or stressed parts. Finding the right balance is vital; the pressure must match the mold size and material properties.
Non-Absolute Proportional Relationships
Machines with the same tonnage may have different injection volumes due to variations in screw diameter and injection stroke length. I’ve seen two 300-ton machines act differently because of these variables. So while pressure matters, it is not everything.
Practical Limitations and Considerations
Pushing with too much pressure might harm the machine by leading to wear and tear or even mechanical issues. Some materials may deform or break under high pressures without degrading their quality. These challenges must be understood to set proper injection settings13. By doing so, efficiency improves without hurting product quality.
Higher injection pressure always improves mold filling.False
Too high injection pressure can cause defects like flying edges.
Tonnage directly determines injection volume capacity.False
Injection volume also depends on screw diameter and stroke.
Conclusion
The tonnage of an injection molding machine affects clamping force and mold size, indirectly influencing injection volume through pressure and design complexity, but is not a simple proportional relationship.
-
Learn how machine tonnage influences mold capacity and production capabilities. ↩
-
Discover potential issues from excessive pressure like flying edges and stress. ↩
-
Understand how screw diameter and stroke impact injection volume. ↩
-
Explore the direct link between mold cavity size and injection volume. ↩
-
Learn about how cavity volume impacts material injection. ↩
-
Understand how injection pressure affects material flow and quality. ↩
-
Discover key factors influencing efficiency in injection molding. ↩
-
Explore how injection pressure impacts molding efficiency and quality. ↩
-
Learn how tonnage influences molding capabilities and processes. ↩
-
Discover methods to enhance efficiency and reduce defects. ↩
-
Discover how injection molding works and its industrial applications. ↩
-
Explore how screw diameter influences injection volume. ↩
-
Find methods to effectively adjust injection pressure. ↩