Creating a plastic mold is more than just a step in manufacturing—it’s a journey filled with decisions and timelines that can make or break your project.
The timeframe for creating a plastic mold can range from 15 days to several months. This depends on the mold’s complexity, production technologies used, and the factory’s production schedule.
But that’s just the tip of the iceberg! Let’s dive deeper into how various factors influence these timelines and discover practical ways to streamline the process.
Simple plastic molds take 15-30 days to create.True
Simple molds require less design and manufacturing time, typically 15-30 days.
How Does Mold Complexity Affect Production Time?
When creating plastic molds, complexity is a key factor influencing production timelines. Understanding its impact is crucial for efficient planning.
Mold complexity directly affects production time. Simple molds may take 15-30 days, while complex molds can extend to 60 days or more, influenced by intricate designs and precision needs.
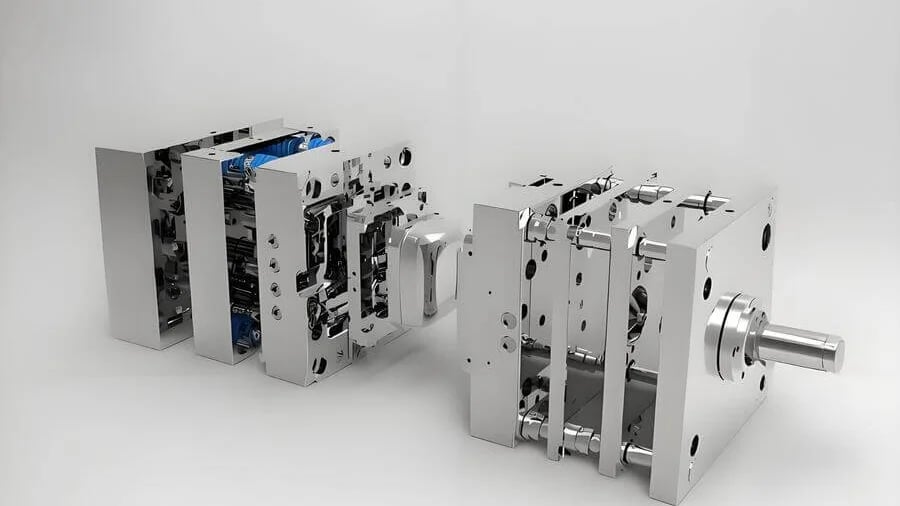
The Impact of Simple vs. Complex Molds
The time required to create a mold varies greatly based on its complexity. A simple mold, such as those used for small, regular-shaped products, can be completed in approximately 15 to 30 days. This includes a design phase of 3 to 5 days, 10 to 20 days for processing and manufacturing, and 2 to 5 days for assembly and debugging.
In contrast, complex molds, like those for large automotive parts, demand significantly more time. These projects may take up to 60 days or longer. The design stage alone might consume 10 to 15 days due to the intricacies involved. The processing phase could extend to 30 or even 40 days, owing to the need for high-precision procedures. Assembly and debugging also require more attention, often taking an additional 10 to 15 days.
Mold Type | Design Time | Processing Time | Assembly & Debugging Time | Total Production Time |
---|---|---|---|---|
Simple Mold | 3-5 days | 10-20 days | 2-5 days | 15-30 days |
Complex Mold | 10-15 days | 30-40 days | 10-15 days | 60+ days |
Factors Amplifying Complexity
Several factors contribute to the complexity of mold making:
-
Design Intricacies: More detailed and intricate designs demand advanced techniques and meticulous attention, extending the design and processing time.
-
Precision Requirements: High precision needs, particularly in industries like automotive or aerospace, necessitate longer machining times and rigorous quality checks.
-
Material Choice: Certain materials are more challenging to work with and may require specialized equipment or processes.
Managing Complexity in Mold Making
To manage the complexities and reduce production time, consider adopting advanced technologies like high-speed machining centers1 and 3D printing2. These innovations can expedite design verification and modifications, streamlining the entire process.
Understanding how mold complexity affects production timelines helps in setting realistic expectations and planning your manufacturing project efficiently.
Complex molds take over 60 days to produce.True
Complex molds require intricate designs, precision, and longer processing.
Simple molds can be completed in 5 days.False
Simple molds typically require 15 to 30 days for completion.
What Role Do Production Technologies Play in Mold Making?
The evolution of production technologies has significantly transformed the landscape of mold making, but what exactly is their role?
Production technologies play a crucial role in mold making by impacting efficiency, precision, and timeframes. Advanced technologies like high-speed machining centers and 3D printing have revolutionized the process, reducing production times and improving accuracy.

Traditional vs. Advanced Production Technologies
In the past, traditional mechanical processing methods were widely used in mold making. These methods often required significant manual intervention, leading to longer production times. For instance, using conventional milling and drilling machines meant that complex shapes were more difficult to process efficiently. As a result, the production cycle was extended due to the need for meticulous manual adjustments and frequent debugging.
However, the introduction of advanced production technologies has markedly improved mold making efficiency and precision. High-speed machining centers, for example, allow for faster processing of complex mold structures with minimal manual intervention. This not only shortens the production cycle but also reduces the margin for error.
The Impact of 3D Printing on Mold Prototyping
3D printing technology has emerged as a game-changer in mold prototyping. By enabling rapid prototyping, 3D printing allows designers to quickly produce and test mold prototypes before committing to full-scale production. This capability is invaluable for design verification and modification, significantly speeding up the entire production cycle.
For example, a designer can use 3D printing to create a prototype of a complex automotive part mold in just a few days. This prototype can then be tested and refined before any traditional mold-making processes begin, reducing overall production time.
Enhancing Precision with EDM and Wire Cutting
Electrical Discharge Machining (EDM) and wire cutting technologies further enhance the precision and efficiency of mold making. These technologies are particularly useful for molds requiring intricate details and high precision. By utilizing EDM, manufacturers can achieve superior surface finishes and tighter tolerances, which are essential for producing high-quality molds.
For instance, EDM is often employed in the production of molds for electronic components that demand exceptional precision. The ability to create detailed and complex shapes with EDM and wire cutting not only improves the quality of the final product but also streamlines the manufacturing process.
By leveraging these advanced production technologies, mold makers can not only reduce production times but also enhance the overall quality and precision of their molds. Exploring these technological advancements3 offers invaluable insights into optimizing mold production processes for various industries.
3D printing reduces mold prototyping time significantly.True
3D printing allows rapid prototyping, speeding up design verification.
Traditional methods are faster than high-speed machining centers.False
High-speed machining centers process complex structures faster.
How Can Factory Scheduling Impact Your Mold Timeline?
Factory scheduling is a pivotal factor in determining the timeline for mold production. But how exactly does it affect your project deadlines?
Factory scheduling impacts mold timelines by influencing equipment availability and prioritizing orders. Efficient scheduling can significantly reduce production delays.

The Role of Production Arrangements
Efficient production arrangements are essential in determining how swiftly a mold can be produced. If a factory is overburdened with tasks, the time required for mold completion might extend due to equipment and technician availability. On the other hand, if a factory can prioritize your order, the timeline may contract significantly.
Consider a situation where a factory is tasked with producing molds for both small gadgets and large automotive parts. In such cases, resources might be allocated first to high-value or bulk orders, affecting the timeline for smaller projects. This makes it crucial to have transparent communication with manufacturers about scheduling priorities and expectations.
Impact of Order Volume
The volume of orders in a factory influences the mold production schedule. A high order volume can result in longer waiting periods as factories might prioritize larger and more profitable orders. Conversely, when order volumes are low, production flexibility increases, potentially leading to faster completion times.
For example, during peak seasons like the holiday rush, a surge in orders might lead to delays. However, during off-peak times, factories often have more bandwidth to accommodate smaller or less urgent orders quickly.
Order Volume | Potential Impact on Timeline |
---|---|
High | Longer delays due to prioritization of larger orders. |
Low | Shorter timelines with more flexible scheduling. |
Strategies to Navigate Scheduling Challenges
To mitigate the impact of scheduling on your mold timeline, consider:
-
Early Engagement: Engage with manufacturers early to discuss potential scheduling challenges and align on expectations.
-
Flexibility in Design: Sometimes, slight modifications in the mold design can align better with available resources, speeding up the process.
-
Choose Advanced Technologies: Factories equipped with advanced technologies can often manage higher volumes more efficiently, reducing bottlenecks.
-
Negotiate Priorities: Developing a relationship where your needs are prioritized can sometimes be negotiated, especially if future business is anticipated.
By understanding how factory scheduling4 impacts your mold timeline, you can make informed decisions and foster a collaborative relationship with your manufacturer.
Factory scheduling can reduce mold production delays.True
Efficient scheduling optimizes resource use, minimizing delays.
High order volume shortens mold production timelines.False
High order volume often leads to longer waiting periods.
What Are Effective Strategies to Reduce Mold Production Time?
Looking to cut down mold production time? Uncover strategies to accelerate your manufacturing process.
To reduce mold production time, employ advanced technologies like high-speed machining, ensure efficient factory scheduling, and maintain open communication with manufacturers. Prioritize planning and utilize rapid prototyping techniques such as 3D printing to streamline the design and testing phases.

Leverage Advanced Technologies
Embracing advanced manufacturing technologies can significantly reduce mold production time. High-speed machining centers and processes like EDM5 and wire cutting enhance precision and efficiency, minimizing manual intervention. Furthermore, 3D printing for prototype development accelerates design verification, enabling quicker modifications and reducing the overall timeline.
Optimize Factory Scheduling
Efficient production scheduling is crucial in reducing delays. Factories should prioritize mold production based on the order’s urgency and complexity. Collaborative planning with the manufacturing team can ensure resources are allocated efficiently. This proactive approach helps avoid bottlenecks in equipment usage and technician availability, thus shortening lead times.
Engage in Effective Communication
Open lines of communication between the client and the manufacturer are vital. Regular updates and discussions about the project can prevent misunderstandings and unnecessary delays. It’s important to align expectations and timelines early in the process, allowing for adjustments if unforeseen issues arise.
Utilize Rapid Prototyping Techniques
Integrating rapid prototyping methods like 3D printing6 not only speeds up design iterations but also helps in identifying potential issues early in the process. This proactive troubleshooting can save significant time during the production phase, as problems are addressed before full-scale manufacturing begins.
Maintain a Streamlined Design Process
Simplifying the mold design where possible can reduce complexity and, consequently, production time. By focusing on essential features and functionalities, you can decrease the time spent on intricate details that may not be necessary for the initial mold version.
Table: Comparison of Traditional vs. Advanced Technologies
Factor | Traditional Technologies | Advanced Technologies |
---|---|---|
Setup Time | Longer | Shorter |
Manual Intervention | High | Low |
Precision | Moderate | High |
Flexibility in Adjustments | Limited | Extensive |
Incorporating these strategies into your mold production process can drastically reduce lead times, ensuring a more efficient transition from design to finished product.
3D printing speeds up mold design iterations.True
3D printing allows quick modifications, reducing design phase time.
Traditional technologies offer higher precision than advanced ones.False
Advanced technologies provide higher precision due to improved techniques.
Conclusion
In summary, understanding the factors influencing mold creation time helps you plan effectively and communicate better with manufacturers.
-
Learn how advanced machining centers reduce production time.: Faster machining, lower force, less tool breakage, no thermal growth, better surface finish and better part quality can be achieved by using … ↩
-
Discover how 3D printing accelerates mold design processes.: 1. 3D printing can help to shorten the production cycle of molds. Molds manufacturing can shorten the whole production cycle. ↩
-
Discover how modern tools transform mold production efficiency and accuracy.: According to the company, the innovation lies in the 3D-printed air spaces that provide insulation to the nozzles from the mold, ensuring a … ↩
-
Learn how scheduling directly affects mold production timelines.: Let’s explore how injection mold manufacturing and delivery may face delays depending on the mold company you choose. ↩
-
Learn how EDM technology enhances precision in mold making.: EDM is a subtractive manufacturing method that uses electrical discharges to machine features on a mold. ↩
-
Discover how 3D printing accelerates design iterations efficiently.: Employing a 3D printing platform to enable rapid prototyping offers numerous benefits compared to prototyping through traditional methods: Shorter lead times. ↩