Injection molding is like the beating heart of modern manufacturing—efficient, versatile, and remarkably powerful. But can it really embrace the rigidity of thermosetting plastics? Let’s find out!
Thermosetting plastics are generally not suitable for injection molding because they undergo irreversible chemical changes when heated, preventing them from being softened and remolded. Injection molding requires materials that can repeatedly melt and solidify, a property of thermoplastics.
While it might seem that thermosetting plastics are out of the game in injection molding, there’s so much to learn from their unique properties. Join me as we dive into this intriguing world!
Thermosetting plastics can be remolded after heating.False
Thermosetting plastics undergo irreversible changes when heated, preventing remolding.
What Are Thermosetting Plastics?
Thermosetting plastics, known for their rigidity and durability, play a crucial role in various industrial applications. But what exactly are they?
Thermosetting plastics are polymers that irreversibly cure to form a rigid structure. Unlike thermoplastics, they can’t be remolded or reheated once set, making them ideal for high-heat environments.
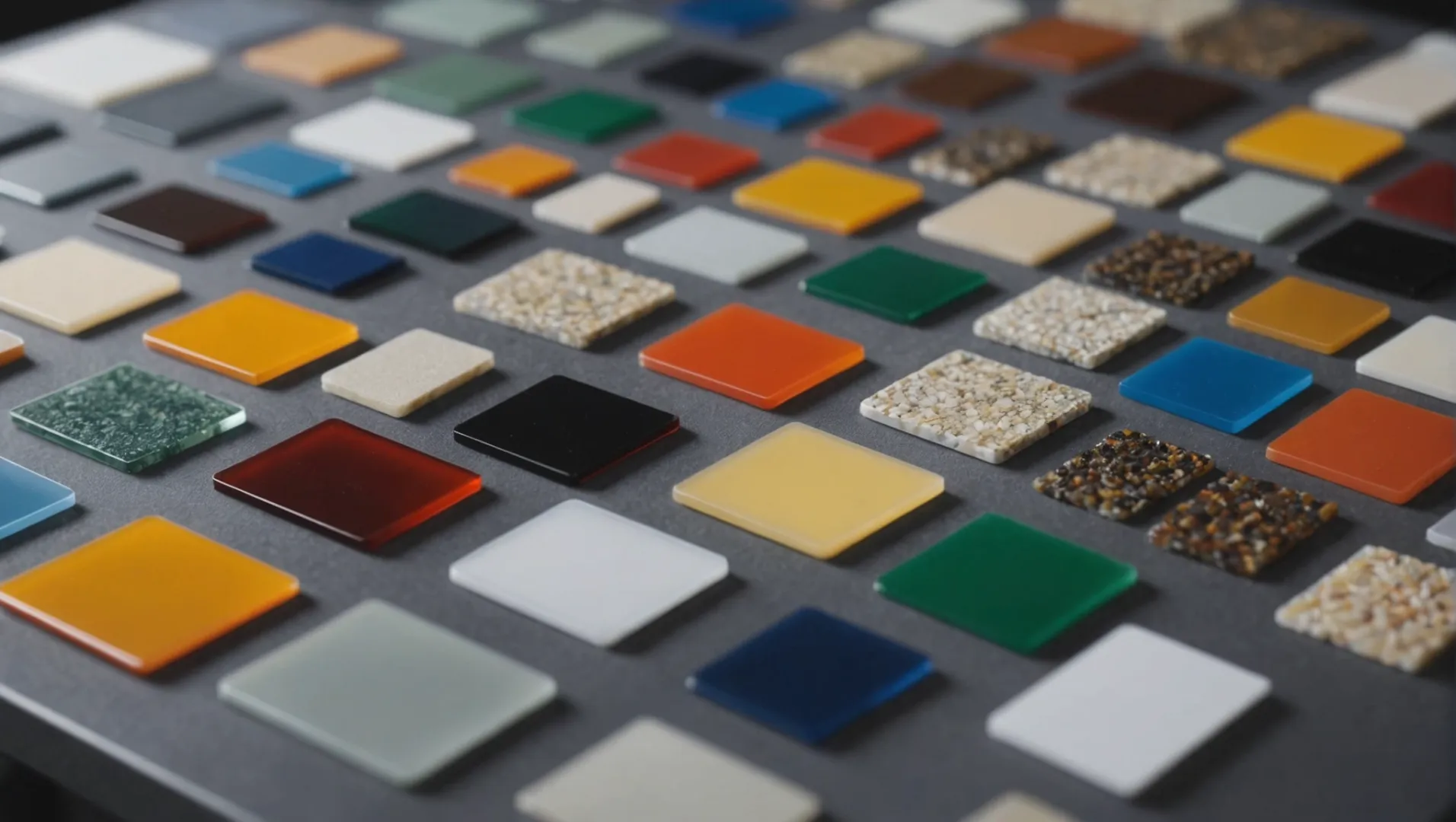
Understanding the Basics of Thermosetting Plastics
Thermosetting plastics, or thermosets, are a type of polymer that solidify and harden when heated. This process, known as curing, involves a chemical reaction that results in a rigid and infusible product. Once cured, these materials can no longer be melted or reshaped, setting them apart from thermoplastics1 that can be remelted and reshaped multiple times.
Chemical Structure and Properties
The chemical structure of thermosetting plastics is characterized by cross-linked polymer chains. This structure provides them with enhanced mechanical properties such as high dimensional stability, heat resistance, and electrical insulation. These properties make them suitable for applications in automotive parts, electronics, and even cookware.
Table 1: Comparison of Thermosetting Plastics and Thermoplastics
Property | Thermosetting Plastics | Thermoplastics |
---|---|---|
Re-molding Capability | Cannot be re-molded | Can be re-molded multiple times |
Heat Resistance | High | Moderate |
Dimensional Stability | Excellent | Varies |
Common Uses | Electronics, automotive parts | Packaging, consumer goods |
Common Types of Thermosetting Plastics
Some of the most common types of thermosetting plastics include epoxy resin, phenolic resin, and melamine resin. Each of these has unique properties that make them suitable for different applications:
- Epoxy Resin: Known for strong adhesive qualities and chemical resistance. Used in coatings and electronics.
- Phenolic Resin: Offers high mechanical strength and flame resistance. Ideal for circuit boards and electrical insulators.
- Melamine Resin: Exhibits excellent hardness and gloss, often used in laminates and dinnerware.
Understanding the distinct characteristics of thermosetting plastics2 can guide industries in selecting appropriate materials for specific applications, ensuring performance and durability.
Thermosetting plastics can be remolded after curing.False
Once cured, thermosetting plastics cannot be remolded or reheated.
Epoxy resin is a type of thermosetting plastic.True
Epoxy resin is a common thermoset known for its adhesive properties.
Why Are Thermosetting Plastics Not Suitable for Injection Molding?
Discover why thermosetting plastics pose challenges for injection molding, a popular manufacturing process.
Thermosetting plastics are generally not suitable for injection molding because they undergo irreversible chemical changes when heated, preventing them from being softened and remolded. Injection molding requires materials that can repeatedly melt and solidify, a property of thermoplastics.
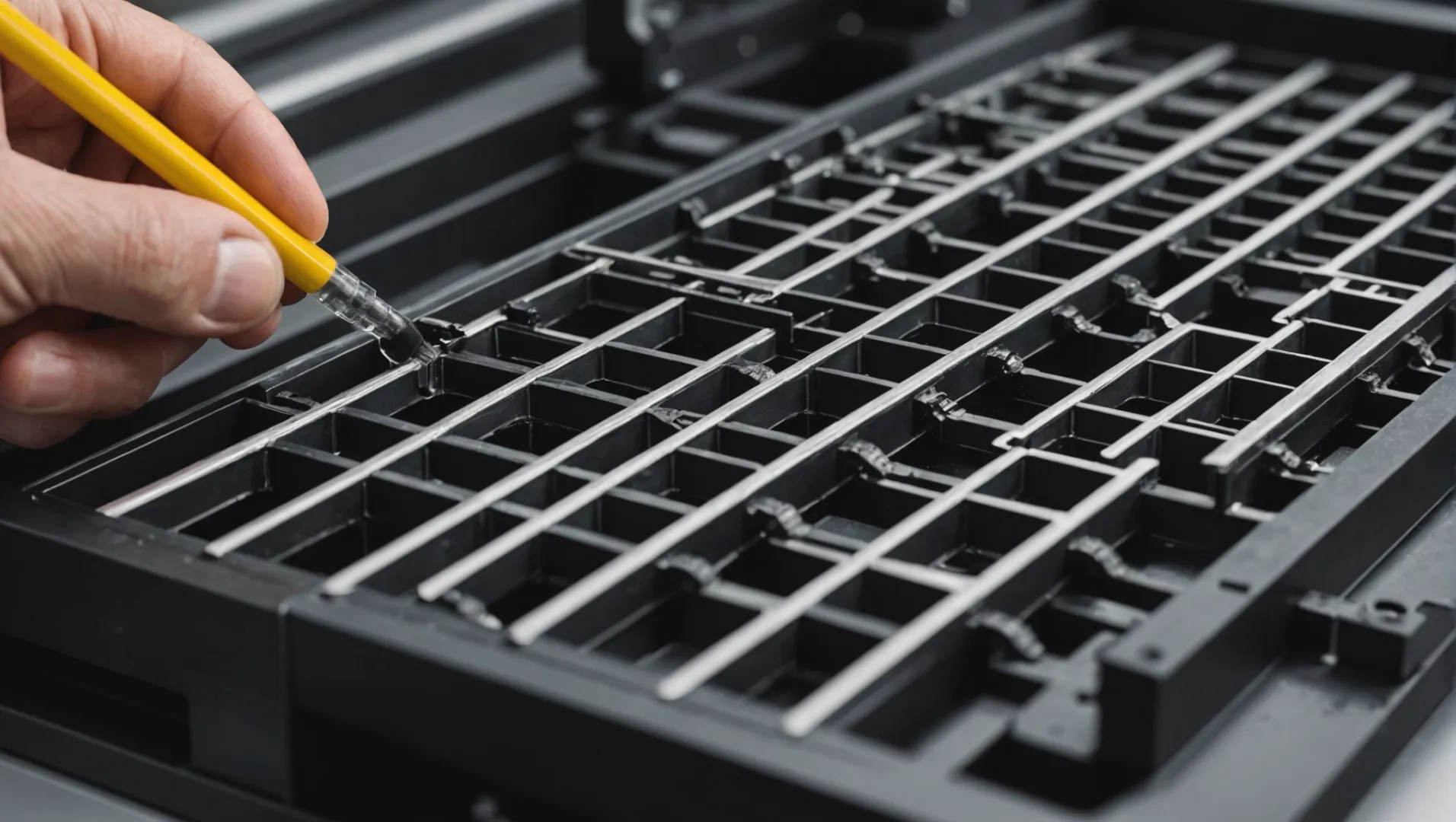
Understanding Thermosetting Plastics
Thermosetting plastics, such as epoxy, phenolic, and melamine, are polymers that solidify or "set" irreversibly when heated. This transformation occurs through a chemical reaction that forms cross-links between polymer chains, converting the material from a malleable state to a rigid structure. Once this cross-linking is complete, the material can no longer be melted or reshaped.
The Injection Molding Process
Injection molding is a manufacturing process that involves injecting molten material into a mold where it cools and solidifies into the desired shape. This process requires the material to be able to transition from a solid to a liquid state and back again multiple times without losing its structural integrity. This capability is crucial for creating consistent and complex shapes at high production speeds.
Why Thermosetting Plastics Fail in Injection Molding
-
Irreversible Setting: As thermosetting plastics undergo chemical changes upon heating, they become permanently hard and cannot be re-melted. This characteristic makes them incompatible with the injection molding process3 which requires materials that can be repeatedly melted and cooled.
-
Structural Limitations: The permanent cross-linked structure of thermosetting plastics means they lack the necessary flexibility to be reshaped. In contrast, thermoplastics like polyethylene and polypropylene can be repeatedly softened by heating and hardened by cooling, making them ideal for injection molding.
-
Processing Constraints: Due to their irreversible setting property, thermosetting plastics require different processing techniques such as compression molding or transfer molding, which are specifically designed to handle these types of materials.
Alternatives and Innovations
While thermosetting plastics aren’t suitable for traditional injection molding, innovations in composite materials and hybrid processing techniques continue to evolve, offering potential alternatives for specific applications. For instance, research into new thermoplastic composites4 aims to combine the beneficial properties of both material types for specialized uses.
To gain a deeper understanding of how these materials interact within different manufacturing processes, it’s helpful to explore further innovative solutions5 in the field.
Thermosetting plastics can be remolded after setting.False
Thermosetting plastics undergo irreversible chemical changes, preventing remolding.
Injection molding requires materials that can melt repeatedly.True
Injection molding needs materials that transition between solid and liquid.
How Do Thermoplastics Differ from Thermosetting Plastics?
Thermoplastics and thermosetting plastics are pivotal in manufacturing, each with distinct characteristics.
Thermoplastics can be repeatedly melted and remolded, unlike thermosetting plastics, which solidify permanently after initial heating due to chemical changes.
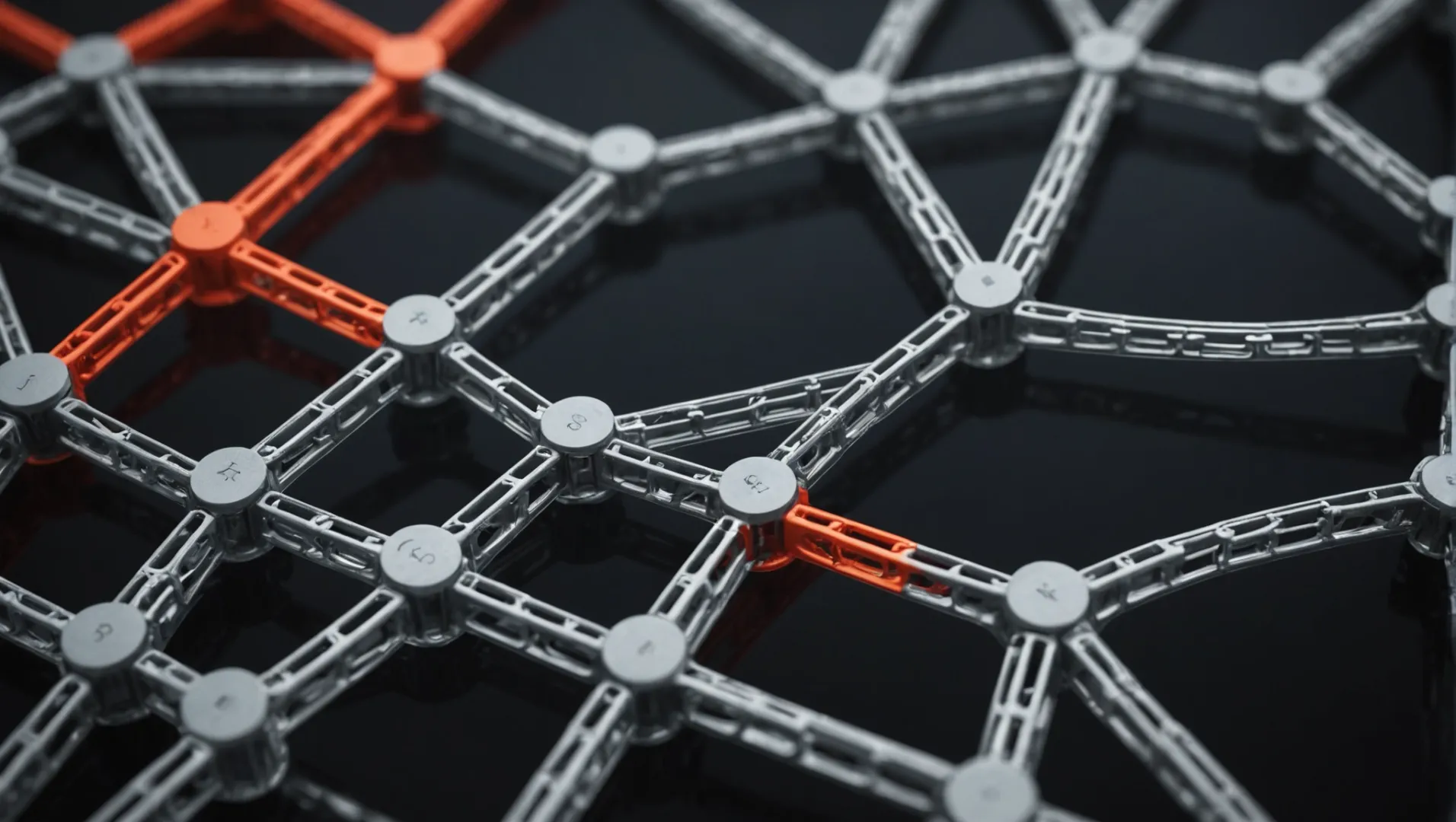
Material Composition and Structure
The fundamental difference between thermoplastics and thermosetting plastics lies in their molecular structure. Thermoplastics have a linear or slightly branched structure that becomes pliable upon heating, allowing them to be reshaped multiple times. This property makes them highly suitable for injection molding processes6, which demand repeated melting and solidification cycles.
In contrast, thermosetting plastics possess a heavily cross-linked, three-dimensional network structure. When initially heated, they undergo a chemical transformation, setting into a rigid form that cannot be re-melted. This irreversible change is due to the formation of covalent bonds between polymer chains during the curing process.
Mechanical Properties and Applications
Due to their structural differences, thermoplastics and thermosetting plastics exhibit varied mechanical properties. Thermoplastics are generally more flexible and have a lower melting point, which allows for easy processing and recycling. They are used extensively in automotive parts, packaging, and consumer goods due to their adaptability and ease of use.
Thermosetting plastics, however, offer superior thermal stability and chemical resistance, making them ideal for high-heat applications such as electronics, aerospace, and appliances. Despite these advantages, their inability to be reshaped after curing limits their use in processes requiring reshaping.
Comparative Table of Key Differences
Feature | Thermoplastics | Thermosetting Plastics |
---|---|---|
Structure | Linear or slightly branched | Cross-linked network |
Processing | Can be re-melted and reshaped | Cannot be re-melted after setting |
Applications | Automotive, packaging, consumer goods | Electronics, aerospace, appliances |
Thermal Stability | Generally lower | Higher |
Environmental Impact and Recyclability
The ability of thermoplastics to be recycled through reheating and reshaping offers a significant environmental advantage over thermosetting plastics. As global industries shift towards sustainable practices, the recyclability of thermoplastics positions them favorably in eco-conscious markets. Efforts are ongoing to develop innovative recycling methods for thermosetting plastics to mitigate their environmental impact.
In conclusion, understanding the inherent differences between these two types of plastics enables manufacturers to make informed decisions about material selection based on application needs.
Thermoplastics can be repeatedly reshaped.True
Thermoplastics become pliable when heated, allowing reshaping.
Thermosetting plastics are easily recyclable.False
Thermosetting plastics cannot be remelted or reshaped after curing.
Are There Any Alternatives to Using Thermosetting Plastics in Injection Molding?
Exploring alternatives to thermosetting plastics in injection molding reveals a world of possibilities.
Thermoplastics, elastomers, and reinforced materials serve as alternatives to thermosetting plastics in injection molding, offering flexibility and recyclability that thermosetting plastics lack.
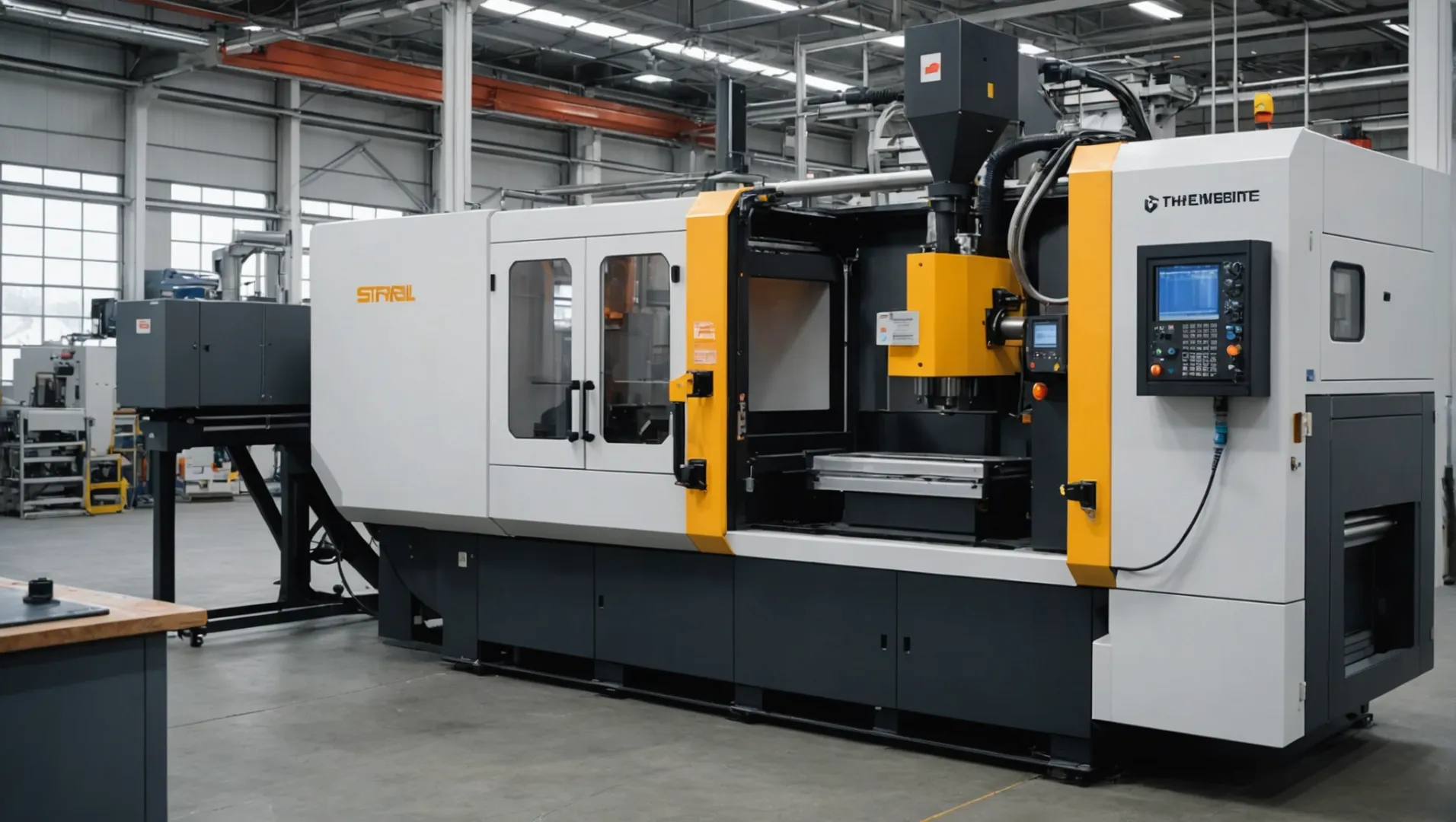
Understanding the Limitations of Thermosetting Plastics
Thermosetting plastics undergo a chemical transformation when exposed to heat, forming a rigid structure that cannot be remelted or remolded. This makes them unsuitable for injection molding processes7, which require materials that can be repeatedly softened and solidified.
Exploring Thermoplastic Options
Unlike thermosetting plastics, thermoplastics soften when heated and harden when cooled without undergoing a chemical change. This property makes them ideal for injection molding. Popular thermoplastics include:
- Polypropylene (PP): Known for its versatility, PP is widely used in automotive parts and household goods.
- Acrylonitrile Butadiene Styrene (ABS): Valued for its toughness and impact resistance, ABS is commonly found in electronic housings and automotive components.
The Role of Elastomers
Elastomers offer a unique combination of elasticity and moldability, making them a viable alternative in injection molding. These materials can endure significant deformation and return to their original shape, beneficial for products requiring flexibility such as seals and gaskets.
Reinforced Materials: A Hybrid Approach
Incorporating fillers like glass fibers into thermoplastics can enhance their mechanical properties, providing a hybrid solution that combines the benefits of thermoplastics with added strength. This approach is particularly advantageous in applications demanding high durability.
Conclusion: Weighing the Alternatives
Each alternative material presents unique benefits and challenges. Thermoplastics offer recyclability and ease of processing, elastomers provide flexibility, and reinforced materials deliver enhanced strength. Choosing the right material depends on the specific requirements of the application, such as durability, flexibility, or environmental considerations.
Thermoplastics can be recycled, unlike thermosetting plastics.True
Thermoplastics can be remelted and reshaped, allowing recyclability.
Elastomers cannot be used in injection molding processes.False
Elastomers are suitable for injection molding due to their elasticity.
Conclusion
In summary, thermosetting plastics present significant challenges for injection molding. Exploring thermoplastics could lead to innovative and versatile manufacturing solutions.
-
Explores key differences between thermoplastics and thermosetting plastics.: Thermoplastics can melt under heat after curing while thermoset plastics retain their form and stay solid under heat once cured. ↩
-
Provides examples and uses of various thermosetting plastics.: Thermosetting Plastic Examples · Epoxy Resins. Commonly used in adhesives, coatings, and composite materials. · Phenolic Resins. Used in circuit boards and … ↩
-
Understand the basic principles and stages of injection molding.: Injection molding is a complex manufacturing process. Using a specialized hydraulic or electric machine, the process melts, injects and sets plastic into the … ↩
-
Explore advancements in composite materials offering new properties.: A new composite material for car manufacture, Rilsan® Matrix is a high-temperature-resistant polyamide ribbon reinforced with continuous carbon fiber and … ↩
-
Learn about cutting-edge techniques reshaping plastic manufacturing.: Some of the most recent and exciting innovations in plastic manufacturing include recycling technology, polymer technology, and more. ↩
-
Explore the detailed process of injection molding and its advantages.: With injection molding, molten plastic is injected into a mold cavity under high pressure, creating a part all at once. Both processes are … ↩
-
Explore why thermosetting plastics are unsuitable for injection molding.: The typical injection molding machine based around the screw auger is not suitable for thermoset plastics due to the nature of the materials. If … ↩