Ever wondered what differences exist between thermoplastics and thermosets? Let’s explore the interesting world of plastics together!
This blog post explores the main differences between thermoplastics and thermosetting plastics. We focus on their molecular structure, mechanical strength, heat resistance and chemical stability. Understanding these differences is crucial for choosing the right material for your projects.
I remember my first project as a designer. I looked at piles of plastic samples and felt overwhelmed by the choices. Understanding the material properties of thermoplastics and thermosets became very important to choose the right one. Thermoplastics are like flexible friends. They soften when heated and harden when cooled. Thermosets behave differently. They form a permanent bond after curing. This is much like how some friendships really strengthen over time. Let us explore these differences more and see how they affect our design choices in manufacturing.
Thermoplastics can be reshaped upon heating.True
Thermoplastics become pliable when heated, allowing for reshaping and recycling, unlike thermosets which cannot be remolded once set.
Thermosets have higher heat resistance than thermoplastics.True
Thermosetting plastics maintain their shape and strength at higher temperatures compared to thermoplastics, making them ideal for heat-resistant applications.
- 1. What Are Thermoplastics and Thermosets?
- 2. How Does Molecular Structure Affect Performance?
- 3. What Are the Mechanical Properties of Each Type?
- 4. Which Plastics Offer Better Heat Resistance?
- 5. How Do Chemical Stability and Environmental Factors Influence My Material Choices?
- 6. What Are the Processing Techniques for Thermoplastics vs. Thermosets?
- 7. Conclusion
What Are Thermoplastics and Thermosets?
Have you ever thought about the materials that form the products we use every day? Let’s explore the interesting world of thermoplastics and thermosets. These materials affect how we design and choose our items.
Thermoplastics are flexible materials. They soften when heated and harden as they cool down. In contrast, thermosets change forever when heated. They form strong bonds. This main difference affects how they are used in manufacturing. It also influences the design of products. The choice of material depends on the project.
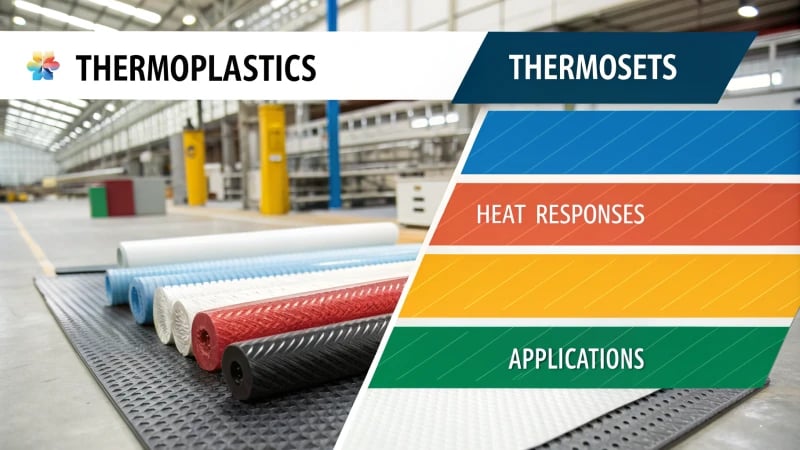
Thermoplastics and thermosets represent two essential classes of polymers, each with unique properties that influence their applications in manufacturing and product design. Understanding these differences can significantly impact material selection for various projects.
Molecular Structure
Thermoplastics feature linear or branched molecular structures without chemical bonds between chains. This flexibility allows them to soften when heated and harden upon cooling. Common examples include polyethylene and polypropylene.
In contrast, thermosetting plastics undergo a chemical reaction during heating, creating a permanent cross-linked structure. This transformation results in a three-dimensional network that cannot be re-melted or reshaped after curing, making them suitable for high-strength applications.
Mechanical Properties
Property | Thermoplastics | Thermosetting Plastics |
---|---|---|
Toughness | Good | High |
Rigidity | Varies (high for crystalline types) | Generally high |
Flexibility | Good (varies by type) | Generally low (often brittle) |
Thermoplastics exhibit good toughness and can withstand deformation. For instance, nylon shows high mechanical strength, while polyvinyl chloride provides flexibility. Thermosets, like epoxy resin, offer superior rigidity and mechanical strength, making them ideal for demanding structural applications.
Heat Resistance
Thermoplastics generally have lower heat resistance, with operational temperatures often below their glass transition temperature (Tg) or melting point (Tm). For example, polyvinyl chloride can handle temperatures around 60°C-80°C, whereas high-performance variants can exceed 150°C-250°C.
On the other hand, thermosets maintain stable performance at higher temperatures due to their cross-linked structure. Some thermosetting plastics can function effectively at temperatures of 200°C-300°C or beyond, making them suitable for applications in extreme environments.
Chemical Stability
Both classes of plastics show good chemical stability, although performance can vary widely:
- Thermoplastics like polytetrafluoroethylene are resistant to strong acids and bases, earning them the title "king of plastics".
- Thermosets, such as phenolic resin, are also resistant to chemical degradation, making them valuable for creating equipment that endures harsh environments.
Dimensional Stability
Thermoplastics are susceptible to deformation under heat or stress, which affects their dimensional stability. To mitigate this, manufacturers often reinforce thermoplastics with fillers or fibers.
Conversely, once cured, thermosetting plastics maintain excellent dimensional stability, resisting environmental changes such as temperature fluctuations and humidity. This property makes them ideal for precision components.
Processing Performance
Processing Method | Thermoplastics | Thermosetting Plastics |
---|---|---|
Molding Techniques | Easy (extrusion, injection) | Complex (requires curing) |
Recycling Potential | High (can be recycled) | Low (once set cannot be remolded) |
The processing characteristics differ notably between the two:
- Thermoplastics can be easily molded into various shapes using techniques like extrusion and injection molding, facilitating large-scale production.
- Thermosets require more complex processes involving heat and pressure for curing, leading to lower production efficiency and limited recycling options.
Electrical Properties
Most thermoplastics provide excellent electrical insulation, suitable for manufacturing insulation layers in cables. Some can be modified to become
In contrast,
thermosetting plastics are also known for their insulating properties and are often utilized in electronic applications due to their good bonding characteristics and ability to withstand high temperatures.
By understanding the distinct properties and behaviors of thermoplastics and thermosets, product designers like Jacky can make informed choices that optimize performance while meeting functional and aesthetic requirements in product design.
Thermoplastics can be reshaped after cooling.True
Thermoplastics soften when heated and harden upon cooling, allowing reshaping. This property is beneficial for various manufacturing processes.
Thermosets can be recycled easily after curing.False
Once thermosets are cured, they form a permanent structure that cannot be remolded or recycled, limiting their reuse in manufacturing.
How Does Molecular Structure Affect Performance?
Do you ever think about how small parts of materials affect what they do every day? Let’s explore this really interesting link together!
The structure of molecules strongly affects how materials perform. It decides their mechanical strength, thermal stability and resistance to chemicals. Understanding this is very important in many industries. It tells us how materials behave in different situations.
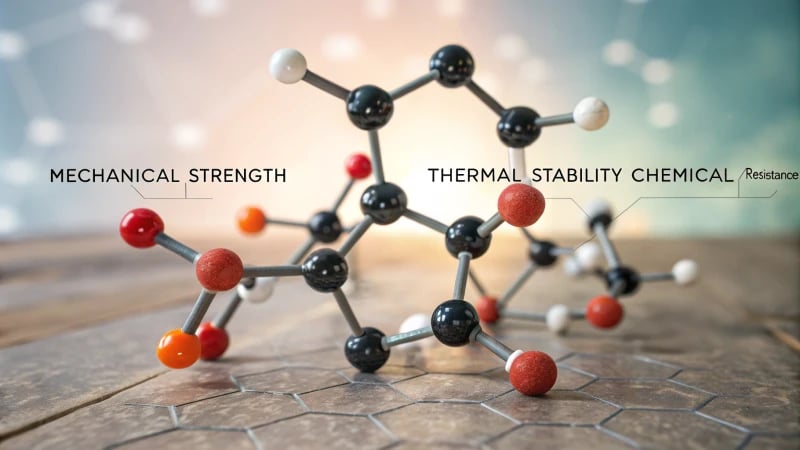
Understanding Molecular Structure
Molecular structure refers to how atoms bond and organize within a molecule. This deeply influences the physical and chemical traits of materials. Let me share a memory. The first time I used thermoplastics, I was amazed. Their linear or branched designs let them soften when heated, transforming into various shapes easily. This seemed like magic as I watched a hard plastic turn soft and moldable. This versatility makes thermoplastics very popular in manufacturing. Different from these, thermosetting plastics were a true revelation for me. Once they set, they form a strong, three-dimensional network that withstands heat and pressure, providing reliability in tough situations.
Performance Characteristics of Thermoplastics vs Thermosetting Plastics
Property | Thermoplastics | Thermosetting Plastics |
---|---|---|
Molecular Structure | Linear or branched | Cross-linked after curing |
Heat Resistance | Lower (60°C-80°C) | Higher (200°C-300°C) |
Chemical Stability | Varies, e.g., polytetrafluoroethylene | Generally good, e.g., epoxy resins |
Dimensional Stability | Poor, prone to deformation | Excellent, maintains shape |
Processing Performance | High efficiency, recyclable | Low efficiency, non-recyclable |
Electrical Properties | Good insulation, some conductive types | Excellent insulation, bonding properties |
The Role of Molecular Weight
Another interesting topic is molecular weight. In the lab, I experimented with several polymers and noticed how those with higher molecular weight felt more robust and flexible. These materials showed great strength and toughness—perfect for high-performance parts that must endure harsh conditions (high-performance parts1).
Implications for Product Design
Understanding molecular structure is crucial for designers like me. It’s not only about looks; it’s about performance and durability. For example, if high thermal resistance is required, choosing thermosetting plastics made perfect sense as they provided the durability we needed. In another project focused on easy processing and recycling, thermoplastics were ideal here.
Summary of Key Considerations
The link between molecular structure and performance is really complex yet vital. It directly affects the mechanical, thermal, chemical, and electrical properties of materials used in countless applications. Making informed choices about materials leads to better and more sustainable products. Exploring more about innovative material uses in technology is very beneficial; consider looking into molecular electronics2.
Through my journey, I have truly appreciated that grasping molecular structures is not just academic; it’s a vital part of crafting products that can really improve lives.
Thermoplastics are more heat resistant than thermosetting plastics.False
This claim is false; thermosetting plastics have higher heat resistance, typically ranging from 200°C to 300°C, compared to thermoplastics' lower resistance of 60°C to 80°C.
Higher molecular weight polymers enhance strength and toughness.True
This claim is true; higher molecular weight polymers generally exhibit improved mechanical properties, making them stronger and tougher for demanding applications.
What Are the Mechanical Properties of Each Type?
Do you ever think about why materials we use daily act so differently under pressure? Let’s explore the interesting world of thermoplastics and thermosetting plastics. These materials have unique features. They influence our engineering decisions.
Thermoplastics are famous for their toughness. They also provide different levels of flexibility. Thermosetting plastics supply high strength and rigidity. However, they are often more brittle. Knowing these mechanical properties is very important. It really helps in choosing the right material for engineering projects.
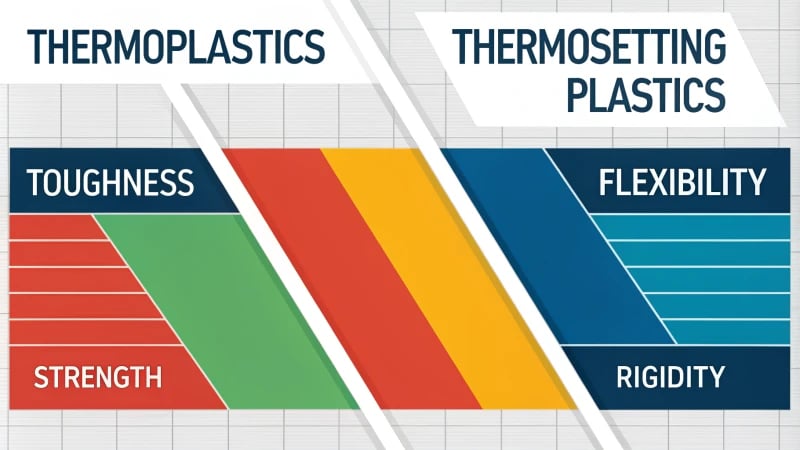
Mechanical Properties of Thermoplastics
Thermoplastics exhibit a wide range of mechanical properties that can vary significantly depending on their molecular structure and the presence of additives. Generally, they are known for their good toughness and impact resistance.
Property | Description |
---|---|
Toughness | Ability to withstand deformation without breaking. |
Impact Resistance | High resistance to sudden forces, making them ideal for protective applications. |
Flexibility | Varies widely; crystalline types (e.g., nylon) are less flexible than non-crystalline types (e.g., polycarbonate). |
For instance, crystalline thermoplastics like nylon and polyoxymethylene exhibit high mechanical strength and rigidity but offer less flexibility. In contrast, non-crystalline varieties like polyvinyl chloride provide better flexibility albeit with lower mechanical strength. This distinction is crucial when selecting materials for applications such as automotive components3 or consumer electronics4.
Mechanical Properties of Thermosetting Plastics
On the other hand, thermosetting plastics are renowned for their superior mechanical strength and rigidity due to their cross-linked molecular structure. Here’s a brief overview:
Property | Description |
---|---|
Strength | High mechanical strength, making them suitable for heavy-duty applications. |
Rigidity | Excellent rigidity due to permanent cross-linking. |
Brittleness | Often brittle, leading to lower toughness compared to thermoplastics. |
For example, phenolic resins and epoxy resins are commonly used in manufacturing components like gears and bearings, which require high strength under stress. However, this brittleness can be a disadvantage in applications where flexibility is required, such as in flexible tubing5.
Comparing Mechanical Properties: A Summary
To better visualize the differences, here’s a comparative table summarizing the key mechanical properties of both types of plastics:
Property | Thermoplastics | Thermosetting Plastics |
---|---|---|
Toughness | Good | Poor |
Impact Resistance | High | Moderate |
Flexibility | Varies (high in non-crystalline types) | Low |
Strength | Moderate to high | High |
Rigidity | Moderate to low | High |
Brittleness | Low | High |
Understanding these properties is vital for professionals like Jacky, who must ensure that designs not only meet aesthetic requirements but also perform effectively under various conditions. For more detailed insights on material properties, consider exploring resources on material selection6 or engineering applications7.
Thermoplastics are generally more flexible than thermosetting plastics.True
Thermoplastics exhibit varying flexibility, especially non-crystalline types, unlike the low flexibility of thermosetting plastics due to their rigid structure.
Thermosetting plastics have better toughness than thermoplastics.False
Thermosetting plastics are often more brittle and have lower toughness compared to the good toughness exhibited by thermoplastics.
Which Plastics Offer Better Heat Resistance?
Selecting the proper plastic for hot conditions is difficult. But knowing the details of heat resistance is crucial. Let’s explore this subject together. Let’s discover the best choices for our needs!
When choosing plastics for high-temperature uses, thermoplastic materials like PEEK give good heat resistance for short times between 150-250°C. Thermosetting plastics such as polyimide show remarkable stability at much higher temperatures, reaching up to 300°C. Knowing these differences is crucial. It really helps in choosing the right plastic.
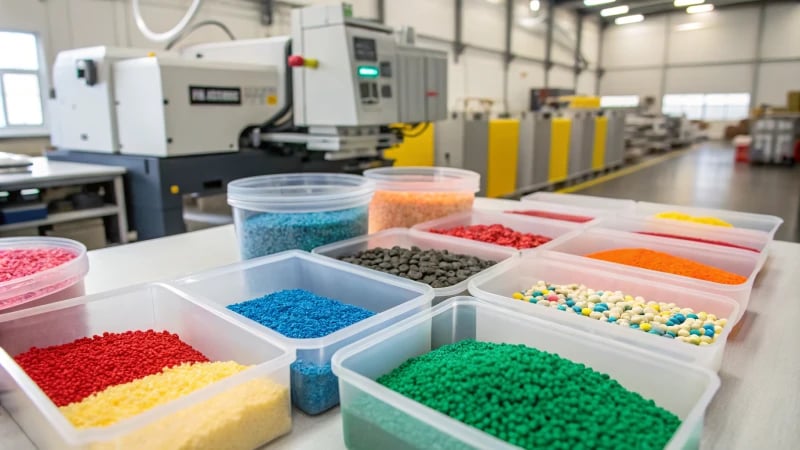
Understanding Heat Resistance in Plastics
Heat resistance is crucial when picking materials for high-temperature use. I know this because using the wrong type led to sticky problems!
Thermoplastics: Pros and Cons
Thermoplastics generally don’t do well with heat. Their molecular structure allows them to soften and flow when heated, which means they probably lose shape at high temperatures. For instance:
Material | Glass Transition Temperature (Tg) | Melting Point (Tm) | Common Uses |
---|---|---|---|
Polyvinyl Chloride (PVC) | 60-80°C | 75-80°C | Pipes, cables |
Polyether Ether Ketone (PEEK) | 143°C | 334°C | Aerospace, automotive applications |
High-performance thermoplastics like PEEK amazed me. They withstand short bursts of 150-250°C! They are very versatile, making them suitable for specialized applications in industries like aerospace8.
Thermosetting Plastics: The Strong Contenders
Thermosetting plastics are like reliable friends in tough spots. After curing, their structure remains very stable at high temperatures. Some examples include:
Material | Maximum Operating Temperature | Common Uses |
---|---|---|
Polyimide | Up to 300°C | Aerospace components, electronics |
Epoxy Resin | Up to 150-200°C | Adhesives, coatings, structural parts |
Thermosetting plastics like polyimide are true powerhouses. They endure exposure to temperatures up to 300°C, making them preferable for high-performance applications in automotive9.
Key Considerations for Material Selection
When choosing between thermoplastics and thermosetting plastics based on heat resistance, I consider a few points:
- Application Requirements: Think about the temperature and mechanical stresses the plastic faces.
- Processing Methods: Thermoplastics are easier to process; however, thermosetting plastics require more complex molding techniques.
- Cost and Availability: Budget can play a very big role in your choices.
Understanding these differences helps designers like Jacky decide well. Good decisions match performance with production efficiency. It’s about finding the perfect balance! If you’re curious about heat-resistant materials, check out our insights on material innovation10.
Thermoplastics generally have lower heat resistance than thermosets.True
Thermoplastics soften under heat, making them less stable than thermosetting plastics, which maintain structural integrity at high temperatures.
Polyimide can operate at temperatures up to 300°C.True
Polyimide is a thermosetting plastic known for its superior heat resistance, suitable for extreme conditions like aerospace applications.
How Do Chemical Stability and Environmental Factors Influence My Material Choices?
When choosing materials, I often think about chemical stability and how the environment affects my choices. These elements are important. These factors really change how products are designed and how they work. Product design and performance improve with this understanding.
Chemical stability is very important for choosing materials. It affects how substances keep their properties in different surroundings. Temperature and humidity significantly change product safety. They also influence effectiveness. Designers rely on these factors when selecting materials.
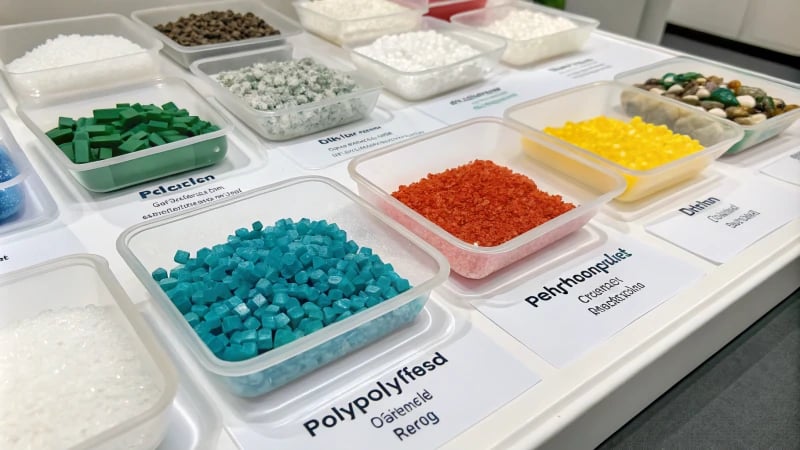
Understanding Chemical Stability
Chemical stability is more than a technical term; it is vital for the products I create. It dictates how well materials endure various situations. For example, I once worked on a project choosing plastic for an electronic device. I had to consider how temperature and humidity would impact materials. This led to surprising discoveries about their lifespan and safety.
Chemical stability refers to the ability of a substance to maintain its chemical structure and properties under various environmental conditions. In the context of material selection, this stability is crucial for ensuring the performance and longevity of a product.
For instance, thermoplastics like polytetrafluoroethylene (PTFE) are known for their exceptional chemical resistance. They can withstand harsh chemicals, making them suitable for applications in corrosive environments. On the other hand, some thermoplastics, like polycarbonate, may degrade when exposed to certain solvents, which can impact their effectiveness in specific applications.
By examining different materials’ stability, designers can make informed choices based on their performance requirements and environmental conditions they will encounter in use.
Environmental Factors at Play
Temperature, humidity and chemical exposure play significant roles in choosing materials. These factors impact everything from durability to how the product functions. They act like an unseen force guiding my designs.
Environmental Factor | Effect on Thermoplastics | Effect on Thermosetting Plastics |
---|---|---|
Temperature | Can soften and lose shape at high temps | Retains shape and structure at high temps |
Humidity | Can absorb moisture, affecting dimensional stability | Generally less affected due to cross-linked structure |
Chemical Exposure | Varies; some resist corrosion, while others degrade | Typically resistant to a wide range of chemicals |
This table highlights the differences in response between thermoplastics and thermosetting plastics under varying environmental conditions, which aids in choosing the appropriate material based on the intended application.
Implications for Product Efficacy
Choosing materials based on chemical stability is very important. I once worked on packaging for a pharmaceutical client. The strength of our materials was crucial. If the packaging’s chemical stability was not right, it could affect the product’s shelf life and safety. This made me realize that my choices could impact someone’s health.
The choice of materials based on their chemical stability can significantly impact product efficacy. For example, in pharmaceutical applications, the chemical stability of the packaging material can influence the shelf life and safety of the product.
Choosing materials that can resist degradation under environmental conditions ensures that pharmaceuticals remain effective until their expiration date. Designers must consider factors like temperature fluctuations during transportation and storage when selecting packaging materials.
Making Informed Decisions
Incorporating chemical stability and environmental factors into designs is challenging. I analyze how materials behave under expected conditions. I focus on truly optimizing designs for both looks and functionality.
Incorporating chemical stability and environmental factors into the decision-making process involves careful analysis. By evaluating various materials’ performance under expected conditions, designers like Jacky can optimize designs not just for aesthetics but also for functionality and longevity.
If you want to learn more, explore chemical stability types11 or methods to determine stability12. Understanding these ideas can really change how you approach the field.
Chemical stability is crucial for product longevity.True
Material selection based on chemical stability ensures products perform effectively over time, resisting environmental degradation.
Thermoplastics generally resist high temperatures better than thermosets.False
Thermosetting plastics retain their shape at high temperatures, while thermoplastics may soften or lose form under similar conditions.
What Are the Processing Techniques for Thermoplastics vs. Thermosets?
Have you ever thought about what makes thermoplastics different from thermosetting plastics? I invite you to explore the interesting world of plastic processing methods. These insights might really help your next project succeed.
Thermoplastics undergo processes such as injection molding and extrusion. Heat reshapes them easily. Thermosetting plastics need curing. This process hardens them forever. The hardening impacts their recyclability. Production efficiency is also affected.
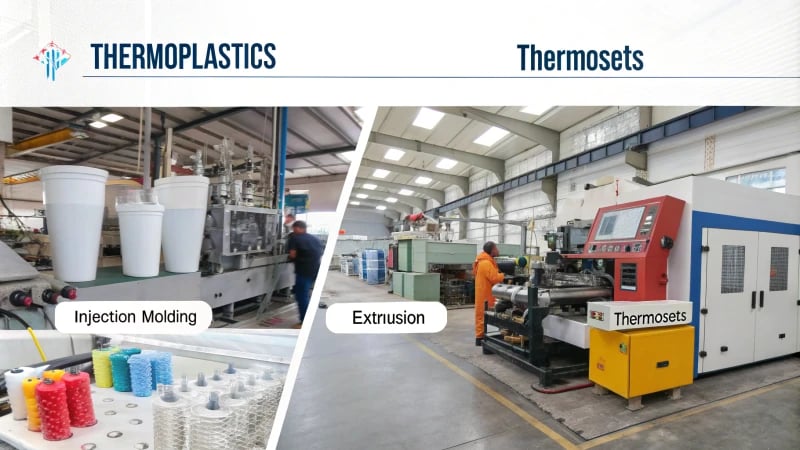
Understanding Thermoplastic Processing Techniques
Thermoplastics are fascinating due to their versatility. Their molecules let them change shape when heated, allowing for various manufacturing methods, including:
- Injection Molding: Imagine melted plastic injected into a mold. It’s like creating a unique piece of art. The options are endless!
- Extrusion: This method pushes thermoplastic through a die to create continuous shapes like pipes or sheets. These shapes serve many uses.
- Blow Molding: I enjoy this technique! Hot plastic inflates inside a mold to create hollow objects, like bottles. It’s like blowing up a balloon but even cooler!
- Thermoforming: A plastic sheet heats up and forms over a mold with vacuum pressure. It’s satisfying to watch a flat sheet become a 3D shape.
These techniques allow efficient production and complex designs. Thermoplastics are recyclable, which comforts me as I strive for sustainable design.
Thermosetting Plastics Processing Techniques
Thermosetting plastics offer a different story. Once cured, their chemical structure becomes rigid, and this change cannot reverse – a fact I respect in designing. Their processing techniques include:
- Compression Molding: Thermosetting material goes into a heated mold where pressure is applied. This is great for large parts and heavy-duty uses.
- Transfer Molding: Resin enters a mold cavity through a sprue; it’s ideal for detailed designs.
- Injection Molding (with limitations): Thermosets also undergo injection molding; however, curing complicates the process and often leads to slower production than thermoplastics.
Curing needs heat and pressure, making it less efficient than thermoplastic methods. Once set, thermosetting plastics cannot remold or recycle easily, raising sustainability issues that matter deeply to me.
Comparative Table of Processing Techniques
Feature | Thermoplastics | Thermosetting Plastics |
---|---|---|
Reprocessability | Yes | No |
Molding Methods | Injection, Extrusion, Blow Molding | Compression, Transfer Molding |
Curing Requirement | No curing needed | Requires curing |
Production Speed | High | Lower due to curing |
Design Complexity | High | Moderate |
This table shows the characteristics of each material that affect their processing methods. Knowing these details helps me choose the right plastic for projects while meeting both aesthetic and functional needs.
Thermoplastics can be reshaped upon heating.True
This characteristic allows thermoplastics to be processed using various methods, making them versatile in manufacturing.
Thermosetting plastics can be remolded after curing.False
Once cured, thermosetting plastics become rigid and cannot be reshaped or recycled, limiting their reprocessability.
Conclusion
Explore the essential differences between thermoplastics and thermosetting plastics regarding their properties, applications, and processing techniques to make informed material choices in design.
-
Discover in-depth insights on how molecular structure influences material properties and applications across industries. ↩
-
Gain comprehensive knowledge about the differences between thermoplastics and thermosetting plastics for better design choices. ↩
-
This link provides comprehensive material comparisons that are essential for understanding mechanical properties in engineering contexts. ↩
-
Gain insights into practical applications and case studies related to the mechanical properties of plastics by visiting this link. ↩
-
Find extensive resources on material selection criteria based on mechanical properties that can enhance your engineering projects. ↩
-
Explore real-world examples and research articles that illustrate the behavior of different materials under stress. ↩
-
Discover advanced insights into engineering applications that require specific material properties for optimal performance. ↩
-
This query will lead you to detailed guides on selecting heat-resistant plastics for industrial applications, providing valuable insights for your projects. ↩
-
Explore this link to learn about innovative materials that can withstand high temperatures and their practical applications across various industries. ↩
-
This search will help you find comprehensive comparisons between different types of plastics regarding their heat resistance capabilities. ↩
-
Clicking this link will enhance your understanding of different types of chemical stability, which is essential for making informed material choices. ↩
-
This resource provides methods for determining chemical stability, which is vital for ensuring product efficacy in varying environments. ↩