Have you ever wondered why some molded plastic parts come out flawless while others fall short? The secret often lies in temperature control.
Temperature control is essential in plastic injection molding because it directly impacts plastic fluidity, product dimensional accuracy, mechanical properties, and production efficiency. Proper temperature management ensures high-quality products and optimizes the molding process.
While understanding the basic importance of temperature control is vital, diving deeper into how it influences specific aspects of the molding process can significantly enhance your production strategy. Let’s explore these elements to maximize efficiency and quality in your operations.
Temperature affects plastic fluidity in molding.True
Temperature alters plastic viscosity, affecting flow and mold filling.
How Does Temperature Affect Plastic Fluidity in Molding?
Temperature plays a crucial role in determining the fluidity of plastic during injection molding, impacting product quality significantly.
Temperature impacts plastic fluidity in molding by altering viscosity. Low temperatures increase viscosity, reducing flow, while high temperatures enhance flow but risk decomposition.

The Role of Temperature in Plastic Flow
In the realm of plastic injection molding1, temperature is a pivotal element that determines the ease with which plastic flows into a mold. A well-managed temperature ensures that the plastic maintains optimal fluidity, a key factor in achieving fully-formed and defect-free products.
Low Temperatures: The Viscosity Challenge
When the temperature is too low, the viscosity of the plastic increases. This heightened viscosity diminishes the plastic’s ability to flow smoothly, often resulting in incomplete mold filling. This situation can lead to defects such as short shots or voids, particularly in intricate designs. For instance, consider manufacturing components with complex geometries like automotive parts, where insufficient flow can significantly impair product quality.
High Temperatures: Balancing Benefits and Risks
Conversely, higher temperatures reduce viscosity, promoting better flow characteristics. However, this benefit comes with risks. Excessive heat can lead to issues like plastic decomposition, which not only alters the material’s properties but can also cause problems such as discoloration or bubble formation. For example, heat-sensitive plastics may decompose rapidly, losing their intrinsic properties and potentially clogging machinery.
Finding the Optimal Temperature Range
Achieving optimal plastic fluidity involves striking a balance between these extremes. This balance ensures that the material flows efficiently into every crevice of the mold without compromising its integrity. In practice, this means calibrating the temperature settings based on the specific type of plastic and the design complexity of the mold.
Temperature Condition | Effects on Fluidity | Potential Issues |
---|---|---|
Low | High Viscosity | Short shots |
Optimal | Balanced Flow | None |
High | Low Viscosity | Decomposition |
By maintaining precise control over temperature settings, manufacturers can optimize the fluidity of plastics, ensuring robust and high-quality end products. This balance is essential not only for maintaining product integrity but also for enhancing overall production efficiency and cost-effectiveness.
Understanding these dynamics allows businesses to improve their injection molding processes significantly by tailoring strategies to specific production needs and challenges. Learn more about optimizing molding processes2.
Low temperature increases plastic viscosity in molding.True
Low temperatures increase viscosity, reducing plastic flow efficiency.
High temperature reduces risk of plastic decomposition.False
High temperatures can cause decomposition, altering material properties.
What Role Does Temperature Play in Dimensional Accuracy?
Temperature fluctuations can dramatically affect the dimensional accuracy of molded plastic products, impacting their functionality and fit.
Temperature affects dimensional accuracy by altering the shrinkage rates of plastics during cooling. Precise temperature control minimizes dimensional deviations and ensures that parts meet strict tolerance requirements.
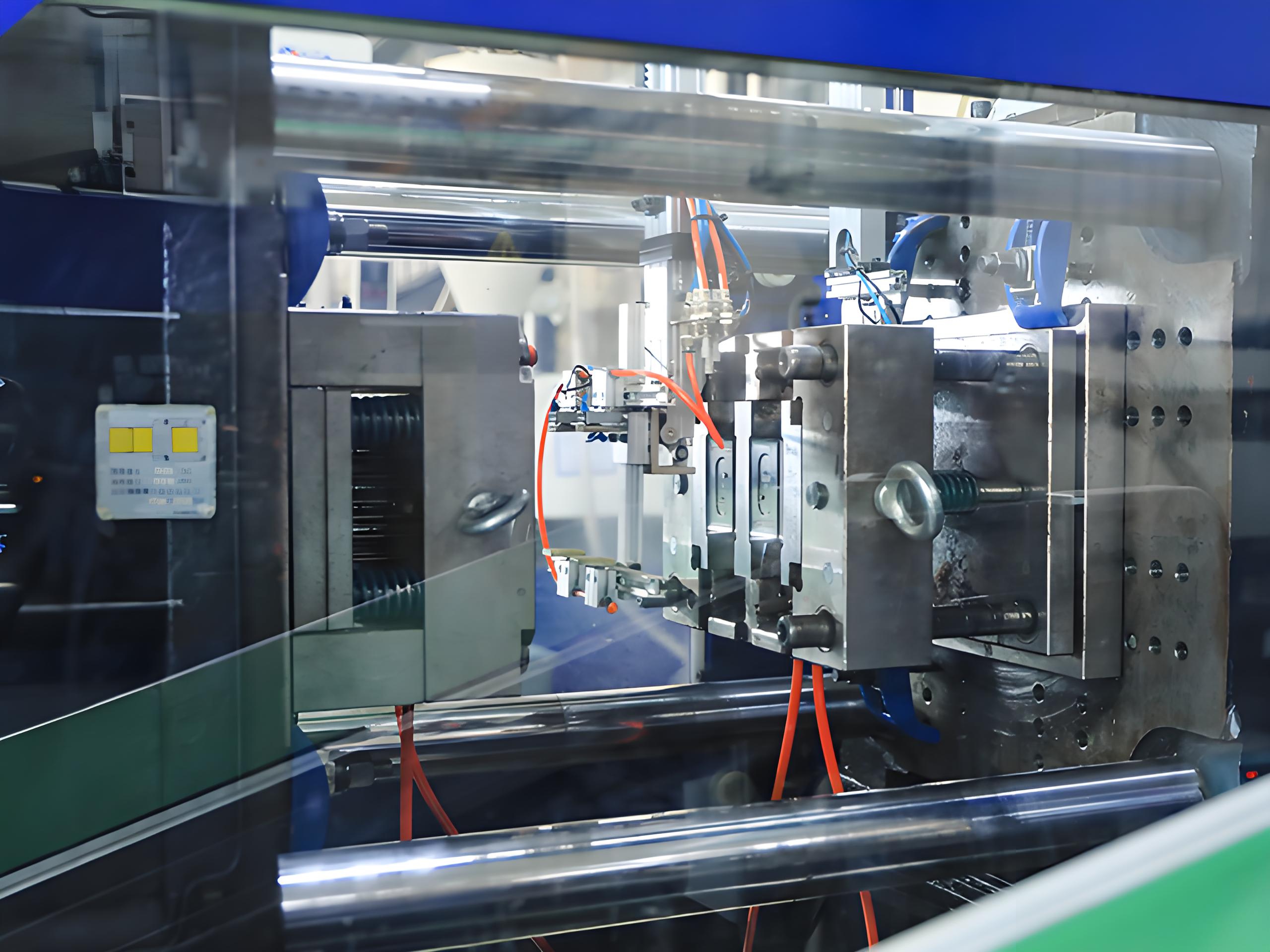
The Science Behind Dimensional Accuracy
Dimensional accuracy in plastic injection molding refers to how closely the finished part matches its intended dimensions. Temperature plays a crucial role in this aspect, primarily through its impact on the shrinkage rate of plastics3.
When plastic cools, it shrinks. The degree of shrinkage depends largely on the material used and the temperature at which it is processed. If the temperature is inconsistent, so too will be the shrinkage, leading to parts that are either too large or too small. This inconsistency is especially problematic for high-precision components.
Effects of Temperature Variations
High Temperatures
At elevated temperatures, plastics may exhibit increased fluidity. While this can help in achieving better mold filling, it also leads to greater shrinkage variability as the material cools, potentially resulting in parts that do not fit their intended design specifications.
Temperature | Fluidity | Shrinkage | Dimensional Accuracy |
---|---|---|---|
Low | Low | Low | High |
Optimal | Optimal | Consistent | Optimal |
High | High | High | Variable |
Low Temperatures
Conversely, lower temperatures reduce plastic fluidity, which can result in incomplete mold filling and defects such as short shots. These defects can lead to parts that are dimensionally inaccurate right from the outset.
Strategies for Maintaining Dimensional Accuracy
To ensure dimensional accuracy, manufacturers must meticulously control the injection molding temperature within an optimal range. This involves:
- Pre-heating molds: To achieve uniform cooling and minimize shrinkage variations.
- Regular calibration of machinery: Ensuring that temperature controls are precise and consistent.
- Using predictive modeling: Software can predict how different temperatures will affect shrinkage, allowing for preemptive adjustments.
Implementing these strategies can significantly enhance the precision and reliability of injection-molded parts.
Understanding the role of temperature4 is essential for manufacturers aiming to produce parts with stringent dimensional tolerances. By maintaining precise temperature control, manufacturers can produce components that not only fit perfectly but also function as intended.
High temperatures increase plastic shrinkage variability.True
Elevated temperatures cause greater shrinkage variability, affecting accuracy.
Low temperatures improve mold filling and dimensional accuracy.False
Low temperatures reduce fluidity, leading to incomplete mold filling.
How Does Temperature Influence Mechanical Properties of Plastics?
Temperature is a key factor that determines the mechanical behavior of plastics during the injection molding process.
Temperature affects the mechanical properties of plastics by altering molecular arrangement and crystallization, impacting strength, hardness, and toughness. Proper temperature control ensures optimal molecular structure and mechanical performance in molded products.

Understanding Molecular Arrangement
The mechanical properties of plastics, such as strength, hardness, and toughness, are significantly influenced by the molecular arrangement within the material. During the injection molding process5, temperature plays a crucial role in determining how these molecules are arranged.
-
Moderate Temperatures: When the molding temperature is set appropriately, it allows plastic molecules to align and crystallize effectively. This molecular alignment results in enhanced mechanical properties, providing strength and stability to the final product.
-
Low Temperatures: If the temperature is too low, it can lead to incomplete crystallization. This lack of crystallization results in loosely packed molecular structures, thereby reducing the material’s mechanical strength.
-
High Temperatures: Conversely, excessive heat can cause molecular chains to break down. This breakdown can lead to a loss of mechanical integrity, making the material less durable.
Impact on Material Crystallization
Crystallization within plastics is vital for achieving desired mechanical properties. The crystallization process is highly temperature-dependent:
Temperature | Crystallization Result | Mechanical Outcome |
---|---|---|
Optimal | Complete crystallization | High strength and toughness |
Low | Incomplete crystallization | Reduced strength and hardness |
High | Over-crystallization or chain degradation | Compromised durability |
By understanding how temperature affects crystallization, manufacturers can adjust their injection molding processes6 to ensure robust product quality.
Ensuring Quality in High-Load Applications
For products that are designed to withstand significant loads, such as automotive components and electrical housings, maintaining precise temperature control is essential. Adequate temperature settings ensure that these parts have the necessary mechanical strength and reliability.
In applications where high load-bearing capacity is a must, manufacturers must consistently monitor and adjust temperatures to maintain product quality standards7.
Proper temperature control not only enhances mechanical properties but also contributes to overall product consistency and reliability across different batches.
Low temperatures reduce plastic strength.True
Low temperatures prevent complete crystallization, weakening molecular structure.
High temperatures enhance plastic durability.False
High temperatures can degrade molecular chains, reducing material durability.
Can Temperature Control Enhance Production Efficiency?
In the realm of plastic injection molding, the careful management of temperature can drastically boost production efficiency, directly affecting cycle times and cost-effectiveness.
Temperature control enhances production efficiency by optimizing mold filling, reducing cooling times, and minimizing cycle durations. Proper temperature settings ensure the plastic flows well, fills molds swiftly, and cools quickly, thus accelerating the production process and cutting down on waste.
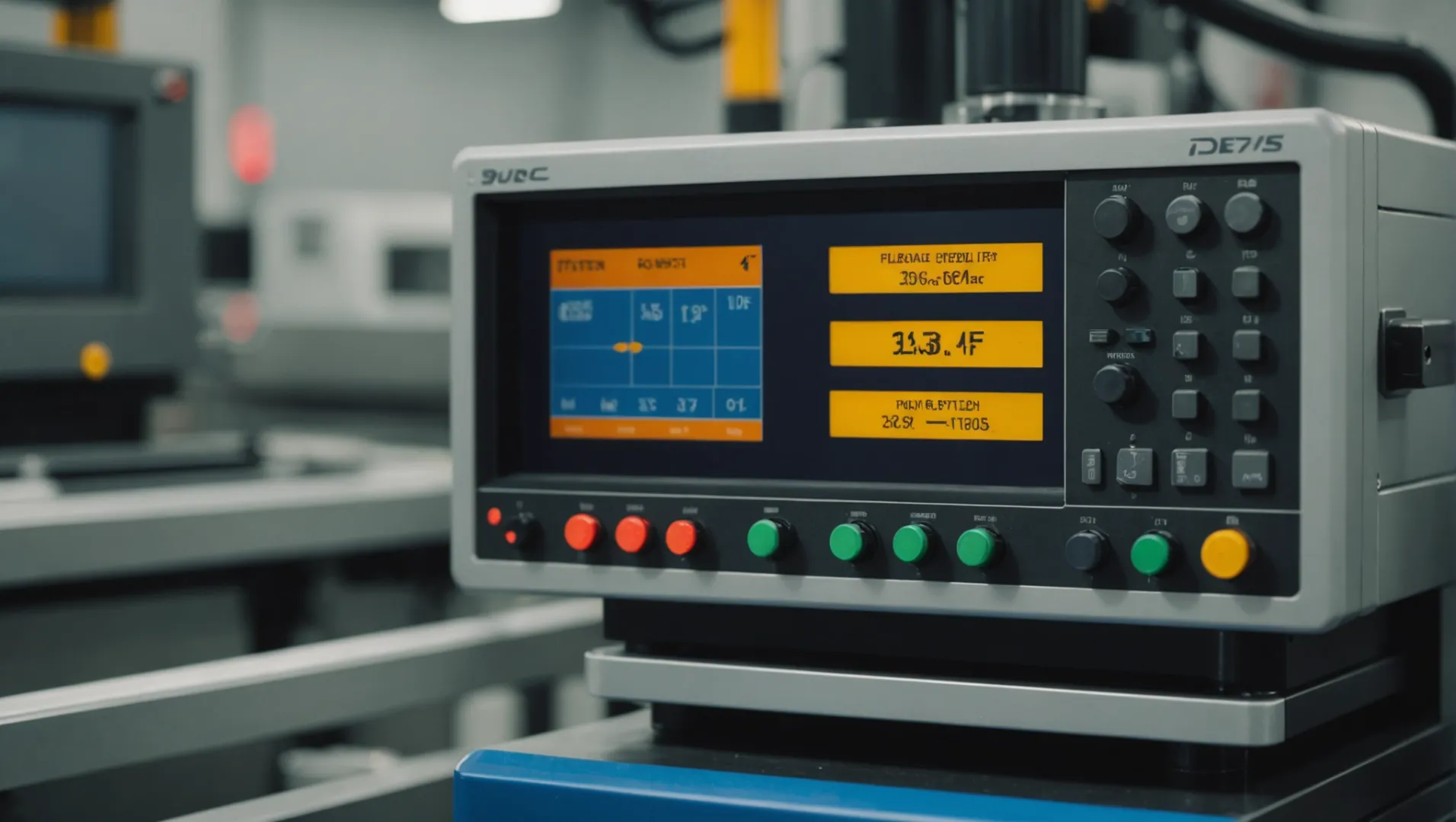
Optimizing Mold Filling for Efficiency
In plastic injection molding, achieving optimal mold filling is crucial for efficiency. By maintaining the right temperature, the plastic’s fluidity8 is enhanced, allowing it to flow smoothly into the mold. This ensures complete filling with fewer defects, such as short shots or incomplete products.
For instance, when molding intricate parts, the plastic must reach every corner of the mold swiftly to form a precise product without gaps or weaknesses. This rapid filling reduces time lost to defects and rework.
Reducing Cooling Times
Once the mold is filled, the cooling phase begins. A well-controlled temperature setting can significantly cut down cooling times. If temperatures are appropriately managed, plastics solidify at a faster rate without sacrificing quality. This quick cooling leads to shorter cycle times and higher throughput.
In contrast, improper temperature control can lead to prolonged cooling periods, resulting in bottlenecks and slower production rates.
Minimizing Cycle Durations
Efficient temperature control not only impacts filling and cooling but also affects the overall cycle duration. By reducing the time spent on each stage of the molding process, manufacturers can increase their output. Consistent temperatures prevent unnecessary adjustments and recalibrations, streamlining operations.
Moreover, frequent temperature fluctuations can cause delays as machines need to stabilize before proceeding with subsequent cycles. Maintaining consistent temperatures leads to smoother transitions between cycles and better machine performance.
Impact on Production Costs
Efficient temperature control in injection molding also directly influences production costs. By decreasing cycle times and minimizing material waste through precision molding, manufacturers save on both time and resources. This efficiency translates into lower operational costs and increased profitability.
In conclusion, by focusing on precise temperature management, manufacturers can achieve enhanced production efficiency, resulting in higher-quality products produced at a faster pace with reduced costs.
Temperature control reduces cooling times in molding.True
Proper temperature management speeds up plastic solidification, cutting cooling time.
Inconsistent temperatures improve cycle durations.False
Fluctuating temperatures cause delays and require machine recalibration.
Conclusion
By mastering temperature control in injection molding, you can ensure exceptional product quality while enhancing production efficiency.
-
Discover why temperature is critical for achieving effective plastic flow.: Resin viscosity: The higher the melt temperature, the lower the viscosity. If it’s too high, your resin will be overly thin and won’t be able to … ↩
-
Explore techniques to enhance molding process efficiency and quality.: Soft computing methods such as back-propagating neural networks and genetic algorithms can be utilized to optimize the injection molding process … ↩
-
Understand how temperature changes influence shrinkage rates and dimensional accuracy.: Decreased set time (less time to pump, place, and finish) · Increased rate of surface drying (potential for abnormal shrinkage cracking) · Increased water demand … ↩
-
Explore how precise temperature control enhances dimensional accuracy.: Temperature significantly impacts each step of the entire plastic injection molding process. This is why temperature control is crucial and … ↩
-
Discover how injection molding shapes plastic products efficiently.: Using a specialized hydraulic or electric machine, the process melts, injects and sets plastic into the shape of a metal mold that’s fitted into … ↩
-
Learn techniques for optimizing injection molding settings.: Steps to INJECTION MOLDING Process Optimization · 1. Tool functionality examination · 2. Short shot testing · 3. Gate seal studies · 4. Sample parts evaluation/data … ↩
-
Understand benchmarks for ensuring consistent product quality.: Specific plastic injection molding quality standards should be applied through the process so that every piece meets a client’s needs and use cases. ↩
-
Explore how temperature influences fluidity for better mold filling.: The mold temperature can be adjusted to enhance the fluidity of plastics with poor viscosity and low flow, such as PC, hard PVC, PSF, PPO, etc. ↩