Have you ever attempted to bake a cake without realizing if the ingredients are correct? It really resembles selecting materials for injection molding.
Materials suitable for injection molding include polypropylene, polystyrene, and polycarbonate, which offer properties like chemical stability and impact resistance. Conversely, materials like polytetrafluoroethylene (PTFE) are unsuitable due to high melting points and poor flowability.
This offers a quick look, but picking the right material takes more than just simple lists. One needs to learn each material’s special qualities and their match with project demands. We should explore these materials farther to discover the keys to effective injection molding.
Polypropylene is unsuitable for injection molding.False
Polypropylene often appears in injection molding because it flows well and withstands high temperatures.
What are the Key Properties of Injection Molding Materials?
Grasping the traits of materials utilized in injection molding holds importance for improving product performance and production efficiency.
Key properties of injection molding materials include thermal stability, impact resistance, chemical resistance, and ease of processing. These properties determine the suitability of a material for specific applications and influence the quality of the final product.
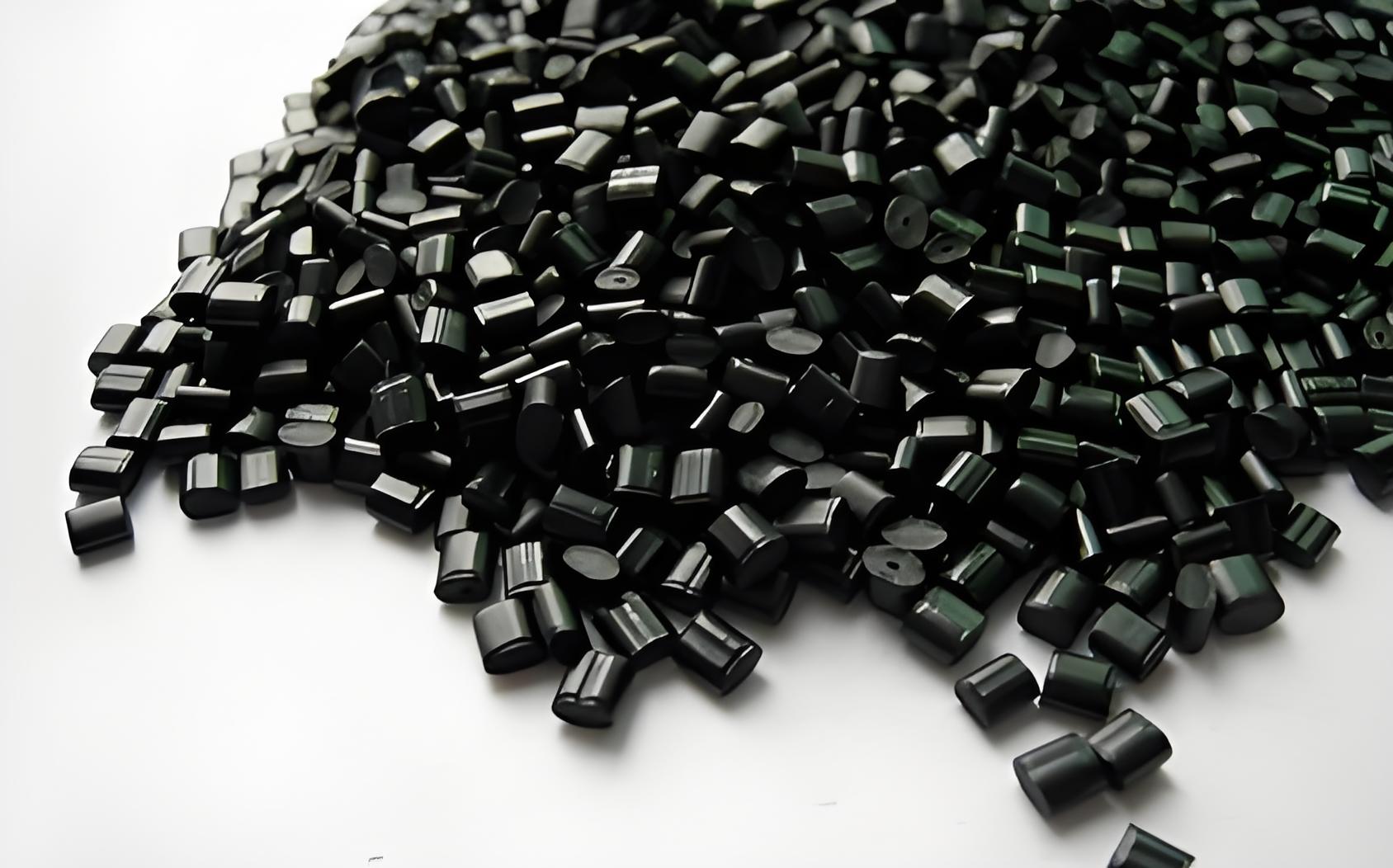
Heat Stability and Melting Points
Heat stability is a key feature of injection molding materials. It controls how a material behaves when hot during molding. For example, polypropylene (PP)1 handles heat very well, so it is great for high-temperature uses like car parts and home goods.
In contrast, polytetrafluoroethylene (PTFE)2 has a high melting point and flows poorly, making it a bad choice for injection molding. Materials need a melting point that lets them enter molds easily without breaking down or losing quality.
Shock Resistance and Mechanical Strength
Materials like polycarbonate (PC)3 have high shock resistance, important for strong products like electronics and medical tools.
Nylon (PA)4 is another example with great mechanical strength, often found in car and machinery parts because it resists wear and handles mechanical stress.
Chemical Resistance
Chemical resistance is very important because it keeps materials from getting damaged by chemicals. This matters a lot in tough places like inside cars or in medical gear.
Polystyrene (PS)5 resists chemicals well and is used in electronics and packaging because it offers a good mix of cost and performance.
Ease of Shaping
How easy it is to shape a material into complex forms matters too. ABS6 and PC+ABS alloys are good for their ease in shaping and holding complex designs while staying strong.
This feature affects the time and cost of making products. It is important for deciding which materials are practical for big manufacturing jobs.
Environmental Factors
With more focus on being green, biodegradable plastics are becoming popular in injection molding. These materials help lower environmental damage and fit with the global trend for eco-friendly items.
To finish, choosing the right material for injection molding means looking at these traits for your product needs. Every material has its own benefits and difficulties, which must be thought over carefully.
Polypropylene is unsuitable for high-temperature applications.False
Polypropylene shows great heat endurance, fitting for hot settings.
PTFE is ideal for injection molding due to its flowability.False
PTFE flows poorly, so it is not fit for injection molding.
How Do Different Materials Affect Injection Molding Processes?
Selecting the right materials is crucial in injection molding, affecting both product quality and process effectiveness.
Materials like polypropylene, polystyrene, and polycarbonate significantly impact injection molding by dictating processing parameters and final product properties.
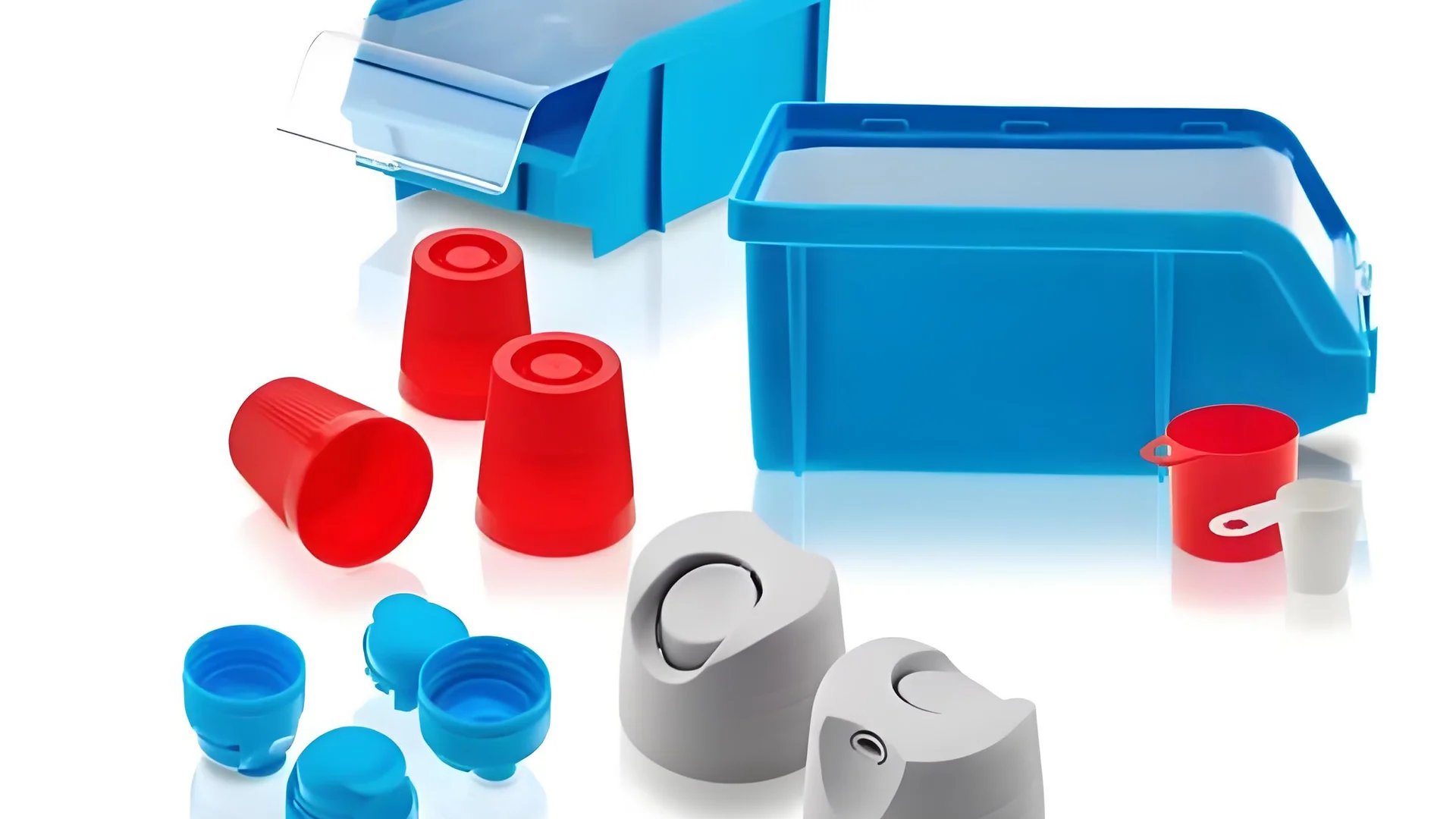
Understanding Material Characteristics
Injection molding holds a key spot in creating plastic items, providing precision and flexibility. Picking the right material is crucial for successful injection molding. Each material has special traits that decide how it acts during different processing situations.
Polypropylene (PP) is light and has good chemical stability. Widely used in car and medical fields because it withstands heat well. This material moves easily, so it’s simple to use in many methods, like injection molding. Its low price and flexibility make it a favorite for producers seeking budget-friendly production.
On the other hand, Polystyrene (PS) is more stiff and less strong but looks nice. It has good optical traits, making it great for clear products. However, it needs careful control of molding heat and pressure because it melts over a wider temperature range.
Impact on Process Conditions
Materials like Polycarbonate (PC) and Nylon (PA) are strong and resist impacts, needing special adjustments for best results. PC is great for electronics and medical tools but might crack if not handled carefully. Nylon is hard-wearing and used in mechanical parts, like gears.
Material | Main Features | Common Uses |
---|---|---|
Polypropylene | Light, Chemically Stable | Cars, Health |
Polystyrene | Firm, Clear | Wrapping, Gadgets |
Polycarbonate | Impact Resistant | Eyes, Electronics |
Nylon | Strong, Durable | Machines, Cars |
Facing Challenges with Material Choice
Choosing the right material means looking at what the product needs, the work environment and the material’s physical and chemical traits. High injection temperatures could damage some materials, calling for careful planning of process conditions.
With rising interest in eco-friendly products, biodegradable plastics are becoming options. They fit the global green trend but might be tricky for stable processing and long-lasting performance.
Learning these elements helps producers adjust their methods to each material’s needs, leading to smooth production and high-quality products. Discover how each material affects design and making choices by investigating material selection strategies7 for injection molding.
Polypropylene is used in automotive and medical industries.True
Polypropylene resists heat well and stays stable with chemicals, fitting many uses.
Polystyrene has excellent impact resistance for electronics.False
Polystyrene is stiff with very clear appearance but does not have strong impact resistance.
Why is Polypropylene Popular in Injection Molding?
Polypropylene, a flexible plastic, leads injection molding due to its special mix of low cost, strength and flexibility.
Polypropylene’s popularity in injection molding stems from its low cost, lightweight nature, chemical stability, and heat resistance, making it ideal for automotive, medical, and household applications.
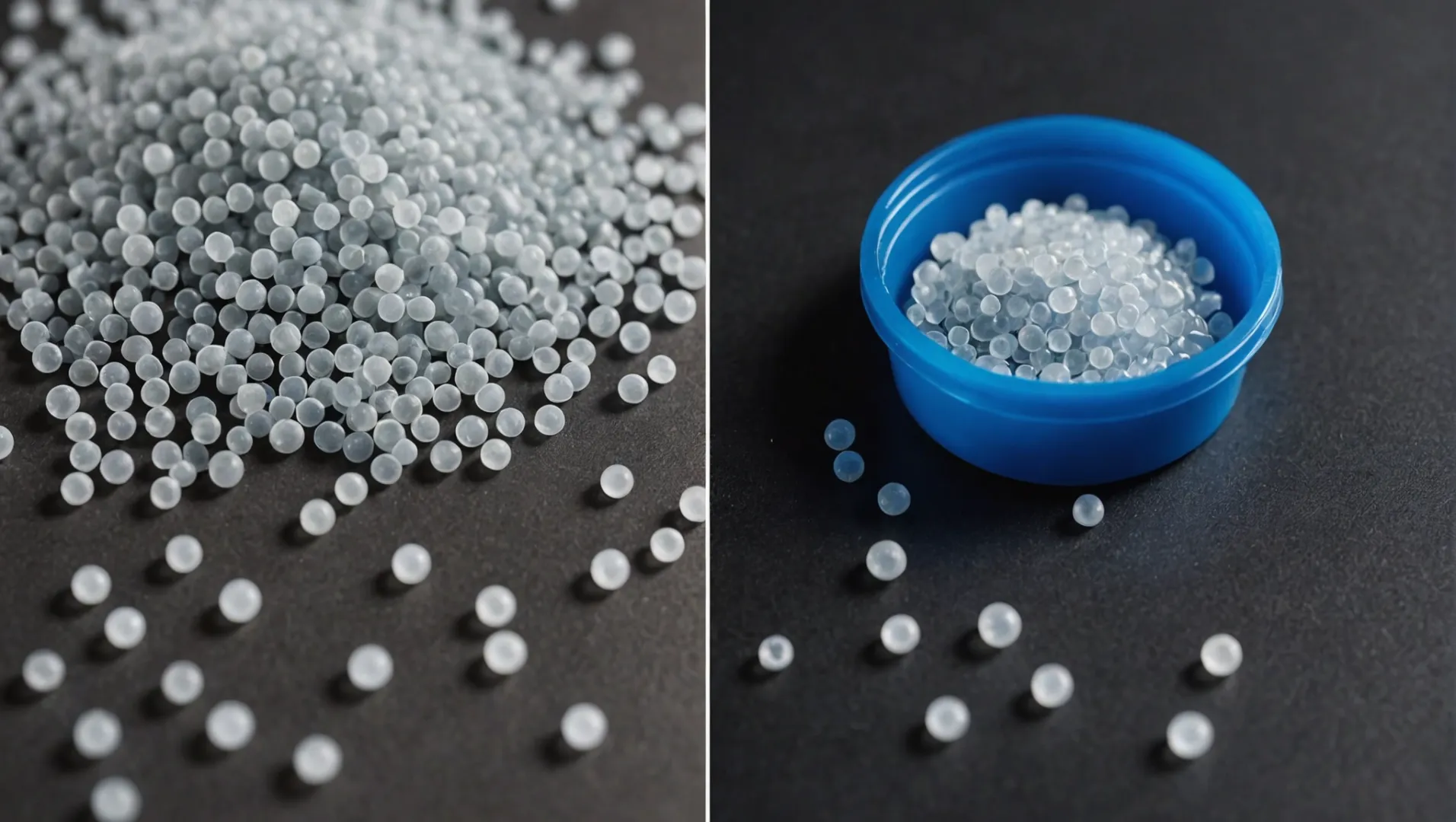
The Many Features of Polypropylene
Polypropylene (PP) is special among materials used in injection molding8 because of its unique traits. It is cheap and not heavy, offering a budget-friendly choice for producers without harming quality. Also, PP has great stability against chemicals and heat, useful for things facing different weather conditions.
Regarding processing, polypropylene flows and molds easily. This allows it to fit well with methods like blow molding and film extrusion. Its flexibility simplifies production and improves manufacturing speed.
Uses of Polypropylene in Industry
Polypropylene is used in many industries through injection molding:
-
Automotive: PP helps in making parts both inside and outside cars because of its low smell and style adaptability, including bumpers and shiny appliance covers.
-
Medical: In health sectors, its chemical stability suits it for items like syringes and nursing pads that are thrown away after use.
-
Household: For home use, it’s found in items like water pipes and waterproof layers due to its resistance to moisture.
Why Manufacturers Choose Polypropylene
Producers choose polypropylene for its strong mechanical features and its capability to keep up under different processing conditions. It supports quick production and delivers steady quality, making it dependable for creating a lot of products.
Moreover, because polypropylene can be recycled, it meets the increasing need for eco-friendly materials. As industries go green, PP allows them to stay on that path while keeping product quality.
Finally, the broad use of polypropylene in injection molding shows its useful qualities that meet many industry needs. Its affordability and strong mechanical properties make it a top choice for producers.
Polypropylene is lightweight and cost-effective.True
Polypropylene provides an inexpensive and light choice for producers.
Polypropylene is not used in medical applications.False
Polypropylene stays stable, so it suits medical products very well.
What Challenges Do Unsuitable Materials Present in Injection Molding?
Avoiding the problems of using wrong materials in injection molding saves time, money and effort.
Unsuitable materials in injection molding, like PTFE, pose challenges such as high melting points, poor flowability, and dimensional instability. These factors complicate processing, increase production costs, and limit design flexibility.
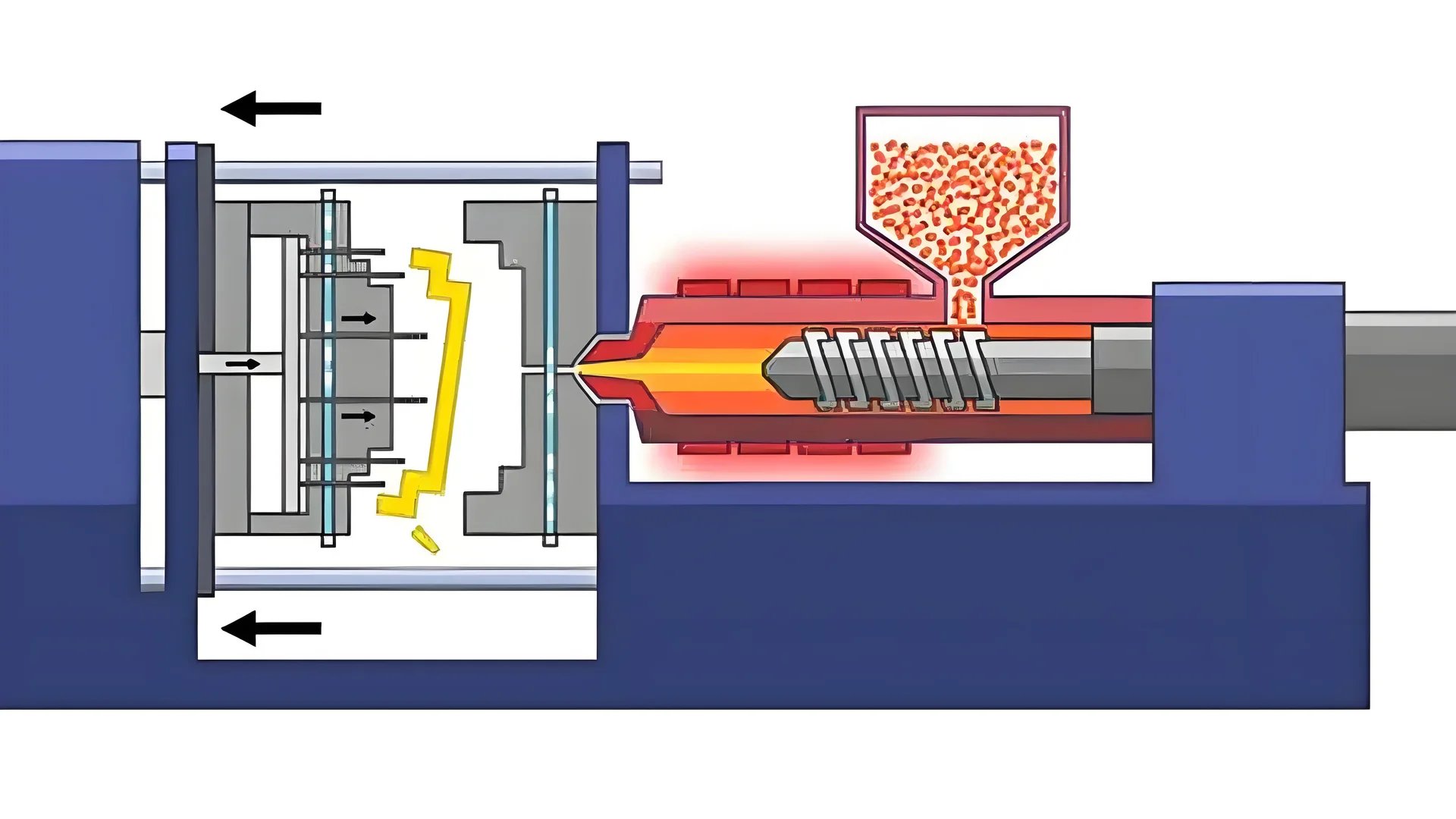
High Melting Points: A Challenge to Efficiency
Materials such as PTFE9 have a high melting point, needing special tools able to handle very high temperatures. This not only complicates the molding process but also increases energy usage and running costs.
Material | Approx. Melting Point (°C) |
---|---|
PTFE | 327 |
PP | 160 |
Using materials with high melting points may also lead to longer cycle times and more wear on equipment.
Poor Flowability: Complicating the Molding Process
Good flowability is vital for detailed designs and filling molds fully. Materials like PTFE have poor flowability10, which leads to incomplete fillings, surface flaws, and more rejected parts.
This problem often means extra processing steps or other manufacturing methods, which increase production expenses.
Dimensional Instability: Uncertain Results
Materials with dimensional instability cause irregularities in product sizes, affecting quality. PTFE‘s dimensional instability11 from its high linear expansion can cause products to warp or not fit their intended uses.
Material | Dimensional Stability Rating |
---|---|
PTFE | Low |
PC | High |
This uncertainty requires extra quality checks, which are both time-heavy and expensive.
Environmental and Economic Effects
Picking wrong materials not only affects production but also has broader environmental and economic effects. For example, inefficient material use leads to higher waste and resource use. Also, the need for special tools or other processes greatly raises production expenses, affecting profitability.
Solutions and Alternatives
Understanding these problems highlights the need to choose good materials for injection molding. Picking materials like polypropylene or polycarbonate can solve many of these issues. Each material has certain properties fitting specific production needs, like chemical stability12 and impact resistance.
By aligning material properties with project requirements, manufacturers can refine their processes, improve product quality, and cut costs.
PTFE has a high melting point of 327°C.True
PTFE's high melting temperature complicates injection molding and needs special equipment.
Poor flowability of PTFE leads to fewer defects.False
PTFE has bad flow and this leads to incomplete fills and surface problems, raising rejection levels.
Conclusion
Select materials such as PP or PC for good injection molding items. Think about the environment. Do not use PTFE because it is not suitable. Keep updated to improve your designs.
-
Explore how polypropylene’s heat resistance suits various applications.: Children’s toys; Sporting goods; Caps; Closures; Automotive applications; Food trays; Cups and to-go containers; Household goods and appliances like dishwashers. ↩
-
Understand the challenges PTFE presents in molding processes.: The main reasons why PTFE polytetrafluoroethylene cannot be injection molded include its high melting point, large melt viscosity, and the shape … ↩
-
Learn how polycarbonate excels in high-impact environments.: Machine grade polycarbonate has high impact strength, high modulus of elasticity, outstanding dimensional stability, and good electrical properties. Glass- … ↩
-
Discover nylon’s strength and wear resistance benefits.: As this data shows, nylon has excellent tensile and flexural strength. Nylon is also inherently hygroscopic and, as such, must be dried … ↩
-
Find out why polystyrene is preferred for chemical exposure.: Continuous exposure to the substance does not cause damage within 30 days. The plastic may remain resistant for years. Continuous exposure to the substance … ↩
-
See how ABS offers easy processing for complex designs.: ABS injection molding requires less energy because of its relatively low processing temperature, which reduces cycle times and overall costs … ↩
-
Learn to choose the best material for your injection molding projects.: Learn how to select the right material for your injection molding design with this technical overview of thermoplastic resins. ↩
-
Explore how polypropylene’s attributes enhance injection molding efficiency.: Importance of use of polypropylene for injection molding · Its low melt viscosity enables it to have a smooth, flowing consistency. · Its extremely slimy surface … ↩
-
Explore why PTFE’s high melting point complicates processing.: There are certain problems that must be addressed for fluoropolymer injection molding, including high melt temperature, high melt viscosity, high shear … ↩
-
Learn how poor flowability impacts PTFE molding.: There are certain problems that must be addressed for fluoropolymer injection molding, including high melt temperature, high melt viscosity, high shear … ↩
-
Discover the effects of dimensional instability in PTFE.: Parting off large dia PTFE can cause big problems with the heat generated by the tool rubbing on the sides causing distortion. You must log … ↩
-
Understand why polypropylene’s chemical stability is beneficial.: The mold should be kept below 80°C for optimal results, and after injection, the part should cool to 54°C before ejection to prevent warping. ↩