Have you ever thought about how mold designers get such a perfect finish on plastic parts? These experts really focus on details. Precise techniques help them shape plastic smoothly. Every step matters. Designers choose high-quality materials that probably improve the end result. Skilled hands carefully refine every surface to create clean lines. Each adjustment makes a big difference. This commitment to quality leads to beautiful plastic parts.
The latent gate design enhances mold efficiency and aesthetics by enabling easy part release and minimal gate traces with a discreet feeder on the mold’s parting surface.
I remember the first time I saw the submerged gate idea. It felt like finding a secret ingredient in cooking. This design is clever. It hides the feeder, putting it diagonally into the cavity. The end result? Molded parts look smoother and very polished. No visible gate marks appear.
Another feature I found amazing was the automatic mold release. Imagine the mold opening and the part separating by itself. It looks like magic. A small connection at the gate’s inlet allows clean separation with little effort.
Now, let’s discuss efficiency. Submerged gates are ideal for automated production. They control sprue speed and prevent defects. The quality stays high. These gates adjust perfectly to fast manufacturing. Maybe it’s like an invisible helper handling all crucial tasks secretly.
Submerged gates reduce gate traces in molded parts.True
Submerged gates are designed to minimize visible gate traces.
Submerged gates complicate the mold release process.False
They actually enable automatic mold release, simplifying the process.
What Are the Key Benefits of Using Submerged Gates?
Do you ever wonder how to get a perfect mold design finish without any stress?
Submerged gates change mold design in big ways. They improve how things look by reducing gate marks. Gates help release molds automatically and easily. Sprue speed becomes more precise. These features create efficiency in manufacturing. Production becomes visually appealing and more streamlined.
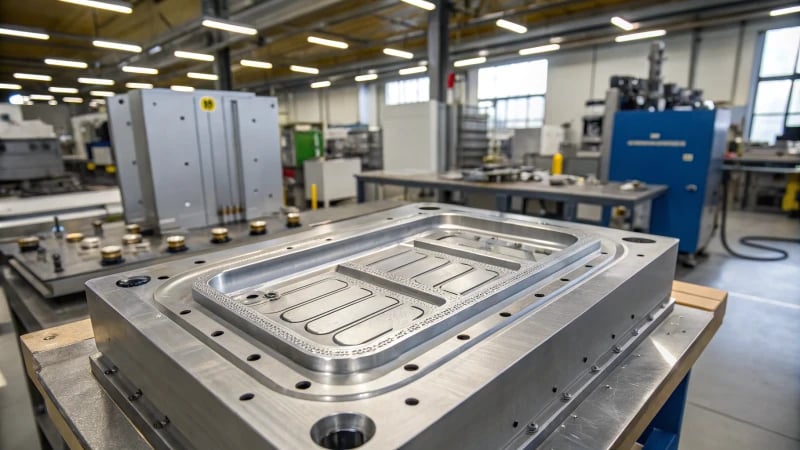
Improved Appearance
I remember seeing a perfectly shaped plastic piece for the first time. It felt like looking at a small piece of art. A lack of visible gate marks changes everything, especially where looks are crucial1. Hidden feeding positions, thanks to submerged gates, let designers focus on creating items that look and work great. In consumer electronics, where every detail really matters, this changes everything.
Automatic Part Release
Have you ever seen a molded part release smoothly? It’s almost magical. First using submerged gates, I felt amazed at how easily parts came away from the gates. This feature makes processes faster and simpler. It feels like having extra hands that never get tired, which supports automated systems2 very well.
Control Over Sprue Speed
Mold design often feels like walking a tightrope. Submerged gates provide good balance by allowing careful control over sprue speed. This reduces defects that might damage the quality of molded parts. Imagine setting things in motion and watching them align perfectly. It’s really satisfying. Best practices in mold design prevent defects3 and use submerged gates.
Benefit | Description |
---|---|
Aesthetic Improvement | Reduces visible gate marks on molded parts, enhancing overall appearance. |
Automatic Demolding | Facilitates automatic release, supporting efficient production workflows. |
Sprue Speed Management | Enables control over flow speed, preventing defects in the molding process. |
Adaptation to Automation
In today’s fast world, switching to automated production is critical. Submerged gates slip right into this approach by offering automatic part release. This improves production efficiency4 greatly. I’ve seen how this technology can change production lines: labor costs drop while turnaround times improve. Designers like me value this innovation immensely as it helps us create both beautiful and useful products.
These important advantages make submerged gates crucial in modern mold design. Learning about their unique features helps designers like Jacky choose wisely, improving both the function and look of their products.
Submerged gates improve the aesthetic quality of molded parts.True
They hide feeding positions, minimizing visible gate marks.
Submerged gates hinder automatic mold release in production.False
They facilitate automatic release, enhancing production efficiency.
How Do Submerged Gates Improve Appearance Quality?
Have you ever thought about how a small change in injection molding could greatly improve how a product looks? Let me guide you through the amazing world of submerged gates and their special effect!
Submerged gates improve the look by feeding plastic into hidden parts of the mold. These gates help reduce visible gate marks. They allow for automatic mold release. This results in a sleeker finish.
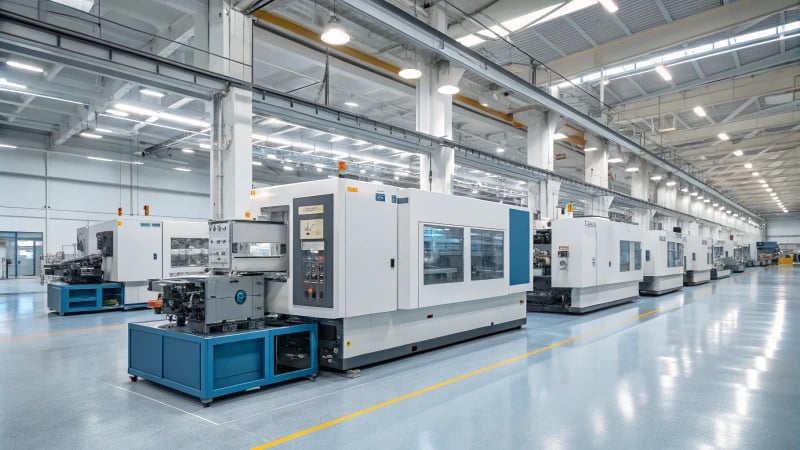
Key Benefits of Submerged Gates
I have spent years exploring the details of mold design. Submerged gates really transform how things work. Picture working on a sleek gadget, similar to the ones crafted by Jacky, a designer in Canada. These gates hide the feeder under the parting surface. This clever trick is like a hidden seam in your favorite shirt. It is unseen but will make a big difference.
-
Feeding Position: Submerged gates enter the cavity at an angle from below. This method probably reduces ugly gate marks, enhancing the surface finish5. It is like sneaking a treat without leaving crumbs. Every finish looks clean and polished.
-
Automatic Mold Release: Imagine opening the mold and seeing the piece come out like toast from a toaster! The small connection between the gate and the part really allows this smooth release, reducing labor and ensuring a cleaner appearance.
-
Trace Reduction: Minimal inlets and smart placements act like perfect makeup. They are just enough to impress but not overwhelm, which is crucial for products with high aesthetic demands.
Enhanced Control and Adaptability
-
Sprue Speed Control: Submerged gates control sprue speed, much like managing rush hour traffic. Smaller inlets prevent defects from fast injection speeds, contributing to smoother surfaces and better visual quality6.
-
Automation-Friendly: Their design suits automation perfectly. Production lines love this consistency and precision as hands-free demolding feels very efficient.
Feature | Benefit |
---|---|
Hidden Feeding | Minimized visible defects |
Small Inlet Size | Controlled injection speed |
Automatic Release | Suits automated production |
Practical Implications for Designers
Designers like Jacky find submerged gates very important when working on consumer electronics that require both utility and good looks. By implementing this technology into molds, they can meet those needs more efficiently, achieving a rare mix of function and beauty.
Exploring further on injection molding techniques7 can provide additional insights into optimizing designs for better visual outcomes. Understanding these methods can elevate your work so each piece becomes a masterpiece, not just another product.
In design, hidden details often make a big difference.
Submerged gates reduce visible gate marks.True
The hidden placement of submerged gates minimizes visible gate marks.
Submerged gates require manual demolding.False
Submerged gates allow automatic detachment, eliminating manual demolding.
Why Are Submerged Gates Ideal for Automated Production?
Have you ever wondered why some factories work better than others? Hidden gates might be the secret. These gates often help in making automated production smooth and precise.
Submerged gates are perfect for automated production. They allow the mold to open automatically. Gate traces appear less. Sprue speed becomes controlled. Efficiency gets really high. The appearance quality improves a lot. Manufacturing benefits greatly.
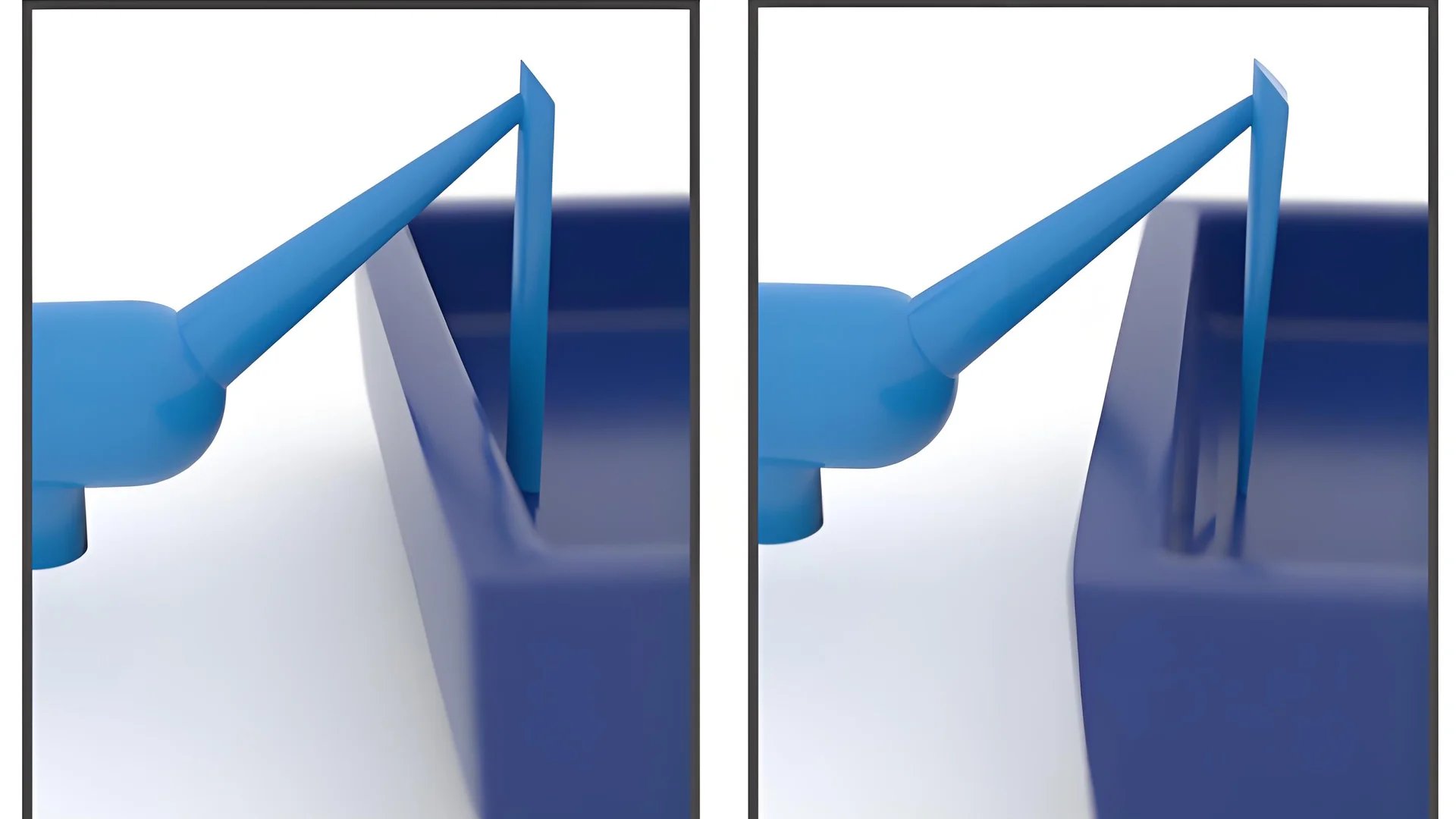
Design Principles of Submerged Gates
I remember my first meeting with submerged gates during a factory tour. Watching these engineering marvels at work felt like seeing a carefully practiced dance. Submerged gates are a precise type of point gates. Their feeder cleverly positions itself on the mold’s parting surface, diving diagonally into the cavity. This smart placement keeps the gate hidden from view, preserving the appearance quality8 of the molded part.
Automatic Mold Release
Once, while working on a project with tight deadlines, I saw the magic of automatic mold release. With submerged gates, as soon as the mold opens, the molded part gently separates from the gate with very little force. This smooth transition is a real help for automated production9, ensuring everything stays on track without any problems.
Reducing Gate Traces
Imagine showing a product where every detail matters. Submerged gates make this possible by reducing visible marks. The smaller inlet and hidden position significantly improve aesthetics, which is perfect for industries where appearance quality is crucial.
Feature | Benefit |
---|---|
Concealed Gate | Enhanced aesthetic quality |
Smaller Inlet | Controlled sprue speed |
Automatic Mold Release | Streamlined production processes |
Control of Sprue Speed
I’ve learned that controlling sprue speed is key in avoiding flaws. Thanks to their smaller inlets, submerged gates manage this easily. Molded parts remain without defects and in very good condition.
Adaptation to Automation
Efficiency is vital in automated production. Submerged gates excel by allowing automatic demolding, syncing perfectly with high-volume manufacturing needs. This adaptability makes them a favorite for industries focused on mass production10.
By embracing these aspects, manufacturers can refine their processes and maintain high standards of quality and efficiency across their production lines. Discover more about how submerged gates transform production lines by exploring more about plastic component manufacturing11 and its harmony with automation technologies.
Submerged gates reduce visible gate traces on parts.True
Their design hides the gate, enhancing the part's appearance.
Submerged gates increase sprue speed in production.False
They control sprue speed with smaller inlets, avoiding defects.
How Does Sprue Speed Influence Submerged Gate Design?
Do you sometimes think about how something as small as sprue speed might really change the quality of your molded parts?
Sprue speed in submerged gate design is crucial for controlling flow rates. It lowers defects and raises the quality of molded parts. This speed allows optimal filling. It does not compromise appearances.
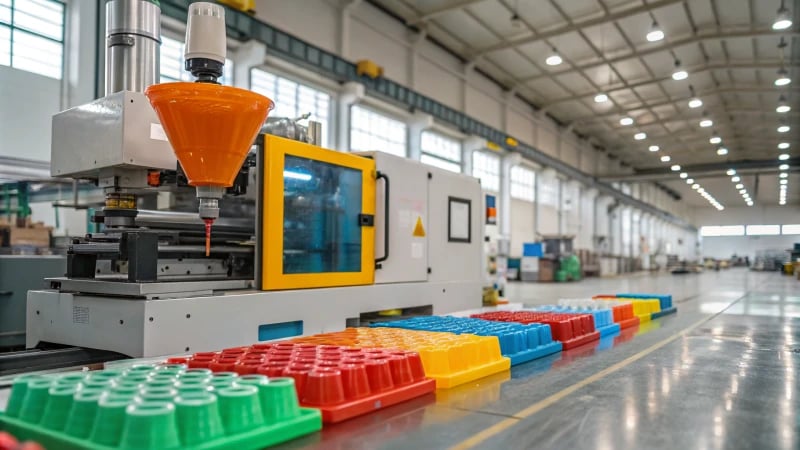
Understanding Sprue Speed
At first, I didn’t realize how important sprue speed was when working with molds. I underestimated it. Only after seeing how it stopped problems like air bubbles and warping did I understand its value. Sprue speed is the speed at which hot material moves through the sprue to fill the cavity. Getting the speed right is very important. If it’s too quick, defects like trapped air might appear. If it’s too slow, parts may not form completely.
Sprue speed refers to the velocity at which molten material travels through the sprue, ultimately reaching the cavity through the submerged gate. This speed is critical in determining the filling efficiency12 of the mold.
Impact on Molded Part Quality
When I started designing molds, I had issues with gate marks spoiling our products’ looks. That’s when I discovered submerged gate design. This design feeds the material under the parting line. It reduces gate marks and improves the look of consumer electronics components. Looks are really as important as how well the product works.
By carefully controlling the sprue speed, designers can ensure that molten material fills the cavity smoothly, thus enhancing appearance quality of final products.
Factor | Impact on Design |
---|---|
Sprue Speed | Controls flow rates, reduces defects |
Submerged Gate | Minimizes gate traces, supports automated mold release |
Automatic Mold Release
I really enjoy how submerged gates help with automatic mold release. This clever design lets parts separate from the gate automatically when the mold opens. But this relies greatly on correct sprue speed management. If the speed is wrong, it affects tension force necessary for smooth release.
Submerged gates facilitate automatic demolding due to their design where gates detach automatically when molds open.
Adaptation to Automated Production
In our factory, automated production13 is absolutely necessary—not just a trend. Submerged gates’ ability to control sprue speed is crucial; it helps with seamless demolding without manual help.
Proper speed balance is critical; it improves both productivity and quality of each part.
Feeding Position
Smart placement of entry in submerged gate designs keeps looks good while maintaining strength.
Sprue speed control feels like mixing art with science; it results in molded products excellent in both appearance and function.
By using this knowledge, I’ve taken my designs and manufacturing processes14 to new levels.
Always remember how each detail affects your specific task for best results.
High sprue speed reduces air entrapment in molds.False
High sprue speed can cause air entrapment, not reduce it.
Submerged gates minimize visible gate marks on parts.True
Submerged gates feed material under the parting line, reducing marks.
Conclusion
Submerged gates enhance mold design by improving aesthetics, enabling automatic part release, controlling sprue speed, and adapting to automation, resulting in high-quality plastic components with minimal defects.
-
Explore how submerged gates enhance the appearance of molded products, vital for industries prioritizing aesthetics. ↩
-
Learn about automated systems that integrate with submerged gates for improved manufacturing efficiency. ↩
-
Find strategies to prevent common defects in mold design using controlled sprue speed. ↩
-
Discover how submerged gates contribute to increased production efficiency in automated environments. ↩
-
Explore the detailed benefits submerged gates offer to injection molding processes, particularly in enhancing aesthetic quality. ↩
-
Learn about how controlling sprue speed impacts the quality and appearance of injection molded products. ↩
-
Discover various injection molding techniques focused on improving the aesthetic quality of molded parts. ↩
-
Explore how concealed gate placement enhances product aesthetics by minimizing visible traces. ↩
-
Understand the advantages of automatic mold release in streamlining production processes. ↩
-
Learn why submerged gates are favored in high-volume manufacturing setups. ↩
-
Discover how automation integrates with plastic manufacturing for efficiency gains. ↩
-
Exploring this link provides insights into optimizing sprue speed for better filling efficiency, crucial for achieving high-quality molded parts. ↩
-
Discover how automated production enhances efficiency and quality in molding processes through this informative link. ↩
-
Learn valuable strategies to optimize manufacturing processes by exploring this link, helping designers achieve superior results. ↩