Choosing the right material for your project can feel overwhelming, especially when strength is a top priority. Let’s dive into the strongest injection molded plastics and discover which one is best for you.
When it comes to selecting the right material for your injection molded project, strength is often a top priority. Polycarbonate (PC), polyphenylene sulfide (PPS), and polyetheretherketone (PEEK) are among the strongest injection molded plastics available. Each offers unique properties such as high mechanical strength, thermal stability, and chemical resistance, making them ideal for demanding applications.
However, determining the ‘strongest’ plastic depends on your specific application needs. Understanding the features and typical uses of these materials will guide you in making an informed decision tailored to your project’s requirements.
Polycarbonate is the strongest injection molded plastic.False
PEEK is generally stronger than polycarbonate, offering higher mechanical strength.
What Factors Determine the Strength of Injection Molded Plastics?
Understanding the factors that influence the strength of injection molded plastics is crucial for optimal material selection.
The strength of injection molded plastics is determined by polymer type, molecular weight, filler materials, and processing conditions. These factors collectively influence mechanical properties such as tensile strength, impact resistance, and elasticity, which are critical for the performance of finished products.
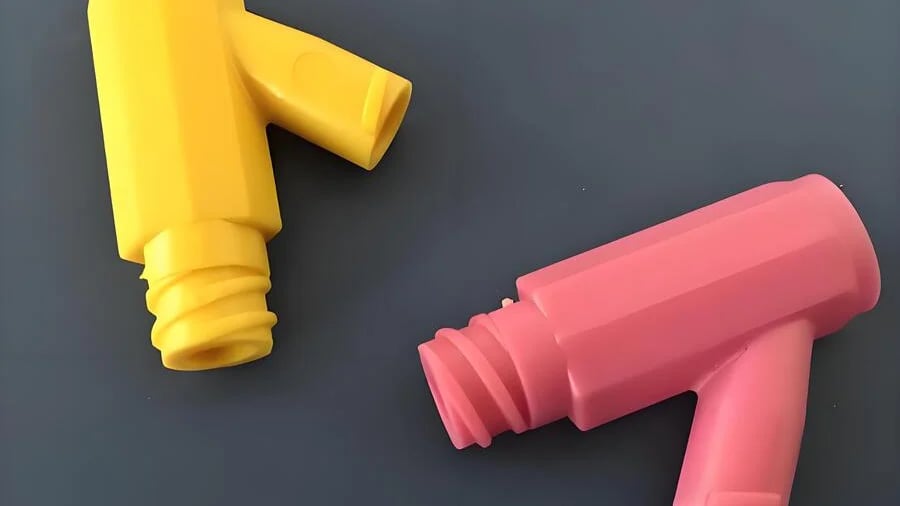
Understanding Polymer Type
The base polymer significantly impacts the strength of injection molded plastics. Materials like polycarbonate (PC), polyphenylene sulfide (PPS), and polyetheretherketone (PEEK) are known for their high strength and specific characteristics tailored for robust applications. Polycarbonate1, for instance, is renowned for its impact resistance and optical clarity, making it ideal for products requiring durability and transparency.
Role of Molecular Weight
Molecular weight affects the viscosity and mechanical properties of the plastic. Higher molecular weights typically result in greater tensile strength and impact resistance. When considering molecular weight2 for your project, balancing it with processing capabilities is essential to ensure efficient manufacturing without compromising the material’s inherent properties.
Impact of Filler Materials
Incorporating fillers can enhance certain properties of injection molded plastics. Glass fibers, carbon fibers, and mineral fillers are common additives that can increase strength and rigidity. However, they can also affect the plastic’s weight and cost. Understanding the trade-offs is crucial when selecting fillers for applications where maximum strength is required.
Filler Type | Effect on Strength | Common Applications |
---|---|---|
Glass Fibers | Increased rigidity | Automotive parts, electronics |
Carbon Fibers | High tensile strength | Aerospace components |
Mineral Fillers | Enhanced stability | Construction materials |
Processing Conditions
The method of processing significantly influences the final strength of the product. Factors such as temperature, pressure, and cooling rate need careful optimization. High temperatures can degrade polymers, while improper cooling can lead to internal stresses, affecting mechanical performance. Exploring optimal processing conditions3 can lead to improved product consistency and strength.
These aspects are foundational in determining which type of injection molded plastic will suit your project’s needs best. By evaluating these factors comprehensively, manufacturers can select materials that not only meet but exceed performance expectations in their specific application scenarios.
Polycarbonate is known for its high impact resistance.True
Polycarbonate's molecular structure provides excellent impact resistance, ideal for durable products.
Higher molecular weight decreases tensile strength.False
Higher molecular weight generally increases tensile strength due to stronger polymer chains.
How Do Processing Conditions Affect Plastic Strength?
Discover how the conditions under which plastics are processed can influence their ultimate strength and performance.
Processing conditions such as temperature, pressure, and cooling rates significantly impact the strength of plastics by affecting molecular orientation and crystallinity. Optimal settings ensure enhanced mechanical properties and durability.

Understanding Molecular Orientation
The molecular orientation of plastics during processing is a critical factor that influences strength. When plastics like polycarbonate4 are stretched under heat, their polymer chains align more closely, enhancing tensile strength. This process is known as orientation, and it significantly affects the final product’s mechanical properties.
- Example: In film blowing, a controlled temperature and stretching process ensures the plastic film has uniform strength across its surface.
The Role of Temperature and Pressure
Temperature and pressure are pivotal in determining a plastic’s strength during molding. Elevated temperatures can increase a material’s flow, allowing for better filling of molds and improved adhesion between layers. However, excessive heat can degrade some plastics, reducing their strength.
- Polyphenylene sulfide (PPS) benefits from precise temperature control to maintain its high mechanical strength and chemical resistance during processing.
Pressure, on the other hand, ensures that the molten plastic fills every part of the mold, reducing voids that could compromise strength. High-pressure conditions help in achieving better surface finishes and structural integrity.
Cooling Rates and Crystallinity
Cooling rates significantly impact the crystallinity of semi-crystalline plastics like polyetheretherketone (PEEK)5. Fast cooling might trap amorphous structures, while slower rates allow for better crystalline structure formation, which enhances strength and thermal stability.
Cooling Rate | Effect on Crystallinity |
---|---|
Fast | Lower crystallinity, less strength |
Slow | Higher crystallinity, more strength |
- Case Study: Adjusting the cooling rate during PEEK processing can optimize its mechanical properties for aerospace applications.
Impact of Additives and Fillers
Additives and fillers are often introduced during processing to enhance plastic strength. For instance, glass fibers can be added to improve tensile strength and rigidity in applications requiring robust materials.
- Insight: The choice of filler must be compatible with processing conditions to avoid compromising the plastic’s inherent properties.
Understanding these factors is crucial for manufacturers aiming to tailor plastic properties to specific application needs. By adjusting processing parameters like temperature, pressure, and cooling rates, manufacturers can significantly enhance the material’s performance for diverse uses in industries ranging from automotive to electronics.
High cooling rates increase plastic crystallinity.False
Fast cooling leads to lower crystallinity, decreasing strength.
Pressure ensures complete mold filling in plastic processing.True
Pressure reduces voids, enhancing surface finish and integrity.
What Are the Cost Implications of Using High-Strength Plastics?
Exploring the financial aspects of high-strength plastics can inform better material choices for projects.
High-strength plastics like polycarbonate (PC), polyphenylene sulfide (PPS), and polyetheretherketone (PEEK) come with higher initial costs. However, their durability, efficiency in demanding applications, and potential for reduced maintenance may offset these expenses over time.
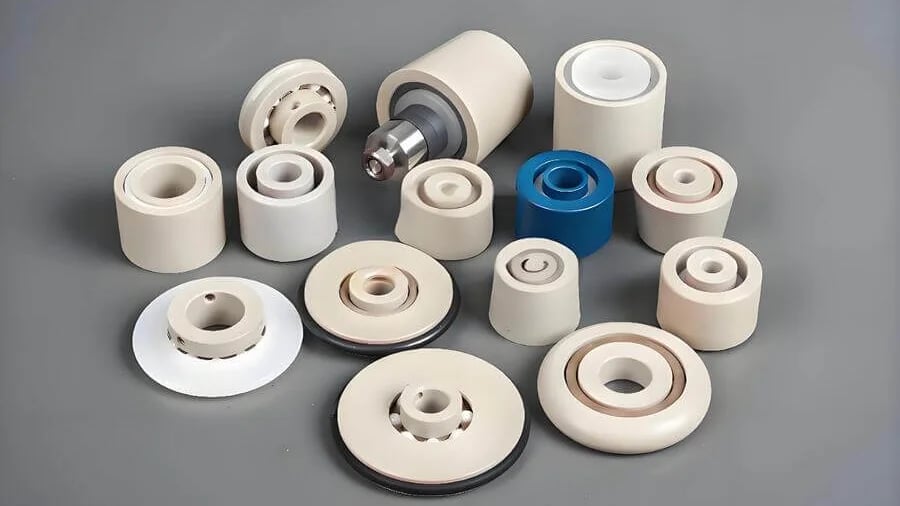
The Price Tag of High-Strength Plastics
When considering high-strength plastics such as polycarbonate (PC)6, polyphenylene sulfide (PPS), and polyetheretherketone (PEEK), the initial cost can be a significant factor. These materials are generally more expensive than standard plastics due to their advanced mechanical properties and specialized manufacturing processes.
Plastic Type | Average Cost per Pound |
---|---|
PC | $2.50 – $3.00 |
PPS | $5.00 – $6.00 |
PEEK | $60.00 – $70.00 |
Long-Term Savings and Benefits
Despite the higher upfront costs, using these materials can lead to long-term savings:
- Durability and Lifespan: High-strength plastics often require fewer replacements, reducing costs over the life of the product.
- Reduced Maintenance: For example, PEEK‘s excellent wear resistance and self-lubrication may lower maintenance expenses in automotive or aerospace applications.
Industry-Specific Considerations
-
Automotive Industry:
- In applications such as under-the-hood components, PPS offers remarkable thermal stability and chemical resistance, which can reduce vehicle weight and improve fuel efficiency, potentially leading to cost savings.
-
Medical Field:
- PEEK’s biocompatibility makes it ideal for implants, where its longevity and resilience justify the higher price in medical applications.
Balancing Cost with Performance
While these high-strength plastics entail higher initial investments, they should be viewed as strategic assets that can enhance product performance and longevity. Weighing the upfront costs against long-term benefits is crucial for industries where reliability and durability are paramount.
Deciding on the right material requires a thorough analysis of application-specific needs. For further insights on the balance between strength and flexibility in plastics, explore Which Plastics Offer the Best Balance Between Strength and Flexibility?7.
PEEK is more expensive than PC and PPS.True
PEEK costs $60-$70 per pound, while PC and PPS are cheaper.
High-strength plastics always increase maintenance costs.False
They can reduce maintenance costs due to durability and wear resistance.
Which Plastics Offer the Best Balance Between Strength and Flexibility?
Finding the perfect plastic for your application means balancing strength with flexibility.
Polycarbonate (PC) is renowned for its blend of strength and flexibility, making it a versatile choice for various applications. It combines high impact resistance with decent elasticity, suitable for products like helmets and eyeglass lenses. Polyetheretherketone (PEEK) also offers a strong yet flexible profile, ideal for aerospace and medical devices.

Understanding the Dual Attributes: Strength and Flexibility
When selecting plastics, it’s crucial to balance strength and flexibility8. Plastics like Polycarbonate (PC) and Polyetheretherketone (PEEK) shine in this regard, offering a harmonious mix that caters to demanding environments.
Polycarbonate (PC)
PC is well-regarded for its exceptional impact strength and reasonable elasticity. This combination makes it an excellent choice for products that need to absorb shock while maintaining their form. For example, PC is often used in safety equipment like helmets and protective eyewear due to its ability to withstand force without shattering.
- Impact Strength: Withstands high-impact situations while retaining shape.
- Elasticity: Provides the necessary flexibility for repeated use without deformation.
Property | Polycarbonate (PC) |
---|---|
Impact Strength | High |
Flexibility | Moderate |
Applications | Helmets, lenses |
Polyetheretherketone (PEEK)
PEEK is another plastic that adeptly balances strength with flexibility. Known for its rigidity, it can also flex under stress, making it suitable for highly technical fields such as aerospace and medicine. Its excellent fatigue resistance ensures durability even under continual strain.
- Mechanical Rigidity: Offers solid structural support.
- Flexibility in Application: Can be used in dynamic environments without compromising integrity.
Property | Polyetheretherketone (PEEK) |
---|---|
Impact Strength | High |
Flexibility | Moderate |
Applications | Aerospace, medical devices |
Factors Influencing Flexibility
Both PC and PEEK owe their adaptability to their molecular structures and processing conditions. Adjusting these factors can further tailor the properties of these plastics to specific applications. While PC‘s transparency adds an extra layer of versatility, PEEK‘s resistance to wear enhances its functional life span.
By evaluating these materials’ performance in real-world applications, engineers and designers can choose the ideal plastic that strikes the perfect balance between strength and flexibility for their unique needs.
Polycarbonate is used in protective eyewear.True
Polycarbonate's high impact strength and moderate flexibility make it ideal for eyewear.
PEEK is unsuitable for aerospace applications.False
PEEK's strength and flexibility make it ideal for aerospace use.
Conclusion
In summary, polycarbonate, PPS, and PEEK each offer unique strengths suited for various applications. Reflect on your specific needs and project conditions to select the best material.
-
Explore why polycarbonate is favored for its impact resistance and clarity.: The Advantages and Disadvantages of Polycarbonate Injection Molding · 1. Quicker Cycle Time · 2. Aids in Producing Parts with Precise Tolerances. ↩
-
Learn how molecular weight influences plastic’s mechanical properties.: How does Molecular weight affect a material’s properties? · A High molecular weight increases how far the material can stretch before rupturing. ↩
-
Discover how processing conditions impact plastic strength and performance.: 1. Temperature Control: · 2. Injection Speed: · 3. Cooling Time: · 4. Plastic Material Selection: · 5. Screw Speed and Back Pressure: · 6. Injection … ↩
-
Learn about polycarbonate’s enhanced tensile strength through molecular orientation.: A simple way to determine the molecular orientation in an injection-molded product is to measure three mutually independent components of … ↩
-
Explore how cooling rates affect PEEK’s strength and thermal stability.: For both the neat PEEK resin and carbon fibre/PEEK composites, the degree of crystallinity decreased as the cooling rate increased (Fig. 4). It is well known … ↩
-
Compare costs of various high-strength plastics for informed decisions.: PEEK. PPS. PAI. PI. HDPE. PP. PVC. Cost Comparison. (USD). +. Phone (952) 933-0993. Fax (952) 935-5380 info@precisionpunch.com www.precisionpunch.com. 21. 27 … ↩
-
Discover options balancing strength and flexibility for diverse applications.: For example, polyethylene (PE) and polypropylene (PP) are known for their flexibility. On the other hand, polystyrene (PS) and polycarbonate (PC) … ↩
-
Learn how different plastics achieve strength-flexibility balance.: Overall, the balanced strength, flexibility and hardness of POM plastic make it suitable for the most demanding mechanical and engineering … ↩