Injection molding is more than just a manufacturing process; it’s a blend of art and science. Have you ever wondered how those intricate parts we use daily are made? Let’s explore the essential steps together!
To create high-quality injection molded parts, start by selecting high-quality raw materials, designing precise molds, optimizing the injection molding parameters, conducting thorough post-processing, and implementing stringent quality control measures.
Understanding these key steps is vital, but there’s so much more to uncover. Let’s dive deeper into each stage, revealing insights that can enhance your production efficiency and outcomes.
High-quality resin is crucial for injection molding.True
High-quality resin ensures durability and performance in molded parts.
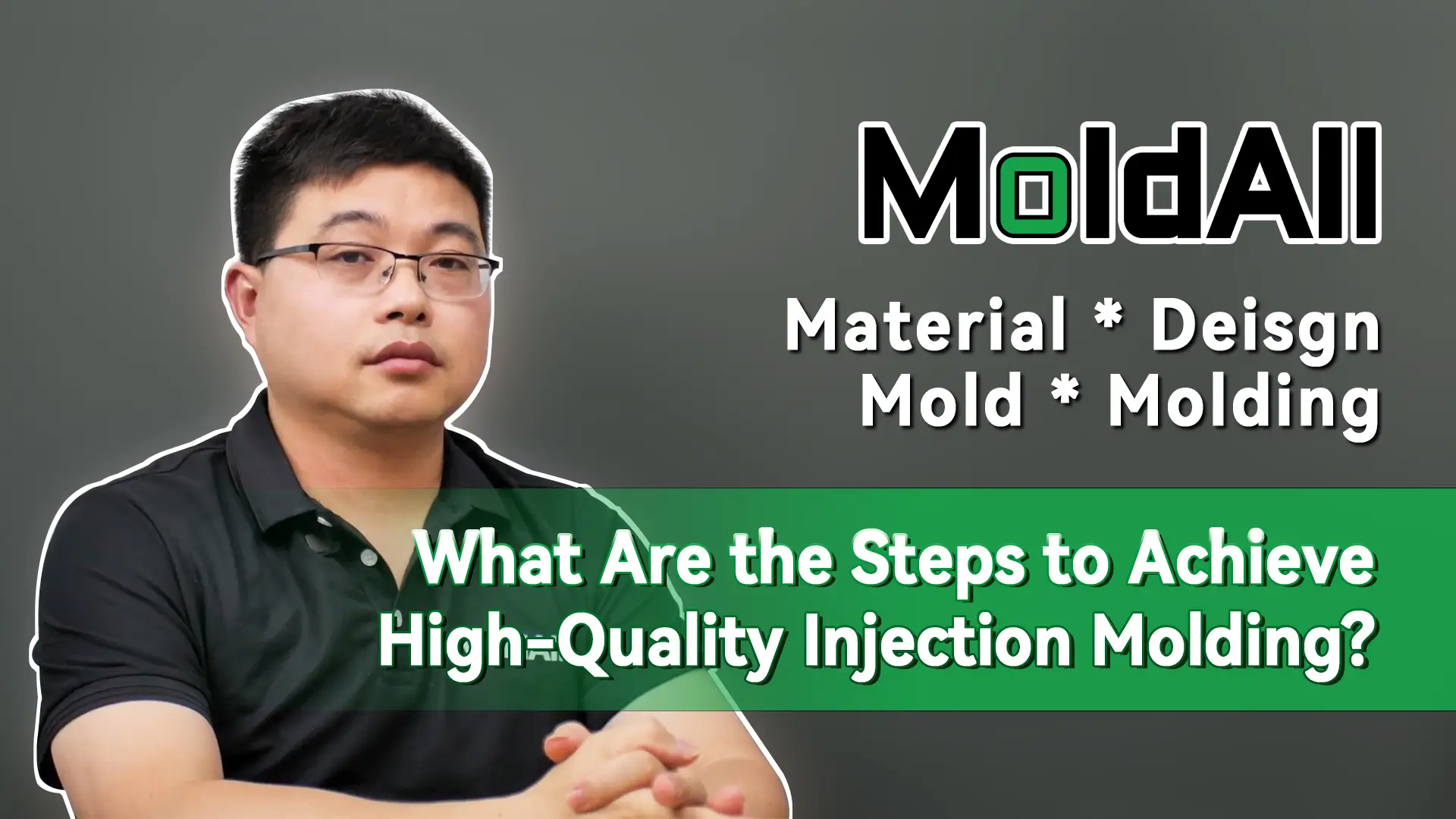
How Do You Choose the Right Raw Materials for Injection Molding?
Choosing the right raw materials is the first critical step in ensuring the quality of injection molded parts. How do you make the best choice?
Select high-quality resin based on part requirements, ensure purity and stability, and add appropriate additives for enhanced performance.
Selecting High-Quality Resin
Choosing the right resin is pivotal in the injection molding process1. The resin should align with the specific functional requirements of the part being produced. For parts demanding high strength, high-performance engineering plastics are ideal. Meanwhile, for items where appearance is critical, resins with excellent fluidity and uniform color are preferable. Ensuring resin purity and stability by avoiding impurities or moisture is vital.
Adding Appropriate Additives
To enhance performance, selecting the right additives is crucial. Additives such as plasticizers, stabilizers, and lubricants can significantly affect the final product’s properties. The type and quantity of additives should be carefully chosen based on the resin characteristics and part requirements. This optimization ensures achieving the best effect without compromising product integrity.
Additives Table
Additive Type | Function | Considerations |
---|---|---|
Plasticizers | Increase flexibility | Must match with resin compatibility |
Stabilizers | Enhance heat and light resistance | Choose based on environmental exposure |
Lubricants | Improve processing flow and reduce friction | Avoid excessive use to prevent degradation |
Understanding these aspects of raw material selection will pave the way for producing robust, reliable, and aesthetically pleasing injection molded parts. For those interested in exploring more about resin types and their applications, delve into comprehensive resources on resin selection2.
High-performance plastics are ideal for high-strength parts.True
High-performance engineering plastics provide necessary strength for demanding parts.
Plasticizers decrease the flexibility of injection molded parts.False
Plasticizers increase flexibility by softening the resin used in molding.
What Are the Key Considerations in Mold Design and Manufacturing?
Designing and manufacturing molds for injection molding is an art and science, demanding precision and thoughtful planning. What are the essential considerations to ensure efficiency and quality?
Key considerations in mold design and manufacturing include selecting a reasonable mold structure and employing high-precision manufacturing processes. These steps ensure the mold meets design specifications, facilitates smooth operations, and produces defect-free parts.
The Importance of Mold Structure Design
A well-designed mold structure is critical to the success of the injection molding process. The structure must accommodate the shape, size, and wall thickness of the parts being produced. This includes:
-
Shape and Size Considerations: The mold must be engineered to allow for easy removal of the finished product without compromising its integrity. Complex shapes might require more intricate designs, including additional moving parts in the mold.
-
Wall Thickness Uniformity: Consistent wall thickness ensures that the part cools uniformly, reducing stress and potential warping. Thinner walls can lead to issues such as short shots, while overly thick walls may cause sink marks.
-
Gate and Runner Design: The gate should be positioned to ensure even distribution of plastic melt into the mold cavities. Runners should be minimized to reduce waste but must be sufficient to carry the melt effectively.
Incorporating these elements reduces defects like bubbles and short shots, ensuring high-quality parts.
Precision in Mold Manufacturing
The manufacturing process of molds significantly impacts the overall quality of the injection molded parts. Employing advanced technologies such as CNC machining3 and EDM machining4 can vastly improve precision. Here are some steps involved:
-
CNC Machining: This computer-controlled process ensures high dimensional accuracy and allows for complex designs that would be challenging to achieve manually.
-
EDM Machining: Particularly useful for hard materials, EDM provides precise cutting capabilities for intricate mold components.
-
Heat Treatment: Applying heat treatment increases the hardness and durability of molds, extending their life span and reducing wear over time.
By incorporating these advanced techniques, manufacturers can achieve tight tolerances and superior surface finishes, which are vital for producing high-quality injection molded parts.
Ensuring Durability and Efficiency
Beyond precision, durability is another key factor in mold design. Molds must withstand repeated cycles without degrading:
-
Surface Treatments: Techniques such as nitriding or plating enhance wear resistance and corrosion resistance.
-
Cooling Systems: Effective cooling systems are crucial for maintaining cycle times and ensuring consistent quality across batches.
These enhancements not only improve the lifespan of molds but also contribute to more efficient production cycles by reducing downtime associated with maintenance or replacements.
Ultimately, attention to detail in mold design and manufacturing underpins the success of injection molding processes, ensuring that products meet stringent quality standards and customer expectations.
Uniform wall thickness reduces warping in molded parts.True
Consistent wall thickness ensures even cooling, reducing stress.
CNC machining is not used for complex mold designs.False
CNC machining allows for high precision and complex designs.
How Can Process Control Improve Injection Molding Quality?
In injection molding, process control is the backbone of producing consistently high-quality parts. But how does it enhance the final product’s quality?
Process control improves injection molding quality by optimizing parameters like temperature, pressure, and speed, ensuring consistent part production with minimal defects.
Understanding Process Control in Injection Molding
Injection molding is a complex process that involves melting plastic pellets and injecting them into a mold to form a part. The quality of these parts is significantly influenced by how well the process is controlled. Process control5 involves the meticulous management of various parameters that define the molding process, such as temperature, pressure, speed, and cooling time.
Key Parameters in Injection Molding
-
Temperature Control
- The melting temperature of the plastic material should be carefully set according to its specific requirements. Too high a temperature can degrade the material, while too low can result in incomplete filling of the mold.
- Real-time monitoring of temperature ensures the melt remains within the optimal range to prevent defects such as warping or incomplete fillings.
-
Pressure Optimization
- Setting the right injection pressure is crucial for ensuring that the molten plastic completely fills the mold cavities without causing excessive internal stress.
- Pressure profiling throughout the injection cycle helps in maintaining dimensional accuracy and reducing issues like sink marks or voids.
-
Speed and Flow Rate
- The speed at which molten plastic is injected into the mold impacts how evenly it fills the mold. An optimal speed prevents defects like flow lines or jetting.
- Adjusting flow rates can also help in managing shear stress on the material, which can affect the strength and appearance of the final part.
Advanced Monitoring Techniques
-
Real-Time Sensor Integration
- By integrating sensors into the molding machines, manufacturers can continuously monitor critical parameters such as pressure and temperature. This allows for immediate adjustments to be made if deviations occur.
- Advanced sensors6 provide data that can be used to predict potential quality issues before they arise, ensuring consistent product output.
-
Automated Feedback Systems
- Implementing feedback loops where machines automatically adjust settings based on sensor data can enhance precision and reduce human error.
- Such systems help in maintaining optimal conditions throughout the molding process, leading to better-quality parts.
Benefits of Effective Process Control
Effective process control leads to:
- Reduced Waste: By minimizing defects, less material is scrapped, leading to cost savings and environmental benefits.
- Consistent Quality: Parts produced are uniform in dimensions and properties, meeting stringent quality standards consistently.
- Increased Efficiency: Optimal settings reduce cycle times and improve machine utilization rates, boosting overall productivity.
To sum up, implementing robust process controls7 in injection molding not only enhances part quality but also optimizes production efficiency, ensuring that manufacturers meet their performance and economic objectives.
Temperature control prevents warping defects.True
Maintaining optimal temperature avoids warping by ensuring uniform material flow.
Pressure profiling increases injection cycle time.False
Pressure profiling optimizes the cycle, preventing defects without increasing time.
Why Is Post-Processing Important in Injection Molding?
Post-processing in injection molding is crucial for refining the appearance and enhancing the functionality of molded parts. But why exactly is it so essential?
Post-processing is vital in injection molding to improve product aesthetics, ensure dimensional accuracy, and enhance surface properties. It involves removing flash, treating surfaces, and making necessary adjustments to meet quality standards, ultimately enhancing the final product’s performance and longevity.
The Role of Post-Processing in Enhancing Quality
Post-processing serves as the final touch in the injection molding process8, ensuring the molded parts meet high standards of quality and functionality. This phase involves several critical steps:
-
Flash Removal: Flash refers to the excess material that can form at the edges of parts during molding. Removing this is crucial to improve both the appearance and functionality of the product. Techniques can include mechanical trimming or manual removal, each selected based on the product’s complexity and material.
-
Surface Treatment: Surface treatments, such as spraying or electroplating9, can significantly enhance a part’s appearance and durability. These treatments are tailored to the product’s end-use requirements, often improving resistance to corrosion and wear.
Improving Dimensional Accuracy and Consistency
During post-processing, parts are measured against strict dimensional standards. This ensures they fit precisely with other components or assemblies, a necessity in industries like automotive or aerospace where precision is paramount.
- Calibration Adjustments: Adjustments might be necessary if parts deviate from required dimensions. This could involve minor modifications or reworking of parts to align with design specifications.
Quality Assurance and Process Traceability
Post-processing includes thorough inspection and quality assurance measures. By implementing a robust quality management system10, manufacturers can ensure every part meets established quality criteria before shipping.
- Traceability Systems: These systems track each part through production, enabling quick identification and rectification of any issues that arise post-production. This traceability is critical for maintaining consistent quality across batches.
Ultimately, post-processing is not just about fixing defects; it’s about elevating the product to meet both aesthetic and functional standards that customers expect.
Post-processing improves injection molded parts' aesthetics.True
Post-processing enhances the appearance of molded parts by removing defects.
Calibration adjustments are not needed in post-processing.False
Adjustments ensure parts meet dimensional accuracy and fit requirements.
Conclusion
Mastering the art of injection molding takes dedication and attention to detail. Apply these insights for improved performance and reliability in your products.
-
Explore why high-quality resin is crucial for durable parts.: Finding the right resin requires a thorough understanding of the physical properties and beneficial qualities of the available materials. To assist you in … ↩
-
Learn about different resins and their specific applications.: Common Applications for Plastic Resin Injection Molding · ABS · Celson® (Acetal) · Polypropylene · HIPS · LDPE. ↩
-
CNC machining offers precision and complexity in mold creation.: CNC machining is the leading production style for mold making. Molds are most commonly machined out of tool steel and stainless steel, but aluminum is also … ↩
-
EDM machining enables intricate cuts in tough materials.: The Ram EDM, sometimes called sinker, die sinker, or plunger uses an electrode to produce the desired shape in material via electrical current. ↩
-
Learn how process control optimizes manufacturing quality and reduces defects.: Injection molding process monitoring and process control can help you achieve several goals: improved process quality, higher-quality products and lower … ↩
-
Discover how advanced sensors enhance real-time monitoring and quality assurance.: Our sensors for the monitoring of injection molding processes includes pressure sensors (direct, indirect, contactless) and temperature sensors. ↩
-
Explore how robust process controls improve quality and efficiency.: Process control allows factory managers to closely monitor the energy efficiency levels of production processes. If the equipment is run at optimum levels … ↩
-
Explains why post-processing is crucial for final product quality.: Injection molding post-processing improves a part’s appearance, removes aesthetic flaws, and even provides additional mechanical properties … ↩
-
Details how surface treatments improve durability and aesthetics.: This process offers both practical and aesthetic benefits, resulting in products that look better, feel better, and work more effectively. ↩
-
Describes how these systems ensure consistent product quality.: A QMS is meant to operate as a framework that directs the manufacturing company in reaching quality goals, ongoing improvement, and customer satisfaction. ↩