Are you navigating the complexities of manufacturing precision with injection molded parts? Knowing the right tolerances is key.
Standard tolerances for injection molded parts are classified by China’s GB/T14486-2008 into levels MT1 to MT7, with varying precision based on size. MT1 offers the highest accuracy, while MT7 is suited for less precise applications, ensuring quality and cost-effectiveness in production.
While understanding these tolerance levels provides a foundation, choosing the right level for your project involves considering various factors such as material, design complexity, and cost implications. Delve deeper as we unpack these elements and more in our comprehensive guide.
MT1 offers the highest precision in injection molding tolerances.True
MT1 provides the smallest tolerance values, ensuring high precision.
How Do Material and Design Complexity Affect Tolerances?
Understanding how material and design intricacies impact tolerances can significantly improve product quality and efficiency.
Material properties and design complexity directly influence the achievable tolerances in injection molding. Materials with high thermal expansion or warping potential, combined with intricate designs, demand tighter control and may necessitate higher precision levels like MT1 or MT2, affecting both cost and manufacturability.
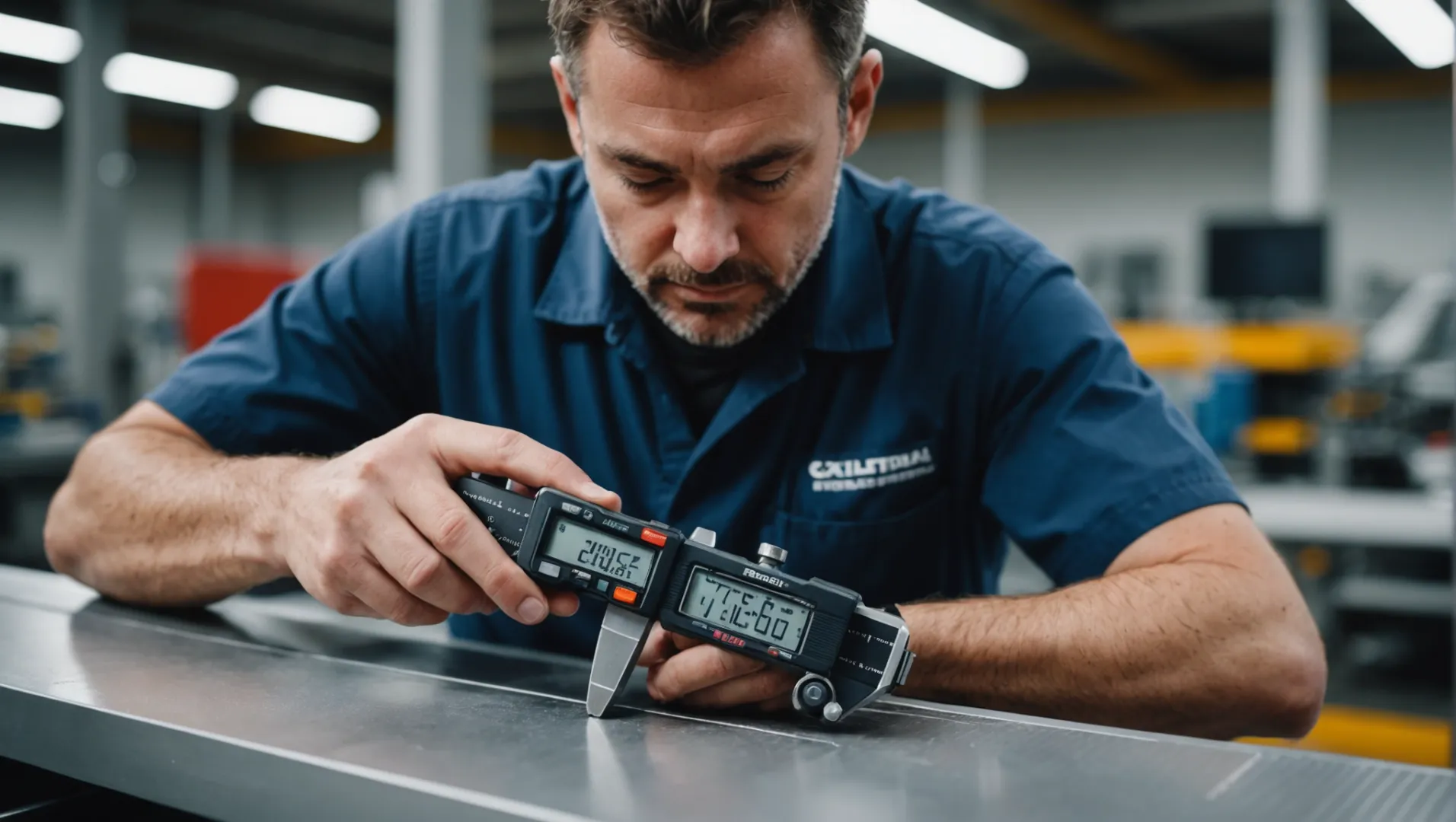
Material Characteristics and Their Impact on Tolerances
The selection of material is crucial when considering tolerances in injection molding. Materials exhibit different properties, such as thermal expansion, shrinkage, and elasticity, which can significantly influence the final dimensional accuracy of molded parts.
- Thermal Expansion: Materials with high thermal expansion rates, like certain plastics, tend to deform more during cooling. This can result in wider tolerances unless compensated by the mold design or process adjustments.
- Shrinkage: High shrinkage materials require careful calculation to maintain dimensional accuracy. For example, using a material with a 2% shrink rate could drastically affect a 100mm part if not properly accounted for.
- Elasticity: Materials that are more elastic might return to a near-original shape after deformation during ejection from the mold. This characteristic can help in maintaining tighter tolerances.
These material properties necessitate choosing appropriate tolerance levels. For materials prone to high variance, MT1 or MT2 levels might be necessary to ensure precision.
Influence of Design Complexity
Design intricacy also plays a pivotal role in determining tolerances. Complex designs often incorporate thin walls, undercuts, or intricate geometries that are challenging to mold consistently.
- Thin Walls: They are susceptible to warping and require tighter control to maintain dimensional stability.
- Undercuts and Complex Geometries: These features can complicate the molding process, potentially necessitating specialized tooling or additional processes like secondary machining to achieve desired tolerances.
For instance, a part with multiple thin sections may demand MT1 or MT2 tolerance levels to ensure consistency and functionality.
Balancing Material and Design in Tolerance Selection
The interplay between material choice and design complexity ultimately influences the selection of tolerance levels. Here’s a quick reference table showing how different factors can affect this decision:
Factor | Impact on Tolerance Selection |
---|---|
High Thermal Expansion | Requires tighter tolerances (MT1, MT2) |
High Shrinkage | Demands precise calculations; potentially tighter |
Elastic Materials | May allow for slightly wider tolerances |
Thin Walls | Necessitates tighter control for stability |
Complex Geometries | Often requires higher precision levels (MT1) |
Understanding these variables enables engineers and designers to make informed decisions about material selection1 and design optimization2, ensuring that parts meet both functional and cost-efficiency criteria.
High thermal expansion materials need tighter tolerances.True
Materials with high thermal expansion deform more, requiring tighter control.
Elastic materials always require MT1 tolerance levels.False
Elastic materials can sometimes allow for slightly wider tolerances.
What Role Do Production Processes Play in Determining Tolerances?
Production processes significantly influence the tolerances in manufacturing, impacting precision and quality.
Production processes determine tolerances by influencing factors such as material flow, cooling rates, and machine precision. These factors affect the dimensional accuracy and consistency of injection molded parts, guiding the selection of appropriate tolerance levels from MT1 to MT7 for optimal performance.

Influence of Material Flow and Cooling Rates
The production process profoundly affects the tolerances achievable in injection molding3. Material flow dynamics are crucial; they determine how well the material fills the mold, which directly impacts the precision of the final part. Uneven or insufficient flow can lead to defects, making it essential to understand how to manage these conditions to achieve the desired tolerances.
Cooling rates also play a significant role. Faster cooling might lead to shrinkage or warping, affecting the dimensional accuracy. Therefore, controlling the cooling process helps in maintaining tolerances within desired limits, especially for higher precision levels like MT1 or MT2.
Machine Precision and Calibration
The equipment used in production is another critical factor. Machines must be precisely calibrated to maintain consistent tolerances across multiple production runs. Advanced machinery with high precision capabilities can help achieve tighter tolerances required by higher tolerance levels such as MT1.
Periodic maintenance and calibration are necessary to ensure that machines operate at optimal efficiency and precision. Without this, even well-designed processes can yield inconsistent parts that fail to meet required standards.
Impact of Process Variations
Variations in the production process can arise from numerous sources, including changes in operator settings or environmental conditions within the manufacturing facility. Such variations can lead to deviations in part dimensions, affecting tolerance levels.
Implementing robust quality control measures helps mitigate these risks by ensuring that parts are consistently produced within the specified tolerance ranges. This is crucial when producing parts that require precision, as any deviation can lead to functional issues or failures in application.
Selecting the Right Process for Tolerance Levels
Choosing the right production process is vital for achieving desired tolerance levels. For example, more sophisticated processes like multi-material molding might be necessary for complex designs requiring high precision (MT1 or MT2).
On the other hand, simpler processes might suffice for parts where MT6 or MT7 tolerances are acceptable. Understanding the capabilities and limitations of different production processes allows manufacturers to make informed decisions that balance cost with performance needs.
China’s “Dimensional Tolerances for Plastic Molded Parts” (GB/T14486-2008) classifies the tolerance levels of injection molded parts into seven levels from MT1 to MT7. The specific tolerance values are as follows:
MT1: the highest precision, the smallest tolerance value. For example, when the basic size is 0-3mm, the tolerance is ±0.07mm; when it is 3-6mm, the tolerance is ±0.08mm; when it is 6-10mm, the tolerance is ±0.09mm, etc. With the increase of the size range, the tolerance value is gradually increased, but in the same size range compared with other grades, the tolerance value of MT1 is the smallest.
MT2: The tolerance requirement is also higher. For example, in the 0-3mm size range, the tolerance is ±0.10mm; in the 3-6mm size range, the tolerance is ±0.12mm, and so on. The overall tolerance value is a little larger than MT1, but still belongs to the higher precision tolerance level.
MT3: Medium precision level. For the 0-3mm size range, the tolerance is ±0.12mm; for the 3-6mm size range, the tolerance is ±0.14mm, etc. The tolerance of MT3 is the same as that of MT1, but it is still a high precision tolerance. In some injection molded parts with certain requirements for accuracy, but not particularly high, the MT3 level of tolerance will be used.
MT4: The accuracy is reduced compared to MT3. In the 0-3mm size range, the tolerance is ±0.16mm; in the 3-6mm size range, the tolerance is ±0.18mm and so on. Some common injection molded parts that do not have very strict requirements for dimensional accuracy may use MT4 grade tolerances.
MT5: General accuracy grade. For example, for 0-3mm size section, the tolerance is ±0.20mm; for 3-6mm size section, the tolerance is ±0.24mm, and so on. Many regular injection molded parts that do not require a high degree of dimensional accuracy will use the MT5 level of tolerance.
MT6: Lower precision. The tolerance is ±0.26mm for 0-3mm size range and ±0.30mm for 3-6mm size range. It is suitable for some injection molded parts which do not require high dimensional accuracy, but pay more attention to the function of the product or other requirements.
MT7: The lowest precision and the largest tolerance value. In the 0-3mm size range, the tolerance is ±0.34mm; in the 3-6mm size range, the tolerance is ±0.42mm and so on. Usually used for injection molded parts with almost no strict requirements for dimensional accuracy, or some large, simple structure injection molded parts.
In conclusion, understanding the role of production processes in determining tolerances is essential for optimizing injection molding operations. By aligning production strategies with tolerance requirements, manufacturers can enhance product quality while maintaining cost-effectiveness.
Material flow affects injection molding precision.True
Material flow determines how well the mold is filled, affecting precision.
Cooling rates have no impact on dimensional accuracy.False
Cooling rates affect shrinkage or warping, impacting accuracy.
Why Is It Important to Align with Industry Standards Like GB/T14486-2008?
Navigating global markets demands adherence to industry standards like GB/T14486-2008 for seamless integration and quality assurance.
Aligning with industry standards such as GB/T14486-2008 ensures product quality, compatibility, and market compliance, particularly in manufacturing sectors where precision and consistency are crucial. This alignment helps manufacturers meet international expectations, reduce errors, and streamline production processes.

Ensuring Product Quality and Consistency
Aligning with standards like GB/T14486-2008 is vital for maintaining a consistent level of product quality. These standards set clear guidelines for dimensional tolerances4 in injection molded parts, which are essential for ensuring that every product meets the necessary specifications. This consistency is crucial in industries such as automotive and aerospace, where even slight deviations can lead to significant issues.
Facilitating International Trade
By adhering to recognized standards, manufacturers can more easily enter and compete in international markets. GB/T14486-2008 provides a framework that aligns with global expectations, thus simplifying the export process and reducing the likelihood of disputes over product specifications. This is especially beneficial in sectors that require high precision components.
Streamlining Production Processes
Implementing these standards can lead to more efficient manufacturing processes. By having a clear set of guidelines, companies can reduce errors and rework, leading to lower production costs. Furthermore, using standardized tolerance levels helps in creating interchangeable parts5, which is a cornerstone of modern manufacturing practices.
Balancing Cost and Precision
One of the significant advantages of aligning with GB/T14486-2008 is the ability to balance cost with precision. By choosing the appropriate tolerance level from MT1 to MT7, manufacturers can optimize the use of materials and production time. For instance, selecting MT1 for critical components ensures the highest precision but at a higher cost, whereas MT7 might be suitable for less critical parts, providing cost savings without compromising functionality.
Enhancing Brand Reputation
Finally, adherence to established industry standards enhances a company’s reputation as a reliable manufacturer. It signals to clients and partners that the company values quality and consistency, which can be a significant competitive advantage in today’s market. It also reassures customers that the products will perform as expected, leading to greater customer satisfaction and loyalty.
GB/T14486-2008 ensures product compatibility globally.True
This standard aligns with global expectations, facilitating international trade.
Aligning with GB/T14486-2008 increases production errors.False
Adhering to standards reduces errors by providing clear manufacturing guidelines.
How Can You Balance Cost and Precision in Injection Molding?
Balancing cost and precision in injection molding is a delicate dance that manufacturers must master to ensure both quality and affordability.
To balance cost and precision in injection molding, manufacturers must consider tolerance levels, material choice, and design complexity. Opting for lower tolerance levels like MT4 to MT7 can reduce costs for parts with less critical dimensions, while higher tolerances are reserved for precision-demanding components.

Understanding Tolerance Levels
Injection molding involves selecting appropriate tolerance levels6 according to the precision requirements of the part. The GB/T14486-2008 standard classifies these into seven categories (MT1 to MT7), with MT1 providing the highest precision.
- MT1: Ideal for high-precision parts, but at a higher cost due to the stringent manufacturing processes required.
- MT7: Suitable for parts where precision is less critical, leading to cost savings in production.
Cost Implications of Tolerance Levels
Choosing a higher tolerance level like MT1 or MT2 typically increases production costs due to the need for advanced machinery and more meticulous quality checks. For parts where such precision is unnecessary, selecting a lower tolerance level can significantly reduce expenses.
Material Selection
The choice of material impacts both cost and precision. Engineering plastics like PEEK or polycarbonate offer high precision but are costlier than alternatives like polypropylene or ABS.
- High-Precision Materials: Used when dimensional accuracy and stability are critical.
- Cost-Effective Materials: Best for non-critical applications where flexibility and cost-effectiveness are prioritized.
Design Complexity
Complex designs often demand higher precision, increasing costs. Simplifying part designs can allow for broader tolerances, reducing the need for expensive precision processes.
Consider breaking complex parts into simpler assemblies that can be molded with lower tolerances, thereby balancing precision needs with cost constraints.
Tips for Cost-Effective Precision
- Early Design Consultation: Engage with engineers early to align design goals with manufacturing capabilities.
- Prototype Testing: Utilize prototypes to refine designs and tolerance levels before mass production.
- Leverage Technology: Use advanced simulation tools to predict manufacturing outcomes and optimize designs.
Balancing cost and precision requires a nuanced approach that considers multiple factors including material choice, design complexity, and desired tolerance levels7. Understanding these elements helps manufacturers make informed decisions, ensuring quality without excessive costs.
MT1 tolerance level is the most cost-effective option.False
MT1 tolerance level is costly due to high precision requirements.
Using polypropylene can reduce injection molding costs.True
Polypropylene is less expensive than high-precision materials like PEEK.
Conclusion
Choosing the right tolerance level is vital for meeting design requirements and controlling production costs. Reflect on your project’s needs and consult industry standards to ensure optimal results.
-
Explore how different materials influence tolerance requirements.: All materials shrink when cooling in a mold. Arguably, one of the most important characteristics of material selection is its shrink rate and … ↩
-
Learn design strategies for maintaining tight tolerances.: Here are some injection molding tolerance guidelines that designers and engineers can follow to optimize part tolerances. ↩
-
Gain insights into how material flow impacts part accuracy.: The phenomenon of fountain flow affects almost every aspect of the molded product, starting with filling, extending to pack and hold, … ↩
-
Understand how these standards define dimensional tolerances for various applications.: This Standard specifies the dimensional tolerances for the moulded plastic parts made from thermosetting and thermoplastic materials. ↩
-
Learn why interchangeable parts are vital for efficient production.: Interchangeable parts, popularized in America when Eli Whitney used them to assemble muskets in the first years of the 19th century, allowed relatively … ↩
-
Learn about tolerance levels for precise manufacturing guidance.: Tolerance is the range of deviation in specifications that still allows your part to function as needed. ↩
-
Discover strategies for selecting cost-effective tolerance levels.: Injection molding tolerances are acceptable variations in size for part features and overall dimensions. They are expressed as plus or minus (±) values in … ↩