Have you ever wondered how something as invisible as static electricity can impact your production line?
To solve static problems in injection molding, consider using antistatic agents, optimizing humidity levels, employing static elimination equipment like ion blowers, and improving mold and conveyor designs. These measures can effectively reduce static charge and its adverse effects.
While these methods provide a solid foundation for addressing static issues, understanding the nuances of each approach can significantly enhance your production efficiency and product quality. Let’s delve deeper into each method to uncover more detailed solutions.
Humidity above 65% reduces static in injection molding.True
Higher humidity increases air conductivity, dissipating static charges effectively.
What Are the Main Causes of Static Electricity in Injection Molding?
Static electricity can silently disrupt injection molding, affecting product quality and safety.
Static electricity in injection molding arises mainly from friction and induction charging. Friction occurs as the plastic melt flows through the mold, while induction happens in charged environments.
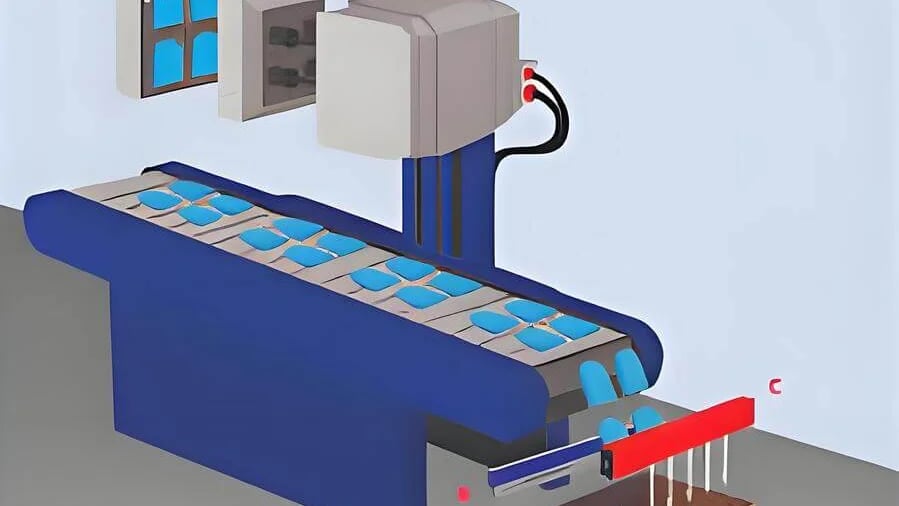
Understanding Friction Charging
Friction charging is a common source of static electricity in injection molding. As the plastic melt moves through the mold cavity, it encounters friction. This friction causes surface molecules to become charged, leading to charge displacement and ultimately generating static electricity.
Additionally, when plastic parts separate from the mold or move along the conveyor belt, similar frictional interactions occur, perpetuating static buildup. This is particularly problematic in cases where molds are complex or where there is significant movement during processing.
Example: Friction in Action
Consider a scenario where thin-walled parts are involved. These parts often experience significant friction due to their surface area relative to mass. Such parts can demonstrate increased static because they require more energy to eject from molds, leading to enhanced charge accumulation.
Induction Charging Dynamics
Induction charging occurs when external electric fields or other charged objects influence plastic parts during production. This type of charging is less about direct contact and more about the presence of an electric field that polarizes the molecules within the plastic.
For instance, in environments with high electromagnetic activity, plastic parts might inadvertently gain charge without any direct interaction. This makes managing the workspace critical to minimizing static electricity.
Example: Inductive Environments
In a factory with heavy machinery, equipment may create electric fields that inadvertently lead to induction charging of nearby components. Ensuring proper grounding and shielding can mitigate such effects, maintaining product integrity.
Friction vs Induction1
While both methods lead to static electricity generation, their mechanisms are distinct. Friction is a result of physical contact and movement, whereas induction is more about proximity and electromagnetic fields. Understanding these differences helps in designing effective strategies to manage static issues.
Both types of charging need careful monitoring and control, which can be achieved by modifying processing environments or employing specialized equipment designed to dissipate or neutralize static charges. This understanding allows for targeted interventions, enhancing production efficiency and ensuring high-quality outputs.
Friction is the main cause of static in injection molding.True
Friction charging occurs as plastic moves through molds, causing static.
Induction requires direct contact to cause static electricity.False
Induction involves electric fields polarizing molecules, not contact.
How Does Static Electricity Affect Product Quality and Efficiency?
Static electricity is an invisible force that can significantly hinder the quality and efficiency of production processes.
Static electricity can degrade product quality by causing dust attraction, equipment malfunctions, and safety hazards, impacting efficiency.
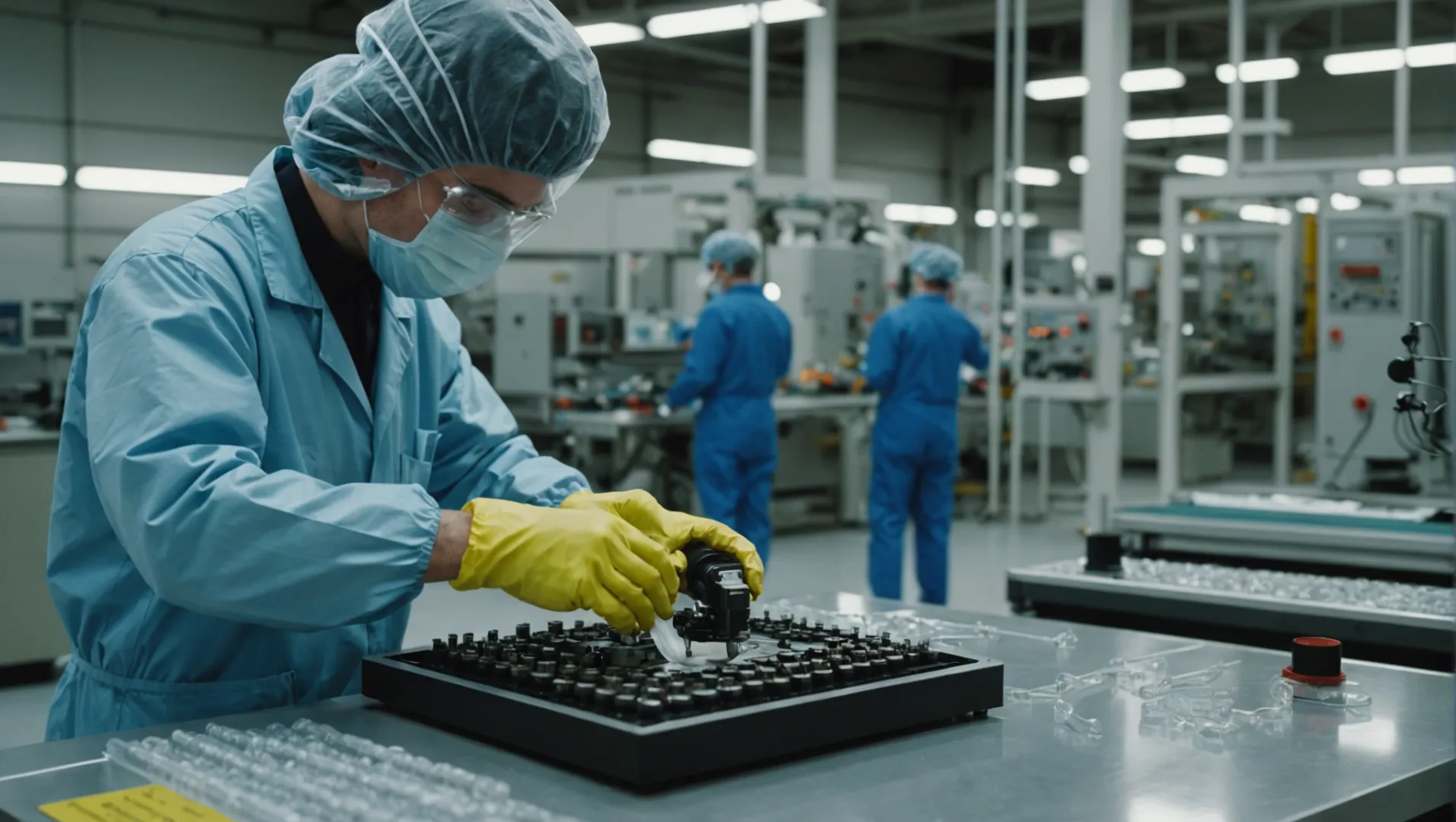
Causes and Effects of Static Electricity on Product Quality
Static electricity in injection molding primarily stems from friction charging and induction charging. As plastic melts flow through mold cavities or separate from surfaces, they become charged. Similarly, nearby electric fields can induce charges on plastic parts. These charges lead to several quality issues:
- Dust Attraction: Charged surfaces attract dust particles, degrading the visual quality of products like optical lenses or electronic casings.
- Adhesion Issues: Parts may stick to molds or conveyor belts, complicating demolding and product handling.
Impact on Production Efficiency
The efficiency of production lines can be severely hampered by static electricity:
- Interference with Processes: Adsorption on molds or equipment due to static can delay production cycles.
- Safety Concerns: Electrostatic discharge (ESD) poses risks in flammable environments, possibly leading to fires or explosions.
Addressing Static Challenges in Injection Molding
The following strategies can mitigate static issues:
- Antistatic Agents: Use internal or external agents to neutralize static charges. Internal agents are mixed with raw materials for lasting effects, while external agents are applied to product surfaces for immediate results.
- Environmental Controls: Increasing humidity helps dissipate static charges; maintaining humidity above 65% is effective.
- Static Elimination Equipment: Install ion blowers or static elimination bars to neutralize charges during production.
By integrating these methods into your process, you can improve product quality and production efficiency, ensuring a safer and more reliable manufacturing environment. For more insights on optimizing injection molding techniques2, explore our detailed guides and expert advice.
Static electricity causes dust attraction on products.True
Charged surfaces attract dust, degrading product quality.
Increasing humidity decreases static electricity issues.True
Higher humidity helps dissipate static charges effectively.
Which Antistatic Agents Are Most Effective for Injection Molding?
Static electricity can wreak havoc in injection molding, leading to product defects and operational issues.
For effective static control in injection molding, consider both internal and external antistatic agents. Internal agents blend into the plastic, offering long-term protection, while external agents are applied to surfaces for immediate, albeit temporary, effect. Choose based on product requirements and production constraints.
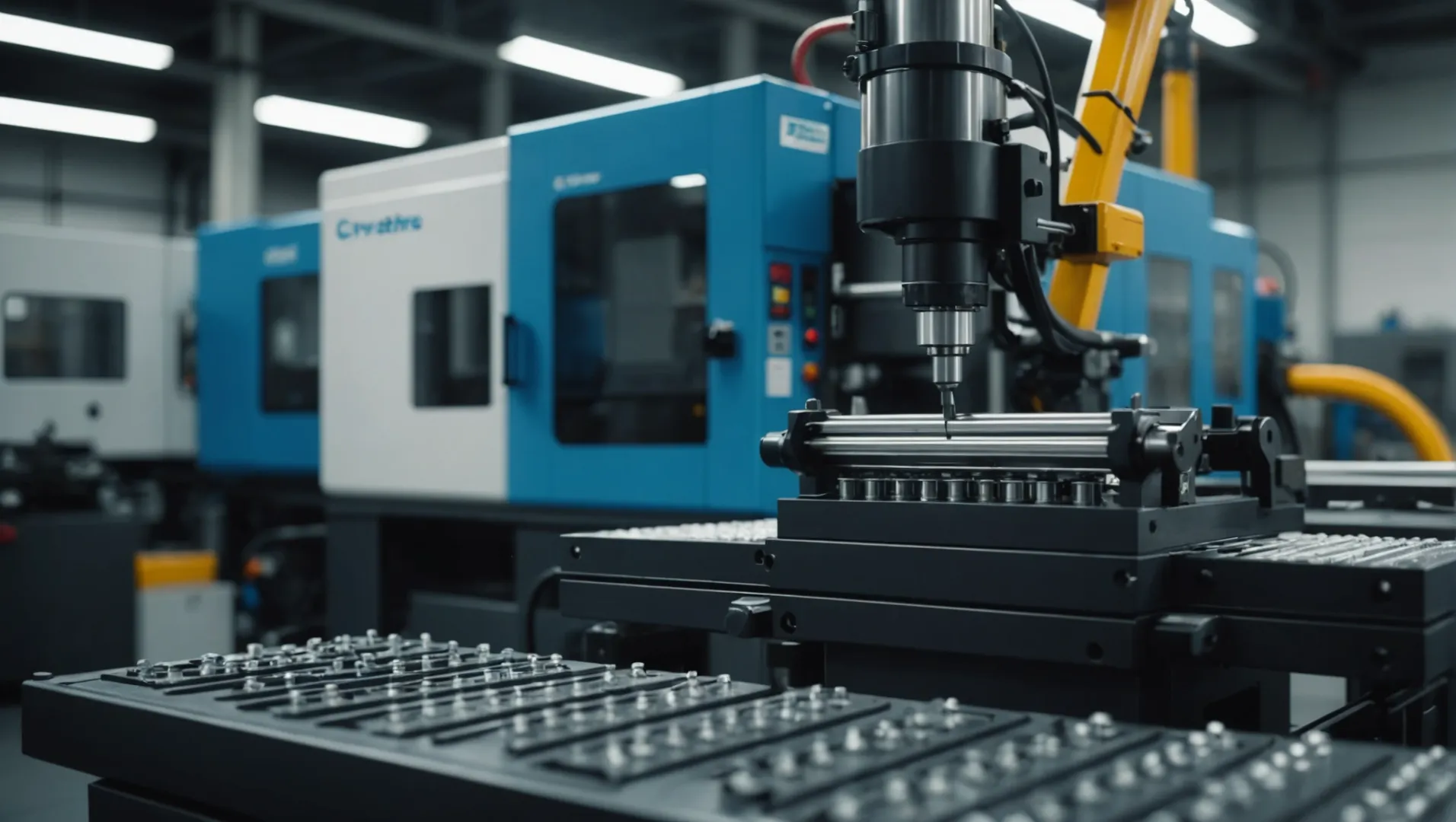
Understanding Antistatic Agents
Antistatic agents play a critical role in minimizing static electricity in injection molding processes. These agents work by increasing the conductivity of the material, allowing charges to dissipate more quickly. There are two primary types: internal and external antistatic agents.
Internal Antistatic Agents
Internal antistatic agents are mixed directly into the plastic raw materials before the injection molding process begins. These agents form a conductive network within the plastic, providing long-lasting protection against static buildup.
-
Advantages:
- Long-lasting effect since they are integrated into the product.
- Suitable for products that require consistent static protection throughout their lifecycle.
-
Examples:
- Quaternary ammonium compounds: Known for their excellent antistatic properties but can be sensitive to humidity.
- Phosphoric acid esters: These provide a good balance of conductivity and are often used in electronic housings.
External Antistatic Agents
External agents are applied to the surface of the molded product. They work by forming a thin conductive layer, typically attracting moisture from the air to reduce static charge.
-
Advantages:
- Quick and easy application.
- Ideal for immediate static reduction needs.
-
Examples:
- Spray-based solutions: Often used for quick fixes in post-production.
- Wipe-on formulations: Provide a temporary solution that can be reapplied as needed.
Comparing Effectiveness
The choice between internal and external antistatic agents often depends on the specific requirements of the injection molded product and the production environment.
Feature | Internal Agents | External Agents |
---|---|---|
Longevity | High | Medium |
Application Ease | Complex (requires mixing with material) | Simple (surface application) |
Immediate Effectiveness | Lower (requires integration) | High (immediate application) |
Cost | Higher (more material needed) | Lower (less material, easier to apply) |
Factors Influencing Effectiveness
- Material Compatibility: Choose agents compatible with the plastic type to avoid altering mechanical properties.
- Environmental Conditions: High humidity environments may enhance the effectiveness of certain external agents.
- Product Design and Usage: Consider how and where the product will be used to determine the necessary level of antistatic protection.
Understanding these factors and characteristics can help manufacturers decide on the most effective antistatic strategy for their specific needs. For more on this topic, explore injection molding static solutions3 or delve into advanced antistatic technologies4.
Internal agents offer immediate static reduction.False
Internal agents require integration into the material, delaying effect.
External agents are ideal for quick static fixes.True
External agents provide immediate static reduction upon application.
How Can Optimizing Production Environment Reduce Static Problems?
Static electricity in production can lead to various operational challenges, affecting both efficiency and safety.
Optimizing the production environment by controlling humidity and using static elimination equipment can significantly reduce static electricity problems. This approach helps prevent product defects, enhances safety, and improves overall production efficiency.
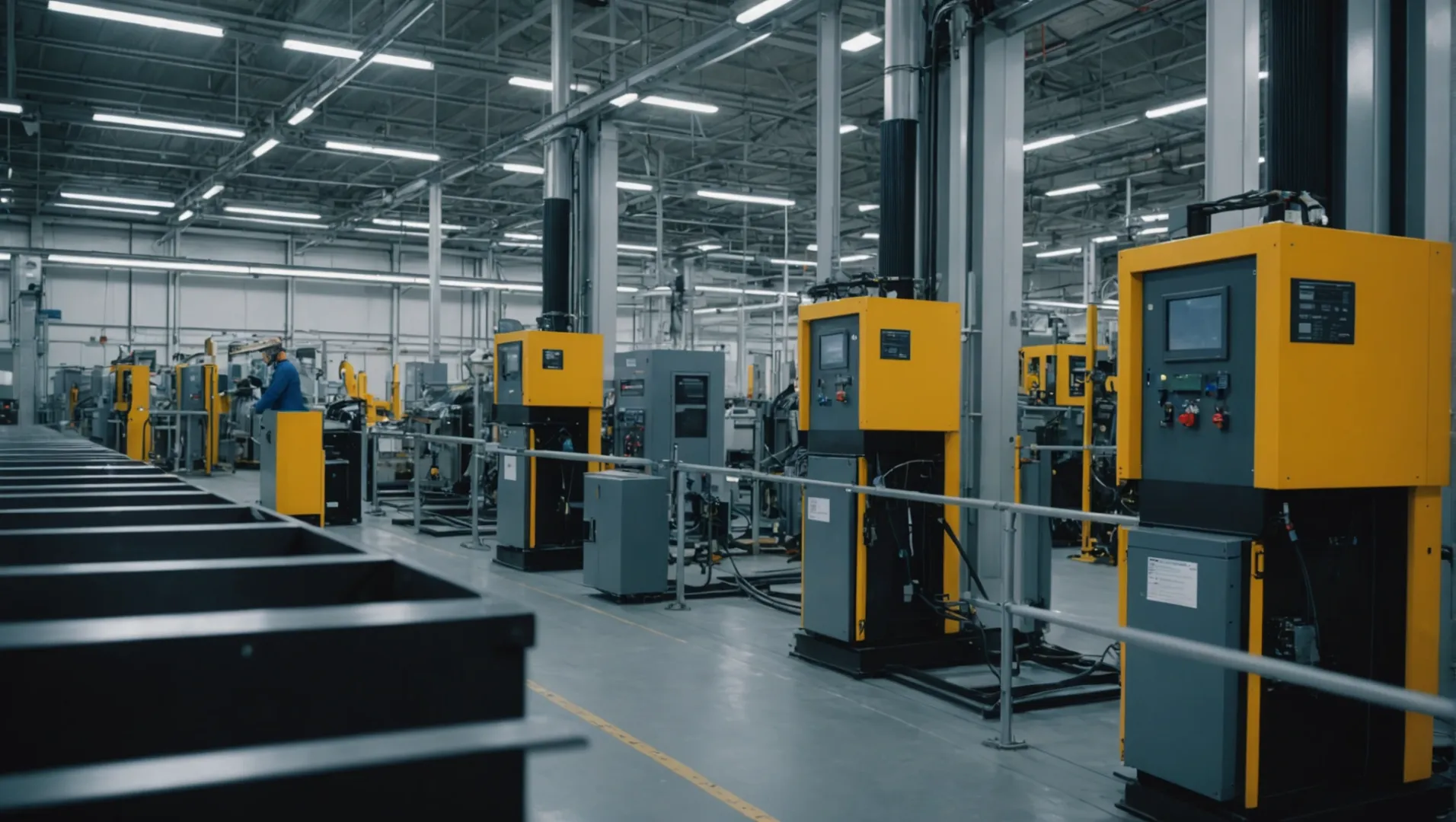
Understanding the Role of Humidity
Humidity control is a pivotal factor in managing static electricity within a production environment. By maintaining a relative humidity level above 65%, the static charge on surfaces can be more readily dissipated. In humid conditions, the air conducts electricity better, allowing charges to escape rather than accumulate on materials.
This method is particularly useful in injection molding5 facilities where dust attraction and equipment interference can impede product quality and safety.
Implementing Static Elimination Equipment
Static elimination devices like ion blowers and static bars play a crucial role in reducing static-related issues.
- Ion Blowers: These devices emit ions that neutralize static charges on surfaces. They are strategically positioned around molds or above conveyor belts to ensure consistent discharge of static electricity from products.
- Static Bars: Installed at potential charge accumulation points, static bars release ions to negate surface charges effectively.
Both tools are essential for maintaining operational efficiency and protecting sensitive electronic equipment from electrostatic discharge (ESD).
Enhancing Production Processes
Improving the design and materials of production equipment can also mitigate static problems. For instance:
- Mold Design Optimization: Incorporating static elimination features such as negative ion blowers within mold designs can prevent parts from sticking due to static.
- Anti-Static Conveyor Belts: Using belts made with conductive materials or adding metallic fibers can enhance conductivity, reducing charge build-up on transported products.
These enhancements not only address static issues but also streamline the production process, leading to increased productivity and product quality.
Benefits of Environmental Optimization
When the production environment is optimized to control static, several benefits emerge:
- Reduced Product Defects: Static can cause dust attraction or part adhesion, leading to defects. Mitigating static results in higher-quality outputs.
- Improved Safety: By minimizing the risk of electrostatic discharge, facilities can prevent shocks and reduce fire hazards in flammable environments.
- Enhanced Efficiency: Less downtime from static-related interruptions means a smoother and more efficient production flow.
By focusing on environmental factors such as humidity control and the strategic placement of static elimination equipment, manufacturers can significantly reduce static-related issues and enhance overall production efficacy.
Humidity above 65% reduces static electricity.True
High humidity helps dissipate static charges by improving air conductivity.
Static bars increase static electricity in production.False
Static bars release ions to neutralize and reduce static charges.
Conclusion
By implementing these strategies, you can effectively mitigate static electricity problems in injection molding, ensuring better product quality and operational efficiency.
-
Explore how friction and induction differ in generating static.: Charging by contact involves physically touching another charged object, while charging by induction does not.Charging Summary: | Charging Method | Initial … ↩
-
Discover advanced techniques to enhance your injection molding processes.: Injection molding tool and process engineers must take these 8 steps to ensure consistent and repeatable manufacturability of flawless molded parts. ↩
-
Explore comprehensive static control strategies tailored for injection molding.: Installing a static eliminator as the plastic is extruded and entering the mold (A) will neutralize the charge preventing quality failures. ↩
-
Discover cutting-edge antistatic innovations in plastic manufacturing.: Current trends include the rising adoption of sustainable and bio-based anti-static additives as industries focus on eco-friendly solutions. ↩
-
Learn how controlling humidity affects static electricity in production.: Moisture-related splay defects can be traced to a material’s drying state, the injection mold fittings, or the drying unit itself. ↩