Navigating the world of plastic injection molding can be daunting, especially when faced with the challenge of high-temperature deformation. This issue affects product quality and reliability significantly, but I’m here to shed some light on practical solutions.
To solve high-temperature deformation in plastic injection molded parts, focus on selecting appropriate materials, optimizing the injection molding process, enhancing product design, and implementing post-processing techniques like annealing. These strategies help maintain dimensional stability and improve high-temperature performance.
While this brief overview offers initial insights, delving deeper into each solution will reveal nuanced strategies and best practices crucial for tackling deformation effectively. Let’s explore these approaches to ensure robust manufacturing outcomes.
Annealing reduces internal stresses in plastic parts.True
Annealing heats and gradually cools plastics, relieving internal stresses.
How Does Material Selection Affect Deformation?
Material selection is crucial in determining the deformation characteristics of plastic parts under high temperatures.
The choice of material directly influences deformation due to differences in heat deformation temperatures, crystallinity, and stress factors. Opt for high-performance plastics and consider additives to enhance stability.
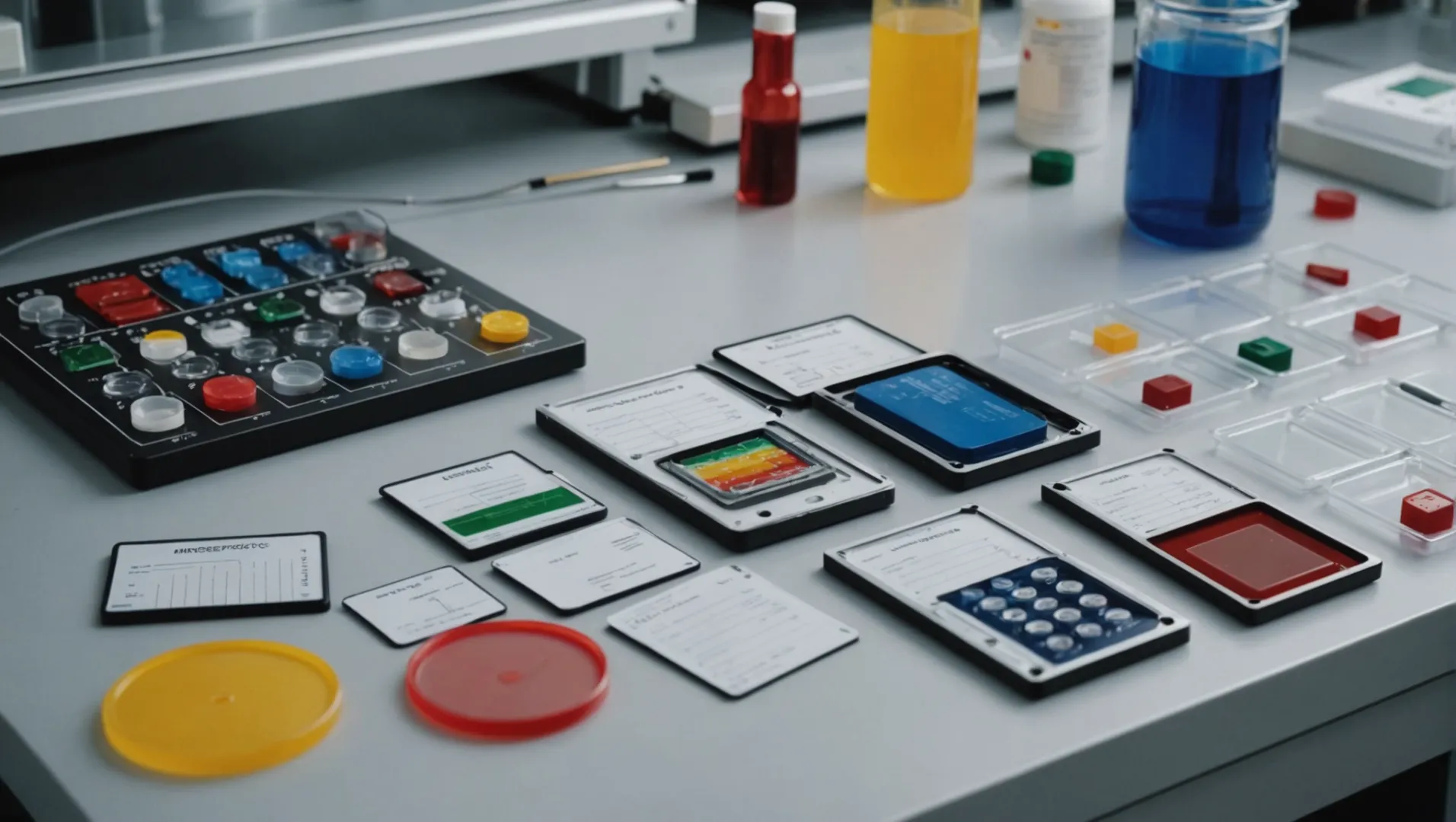
Understanding Material Properties
Material properties are pivotal in influencing how a plastic part will behave under thermal stress. Different materials possess varying heat deformation temperatures, which can significantly affect their performance. For instance, plastics with a low heat deformation temperature are more likely to deform when exposed to high temperatures. Additionally, the crystallinity of plastics1 plays a role; higher crystallinity often means a higher heat deformation temperature, but this can also introduce internal stresses that contribute to deformation.
Material Type | Heat Deformation Temperature | Crystallinity Impact |
---|---|---|
Low-Performance Plastic | Low | Low crystallinity, less stability |
High-Performance Plastic | High | High crystallinity, more stability but potential internal stress |
Selecting the Right Materials
When choosing materials, it is crucial to prioritize those with higher heat deformation temperatures. Engineering plastics or high-performance plastics are generally more reliable in maintaining dimensional stability at elevated temperatures. Additionally, incorporating heat-resistant agents can further enhance the thermal stability of the material.
For products requiring exceptional high-temperature performance, exploring materials with added heat-resistant agents2 can be beneficial. These agents modify the polymer’s structure to improve its ability to withstand heat without significant deformation.
Balancing Performance and Cost
While high-performance plastics offer superior stability, they often come at a higher cost. It is essential to balance the material properties with cost-effectiveness. Evaluating the specific requirements of your application will guide you in selecting a material that meets both performance and budget constraints. Exploring cost-effective solutions3 in material engineering can provide insights into achieving this balance.
Understanding these aspects helps in making informed decisions that mitigate deformation issues in plastic injection molded parts.
High-performance plastics resist deformation at high temperatures.True
They have higher heat deformation temperatures, enhancing stability.
Low crystallinity in plastics increases their heat resistance.False
Higher crystallinity typically enhances heat resistance, not lower.
What Role Does the Injection Molding Process Play?
Understanding the nuances of the injection molding process is key to preventing high-temperature deformation in plastic parts.
The injection molding process significantly influences the dimensional stability of plastic parts. Factors like injection temperature, cooling uniformity, and holding time are crucial in managing internal stresses that lead to deformation under high temperatures. Optimizing these parameters is essential for robust and reliable production outcomes.
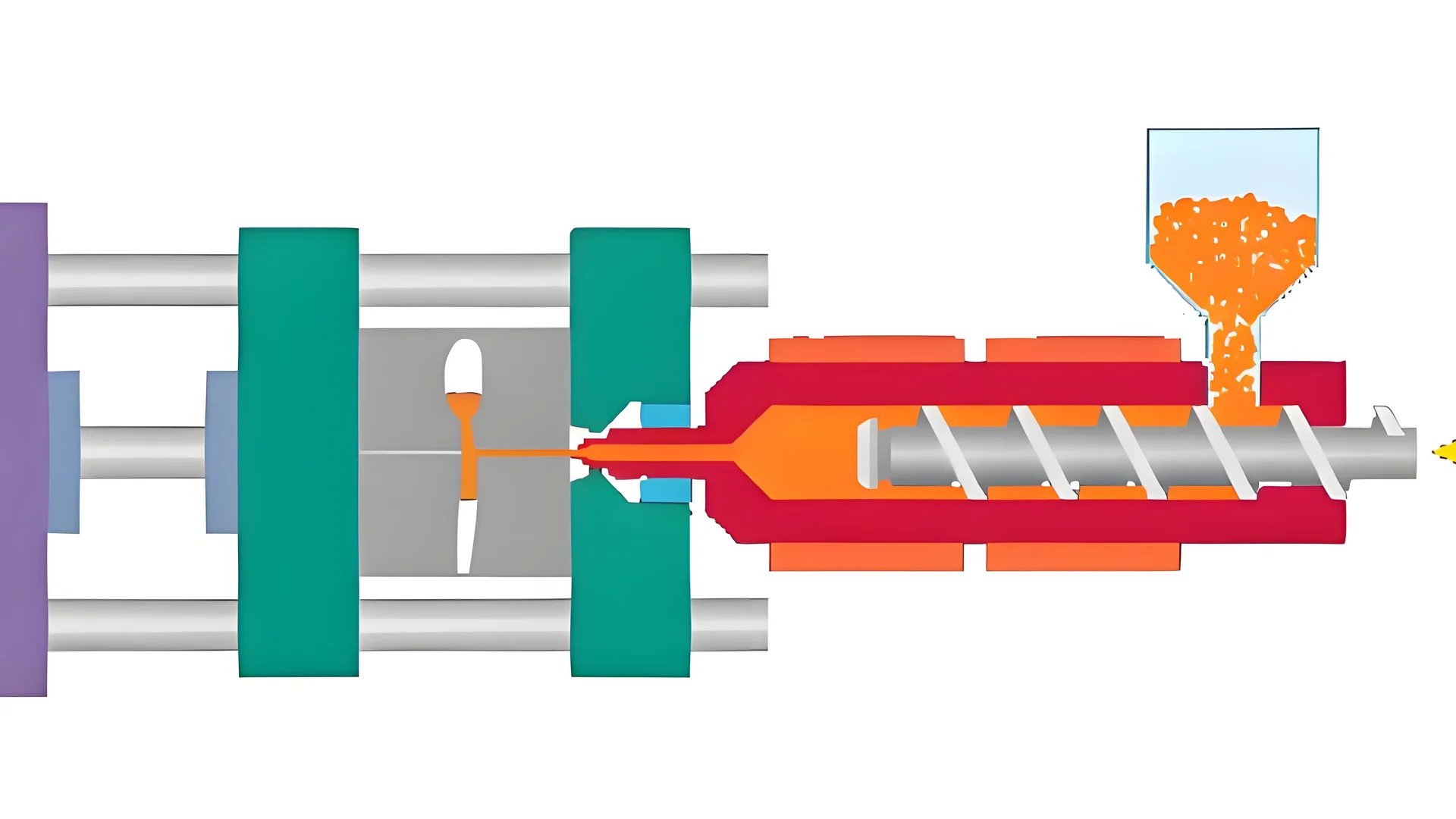
Understanding Injection Temperature’s Impact
Injection temperature is pivotal in shaping the final properties of molded parts. If the temperature is too high, it can increase the movement of plastic molecular chains, resulting in heightened internal stress during cooling. This internal stress can cause deformation when exposed to high temperatures. To mitigate this, manufacturers should aim to reduce the injection molding temperature while ensuring complete plastic melting. Adjustments in screw speed and heating temperature4 of the molding machine can help achieve this balance.
Ensuring Uniform Cooling
Uniform cooling is essential to prevent uneven shrinkage, which often leads to deformation. Discrepancies in cooling rates across different sections of a part can cause warping. To address this, it’s important to optimize the mold’s cooling system. A well-designed cooling system includes strategically arranged water channels and controlled water flow rate and temperature. These measures ensure consistent cooling throughout the part, minimizing stress concentrations.
Importance of Sufficient Holding Time
Holding time plays a crucial role in managing the shrinkage behavior of molded parts. Inadequate holding time can result in uneven shrinkage, increasing the risk of deformation. By extending the holding time appropriately, parts can fully compensate for shrinkage during cooling, leading to improved dimensional accuracy. Adjusting holding pressure and time to align with specific material properties is critical in achieving optimal results.
Practical Examples: Case Studies
Consider a scenario where a manufacturer reduced injection temperature and optimized cooling channels for a complex automotive component. By doing so, they achieved a significant reduction in deformation rates, enhancing the part’s performance under high thermal loads. Another case involved extending the holding time for a high-crystallinity polymer part, which resulted in superior dimensional stability and reduced post-processing requirements.
These examples highlight how tailored adjustments to the injection molding process can effectively address deformation challenges, ensuring robust product quality and consistency.
Injection temperature affects plastic part stability.True
High injection temperatures increase internal stress, affecting stability.
Uniform cooling prevents uneven shrinkage in molded parts.True
Consistent cooling minimizes warping by ensuring even shrinkage.
How Can Product Design Minimize Deformation?
In the realm of product design, meticulous attention to structural details can significantly minimize deformation, especially under high-temperature conditions.
To minimize deformation in product design, ensure uniform wall thickness, simplify shapes, and optimize rib placement. These design strategies reduce stress concentration and improve the product’s ability to withstand temperature-induced deformation.
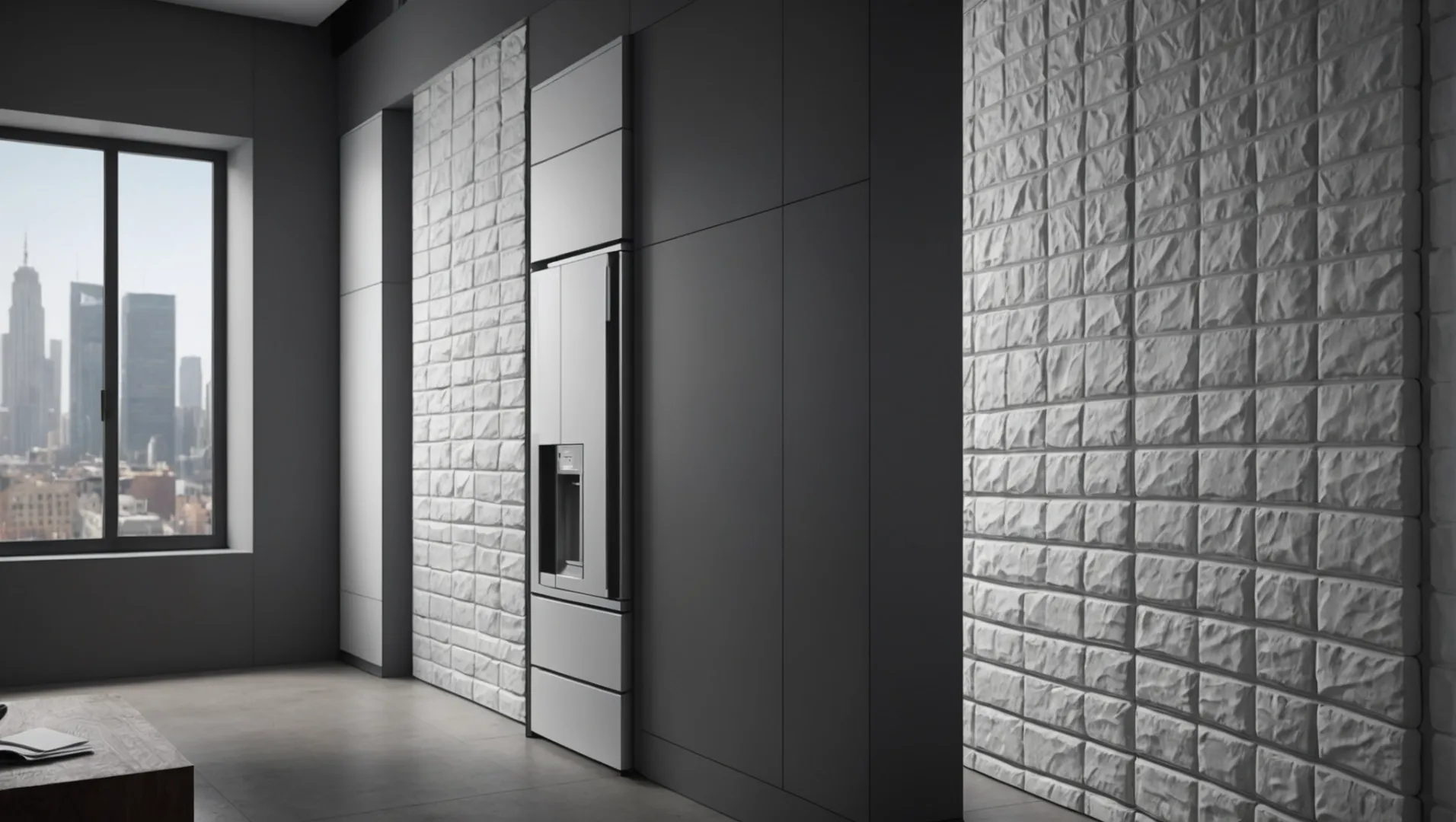
Understanding the Impact of Design on Deformation
Product design plays a crucial role in mitigating deformation by reducing stress concentrations and ensuring uniform load distribution. A well-thought-out design can significantly enhance a product’s resilience against high-temperature deformation.
Uniform Wall Thickness
One primary strategy is ensuring uniform wall thickness throughout the product. Variations in wall thickness can lead to uneven cooling and internal stresses, increasing the likelihood of deformation. By maintaining consistent thickness, the product cools uniformly, reducing shrinkage disparities.
Example Table: Wall Thickness Recommendations
Feature | Recommended Thickness |
---|---|
Thin Walls | 1.0 – 2.5 mm |
Standard Walls | 2.5 – 4.0 mm |
Thick Walls | 4.0 – 6.0 mm |
Simplifying Shapes
Complex shapes can introduce stress concentrations due to uneven material distribution. Simplified designs with streamlined contours not only facilitate more consistent cooling but also enhance the material’s structural integrity. Employing curves and avoiding sharp angles can diminish stress points.
Optimizing Rib Placement
Ribs are essential for enhancing stiffness without adding excessive weight, but their placement must be strategic. The position, number, and shape of ribs should be designed to distribute stresses evenly across the product. It’s advisable that rib thickness not exceed 60% of the wall thickness to prevent stress concentration.
Considerations for Advanced Design Techniques
Beyond basic structural considerations, advanced techniques such as Finite Element Analysis5 can be employed to predict potential stress points and deformation under simulated conditions.
Use of Simulation Tools
Simulation tools allow designers to visualize how a product will perform under various conditions, thereby refining designs before production. For instance, adjusting rib configurations or modifying wall angles can be tested virtually to assess their impact on deformation.
By prioritizing these design principles, manufacturers can significantly reduce the risk of deformation in high-temperature environments, ensuring product reliability and longevity.
Uniform wall thickness reduces deformation risk.True
Consistent wall thickness ensures even cooling, reducing stress.
Rib thickness should exceed 60% of wall thickness.False
Rib thickness should not exceed 60% to prevent stress concentration.
What Post-Processing Techniques Are Effective?
Post-processing techniques play a pivotal role in minimizing deformation in plastic injection molded parts, enhancing their dimensional stability.
Effective post-processing techniques include annealing and humidity conditioning. Annealing reduces internal stresses, while humidity conditioning addresses water absorption in certain plastics, improving their dimensional stability and high-temperature performance.
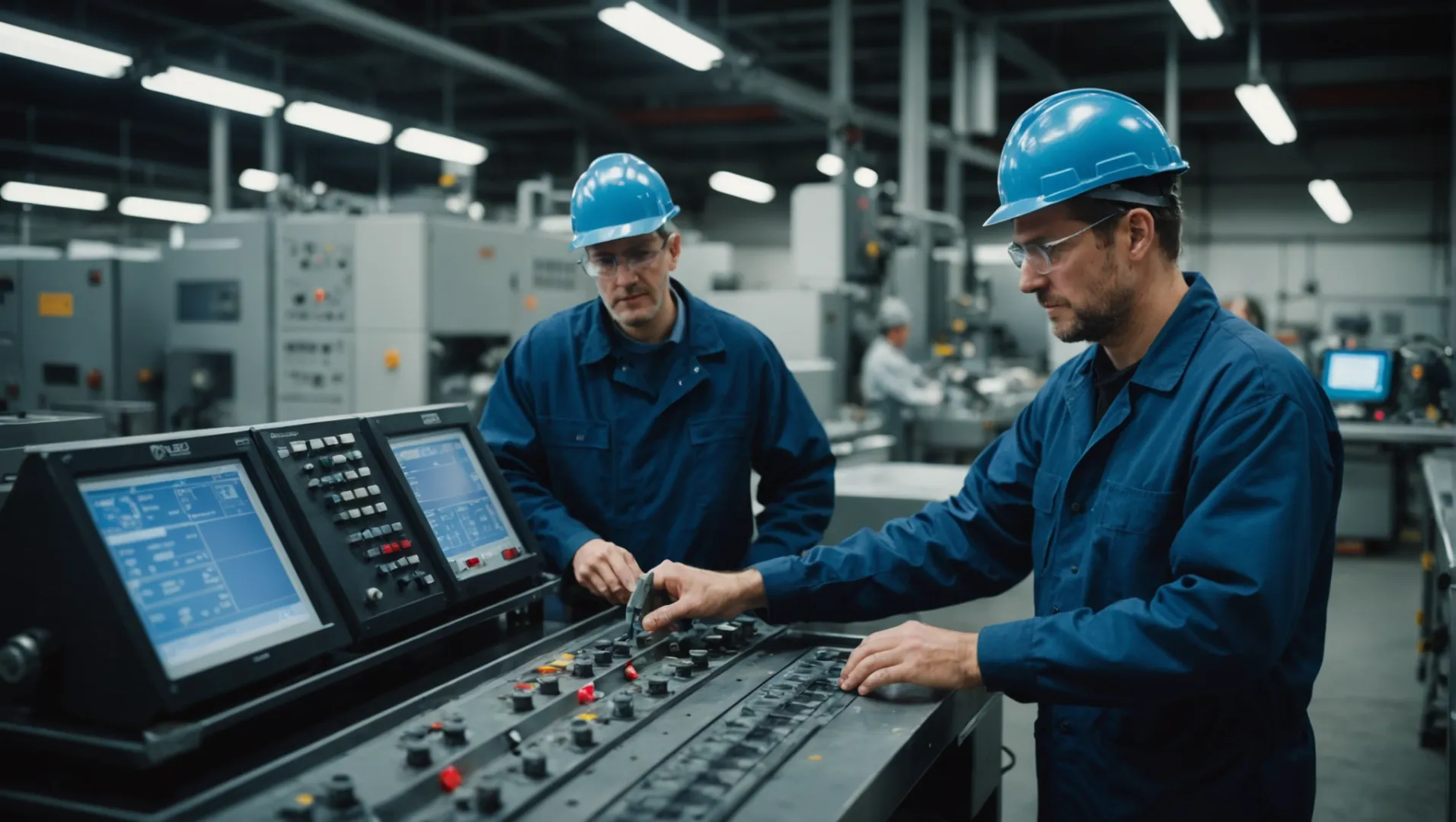
Understanding Post-Processing Techniques
Post-processing is an essential phase in the lifecycle of plastic injection molded parts. It not only improves the aesthetic and functional qualities of the parts but also plays a critical role in enhancing their performance under varying environmental conditions. Two widely adopted post-processing techniques are annealing and humidity conditioning, both of which serve distinct purposes.
Annealing Treatment
Annealing involves heating a plastic part to a temperature slightly below its thermal deformation point and then gradually cooling it down. This process relieves internal stresses that might have developed during the injection molding process.
Benefits of Annealing
- Stress Reduction: By reducing residual stress, annealing enhances the dimensional stability of the part.
- Enhanced Performance: It improves mechanical properties such as toughness and resistance to cracking.
Application Considerations
- Temperature Control: Typically, the annealing temperature is set 10-20°C below the product’s heat deflection temperature.
- Time Requirements: The duration depends on factors such as part size and wall thickness.
This treatment is particularly effective for products subjected to high temperatures during their service life.
Humidity Conditioning
Humidity conditioning is crucial for plastics with high water absorption rates, such as nylon. By allowing the part to absorb a controlled amount of moisture, this technique mitigates internal stress and enhances stability.
Advantages of Humidity Conditioning
- Dimensional Accuracy: Maintains dimensional accuracy by preventing warping due to moisture content changes.
- Enhanced Flexibility: Increases the flexibility of certain plastics, reducing brittleness.
Implementation Tips
- Controlled Environment: Ensure a stable humidity environment to prevent over-conditioning.
- Monitoring: Regular checks on moisture levels to maintain consistency.
Comparing Techniques
Below is a table summarizing the two post-processing methods:
Technique | Purpose | Benefits | Key Considerations |
---|---|---|---|
Annealing | Stress reduction | Improved toughness and stability | Temperature and time management |
Humidity Conditioning | Moisture control for certain plastics | Dimensional accuracy, reduced brittleness | Controlled humidity environment |
Implementing these post-processing techniques effectively requires understanding the material properties and service conditions of the molded parts. Learn more about annealing processes6 and explore humidity conditioning strategies7. These resources provide detailed insights into optimizing post-processing for various applications.
Annealing reduces internal stresses in plastics.True
Annealing relieves internal stresses from the molding process.
Humidity conditioning decreases plastic flexibility.False
Humidity conditioning actually increases flexibility by reducing brittleness.
Conclusion
Addressing high-temperature deformation requires a multifaceted approach involving careful material selection, process control, and design optimization. Implementing these strategies will enhance product quality and ensure long-term performance, encouraging continued innovation and efficiency in manufacturing.
-
Gain insights into how crystallinity influences material stability under heat.: the deformation? • What is the difference between deformation of single crystal and polycrystal? • How does the loading rate affect the deformation? Page 9 … ↩
-
Discover how additives enhance plastic performance at high temperatures.: The fibers also have the added benefit of increasing overall stiffness and material strength. ↩
-
Explore affordable options for using high-performance materials.: Advanced thermoplastic contributes to cost-effective high performance … “PLQ Series QDs are among the highest-performing engineered polymer connectors for … ↩
-
Learn optimal parameters for adjusting screw speed and heating temperature.: It is better to adjust the rotation speed of the screw according to the type of construction plastics and the length of the production cycle. ↩
-
Learn how simulation predicts stress and deformation in design.: Finite element analysis (FEA) is the process of simulating the behavior of an object or assemblage of objects when it’s exposed to specified physical … ↩
-
Discover detailed annealing procedures for stress reduction.: Well it’s simply a process that involves heating a specific type of plastic below its glass transition temperature in order to ease all the internal pressures … ↩
-
Explore methods for effective humidity conditioning in plastics.: The purpose of plastic annealing is to eliminate internal stress,Moisture conditioning of plastic products is mainly for polyamide (nylon) … ↩