Do you know the frustration from underfill problems in your mold designs? Believe me, I’ve experienced it as well. Let’s explore some good solutions together.
Fixing underfill issues in mold design requires focusing on gate placement. Runner systems also need careful adjustment. Exhaust gas systems should be improved. Smart changes in these areas help melt flow very well. Thorough cavity filling becomes much better with these strategies.
Thinking about my own experience, I recall a time when I designed a complicated toy figure mold. Issues with underfilling kept me awake at night. Changing the gate to line up with the center helped a lot, letting the melt spread evenly everywhere on the figure. This was only the start. Looking into better runner systems and exhaust gas design changed my way of working, taking my designs to a whole new level. Let’s look at these special methods and strategies so you achieve the same success.
Adjusting gate location improves mold filling efficiency.True
Positioning gates near thin-walled areas ensures better melt flow.
Increasing runner length reduces heat dissipation in molds.False
Shorter runners reduce heat loss, improving melt flow efficiency.
- 1. How Does Gate Design Optimization Impact Mold Filling?
- 2. How Does Runner System Design Help Prevent Underfills?
- 3. How can exhaust gas design enhancements improve mold efficiency?
- 4. How Do Breathable Materials Benefit Mold Design?
- 5. How can I effectively address underfill issues in manufacturing?
- 6. Conclusion
How Does Gate Design Optimization Impact Mold Filling?
Have you ever thought about how small details like gate design affect the mold filling process? Learn more to understand why this is important!
Gate design optimization is very important in mold filling. It carefully adjusts the gate’s location, size and number. This balance helps materials flow evenly. This precise tuning reduces defects such as underfilling. Better product quality results from this. Production efficiency probably increases too.
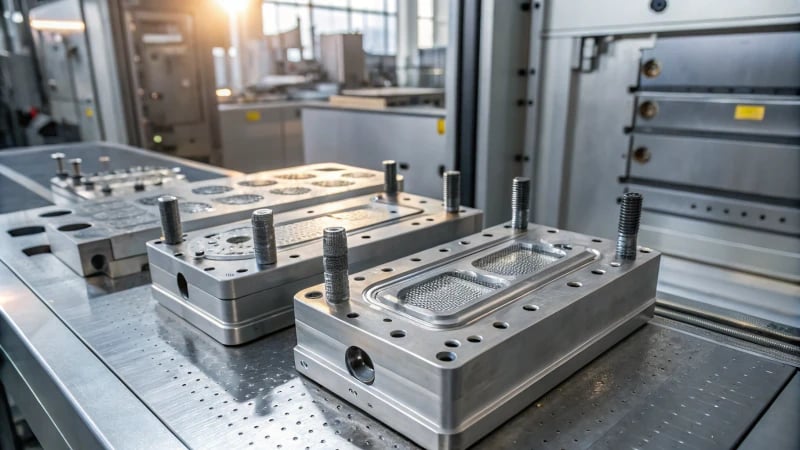
The Importance of Gate Location
I remember my first time with injection molding. I had to design a complicated plastic container. It was a big learning experience! Placing the gate near the handle changed everything. This let the plastic melt1 smoothly into the thin parts, stopping annoying underfills. It’s like pouring pancake batter at just the right angle to avoid spills!
Symmetrical Products
Placing the gate on the symmetry line is important for symmetrical designs, like a plastic toy figure2. This lets material flow evenly on both sides. This way, each part of the toy soldier fills equally. It’s like finding balance in yoga. Everything aligns perfectly.
Gate Size and Number
Working on larger products taught me to change gate sizes. For instance, I needed larger gates for big plastic trays. I increased the gate size from 3mm to 5mm. This allowed faster melt flow. It’s like opening a wider door to let more people into a party quickly!
Product Type | Recommended Gate Diameter |
---|---|
Small Parts | 2-3 mm |
Large Trays | 4-5 mm |
For complex structures, more gates help. Imagine designing a toolbox3. Extra gates near each section ensure every spot gets filled right.
Runner System Improvements
Short runner paths are another trick for better fill efficiency. Less heat loss and resistance make a big change. Polishing runners to a smooth finish also really helps. It’s like sanding a rough surface to make it slide easily.
- Example: Polishing runners to Ra0.8μm resulted in smoother flow and fewer defects in my work.
Exhaust Gas Design
Exhaust systems matter too! Adding exhaust grooves in the right places can stop unwanted air traps. It’s like making sure a room isn’t stuffy, letting air move freely.
In conclusion, designing gates isn’t only about technical details; it involves knowing how changes affect the final product. It’s about learning through experience and sometimes trying different ideas. In the end, it’s about creating products with great precision and care.
Adjusting gate location improves mold filling.True
Placing gates near thin-walled areas ensures even melt flow, reducing underfilling.
Increasing runner diameter decreases melt flow resistance.True
Larger runner diameters allow more melt to pass, enhancing flow efficiency.
How Does Runner System Design Help Prevent Underfills?
Curious about how the design of a runner system could really help or ruin your molding process?
The runner system design plays a key role in preventing underfills during injection molding. The system needs the right runner length, diameter and surface quality. These changes allow the melt to flow smoothly. They reduce defects. This results in better product quality. Quality really improves.
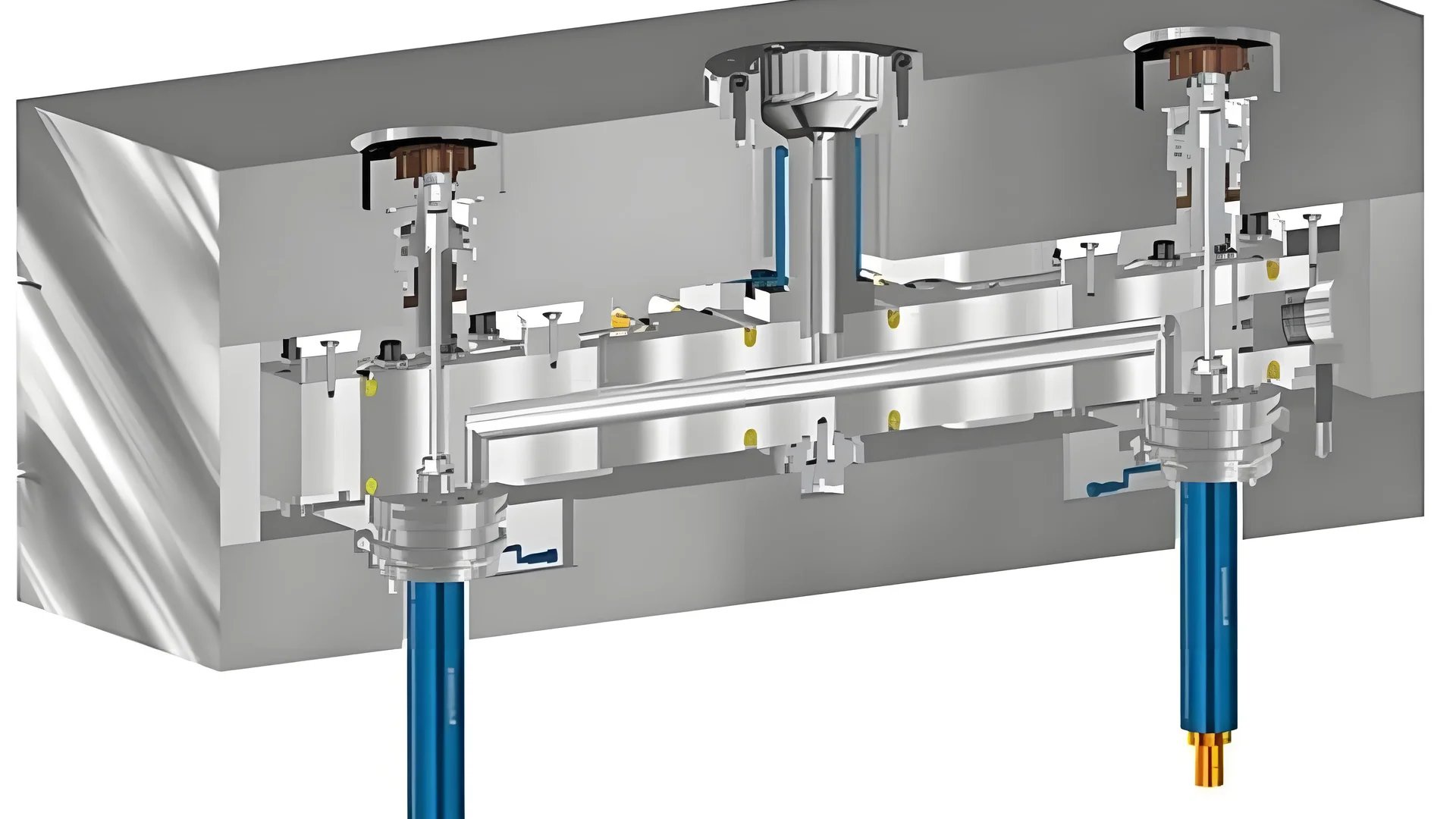
Runner Length and Diameter Optimization
Adjusting Runner Length: I remember my first big project dealing with underfill problems. Shortening the runner length reduced heat loss and melt resistance. It felt like finding a shortcut to get to a destination faster and smoother. Swapping winding, curved runners with straight ones changed everything.
Original Length | New Length |
---|---|
Long & Curved | Short & Straight |
Adjusting Runner Diameter: Runner diameter mattered as well. For a large product with thick walls, increasing the runner diameter allowed the melt to fill the cavity correctly. It was like opening a second lane in busy traffic and letting everything flow.
Surface Quality Improvement
Polishing Runners: Polished runners worked like magic! High-precision polishing reduced friction, which made a difference. It felt like gliding on a freshly waxed floor. Smoother surfaces greatly decreased underfill problems by lowering surface roughness from Ra1.6μm to below Ra0.8μm.
Gate Design Optimization
- Gate Location Adjustment: Designing gate placement proved tricky, much like finding the right spot for a painting. Adjusting gate locations near thin-walled areas or awkward shapes ensured effective filling. When creating a container with a fragile handle, moving the gate closer made a huge difference.
-
Gate Size and Number: For symmetrical products, placing gates on the center line helped balance the melt. Once, while designing a toy figure, placing the gate on the central axis resulted in perfect filling.
Exhaust Gas Design Enhancements
Improving exhaust designs is very important. Adding exhaust grooves or using breathable materials lets air escape in tight spaces, lowering back pressure. It’s similar to letting steam out from a boiling pot to avoid overflow.
Exploring Runner System Types
Knowing different runner systems – hot or cold – is key in improving production processes. Each system has its unique benefits, like choosing between a classic book and its modern version.
Reflecting on these projects shows how small changes bring big progress. Refining details crafts products that are really functional and beautiful.
Adjusting gate location prevents underfilling in complex shapes.True
Positioning gates near thin-walled areas ensures even melt distribution.
Increasing runner diameter reduces melt flow resistance.True
Larger runner diameters facilitate smoother and faster melt flow.
How can exhaust gas design enhancements improve mold efficiency?
Have you ever thought about how changing the design of exhaust systems might really improve mold efficiency?
Changes in exhaust gas design, such as adding exhaust grooves and using breathable materials, greatly increase mold efficiency. These upgrades let trapped air escape, improve how materials move and reduce defects. Better flow means fewer problems.
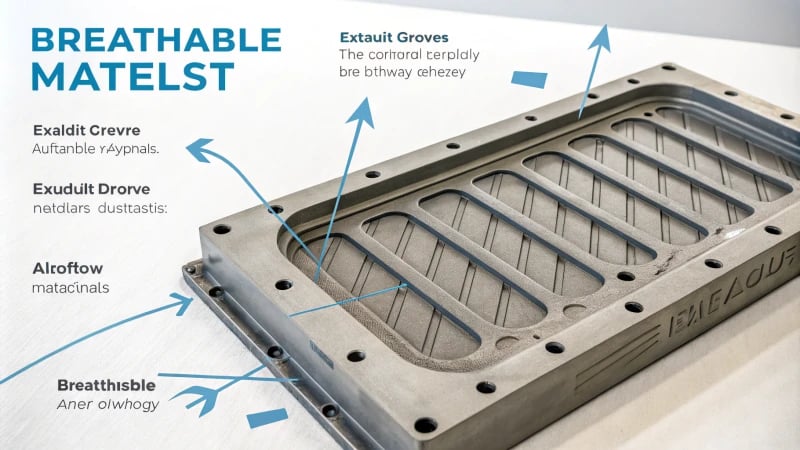
Important Changes in Exhaust Gas Design
1. Adding Exhaust Grooves and Holes
I remember working on a mold design that was very stubborn. It felt like squeezing toothpaste back into its tube. Then I found the power of exhaust grooves. Tiny passages in deep spots helped a lot. For example, a 0.2-0.3mm groove in a plastic shell6 greatly reduced air problems.
Area | Groove Width | Groove Depth |
---|---|---|
Deep cavity | 0.03-0.05mm | 0.2-0.3mm |
Parting surface | 0.3-0.5mm | 0.4mm |
These adjustments ensure the smooth discharge of air, solving underfilling and improving quality.
2. Using Breathable Materials
One time, a mold with complicated internal parts was very frustrating. Using breathable steel was a perfect solution.
This material let air escape easily without harming the mold, resolving underfilling issues nicely.
Especially in molds with complex internal structures7, it solved underfilling problems effectively.
Extra Design Changes
Gate Design Improvement
Improving gate design resembles tuning a violin. Changing gate positions for products with tricky shapes is very helpful.
Place gates near thin areas and plastic flows better, reducing defects and raising quality.
Think about molding a plastic jar with a thin handle – moving the gate near the handle was key!
Better Runner System
Runner systems can be very tricky! Shorter and smoother runners make melt flow better.
At one time, I switched curved runners for straight ones; melt flowed perfectly.
Small changes like this often bring big success in mold performance.
By mixing exhaust changes with other design improvements, like gate and runner changes,
significant improvements in mold efficiency and product quality were achieved.
Adjusting gate location reduces underfilling risk.True
Placing gates near thin-walled areas ensures even melt distribution.
Increasing runner diameter decreases melt flow resistance.True
Larger diameters allow more melt to pass, reducing resistance.
How Do Breathable Materials Benefit Mold Design?
Ever thought about how breathable materials change mold design and production?
Breathable materials in mold design help air move freely. They reduce defects. They improve product quality. Trapped gases escape efficiently. This leads to smoother injection. Production efficiency increases. Less waste occurs. Fewer errors happen.
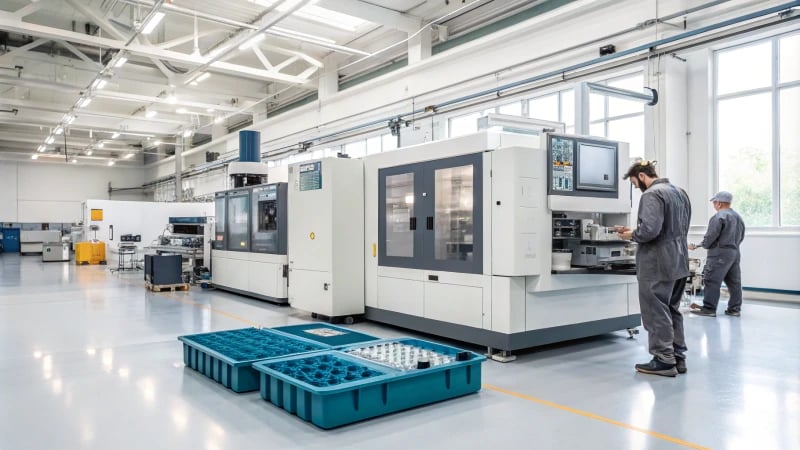
Improving Air Movement with Breathable Materials
I’ve always found it interesting how small changes might create noticeable effects. Take breathable steel8 used in mold design, for instance. This is a revolutionary choice, especially with complex structures where old venting methods fail. Picture working on a task where the mold’s small areas trap air, leading to flaws. Using breathable steel allows air to pass right through the material, helping me achieve perfect venting even in the trickiest designs.
Preventing Flaws and Raising Product Quality
One of my happiest achievements was using breathable materials on a tough project. The client demanded perfect surface finishes with no errors allowed. Breathable materials9 stopped defects like burn marks because they let gases escape easily, keeping the mold cavity in the best state. This meant fewer faulty parts and better quality products. This truly brought joy to my client and me. It was very satisfying.
Streamlining the Injection Process
Ever struggled with a piece that seemed impossible to perfect? I dealt with a product with thin-walled sections that caused lots of troubles. Adjusting the gate design and using breathable materials helped me simplify the injection process. Moving the gate closer to those hard-to-reach areas changed everything, making flow smoother and fills more efficient.
Gate Design Optimization | Description |
---|---|
Adjustment of Gate Location | Enhances filling in thin-walled areas |
Change of Gate Size/Number | Supports complex structures |
This improvement was quite significant.
Boosting Production Efficiency
Using breathable materials in mold design felt like discovering a magic formula for efficiency. Better dynamics led to fewer defects and shorter cycle times. I worked with Jacky’s team on a consumer electronics project where saving even a second was vital. By transforming the runner system – shortening lengths and polishing surfaces – we saw remarkable improvements in production.
These tactics matched perfectly with our aim for high-quality output while cutting costs, aligning well with companies focusing on high-quality consumer electronics components like Jacky’s team does.
Knowing these benefits let me select materials wisely, improving both the function and look of the products I develop. Applying this knowledge has been crucial to achieving successful large-scale productions.
Gate location affects melt flow in complex shapes.True
Adjusting gate location helps fill thin-walled areas efficiently.
Runner length does not impact melt flow resistance.False
Shortening runners reduces resistance and improves filling efficiency.
How can I effectively address underfill issues in manufacturing?
Do you ever think about fixing those annoying underfill problems in electronics manufacturing forever and completely?
To fully solve underfill problems, engineer needs to optimize gate design, improve runner systems and redesign exhaust gas configurations. Gate size and location must be adjusted. Runner dimensions require improvements. Exhausts should sit at effective spots. Seamless production relies on this.
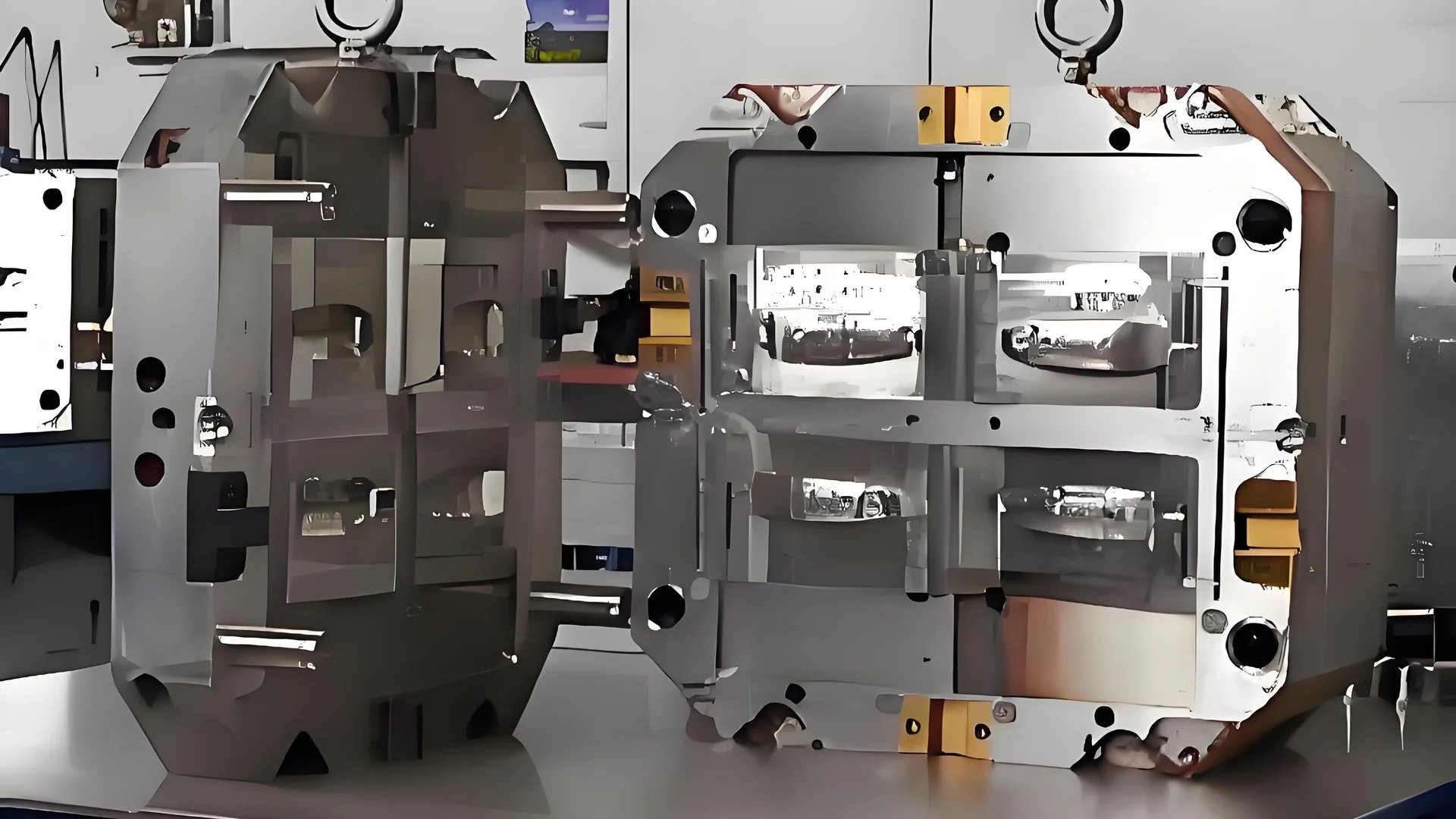
Optimizing Gate Design
Gate design plays a crucial role in successful molding. Adjusting the gate location10 near thin-walled or hard-to-fill areas is essential. For instance, I worked on a complex plastic container with a thin-walled handle. Moving the gate near the handle changed everything, ensuring the material filled smoothly and quickly, saving us many problems.
Scenario | Solution |
---|---|
Complex shapes with thin walls | Move gate close to thin areas |
Larger products | Increase gate size |
Symmetrical products | Set gate on symmetry axis for even melt distribution |
Changing gate size and number brings results. Bigger gates help with larger products, while more gates increase efficiency for complex shapes.
Runner System Improvements
Runner systems also hold great importance. Reducing runner length means less heat loss and resistance. In small molds, a straight runner path improved melt flow dramatically by connecting more directly with the cavity.
Improving runner surface quality by polishing can significantly reduce friction. A smooth path allows material to flow openly, solving underfill problems.
Enhancing Exhaust Gas Design
Exhaust gas design can prevent air entrapment effectively. Increasing exhaust grooves or holes reduces trapped air. Arranging exhaust holes around ejector pins was a major improvement.
Exhaust Enhancement | Example |
---|---|
Deeper cavities or blind holes | Add exhaust grooves of specific depth and width |
Around ejector pins | Set exhaust holes at intervals for air release |
Using breathable materials helps air escape in challenging mold areas, solving many underfill issues by allowing air to escape through the material itself.
These techniques improve more than just underfill problems; they support better manufacturing processes11. They ensure that electronic assemblies remain intact and improve component reliability by mitigating risks associated with thermal expansion mismatches.
By using these strategies, manufacturers create higher-quality products that please our customers every time.
Adjusting gate location improves filling efficiency.True
Placing gates near thin-walled areas reduces melt flow path, enhancing fill.
Increasing runner diameter decreases melt flow resistance.True
Larger runner diameters allow more melt to pass, reducing resistance.
Conclusion
Explore effective solutions for underfill problems in mold design, focusing on gate optimization, runner system improvements, and exhaust gas enhancements to ensure better melt flow and product quality.
-
This link provides insights into how gate location affects melt flow patterns. ↩
-
Explore how symmetry in gate design ensures balanced material distribution. ↩
-
Learn why multiple gates are used for complex mold designs with high flow resistance. ↩
-
This link explores how adjusting gate size and location improves mold filling efficiency, reducing defects. ↩
-
Learn about different runner systems and their benefits to choose the best option for your production needs. ↩
-
Discover how exhaust grooves effectively reduce air compression in plastic molds. ↩
-
Explore how breathable steel aids in venting trapped air in intricate mold designs. ↩
-
Learn how breathable steel solves venting challenges in complex mold designs. ↩
-
Discover how effective venting ensures high-quality surface finishes in molded products. ↩
-
This link provides detailed strategies for optimizing gate locations, crucial for ensuring effective filling in complex designs. ↩
-
Explore comprehensive guides on injection molding best practices to enhance overall manufacturing efficiency and product quality. ↩