Demolding problems can feel like an insurmountable mountain, but I assure you, there’s a way over it!
To solve demolding issues in complex injection molding, manufacturers should optimize mold design, adjust injection processes, improve mold surface quality, and use appropriate demolding mechanisms.
While this brief overview provides a starting point, the detailed insights and expert strategies discussed below offer a comprehensive approach to overcoming these challenges effectively.
Optimizing mold design eases demolding in complex structures.True
Effective mold design reduces friction and prevents product damage during demolding.
How Does Mold Design Affect Demolding in Complex Structures?
Mold design intricately influences the ease of demolding in complex structures, affecting product integrity and production efficiency. Let’s delve into the nuances.
Effective mold design in complex structures ensures easier demolding by optimizing slopes, avoiding difficult structures, and accounting for material shrinkage.
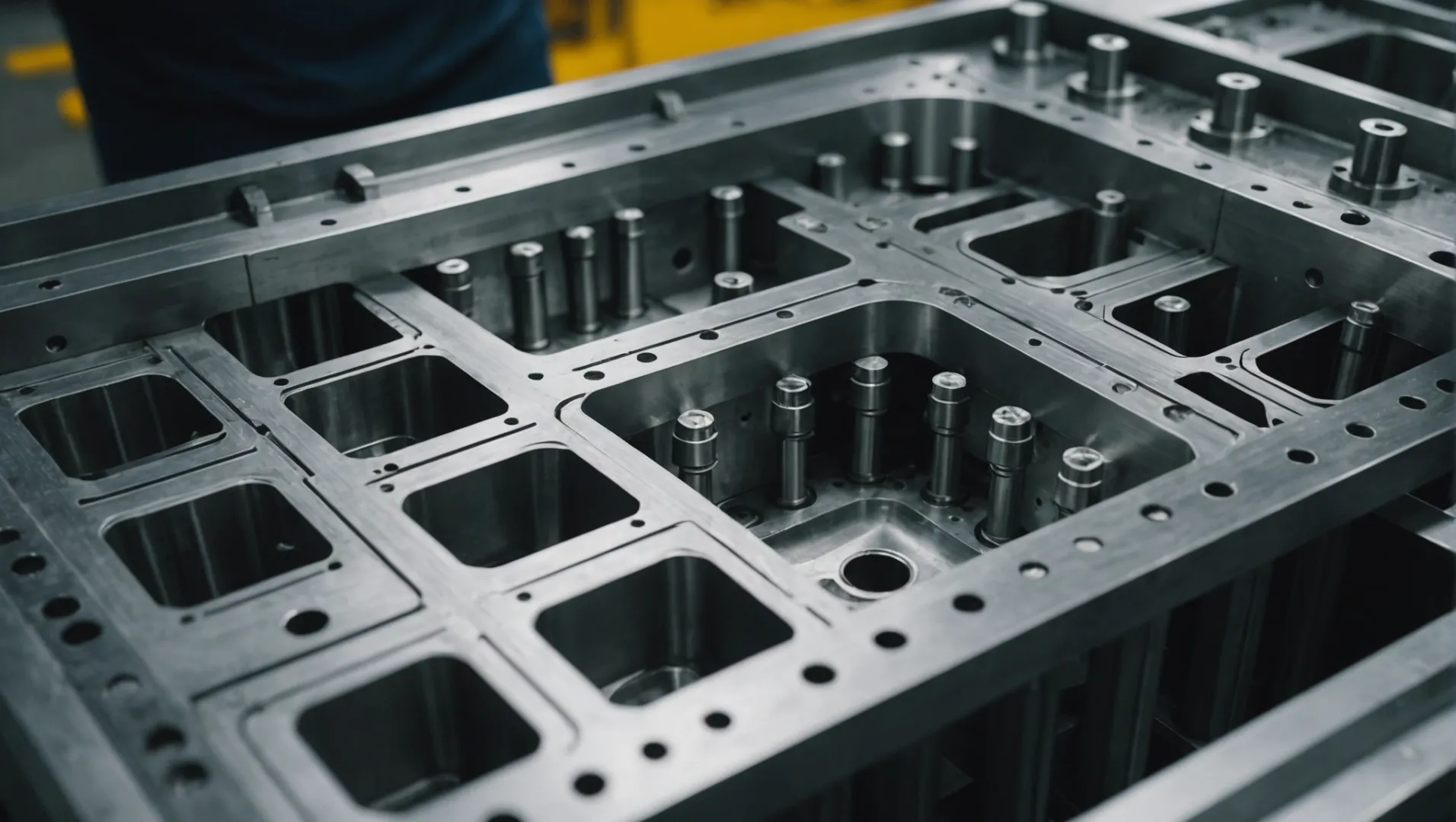
Understanding Mold Design Challenges
The design of a mold directly influences how a product will release during the demolding phase. In complex structures, this becomes even more critical. Some designs fit too snugly against the product, increasing friction and making demolding difficult.
- Deep Cavities and Undercuts: These features can trap the product within the mold, requiring significant force to release, which can damage both the mold and the product.
- Material Shrinkage: As the product cools, it shrinks, often wrapping tightly around mold cores.
Optimizing Mold Design for Better Demolding
To address these issues, several strategies can be implemented:
-
Demolding Slope Optimization
- Increasing the demolding slope generally eases demolding. For intricate designs, the slope must be tailored to the specific complexities of the product.
-
Avoidance of Difficult Structures
- While designing, avoid deep cavities and undercuts where possible. If unavoidable, implement mechanisms like sliders or inclined tops to facilitate easier release.
-
Accounting for Shrinkage
- During the design phase, consider the shrinkage rate of materials. Allocate suitable margins to prevent the product from adhering too tightly post-cooling.
Feature | Challenge | Solution |
---|---|---|
Deep Cavities | Traps product | Use sliders or inclined tops |
Shrinkage | Tight fitting post-cooling | Reserve shrinkage margins |
Balancing Innovation with Practicality
While innovative designs are essential for competitive edge, they must balance with practical considerations for manufacturing efficiency. For instance, innovative mold designs1 should always incorporate a feasibility analysis for demolding processes.
By thoroughly understanding and applying these design principles, manufacturers can significantly reduce common demolding issues like deformation, scratches, and adhesion.
Increasing demolding slope eases product release.True
A greater slope reduces friction and facilitates easier product release.
Deep cavities always improve mold efficiency.False
Deep cavities can trap products, making demolding difficult and inefficient.
What Role Does the Injection Molding Process Play in Demolding Success?
The injection molding process intricately impacts demolding success, influencing product integrity and production efficiency. Discover how strategic adjustments can enhance outcomes.
Successful demolding in injection molding hinges on precise control of process parameters like pressure, speed, and cooling time, ensuring structural integrity and minimizing defects.
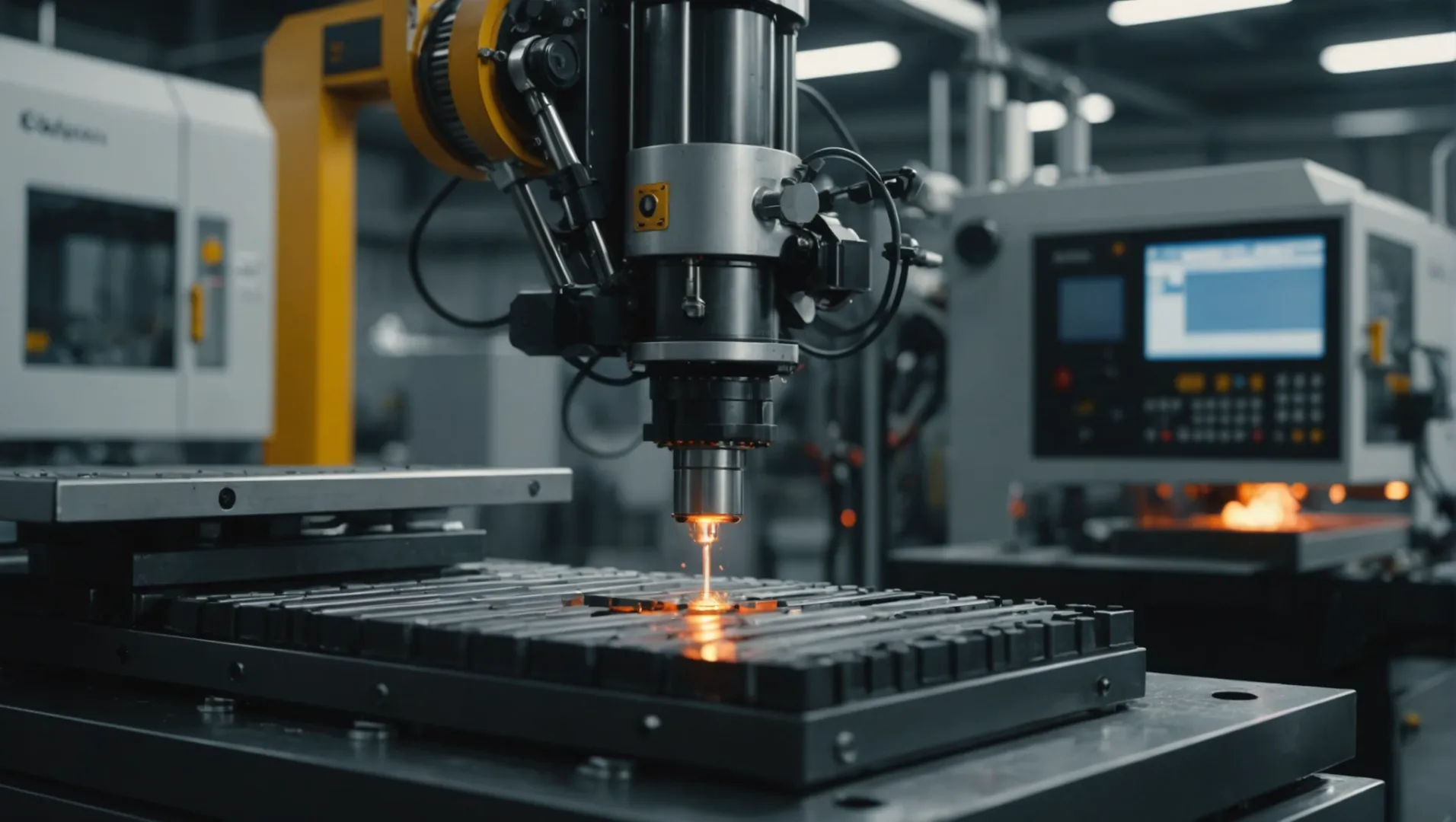
Understanding the Injection Molding Process
The injection molding process involves injecting molten material into a mold cavity, where it cools and solidifies into the final product shape. This process is pivotal in determining the ease and success of demolding, especially for complex structures. The intricacies of this process include parameters such as injection pressure, speed, and cooling time, all of which require meticulous control to achieve optimal results.
Key Factors in the Injection Molding Process
Injection Pressure and Speed
Injection pressure and speed are critical variables that directly influence the stress distribution within the molded product. High pressure can lead to excessive stress, increasing the risk of deformation during demolding. Conversely, reducing pressure and speed helps alleviate internal stresses, thus minimizing potential deformation issues.
For instance, when working with materials that exhibit high shrinkage rates, adjusting these parameters can help prevent the product from becoming tightly wrapped around the mold core. This adjustment reduces friction and force required during demolding, which is vital for maintaining product integrity.
Cooling Time Optimization
Cooling time is another significant factor that impacts demolding success. Allowing adequate cooling time ensures the product fully solidifies, thereby reducing the likelihood of deformation or damage during demolding. Additionally, proper cooling helps manage shrinkage rates, further aiding in smooth demolding.
By extending the cooling period appropriately, manufacturers can ensure that products are less likely to adhere to molds or suffer from scratches and deformations upon removal.
Material Selection and Formula Optimization
Selecting appropriate materials with low shrinkage rates and good fluidity can greatly improve demolding outcomes. By optimizing the material formula, manufacturers can enhance the flow characteristics of the molten material, ensuring even filling of the mold and reducing stress concentrations.
For example, using materials with inherent lubricating properties can decrease friction between the mold and product, facilitating easier demolding.
Conclusion: An Integrated Approach to Demolding Success
In summary, the injection molding process plays a critical role in demolding success by managing variables such as pressure, speed, cooling time, and material selection. Manufacturers can significantly improve demolding outcomes by integrating strategic adjustments into these parameters. For those looking to delve deeper into specific techniques for optimizing these variables, exploring injection molding pressure optimization2 offers valuable insights into achieving successful demolding results.
High injection pressure increases demolding stress.True
High pressure causes excessive stress, risking deformation during demolding.
Cooling time has no impact on demolding success.False
Adequate cooling ensures solidification, reducing deformation risk during demolding.
Why Is Mold Surface Quality Crucial for Problem-Free Demolding?
Mold surface quality plays a pivotal role in the success of demolding processes in injection molding. A well-maintained mold surface ensures smoother demolding, minimizing defects and enhancing product quality.
Mold surface quality is crucial as it directly affects friction, adhesion, and product integrity during demolding. Polished, defect-free surfaces reduce friction, prevent scratches, and facilitate smoother, damage-free product release.
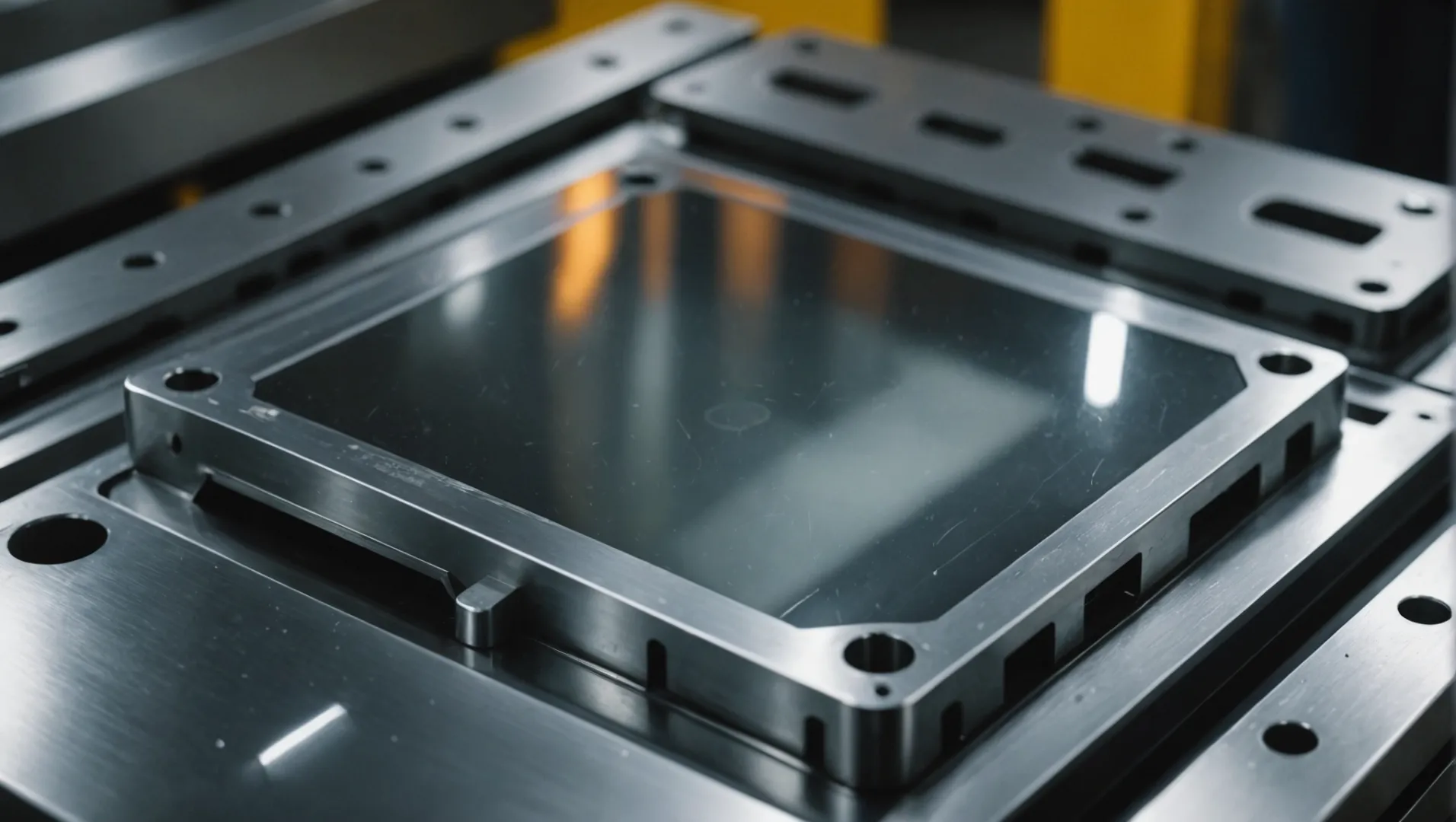
Understanding the Impact of Mold Surface Quality
The quality of the mold surface is often underestimated, yet it profoundly affects the demolding process. A polished mold surface reduces friction between the mold and the product. This is especially important for complex structures, where friction can lead to significant damage or deformation of the product.
Friction Reduction
- A smooth mold surface decreases the force needed to remove the product, thereby protecting delicate parts from breakage.
- Polished surfaces also help in reducing the stress on molds and products during the demolding process.
Adhesion Prevention
- Materials with high affinity to mold materials can stick or adhere, leading to defects like scratches. A well-maintained mold surface can mitigate this issue by reducing adhesion.
- Regular maintenance and use of release agents can keep molds in optimal condition.
Strategies for Enhancing Mold Surface Quality
Polishing Techniques
Polishing the mold is one of the most effective ways to improve its surface quality. It involves:
- Using specialized tools and compounds to achieve a mirror-like finish.
- Regular inspections to identify and address wear and tear before they affect production.
Use of Release Agents
Applying release agents is another strategy to enhance mold surface quality:
- These agents form a barrier between the mold and the product, preventing adhesion.
- It’s crucial to select appropriate agents compatible with both the mold material and the product material.
Routine Maintenance and Repair
Preventative maintenance is key:
- Regular checks for scratches, rust, and other defects ensure that molds remain in top condition.
- Addressing minor issues promptly can prevent more significant problems that could disrupt production.
Real-World Examples of Mold Surface Optimization
Consider an example from the automotive industry where high-volume production requires impeccable mold maintenance. Companies routinely polish molds and apply suitable release agents to maintain high throughput without compromising quality.
These practices are not just limited to automotive; they are prevalent in electronics and consumer goods manufacturing too, where precision and finish are paramount.
By focusing on improving mold surface quality3, manufacturers can ensure smoother demolding processes, reduce waste, and enhance product integrity. Such meticulous attention to detail directly translates into better product quality and higher customer satisfaction.
Polished mold surfaces reduce demolding friction.True
A polished mold surface decreases friction, aiding smoother demolding.
Adhesion is unaffected by mold surface quality.False
Mold surface quality reduces adhesion, preventing defects like scratches.
Which Demolding Mechanisms Are Best for Complex Molded Products?
Selecting the right demolding mechanisms is crucial for maintaining the integrity of complex molded products. Various techniques can be employed to ensure smooth, damage-free demolding.
For complex molded products, employing mechanisms like ejectors, sliders, and inclined ejectors ensures efficient demolding without damaging intricate structures.
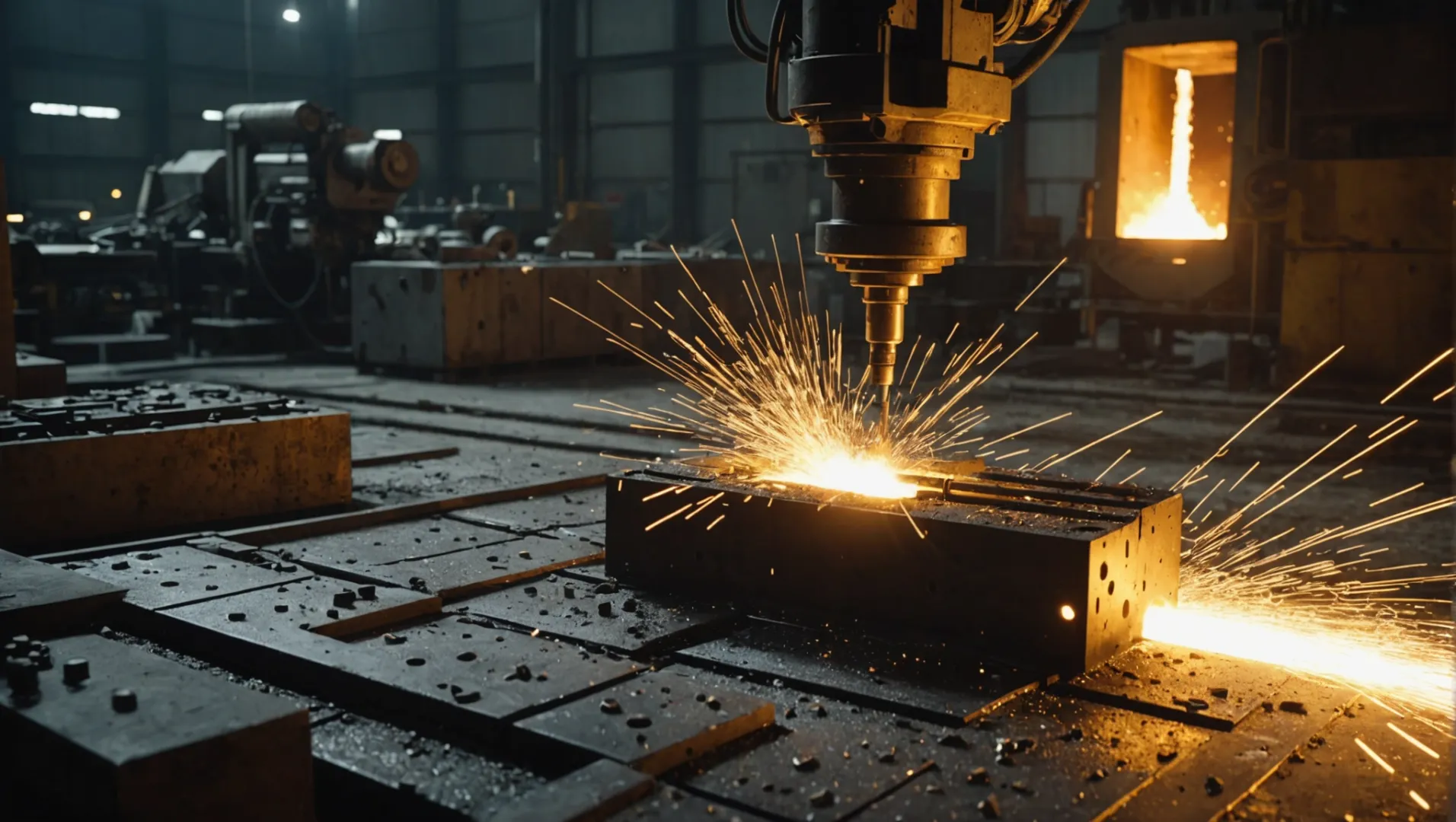
Understanding Demolding Challenges
Demolding complex molded products poses significant challenges due to intricate structures, undercuts, and deep cavities. These complexities require carefully selected demolding mechanisms to prevent damage and ensure production efficiency.
Types of Demolding Mechanisms
-
Ejector Pins
- Function: Ejector pins push the molded part out of the mold.
- Application: Suitable for products with simple geometries.
- Limitation: Can cause deformation if not evenly distributed.
-
Sliders
- Function: Allow parts of the mold to move sideways, releasing undercut areas.
- Application: Ideal for products with complex undercuts.
- Benefit: Reduces the need for post-processing.
-
Inclined Ejectors
- Function: Eject parts at an angle to accommodate complex shapes.
- Application: Used for products requiring angled demolding.
- Advantage: Minimizes surface defects and strain.
-
Push Plates
- Function: Use flat plates to push the entire part out uniformly.
- Application: Beneficial for large, flat products.
- Strength: Ensures even force distribution.
Selecting the Right Mechanism
Choosing the best mechanism depends on the product’s design and material properties. For instance, selecting a demolding mechanism4 that aligns with the structural characteristics of the molded product is critical for maintaining quality and efficiency.
Multi-Point Demolding Techniques
For particularly large or intricate products, employing multi-point demolding can enhance stability and reliability. This approach distributes forces evenly across the product, reducing stress concentrations and potential deformations.
Conclusion
Incorporating appropriate demolding mechanisms requires a deep understanding of the product design and material behavior. By tailoring the mechanism to fit these parameters, manufacturers can achieve efficient demolding while preserving the integrity of complex molded products.
Ejector pins are ideal for complex molded products.False
Ejector pins are more suited for simple geometries, not complex molds.
Sliders reduce the need for post-processing in molded products.True
Sliders allow release of undercut areas, minimizing post-processing.
Conclusion
By implementing these solutions, manufacturers can enhance product quality and production efficiency. Remember, overcoming demolding challenges is within reach!
-
Explore cutting-edge mold designs that simplify complex demolding.: We specialize in plastic injection, thermoset injection, thermoset compression & diecast molds along with custom machining, and contract design & EDM work. ↩
-
Explore strategies to optimize pressure for better demolding outcomes.: Steps to INJECTION MOLDING Process Optimization · 1. Tool functionality examination · 2. Short shot testing · 3. Gate seal studies · 4. Sample parts evaluation/data … ↩
-
Explore practical methods for enhancing mold surfaces to improve production quality.: 1. Polishing and Texturing. Surface finishing is another critical step in improving injection mold quality. Polishing the mold surface helps … ↩
-
Explore how different mechanisms suit various complex designs.: Explore effective demolding techniques in injection molding to enhance product quality, reduce cycle time, and minimize defects in the finished products. ↩