Are you exploring extrusion molding? Knowing its size limits proves important. This knowledge is vital. Believe me, learning this took some hard lessons!
Extrusion molding size limits are dictated by mold design, material properties, and equipment capabilities. Width and thickness are confined by mold size, while excessive thickness can cause warping. Length can be extensive, but depends on equipment and quality control. Complex shapes require innovative mold designs.
As I explored product design, I quickly discovered that extrusion molding has its own quirks. The mold design largely affects the width and thickness of your product. I remember feeling excited about making a wide plastic sheet. My excitement faded when I realized my mold was unsuitable. I also tried crafting a thicker product. Warping issues taught me how important material characteristics are in this process.
Creating long extruded products seems possible, but reality often brings limits. When items become very long, quality control becomes a nightmare. I saw this happen when plastic pipes twisted during production! Extrusion works well for consistent cross-sectional shapes. However, crafting complex forms can lead to frustration. Through trial and error (and some creative mold designs), I learned to push these boundaries. My initial setbacks became stepping stones for better designs.
Extrusion molding has specific size limitations for products.True
The limitations in extrusion molding are influenced by mold design and material characteristics, impacting width, thickness, length, and shape complexity.
Designers can ignore size limits when using extrusion molding.False
Designers must consider size limits in extrusion molding to ensure successful production and functionality of their products.
What Are the Key Factors Influencing Width and Thickness Limits?
Do you ever think about why some products have strict limits on width and thickness? I explore the main reasons for these size rules in manufacturing. I share my own experiences too.
The key factors that influence width and thickness limits include mold design constraints. Material properties impact viscosity and shrinkage. Equipment capacity affects how long production can reach. The complexity of shape impacts dimensional accuracy. Shape complexity is very important.
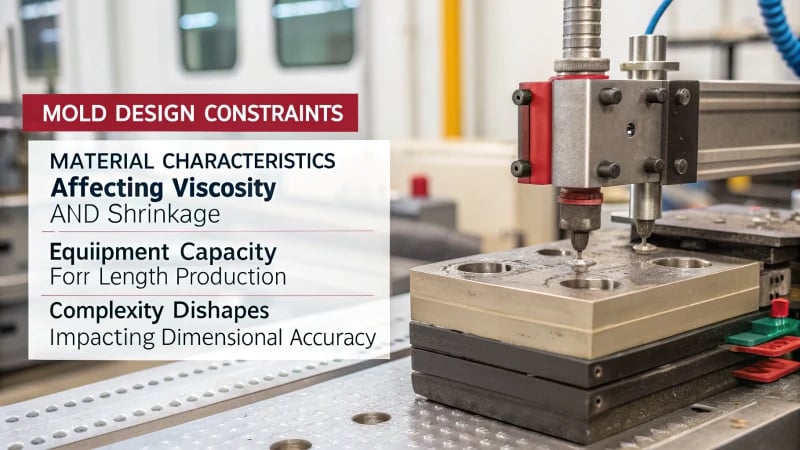
Size Limits in Width and Thickness
When I started with extrusion molding, I felt surprised by how mold design decides what products we get. Picture standing by a sleek machine, dreaming of making a wide plastic sheet. Then, you see the mold’s small opening and realize it’s not possible. It’s like trying to fit a big pizza into a tiny box. Very frustrating! This problem usually comes from the mold’s design. If the opening is small, wide sheets become impossible. Also, products that are very thick face other challenges. I remember a project where we created thick parts and they warped due to uneven stress in the extrusion process. That taught me a lot.
The material choice plays a big role, too. High-viscosity materials need more force to extrude thicker items. Sometimes, this can push machines too hard. In various projects, I observed that even small changes in thickness affected size accuracy. This is especially true for high-precision items. Find more details at material characteristics1.
Thickness Range | Application | Challenges |
---|---|---|
0.1 mm to 10 mm | Plastic sheets | Shrinkage during cooling |
10 mm to 50 mm | Heavy-duty components | Increased extrusion force required |
Size Limits in Length
Now, let’s discuss length – it seemed simple at first but was tricky. In theory, an extruded product’s length could be endless with enough raw material and well-maintained machines. Yet, reality often brings surprises. When making plastic pipes, I noticed very long pipes bending during the pulling process.
This results in:
- Bends or warps
- Quality check problems due to increased length
Length Challenges | Examples | Solutions |
---|---|---|
Deformation | Plastic pipes | Enhanced traction technology |
Winding difficulties | Plastic films | Advanced winding machinery |
Luckily, modern equipment is very advanced. I’ve seen new traction and winding techs help us create thousands of meters of pipe without losing quality. It’s amazing progress! Discover more about advanced extrusion technologies2.
Shape Complexity Restrictions
In my deeper dive into extrusion molding, I found it does well with products that have constant shapes. But complex designs or parts with many internal structures presented big challenges. Extrusion depends on a steady material flow through the die, which complicates achieving complex shapes.
For example:
- Parts with many internal hollows are very hard to make.
- Constant cross-section changes mean frustration in keeping dimension accuracy.
Shape Complexity | Limitations | Alternatives |
---|---|---|
High complexity | Difficult to achieve through extrusion | Consider injection molding |
Frequent changes | Dimensional inaccuracy | Use co-extrusion for multiple materials |
Despite these hurdles, I’ve seen significant advancements like co-extrusion improve both complexity and shape accuracy. This technique lets us extrude several materials at once, opening many design opportunities. It’s truly exciting! See insights on co-extrusion techniques3.
Mold design directly affects extrusion width limits.True
The size of the mold mouth determines the maximum width of extruded products, impacting manufacturing efficiency.
High-viscosity materials can be extruded into any thickness.False
Extruding high-viscosity materials often exceeds machine capacity, limiting achievable thickness.
How Does Length Affect the Quality of Extruded Products?
Have you ever thought about how the length of extruded products truly affects their quality and performance? Let’s explore this fascinating topic together!
The length of extruded products greatly affects their quality. It influences parts like structural strength and defect management. Longer products might encounter issues like bending and deformation. Understanding these dynamics is essential for successful manufacturing.
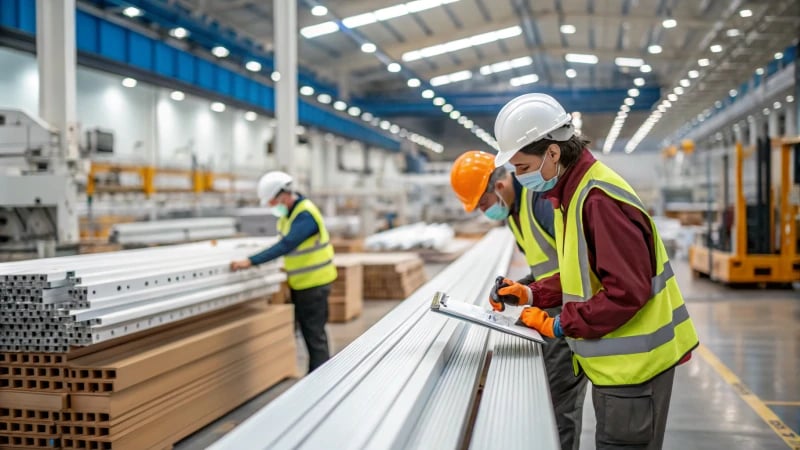
Understanding Length and Its Influence on Extrusion Quality
The length of extruded products plays a significant role in determining their quality and performance.
In theory, extrusion allows for the production of very long items, provided there is enough raw material and the equipment can maintain continuous operation. However, practical challenges arise when producing longer products. One of the primary concerns is bending and deformation during the traction process. For instance, when producing plastic pipes, excessive length can lead to these issues, compromising the structural integrity of the product.
Furthermore, longer products4 face challenges in winding and stacking. Wrinkles and uneven tightness during winding can detract from the quality of extruded films. This is particularly critical for applications where surface smoothness is paramount. As the length increases, so does the complexity of quality control, making defect detection more challenging.
The Equipment’s Role in Length Quality Control
Modern extrusion technology addresses some of these challenges by employing advanced systems for traction and winding. For example, large-scale plastic pipe production lines can produce thousands of meters of pipes effectively.
Equipment Type | Length Capacity | Quality Control Features |
---|---|---|
Standard Extrusion Line | Up to 1000 meters | Basic tension monitoring |
Advanced Pipe Production | Over 5000 meters | Automated defect detection |
High-Precision Film Line | Variable | Real-time quality feedback system |
These advancements help to mitigate the quality issues associated with long extruded products.
Material Properties and Length Limitations
The material being extruded also influences how length affects quality. For high-viscosity materials, longer products may require increased extrusion forces, which can strain equipment. Moreover, cooling and shrinkage become significant factors for longer extrusions, leading to dimensional accuracy challenges.
It’s important to note that while longer products may be desirable in certain scenarios, they also pose risks during handling and transportation. The longer an extruded product is, the more likely it is to encounter issues such as:
- Bending during transport
- Deformation under stress
- Difficulty in storage
The Complexity of Shapes and Lengths
Extrusion is primarily suited for creating products with consistent cross-sectional shapes. Longer items that require complex shapes or features can struggle in terms of production quality. The die design plays a crucial role here; the more intricate the design, the harder it is to maintain consistent quality across longer lengths.
To combat these limitations, techniques such as co-extrusion5 allow for more sophisticated designs by combining materials during the extrusion process. This can potentially enhance the dimensional accuracy of long extruded products.
In summary, while the length of extruded products can theoretically be extended significantly, practical limitations regarding equipment capacity, material properties, and quality control must be taken into account to ensure that the final product meets required specifications. Understanding these factors can significantly influence production outcomes in extrusion processes.
Longer extruded products are more prone to bending and deformation.True
Excessive length in extrusion can lead to structural weaknesses, making products like plastic pipes vulnerable to bending and deformation during traction.
Advanced equipment improves quality control for longer extrusions.True
Modern extrusion technology enhances defect detection and quality management, addressing challenges associated with producing long extruded products effectively.
What Challenges Arise from Shape Complexity in Extrusion?
Did a difficult design challenge ever make you doubt your skills? Product designers like us must really understand shape complexity challenges in extrusion. Let’s explore the actual problems we face in this complex manufacturing process.
Shape complexity in extrusion creates problems like limits on width, thickness and length. These limits affect product quality a lot. Tooling design also suffers from these restrictions, needing attention. Manufacturing processes require very careful planning because of these challenges.
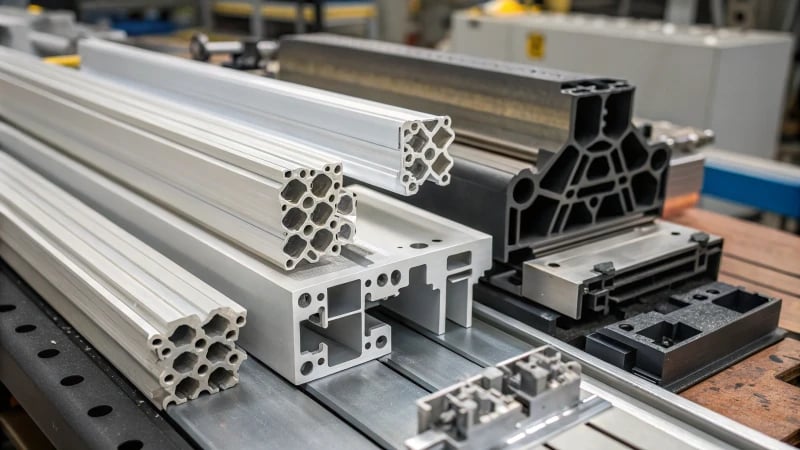
Size Limits in Width and Thickness
In extrusion molding, width and thickness limits often feel heavy on our shoulders. Mold design decides these limits. Sometimes, a small mold opening ruined my plans for a wide sheet. It was very frustrating. Also, thicker products are not just about the material; they may warp or crack due to uneven stress.
Key Factors to Consider:
Factor | Impact on Extrusion |
---|---|
Material Viscosity | Higher viscosity requires more extrusion force. |
Cooling Shrinkage | Thicker products may shrink unevenly. |
Dimensional Accuracy | Greater control needed for high-precision items. |
Size Limits in Length
Extruded products can be very long, limited only by raw material. However, excessive length causes bending and deformation during traction. This happens especially with pipes. Longer products seem useful, yet they make winding and stacking harder, leading to wrinkles and uneven tightness.
Challenges in Length Management:
- Bending during Traction: Longer pipes can bend and deform.
- Winding Troubles: Longer films may wrinkle during winding.
- Checking Quality: Finding defects in long products is complex.
Shape Complexity Limitations
Extrusion molding works best for products with constant cross-sectional shapes. Designing parts with complex shapes shows the limits of die structures. It is hard, especially for parts with hollow spaces or complex branches.
Thoughts on Shape Complexity:
Challenge | Description |
---|---|
Die Structure Limitations | Difficulty in producing complex shapes reliably. |
Dimensional Accuracy | Achieving precision is tougher with complex designs. |
Alternative Technologies | Co-extrusion may help produce more complex shapes. |
New methods like co-extrusion offer some hope. They allow different materials to be extruded together, improving shape complexity – a real breakthrough for us.
For those curious about how shape complexity affects extrusion, explore links like extrusion technology advancements6 or case studies on shape limitations7. These have been precious resources in my path as a product designer.
Extrusion molds limit the width and thickness of products.True
Mold design directly affects the maximum dimensions of extruded items, restricting production capabilities.
Long extruded products are easier to quality inspect.False
Increased length complicates defect detection, making quality inspection more challenging for longer items.
How Can Advanced Techniques Enhance Extrusion Capabilities?
Have you ever thought about how new methods change extrusion processes? These advances solve usual problems. Production becomes smoother. Quality improves.
New methods in extrusion improve capabilities by overcoming size limits in width, thickness and shape complexity. Innovations like co-extrusion and real-time monitoring really help with quality control. These advancements lead to better production efficiency. Production becomes very efficient.
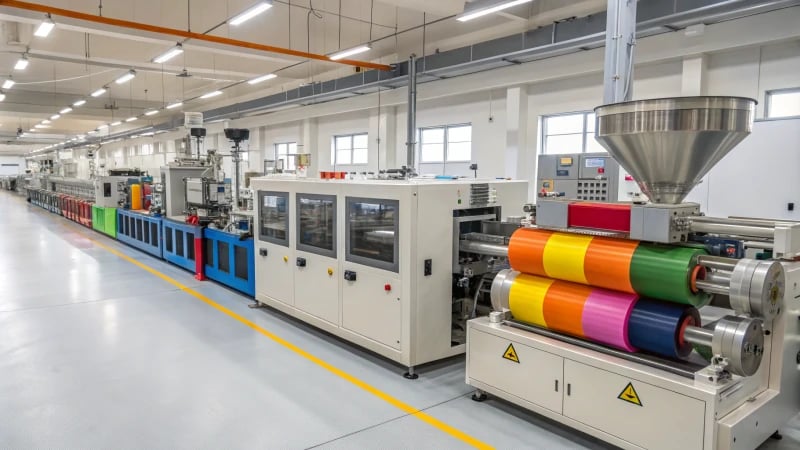
Understanding Extrusion Limitations
Extrusion plays a big role in manufacturing, especially for plastic items. However, it brings its own hurdles. One major challenge was size limits in width and thickness. The mold design controls how wide or thick an extruded product can become. I recall our attempt to create a wider plastic sheet; the narrow mold opening made it impossible. Frustrating, right? Also, thick products warped due to uneven internal stress.
For instance, high-viscosity materials require much more force to push through the extruder. This often pushed our equipment to the edge. Knowing these material characteristics was essential to avoid common extrusion pitfalls.
Length Limitations in Production
You might think there are no limits to the length of extruded products since it’s a continuous process. But that’s not true. Size limitations in length are influenced by equipment capabilities and quality control measures. I remember creating plastic pipes that were too long; they bent and deformed during traction, which hurt quality and stressed our work process.
Aspect | Impact on Production |
---|---|
Length of Product | Can cause bending and deformation |
Quality Control | Becomes increasingly difficult with longer lengths |
Winding Challenges | Wrinkles and uneven tightness may occur |
Modern technology introduced very advanced traction and winding systems that helped solve these troubles. I was amazed when I saw new production lines creating plastic pipes continuously for thousands of meters using innovative technologies.
Shape Complexity Challenges
Challenges grow with shape complexity. Size restrictions on shape complexity mean that extrusion is ideal for products with constant cross-sections, but intricate mold designs are tough. It’s like trying to sculpt clay with just fingers! I felt stuck when facing complex designs needing multiple internal structures.
Then came co-extrusion! This technique allows multiple materials to be extruded at the same time, enhancing both complexity and dimensional accuracy of the final product.
- Co-extrusion Benefits:
- Allows complex designs
- Improves material properties by layering
- Expands application range across many industries
Advanced Techniques Leading to Improved Capabilities
Using advanced techniques has transformed our extrusion abilities. Here are some very helpful methods:
- Computer-Aided Design (CAD) – Optimizes mold design for good performance.
- Real-time Monitoring Systems – Keeps quality control throughout extrusion better.
- Material Science Innovations – New materials with better flow characteristics are available.
- Automation and Robotics – Efficiency really improved and human error greatly decreased in production.
Applying these advanced technologies, I’ve seen firsthand how they not only improve production efficiency but also raise product quality. Embracing innovations in extrusion is crucial to staying competitive in this fast-paced market.
If you’re curious about improving your extrusion abilities further, I very much recommend exploring our resources on advanced techniques8 and material innovations9. They probably make a huge difference!
Extrusion has no practical limits on product length.False
While theoretically unlimited, practical production constraints affect the length of extruded products due to equipment capabilities and quality control measures.
Co-extrusion allows for more complex shapes in extrusion.True
Co-extrusion enables manufacturers to produce intricate designs by layering multiple materials, enhancing dimensional accuracy and complexity.
Conclusion
Learn about the size limits in extrusion molding regarding width, thickness, length, and shape complexity, emphasizing the impact of mold design and material characteristics.
-
Explore this link for insights on how trace width affects PCB performance, ensuring your designs meet industry standards. ↩
-
This resource provides tools for calculating optimal trace widths for various applications, helping you enhance your PCB designs. ↩
-
Find out more about co-extrusion techniques and how they can improve design flexibility in your projects. ↩
-
Explore how different lengths impact extrusion quality; gain insights that could enhance your manufacturing processes. ↩
-
Learn about co-extrusion methods that improve product design flexibility and quality over longer lengths. ↩
-
This link provides insights into advanced technologies that can help mitigate the challenges of shape complexity in extrusion processes. ↩
-
This resource offers case studies that detail practical examples of overcoming shape complexity challenges in extrusion. ↩
-
This link provides insights on innovative extrusion techniques that can greatly enhance manufacturing processes and efficiency. ↩
-
Explore the latest advancements in materials used for extrusion to improve product quality and efficiency. ↩