Diving into the world of injection molding can be like navigating a maze, especially when choosing between single and multi-cavity molds.
Single cavity molds produce one product per cycle, perfect for small-batch, high-precision needs. Multi-cavity molds make several products per cycle, enhancing efficiency for large-scale production.
Every time I delve into injection molding decisions, it’s like embarking on a new adventure. The choice between single and multi-cavity molds feels crucial, almost like picking the right path in a storybook. Understanding how each mold type affects output, quality, and strategy can be the key to unlocking successful production outcomes.
I remember working on a project where precision was paramount. The single cavity mold was my go-to because it allowed me to focus on every tiny detail, ensuring the highest quality for a complex product. But when faced with high-demand projects, multi-cavity molds became my allies, churning out products like magic. Each choice carries its own story, dictated by the needs of the moment.
Single cavity molds are best for large-scale production.False
Single cavity molds are ideal for high-precision, small-batch production.
Multi-cavity molds increase production efficiency.True
They produce multiple products per cycle, enhancing manufacturing speed.
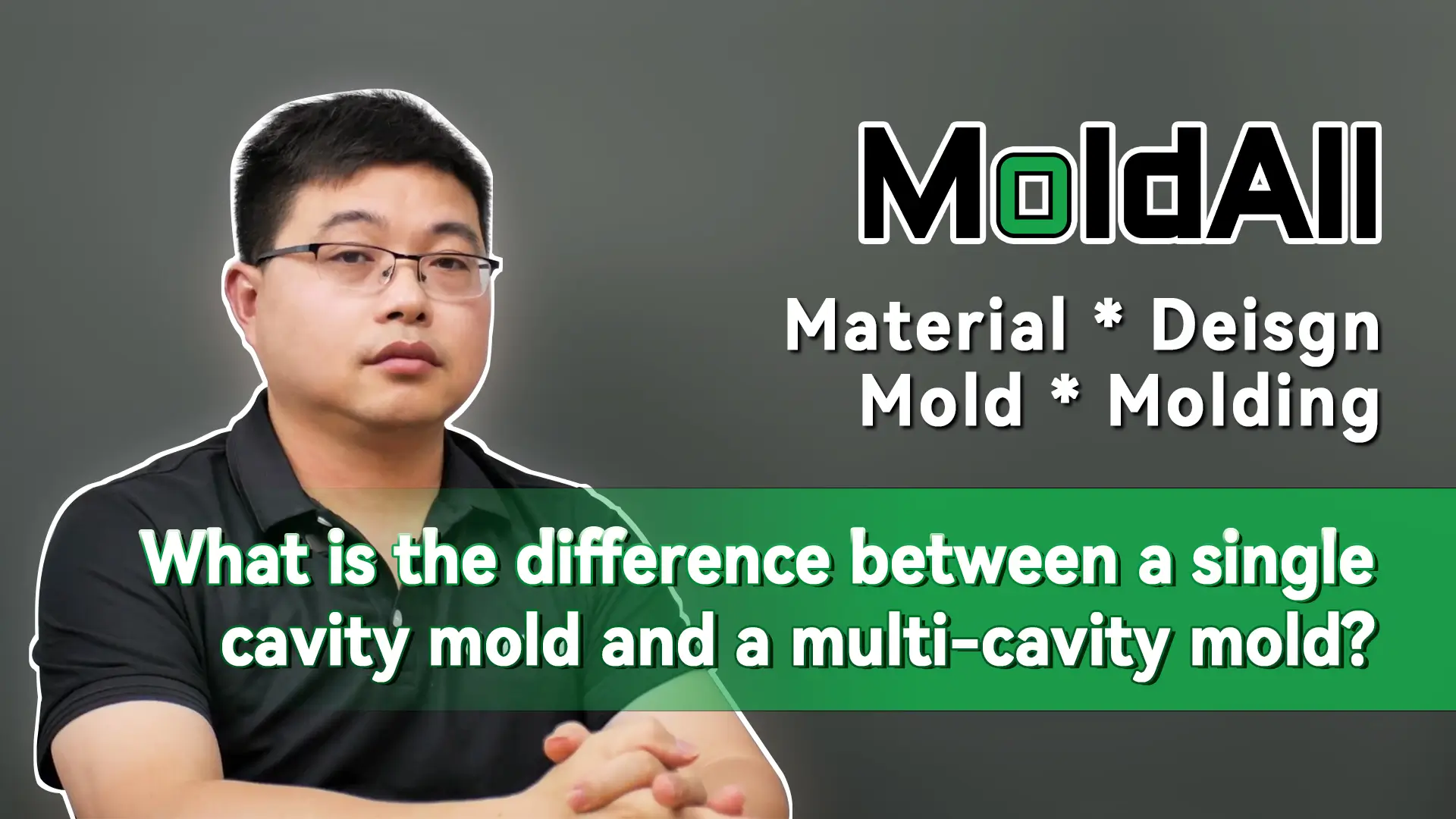
- 1. What Are the Production Capabilities of Single and Multi-Cavity Molds?
- 2. How Do Mold Size and Complexity Influence Production Decisions?
- 3. Why is product quality control different between mold types?
- 4. How Does the Cost of Molds Affect Manufacturing Choices?
- 5. Which Mold Type Fits Your Production Needs Best?
- 6. Conclusion
What Are the Production Capabilities of Single and Multi-Cavity Molds?
Ever wondered how single and multi-cavity molds shape the world of manufacturing? Dive into the intricacies of these mold types and discover which one suits your production goals.
Single-cavity molds create one item per cycle, perfect for precision tasks, while multi-cavity molds deliver multiple identical items per cycle, ideal for mass production. Both have unique benefits tailored to specific manufacturing needs.
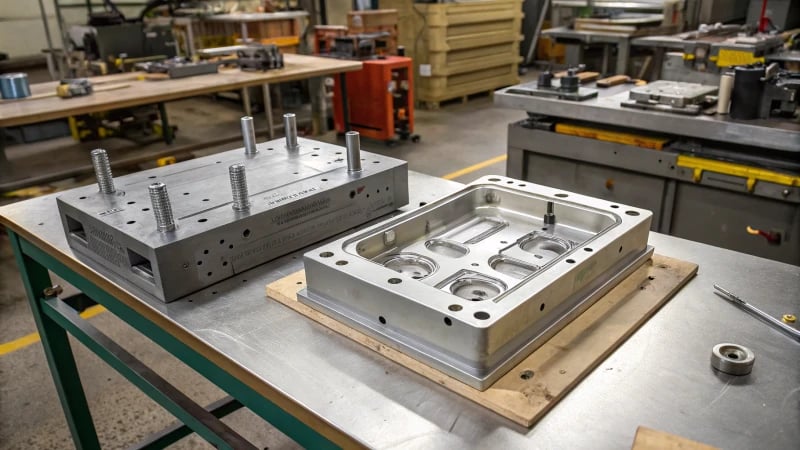
Number of Cavities and Product Output
Whenever I’m faced with a decision about which mold to use, I think back to a time when I needed to choose between precision and quantity. It was like picking between a handcrafted masterpiece and a batch of perfectly identical replicas.
Single Cavity Molds: Imagine having only one shot at making something perfect—like crafting a large aircraft wing1. These molds are ideal for such precision tasks, creating one product per cycle. It’s like putting all your eggs in one basket but knowing that basket is expertly crafted.
Mold Type | Cavities | Output Per Cycle |
---|---|---|
Single Cavity Mold | 1 | 1 Product |
Multi-Cavity Molds: On the flip side, when I need to churn out multiple products quickly—like plastic bottle caps2—multi-cavity molds come to the rescue. They turn each injection cycle into a mini assembly line, producing several identical products at once. It’s like having a magical machine that clones your favorite items instantly.
| Multi-Cavity Mold | 2 or more| Multiple Products|
Mold Sizes and Complexity
The complexity and size of molds often remind me of assembling intricate puzzles. Each piece needs to fit perfectly, or the whole picture doesn’t come together.
Single Cavity Mold: These molds are the simpler puzzles, with fewer pieces to manage. They’re usually smaller, making them easier to design and manufacture. Consider a mold for a silicone cell phone holder3; simplicity is key here.
Multi-Cavity Molds: These are the 1,000-piece puzzles. Their larger size and complexity ensure that plastic is evenly distributed across all cavities, requiring a meticulous approach to design.
Product Quality Control
Quality control can feel like playing a game of Jenga—one wrong move, and everything can fall apart.
Single Cavity Molds: With these, quality control is straightforward since you’re only managing one product per cycle. It’s like focusing on perfecting a single dish for dinner.
Multi-Cavity Molds: Here, ensuring consistent quality is more challenging. It’s about maintaining balance across multiple items, much like hosting a dinner party where every dish needs to be equally delicious.
Mold Cost and Suitability
The financial aspect of choosing molds feels like budgeting for a vacation—balancing cost with experience.
Mold Type | Initial Cost | Cost Per Product | Best For |
---|---|---|---|
Single Cavity Mold | Low | High | Small batches, precision needs |
Multi-Cavity Mold | High | Low | Mass production |
Single Cavity Molds: Think of these as your budget-friendly travel options—great for small trips or when you’re just testing the waters.
Multi-Cavity Molds: Although they require a bigger initial investment, they pay off in mass production scenarios. It’s like investing in an all-inclusive resort for maximum enjoyment with minimal fuss.
By understanding these nuances, I’ve learned to tailor my mold choices to fit the specific needs of each project, optimizing both production and efficiency.
Single cavity molds are best for mass production.False
Single cavity molds are ideal for precision, not mass production.
Multi-cavity molds require more complex design than single cavity molds.True
Multi-cavity molds need intricate design to ensure even distribution.
How Do Mold Size and Complexity Influence Production Decisions?
Ever wondered how something as simple as mold size can make or break your manufacturing game plan?
Mold size and complexity shape production by affecting efficiency, cost, and quality. Single cavity molds offer precision and ease, while multi-cavity molds boost output and consistency, though they bring increased complexity and cost.
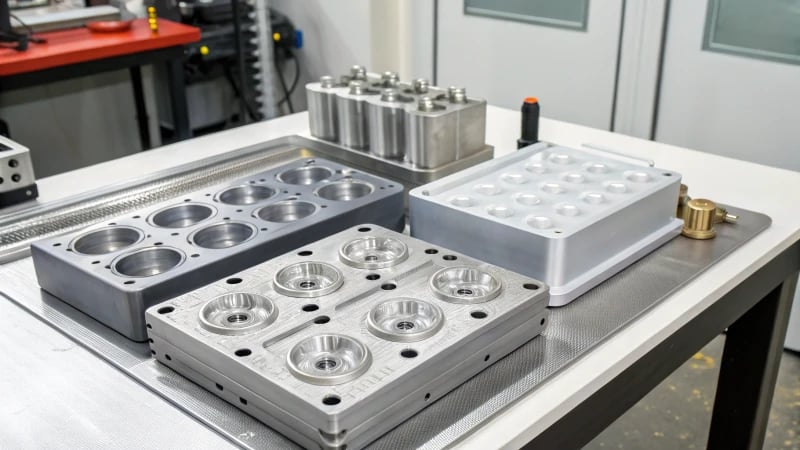
The Role of Mold Size in Production
Mold size isn’t just about fitting a product; it’s about setting the pace of production. A larger mold, like a multi-cavity one, lets you churn out multiple items at once, ramping up efficiency. Think of it like a busy bakery churning out dozens of cupcakes in one go compared to the meticulous care of crafting a single, exquisite cake.
For example:
Mold Type | Number of Cavities | Product Output |
---|---|---|
Single Cavity | 1 | Lower output, high precision |
Multi-Cavity | 8-16 | Higher output, consistent |
Understanding Mold Complexity
The complexity of a mold can feel like solving a puzzle. I’ve spent countless hours grappling with design intricacies, especially when working on multi-cavity molds. They demand precision to ensure each product turns out identical. It’s like creating an orchestra where every instrument must play in perfect harmony—one wrong note and the melody is off.
Complexity in molds is often dictated by the number of cavities and the intricacies of the product design. A single cavity mold generally has a simpler design suitable for products needing high precision, like an optical lens4. Conversely, multi-cavity molds require meticulous design to ensure uniformity across all products.
Balancing Quality and Quantity
When I’m using single cavity molds, I appreciate the control they offer. I can tweak every little detail to achieve perfection, which is crucial for high-precision items. However, with multi-cavity molds, it’s a dance of maintaining uniformity across the board. This requires sophisticated controls to keep quality consistent.
Single cavity molds allow precise control over production parameters, enhancing product quality. In contrast, multi-cavity molds may face challenges in maintaining quality consistency across all products. This necessitates sophisticated process controls and design optimization5.
Cost Implications
Costs are always top of mind in manufacturing. Single cavity molds are like that entry-level job—you start small with fewer resources. But as you scale up to multi-cavity molds, you’re investing more upfront. However, they become cost-effective giants in mass production scenarios.
The cost of mold manufacturing is closely tied to its size and complexity. Single cavity molds are cheaper to produce but may incur higher costs per unit in mass production. Multi-cavity molds, though costly to design and manufacture initially, offer cost-effective solutions in large-scale production.
Strategic Suitability
Deciding between single or multi-cavity molds is like choosing between a solo artist or a band. Multi-cavity molds are your go-to for high-demand smaller products—imagine mass-producing plastic bottle caps. On the flip side, single cavity molds shine when precision is paramount, like crafting an aircraft wing.
Choosing between single or multi-cavity molds depends on production needs. Multi-cavity molds suit high-demand scenarios with small product specifications whereas single cavity molds are ideal for trial productions or high-precision requirements.
For instance, a plastic bottle cap6 may use a multi-cavity mold for mass production while an aircraft wing might require a single cavity due to its size and precision demands.
Understanding these nuances has been key for me in making decisions tailored to each project’s unique needs. Just like choosing the right tool for the job ensures success selecting the right mold type can elevate a manufacturing process from good to great.
Larger molds increase production efficiency.True
Larger molds, like multi-cavity ones, allow simultaneous production of multiple items.
Single cavity molds are costlier for mass production.True
Single cavity molds incur higher per unit costs despite lower initial manufacturing expenses.
Why is product quality control different between mold types?
Ever wondered why some molds demand more attention than others when it comes to quality control?
Product quality control differs between mold types due to the variations in cavity numbers, mold sizes, and complexities. Single-cavity molds offer precise control, ideal for high-precision items, while multi-cavity molds require careful design to ensure uniformity across multiple products.
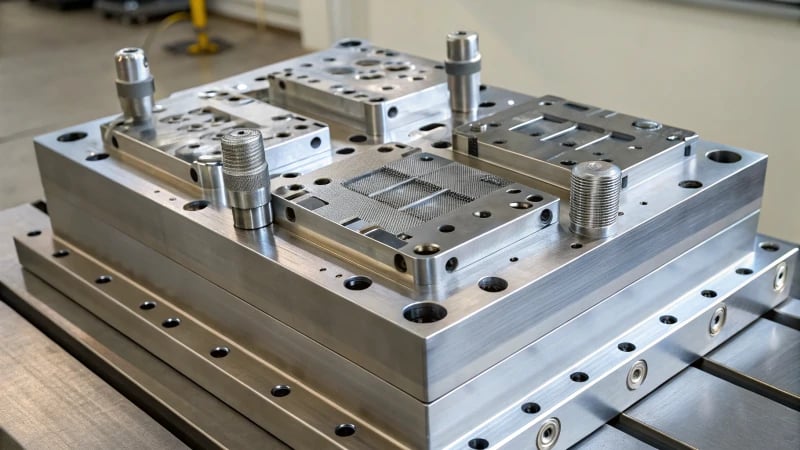
Influence of Cavity Numbers on Quality Control
When I first started working with molds, I was amazed by how the number of cavities could change the game in production. With a single-cavity mold, I learned to appreciate the art of precision. Each cycle produces just one product, which means I could tweak every detail—temperature, pressure, and timing—to ensure perfection. This is exactly what you’d want when creating something like an optical lens where every tiny flaw matters.
In contrast, multi-cavity molds were a different beast altogether. I remember my first attempt at using one to produce multiple parts at once—it felt like juggling, trying to keep everything uniform. The challenge was to maintain consistent quality across each cavity because if one was slightly off, it could lead to a whole batch of imperfect products. That’s why these molds require such meticulous planning and execution.
Mold Type | Quality Control Focus |
---|---|
Single-Cavity | Precision, Parameter Control |
Multi-Cavity | Uniformity, Design Complexity |
Size and Complexity’s Role in Quality Control
The size and complexity of a mold also play significant roles in quality control. I remember designing a single-cavity mold for a simple silicone phone holder. It was relatively straightforward, with fewer variables to consider—just a clean, uncomplicated path from design to production.
But then came the multi-cavity molds, which were like a puzzle waiting to be solved. Ensuring even melt distribution and consistent cooling was key. I had to dive into advanced engineering7 techniques to prevent issues like warping or inconsistent dimensions. It was challenging but rewarding to see everything come together seamlessly.
Cost Implications and Suitability
Initially, I thought that single-cavity molds would always be the cheaper option. And they are, in terms of manufacturing costs—fewer materials and simpler processes. However, when it comes to large-scale production, these molds can turn out to be less cost-effective due to their lower efficiency. They’re perfect for small batches or prototypes where quality can’t be compromised.
In contrast, multi-cavity molds come with a heftier price tag upfront due to their complexity. But once they’re set up, they can produce products en masse at a much lower cost per unit. This is ideal for mass production scenarios like making plastic bottle caps where consistency and volume are crucial.
Mold Type | Cost Efficiency | Suitability |
---|---|---|
Single-Cavity | Lower initial | Small batch/prototypes |
Multi-Cavity | Higher initial | Mass production |
Process Control Challenges
Multi-cavity molds present unique challenges in maintaining quality control. I’ll never forget the first time I had to ensure that each cavity received the same melt pressure and temperature—it felt like managing a finely tuned orchestra. Any variation could result in inconsistencies across products.
Single-cavity molds allowed me more precise adjustments, mitigating many of these issues. Yet optimizing multi-cavity systems often required advanced process controls and sometimes iterative adjustments to hit that sweet spot8 of desired quality standards. This journey taught me the value of patience and precision in manufacturing.
Single-cavity molds offer better precision control.True
Single-cavity molds allow detailed control over parameters, enhancing precision.
Multi-cavity molds are cheaper to manufacture.False
Multi-cavity molds have higher initial costs due to complex design needs.
How Does the Cost of Molds Affect Manufacturing Choices?
Ever wondered how the cost of molds shapes the choices we make in manufacturing?
Mold costs significantly impact manufacturing choices by dictating production volume, efficiency, and quality. Single-cavity molds are more economical for smaller batches, while multi-cavity molds lower the cost per unit in mass production, optimizing efficiency and maintaining product quality.
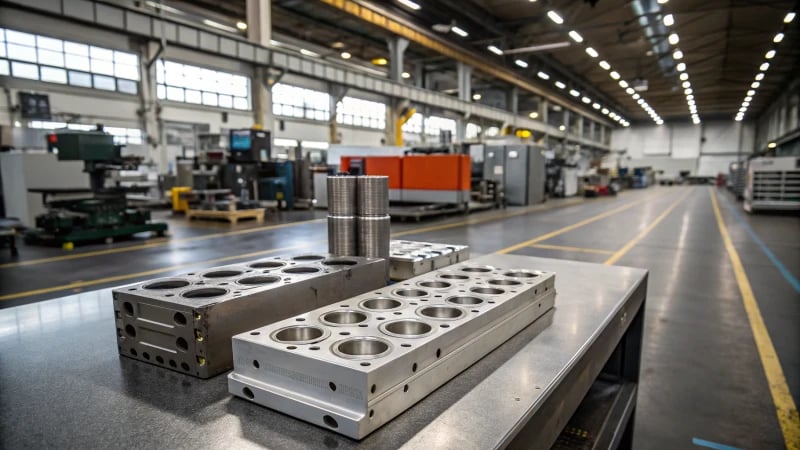
Understanding Mold Costs
Mold costs are a substantial part of manufacturing budgets. They influence whether to use single-cavity molds9 or multi-cavity molds. Single-cavity molds are simpler and cheaper, ideal for small batches or complex products needing high precision.
Mold Type | Features | Cost Implications |
---|---|---|
Single-Cavity | Simple, cheaper | Higher cost per unit in mass production |
Multi-Cavity | Complex, costly | Lower cost per unit in mass production |
Production Volume and Efficiency
In large-scale production, multi-cavity molds are preferred because they produce more units per cycle. This efficiency reduces costs per product, making them ideal for high-demand scenarios like plastic bottle caps10.
Impact on Product Quality
Quality control is more manageable with single-cavity molds as they allow precise control of injection parameters. This is crucial for products like high-precision optical lenses. Conversely, multi-cavity molds may introduce inconsistencies across cavities, necessitating advanced design and process control.
Design Complexity and Material Choices
The complexity of the mold design impacts costs significantly. Multi-cavity molds require intricate designs to ensure even distribution of plastic melt and consistent cooling, as seen in a 16-cavity toy mold. Material choice, such as steel or aluminum, also affects both cost and suitability for certain products.
Selecting the right mold type involves balancing initial mold costs against long-term production savings. Each decision should consider product demand, complexity, and quality requirements to optimize manufacturing11.
Single-cavity molds are cheaper than multi-cavity molds.True
Single-cavity molds have simpler designs, reducing manufacturing costs.
Multi-cavity molds increase quality control precision.False
Multi-cavity molds can introduce inconsistencies, complicating quality control.
Which Mold Type Fits Your Production Needs Best?
Navigating the world of mold types feels like an art form, doesn’t it? Whether you’re crafting a single masterpiece or churning out thousands, choosing the right mold is pivotal.
Choosing between single-cavity and multi-cavity molds hinges on your production goals. Single-cavity molds excel in precision for smaller batches, while multi-cavity molds boost efficiency in large-scale production.
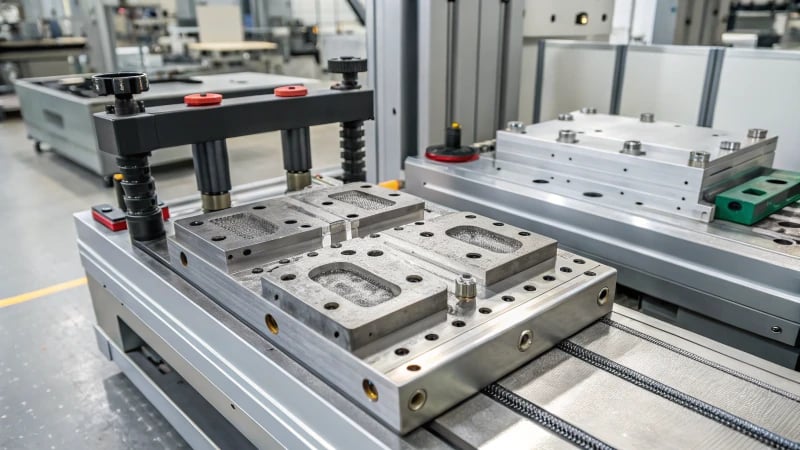
Analyzing Production Volume and Efficiency
I remember the first time I had to decide between mold types for a project. It was like standing at a crossroads, each path leading to a different future for the production line. For low-volume or trial runs, single-cavity molds are the clear choice. They produce one item per cycle, making them perfect for meticulous projects where precision trumps speed. Picture crafting a prototype for a cutting-edge gadget; you want every detail to be perfect before scaling up.
On the flip side, if you’re like me and love the thrill of mass production, multi-cavity molds are your best bet. These molds can churn out several items simultaneously, skyrocketing efficiency. Imagine a factory floor buzzing with activity as thousands of bottle caps roll out effortlessly—it’s a sight to behold.
Mold Type | Production Volume | Efficiency |
---|---|---|
Single-Cavity | Low | Low |
Multi-Cavity | High | High |
Understanding Mold Complexity and Design
The complexity of mold design can feel overwhelming, but it’s a fascinating challenge. Single-cavity molds are relatively straightforward. They’re ideal when the design needs to be just right, like crafting a large or intricate product. I once worked on a project that required the utmost precision, and the simplicity of a single-cavity mold was a lifesaver.
In contrast, multi-cavity molds demand careful planning. You have to ensure every cavity is evenly filled and cooled, which sounds daunting but is incredibly rewarding when done right. The process reminds me of solving an intricate puzzle—every piece must fit perfectly to create a seamless whole.
Quality Control Considerations
Quality control is where single-cavity molds shine. With one product per cycle, it’s easier to fine-tune the injection parameters to achieve perfection. I recall working on a high-precision optical lens where every detail had to be flawless. Single-cavity molds made this possible.
Multi-cavity molds, however, require a delicate balance. Ensuring consistent quality across multiple products is no small feat. It’s like orchestrating a symphony where every instrument must play in harmony, and when it does, the result is nothing short of spectacular.
Explore quality control techniques12 in injection molding for further insights into maintaining product standards.
Balancing Cost and Suitability
Cost considerations can heavily influence your decision. Single-cavity molds are less expensive to manufacture but may not be cost-effective for mass production due to lower output rates. They’re perfect for small batches or new product development phases where quality is paramount.
Meanwhile, multi-cavity molds come with higher upfront costs but pay off in large-scale operations by spreading costs over more units. I’ve seen firsthand how this can drastically reduce production costs, making them ideal for scenarios demanding high product volumes and consistency.
Mold Type | Initial Cost | Cost-effectiveness (Mass Production) |
---|---|---|
Single-Cavity | Low | Low |
Multi-Cavity | High | High |
Understanding these elements can guide you in choosing the right mold type for your production context. Dive deeper into mold design principles13 to enhance mold efficiency and functionality.
Single-cavity molds are ideal for mass production.False
Single-cavity molds are better suited for low-volume production due to their lower output.
Multi-cavity molds have higher initial costs than single-cavity molds.True
Multi-cavity molds require more complex design, increasing initial costs compared to single-cavity molds.
Conclusion
Single cavity molds excel in precision for small batches, while multi-cavity molds enhance efficiency for mass production. Each type has unique benefits tailored to specific manufacturing needs.
-
Discover how single-cavity molds are employed in aerospace applications demanding high precision. ↩
-
Explore how multi-cavity molds enhance efficiency in producing common items like bottle caps. ↩
-
Learn why single-cavity molds are preferred for simple items with quick manufacturing needs. ↩
-
Learn about the precision benefits of single cavity molds in lens production. ↩
-
Discover how advanced controls maintain quality in multi-cavity molds. ↩
-
Understand why multi-cavity molds are chosen for high-volume items like caps. ↩
-
Discover advanced engineering methods used to design intricate multi-cavity molds. ↩
-
Learn about common issues faced in ensuring consistent quality across multiple cavities. ↩
-
Explore why single-cavity molds are beneficial for small batch production and high-precision needs. ↩
-
Discover how multi-cavity molds enhance production efficiency, particularly for high-volume items like bottle caps. ↩
-
Learn about effective strategies to balance mold costs with production efficiency. ↩
-
Discover effective quality control methods that ensure consistent product quality in injection molding. ↩
-
Gain insights into advanced mold design principles that improve efficiency and product quality. ↩