Have you ever wondered how those sleek, flexible silicone products are made? Let’s dive into the fascinating world of silicone injection molding!
Silicone injection molding is a process where liquid silicone is injected into a mold to create products. It leverages the material’s fluidity and vulcanization under heat to transform into solid shapes, ensuring high precision and efficiency.
While the basics are simple, the depth of silicone injection molding is truly remarkable. Join me as we explore its intricate processes, advantages, and diverse applications!
Silicone injection molding uses liquid silicone rubber.True
Liquid silicone rubber is the primary material in silicone injection molding.
What Materials are Used in Silicone Injection Molding?
Silicone injection molding relies on specific materials that enhance the precision and versatility of the process. Discover what these materials are and their unique roles.
The primary materials used in silicone injection molding include liquid silicone rubber, vulcanizers, catalysts, pigments, and fillers. These materials are selected based on the desired properties of the final product, such as flexibility, durability, and color.
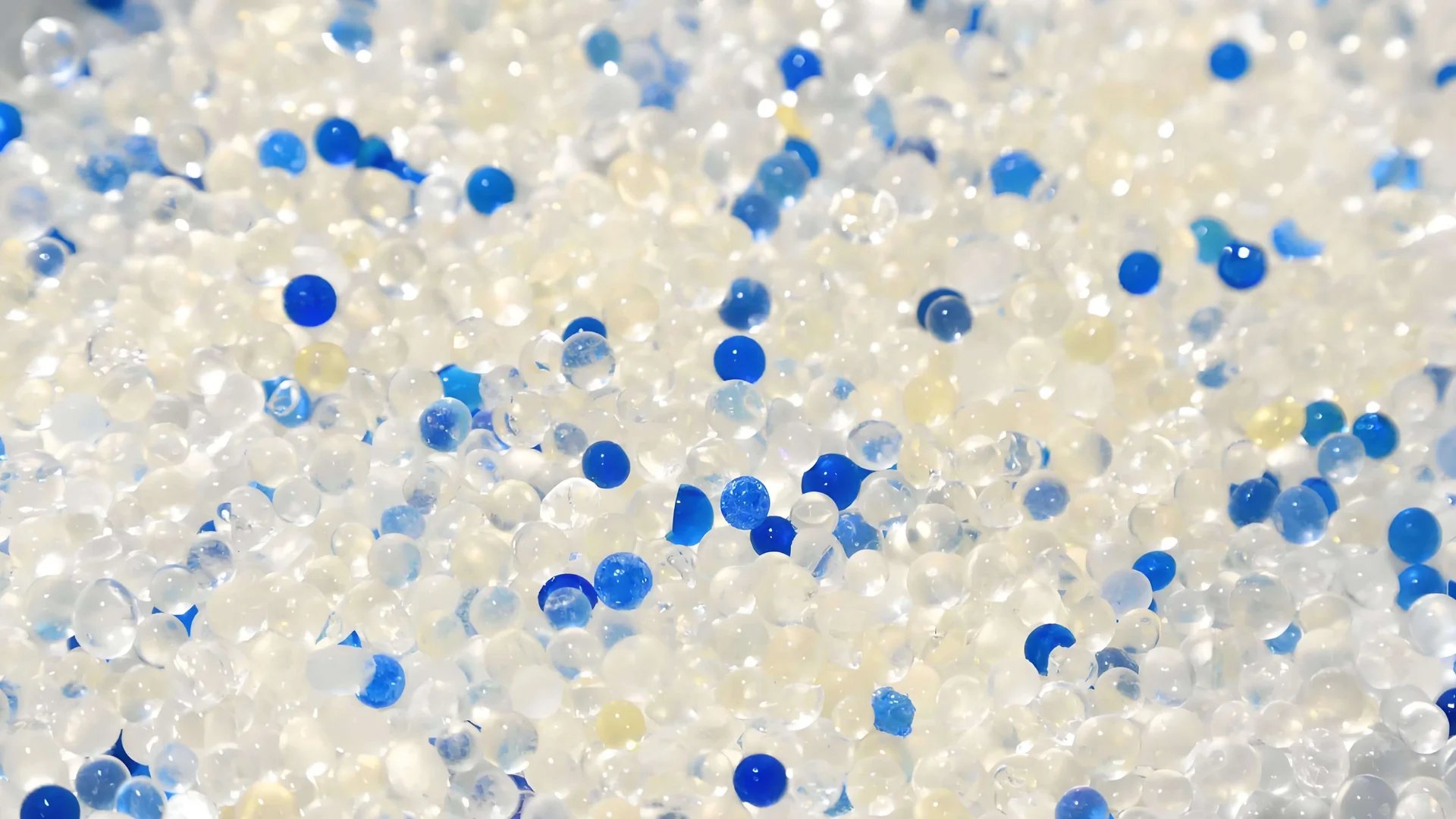
The Core Material: Liquid Silicone Rubber
At the heart of silicone injection molding1 is liquid silicone rubber (LSR). This material is favored for its excellent thermal stability, chemical resistance, and flexibility. LSR starts as a two-part compound that cures into a durable, rubber-like substance when heated. Its inherent properties make it suitable for producing components with tight tolerances and complex geometries.
Vulcanizers and Catalysts
To transform LSR from a liquid into a solid form, vulcanizers and catalysts are employed. Vulcanization involves heating the silicone to trigger chemical reactions that link the polymer chains, thereby solidifying the material. Catalysts accelerate this process, ensuring efficient production cycles and enhancing the overall physical properties of the silicone products.
Additives: Pigments and Fillers
Additives like pigments and fillers play crucial roles in customizing the properties of silicone products. Pigments are used to impart vibrant colors, allowing manufacturers to meet specific design aesthetics or branding requirements. Fillers can enhance the mechanical properties of silicone, such as tensile strength or elasticity, and are selected based on the end-use application.
Material | Function |
---|---|
Liquid Silicone Rubber | Forms the base of the product; offers flexibility and stability. |
Vulcanizers | Initiate the curing process to solidify the silicone. |
Catalysts | Speed up vulcanization for faster production. |
Pigments | Provide color customization to meet design needs. |
Fillers | Enhance mechanical properties like strength and elasticity. |
Tailoring Material Selection to Application Needs
The selection of materials in silicone injection molding is heavily influenced by the intended application of the product. For example, medical-grade silicone2 might require biocompatible fillers and specific curing agents to ensure safety and compliance with health standards. Similarly, products exposed to harsh environments might use specialized additives to improve UV resistance or thermal stability.
In conclusion, understanding the various materials used in silicone injection molding is essential for optimizing product performance across diverse applications. By carefully selecting and combining these materials, manufacturers can create high-quality silicone products tailored to specific industry needs.
Liquid silicone rubber is the only material in molding.False
Besides LSR, vulcanizers, catalysts, pigments, and fillers are used.
Vulcanizers initiate the curing process in silicone molding.True
Vulcanizers trigger chemical reactions that solidify liquid silicone.
How Does Mold Design Impact the Quality of Silicone Products?
Mold design is pivotal in determining the quality and precision of silicone products. An expertly crafted mold ensures optimal functionality and aesthetic appeal, crucial for competitive markets.
Mold design directly influences the accuracy, surface finish, and durability of silicone products. Key factors include precise measurements, material choice, and innovative features to facilitate even silicone flow and effective vulcanization.
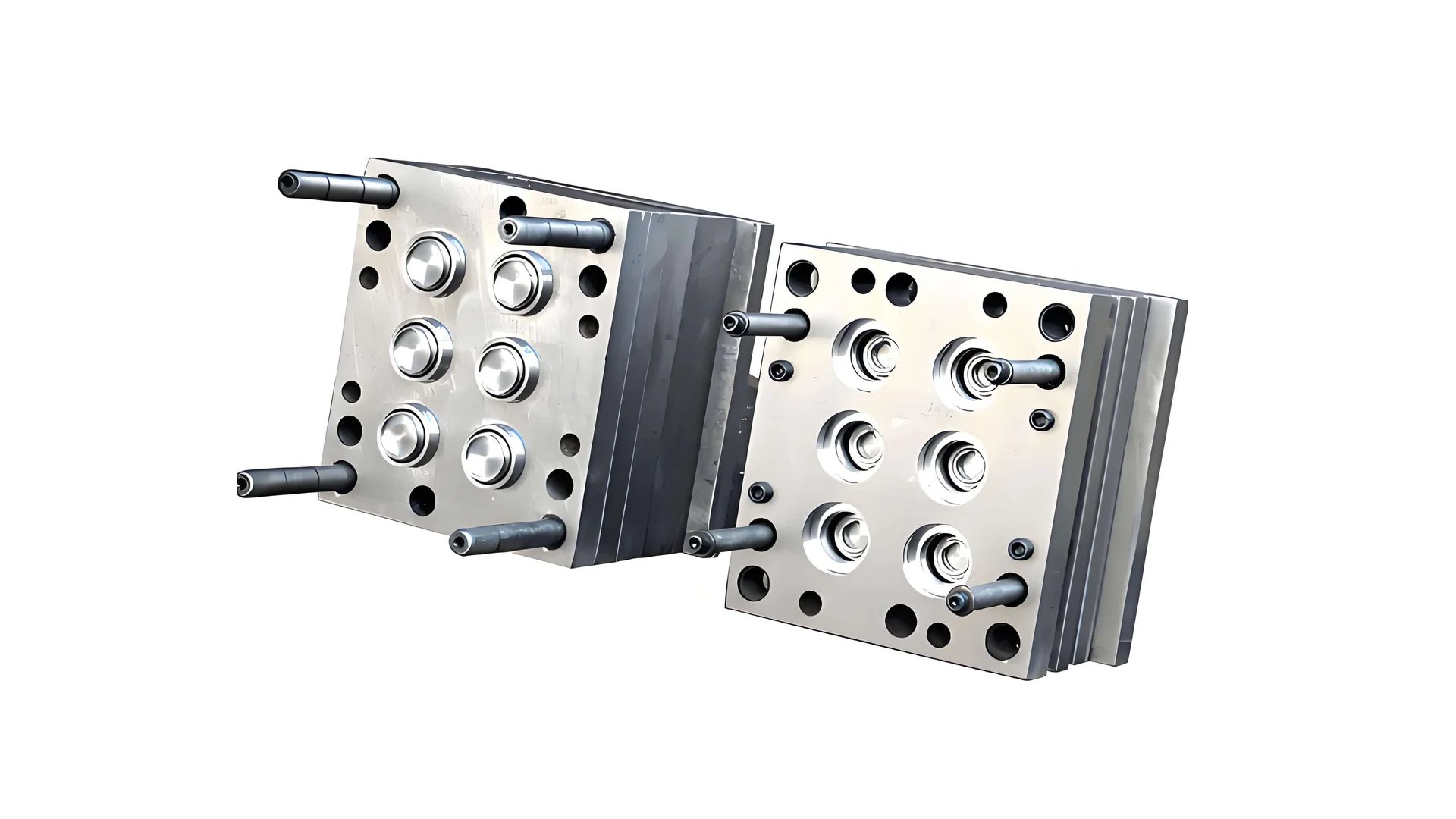
Importance of Accurate Measurements
One of the primary aspects of mold design affecting the quality of silicone products is measurement accuracy. The slightest deviation in dimensions can lead to significant flaws in the final product. Precision in mold design ensures that each silicone item meets its intended specifications, vital for applications requiring high dimensional accuracy, such as medical-grade silicone components3.
Material Choice for Mold Construction
The materials used for creating molds are as crucial as the silicone itself. Typically, molds are made from high-grade steel due to its durability and ability to withstand high temperatures and pressures during the vulcanization process4. This choice ensures longevity and consistency across production runs, reducing downtime and maintenance costs.
Innovative Features in Mold Design
Modern mold designs incorporate advanced features that enhance product quality. For instance, implementing well-designed runner systems can facilitate smooth silicone flow, minimizing air traps and ensuring uniformity in thickness. Additionally, advanced venting techniques can prevent defects like bubbles or voids, critical for maintaining the structural integrity of products such as automotive silicone seals5.
Table: Key Features Impacting Mold Design
Feature | Impact on Quality |
---|---|
Runner Systems | Ensures even flow, reduces air entrapment |
Venting Techniques | Prevents bubbles, enhances structural integrity |
Precision Engineering | Maintains dimensional accuracy |
Heat Distribution | Consistent vulcanization, avoids uneven curing |
Heat Distribution Considerations
Efficient heat distribution within the mold is crucial for proper vulcanization. Uneven heat can result in incomplete curing or deformation. Strategic placement of heating elements and insulation materials can improve heat distribution, leading to superior product quality.
In conclusion, mold design is a sophisticated blend of engineering precision and creative problem-solving. By understanding and implementing these critical elements, manufacturers can achieve high-quality silicone products tailored to diverse industry demands.
Accurate mold measurements prevent silicone product flaws.True
Precision ensures products meet specifications, vital for quality.
Steel molds are unsuitable for high-temperature vulcanization.False
Steel withstands high temperatures, making it ideal for molds.
What are the Key Advantages of Using Silicone Injection Molding?
Silicone injection molding offers unparalleled benefits, transforming how various industries produce high-quality silicone products.
Silicone injection molding provides high-precision molding, excellent material performance, high production efficiency, environmental friendliness, and vast design flexibility, making it ideal for diverse applications.
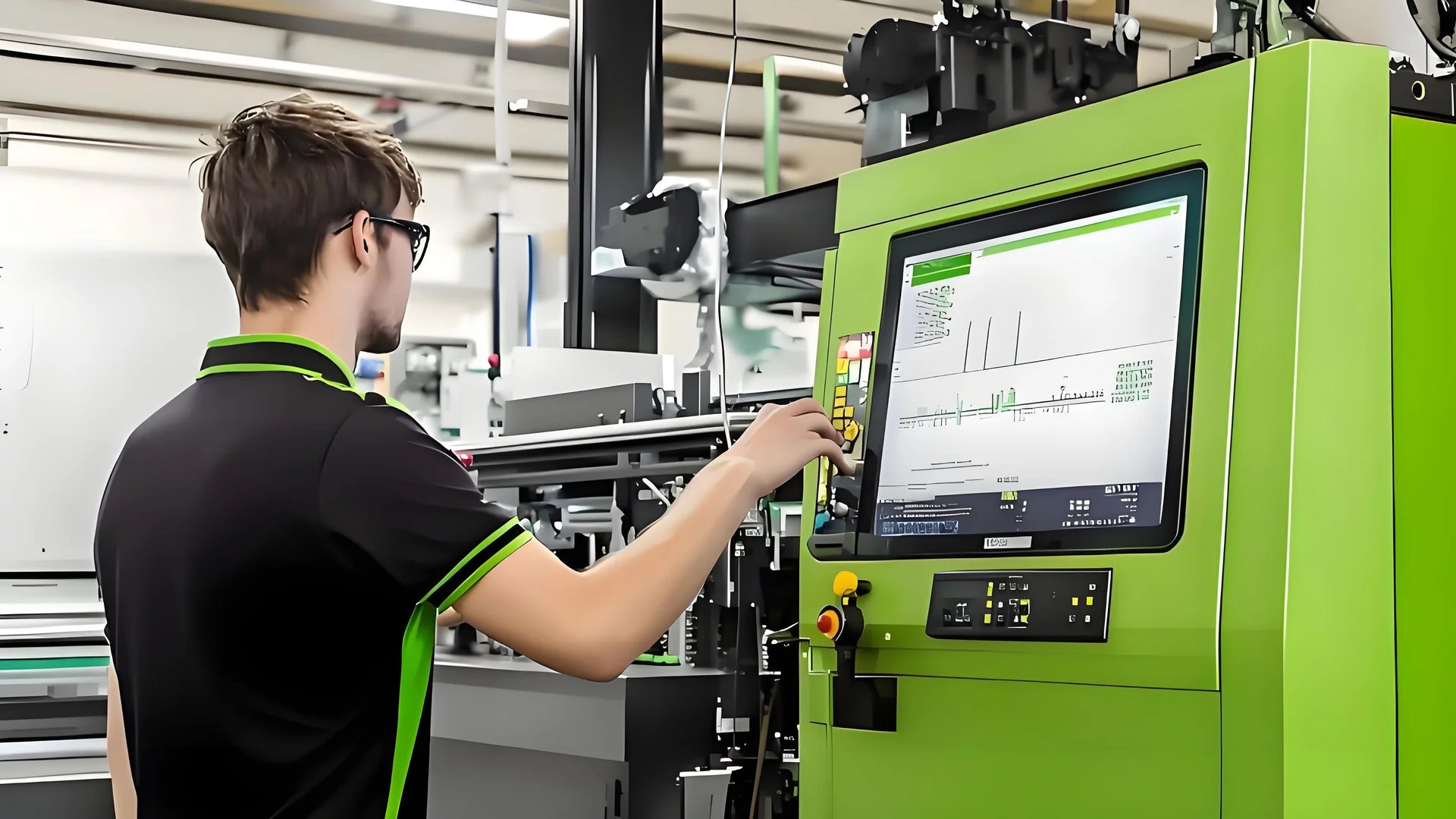
High-Precision Molding
Silicone injection molding excels in producing complex and precise parts with tight tolerances. This process ensures that products meet exact specifications, which is crucial in industries like medical device manufacturing6 and electronics where precision is paramount. The ability to consistently replicate intricate designs makes it a preferred choice for high-demand applications.
Excellent Material Performance
Silicone is renowned for its remarkable properties, including high-temperature resistance, low-temperature resilience, and resistance to aging and corrosion. These characteristics make silicone injection molded products suitable for harsh environments. For instance, components used in the automotive industry7 benefit significantly from silicone’s durability and adaptability.
High Production Efficiency
The automation involved in silicone injection molding shortens the production cycle, allowing for mass production without compromising quality. This efficiency is beneficial in fast-paced sectors such as consumer electronics, where timely delivery is critical. By automating the process, manufacturers can reduce labor costs and improve output consistency.
Environmentally Friendly and Non-Toxic
Silicone is an eco-friendly material that is non-toxic and odorless, aligning with stringent environmental regulations. This quality is particularly important in the maternal and child product market8, where safety is a top priority. Products like baby bottle nipples and toys are safer due to silicone’s harmless nature.
Large Design Flexibility
The versatility of silicone injection molding allows for customized designs to meet unique customer needs. Whether creating vivid colors or intricate shapes, this process can cater to diverse requirements without sacrificing quality. Industries like consumer goods9 greatly benefit from this flexibility, enabling the production of innovative products that stand out in the market.
Silicone injection molding ensures high precision.True
This process produces complex parts with tight tolerances.
Silicone is not suitable for high-temperature environments.False
Silicone withstands high temperatures, ideal for harsh conditions.
In Which Industries is Silicone Injection Molding Most Commonly Used?
Silicone injection molding is a versatile technique employed across numerous industries, thanks to its precision and adaptability. Discover where this method finds its best applications.
Silicone injection molding is prominently used in medical, electronics, automotive, maternal and child products, and various consumer goods industries due to its precision and material advantages.
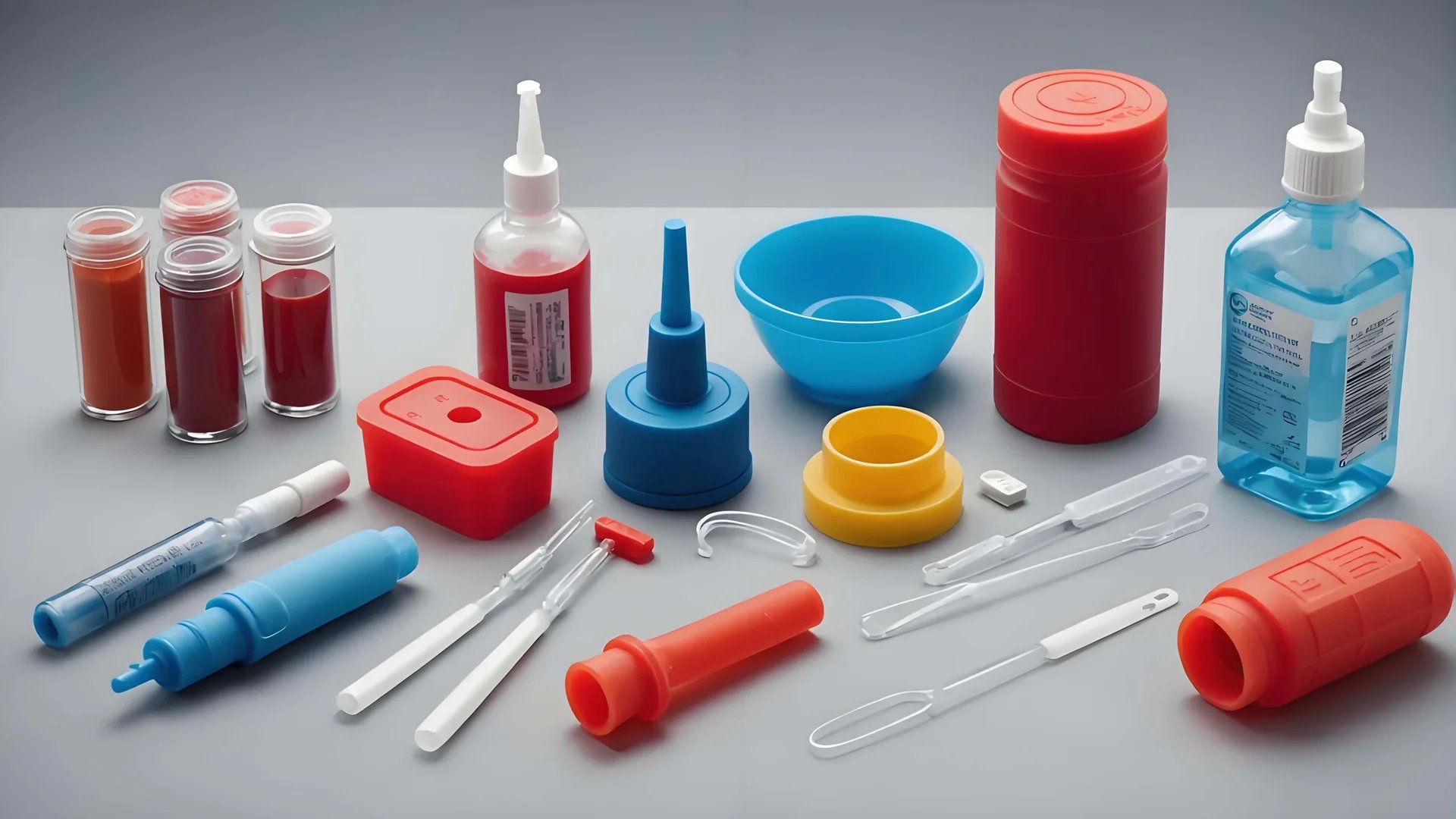
Medical Industry: Precision and Safety
Silicone injection molding’s ability to create high-precision components makes it invaluable in the medical industry10. Products such as catheters, earplugs, and gloves demand not only exact dimensions but also materials that are safe for human contact. Silicone’s non-toxic properties and its capability to withstand sterilization processes make it an ideal choice.
Electronics Industry: Ensuring Durability
The electronics sector often utilizes silicone injection molding for items like buttons, sealing rings, and protective covers. Silicone’s excellent thermal stability and electrical insulation properties safeguard sensitive electronic components against environmental factors, such as dust and moisture.
Automotive Industry: Reliability in Harsh Conditions
In the automotive industry11, silicone injection molding is employed to produce tubes, seals, and pads. Its resistance to extreme temperatures and chemical exposure ensures longevity and reliability, crucial for vehicle performance.
Maternal and Child Products: Safety First
Parents value safety and hygiene in products like nipples, bottles, and toys. The use of silicone in these products ensures they are free from harmful substances while providing durability and comfort. Silicone injection molding enables manufacturers to meet stringent safety standards with customized designs.
Consumer Goods: Versatility and Customization
Beyond these specific sectors, silicone injection molding is used in various consumer goods, including kitchenware, sports equipment, and cosmetic packaging. The flexibility of design allows manufacturers to cater to diverse customer preferences while maintaining product quality.
The industries benefiting from silicone injection molding are vast and varied, each leveraging the process’s unique advantages to meet their specific needs.
Silicone injection molding is used in the medical industry.True
It's used for precision components like catheters and gloves.
Silicone injection molding is rarely used in electronics.False
It's commonly used for buttons and protective covers.
Conclusion
In summary, silicone injection molding merges precision with versatility, making it crucial in various industries. Explore how this method can elevate your projects!
-
Learn about LSR’s properties and why it’s crucial for molding.: A Liquid Silicone Rubber material is a two-part platinum-cured elastomer that can be injected into a mold cavity to manufacture a part. ↩
-
Explore why medical-grade silicone is safe and effective.: Medical grade silicones are generally grouped into three categories: non implantable, short term implantable, and long-term implantable. Materials approved as … ↩
-
Explore why precision is critical for medical-grade silicone components.: Medical equipment often relies on precision seals and gaskets to maintain sterility and prevent leaks. Medical molding ensures the production of … ↩
-
Discover which materials are ideal for molds during vulcanization.: I have used natural rubber and a few of the silicone variants of the vulcanizable types and also some of the ‘mixit’ type, but I have not used … ↩
-
Learn about innovative designs improving automotive silicone seals.: For reliable and innovative silicone product manufacturing, Extreme Molding is the top choice. Our commitment to quality and customer satisfaction makes us … ↩
-
Precision ensures safety and effectiveness in medical devices.: Manufacturing for precision and accuracy is critical in medical applications to ensure proper function, long service life, patient safety, and … ↩
-
Learn how silicone enhances durability and performance in vehicles.: Silicone elastomers provide exceptional durability and stable performance over a wide temperature range. In this article, we’ll focus on car electronics as we … ↩
-
Discover why silicone is ideal for baby products.: Unlike plastic toys, silicone toys do not contain any harmful chemicals such as BPA, phthalates, or PVC. ↩
-
Explore how design flexibility boosts innovation in consumer products.: In this article, we review literature from the last two decades that focuses on the application of Operations Research methods in manufacturing system design. ↩
-
Learn how silicone enhances precision and safety in medical products.: Our fully automated hands-free injection molding, and ISO class 8 clean room ensure precision accuracy, high quality and protect critical components. ↩
-
Explore how silicone ensures reliability in automotive components.: It can produce excellent automotive components such as car lights, dashboards, air deflectors, and hoses. Silicone is known for its high … ↩