Do you ever think about why some plastic items don’t fit well or appear just right?
Too much shrinking leads to wrong sizes and looks bad, while too little shrinking causes problems with fitting and stress inside plastic products.
I remember designing a plastic part for a device. Small errors in shrinkage size caused big problems. Too much shrinkage led to smaller parts, which created gaps in the assembly. This problem increased with precise parts. Too little shrinkage made parts too large. These parts jammed or fit badly. Such issues damaged how the product worked. Product look also suffered. Aesthetic design was important too. It is interesting how small details affect durability and looks. It is very interesting.
Excessive shrinkage causes aesthetic defects in plastics.True
Excessive shrinkage can lead to warping and surface irregularities.
Insufficient shrinkage improves plastic product durability.False
Insufficient shrinkage can cause internal stress, reducing durability.
Why Do Plastic Products Experience Excessive Shrinkage?
Ever thought about why some plastic pieces don’t fit well? The mystery lies in too much shrinking, which creates or destroys a product’s quality.
Too much shrinkage in plastic products comes from the material’s nature, the way of processing and how the mold is built. Fast cooling, wrong temperatures and bad material selections usually cause this problem. This affects size accuracy and looks. Size matters. Appearance too.
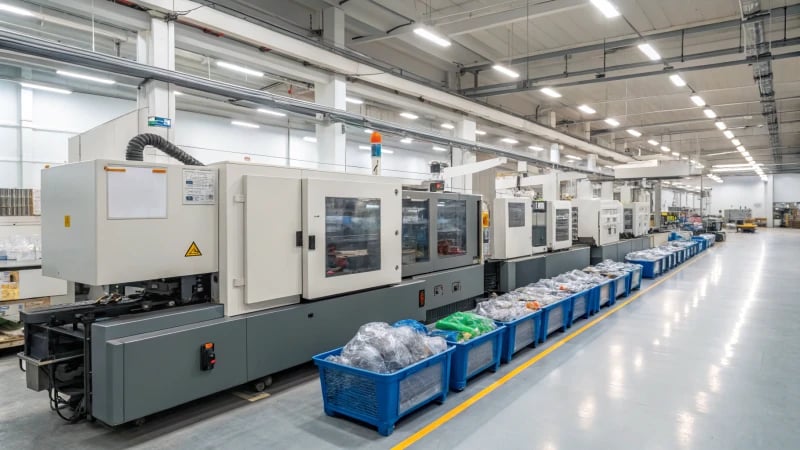
Material Properties and Their Role
Pick up a plastic object. It might appear smaller than expected. This is due to the plastic type. Picture tiny molecules moving inside as the plastic cools. Semi-crystalline polymers shrink more because their molecules pack tightly. It’s like cramming items into a suitcase before a trip.
Processing Conditions
-
Cooling Rate: Cool a hot drink very fast and the glass may crack. Plastics are similar. Quick cooling causes more shrinkage because the outer layers solidify quickly, while the inner layers continue to contract. Balance when cooling to prevent this.
-
Temperature Settings: Bake a cake at the wrong heat and it won’t rise well. Molds behave the same way. A cold mold keeps plastic from expanding properly, leading to more shrinkage.
Temperature | Effect on Shrinkage |
---|---|
Low | Increases |
Optimal | Reduces |
Mold Design Considerations
The mold’s design matters a lot. Pouring pancake batter on an uneven pan doesn’t spread it evenly, just like poor mold design leads to dimensional inconsistencies1 due to uneven material flow and shrinkage.
For creators of precise tools like Jacky, who works with consumer electronics, uniform wall thickness prevents problems by ensuring consistent molding conditions.
Examples and Insights
Think of automotive interiors where aesthetic quality is crucial; seeing dents on a dashboard due to shrinkage is disappointing and impacts overall appearance, potentially leading to customer dissatisfaction.
In electronic device housings, where interchangeability is paramount, inconsistent shrinkage could mean parts that don’t fit together seamlessly, thus affecting functionality.
These examples show why knowing shrinkage matters for product designers like Jacky2, who strive for perfection in both functional and aesthetic aspects of their creations.
Semi-crystalline polymers shrink more than amorphous ones.True
Semi-crystalline polymers pack tightly upon cooling, causing higher shrinkage.
Low mold temperature decreases plastic shrinkage.False
Low mold temperatures increase shrinkage by preventing full polymer expansion.
How Can Designers Mitigate Shrinkage Effects in Mold Design?
Ever experienced that moment when you succeed with a design, only to watch it warp and shrink? Let’s explore how designers defeat those annoying shrinkage effects in mold design.
Designers reduce shrinkage effects in mold design by adjusting processing settings, selecting appropriate materials and applying clever mold design techniques. This method achieves precise dimensions and produces top-quality items. Dimensional accuracy and superior products.
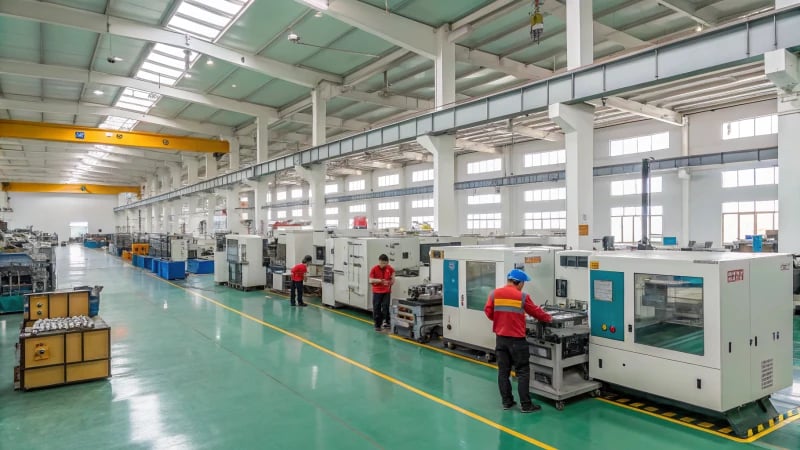
Understanding Shrinkage Effects
As a designer, I often see how tricky shrinkage becomes. It’s similar to planning a perfect dinner and then the soufflé collapses unexpectedly. Shrinkage affects both the appearance and real size of our products. Maybe you’ve noticed how too much shrinkage leads to smaller products, causing gaps that disrupt assembly lines completely.
Material Selection
Over the years, I realized that choosing the right material is really important. It’s like picking the best ingredient for a dish. Some polymers, such as polycarbonate and ABS, shrink less. They work well for detailed parts. I recall a project where switching to ABS stopped a lot of defective parts.
Material | Typical Shrinkage Rate |
---|---|
Polycarbonate | 0.5% – 0.7% |
ABS | 0.4% – 0.7% |
Evaluating the material’s shrinkage rate before designing3 can help avoid potential issues.
Mold Design Techniques
Optimizing mold design feels like creating art. It’s about balance – similar to baking a perfect pie crust. By adjusting cooling channels and gate positions, shrinkage marks and warping decreased a lot in my past work.
- Cooling Channels: These resemble a reliable kitchen timer, keeping temperature even throughout.
- Balanced Gates: They distribute material evenly, reducing stress – just like spreading batter smoothly in a cake pan.
Processing Parameters
Changing injection speed and pressure feels like adjusting a song’s rhythm. A slower speed reduces stress, just like a deep breath before a busy day.
- Injection Speed: Slow pacing allows controlled filling.
- Pressure: Correct holding pressure can fight material shrinkage during cooling.
Simulation Tools
In my kit, simulation software acts like a crystal ball – it foresees shrinkage problems before they occur. These tools have prevented many headaches by showing possible changes early on.
Simulation Software4 provides insights by displaying how different settings change the final product.
Using these methods, I stay ahead of shrinkage issues in mold design, producing very high-quality plastic parts ready for market needs.
Polycarbonate has a lower shrinkage rate than polypropylene.True
Polycarbonate's typical shrinkage rate is 0.5% - 0.7%, lower than polypropylene's 1.5% - 2.5%.
Simulation tools cannot predict shrinkage effects in mold design.False
Simulation software can predict shrinkage effects, allowing for design adjustments.
What Are the Consequences of Inconsistent Shrinkage in Manufacturing?
A small error in shrinkage often affects the whole manufacturing process. This little mistake sometimes disrupts production. Changes in size usually create problems in assembling parts. Workers may struggle to fit pieces together. If parts do not align, machines might not work correctly. A very tiny miscalculation sometimes leads to big delays. Teams occasionally need more time to fix issues, costing the company extra money.
Inconsistent shrinkage probably causes problems during assembly, surface flaws and weak structures. It very often increases production costs and complicates quality control. These issues are serious.
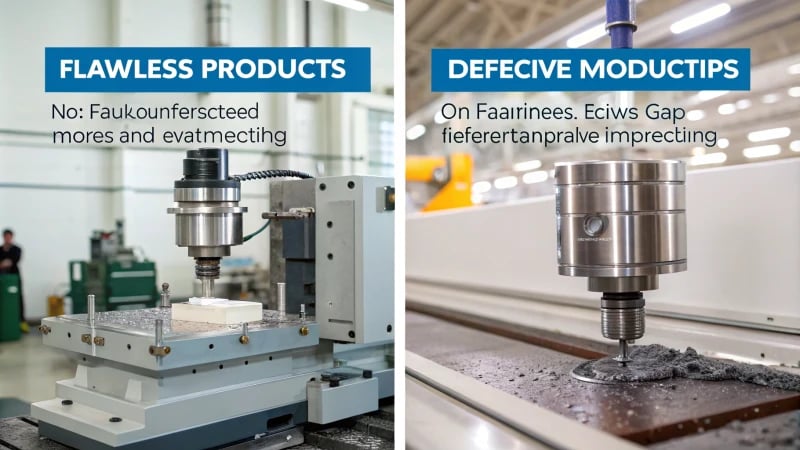
Impact on Dimensional Accuracy
I recall the first time I found inconsistent shrinkage at work. It surprised me, like a twist in a mystery story. We produced parts for precise machines and the specs were very tight. But, wow, shrinkage had other ideas. Parts came out smaller, leaving spaces like they played hide and seek with the assembly.
Dimensional inaccuracy causes real problems. You expect a perfect fit, but then the parts fail to meet size rules. It’s not just about fitting; it’s about staying away from the scrap pile when stakes are high.
Table: Dimensional Impact of Shrinkage Variations | Shrinkage | Resulting Size | Consequence |
---|---|---|---|
Excessive | Smaller | Gaps between parts | |
Too Small | Larger | Tight fits or no fit |
Effects on Appearance Quality
I enjoy fine details in life and design. So, it was frustrating when shrinkage left our products with dents. Like watching a favorite painting fade. Products looked like they went through tough times.
In fields like car-making, looks matter as much as function. Shrink marks5 aren’t just marks. They are real problems. Warping from shrinkage can twist not just the appearance but the product’s purpose.
Internal Quality Concerns
Then come internal quality issues. High shrinkage leads to pores and less density. It’s like building a house on shaky ground. Weak foundations create issues. Strong structures need good qualities and high shrinkage is a challenge to avoid.
Too little shrinkage causes other problems—makes things strong but brittle. It’s like holding on too tightly and losing grip anyway.
Understanding these details is crucial in design and manufacturing. It’s finding the balance where performance and perfection meet. Bringing customer joy becomes real, not just a catchphrase.Control of shrinkage6 very possibly changes the game, making products better and providing peace of mind.
Excessive shrinkage causes assembly issues.True
Excessive shrinkage results in smaller parts, leading to gaps.
Too little shrinkage improves product strength.False
Too little shrinkage increases internal stress, risking cracks.
Why Is Monitoring Shrinkage Crucial for Product Reliability?
Did you ever think about why that bright, new device sometimes seems wrong? Shrinkage is the hidden force at play. It is often the unnoticed hero or the unexpected villain in creating reliable products.
Observing shrinkage keeps product dimensions accurate. Products look good. Internal quality stays high. Very important to stop problems like warping. Also stops size mismatches.
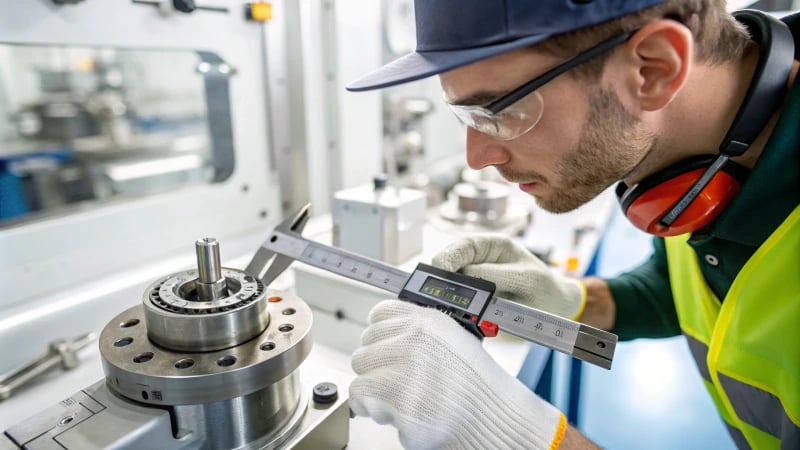
Understanding the Impact of Shrinkage
Shrinkage refers to the change in volume of materials like plastics during cooling. When not monitored, it can lead to significant deviations from design specifications.
Dimensional Accuracy
I know this all too well. Imagine you’re ready to put together a new batch of products, but the pieces simply don’t fit. Very annoying, right? That’s when shrinkage happens. Excessive shrinkage can cause plastic parts to be smaller than intended. This affects assembly, causing gaps and malfunctioning equipment. For precision products, excessive shrinkage7 can lead to unusable components.
Table: Impacts of Shrinkage on Dimensional Accuracy
Shrinkage Level | Impact on Size | Assembly Issues |
---|---|---|
Excessive | Too Small | Gaps in fitting |
Too Small | Too Large | Tight fittings |
Appearance Quality
I’ve watched it happen – those ugly surface marks that shout "low quality." Shrinkage affects the appearance of products. Excessive shrinkage may result in surface depressions or marks, compromising aesthetics. In products like automotive interiors, these defects reduce quality.
- Surface Marks: These little dents appear in thick areas due to shrinking.
- Warping: Uneven shrinkage bends products out of shape, leaving them twisted and bent.
Internal Quality
Then there’s what you can’t see – inside. Excessive shrinkage indicates a loose internal structure, reducing strength and increasing vulnerability to damage. Conversely, too small shrinkage can cause high internal stress, making products prone to cracking.
Imagine a plastic piece that breaks easily; that’s very disappointing. On the other hand, if products do not shrink enough, they might crack instead of bending.
Monitoring Techniques
What’s the answer? Effective monitoring strategies help manage shrinkage. Using real-time analysis tools and quality control measures ensures products meet design specifications. Monitoring techniques8 like these can significantly improve product reliability.
- Real-time Analysis: Provides immediate feedback on shrinkage levels.
- Quality Control: Regular checks ensure consistent production standards.
By keeping an eye on shrinkage, my designs meet high standards in various fields – from gadgets to car parts. Being careful saves money and increases customer happiness by providing strong and trustworthy products. These insights into shrinkage management9 offer valuable guidance for designers aiming to refine their processes and deliver superior products.
Excessive shrinkage leads to product size reduction.True
Excessive shrinkage causes parts to be smaller, affecting assembly.
Shrinkage has no impact on product appearance quality.False
Shrinkage affects aesthetics, causing surface marks and warping.
Conclusion
Excessive or insufficient shrinkage in plastic products affects dimensional accuracy, appearance quality, and internal strength, leading to assembly issues and increased production costs.
-
Understand the impact of mold design on shrinkage to improve dimensional accuracy. ↩
-
Discover strategies for designers to minimize shrinkage impacts on product quality. ↩
-
Exploring material properties aids in selecting options that minimize shrinkage issues. ↩
-
Simulation software provides foresight into design adjustments needed to address shrinkage. ↩
-
Learn why shrink marks can degrade the appearance and quality of automotive interiors. ↩
-
Understand how internal stress from inconsistent shrinkage affects plastic product durability. ↩
-
Explore how excessive shrinkage leads to unreliable product dimensions, affecting assembly and functionality. ↩
-
Learn about advanced monitoring techniques that ensure optimal shrinkage control during production. ↩
-
Discover effective strategies for managing shrinkage to enhance product reliability and quality. ↩