In the fascinating realm of injection molding, shear heat plays a pivotal role that often goes unnoticed. But as I’ve learned, understanding its influence can be a game changer for product quality.
Shear heat in injection molding affects both the quality and efficiency of products. While it enhances fluidity and molecular orientation, excessive heat can lead to material degradation and dimensional instability. Balancing shear heat is key to achieving optimal product results.
Let’s dive deeper into the world of shear heat, where I’ll share insights on its beneficial effects and the challenges it poses, drawing from real-life experiences that highlight its importance.
Excessive shear heat causes product warping in injection molding.True
Excessive shear heat leads to uneven stress distribution, causing warping.
What Are the Positive Effects of Shear Heat on Product Quality?
In injection molding, shear heat can significantly enhance the quality of products, benefiting various aspects of production.
Shear heat improves product quality by enhancing fluidity, promoting molecular orientation, and improving surface finish. These effects result in better mechanical properties and aesthetics.
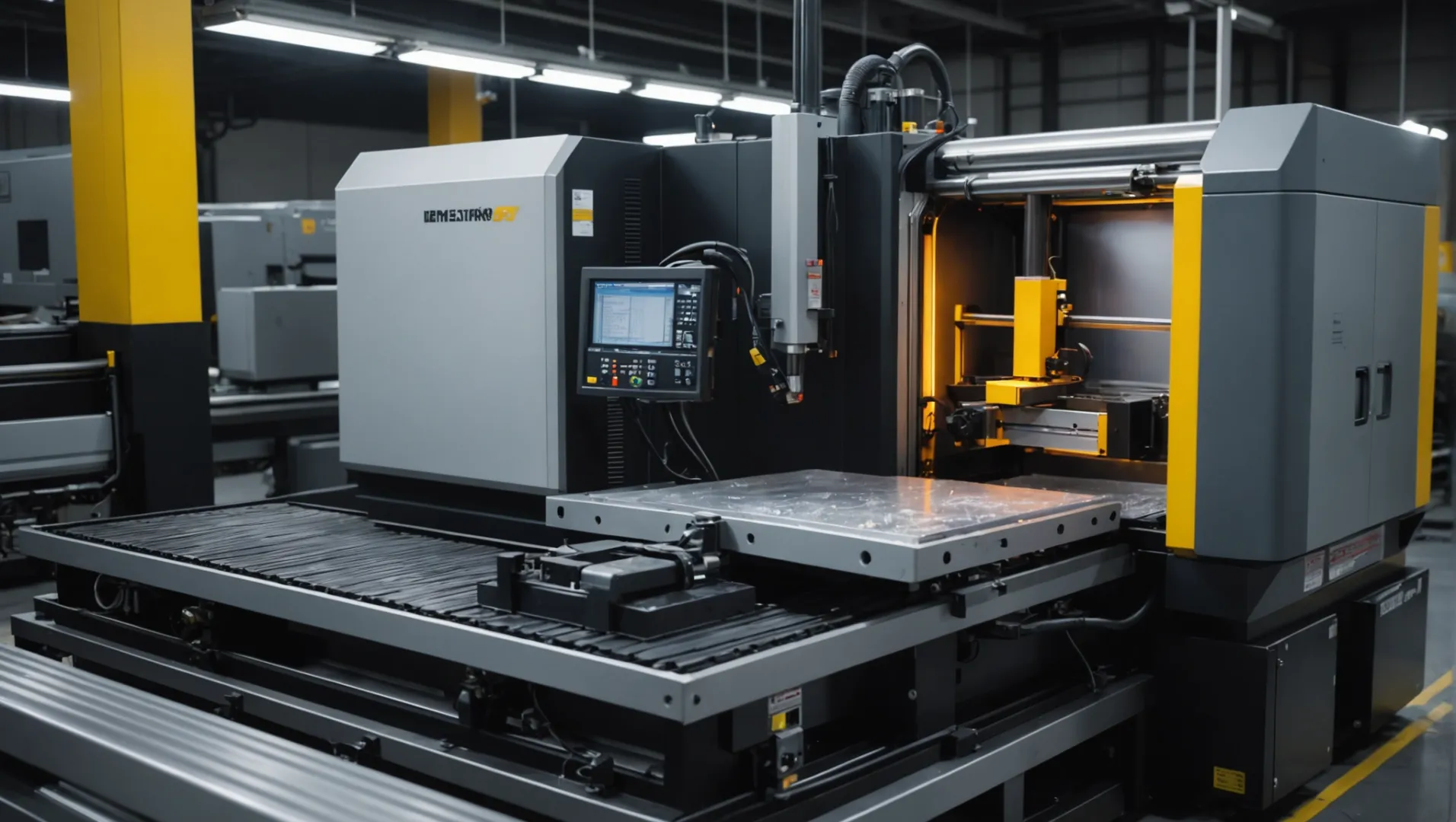
Enhanced Fluidity: A Key to Complex Designs
One of the most notable benefits of shear heat1 is the improved fluidity it imparts to plastic melts. By raising the melt temperature and reducing viscosity, shear heat facilitates the smooth flow of plastics through mold cavities. This process is crucial when dealing with intricate designs or products with fine structures, as it ensures comprehensive filling and reduces defects like short shots.
Consider the production of thin-walled components. Here, enhanced fluidity from shear heat allows the plastic to seamlessly fill narrow spaces, ensuring every detail is captured without compromising structural integrity.
Promoting Molecular Orientation for Strength
Shear heat’s ability to promote molecular orientation significantly enhances mechanical properties. In materials like fiber-reinforced plastics, shear heat aligns fibers along the flow direction, resulting in improved strength and stiffness. This alignment is especially beneficial for products that require high tensile strength in specific orientations.
For instance, in automotive components where durability is paramount, shear heat ensures that fiber reinforcements contribute optimally to the product’s overall performance.
Surface Finish Improvements
A higher melt temperature due to shear heat contributes to an improved surface finish. When plastics are at optimal temperatures, they better replicate mold surfaces, minimizing defects such as ripples or unwanted textures.
This effect not only enhances the visual appeal but also impacts functional attributes like friction and wear resistance. Products in consumer electronics or medical devices benefit greatly from this improvement, where aesthetics and precision are critical.
Balancing Shear Heat for Optimal Results
While the positive effects are evident, it’s crucial to manage shear heat carefully. Overheating can lead to issues like material degradation2, so understanding and controlling this heat is essential for maintaining product quality across various dimensions.
Shear heat enhances fluidity in injection molding.True
Shear heat raises melt temperature, reducing viscosity, improving flow.
Excessive shear heat has no negative effects.False
Overheating can cause material degradation, affecting product quality.
How Can Excessive Shear Heat Lead to Material Degradation?
In the world of injection molding, managing shear heat is crucial to prevent material degradation and ensure product quality.
Excessive shear heat during injection molding can degrade plastics by breaking down molecular chains. This results in weakened mechanical properties and potential product defects. Carefully regulating shear heat is essential to maintain the integrity and appearance of molded products.
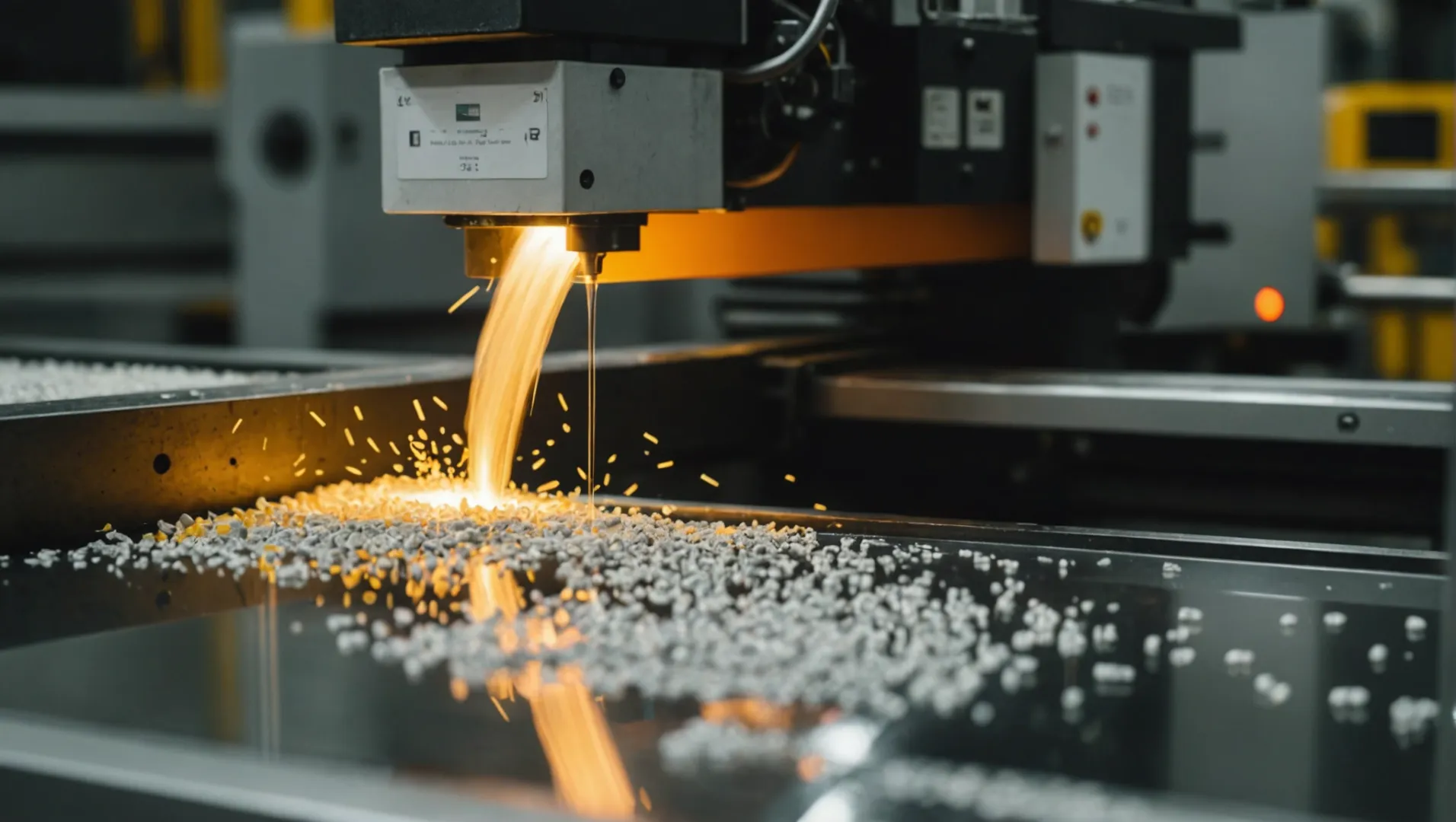
The Mechanism of Material Degradation
Material degradation due to excessive shear heat is a result of the breakdown of the molecular chains in plastics. As plastics are heated beyond their stability threshold, the molecular integrity is compromised, leading to a reduction in their mechanical strength. This breakdown is particularly pronounced in materials like polyolefins, including polyethylene and polypropylene, where high temperatures cause yellowing and brittleness.
When these molecular chains break, the once robust plastic becomes fragile, increasing susceptibility to cracking under stress. For example, products made from polypropylene that experience excessive shear heat may exhibit signs of brittleness, compromising their durability and performance.
Impact on Product Properties
The consequences of this degradation extend beyond just mechanical weaknesses. The aesthetic appeal of a product can also be compromised. High temperatures may lead to discoloration or surface defects, affecting the visual quality of the product. Additionally, products may not meet color specifications, which is crucial for consumer-facing applications where appearance matters.
Case Study: Polyethylene in Injection Molding
Consider polyethylene, a common thermoplastic used across various industries. When subjected to excessive shear heat, polyethylene’s molecular chains start to degrade, resulting in yellowing and reduced flexibility. This affects not only the physical appearance but also the tensile strength of the finished product. By controlling the shear heat through careful process adjustments, manufacturers can preserve the desirable qualities of polyethylene while avoiding degradation.
To further understand how shear heat impacts different materials, explore case studies or expert analyses that detail the specifics for various plastics. This knowledge can be pivotal in tailoring injection molding processes for optimal outcomes.
Techniques to Mitigate Shear Heat Effects
To prevent material degradation, manufacturers can adopt several techniques:
- Process Optimization: Adjusting parameters like injection speed and screw rotation speed can help manage shear heat levels.
- Material Selection: Choose materials with higher thermal stability or additives that enhance heat resistance.
- Cooling Systems: Implementing effective cooling strategies post-molding can reduce residual heat effects.
These methods can significantly mitigate the adverse effects of excessive shear heat, ensuring that products retain their mechanical and aesthetic properties.
By understanding these mechanisms and implementing strategic process controls, manufacturers can protect against material degradation and improve the overall quality and reliability of injection-molded products. To learn more about the impact of shear heat on other aspects such as dimensional stability, explore related articles on shear heat effects3.
Excessive shear heat breaks molecular chains in plastics.True
Shear heat degrades plastics by breaking molecular chains, weakening them.
Polyethylene is unaffected by excessive shear heat.False
Excessive shear heat causes yellowing and brittleness in polyethylene.
What Role Does Shear Heat Play in Dimensional Stability?
Dimensional stability is crucial in injection molding, and shear heat significantly influences it. Understanding this relationship helps in producing precise, durable products.
Shear heat impacts dimensional stability by causing uneven stress distribution, potentially leading to warping and deformation. Proper management of shear heat ensures product accuracy and reliability.
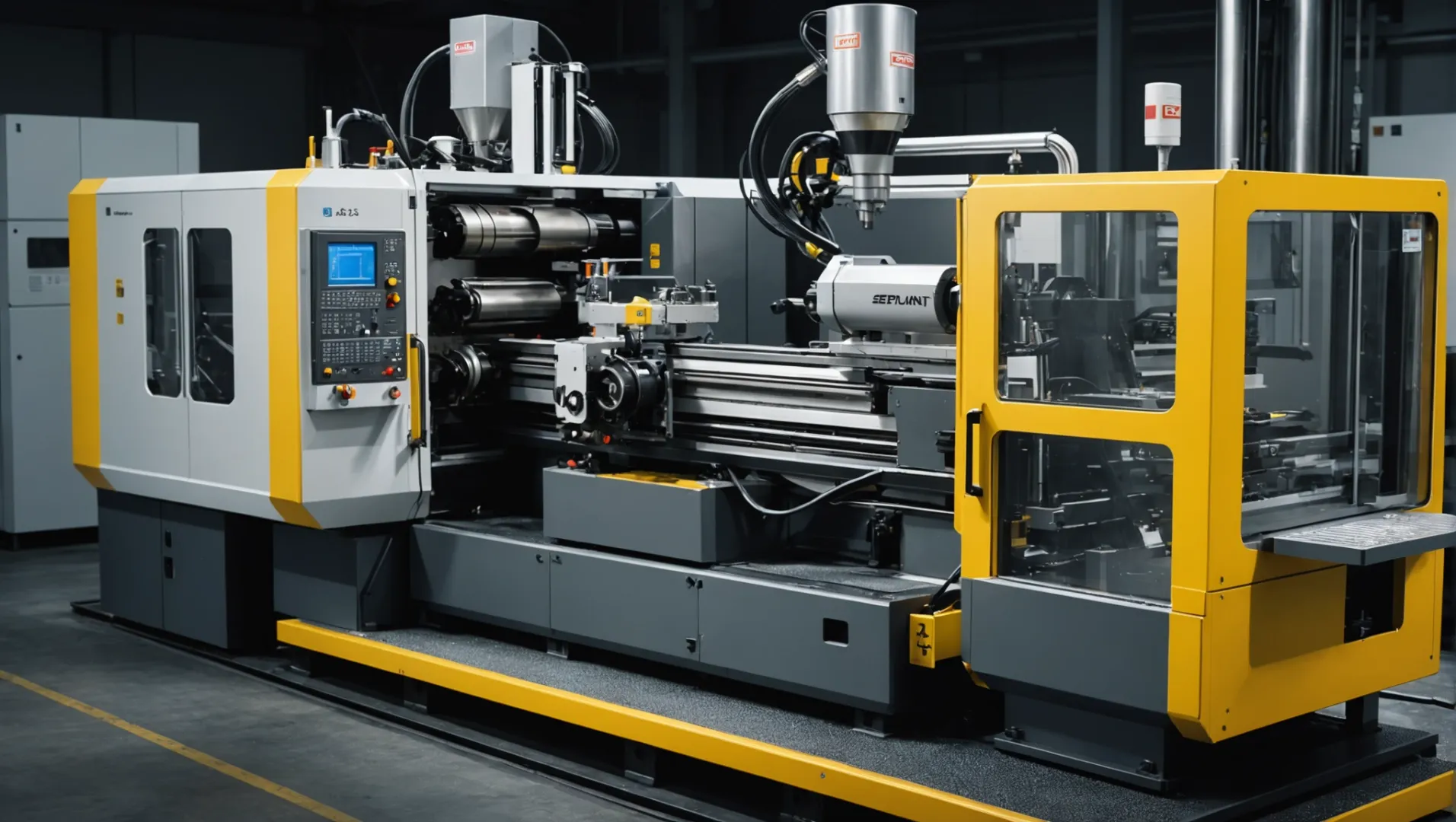
The Influence of Shear Heat on Product Dimensions
During the injection molding process4, shear heat arises from the friction between plastic melt and the mold walls. This heat can cause internal stresses within the molded product, leading to dimensional instability if not carefully controlled.
Uneven Stress Distribution
Shear heat often results in uneven distribution of stress across the product. This occurs because different areas of the product may experience varying levels of heat and cooling rates. Such inconsistency can lead to warping or deformation, particularly if the product has complex geometries.
Aspect | Impact of Shear Heat |
---|---|
Stress Distribution | Causes uneven internal stresses |
Cooling Rate | Influences cooling time and uniformity |
Mold Interaction | Affects the replication of mold details |
Warping and Deformation
When shear heat is not uniformly distributed, it may cause certain sections of the product to shrink more than others as they cool, leading to warping. For instance, products with thin walls are particularly susceptible as they can cool at a different rate than thicker sections.
To prevent such issues, manufacturers might need to adjust mold design or control the cooling process more precisely. This can be achieved by maintaining a consistent temperature across the mold and employing advanced cooling techniques.
Strategies for Managing Shear Heat
To enhance dimensional stability, managing shear heat involves regulating both the injection speed and screw speed during molding. By optimizing these parameters, manufacturers can ensure a uniform temperature distribution, reducing the likelihood of internal stresses.
Implementing computer-aided engineering tools5 can also help predict areas of potential stress concentration, allowing for preemptive adjustments in design or process parameters.
Overall, understanding and controlling shear heat is pivotal for ensuring that molded products maintain their intended dimensions and structural integrity after demolding.
Shear heat causes warping in injection molding.True
Shear heat leads to uneven stress, causing warping and deformation.
Uniform cooling rates eliminate shear heat issues.False
While helpful, uniform cooling alone doesn't fully address shear heat effects.
How Does Managing Shear Heat Affect Production Efficiency?
Efficiently managing shear heat in injection molding can significantly impact production speed and product quality, crucial for competitive manufacturing.
Managing shear heat optimizes production by balancing cycle times and minimizing defects, enhancing overall efficiency.
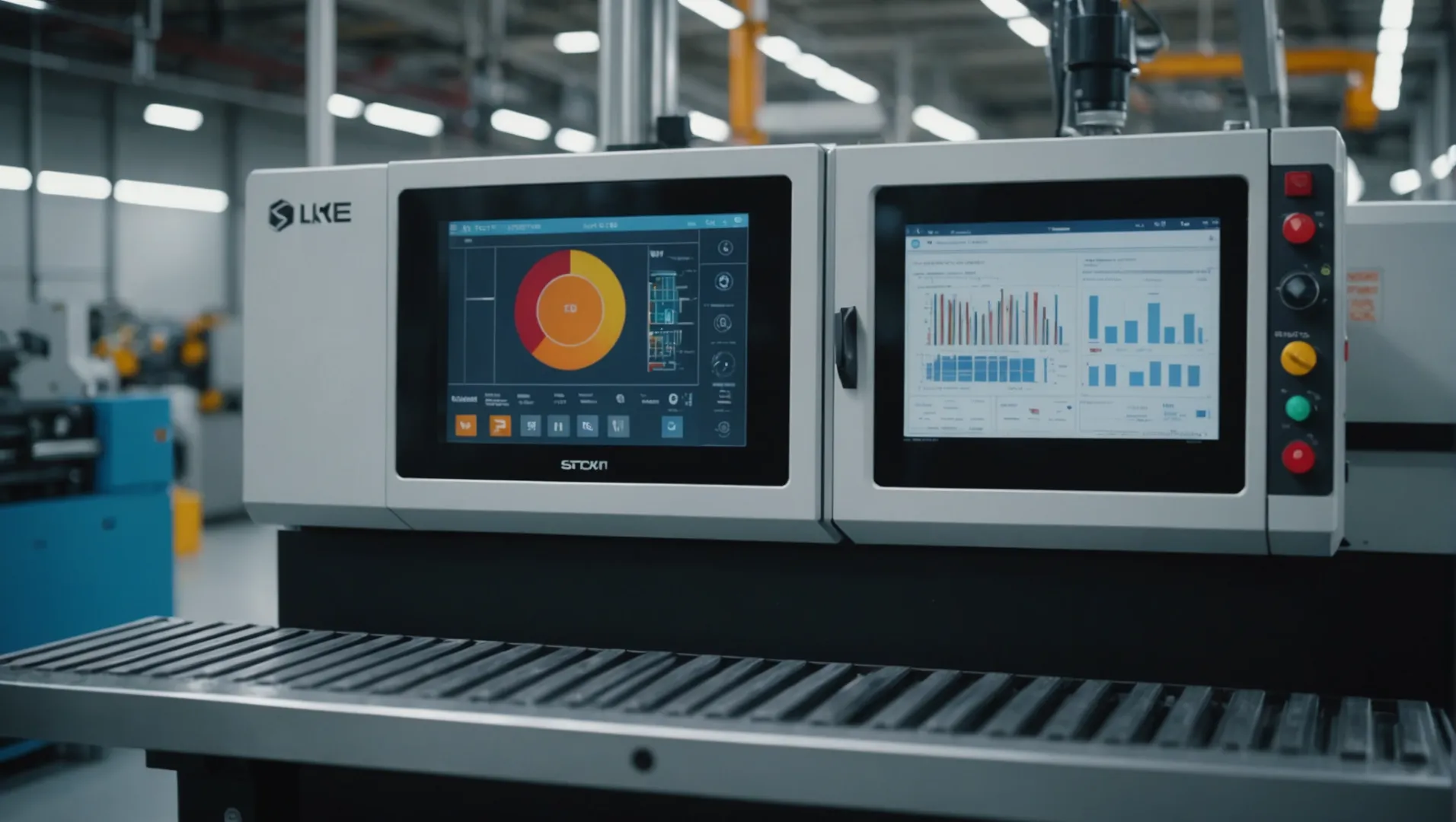
The Importance of Shear Heat Management
In injection molding, managing shear heat is pivotal for maintaining production efficiency. Shear heat arises when material layers slide over each other, increasing temperature due to friction. This heat can benefit the process by improving the fluidity of the plastic melt, making it easier to fill complex molds. However, if not controlled, excessive shear heat can lead to several issues that hinder production.
Balancing Cycle Times
Controlling shear heat involves adjusting parameters such as injection speed and screw speed. While higher speeds increase shear heat, they can also reduce cycle time by allowing faster material flow. However, this must be balanced carefully; excessive speed can lead to overheating, causing material degradation and necessitating longer cooling times, thus extending the cycle. Therefore, optimizing cycle time6 is critical for maintaining efficiency.
Minimizing Defects and Waste
Excessive shear heat can cause defects such as warping and dimensional instability. When material properties are compromised, products may not meet quality standards, resulting in increased waste. By controlling shear heat, manufacturers can reduce these defects, thereby minimizing waste and rework costs. This not only conserves resources but also enhances production efficiency7 by ensuring that fewer defective parts are produced.
Cost Implications of Heat Management
While managing shear heat can improve efficiency, it also incurs costs. Adjusting machinery settings may lead to increased energy consumption or equipment wear. Furthermore, implementing monitoring systems to control and adjust shear heat in real-time can require significant initial investment. However, these costs are often offset by the savings from reduced waste and improved product quality.
Efficient management of shear heat is a balancing act that requires careful consideration of various factors to enhance production efficiency without incurring unnecessary costs.
Managing shear heat reduces injection molding cycle time.True
Controlling shear heat allows faster material flow, reducing cycle time.
Excessive shear heat improves product quality in molding.False
Excessive shear heat causes defects like warping, reducing product quality.
Conclusion
Understanding and managing shear heat is vital for achieving high-quality injection-molded products while ensuring production efficiency.
-
Explores how shear heat enhances plastic flow in molds.: Struggling with shear heat in injection molding? Learn 3 effective tips to reduce shear heat, improve part quality, and boost productivity … ↩
-
Highlights risks of overheating during injection molding.: Shear heat can be a hidden culprit behind inefficiencies in your injection molding process, causing costly downtime and defects in molded parts … ↩
-
Explore how shear heat influences product dimensions and stability.: The heat-treatment influences on material’s crystallinity, porosity and dimensional stabilities with underlying mechanisms were discussed. Flexural properties … ↩
-
Explore how shear heat affects stress distribution in molding.: Shear heating occurs as plastic flows through a closed channel. This can include the molding machines nozzle and the molds sprue, runner, gates and cavities. ↩
-
Discover tools for predicting stress in molding processes.: We invest in systems that enable injection simulation analysis and work in an integrated CAD environment (Computer Aided Design) within the entire KNAUF … ↩
-
Learn effective strategies for reducing cycle time efficiently.: Some effective strategies for cutting cycle times involve optimizing cooling time, minimizing filling time, setting appropriate pause times … ↩
-
Discover methods to enhance overall manufacturing efficiency.: Step 1: Improve Your Business Processes · Step 2: Evaluate Your Production Line · Step 3: Update Technology · Step 4: Identify Production Bottlenecks · Step 5: Find … ↩