Injection molding can be a delicate dance, and salivation during this process is like stepping on a toe—unexpected and messy!
Salivation during injection molding is caused by excessive material fluidity, inappropriate material viscosity, excessive injection pressure, high nozzle temperature, and equipment faults such as damaged check rings.
But don’t worry! Understanding these causes is crucial for optimizing your injection molding operations. Let’s delve deeper into each factor and discover how to mitigate drooling, enhancing your manufacturing efficiency.
Excessive material fluidity causes drooling in molding.True
High fluidity allows plastic to flow easily, leading to drooling.
How Does Material Selection Affect Drooling?
Choosing the right material is key to preventing drooling in injection molding. Learn how material properties influence this common issue.
Material selection affects drooling by influencing fluidity and viscosity. High-fluidity or low-viscosity materials can lead to excessive leakage during injection molding, causing drooling.
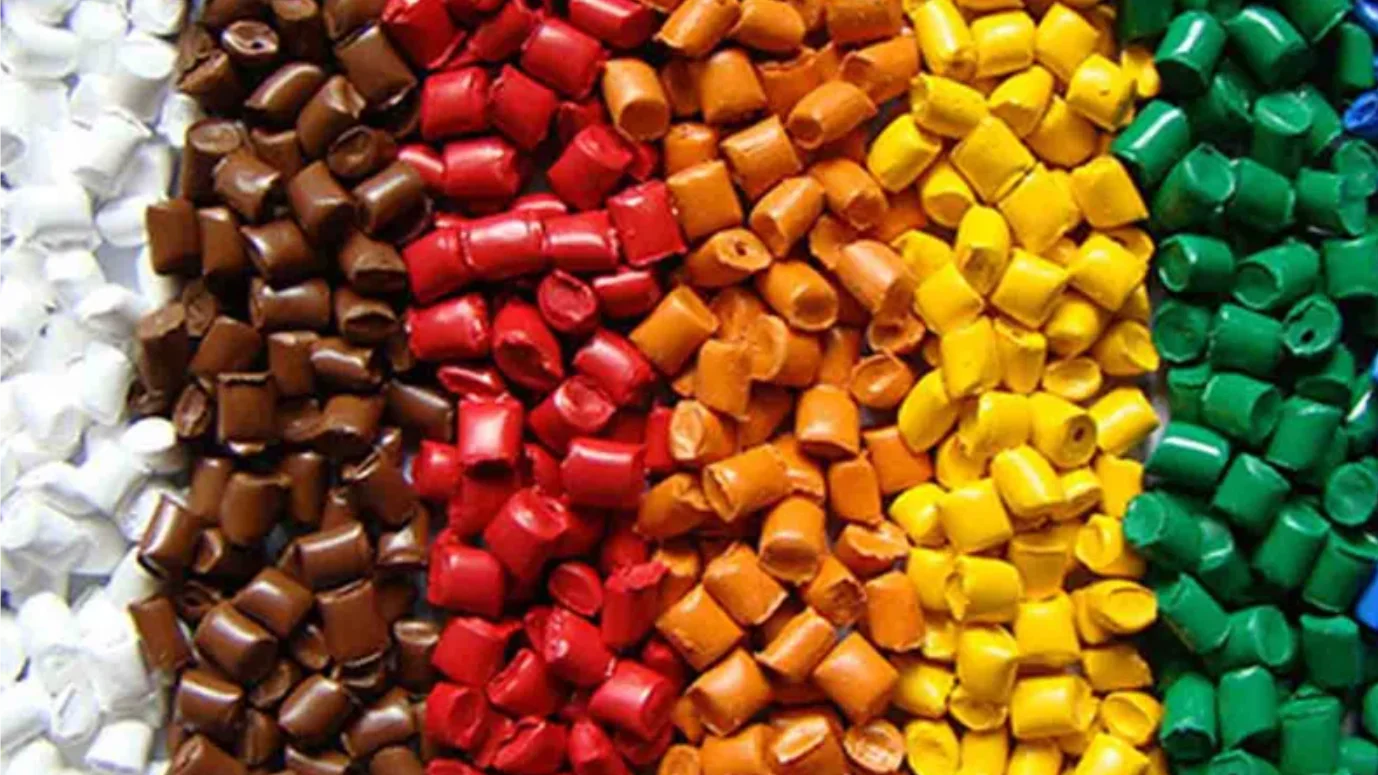
Understanding Material Properties
In injection molding, material selection directly impacts drooling, primarily through two properties: fluidity and viscosity.
-
Fluidity: Materials with high fluidity tend to flow more easily, which can lead to unwanted leakage. For instance, high-fluidity engineering plastics are often used for their ease of molding but can result in drooling if not properly managed. Evaluating the fluidity of potential materials1 is crucial to control drooling.
-
Viscosity: Low-viscosity materials pose a similar risk as they resist flow less effectively. This reduced resistance allows the molten plastic to escape more readily from the nozzle, leading to drooling. Comparing the viscosity properties of different plastics2 can aid in selecting a more suitable material.
Examples of Material-Induced Drooling
- Polycarbonate (PC): Known for its high fluidity, PC is prone to drooling under certain conditions. Adjusting injection parameters can help manage this.
- Polypropylene (PP): With varying grades, some PP types may exhibit low viscosity, leading to increased risks of drooling unless carefully selected.
Balancing Material Characteristics
Balancing fluidity and viscosity is essential for minimizing drooling. Here’s a simplified table illustrating how different materials compare:
Material | Fluidity | Viscosity |
---|---|---|
Polycarbonate | High | Moderate |
Polypropylene | Moderate | Variable |
ABS | Moderate | High |
This balance requires a comprehensive understanding of each material’s properties and how they interact with your specific molding process.
For a detailed analysis on managing these aspects, consider exploring how material grades impact drooling3.
High-fluidity materials increase drooling risk.True
Materials with high fluidity flow easily, leading to leakage.
ABS has low viscosity compared to Polycarbonate.False
ABS has high viscosity, while Polycarbonate has moderate viscosity.
What Role Does Temperature Play in Preventing Salivation?
Temperature is a crucial factor in managing drooling during injection molding, directly influencing material flow and process stability.
Proper temperature control prevents salivation in injection molding by optimizing material fluidity and reducing excessive flow at the nozzle.

The Importance of Temperature Control
Temperature control in injection molding is pivotal in maintaining the ideal balance between fluidity and viscosity of plastic materials. When the nozzle temperature is set appropriately, the plastic melts to the desired consistency, preventing it from dripping out of the nozzle excessively.
High Nozzle Temperature and Salivation
Excessively high nozzle temperatures can lead to a more fully melted plastic, enhancing its fluidity. This excessive fluidity increases the risk of salivation as the plastic flows uncontrollably from the nozzle. Such conditions can arise due to heating system failures or improper settings. Thus, maintaining the nozzle temperature within optimal ranges is essential.
Balancing Temperature with Other Parameters
The interaction between temperature and other parameters like injection pressure and material type is critical. For instance, high temperatures combined with high injection pressure can exacerbate drooling issues. It’s vital to balance these factors4 to ensure seamless operation.
Monitoring and Adjusting Temperature Settings
Regular monitoring of temperature settings helps in maintaining process stability. Employing sensors and automated systems can assist in keeping the temperature within desired limits, reducing manual errors. Moreover, adjusting temperature settings5 based on real-time feedback can further prevent salivation.
Temperature plays an integral role in mitigating salivation during injection molding by controlling material characteristics. Understanding its influence allows manufacturers to fine-tune their processes for improved efficiency and product quality.
High nozzle temperature increases salivation risk.True
Excessive heat fully melts plastic, causing uncontrolled flow.
Low temperature prevents salivation in injection molding.False
Low temperature may cause improper melting, not preventing salivation.
How Can Equipment Design Influence Material Flow?
In the world of injection molding, equipment design plays a pivotal role in determining material flow, impacting both efficiency and quality of output.
Equipment design influences material flow through nozzle structure, check ring condition, and overall machine design. Proper design minimizes drooling by controlling flow resistance and maintaining optimal pressure.
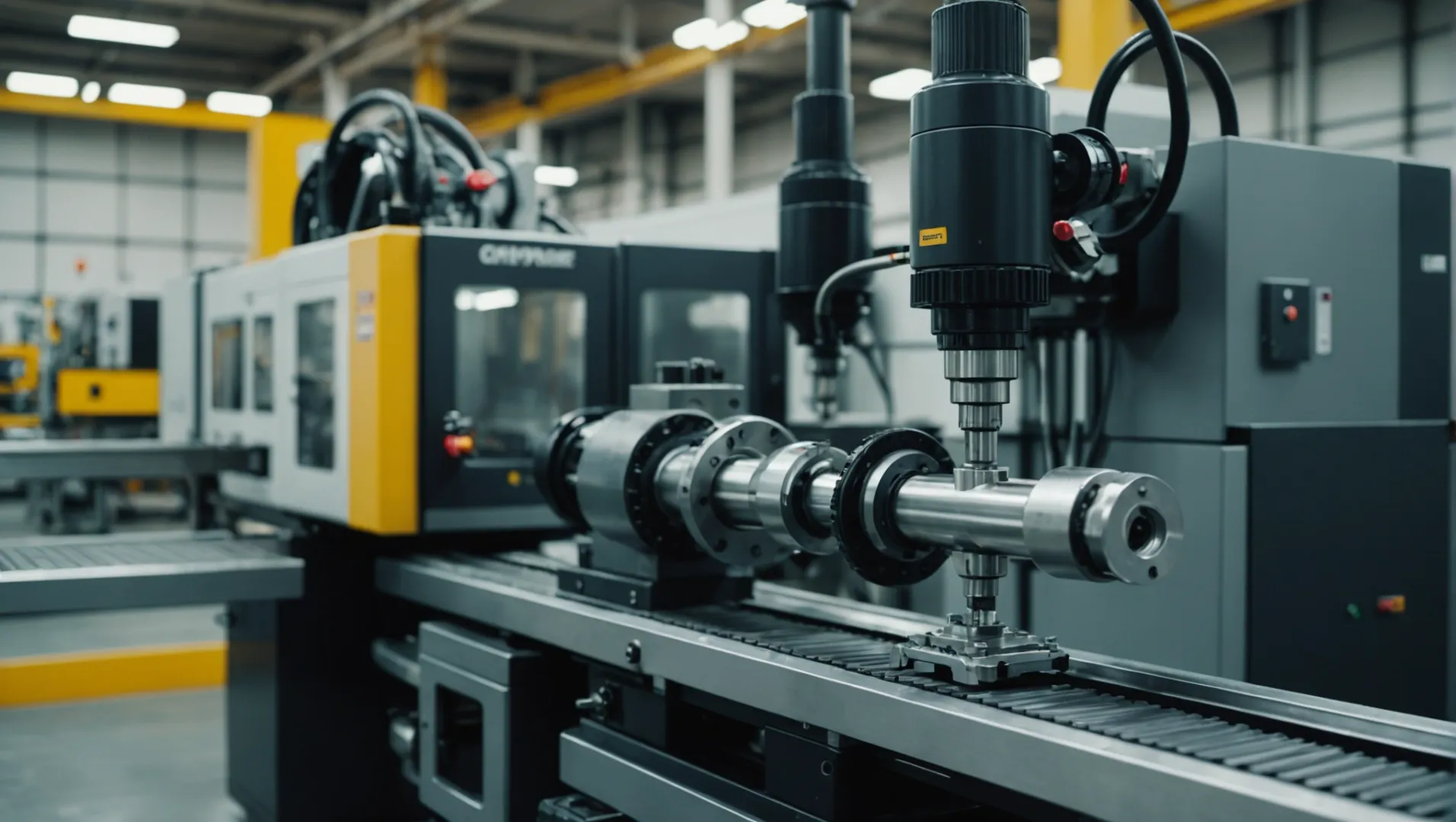
Nozzle Structure
The design of the nozzle6 is a critical component in controlling material flow during injection molding. The shape, size, and surface texture of the nozzle directly affect how plastic flows through it. For instance, a nozzle with a larger aperture may allow for excessive flow, leading to drooling. Conversely, a smaller or optimally-sized nozzle can regulate the flow more effectively.
Example: In high-precision applications, such as those requiring thin-walled parts, a well-designed nozzle can prevent material wastage and ensure consistent quality.
Check Ring Condition
The check ring serves as a gatekeeper, preventing backflow of the molten plastic once injected. A damaged or worn-out check ring can lead to backflow issues, resulting in drooling. Regular inspection and maintenance of the check ring are vital to ensure it functions effectively.
Example: In industries where precision is key, like in the medical device manufacturing sector, maintaining the integrity of the check ring is essential to prevent defects and maintain production standards.
Overall Machine Design
Beyond individual components like the nozzle and check ring, the overall design of the injection molding machine impacts material flow. Machines designed with advanced flow control systems7 can adjust pressure and temperature dynamically to optimize flow characteristics. This adaptability helps reduce issues like drooling by compensating for material variability and environmental conditions.
Example: Modern machines equipped with digital controls can automatically adjust parameters in real-time, ensuring optimal flow and reducing manual intervention.
By focusing on these key aspects of equipment design, manufacturers can significantly enhance material flow, reducing waste and improving product quality.
Nozzle size affects material drooling in molding.True
A larger nozzle can cause excessive flow, leading to drooling issues.
Check rings are irrelevant to material flow control.False
Check rings prevent backflow, crucial for maintaining proper material flow.
What Maintenance Practices Can Prevent Salivation?
Proper maintenance can significantly reduce salivation in injection molding, saving costs and improving product quality.
Regular maintenance practices like inspecting nozzles, replacing worn check rings, and optimizing equipment settings can prevent salivation by ensuring consistent material flow and pressure.
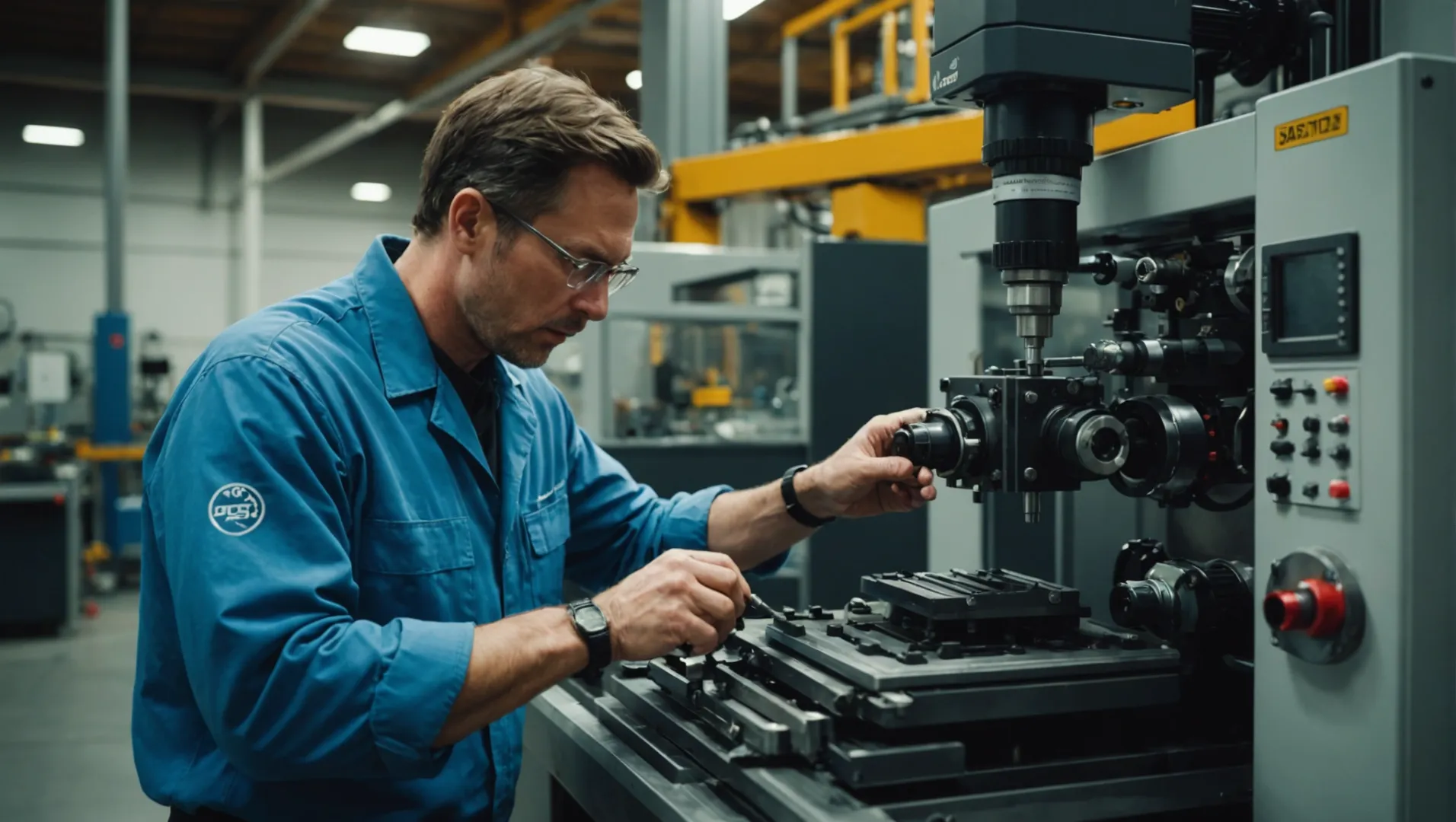
Inspect and Maintain Nozzles Regularly
The nozzle’s structure and condition are critical in preventing salivation. Regularly inspect the nozzle for signs of wear, damage, or blockage that might impede the flow of plastic. It’s important to ensure the nozzle’s aperture is appropriate for your specific application. If the nozzle surface is too smooth or its diameter is too large, it may lead to unwanted drooling.
Nozzle Issues | Maintenance Practice |
---|---|
Worn or damaged nozzle | Replace with a new one |
Inappropriate aperture size | Adjust or change the nozzle size |
Blockages | Clean regularly to prevent build-up |
Regularly Check and Replace Damaged Check Rings
The check ring is vital in controlling the backflow of molten plastic after injection. If damaged, it can lead to salivation due to unregulated material flow. Regular inspection of the check ring and timely replacement of worn parts is crucial. This maintenance practice ensures that the material does not leak through the nozzle, maintaining efficient and clean production.
Optimize Equipment Settings
Equipment settings such as temperature and pressure play a pivotal role in preventing drooling. Ensure that the injection pressure is not excessively high, as this could push more molten plastic through the nozzle than needed. Additionally, calibrating the temperature control systems to maintain an optimal nozzle temperature helps reduce excessive fluidity of the plastic.
- Pressure Control: Avoid setting injection pressure too high, especially for thin-walled products.
- Temperature Regulation: Regularly calibrate temperature controls to avoid overheating.
Schedule Regular Maintenance Checks
Implementing a routine maintenance schedule can preemptively address potential issues leading to drooling. During these checks, focus on:
- Inspecting all components for wear and tear.
- Calibrating equipment settings to ensure they remain within specified ranges.
- Cleaning essential parts to remove any build-up that might affect performance.
By adopting these preventive maintenance practices8, manufacturers can significantly minimize salivation issues, ensuring a smoother and more efficient injection molding process.
Inspecting nozzles prevents salivation in molding.True
Regular inspection of nozzles ensures proper flow and reduces drooling.
High injection pressure reduces salivation risk.False
Excessive pressure increases drooling by pushing more plastic through.
Conclusion
By tackling the root causes of salivation in injection molding, you can significantly boost product quality and efficiency. Take action today to optimize your process!
-
Find materials with varying fluidity levels to control drooling risks.: ShapesPlastics offers a wide variety of engineering plastic that possess better mechanical and/or thermal properties than the more widely used standard … ↩
-
Discover different plastic viscosities to choose the right material.: Plastic viscosity is essentially described as the resistance of a fluid to flow (Davoodi et al., 2018). It is used as an indicator of the size, shape, … ↩
-
Learn how material grades influence drooling in molding processes.: The lower melt flow rate values are associated with grades having higher average molecular weights. This property has a significant influence on the temperature … ↩
-
Learn strategies for balancing key parameters to avoid drooling issues.: Temperature affects the fluidity of the molten material, while pressure affects its flow rate and packing. ↩
-
Discover methods for fine-tuning temperature to prevent material salivation.: Most injection molding machine barrel heating zones are set with a gradually increasing temperature profile from the rear zone to the front or metering zone. ↩
-
Understand how nozzle design impacts flow control in injection molding.: Machine nozzles today can provide a variety of functions, including filtering, mixing, and shut-off of melt flow. ↩
-
Discover how modern systems optimize flow and reduce defects.: New styles of mold water flow controllers are designed to perform like an advanced temperature control unit (TCU) to achieve consistent cooling and quality … ↩
-
Explore additional strategies to maintain injection molding equipment effectively.: 1. Keep Molds and Components Clean and Dry 2. Perform Safety Checks 3. Ensure Your Machine Is Level and Parallel 4. Check Your Oil 5. Check Electrical … ↩