Injection molding is a cornerstone of modern manufacturing, yet achieving optimal efficiency remains a challenge.
Runner design plays a crucial role in boosting injection molding efficiency by optimizing the flow of molten plastic into molds. Properly designed runners can reduce cycle times, minimize waste, and ensure consistent product quality, ultimately enhancing the overall efficiency of the molding process.
While understanding the basic principles of runner design is crucial, exploring detailed strategies and best practices can significantly enhance your injection molding operations. Let’s delve deeper into specific runner design techniques that can transform your manufacturing efficiency.
Hot runner systems minimize material waste in injection molding.True
Hot runners keep plastic molten, eliminating solidified waste, enhancing efficiency.
What Are the Key Differences Between Hot and Cold Runner Systems?
Hot and cold runner systems are pivotal in molding, each offering unique benefits for different applications.
Hot runner systems maintain the plastic melt in a molten state within the mold, eliminating waste and improving cycle time. Cold runner systems, on the other hand, require ejection of solidified runners with each cycle, leading to more material waste but often lower initial costs.
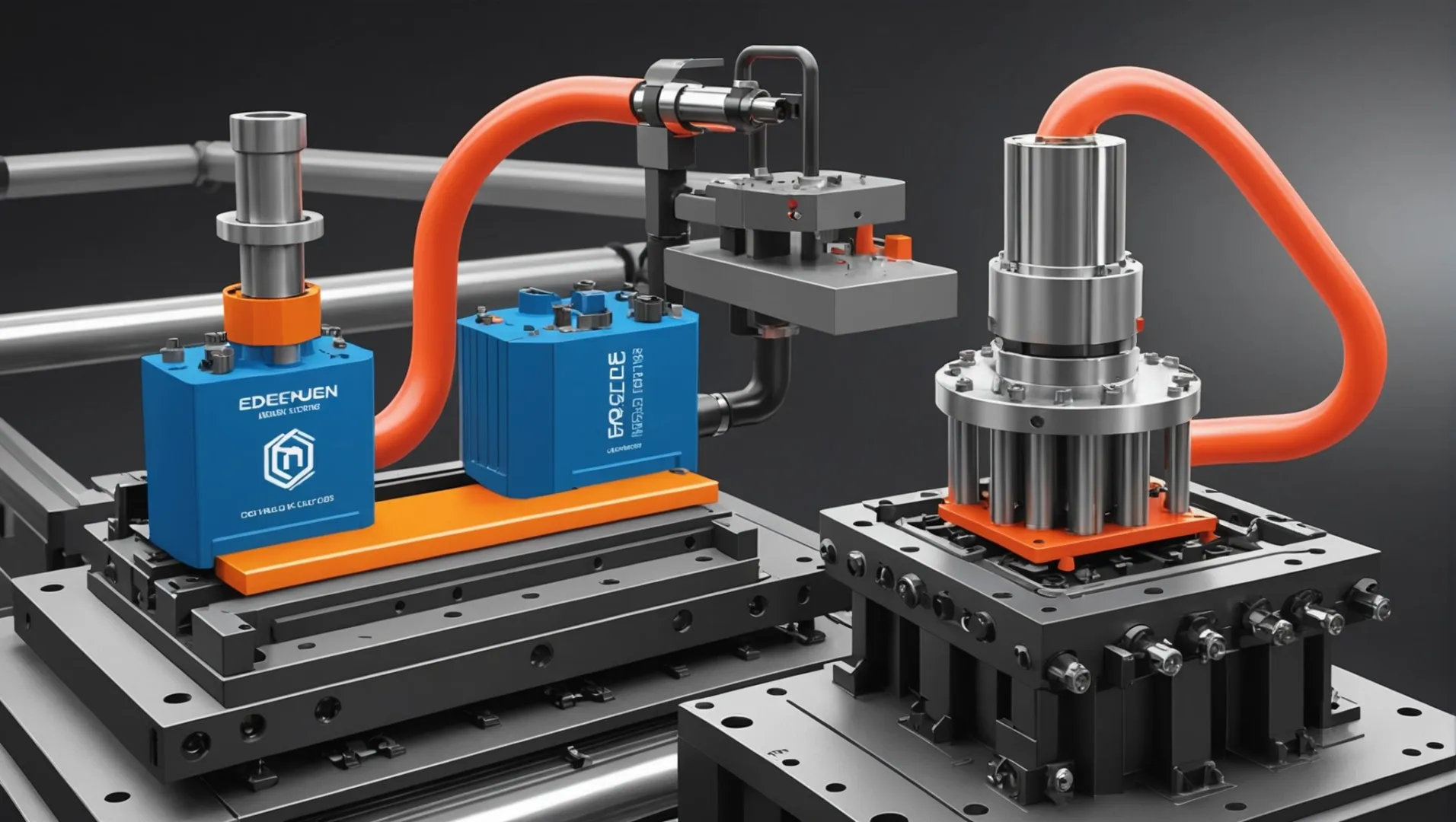
Exploring Hot Runner Systems
Hot runner systems are designed to keep the plastic material hot and in a liquid state while it flows through the runner into the mold cavity. This system can be highly efficient for large-scale production due to several advantages:
- Waste Reduction: Since there’s no solidified runner to eject with each cycle, material waste is minimized.
- Improved Cycle Times: By maintaining a constant temperature, hot runners shorten the cooling phase, thus reducing overall cycle times.
- Consistent Quality: The stable melt temperature ensures uniformity in each part produced.
For instance, in manufacturing large automotive components like bumpers, a hot runner system can maintain optimal melt flow throughout the process, enhancing both efficiency and product quality.
Understanding Cold Runner Systems
Cold runner systems are typically more straightforward and consist of a simple channel cut into the mold that guides the molten plastic into the cavities. The runners solidify along with the parts and are ejected at the end of each cycle. Key characteristics include:
- Lower Initial Costs: The simplicity of cold runner molds generally makes them cheaper to produce.
- Flexibility in Material Use: Cold runners are compatible with a wider range of materials compared to hot runners.
- Design Optimizations: By optimizing design—using short, straight runners or selecting optimal cross-section shapes—the efficiency can be increased significantly.
Consider a scenario where small plastic items like caps or buttons are produced; using a cold runner system can be cost-effective while still achieving reasonable efficiency by refining the runner design.
Comparative Analysis: Hot vs Cold Runner Systems
Feature | Hot Runner System | Cold Runner System |
---|---|---|
Material Waste | Minimal (only sprue if present) | High (runners are waste) |
Initial Cost | Higher (complex system) | Lower (simpler design) |
Cycle Time | Faster (no need to cool solid runners) | Slower (runners need to cool) |
Material Compatibility | Limited to thermoplastics that can tolerate higher temperatures | Wide range of thermoplastics |
Maintenance | More complex due to heaters and manifold systems | Simpler, less maintenance required |
Ultimately, choosing between hot and cold runner systems depends on factors like production volume, material choice, and cost considerations. For large-scale operations requiring high efficiency and minimal waste, hot runners are often preferred. Meanwhile, cold runners can be an excellent choice for smaller production runs or when initial costs need to be minimized. By understanding these differences1, manufacturers can better tailor their processes to achieve optimal efficiency.
Hot runner systems reduce material waste by eliminating solid runners.True
Hot runners keep plastic molten, preventing solid runner waste.
Cold runner systems are more expensive to maintain than hot runners.False
Cold runners are simpler, requiring less maintenance than hot runners.
How Does Runner Size Affect Injection Molding Efficiency?
Runner size is pivotal in injection molding, influencing both efficiency and product quality.
Adjusting runner size impacts injection molding efficiency by balancing flow resistance and material usage. An optimal runner size ensures minimal pressure loss and efficient material flow, reducing cycle times and enhancing product consistency.
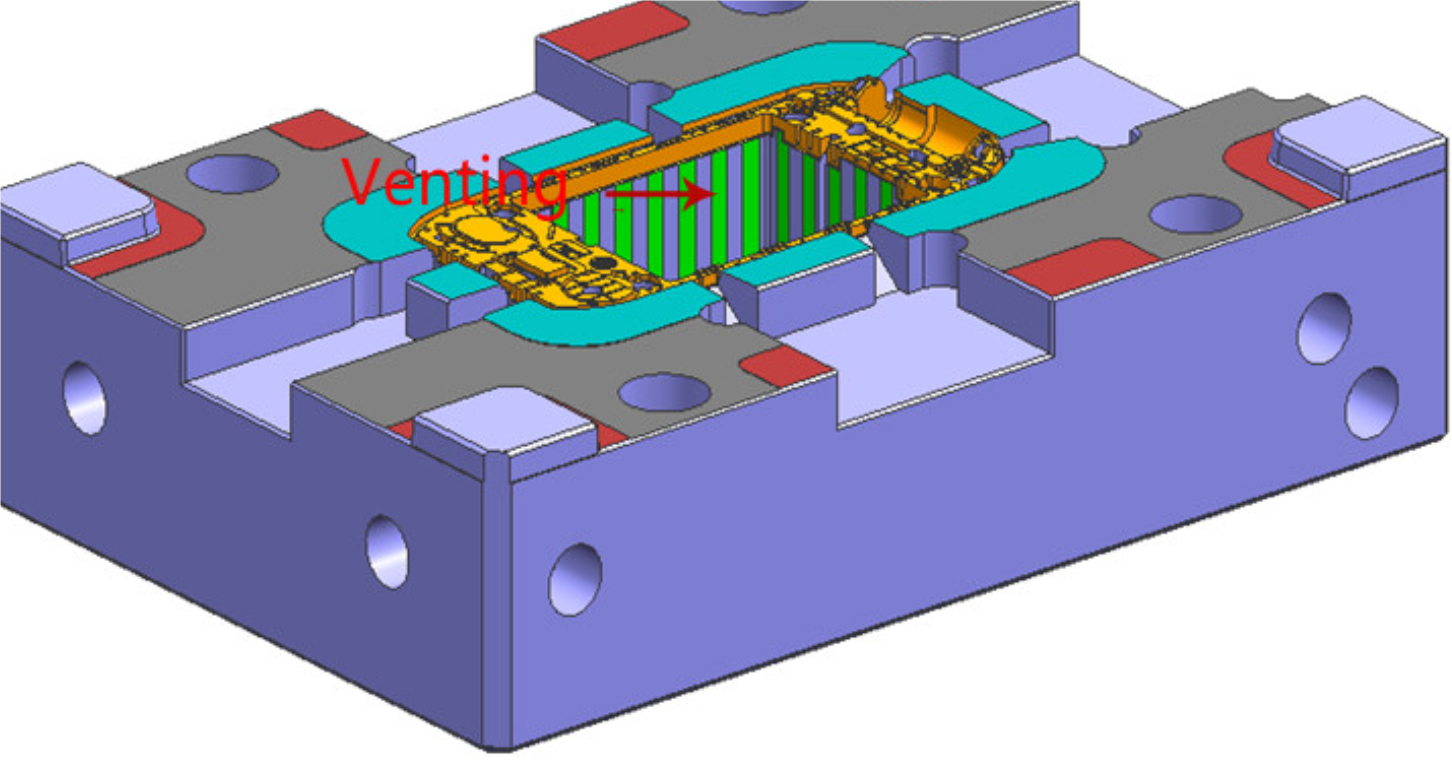
Understanding the Impact of Runner Diameter
The runner diameter directly influences the flow resistance and injection pressure in the injection molding process2. A well-chosen diameter optimizes the flow of plastic, crucial for achieving high efficiency.
- Small Runner Diameter: Ideal for small parts and plastics with good fluidity, this choice minimizes material waste. However, it can increase flow resistance, impacting cycle time if not chosen carefully.
- Large Runner Diameter: Suitable for large parts and plastics with poor fluidity. While it reduces flow resistance, it might result in material wastage if too large.
For example, producing small items like mobile phone cases often requires a 2-4 mm diameter, whereas large items like car bumpers may need over 10 mm.
Importance of Runner Length
Runner length should be minimized to reduce pressure loss and prevent premature cooling of the plastic.
- Short Runners: These are efficient as they decrease flow time, crucial for parts requiring quick cycles.
- Long Runners: May lead to solidification of plastic before filling the cavity, affecting quality and efficiency.
Implementing a multi-point injection method can efficiently shorten runner length.
Optimizing Runner Layout for Efficiency
A well-planned runner layout can significantly enhance efficiency by ensuring balanced filling and minimal flow resistance.
- Balanced Runner Design: This approach ensures equal pressure distribution across cavities, avoiding overfilling or underfilling.
- Smooth Flow Channels: Reducing turns and corners in the runner design minimizes resistance, enhancing flow rate.
Using runner balancing software3 can help achieve an ideal layout.
Evaluating Material Properties
Material characteristics such as fluidity and shrinkage significantly affect runner size decisions.
- Fluidity Considerations: Plastics with high fluidity can use smaller runners; those with low fluidity require larger sizes to maintain efficiency.
- Shrinkage Factors: High-shrinkage materials might need adjustments in runner design to ensure dimensional stability post-molding.
Considering these factors ensures that the chosen runner size supports optimal injection molding outcomes.
Smaller runners reduce material waste in injection molding.True
Small runners minimize material usage but may increase flow resistance.
Large runner diameters always enhance injection molding efficiency.False
Large runners reduce resistance but can waste material if oversized.
Why Is Balanced Runner Layout Essential for Consistent Quality?
Ensuring consistent quality in injection molding hinges on a well-balanced runner layout.
A balanced runner layout is vital for maintaining consistent quality in injection molding. It ensures uniform filling of cavities, preventing defects like underfilling or overfilling, and stabilizing the quality of the molded parts. By optimizing the runner layout, manufacturers can achieve higher efficiency and better product consistency.
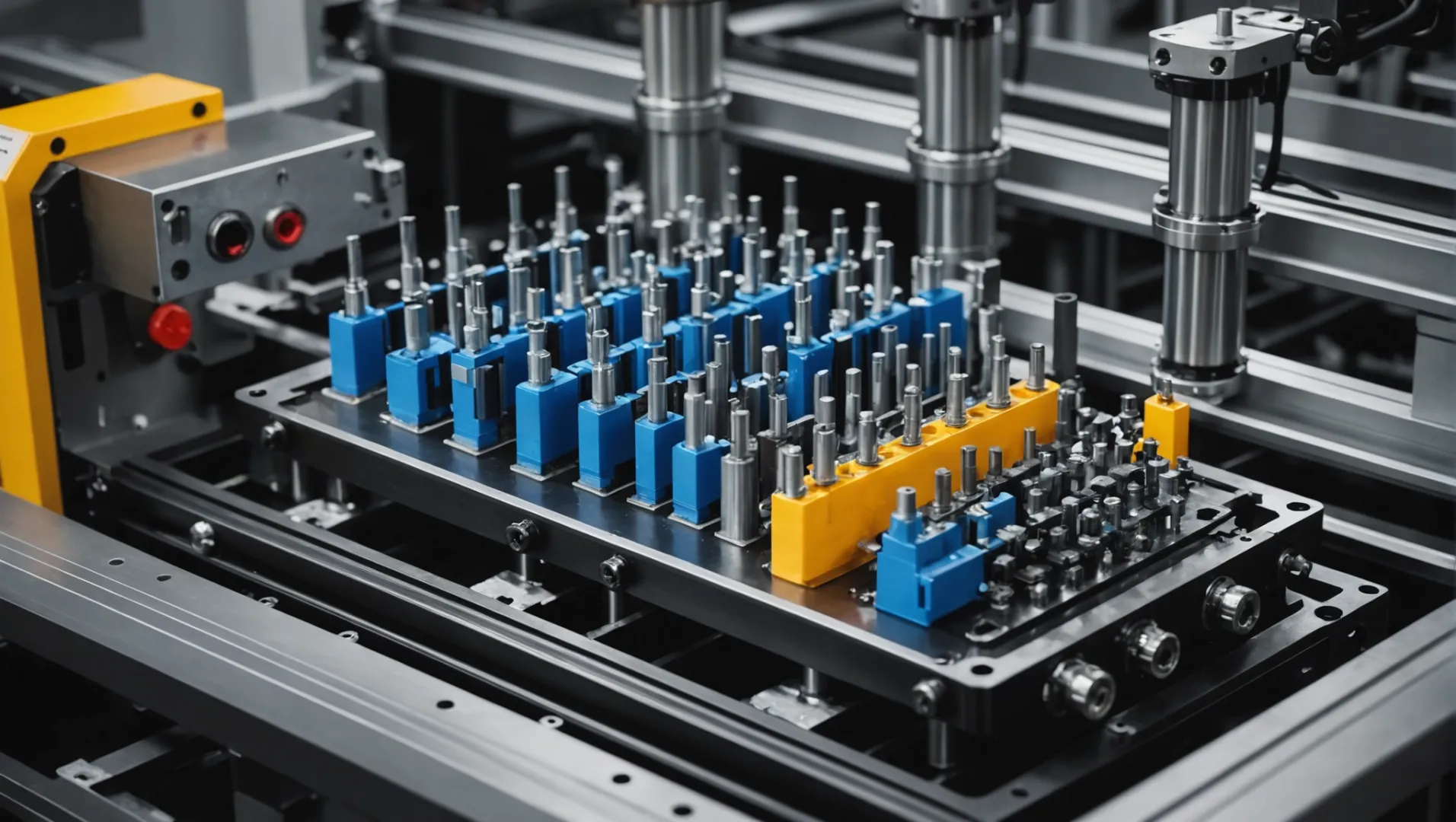
Understanding the Role of Runner Layout
A balanced runner layout4 is crucial because it ensures that the molten plastic fills each cavity evenly during the injection process. This uniform filling is essential to avoid defects such as short shots, flash, or warping, which can occur when some cavities are underfilled or overfilled. A consistent runner layout allows for stable pressure and temperature distribution across all cavities, ensuring that each molded part meets the required quality standards.
Techniques for Achieving Balance
-
Runner Balancing Software
Utilizing software tools can assist in designing a balanced runner system. These programs simulate the flow of plastic through the runner system, helping designers adjust the size and layout to achieve uniform filling times and pressures.
-
Empirical Formulas
Experienced designers often rely on empirical formulas to calculate optimal runner dimensions. These calculations take into account factors like the number of cavities, plastic viscosity, and desired cycle time.
-
Adjusting Branch Angles and Lengths
In multi-cavity molds, adjusting the branch angles and lengths can help distribute the plastic evenly. This involves tweaking the geometry of the runners so that each cavity receives an equal volume of material in a synchronized manner.
Challenges and Solutions
Challenge: Variations in cavity filling due to unbalanced runners can lead to inconsistent part quality.
Solution: Implementing a balanced runner layout using streamlined flow channels5 minimizes pressure loss and reduces cycle times.
Case Study: Improving Efficiency with Balanced Runners
Consider a manufacturer producing complex multi-cavity molds for automotive components. Initially, they faced issues with varying product quality due to an unbalanced runner layout. By adopting a balanced design approach, including software simulation and empirical adjustments, they achieved uniform cavity filling. This resulted in a 15% reduction in cycle time and significant improvements in part consistency.
In summary, a balanced runner layout not only enhances the efficiency of the injection molding process but also ensures that each product meets stringent quality standards.
Balanced runner layout prevents injection molding defects.True
A balanced layout ensures uniform filling, preventing defects like warping.
Unbalanced runners reduce cycle time in molding processes.False
Unbalanced runners cause uneven filling, potentially increasing cycle time.
How Do Material Properties Influence Runner Design Decisions?
Material properties directly impact runner design, dictating flow channel size and layout adjustments for optimal efficiency.
Material properties such as plastic fluidity and shrinkage significantly influence runner design decisions. Adjustments in runner size and layout cater to these properties, ensuring smooth flow, reducing waste, and maintaining product quality. Understanding these material characteristics is essential for enhancing injection molding efficiency.
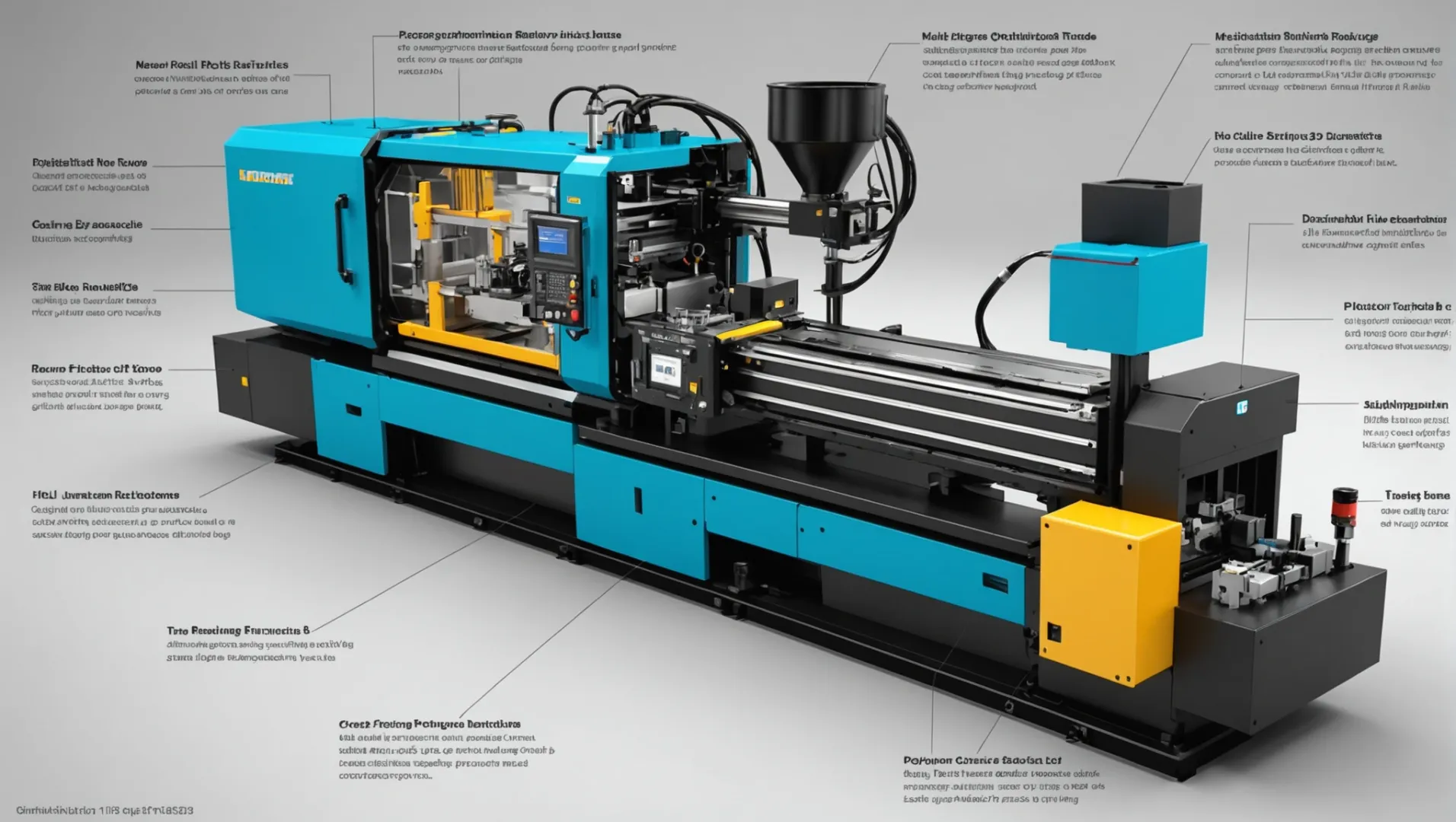
Understanding Plastic Fluidity
The fluidity of a plastic material dictates how easily it can flow through a runner system during the injection molding process. For instance, materials like polyethylene and polypropylene exhibit high fluidity, allowing for the use of smaller runner sizes. These materials require less force to move through the runner, reducing cycle times and energy consumption.
Conversely, plastics with lower fluidity, such as polycarbonate and polyphenylene ether, necessitate larger runner sizes to facilitate proper flow. This adjustment is crucial to prevent defects and ensure that the molten plastic reaches all parts of the mold efficiently.
Moreover, runner length also comes into play. Shorter runners are preferred for high-fluidity plastics to minimize pressure loss and prevent premature cooling. For materials with lower fluidity, longer runners may be needed, but they must be carefully designed to maintain sufficient heat and pressure throughout the flow.
Material Shrinkage Considerations
Shrinkage is another critical factor that influences runner design. Materials with high shrinkage rates, such as ABS plastics, require careful consideration of runner dimensions. A larger diameter may be necessary to compensate for the material’s tendency to contract upon cooling. Additionally, leaving a shrinkage margin in the design can prevent dimensional inaccuracies in the final product.
The layout of the runner system should also be adjusted based on shrinkage characteristics. A well-designed layout can ensure that the material fills the mold evenly despite shrinkage tendencies, maintaining product consistency and quality.
To illustrate, let’s examine a comparison of material properties and their corresponding runner design implications:
Material | Fluidity | Shrinkage Rate | Runner Size Suggestion |
---|---|---|---|
Polyethylene | High | Low | Small |
Polycarbonate | Low | High | Large |
Polypropylene | High | Moderate | Small |
ABS | Moderate | High | Large |
Tailoring Runner Designs to Material Properties
Incorporating the unique properties of different materials into runner design requires a nuanced approach. Beyond fluidity and shrinkage, factors like thermal conductivity and chemical resistance also play roles in determining optimal design features.
For example, some materials might require hot runner systems6 to maintain consistent temperatures throughout the process, minimizing the risk of premature solidification. Others may benefit from cold runner systems7 that are optimized for cost-effectiveness in high-volume production.
Ultimately, understanding and leveraging material properties allows manufacturers to optimize their injection molding processes, reducing waste, improving cycle times, and ensuring high-quality outputs.
High fluidity plastics use smaller runners.True
High fluidity materials require less force to flow, allowing smaller runners.
ABS plastics have low shrinkage rates.False
ABS plastics exhibit high shrinkage, needing larger runner designs.
Conclusion
Optimizing runner design is pivotal in elevating injection molding efficiency. By applying these insights, manufacturers can achieve faster cycles, less waste, and superior product quality.
-
Discover in-depth insights on choosing between hot and cold runner systems.: Hot runner systems generally possess significantly faster cycle times than cold runner systems. The elimination of the runners greatly reduces the number of … ↩
-
Explores how runner diameter affects molding efficiency and quality.: Runner diameter plays a significant role: if it’s too small, it can freeze too quickly, creating too small of an effective flow channel to pack … ↩
-
Learn how software aids in optimizing runner layouts efficiently.: With the power of Moldex3D Flow, you can clearly observe melt flow behavior, accurately detect potential weldline and detect short shot, air trap problems, etc. ↩
-
Learn why uniform filling is critical for defect-free molding.: The design is to ensure each cavity has a balanced material flow and is filled out at the same time. for example, radiate runners, linear runners, Y-shape … ↩
-
Explore how reducing pressure loss improves cycle times.: This blog post provides 6 solid, repeatable steps that create the best approach to streamline a plastic part project utilizing custom injection molding. ↩
-
Explore how hot runners improve temperature consistency and reduce waste.: Also, with hot runner systems, lower injection pressures can generally be used, which will reduce mold and platen deflection and keep flash … ↩
-
Learn about cost-effective benefits for high-volume production.: Cold runner molds are also much less expensive, and much simpler for manufacturers to design and produce. This helps reduce tooling costs and lead times for … ↩