Ever thought about what happens inside an injection mold? Let’s jump in and discover the wonder behind the process!
Injection molds have essential parts, such as the casting system, molded parts, guide parts, ejection mechanism, cooling system and exhaust system. These components help plastic melt flow smoothly. They shape precisely. Solidification happens without defects.
Picture yourself in a busy factory filled with the sound of machines. My first time with an injection mold felt like watching a precise dance of machines. Every piece does its job perfectly to create flawless plastic parts.
The casting system acts as the leader, guiding melted plastic through pathways like a skilled orchestra conductor. Once, I spent a long night adjusting a branch channel, making sure every cavity got filled. The joy when it finally worked was worth every single coffee cup.
Molded parts like the cavity and core are like artists shaping the final piece. Even a small mistake in alignment can waste hours of effort. Guide parts, such as the guide pin and sleeve, are essential.
The ejection mechanism quietly pushes out the finished product without issues. The cooling system plays a crucial role, stopping overheating and deformation. It cools everything perfectly.
The exhaust system might not seem exciting, but it vents out unwanted air and gases. This reminds me how little things, often unnoticed, greatly impact the final result.
All these systems join forces to create excellent plastic components. Knowing how each part works is very important in mastering injection molding.
The ejection mechanism removes the part from the mold.True
The ejection mechanism pushes the finished part out of the mold.
Cooling systems in molds increase production time.False
Cooling systems reduce production time by speeding up solidification.
How Does the Casting System Ensure Proper Flow?
Curious about how hot, liquid metal flows into complex molds? This is an exciting story. Welcome to the captivating realm of casting systems.
A casting system controls the flow. The main channel guides the material. Branch channels spread it evenly. Gates adjust the speed and quantity into the mold. Precision is very important in every cast. Each piece matters.
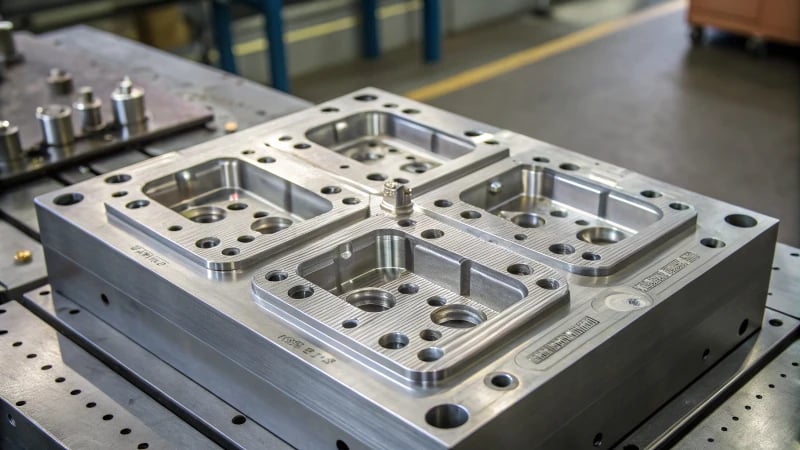
Components of the Casting System
The casting system works like helpful staff behind the scenes of a theater show. It quietly makes sure everything goes perfectly without any problems. There are three main parts: the main channel, branch channel, and gate.
Main Channel
The main channel acts like a big road linking the injection machine’s nozzle to the branch channels. Its cone shape is not a mistake. This design helps the material move easily, changing direction and pressure smoothly.
Main Channel | Function |
---|---|
Shape | Conical |
Role | Guides melt, adjusts pressure |
My first time seeing this was unforgettable. It felt like watching a beautiful dance.
Branch Channel
Branch channels are like smart road systems that spread traffic from a big highway. They cleverly change the flow direction, giving material evenly to every cavity or gate. The shape—either round or trapezoid—affects resistance and speed.
Learn more about channel design1
Precision is very important, so each cavity receives its share at the same time.
Gate
The gate controls how fast material enters the cavity. Its small size helps manage flow carefully, much like a conductor guiding musicians.
Changing the gate size once improved surface quality a lot. It was amazing.
Importance in Manufacturing
A good casting system is key in making products. It saves material, increases accuracy, and reduces flaws like air pockets or uneven filling.
Moreover, knowing these parts matters for mold planners3 who want nice looks and great function.
Real-world Application
In real life, engineers like me use computer programs to see how these systems work. By changing channel shapes and gate sizes on the computer, people probably guess the results and adjust designs before real production begins.
Discover CAD simulation techniques4
This detailed system helps each casting step follow industry rules, giving consistent results that please even the toughest manufacturing standards. Whether you create products or build systems, designing these correctly is a must.
Main channels are typically cylindrical in shape.False
Main channels are conical, not cylindrical, to adjust pressure.
Gates influence injection speed and surface quality.True
Gates regulate flow rate, affecting speed and surface marks.
How Do Molded Parts Shape Our Everyday Products?
Ever thought about the stylish devices we use every day? Molded parts bring them to life!
Molded parts form the backbone of product design. They give products strength, beauty and exact function. These parts shape both the outside and inside of items. Every piece looks the same and offers high quality, especially during mass production.
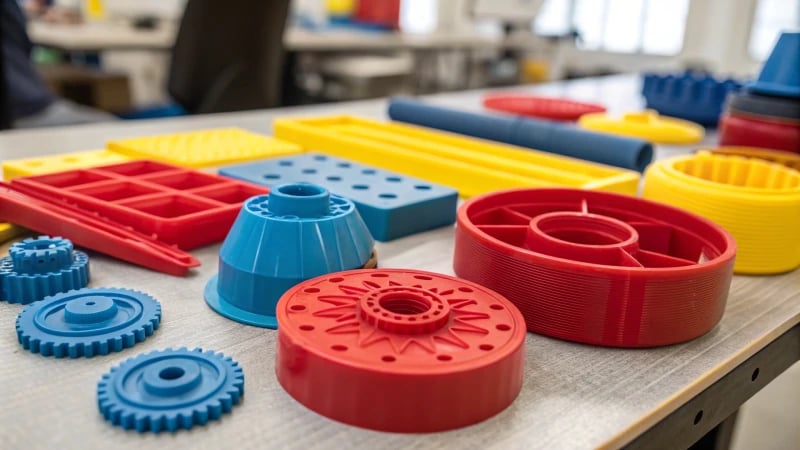
The Anatomy of Molded Parts
In the beginning of my career, the transformation of raw materials into finished products intrigued me. Molded parts are very important in this transformation. Picture the mold as an artist with clay. The cavity shapes the outside, creating smooth surfaces and precise sizes. The core crafts internal details like grooves or holes.
Functionality and Precision
Precision holds great importance in injection molding. Once, during a consumer electronics project, every millimeter was critical. The design of the cavities and cores makes sure molten plastic fills every space perfectly. Product parts align effortlessly, similar to puzzle pieces, due to the casting system5 that expertly handles melt flow and pressure.
Efficiency in Manufacturing
Efficiency drives manufacturing—a lesson I learned on a tight-schedule packaging project. The ejection mechanism removes finished items quickly, cutting down time. An effective cooling system keeps mold temperatures optimal, avoiding issues like shrinkage or warping.
Mold Component | Primary Function |
---|---|
Cavity | Shapes external features |
Core | Shapes internal structures |
Ejection Mechanism | Removes finished items swiftly |
Speed is especially important in packaging where quality stays a priority. The exhaust system6 helps by removing air and gases during molding, preventing mistakes.
Enhancing Product Design
Molded parts bring many design options. Adjusting the gate allows control over the speed and smoothness of melt flow into cavities. This freedom means detailed designs do not need to sacrifice function or appearance.
With advanced injection mold techniques7, companies respond to market demands swiftly while maintaining high quality. Molded parts continue to efficiently create products, satisfying both practical and creative needs across different industries.
Cavity shapes internal features of molded parts.False
The cavity shapes external features, while the core shapes internal ones.
Ejection mechanism reduces cycle times in manufacturing.True
The ejection mechanism enables quick removal of products, speeding up cycles.
How Do Guide Parts Enhance Mold Precision?
Do tiny parts really have a big impact on mold precision? Discover guide parts and witness their wonderful effects!
Guide parts such as guide pins and sleeves hold great importance for accurate alignment in injection molding. This precise alignment keeps wall thickness and dimensions of plastic products consistent. Defects get prevented through this process. It increases product quality. It also raises operational efficiency.
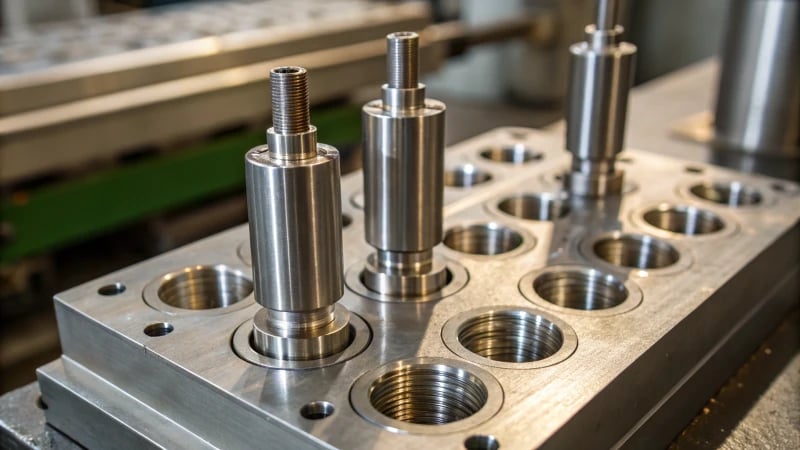
The Role of Guide Pins and Guide Sleeves
Have you ever noticed how some products come perfectly aligned right from the mold? Guide pins and sleeves work quietly behind this precision. The guide pin8 rests on one part of the mold, while the guide sleeve receives them on the other side. Everything lines up just right when molds meet.
Component | Function |
---|---|
Guide Pin | Ensures precise alignment between molds, aiding in consistent product dimensions. |
Guide Sleeve | Facilitates smooth insertion of guide pins, enhancing alignment and reducing lateral movement. |
This alignment is not magic. It’s necessary for even wall thickness9, which affects the product’s look and feel.
Impact on Mold Precision
Once, a batch was slightly off because of pressure changes during injection. Guide parts showed their true value by stopping molds from moving under stress. They keep everything steady and accurate throughout production.
Moreover, guide parts withstand lateral pressure during injection molding, preventing the mold from shifting under stress. This stability ensures that each component of the mold functions as intended, contributing to the overall precision of the final product.
Improving Product Quality
In big manufacturing jobs, even a small defect really matters. By ensuring exact alignment, guide parts help produce high-quality plastic products with minimal defects. This level of precision reduces waste and enhances operational efficiency, a significant concern in large-scale manufacturing settings.
Guide parts helped save a project by keeping everything perfectly aligned. Wasted material dropped. The ejection process10 got smoother with less damage.
For those focused on precision, knowing the role of guide parts is crucial. They improve product quality and make manufacturing more efficient.
Guide pins align molds for consistent dimensions.True
Guide pins ensure precise alignment, aiding in consistent product dimensions.
Guide sleeves increase lateral movement during molding.False
Guide sleeves reduce lateral movement, enhancing alignment and mold precision.
What Is the Ejection Mechanism’s Purpose?
Do you ever wonder how detailed plastic pieces smoothly exit molds? The ejection mechanism is the real hero here. This tool works tirelessly in injection molding. It releases each part with precision. It truly excels in this task.
The ejection mechanism in injection molding allows for easy removal of molded plastic parts from the mold. Parts remain undamaged and undeformed. Push rods and plates play important roles in this process. They work together for this vital task. They stand crucial.
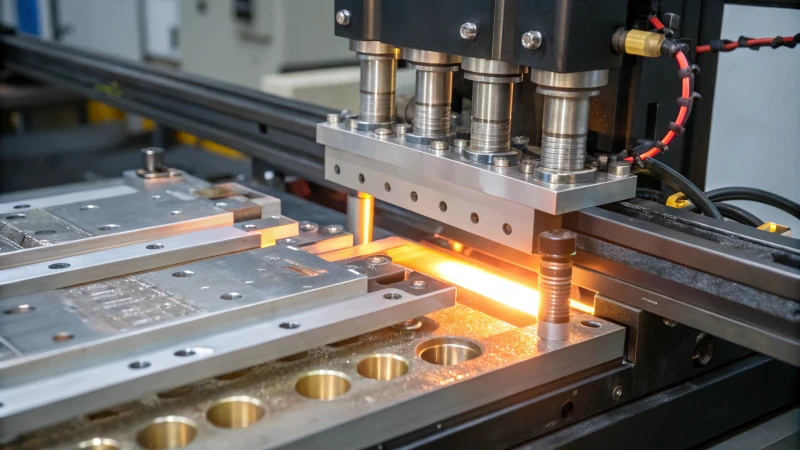
The Role of the Ejection Mechanism
Picture yourself working on a project where every detail matters – no room for mistakes, right? That’s what happens in the world of injection molding. The ejection mechanism11 is crucial. It’s like a gentle push that helps each plastic piece leave its mold without damage. I’ve noticed firsthand that avoiding warp or break can really influence product quality.
Components Involved
During my time with many molds and designs, I have learned to value the group of parts in the ejection mechanism:
- Push Rods: These touch the plastic first, gently helping each part out of its snug mold space.
- Push Plates: Like a supportive friend, they help everything go smoothly by spreading out the force.
- Push Tubes: With complex shapes, these provide extra assistance.
Component | Function |
---|---|
Push Rod | Initiates contact with the product |
Push Plate | Distributes force evenly |
Push Tube | Supports complex shapes during ejection |
How It Works
After a long cycle in injection molding, watching the mold open feels magical as the ejection system begins its work. Think of a well-timed dance where push rods softly nudge the cool product out, all perfectly timed to avoid any harm. It’s like seeing an artist carefully show their masterpiece.
Importance in Product Design
For people like me, understanding the details of ejection mechanisms has changed how I design. Imagine realizing that altering a design element boosts efficiency and quality. Balancing material properties, shape complexity, and cooling time creates the perfect ejection process. This way, I keep production smooth and standards high, making sure each product fits its design plans without any compromise while maintaining quality standards12.
Ejection mechanisms prevent product warping.True
They ensure smooth release of molded parts, avoiding defects like warping.
Push plates provide a smaller surface area than push rods.False
Push plates offer a larger surface area to distribute force evenly.
Why Is a Cooling System Essential in Injection Molding?
Have you ever thought about why a cooling system is the quiet champion of injection molding? I often did, until I noticed how it changed our production line completely.
A cooling system in injection molding is very important to keep the mold at the right temperature. It lets the plastic melt harden quickly. This speeds up production. It reduces defects. Fewer errors occur. Products have better size accuracy.
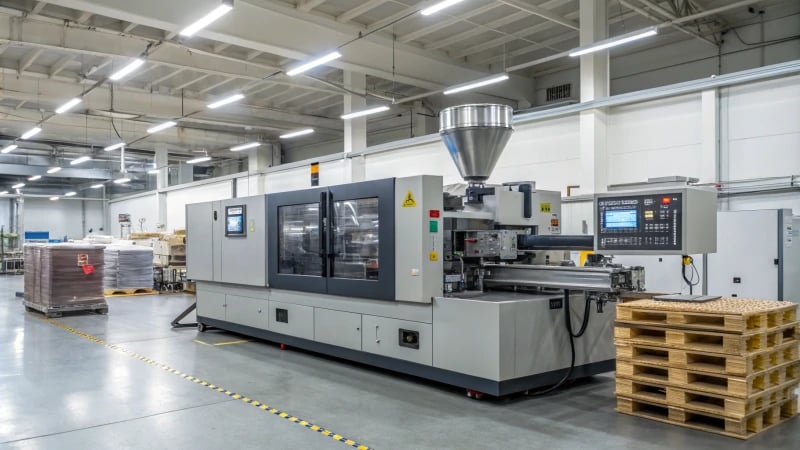
The Role of Cooling Systems in Injection Molding
Memories of my first time seeing a cooling system at work remain clear. It felt magical. Molten plastic turned into a solid item as intricate channels carried coolants through the mold. These systems circulate coolant, often water, to draw heat away from the mold. The process fascinates many because while the plastic melt fills the mold, it releases a lot of heat that must be handled effectively.
Key Functions of Cooling Systems:
- Rapid Solidification: Helps the plastic harden fast, cutting cycle time and raising production efficiency.
- Dimensional Accuracy: Keeps steady dimensions by controlling cool rates, stopping warping or shrinkage.
Components of a Cooling System
- Cooling Channels: Amazing hidden workers that boost heat exchange between mold and coolant. The design and location13 of channels matter for even mold cooling.
- Temperature Control Units: Steady the coolant’s heat, making sure each cycle is identical to the last one.
Impact on Production Efficiency
A good cooling system raises production efficiency. Shorter cycles let manufacturers like us increase output without losing quality. High-volume manufacturing depends on even small gains in efficiency for huge improvements.
Feature | Benefit |
---|---|
Rapid Solidification | Shorter Cycle Times |
Dimensional Accuracy | Improved Product Quality |
Temperature Control | Consistent Production |
Reducing Defects Through Proper Cooling
Defects like warping or shrinkage often arise when cooling is wrong. A well-planned cooling system prevents these by making sure the product keeps its shape and size throughout.
Additionally, this system lowers internal stress from uneven cooling, which leads to cracking and weaknesses. The exhaust system14 is very important too. It removes air and gases during molding, cutting possible defects.
Understanding these parts of injection molding greatly benefits professionals. They learn to design molds that meet style and function needs while optimizing for big-scale jobs with fewer faults.
Cooling systems reduce cycle time in injection molding.True
Cooling systems speed up solidification, thus reducing the cycle time.
Without cooling systems, molds can warp and shrink.True
Cooling controls the rate, preventing warping and shrinkage of molds.
Conclusion
This article explores the essential components of injection molds, detailing the functions of casting systems, molded parts, guide parts, ejection mechanisms, cooling systems, and exhaust systems.
-
Understanding branch channel design helps optimize material flow, improving product quality by ensuring even distribution. ↩
-
Exploring gate designs offers insights into controlling flow rate and minimizing defects. ↩
-
Learning about mold designers’ roles reveals how design optimizations enhance manufacturing efficiency. ↩
-
Exploring CAD simulation techniques showcases predictive tools for refining casting system designs. ↩
-
Explore how casting systems control melt flow and pressure for precision molding. ↩
-
Learn how exhaust systems prevent flaws by removing air and gases during molding. ↩
-
Discover cutting-edge techniques that enhance design flexibility and product quality. ↩
-
Discover how guide pins ensure precise alignment between mold components during injection molding. ↩
-
Learn about the significance of achieving uniform wall thickness for structural integrity in molded products. ↩
-
Explore how precise mold alignment minimizes damage during the ejection of molded products. ↩
-
Learn about the fundamental role of ejection mechanisms in molding processes. ↩
-
Discover techniques for ensuring high-quality production outcomes. ↩
-
Discover best practices for designing cooling channels to enhance heat exchange efficiency. ↩
-
Understand how exhaust systems help remove trapped air, enhancing product quality. ↩