Have you ever wondered why the length of a film gate is really important in shaping?
A film gate usually measures between 0.5 to 2mm. This very short length reduces pressure and heat loss during molding. It helps the melted material flow efficiently into the cavity. The precise length relies on factors like product size, material traits and how the mold is designed. Different elements dictate the exact measurement. Different needs.
When I started in mold design, I struggled with gate length details. It was like solving a puzzle where every part counted. A tiny mistake in length could mess up the molding. Imagine making a thin smartphone case. A short gate, from 0.5 to 1mm, works perfectly because it stops the plastic from cooling too soon. For larger items, you need a longer gate but not more than 2mm. This keeps the process smooth.
Mold design also involves knowing the material well. Plastics flow differently. Polystyrene flows easily, allowing for a shorter gate. Add glass fibers and you need a longer gate to stop clogs. The mold’s complexity affects gate length too. I once worked on a project with a complex mold. High precision meant shorter gates were fine. Deviations in accuracy needed adjustments to avoid uneven flow.
These details taught me a lot. Each decision affects efficiency and quality. Early lessons on gate lengths remind me how mold design combines science and art.
Film gate length affects pressure and heat loss.True
Shorter film gates reduce pressure and heat loss, aiding efficient flow.
All film gates are exactly 1mm in length.False
Film gate lengths vary from 0.5 to 2mm based on several factors.
How Does Product Size and Wall Thickness Affect Gate Length?
Do you ever think about how the size of your big project affects its creation? Let’s explore the interesting world of injection molding, where size is really important.
Product size and wall thickness are important in deciding gate length in injection molding. Smaller items with thin walls usually need gates around 0.5-1mm. Bigger products with thicker walls might need longer gates. These gates generally do not go beyond 2mm.
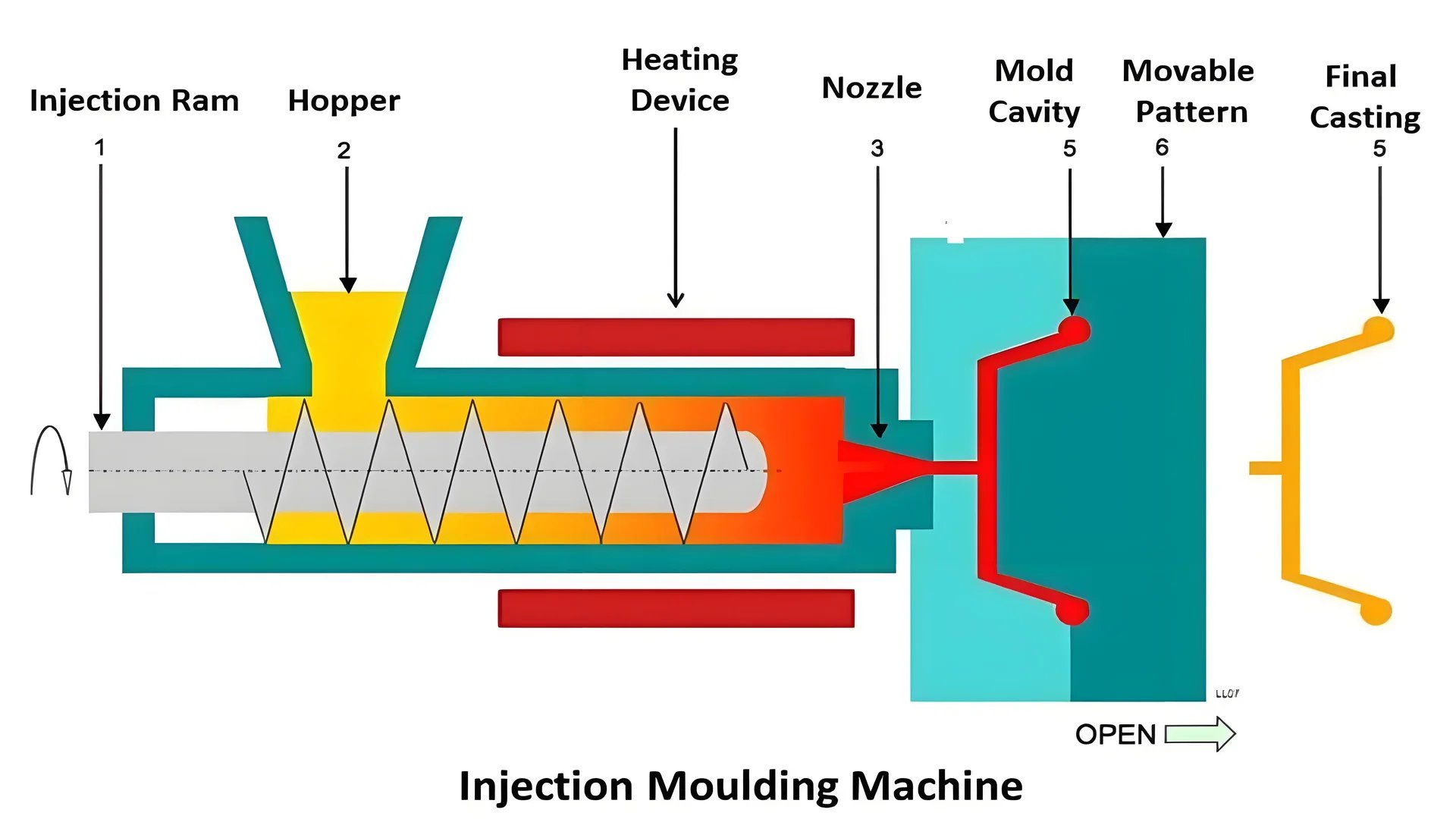
Understanding the Role of Gate Length
In the complex process of injection molding, gate length acts like a guide, directing flow for good results. I have seen how a well-set gate allows melted material to fill all parts of a mold smoothly, keeping the final product strong. It’s similar to baking a cake – too little or too much can ruin it.
Typically, the gate length is short, ranging from 0.5 – 2mm, as this minimizes pressure and heat loss.
Effect of Product Size
Remember trying to get a big couch through a tiny door? Ignoring product size in molding is like that. Smaller items, like thin plastic sheets or fragile boxes, need shorter gates (about 0.5-1mm). They fill fast and do not cool too early, much like pouring pancake batter on a hot pan. Bigger products need more space to flow well and should not exceed 2mm.
Product Size | Typical Gate Length |
---|---|
Small | 0.5 – 1mm |
Large | Up to 2mm |
Influence of Wall Thickness
Wall thickness is different. Thin walls are like book pages – easy with shorter gates. Thicker walls are like heavy books needing more time. Longer gates help prevent the material from hardening too soon.
Material Properties Impact
Material type changes everything. Normal plastics feel like spreading soft butter – simple with short gates. Add things like glass fibers and it’s more like spreading sticky peanut butter, needing more time and a slightly longer gate, maybe around 2mm.
Materials with high fluidity allow for shorter gates; however, materials with additives may necessitate longer gates within the 2mm limit.
Mold Design Considerations
Mold design often affects gate length. Precise molds keep gates short, like threading a needle. But for complex shapes, small changes are needed to fit all details without stopping flow.
- For more on mold processing1, understanding details is important.
- Complex mold shapes need the right gate lengths for good flow.
Practical Applications
Consider Jacky, a friend who designs electronic gadgets nicely and effectively. He’s skilled in balancing good looks with practicality, keeping molds efficient and nice-looking. By learning these basics, Jacky avoids slowing down production or wasting material.
For further insights on design considerations2 in injection molding, additional resources can be explored.
Smaller products need longer gate lengths in molding.False
Smaller products typically require shorter gate lengths for efficient filling.
Thicker walls require shorter gates for faster cooling.False
Thicker walls often need longer gates to accommodate more material volume.
Why Does Material Fluidity Matter in Gate Design?
Think of pouring syrup into a mold – a process that decides the result. Material flow works the same way. In gate design for injection molding, how materials move is very important. It shapes both quality and efficiency. Flow is everything.
Material flow impacts gate design by altering gate length and type. These factors directly determine how smoothly material fills the mold cavity. This has effects on both product quality and how efficiently items are produced. Product quality relies heavily on this process. Efficiency also depends on it significantly.
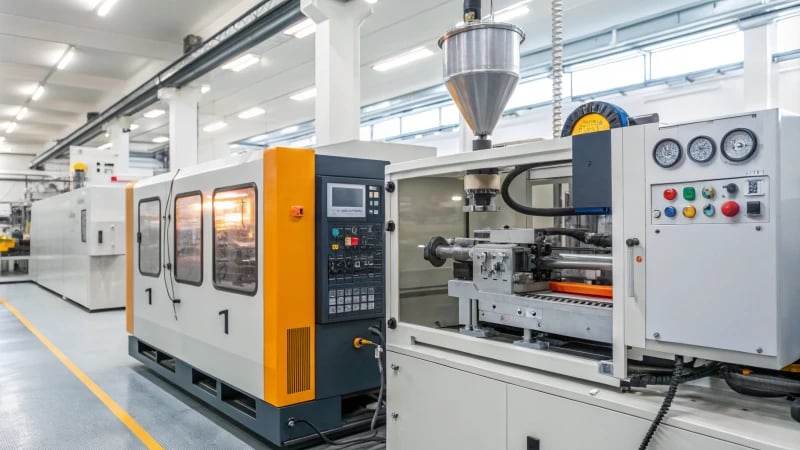
Understanding Material Flow
When I first explored injection molding3, I learned quickly that material flow is very important. Material flow describes how easily a material moves under pressure, similar to how syrup spreads smoothly on pancakes. In injection molding, the way plastic moves through the system and into the mold can either succeed or fail the product.
-
High Flow Materials: Imagine pouring a thin smoothie into a glass. High flow materials like polypropylene move easily through short gates, reducing pressure and heat loss.
-
Low Flow Materials: Picture trying to push thick honey through a small hole. Materials with fillers, like glass fiber, need longer gates for smooth flow without losing pressure.
Gateway Length Factors
Product Type | Typical Gate Length |
---|---|
Small & Thin-Walled | 0.5 – 1mm |
Large & Thick-Walled | Up to 2mm |
Product Size and Wall Thickness
Designing small, thin products involves using shorter gates. It’s similar to getting the smoothie to all parts of the glass before it cools. For bigger items, longer gates fit their size and wall thickness4.
Mold Structure and Precision
Precision in molding is vital. High accuracy allows for shorter gates, improving flow. If precision is low, longer gates prevent clogs – like ensuring syrup flows smoothly.
Flow’s Part in Efficiency
A smart gate design aligns with material properties, reducing defects like warping for even filling.
- Efficiency: Controlling flow results in fewer defects, faster cycles and high-quality products.
Learning these factors helps mold designers choose the best gate designs for successful production. Explore more about mold structure5 and its impact on design choices in injection molding processes. This information is crucial for professionals seeking to improve designs for top performance and reliability in large-scale manufacturing.
High fluidity materials require longer gate lengths.False
High fluidity materials need shorter gates due to easier flow.
Gate length affects manufacturing efficiency in injection molding.True
Correct gate length minimizes defects and improves flow efficiency.
How Does Mold Structure Influence Gate Length?
I remember the first time I truly understood how mold shape changes gate length. This moment opened my eyes and changed how I thought about design.
Mold shape plays a critical role in deciding gate length. Mold shape impacts product size, material qualities and processing exactness. These factors all affect how melted plastic moves. Product quality heavily depends on this flow. Quality is very important.
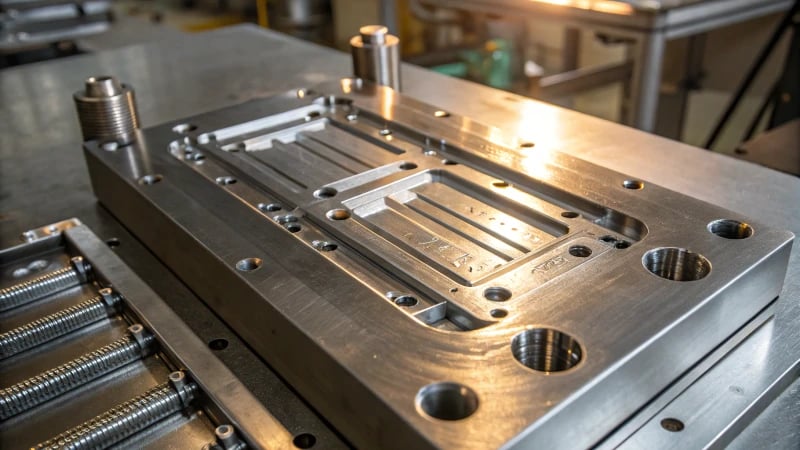
Things that Affect Mold Design
Experience taught me that the size and wall thickness of a product are important in molding. Smaller products with thin walls need gates about 0.5 to 1mm long. Short gates help fill the mold fast and stop the melt from cooling too much.
Material Features
Plastic type strongly affects how long gates should be. I remember working with polystyrene; it flows very well, so we used shorter gates without losing pressure. However, plastics with fillers usually need longer gates to keep the flow steady.
Material Type | Fluidity | Recommended Gate Length |
---|---|---|
General Plastics | High | 0.5 – 1mm |
Filled Plastics | Moderate | Up to 2mm |
Processing Precision and Design
Precision in mold processing has been crucial for me. High precision allows shorter gates, greatly increasing efficiency. When precision drops, gates must be longer to prevent blockages or uneven flow.
Complex designs may require different gate lengths to match runner layout and filling demands. I once faced a tricky mold project that forced me to adjust my original gate assumptions.
Practical Points
Designing molds involves more than technical details; it requires understanding each part’s role in getting excellent results. Helpful tools and guidelines6 really support making wise choices about gate lengths.
Mold structure impacts gate length directly and strongly affects production. Using these insights, I probably improved both the efficiency and quality of my molded products.
Small products require shorter gates for rapid filling.True
Small products with thin walls need gates between 0.5 to 1mm for quick filling.
Materials with fillers always require gates over 2mm.False
Filled plastics may need longer gates, but typically not exceeding 2mm.
What Are the Best Practices for Achieving Optimal Gate Length?
Have you ever thought about how the ideal gate size changes your injection molding projects?
The best gate length in injection molding depends on product size, material properties and mold structure. Usually, an ideal gate length is between 0.5 and 2mm. This range is typical.
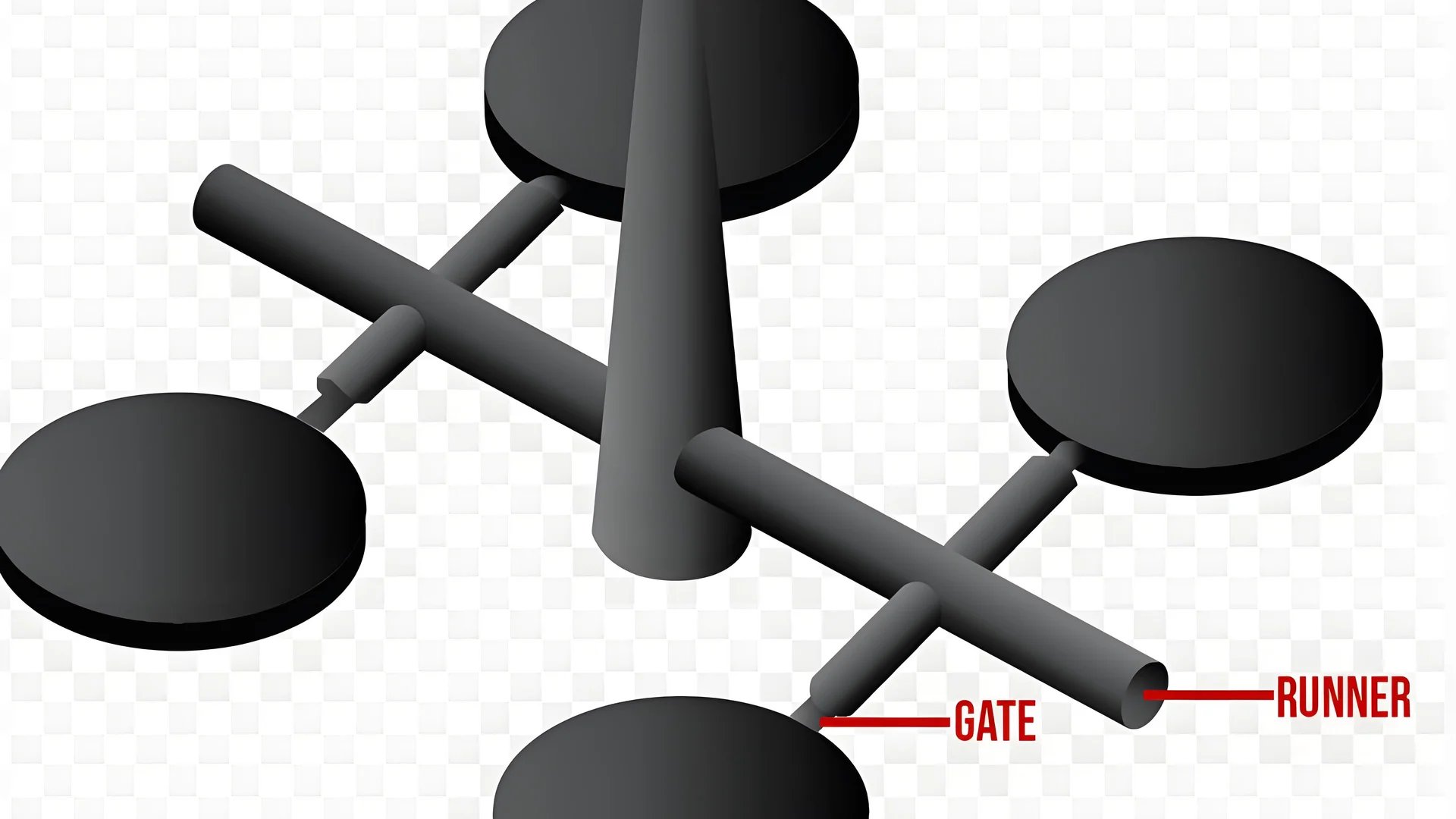
Understanding the General Range
When I first started experimenting with plastic injection molding, I saw how crucial the gate length was for success. The magic number usually sits between 0.5 and 2mm. This lets the melt flow smoothly into the mold with minimal pressure and heat loss.
The optimal gate length in plastic injection molding typically falls between 0.5 and 2mm. This range is primarily due to the need to minimize pressure and heat loss during the injection process. A shorter gate length7 ensures that the melt enters the cavity efficiently, making the filling process smoother and faster.
Product Type | Recommended Gate Length |
---|---|
Small, Thin-Walled Items | 0.5 – 1mm |
Large, Thick-Walled Items | Up to 2mm |
I remember a project involving a tiny, complex gadget where even a small mistake in gate length caused big problems. For small, thin-walled items like this, sticking to a gate length of about 0.5 to 1mm was important. This length lets the material fill effectively without cooling too fast.
For a bulky product with thicker walls, I learned sometimes it’s necessary to use a gate closer to 2mm. Staying within this range is vital for controlling pressure loss.
Specific Influencing Factors
Product Size and Wall Thickness: Smaller, thinner products do well with shorter gate lengths, around 0.5 to 1mm. They fill up swiftly without the melt cooling too much.
Material Properties: Material type has a big impact. For example, with polystyrene or polypropylene—easy-flowing materials—you possibly use a shorter gate. But with materials like glass fiber-filled ones, a slightly longer gate might be needed to keep the flow smooth.
Mold Structure and Processing Accuracy: A high-precision mold setup lets you opt for shorter gates confidently. Yet, with complex or lower precision mold designs, extending the gate length a bit may be necessary.
Design Considerations for Optimal Gate Length
Getting the gate length right combines art and science:
- Evaluate Material Characteristics: Understand how your material flows; this will guide you to the correct gate length.
- Consider Product Dimensions: Select the gate length based on handling small and thin-walled or large and thick-walled products.
- Mold Complexity and Accuracy: Examine your mold’s design and precision limits; this will reveal if a shorter or longer gate is suitable.
For more insights into injection molding8, exploring case studies and industry guidelines is highly recommended as they provide valuable knowledge on how these factors interact in real-world situations.
Optimal gate length is always 0.5 to 2mm.False
While generally recommended, specific requirements may vary based on factors like material.
High-precision molds allow shorter gate lengths.True
Precision in mold design enables consistent flow, supporting shorter gate lengths.
Conclusion
Film gate lengths in injection molding typically range from 0.5 to 2mm, influenced by product size, wall thickness, material properties, and mold design for optimal flow and efficiency.
-
Discover why precision in mold making is crucial for successful production. ↩
-
Explore essential factors for optimizing design in injection molding processes. ↩
-
This link provides a detailed overview of why fluidity is crucial in molding processes. ↩
-
Explores how wall thickness influences gate length decisions and molding outcomes. ↩
-
Offers insights into how different mold structures can affect gate design strategies. ↩
-
Discover practical tools and guidelines that help in selecting appropriate gate lengths for various materials and products. ↩
-
Explore how varying gate lengths affect mold efficiency and quality. ↩
-
Learn about proven strategies in injection molding for optimal results. ↩