Ever wondered how to make your injection molded surfaces look stunning and function flawlessly? Let me walk you through some of the best techniques I’ve discovered.
Effectively texture injection molded surfaces using EDM, chemical etching, laser texturing, and mechanical engraving. These methods offer precision, cost-effectiveness, and adaptability for diverse design and material requirements.
I remember my first project where I had to design a mobile phone case with a complex texture. It was a bit overwhelming at first. I decided to use electrical discharge machining (EDM) because it allowed me to create high-precision patterns, something crucial for the intricate design I had in mind. Seeing the final product, with its perfectly detailed surface, was a rewarding experience.
On another occasion, I needed to create a leather-like texture for automotive interior parts. Chemical etching was my go-to method here. The process was not only cost-effective but also delivered that genuine leather feel I was aiming for. Of course, I had to be mindful of the environmental impacts and ensured proper disposal of the chemical solutions.
When it comes to high-resolution designs, especially on electronic products, laser texturing is unmatched. I once worked on a project where I had to deliver a gradient texture on a device case. The precision and flexibility of laser texturing made it possible to achieve exactly what was envisioned.
Each method has its place in my toolkit, offering unique benefits depending on the project’s requirements. Whether it’s the artistic flair of mechanical engraving or the straightforward approach of adjusting molding process parameters, understanding these techniques has greatly enhanced my design capabilities.
EDM is the most cost-effective texturing method.False
While EDM offers precision, it is not the most cost-effective method.
Laser texturing provides high precision for intricate designs.True
Laser texturing allows for precise control, ideal for detailed work.
- 1. What Are the Advantages of Electrical Discharge Machining (EDM) in Mold Texturing?
- 2. How does chemical etching create unique mold surface textures?
- 3. Can Laser Texture Processing Enhance Product Personalization?
- 4. Why is Mechanical Engraving Perfect for Artistic Mold Designs?
- 5. How Do Injection Molding Process Parameters Affect Surface Textures?
- 6. Conclusion
What Are the Advantages of Electrical Discharge Machining (EDM) in Mold Texturing?
Imagine having the power to etch intricate designs into tough materials with ease. That’s the magic of Electrical Discharge Machining (EDM) in mold texturing.
EDM in mold texturing allows precise and effortless crafting of complex patterns on hard materials, reduces tool wear, and enhances aesthetic and functional aspects, offering advantages over traditional methods.
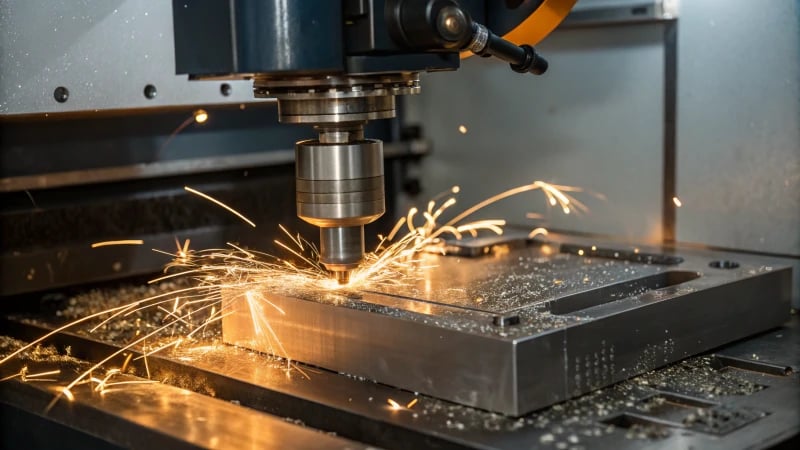
The Precision Edge of EDM
I remember the first time I saw Electrical Discharge Machining (EDM) in action—it was like watching an artist at work. The way it uses pulse discharge between an electrode and the workpiece is fascinating. This process allows us to etch fine patterns onto hard surfaces without worrying about tool wear. The high temperatures generated make it seem like the material just melts away exactly where we need it to, leaving behind detailed textures that are nothing short of artwork.
For example, working on mobile phone cases can be quite challenging due to their intricate design requirements. But with EDM, it’s like having a magic wand that produces highly accurate and high-resolution patterns, making products visually appealing and functionally superior.
EDM Versus Traditional Methods
When I started comparing EDM to other methods, like chemical etching or mechanical engraving, I was blown away by its precision and control. Chemical etching, while cost-effective, comes with its environmental baggage. And mechanical engraving, although safer, doesn’t quite achieve the level of detail I often aim for in my projects.
Here’s a quick comparison:
Method | Precision | Environmental Impact | Complexity of Patterns |
---|---|---|---|
EDM | High | Low | Complex |
Chemical Etching | Moderate | High | Simple |
Mechanical Engraving | Moderate | Low | Moderate |
Application Scenarios
One of the things I love about EDM is its versatility. Whether I’m designing electronic product molds with dot or gradient textures or creating intricate patterns for automotive parts, EDM never disappoints. Its ability to handle complex shapes with precision is a game-changer.
Take injection molded parts with anti-slip textures, for instance. By tweaking the electrode shapes and discharge parameters, I’ve managed to create unique textures that would be nearly impossible with other methods. Understanding EDM‘s potential has allowed me to enhance product quality significantly and improve my design capabilities.
Learn more about EDM applications1 and see how it can elevate your projects too.
EDM minimizes tool wear during mold texturing.True
EDM uses pulse discharge to etch patterns without physical contact, reducing wear.
Chemical etching achieves higher precision than EDM.False
EDM offers higher precision due to its controlled discharge process, unlike chemical etching.
How does chemical etching create unique mold surface textures?
Ever wondered how a simple mold can turn into a textured masterpiece? Chemical etching is the secret behind these intricate designs.
Chemical etching uses chemical solutions to selectively dissolve materials, creating unique, cost-effective, and precise surface textures ideal for large areas like car interiors.
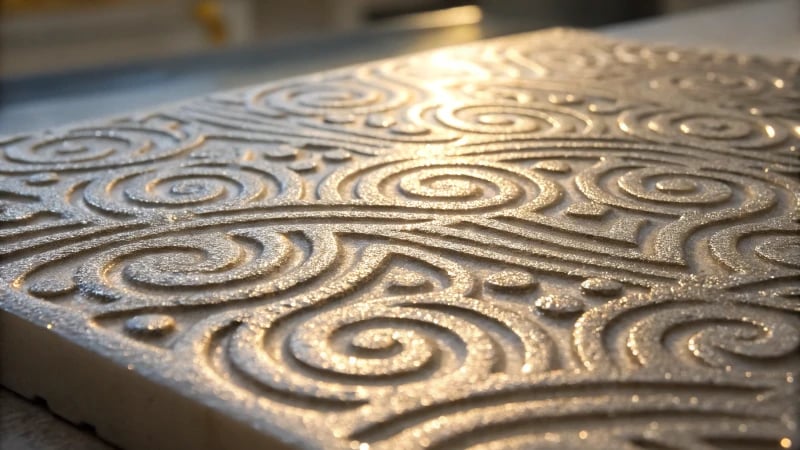
The Basics of Chemical Etching
Imagine having the ability to sculpt something with just a liquid! That’s pretty much what chemical etching feels like to me. The process involves using chemical solutions that react with mold materials, selectively dissolving parts of the surface. It’s like painting a picture, but instead of colors, I’m using acids and solutions to create depth and detail. By tweaking the solution’s composition, concentration, timing, and temperature, I can craft textures that are as varied as my imagination allows. And the best part? I don’t have to touch the mold physically as I would with mechanical engraving2, which makes it perfect for detailed work.
Parameter | Effect on Texture |
---|---|
Solution Composition | Determines chemical reaction |
Concentration | Influences texture depth |
Etching Time | Controls texture uniformity |
Temperature | Affects reaction speed |
Application Scenarios
In my world, chemical etching is like a magic wand for large-area textures. One of my favorite uses is in automotive interiors. Picture the soft, leather-like feel of a car’s dashboard. That’s often achieved through chemical etching. It gives parts that genuine leather appearance without breaking the bank. Of course, we have to be mindful of the environment due to potential chemical waste, but innovations are constantly helping us reduce that impact.
Comparison with Other Methods
Now, if I had to choose between electrical discharge machining (EDM) and chemical etching, it would really depend on the project. EDM uses pulse discharge to etch the material, creating intricate patterns that can handle high precision tasks, like those on mobile phone cases3. But if I’m working with heat-sensitive materials or need a broad area textured uniformly, chemical etching is my go-to.
Environmental Considerations
One thing that’s always on my mind is the environmental impact. Chemical etching is cost-effective and powerful, but it requires careful handling of chemical solutions. Innovations in chemical management systems4 are essential to keep our planet safe while enjoying the benefits of this versatile technique.
In essence, chemical etching is an artist’s tool in the world of molds, allowing us to design intricate surfaces across various applications—from automotive to consumer electronics. As I continue to explore this field, balancing precision with sustainability remains a crucial part of my journey.
Chemical etching is a contact-based process.False
Chemical etching is non-contact, using chemical solutions to dissolve surfaces.
Temperature affects the speed of chemical reactions in etching.True
Higher temperatures generally increase reaction rates, affecting texture formation.
Can Laser Texture Processing Enhance Product Personalization?
Remember when you first got a gift that had your name or initials on it? There’s something special about owning something uniquely yours.
Laser texture processing enhances product personalization by allowing manufacturers to create detailed, unique designs on various materials, improving both aesthetics and functionality, and offering flexible, truly personalized textures.
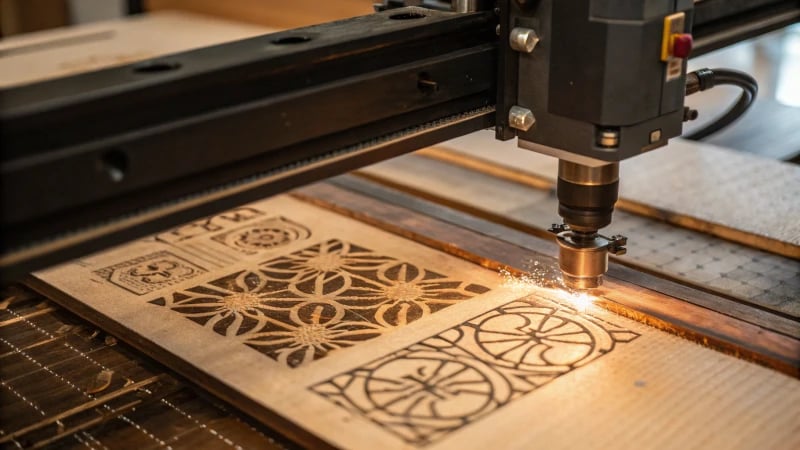
Understanding Laser Texture Processing
I still remember the first time I saw a laser in action at a factory. The way it effortlessly danced over surfaces, leaving behind patterns that seemed impossible just moments before, was pure magic. Laser texture processing works by using a high-energy laser beam to alter the surface of a material, creating unique textures and patterns. It’s like giving an artist’s brush to a machine but with precision and control that only technology can provide.
This method allows precise control5 over the texture’s depth, shape, and distribution, facilitating customization.
Advantages Over Traditional Methods
Back in the day, traditional methods like electrical discharge machining6 (EDM) and chemical etching were the go-to for adding textures. My early days involved a lot of watching EDM in action, where the pulse discharge between an electrode and workpiece would create those tiny, intricate patterns. But laser texturing takes it up a notch with its unmatched flexibility and precision, capable of crafting complex designs without the need for physical contact like in mechanical engraving.
Method | Principle | Application |
---|---|---|
Laser Texturing | Uses lasers to melt, vaporize, or chemically change material surfaces | High precision personalization |
EDM | Pulse discharge between electrode and workpiece | Complex molds with fine textures |
Chemical Etching | Selective dissolution of material using chemical solutions | Large-area textures |
Application Scenarios
Laser texture processing shines in scenarios demanding high precision, like molds with high precision7 requirements. Imagine creating dot or gradient textures with such high resolution that they appear almost lifelike. That’s the power of lasers in action!
Impact on Product Design
One of my favorite parts about working with laser texture processing is how it empowers designers to let their imaginations run wild without worrying about cost or time constraints. This technology is a game-changer in fast-paced industries like fashion, automotive, and consumer electronics where staying ahead of trends is crucial.
With the ability to quickly design and modify patterns, laser texture processing allows designers to experiment with new styles8 without incurring significant costs or delays.
Moreover, it’s not just about looks. Think about tools or electronics with anti-slip surfaces—these aren’t just functional but also add to user safety and satisfaction.
Future Potential
As technology continues to evolve, I can’t help but feel excited about the future possibilities laser texture processing holds. By merging with AI-driven design algorithms, we’re stepping into an era where innovation knows no bounds. This doesn’t just enhance how products look but also boosts their durability and usability through clever texture design.
By offering customization at scale, it enables companies to meet diverse consumer demands efficiently. Additionally, by combining laser processing with emerging technologies such as AI-driven design algorithms, the scope for innovation9 becomes virtually limitless.
The future’s looking bright and textured!
Laser texturing offers more precision than EDM.True
Laser texturing allows for precise control over texture depth and shape.
Chemical etching requires physical contact like laser texturing.False
Chemical etching uses chemical solutions, not physical contact.
Why is Mechanical Engraving Perfect for Artistic Mold Designs?
Imagine turning raw material into stunning art with just the right touch of precision and flair. That’s the magic of mechanical engraving in mold design.
Mechanical engraving is ideal for artistic mold designs due to its precision in creating intricate textures, efficiency in producing unique patterns, and ability to blend artistry with technical skill.
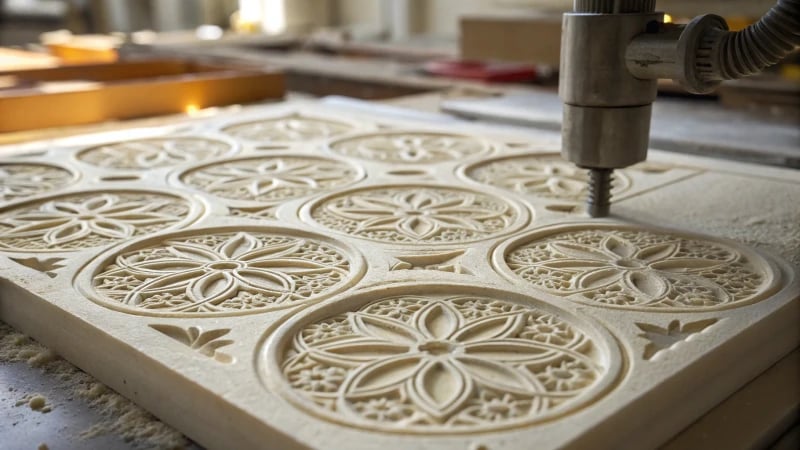
The Art of Mechanical Engraving
I still remember the first time I watched a mechanical engraving machine in action—it was like witnessing art being carved out of sheer precision. This technique involves a tool meticulously cutting into the mold surface to create textured patterns. Whether done by hand or using CNC machines, the results are nothing short of amazing. The three-dimensional10 and artistic textures that emerge are a testament to both craftsmanship and technology.
Key Benefits of Mechanical Engraving:
Feature | Description |
---|---|
Precision | Achieves intricate details with high accuracy. |
Depth Control | Allows for precise control over texture depth, enhancing design complexity. |
Material Versatility | Suitable for various mold materials, including metals and plastics. |
Efficiency | CNC machines enable rapid production without compromising quality. |
Comparing Engraving Techniques
When I first started exploring different engraving methods, I was fascinated by how each technique had its unique flair. Unlike electrical discharge machining (EDM), which uses pulse discharge to etch the mold surface, mechanical engraving physically removes material, offering a tactile depth that EDM just can’t match. EDM works wonders on complex shapes11 but lacks the artistic nuance that mechanical engraving delivers.
Chemical etching offers another path, dissolving mold surfaces with solutions to create textures. While it’s cost-effective for large areas, it doesn’t quite capture the fine detail or environmental friendliness of mechanical engraving.
Artistic Mold Design Applications
Mechanical engraving truly shines when detail and design are paramount. It’s like having a magic wand that adds decorative charm to high-end crafts with brand logos or exquisite relief patterns. Imagine producing relief patterns12 that not only look beautiful but serve a functional purpose—it’s a win-win.
Example Applications:
- Luxury Packaging: Enhances product appeal with detailed logos and textures.
- Consumer Electronics: Adds unique texture to device casings, improving grip and style.
Technical Advantages:
- Consistency: CNC machines ensure consistent quality across multiple runs.
- Customization: Offers flexibility in pattern design, accommodating specific artistic visions.
In mold design, mechanical engraving isn’t just a process; it’s an art form that seamlessly blends tradition and modern technology, offering unparalleled creative freedom and precision.
Mechanical engraving offers better depth control than EDM.True
Mechanical engraving allows precise depth control, enhancing design complexity.
Chemical etching is more environmentally friendly than mechanical engraving.False
Chemical etching lacks the environmental friendliness of mechanical engraving.
How Do Injection Molding Process Parameters Affect Surface Textures?
Ever wondered why some plastic products feel smooth as glass, while others are all matte and textured? It’s not magic—it’s injection molding magic! Let me walk you through how tweaking some parameters can change the whole game.
Injection molding parameters—temperature, pressure, and speed—determine surface textures, influencing plastic flow for effects like smooth, matte, or frosted finishes. Adjusting these enhances product aesthetics and functionality.
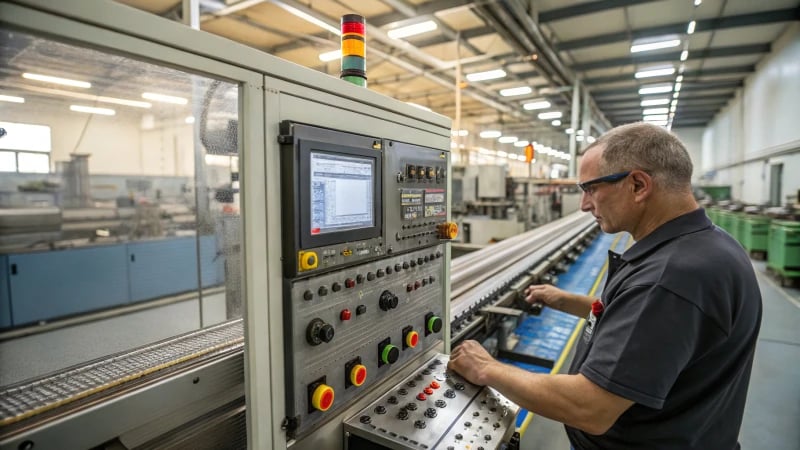
Key Parameters in Injection Molding
I’ve spent countless hours in the workshop, adjusting knobs and dials on the injection molding machines, always marveling at how a slight tweak can change the texture of a plastic part entirely. Here’s how it breaks down:
-
Temperature: Picture this—you’re trying to pour honey on a cold morning versus a warm afternoon. The melt temperature works similarly for plastics; higher temperatures make the material flow easier, often resulting in smoother surfaces. On the flip side, cooler temps might leave you with a rougher finish.
-
Pressure: Imagine squeezing toothpaste out of a tube. The force you apply determines how quickly and smoothly it comes out. High pressure during injection means denser and smoother textures, while lower pressure might give you something less defined.
-
Speed: Remember when you’d pour soda too fast and it frothed over? Fast injection speeds can do something similar, creating turbulence that might just give you a unique frosted pattern.
Processing Methods and Their Effects
Thinking back to my early days learning about molds, I recall how fascinated I was by the various methods used to create textures. Each method seems almost like an art form.
Mold Texture Processing Method
-
Electrical Discharge Machining (EDM): It’s like watching a magician at work. This technique uses pulse discharges to etch patterns into molds—perfect for those intricate designs you find on your smartphone case.
-
Chemical Etching: Here’s where science meets art—using chemicals to dissolve parts of the mold for textures like imitation leather in car interiors.
-
Laser Texture Processing: Imagine harnessing lasers to craft precise textures—ideal for electronics where every millimeter counts.
-
Mechanical Engraving: Think of this as digital carving, where CNC machines create detailed three-dimensional patterns on molds.
Directly Forming Textures During Molding
Sometimes, the magic happens during the molding itself. By using special materials or tweaking those parameters we talked about earlier, textures can emerge as if by design.
-
Special Injection Molding Materials: Some materials come with built-in texture properties. For instance, certain fibers in composites can lend a unique texture right from the mold.
-
Changing Parameters: As simple as altering temperature or speed can result in effects like frosting—perfect for products where cost efficiency is key.
Post-Processing Texturing Methods
Even after molding, the artistry continues with post-processing techniques that can refine or completely transform surface textures:
Method | Principle | Applications |
---|---|---|
Sandblasting | Uses high-speed sand particles | Ideal for anti-slip effects |
Chemical Treatment | Utilizes solvents for texturing | Suitable for decorative finishes |
Each technique brings its own flair to the final product, allowing us to tailor design and functionality precisely to our needs. Exploring these injection molding techniques13 opens up a world of possibilities for designers like us.
Higher temperature creates smoother injection-molded surfaces.True
Higher melt temperatures reduce viscosity, leading to smoother textures.
Chemical etching is ideal for small-area texture applications.False
Chemical etching is better suited for large-area textures, like car interiors.
Conclusion
Explore effective techniques for texturing injection molded surfaces, including EDM, chemical etching, laser processing, and mechanical engraving, enhancing both aesthetics and functionality in product design.
-
Gain insights into diverse applications of EDM across various industries. ↩
-
Explore how mechanical engraving compares with chemical etching in terms of precision and application scenarios. ↩
-
Learn why EDM is favored for high-precision mold patterns, such as those on mobile phone cases. ↩
-
Discover innovations in chemical management that help reduce pollution risks during manufacturing processes. ↩
-
Understand how laser texturing allows for precise control over texture characteristics. ↩
-
Learn about EDM and its role in mold texture processing. ↩
-
Explore how high precision is achieved in mold manufacturing. ↩
-
Discover how laser texturing influences current design trends. ↩
-
Explore potential advancements in laser texturing technology. ↩
-
Understand how three-dimensional textures enhance the visual and tactile qualities of products. ↩
-
Learn how EDM creates detailed patterns for molds with intricate shapes. ↩
-
Discover how relief patterns add depth and aesthetic value to designs. ↩
-
Explore various techniques in injection molding for achieving diverse surface textures. ↩