Have you ever found yourself in a dilemma over which steel to choose for your injection molding project? It’s a crucial decision!
Injection mold steel is classified into low, medium, and high hardness grades. These classifications help in selecting the right material for specific applications based on wear resistance, strength, and processing needs.
Let’s dive deeper into each classification, exploring their unique properties and applications to empower your decision-making.
Low hardness steels offer better machinability than medium steels.True
Low hardness steels are easier to machine, reducing tooling costs.
How Do Low Hardness Steels Differ from Medium Hardness Steels?
Steel selection is a pivotal decision in injection molding. How do low and medium hardness steels compare in performance?
Low hardness steels offer better machinability and cost-effectiveness, while medium hardness steels provide improved strength and wear resistance, making them suitable for more demanding applications.
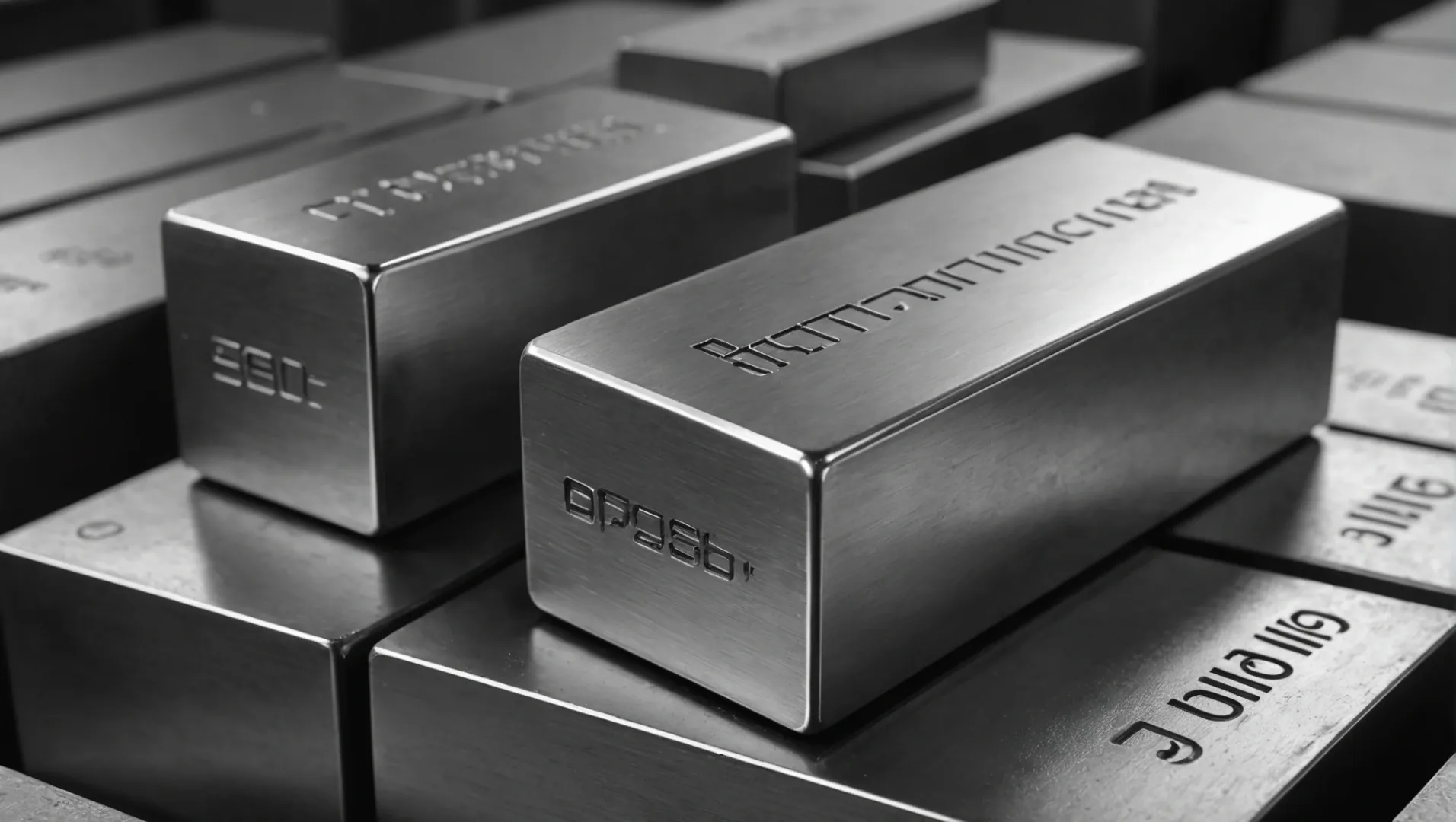
Characteristics of Low Hardness Steels
Low hardness steels, such as 45# steel, are typically chosen for their excellent machinability1 and cost-effectiveness. These steels are characterized by their decent strength and toughness, although they do not exhibit high wear resistance. This makes them ideal for projects with less stringent requirements, such as small batch production or simple plastic product molds.
Example: 45# Steel
- Strengths: Cost-effective, easy to process
- Limitations: Lower wear resistance, suitable for simpler applications
- Applications: Simple mold designs, short production runs
Characteristics of Medium Hardness Steels
Medium hardness steels like P20 and 718H are pre-hardened, providing a uniform hardness level that does not require additional heat treatment before use. These steels are known for their enhanced processing and polishing capabilities. P20, for instance, is widely used for creating molds for everyday products due to its balanced properties.
718H takes these attributes further, offering higher strength and wear resistance compared to P20, making it suitable for more challenging applications such as automotive interiors or electronic housings.
Example: P20 Steel
- Strengths: Pre-hardened, excellent processing and polishing properties
- Applications: General mold requirements, like appliance shells and daily necessities
Example: 718H Steel
- Strengths: Improved hardness and wear resistance over P20
- Applications: Medium volume production, higher requirement molds such as automotive parts
Comparison Table
Feature | Low Hardness Steel (45#) | Medium Hardness Steel (P20, 718H) |
---|---|---|
Cost | Lower | Higher |
Machinability | Higher | Moderate |
Wear Resistance | Lower | Higher |
Typical Applications | Simple molds | General to more complex molds |
Choosing between low and medium hardness steels involves assessing the specific needs of the injection molding project. While low hardness options are budget-friendly and easy to machine, medium hardness steels offer the durability needed for more demanding applications. Understanding these differences helps in optimizing mold design and longevity.
Low hardness steels are more cost-effective than medium hardness.True
Low hardness steels like 45# are chosen for their cost-effectiveness.
Medium hardness steels require additional heat treatment before use.False
Medium hardness steels like P20 are pre-hardened, needing no extra treatment.
What Are the Advantages of Using High Hardness Mold Steel?
High hardness mold steel offers unparalleled benefits in injection molding, crucial for high-precision and long-lasting applications.
High hardness mold steel provides superior wear resistance, excellent surface finish, and enhanced durability, making it ideal for high-precision injection molds such as those used in optical and medical industries.
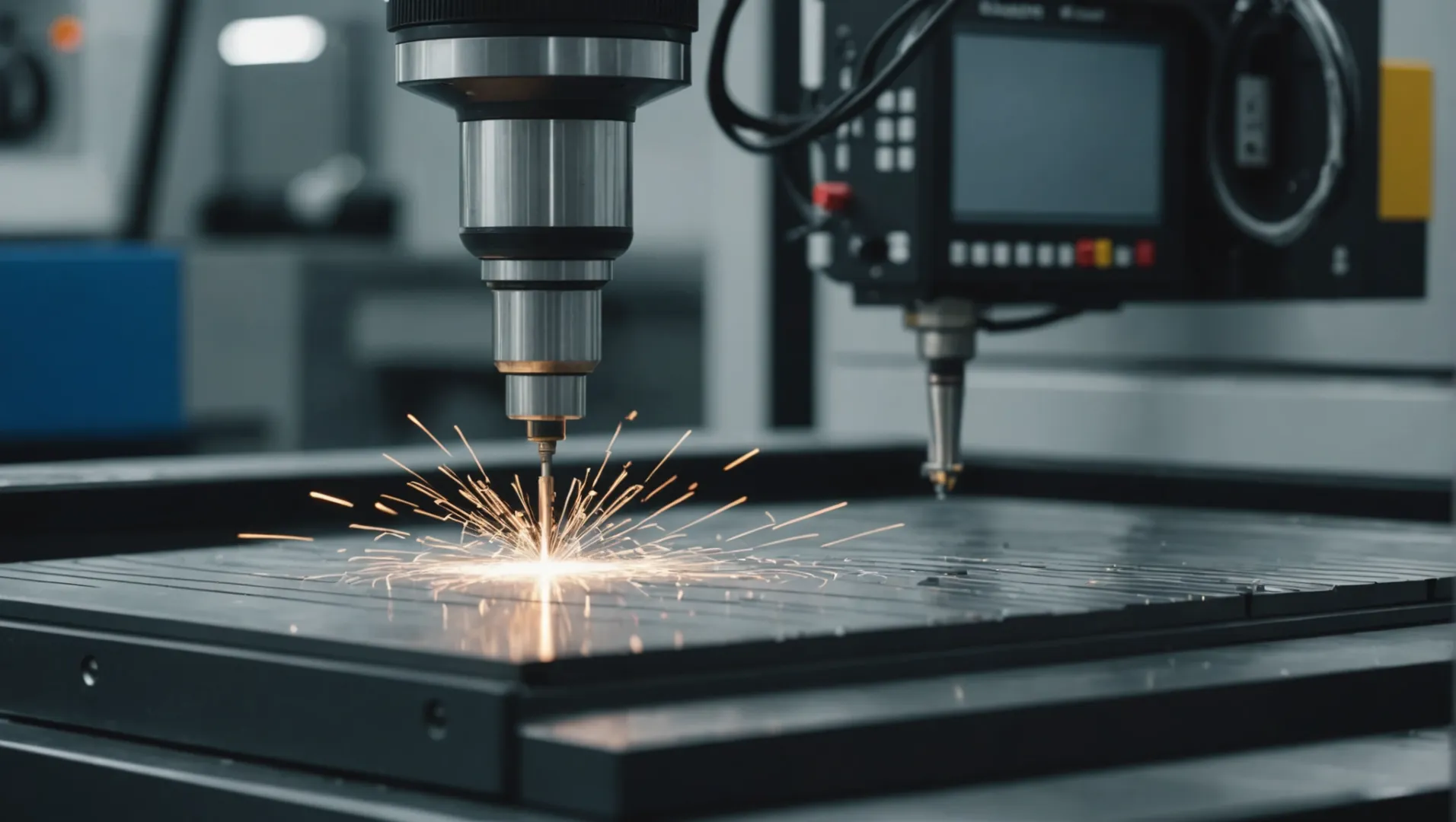
Superior Wear Resistance and Durability
One of the primary advantages of high hardness mold steel is its exceptional wear resistance. This characteristic ensures that the molds can endure prolonged use without significant degradation. As a result, they are suitable for high-volume production environments where molds are subject to repeated stress and abrasion.
For instance, S136 steel2 offers high corrosion resistance along with its impressive hardness, making it ideal for environments where exposure to corrosive materials is common.
Exceptional Surface Finish
Molds crafted from high hardness steel often yield products with superior surface finishes. This quality is crucial for industries where aesthetics and precision are paramount, such as in the production of optical lenses or medical equipment.
H13 steel3, known for its excellent thermal properties and toughness, enables the production of molds that maintain integrity even under high thermal and mechanical loads.
Steel Type | Key Properties | Application Scenarios |
---|---|---|
S136 | Corrosion resistance, high polishability | Optical lenses, medical equipment |
H13 | Thermal strength, durability at high temperatures | Large plastic products, engineering plastics |
Enhanced Precision and Reliability
High hardness steels provide consistent performance under stringent conditions. This reliability is critical in applications requiring precise dimensions and minimal tolerances.
The ability to achieve and maintain tight tolerances is a significant advantage in industries like automotive and electronics, where components must fit together perfectly to function correctly.
Extended Tool Life
Using high hardness mold steel can significantly extend the lifespan of molds. This longevity reduces the need for frequent replacements or repairs, offering substantial cost savings over time.
In summary, choosing high hardness mold steel enhances both the efficiency and effectiveness of the injection molding process. Whether it’s for its superior wear resistance, outstanding surface finish, or prolonged tool life, high hardness mold steels are indispensable in achieving high-quality, precision products across various demanding industries.
High hardness mold steel is ideal for optical lenses.True
Its superior surface finish and precision suit optical industries.
H13 steel has poor thermal properties for mold making.False
H13 steel is known for excellent thermal strength and toughness.
How Does Heat Treatment Affect Steel Hardness in Injection Molds?
Understanding the impact of heat treatment on steel hardness is essential for ensuring the longevity and performance of injection molds.
Heat treatment significantly enhances the hardness of steel used in injection molds by altering its microstructure, increasing wear resistance and strength. This process involves controlled heating and cooling, which helps achieve desired mechanical properties essential for various molding applications.
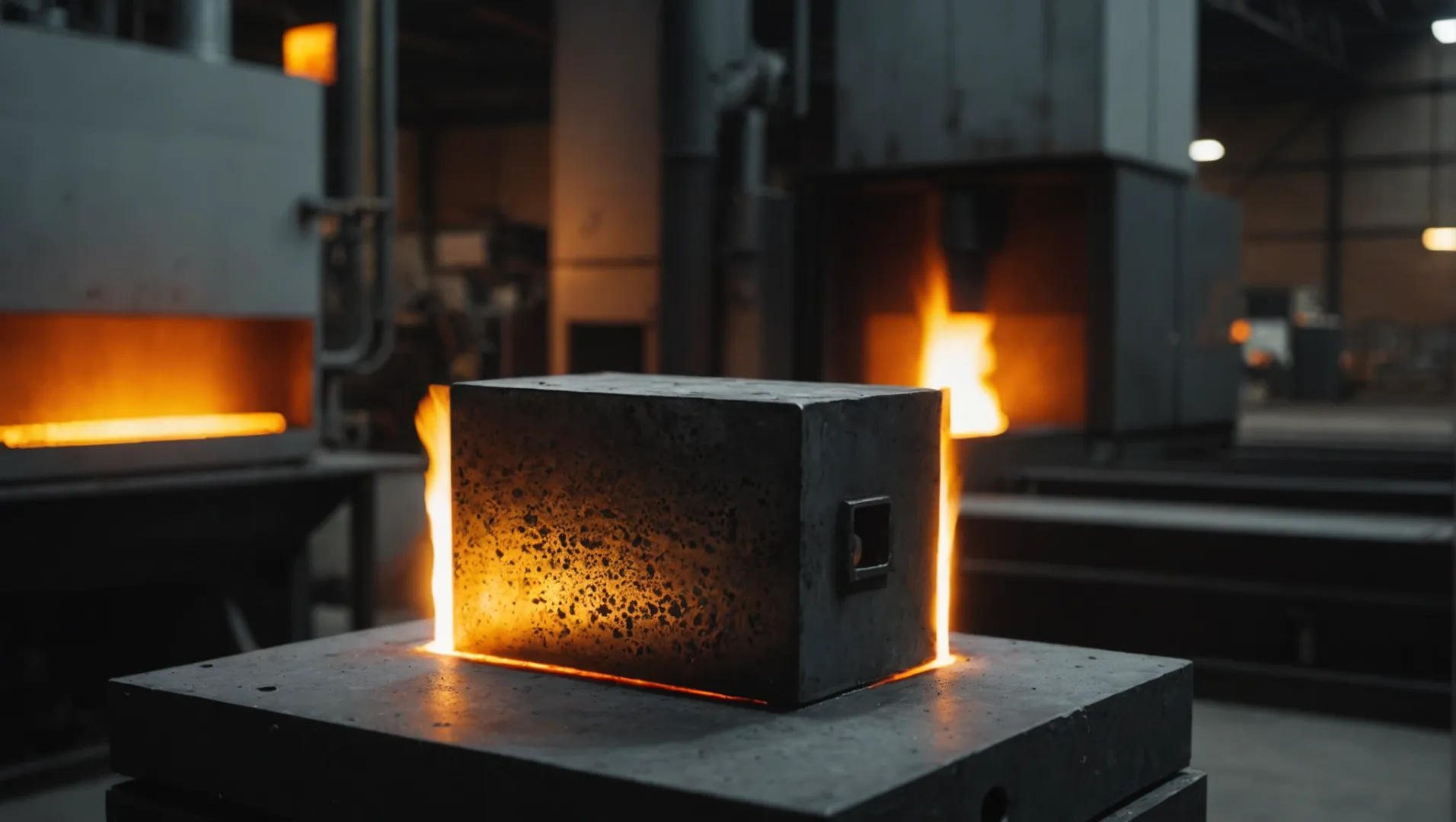
The Science Behind Heat Treatment
Heat treatment involves a series of thermal processes that change the physical and sometimes chemical properties of steel. These processes typically include heating the steel to a specific temperature, holding it at that temperature, and then cooling it down at a controlled rate.
During heat treatment, changes occur in the steel’s microstructure4, such as the transformation from austenite to martensite, which increases hardness and strength. This transformation is crucial for injection molds that need to withstand repeated cycles under high pressure and temperature.
Effects on Different Steel Grades
-
Low Hardness Steels (e.g., 45# Steel):
- Heat treatment is generally not required due to their application in low-stress environments. However, when necessary, minor treatments can improve their wear resistance slightly.
-
Medium Hardness Steels (e.g., P20, 718H):
- These steels are often pre-hardened, meaning they undergo initial heat treatment before being supplied for mold making. Further heat treatment5 may not be necessary unless specific adjustments to their hardness or wear resistance are required.
-
High Hardness Steels (e.g., S136, H13):
- Heat treatment is essential to achieve the desired properties like corrosion resistance and uniform hardness. For example, H13 steel requires precise tempering to reach a hardness above HRC50.
Practical Applications and Considerations
In practice, heat-treated steels are chosen based on the type of plastic being molded and the production volume. For instance, S136 is ideal for corrosive plastics due to its superior resistance after heat treatment. In contrast, H13’s high thermal strength makes it suitable for high-temperature applications.
Moreover, understanding the specific heat treatment cycle is crucial. Factors like soaking time, quenching medium, and tempering temperatures must be meticulously controlled to ensure that the steel achieves its intended characteristics without compromising its integrity.
Injection mold designers6 often collaborate closely with metallurgists to select the appropriate heat treatment process tailored to their specific molding needs.
Heat treatment increases steel hardness by altering microstructure.True
Heat treatment changes steel's microstructure, enhancing hardness and strength.
All steel grades require heat treatment for injection molds.False
Low hardness steels often do not require heat treatment for mold use.
Why Is Steel Hardness Critical in Injection Mold Design?
Understanding the importance of steel hardness in mold design is crucial for achieving optimal product quality and longevity.
Steel hardness in injection mold design affects durability, wear resistance, and the precision of the final product. High hardness improves mold longevity, while lower hardness offers better machinability, crucial for different production requirements.
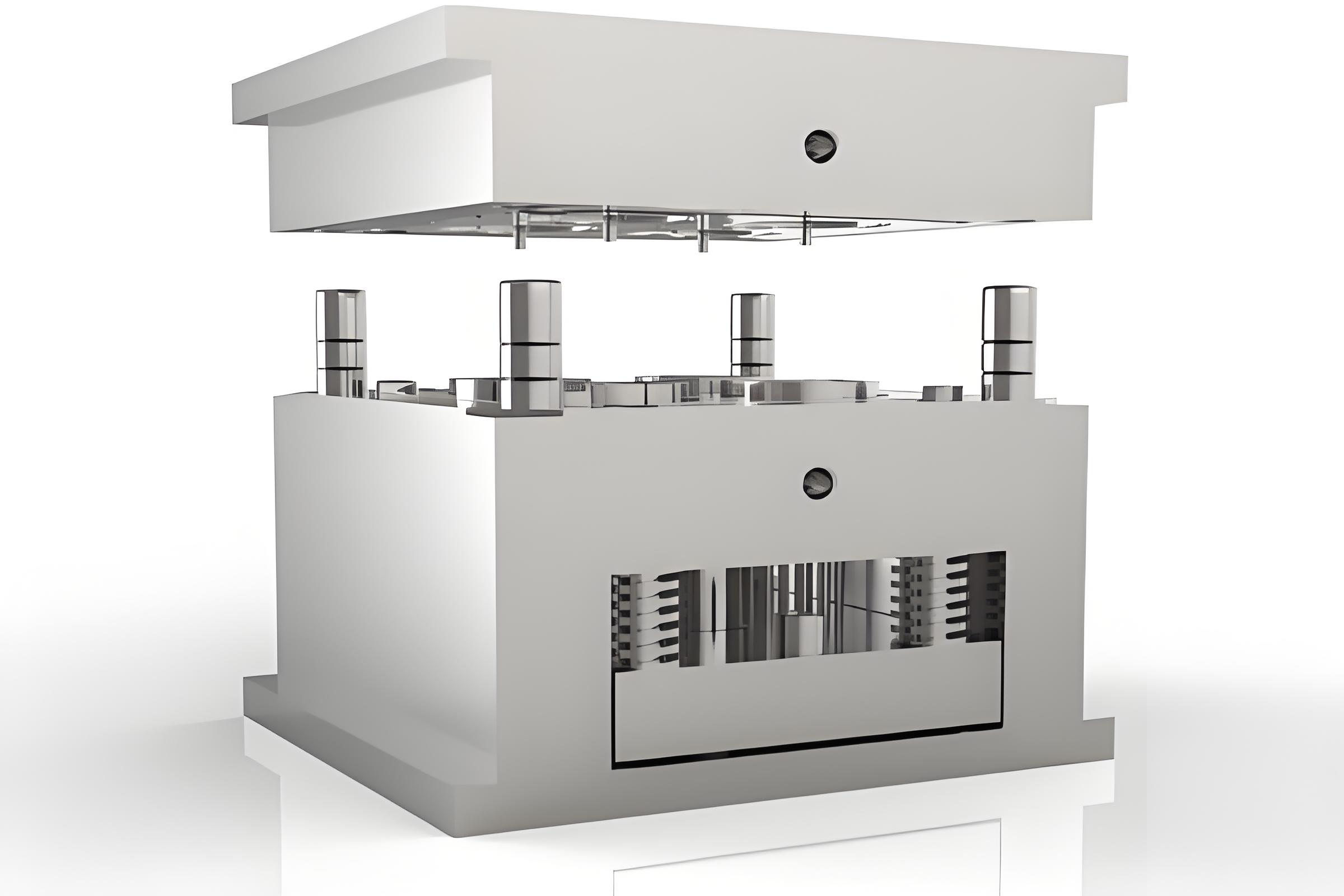
The Role of Steel Hardness in Mold Longevity
Hardness directly impacts a mold’s wear resistance and durability. Higher hardness steels, like S136 steel7, are essential for molds producing high-volume parts, as they withstand the wear from repeated use. Lower hardness steels may wear out faster, necessitating more frequent replacements and increasing production costs.
Steel Type | Typical Hardness (HRC) | Usage Scenario |
---|---|---|
45# Steel | 16-20 | Low-demand molds |
P20 Steel | 24-38 | General-purpose molds |
S136 Steel | 48-52 | High-precision molds |
Precision and Surface Finish
Higher hardness ensures minimal deformation under pressure, which is critical for maintaining tight tolerances and achieving a smooth surface finish. This is particularly crucial in industries like automotive and electronics, where precision is non-negotiable.
Machinability and Production Speed
While harder steels offer superior durability, they are also more challenging to machine. P20 steel8, known for its balance between hardness and machinability, is often used when quicker production times are necessary without sacrificing too much on durability.
Balancing Hardness with Other Properties
Choosing the right steel involves a trade-off between hardness and other properties like toughness and corrosion resistance. For instance, while H13 steel offers excellent thermal resistance, it requires precise heat treatment to achieve the desired hardness without compromising toughness.
The choice of steel impacts not only the mold’s life but also the quality of the products it produces. Understanding these nuances allows manufacturers to make informed decisions, optimizing both cost and quality in their production processes.
Higher steel hardness increases mold longevity.True
Higher hardness improves wear resistance, reducing replacements.
Lower hardness steels are ideal for high-precision molds.False
High-precision molds require higher hardness for minimal deformation.
Conclusion
Understanding the hardness grades of injection mold steel allows for better material selection, ensuring efficiency and longevity in production.
-
Explore why machinability is crucial in selecting low hardness steels.: A work material having a low hardness and low work-hardening rate produces small cutting forces and low contact pressure at the tool–chip … ↩
-
Discover S136’s corrosion resistance and polishing capabilities.: S136 is plastic mold steel with excellent corrosion resistance and has excellent production characteristics. After long-term use of the mold, the surface of the … ↩
-
Learn about H13’s thermal strength and durability benefits.: Physical Properties · Density: 0.280 lb/in3 (7750 kg/m3) · Specific Gravity: 7.75 · Machinability: 65-70% of a 1% carbon steel. ↩
-
Learn how microstructure changes affect steel’s mechanical properties.: The microstructure is predominantly martensite but also has allotriomorphic ferrite, Widmanstätten ferrite, bainite and pearlite. Notice that the spherical … ↩
-
Explore detailed processes and benefits of heat treating mold steels.: Preparatory heat treatment, Pre-heat treatment processes such as annealing, normalizing or quenching and tempering should be used depending on the materials and … ↩
-
Discover key factors in designing efficient and durable injection molds.: Not all product designs are suitable for injection molding. Material, shape and feature choices must all be carefully considered before manufacturing begins. ↩
-
Learn why S136 is ideal for high-precision, corrosive-resistant molds.: The s136 material is a kind of mold steel, which belongs to plastic mold steel. Due to the high chromium content, it has anti-rust function in the air. ↩
-
Discover why P20 steel balances hardness and machinability effectively.: 1. P20 Steel · Wear resistance lower than other tool steels · Hardness lower than other common tool steels · Short tool lifetime when molding … ↩