Picking the best cooling channel layout seems difficult. It is, however, a very crucial aspect in mold design. This task truly transforms how molds are designed. I have really grown to appreciate its importance.
When selecting a cooling channel layout in mold design, consider product shape, wall thickness, and precision needs, as these factors significantly impact cooling speed and product quality.
Over the years, I learned that understanding cooling channel layouts improves my designs. Designs probably get better with this knowledge. Each project has its own challenges and opportunities. A mold for a round plastic bottle cap needs a special approach. I used a simple ring-shaped channel for this. It cooled the product’s outer edge well. Small wins like this are very important. They remind me to adjust my methods for each unique shape and thickness. I really want to share my insights with you!
Cooling channel layout affects product quality in mold design.True
The layout directly influences cooling efficiency, impacting the final product's quality and consistency.
Wall thickness is irrelevant when choosing cooling channels.False
Wall thickness significantly affects heat transfer rates, making it a crucial factor in cooling channel design.
How Does Product Shape Influence Cooling Channel Design?
Did you ever think about how a product’s shape changes cooling channel designs? This topic is really interesting. The product shape plays an important role in improving manufacturing processes. Let’s explore this together!
Product shape significantly impacts cooling channel design by determining layout and heat removal efficiency. This affects temperature uniformity during manufacturing, crucial for enhancing production quality and reducing defects.
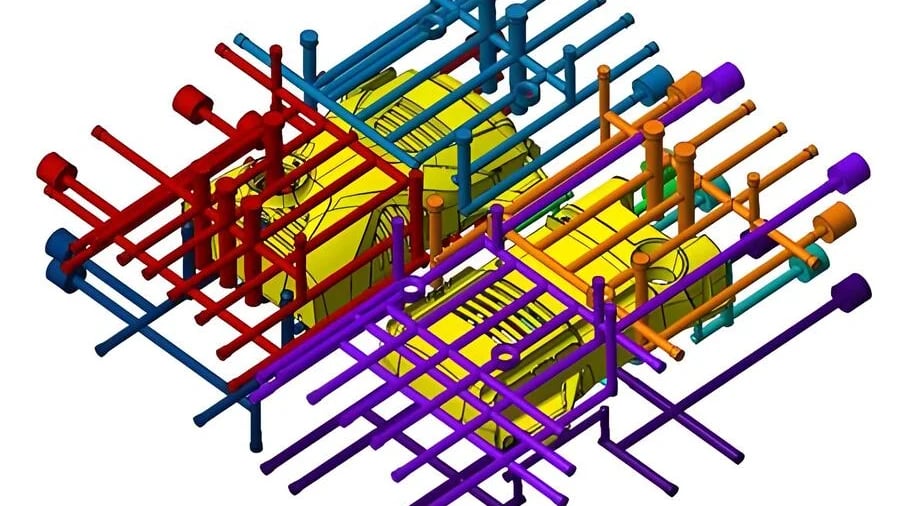
The Impact of Product Shape on Cooling Channel Design
The shape of a product significantly influences how cooling channels are designed, as it dictates the layout, efficiency, and effectiveness of heat removal during the manufacturing process. Understanding these relationships is vital for optimizing production quality and minimizing defects.
Simple and Regular Shapes
For products with simple and regular shapes, such as round or square parts, a straight-through layout is often the most effective approach. This type of cooling channel is relatively straightforward to implement and can efficiently manage heat removal.
- Example: A mold for a round product, like a plastic bottle cap, may use a ring-shaped, straight-through cooling channel that wraps around the cavity, cooling the outer perimeter effectively.
Product Shape | Recommended Cooling Channel Layout | Example |
---|---|---|
Round | Straight-through | Plastic bottle cap |
Square | Straight-through | Square plastic component |
Complicated and Irregular Shapes
On the other hand, products with complex and irregular shapes benefit from more intricate cooling channel designs. For these shapes, circular layouts such as serpentine or spiral channels provide better coverage and uniform cooling.
- Example: Automotive interior parts often feature complex curved surfaces. Using serpentine cooling channels allows for better fitting within the mold cavity and ensures all areas cool evenly, preventing deformation due to uneven temperatures.
Product Shape | Recommended Cooling Channel Layout | Example |
---|---|---|
Complex | Serpentine or Spiral | Automotive interior parts |
Influence of Wall Thickness
The thickness of the product walls also plays a crucial role in cooling channel design:
- Uniform Wall Thickness: Products with uniform thickness can utilize either straight-through or simple circulation layouts depending on their size.
- Example: Large plastic pallets may use spiral cooling channels that facilitate uniform heat distribution.
Wall Thickness Type | Recommended Cooling Channel Layout | Example |
---|---|---|
Uniform | Straight-through or Spiral | Large plastic pallets |
Uneven | Zoned layout | Thick-walled reinforcements |
For products with uneven wall thickness, a zoned layout is more suitable. This design divides the cooling areas based on wall thickness, allowing for customized flow rates and channel sizes to achieve optimal cooling.
Functionality and Precision Requirements
Finally, the product’s functionality and precision requirements significantly influence cooling channel design.
- General Functionality: For everyday items with less stringent accuracy demands, simpler layouts suffice.
- Example: Common household items can typically meet cooling needs with straightforward channel designs.
- High Precision Needs: Conversely, items like optical lenses require more sophisticated inlay layouts ensuring precise temperature control in critical areas.
Functionality Requirement | Recommended Cooling Channel Layout | Example |
---|---|---|
General Functionality | Straight-through or Simple Circulation | Household items |
High Precision | Inlay Layout | Optical lenses |
Understanding these dynamics helps product designers make informed decisions about their cooling channel designs aligning them with production goals while maintaining quality standards. For more insights on conformal cooling channels, check out this resource1 to enhance your design strategies.
Simple shapes require straight-through cooling channels.True
Products with simple shapes like round or square can efficiently use straight-through cooling channels for optimal heat removal.
Complex product shapes benefit from serpentine cooling layouts.True
Irregularly shaped products utilize serpentine channels for better cooling coverage, ensuring uniform temperature control during manufacturing.
How Does Wall Thickness Affect Cooling Efficiency?
Have you ever thought about how wall thickness affects cooling efficiency in manufacturing? This topic is interesting because it relates to design and function. Understanding it really helps improve the quality of our products. It’s that important.
Uniform wall thickness ensures efficient cooling during manufacturing, while uneven thickness demands specialized cooling techniques. Understanding wall thickness’s impact on cooling can prevent errors and enhance product quality.
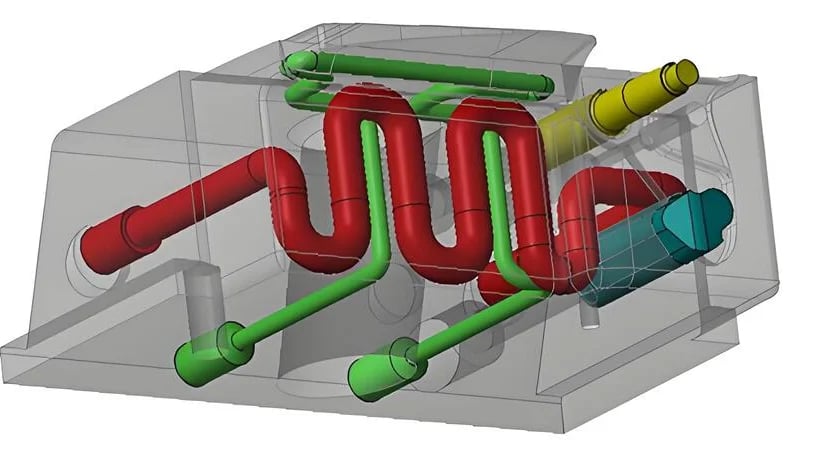
The Influence of Wall Thickness on Cooling Dynamics
Wall thickness significantly influences cooling efficiency, particularly in manufacturing processes such as injection molding. Understanding the correlation between wall thickness and cooling dynamics is essential for optimizing product designs and ensuring performance efficiency.
Uniform Wall Thickness: Cooling Strategies
For products with uniform wall thickness, both straight-through and simple circulation cooling layouts can be effective. However, the choice depends on product size:
- Straight-Through Layout: Suitable for smaller items, where cooling needs are easily met.
- Circulation Layout: Recommended for larger products, ensuring even cooling throughout the item.
- A great example is large plastic pallets2 that benefit from spiral cooling channels to remove heat from edges to the center. This approach helps prevent uneven cooling, which can lead to defects like warping or shrinkage.
Uneven Wall Thickness: Customized Cooling Solutions
Products featuring uneven wall thickness present unique challenges. Implementing a zoned cooling layout is crucial:
Wall Thickness Area | Recommended Cooling Strategy |
---|---|
Thick-walled | Increase channel size or adjust flow rate |
Thin-walled | Standard cooling channel configuration |
For instance, in molds for thick-walled items, adjusting the cooling channel in thicker sections ensures uniform temperature distribution. This tailored approach mitigates issues like shrinkage marks, enhancing product quality greatly.
High Precision Requirements: Advanced Cooling Techniques
When dealing with high precision and functional requirements, such as in optical components or electronic devices, advanced cooling methods are necessary:
- Cooling Inserts: These can be integrated into critical mold areas to achieve precise temperature control.
- An example is using inserts in optical lens molds3, where maintaining exact temperatures is paramount for quality.
The use of inlay layouts allows for fine-tuning of cooling processes, ensuring that complex geometries are uniformly cooled without compromising product integrity.
Conclusion
During my design journey, I recognized the importance of wall thickness in cooling efficiency. By leveraging various cooling strategies tailored to specific wall thickness configurations, designers can significantly enhance the performance and quality of manufactured products. Understanding these principles not only aids in producing defect-free items but also optimizes energy consumption during the manufacturing process, contributing to overall efficiency in production systems.
Wall thickness directly affects cooling efficiency in manufacturing.True
The thickness of walls in products influences how effectively heat is dissipated during manufacturing, impacting overall cooling efficiency.
Uneven wall thickness requires customized cooling strategies.True
Products with uneven wall thickness need tailored cooling solutions to ensure uniform temperature distribution and prevent defects like shrinkage.
Why Are Precision Requirements So Critical in Cooling Channel Selection?
Have you ever thought about how a cooling channel can greatly affect a product’s quality? Precision is very important. Understanding precision might change how you design things. Let’s explore this together.
Precision in cooling channel selection is crucial for heat transfer efficiency and product quality. Designers optimize performance by aligning channel layouts with the product’s shape and function, ensuring superior outcomes.
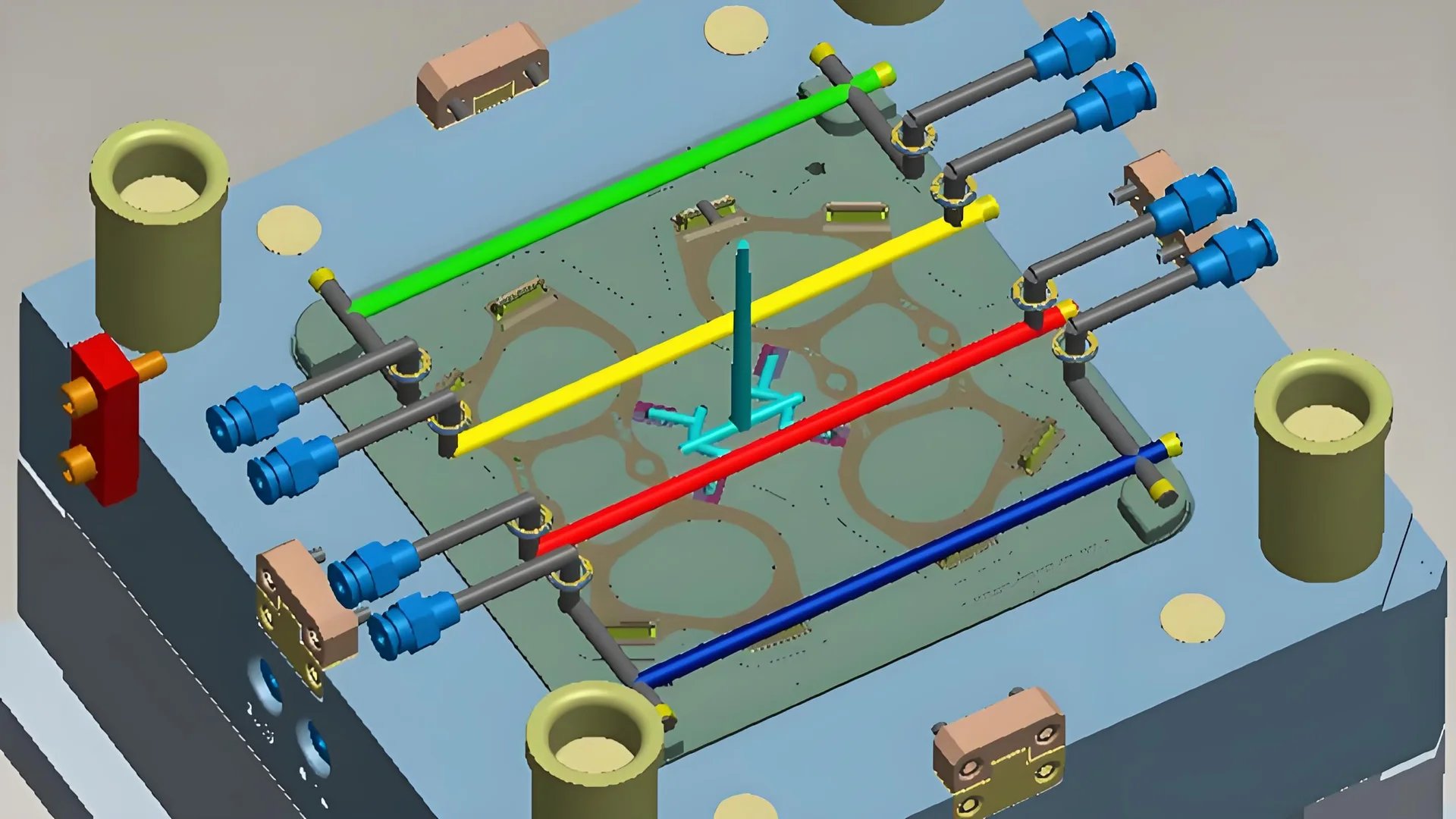
Understanding Precision Needs in Cooling Channel Selection
Precision needs guide the selection of cooling channels, especially in fields where details are crucial. I think back to my early days in product design. Back then, I struggled to understand how important these choices were. I only realized their impact after seeing them in action. Choosing the correct channel improves cooling efficiency and raises product quality. This is significant for precision parts like optical lenses or electronic components.
When selecting cooling channels, designers must consider the shape of the product and how it influences cooling efficiency.
- Simple Shapes: I once worked on plastic bottle caps. We used a straight-through layout. Cooling water surrounded the cavity, leading to even cooling along the edge. It was such a relief to see even cooling!
- Complex Shapes: Another time, I designed a mold for complex automotive parts. We used a serpentine layout for better cooling distribution. This layout lengthened the cooling path and improved heat exchange efficiency. It prevented issues like deformation from uneven cooling. I’ve learned to avoid these mistakes!
Considering Product Wall Thickness
Product wall thickness is crucial when choosing cooling channel layouts:
Wall Thickness | Recommended Layout | Example |
---|---|---|
Uniform | Straight-through or circulation | Spiral design for large plastic pallets |
Uneven | Zoned approach | Tailored channels for thick reinforcement products |
For uniform wall thickness products, a straight-through layout suits smaller items. Larger products benefit from a spiral design that enhances uniform cooling. I once joined a team making large plastic pallets. The spiral channels effectively managed heat from edge to center, ensuring even cooling.
For products with uneven wall thickness, I use a zoned approach involving dividing the mold by thickness and creating separate channels. I clearly remember working on thick reinforcement products where tailored cooling channels solved quality issues like shrinkage marks.
Functionality and Precision Needs
The product’s purpose also influences cooling channel design:
- General Functionality: For items with regular accuracy needs, I pick simple layouts like straight-through channels. They simplify mold design and cut costs while maintaining quality, which is vital for daily items.
- High Precision Needs: For high-precision products like optical lenses, advanced solutions are necessary, like cooling inserts. I once worked on a project needing strict temperature control; inserts near the molding surface ensured consistent cooling, achieving high standards.
No Conclusion Here
While we won’t draw a broad conclusion, one fact is clear: understanding precision needs is key in choosing cooling channels. Grasping the subtleties of product shapes, wall thickness and purpose allows designers to create efficient solutions that meet high-quality standards. To explore further into best practices in cooling channel design, learn more about cooling layouts4 and precision molding techniques5.
I hope these insights into precision needs help you tackle your design challenges with more confidence!
Precision cooling channels enhance product quality and efficiency.True
Selecting the right cooling channel design directly impacts heat transfer efficiency and overall product integrity, especially for precision components.
Serpentine layouts are best for simple-shaped products.False
Simple-shaped products benefit from straight-through layouts, while complex shapes require serpentine designs for effective cooling distribution.
How Can Innovative Cooling Techniques Improve Mold Performance?
Do you ever think about how new cooling methods are changing mold performance in manufacturing? Let’s look at how these improvements make work faster and better. These changes are really interesting and useful.
Innovative cooling techniques enhance mold performance by optimizing heat transfer, reducing production times, and improving product quality through customized cooling designs, ensuring consistently high manufacturing standards and demonstrating a commitment to excellence.
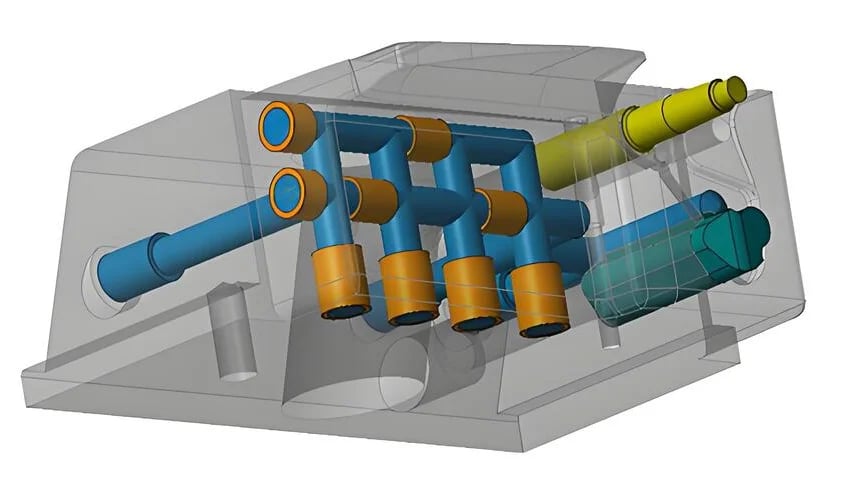
Understanding the Role of Cooling Techniques in Mold Performance
In the beginning, I explored mold manufacturing. I was amazed by how cooling affected the final product deeply. Cooling techniques are more than technical talk. These methods are the hidden heroes. They help molds work very well. This technology is really changing our industry. Let’s explore this important technology.
Innovative cooling techniques play a crucial role in enhancing mold performance by optimizing heat transfer during the injection molding process. Efficient cooling not only improves cycle times but also ensures that the final product meets quality standards.
For instance, molds designed with serpentine or spiral cooling channels can adapt to complex shapes, promoting uniform cooling throughout the product. This is particularly important for components with intricate geometries, such as automotive parts, where uneven cooling can lead to deformation.
Key Factors Influencing Cooling Techniques
1. Shape of the Product
The shape of the product is a vital consideration in selecting an appropriate cooling layout. Here’s a breakdown:
Product Shape | Recommended Cooling Layout | Example |
---|---|---|
Simple | Straight-through | Mold for a round plastic bottle cap |
Complicated | Serpentine or Spiral | Mold for automotive interior parts |
-
Simple and Regular Shapes: For items like plastic bottle caps, a straight-through cooling channel can be effective, wrapping around the cavity and providing efficient cooling.
-
Complicated and Irregular Shapes: Products with curves and varying thickness benefit from serpentine layouts which maximize heat exchange and ensure uniform cooling.
2. Wall Thickness Considerations
Cooling strategies must also be adapted based on wall thickness:
Wall Thickness | Cooling Layout | Application Example |
---|---|---|
Uniform | Straight-through / Simple Circulation | Large plastic pallets |
Uneven | Zoned Layout | Thick-walled reinforcement products |
-
For products with uniform wall thickness, both straight-through and circulation layouts can suffice. However, for larger items, circulation helps maintain even temperature across the entire component.
-
For products with uneven wall thickness, a zoned layout is essential. By dividing the mold cooling areas based on thickness, it allows for optimized cooling flow rates, preventing defects like shrinkage marks.
3. Functionality and Precision Requirements
The intended functionality and precision requirements of the product greatly influence cooling design:
Functionality Level | Cooling Technique | Example |
---|---|---|
General Functionality | Straight-through / Simple Circulation | Common daily necessities |
High Precision | Inlay Layout (Cooling Inserts) | Optical lenses, electronic components |
- Products with general functionality can utilize simpler layouts, keeping design costs low while ensuring quality.
- For high-precision applications, such as optical lenses, inlay layouts are necessary. These specialized cooling inserts allow for precise temperature control in critical areas of the mold, achieving the required cooling uniformity.
Benefits of Advanced Cooling Techniques
Implementing innovative cooling techniques offers numerous advantages:
- Reduced Cycle Times: Efficient heat removal leads to faster production rates.
- Improved Part Quality: Uniform cooling minimizes defects, ensuring higher quality parts.
- Enhanced Design Flexibility: Designers can explore complex shapes without compromising performance due to cooling constraints.
- Cost Efficiency: Optimized cooling reduces energy consumption and operational costs over time.
For more insights into the impact of advanced cooling techniques on mold performance, consider exploring cooling technology advancements6 that highlight case studies demonstrating their effectiveness.
Serpentine cooling channels enhance mold performance.True
Serpentine cooling channels promote uniform cooling, crucial for complex shapes, improving overall mold performance and product quality.
Straight-through cooling is best for all product shapes.False
Straight-through cooling is effective only for simple shapes; complex geometries require advanced layouts like serpentine for optimal cooling.
Conclusion
Selecting an appropriate cooling channel layout in mold design is essential for enhancing cooling efficiency and product quality, influenced by factors such as shape, wall thickness, and precision needs.
-
Explore detailed strategies and examples to improve your cooling channel designs based on product shapes. ↩
-
Exploring this link will deepen your understanding of how wall thickness impacts thermal performance and help you make informed design choices. ↩
-
This resource offers practical insights into optimal wall thickness measurements and their implications for energy efficiency and comfort. ↩
-
Discover detailed insights into how precision impacts cooling channel effectiveness, ensuring your designs meet industry standards. ↩
-
Learn about best practices for designing cooling systems that maintain product integrity through precise temperature control. ↩
-
Discover how innovative cooling techniques can enhance mold performance and lead to better quality products. ↩