Have you ever wondered about the expense of processing injection molds? You are not the only one! Let’s explore this topic.
Injection molds often range in price from $10,00 to over $10,000. Cost varies because of mold complexity, choice of material and techniques. Simple designs typically cost less. Intricate designs really raise the price.
I remember my first experience with injection molding costs. It felt confusing and strange! I learned that mold design and raw material costs are important to know. Simple molds might cost between $500 to $1000. For complicated automotive parts, just the design might reach $5000 or more.
Raw material is another factor꞉ steel price changes a lot with quality and specifications. Processing methods like CNC machining and EDM also increase costs significantly! By understanding these details, I discovered methods to keep quality while saving money. Maybe you really could do the same.
Simple mold designs cost $500 to $1000.True
Simple molds with basic structures and small sizes have lower design costs.
Mold assembly labor costs are fixed at $50 daily.False
Labor costs vary by region and skill level, ranging from $50-$100.
- 1. What Factors Influence the Cost of Injection Molds?
- 2. How Does Mold Design Complexity Influence Costs?
- 3. Why Do Raw Material Choices Impact Mold Processing Costs?
- 4. How Do Processing Techniques Impact Costs?
- 5. How Do Assembly and Debugging Affect Overall Mold Costs?
- 6. What are the hidden costs in mold processing?
- 7. Conclusion
What Factors Influence the Cost of Injection Molds?
Have you ever thought about why injection mold prices sometimes seem unpredictable?
Injection mold costs mostly depend on factors like design complexity, material choice, processing methods and assembly needs. Each factor greatly affects the production budget. Understanding these factors is very important.
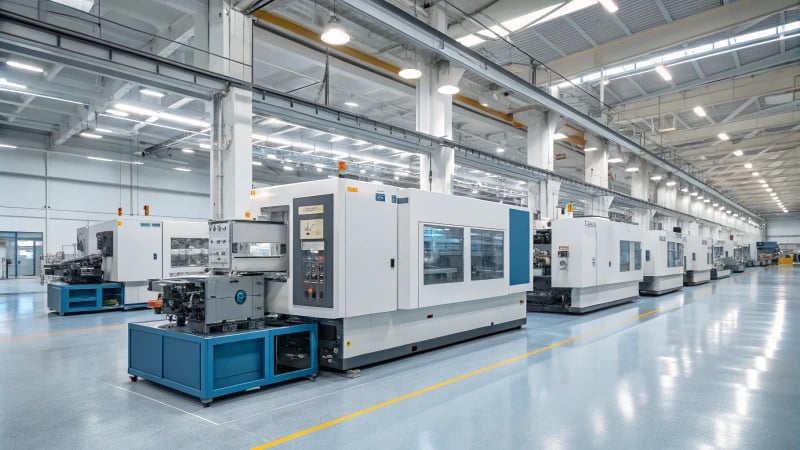
Mold Design Complexity
The complexity of a mold’s design plays a crucial role in determining its cost. Simple molds may cost between $500 to $1,000. However, complex molds with features like multiple sliders or core pulling structures can reach up to $15,000 or more, especially in automotive parts1 manufacturing.
Raw Material Selection
Choosing materials feels like picking apples from a tree. Steel is common and costs from $1,500 to $10,000 per ton, depending on quality. High-grade steels like H13 are more expensive but offer better durability and precision for demanding applications2. It’s like getting peace of mind for hard projects. Very reliable steel is worth the price.
Material | Price Range (USD/ton) |
---|---|
Ordinary | $1,500 – $3,000 |
High-grade | $5,000 – $10,000+ |
Processing Techniques
Art in injection molding is processing techniques. In my early days, I admired CNC machines and EDM for their accuracy. These methods add up to the cost but ensure high precision and quality in the final product.
- CNC Machining: Costs range from $30 to $80 yuan per hour.
- EDM: Charges are based on area and depth, typically $1 to $2 per square centimeter.
- Wire Cutting: Stable at around $25 to $50 per hour.
Assembly and Debugging
Assembly shows true skill. Labor costs depend on local wages and skill levels, averaging around $50 to $100 daily. Complex molds take longer. Additionally, debugging involves usage costs for equipment like injection molding machines which are calculated per ton per hour at $10-$20.
Other Influencing Costs
Transportation and management costs matter too. Transportation depends on distance and size while management adds another 5% to 10% to costs. Understanding these factors helps businesses plan budgets well for injection molding3 projects.
Complex mold designs cost over $15,000.True
Complex molds require precise structures, increasing design costs significantly.
Standard parts for molds always cost over $1,000.False
Standard parts vary in price, ranging from hundreds of dollars.
How Does Mold Design Complexity Influence Costs?
I remember when I first designed a mold. It felt like solving a puzzle with invisible pieces. The task showed me how complexity really increases costs. Costs rise.
Complicated mold designs affect costs a lot because they require accuracy and special features. Different shapes, exact measurements and extra parts increase material, processing and work costs. This means total costs really rise. Costs go up.
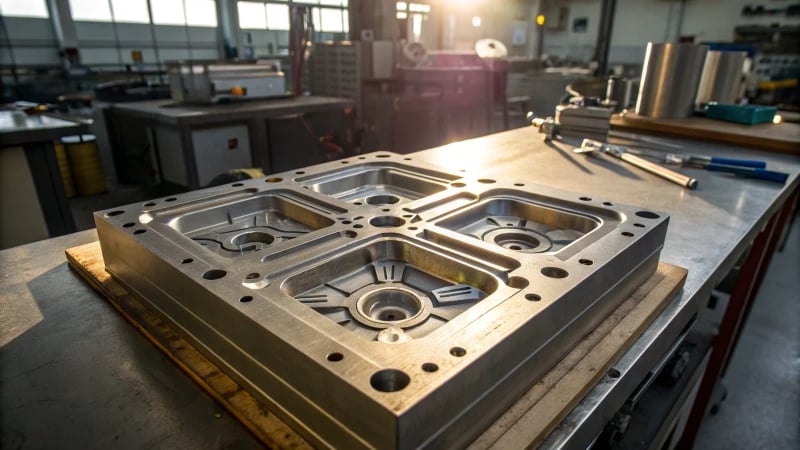
Understanding the Impact of Design Complexity
The complexity of a mold design is a primary cost driver. Simple designs, often used for small injection molds4, may cost between $500 and $1,000. In contrast, complex molds incorporating multiple sliders, core-pulling structures, and precise cavity details can exceed $15,000.
Factors Influencing Costs:
- Tight Tolerances: Achieving high precision necessitates advanced machinery and skilled labor, elevating costs. For instance, CNC machining costs range from $30 to $80 per hour due to its precision.
- Intricate Geometries: Complex shapes require more time-consuming processes like EDM and wire cutting, with costs ranging from $1 to $2 per square centimeter.
Material Selection and Its Cost Implications
Choosing the right materials significantly affects both cost and performance:
Material Type | Price Range (USD/Ton) |
---|---|
Ordinary Steel | 1,500 – 3,000 |
High-grade Steel | 5,000 – 10,000+ |
Higher-grade steels like H13 offer superior hardness and wear resistance but come at a premium price.
Labor and Assembly Challenges
Complex molds require intricate assembly and debugging:
- Assembly Costs: Skilled labor is essential here. Daily costs range from $50 to $80. Difficult assemblies further increase labor expenses.
- Debugging: Involves using specialized equipment like injection molding machines, costing about $10 to $20 per ton per hour.
Additional Considerations
- Surface Treatments: Enhance mold durability but add to costs. Treatments like chrome plating can cost up to $300 per square meter.
- Standard Parts: Components such as ejectors and springs add hundreds to thousands of yuan based on quality and specifications.
Understanding these factors aids in making informed decisions regarding mold design. Balancing complexity with cost-efficiency is crucial for optimal production outcomes. Leveraging insights from industry leaders like MoldAll5 can provide valuable guidance in navigating these complexities.
Simple mold designs cost $500 to $1,000.True
Simple molds with basic structures cost less due to fewer complexities.
CNC processing costs $15 per hour.False
CNC processing costs range from $30 to $80 per hour due to precision.
Why Do Raw Material Choices Impact Mold Processing Costs?
Have you ever thought about why selecting the correct raw materials is crucial for your mold processing budget? Picking the right ones is vital. It’s really essential. It affects costs directly. Incorrect choices might lead to higher expenses. Wrong materials could cause problems. Avoiding costly errors begins with wise selection. Making informed decisions saves money. Being smart about your choices is key.
Different raw materials affect the cost of molding. Material prices, machining details and surface treatments differ a lot. This difference impacts mold processing expenses deeply. Each material type influences the mold production costs. Each one plays its part.
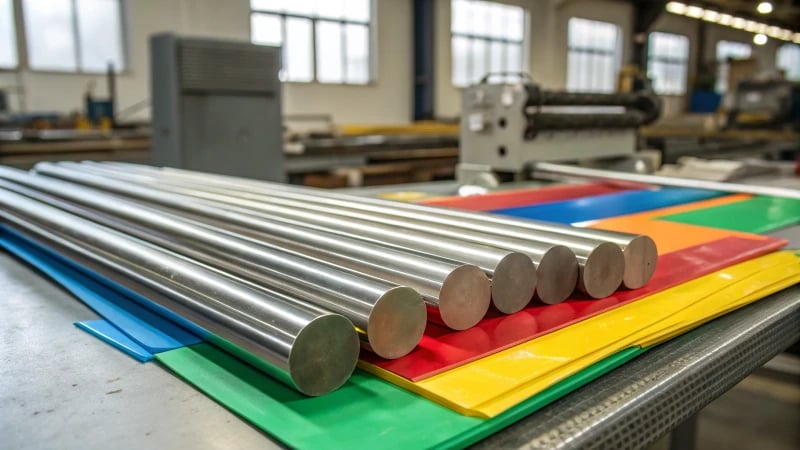
Material Cost
I recall the first time I chose between standard steel and a fancy alloy for a project. It felt like picking between a simple car and a luxury one – both had benefits, but their prices were far apart.
The type of raw material used directly affects the overall cost. For instance, steels like P20 offered a cheaper option, costing $1,500 to $3,000 per ton, allowing me to relax. When the project needed the strength of H13, costing over $10,000 per ton due to their enhanced properties, it became clear that the choice involved more than just money. It involved toughness and precision.
Material | Price Range (per ton) | Properties |
---|---|---|
P20 | $1,500-$3,000 | Standard |
H13 | $5,000-$10,000 | High-grade |
Machining Complexity
Picking the right material felt risky. Different materials require varying levels of machining complexity. One time, I underestimated machining complexity and wondered "How hard could it be?" Softer materials like P20 steel were easy to work with; they saved time and money. Conversely, tackling harder materials such as H13 showed me CNC machining was its own challenge.
The processing time for these techniques often determines cost efficiency6, with CNC costs ranging from $30 to $80 per hour. It was quite challenging—a tough lesson learned.
Surface Treatment Impact
Surface treatment added another layer to the decision-making process. Basic materials often just needed polishing while tougher ones required treatments like nitriding or chrome plating to enhance surface quality and wear resistance.
Treatment Type | Cost (per sq. meter) |
---|---|
Polishing | $20-$30 |
Nitriding | $80-$150 |
Chrome Plating | $150-$300 |
I remember holding my breath when the chrome plating cost nearly $300 per square meter—it was expensive indeed.
Material Choice and Production Efficiency
Material selection affects production efficiency7. I learned that choosing materials isn’t just about initial costs; one must look to the future. High-quality materials might hurt the budget at first yet save trouble later with faster production and fewer breakdowns.
Cheaper materials might seem good but often increase downtime due to wear and tear—turning savings into extra expenses.
These choices taught me to balance cost and performance. Every designer should understand this balance in order to create plastic parts that meet looks requirements while working well within budget constraints.
Simple mold designs cost $500 to $1,000.True
Simple molds with basic structures and small sizes have lower design costs.
CNC machining costs $80 per hour.False
CNC machining costs range from $60 to $80 per hour.
How Do Processing Techniques Impact Costs?
Finding your way through the expense puzzle of processing methods feels challenging for manufacturers. Budget balance and profit growth hold great importance. Let’s explore the details of mold design, raw materials and worker wages. Smart decisions rely on understanding these costs.
Different ways of processing have different costs. Mold design complexity, raw material quality and labor intensity really influence costs. Simple mold designs cost less. Detailed designs very much increase costs. Understanding these factors helps in planning and choosing the right process.
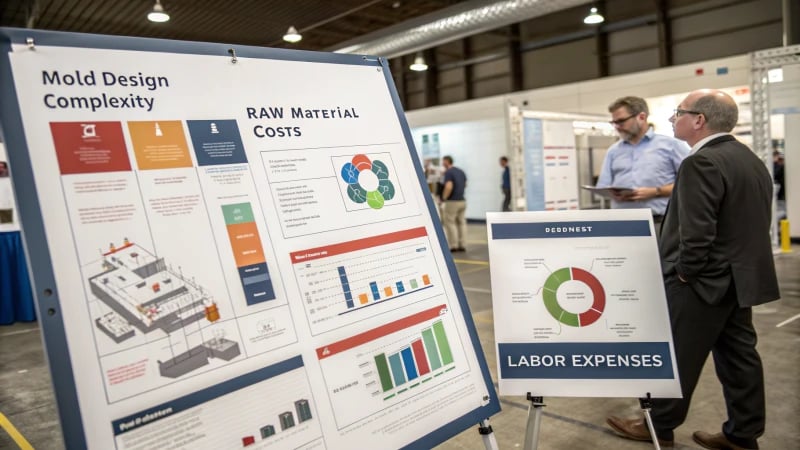
Impact of Mold Design on Costs
When I first started learning about mold design, the wide range of costs surprised me. A simple mold design8 might appear cheap, costing just a few thousand yuan. For example, small injection molds with uncomplicated structures can range from $500 to $1,000. Be careful though! If you need a complex mold with many features, prices rise fast. Automotive part molds often demand rigorous accuracy and strength, potentially pushing design costs to over $8,000.
Influence of Raw Material Selection
Choosing raw materials is another challenging task. Steel prices change greatly based on type and quality. Standard P20 or 718 steels cost between $1,500 and $3,000 per ton, which seems alright. However, if you need something stronger like H13, expect to pay $5,000 to $10,000 per ton.
Material Type | Cost Range per Ton |
---|---|
P20, 718 | 1,500 – 3,000 |
H13 | 5,000 – 10,000 |
Labor and Equipment Costs
Labor and equipment costs add more complexity. I initially underestimated how fast basic processing costs could rise—around $15-$30 an hour for simple cutting. Finer work like CNC machining or EDM raises rates to $30-$80 per hour or more.
Process Stage | Cost Description |
---|---|
Rough Processing | $15-$30 /hour |
CNC Machining | $30-$80 /hour |
EDM Processing | Calculated by area/depth |
Assembly and Debugging Expenses
Assembly and debugging offer their own difficulties. Labor costs differ by skill and location but usually range from $50-$100 daily. In one difficult assembly project involving car parts; we needed an injection molding machine just for testing—an extra cost calculated at about $10-$20 per ton per hour.
Assembly/Debugging | Cost Description |
---|---|
Assembly Labor | $50 – $100 /day |
Debugging Equipment Usage | Calculated by tonnage/time ($10-$15 /ton/hour) |
These cost factors are important in my journey as a designer. Designers must know these things as it helps in making smart decisions to improve both efficiency and profit. Anyone facing this challenging field might find it wise to study cost management strategies9 to improve their processes.
Mold design costs can exceed $15,000.True
Complex automotive molds require high precision, raising costs above $15,000.
EDM processing is cheaper than rough processing.False
EDM processing costs are higher due to complexity, unlike rough cutting.
How Do Assembly and Debugging Affect Overall Mold Costs?
Do you ever wonder why your mold manufacturing costs suddenly rise? Maybe assembly and debugging are the reasons behind it! Assembly and debugging stages often have a big effect on how much you spend.
Assembly and debugging greatly affect mold costs. They increase labor, waste material and equipment fees. More complex projects have higher costs. These elements are very important when planning mold production expenses. Important indeed.
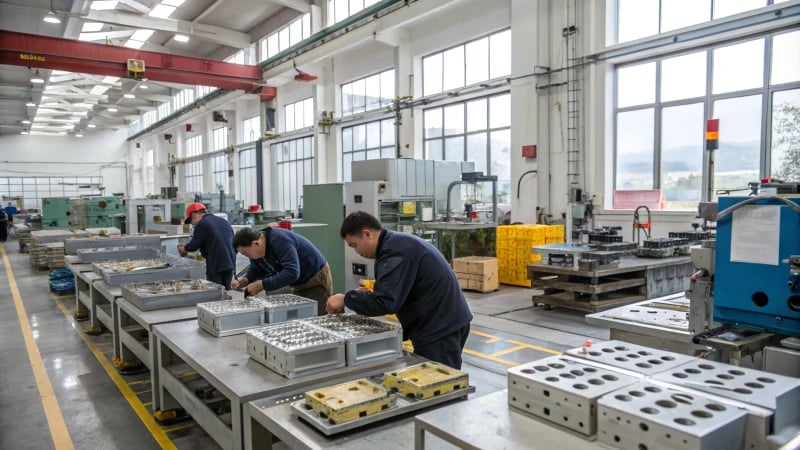
The Role of Assembly in Mold Costs
The assembly phase involves bringing together various components of a mold, which requires skilled labor. I remember my first time with a complex mold assembly; details seemed endless, with each part needing careful alignment and fit. It’s not just about putting parts together; it’s an art needing skilled hands. Mold costs vary greatly depending on complexity and local labor costs.
For instance, while simple molds are quick and easy to assemble, complex ones really challenge you, taking many hours and increasing labor costs10 from $50 to $80 daily. Specialized tools are also necessary, adding to the overall expense11.
Debugging: The Hidden Cost Factor
Debugging is like hunting for clues. Finding what doesn’t fit and fixing it must happen before mass production. Imagine doing many trial runs, which use both time and materials, just to check if the mold works perfectly.
In my early days, I spent endless hours debugging. Injection molding machine fees are based on tonnage and time—ranging from $8 to $15 hourly—and they add up fast. Plus, wasting materials during debugging can add to the costs, especially if high-grade materials are involved.
Balancing Efficiency and Cost
Eventually, I learned to juggle efficiency and cost. Optimizing assembly—sometimes using machines or training workers—helped reduce unneeded expenses.
A good initial design review saves big problems later. Using advanced simulation tools let me find problems early in the design phase; this was very helpful.
Cost Aspect | Simple Mold | Complex Mold |
---|---|---|
Assembly | Low | High |
Debugging | Moderate | Very High |
Understanding these factors allows us to budget smarter and plan better. It ensures competitive pricing without losing quality by exploring different strategies12 that can reduce unnecessary expenses while maintaining production standards.
Complex mold designs can exceed $15,000.True
Complex molds require precise structures, increasing design costs.
Nitriding treatment costs less than polishing.False
Nitriding is costlier, ranging from $80 to $150 per sq. meter.
Exploring the complex world of mold processing costs really feels overwhelming. Knowing what expenses to expect probably saves many problems later. Examine the expenses often ignored that could affect your budget.
Mold processing involves extra costs beyond the initial setup. These include mold design, buying raw materials, processing, assembly, debugging and other logistical expenses. Each factor probably affects the overall budget a lot.
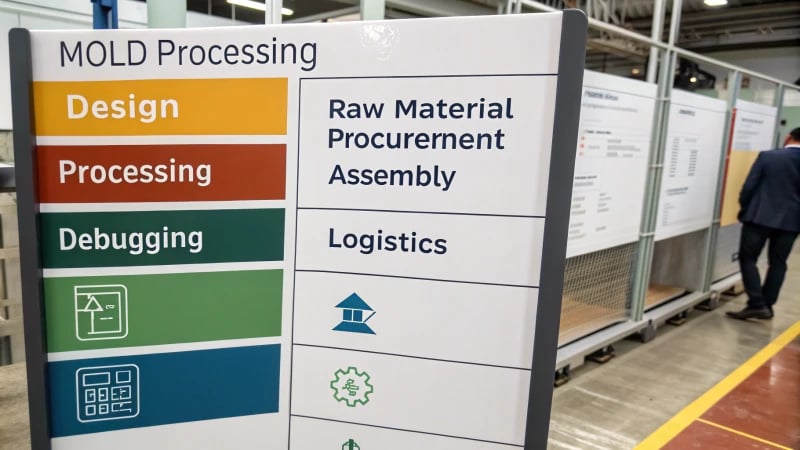
Mold Design Costs
When I first entered the mold processing world, I faced many unexpected costs. Starting wasn’t just about setting up; many small costs appeared. Each project taught me new things about managing money.
Designing molds is complex and varies in cost based on intricacy. I remember a simple mold design that cost more because it was complex. Automotive part molds often cost up to $15,000 due to precision requirements13. Precision is not just a nice-to-have; it is necessary.
Raw Material Expenses
Prices for raw materials like steel fluctuate a lot. Steel prices fluctuate based on type and quality. Basic steels like P20 or 718 sometimes cost between $1,500-$3,000 per ton. High-grade steels like H13 reach more than $5,000 per ton.
Material | Approximate Cost (USD) |
---|---|
P20/718 | 1,500 – 3,000 |
H13 | 5,000 – 10,000 |
Choosing the right material is highly important.
Processing Costs
Processing involves many steps, each adding costs. Processing includes rough and fine stages. I found costs from rough processing were around $15-$30/hour. Rough processing like cutting is cost-effective at around this rate. Fine CNC machining often costs between $30-$80/hour because it needs high precision requirements14.
Assembly and Debugging
First budgeting for assembly labor surprised me with fast-rising costs. Labor for assembly is another expense, with daily rates ranging from $50-$80. Debugging involves equipment usage costs like using injection molding machines at $10-$15 per ton/hour.
Miscellaneous Expenses
Transporting molds and extra processing fees surprise many, ranging from hundreds to thousands of yuan. Transportation for delivery or additional processing adds these costs as well as management overheads which can take up to 5%-10% of total costs.
Thinking about these expenses shows me that careful planning for each part of mold processing stops bad surprises. Better preparation saves finances and keeps production running smoothly.
Complex mold designs cost over $8,000.True
Complex molds require precision and specialized structures, increasing costs.
Standard mold parts cost over $1,500 each.False
Standard parts generally range few hundred dollars.
Conclusion
Injection mold processing costs vary widely based on design complexity, material choice, and labor. Simple molds may cost $500-$1,000 yuan, while complex designs can exceed $15,000.
-
Explore this link to understand why automotive molds can be costly due to high design requirements. ↩
-
Discover how high-grade steel enhances mold durability and precision in demanding applications. ↩
-
Learn strategies to optimize injection molding costs for more efficient production processes. ↩
-
Explore how different design elements affect mold costs to better understand budget planning for projects. ↩
-
Discover expert services that can guide you in balancing design complexity with cost efficiency for optimal production outcomes. ↩
-
Learn how CNC machining time and costs influence the overall expenses of mold processing. ↩
-
Discover how different raw materials impact production efficiency and cycle times in molding processes. ↩
-
Discovering simple mold designs’ cost can help identify budget-friendly options for small-scale production. ↩
-
Exploring cost management strategies can enhance your understanding of optimizing production efficiency and profitability. ↩
-
Learn about the influence of skilled labor on mold assembly costs to manage budget effectively. ↩
-
Discover essential equipment for accurate mold assembly to optimize your manufacturing process. ↩
-
Explore effective strategies to lower mold production costs while maintaining quality. ↩
-
Understand the high standards for automotive molds to justify their design cost. ↩
-
Learn about CNC machining’s role in achieving precise mold structures. ↩