Have you ever thought about why some molds seem to last a long time while others fall apart quickly during a project?
Mold processing methods impact mold lifespan. Dimensional accuracy, surface quality and heat treatment order play parts. Accurate processing creates uniform molds. This uniformity decreases wear and stops defects. This prolongs mold life.
I remember my early days in mold design. The lifespan of my designs puzzled me. Technology in processing plays a very important role. It is the hidden hero that decides if a mold lasts or not. Dimensional accuracy remains vital. Imagine baking a cake. Wrong measurements lead to unexpected results. Keeping mold parts in the right position stops friction and wear.
Surface quality matters a lot. Think of it this way꞉ smoother surfaces face less resistance during demolding. By reducing roughness, wear and tear really decreases. Mold processing order is crucial too. Like baking, you don’t frost a cake before baking it. Correct order of roughing and finishing keeps molds accurate and intact.
Special techniques like EDM and wire cutting demand careful attention. Treating surfaces after processing prevents defects. Extra care helps a mold last. These details in processing taught me this꞉ extending mold life is practical with the right approach.
High dimensional accuracy extends mold service life.True
Accurate dimensions reduce local wear and ensure uniform flow, prolonging mold life.
EDM improves mold surface quality without further treatment.False
EDM creates a metamorphic layer that requires removal to maintain mold quality.
- 1. Why is Dimensional Accuracy Essential for Mold Longevity?
- 2. How Does Surface Quality Impact Mold Wear and Tear?
- 3. Why is the processing sequence crucial for mold durability?
- 4. Can Special Processing Techniques Extend Mold Life?
- 5. How Do Heat Treatment Processes Affect Mold Performance?
- 6. Conclusion
Why is Dimensional Accuracy Essential for Mold Longevity?
Precision in mold crafting is not only about perfect fits. It plays a crucial role in the durability of molds and their excellent performance.
Exact dimensions are critical for mold life. Proper alignment during the injection process reduces stress and wear. This accuracy lessens friction, leading to even flow. If flow is smooth, deformation is avoided. These factors help the mold last longer. A longer-lasting mold is always beneficial.
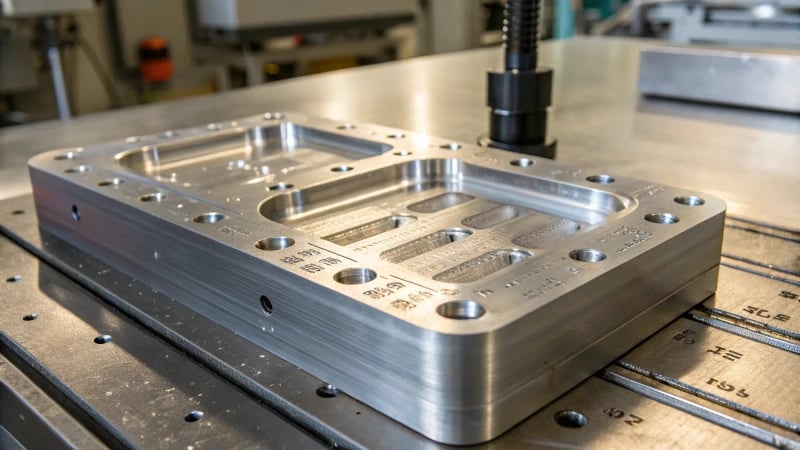
Importance of Dimensional Accuracy
Dimensional accuracy is more than just a technical term; it is the quiet hero that keeps everything working well. From my own design work, I’ve learned that ensuring each component meets design specifications allows for perfect alignment during injection molding1. This precision prevents local pressure build-up, which can lead to increased wear.
Key Factors Influencing Mold Longevity
1. Processing Accuracy
-
Dimensional accuracy ensures the mold’s parts fit perfectly, leading to uniform wall thickness. A lack of precision can cause local pressure points, resulting in accelerated wear.
Aspect Impact on Mold Dimensional Ensures matching during molding Positional Reduces friction and part collision
2. Surface Quality
- Imagine a smooth stone in a river compared to a rough rock. The smoother the surface, the less resistance during plastic flow. Reduced friction means less wear and prolonged mold life. For instance, a surface roughness of Ra0.1μm can lower wear by up to 50%.
3. Processing Sequence
- Proper sequencing, like roughing before finishing, feels like arranging a dance. It ensures even machining allowances and mitigates stress-induced deformations.
4. Special Processing Technology
- Technologies like EDM introduce complexity and possible pitfalls that need addressing post-processing to maintain mold integrity.
Practical Considerations for Designers
For designers like me, incorporating dimensional accuracy into the early stages of mold design is not only clever; it’s very important. Understanding how different factors2 affect mold life helps in planning for durability and cost efficiency. Adjustments in design can lead to significant improvements in longevity.
- Heat Treatment: Timing matters a lot; proper timing and execution of heat treatments are crucial to avoid post-processing deformations that might ruin all the careful planning.
- EDM Surface Treatment: Post-EDM polishing or grinding removes any detrimental surface layers, keeping molds in really good condition.
By focusing on these elements, I can extend mold life significantly, ensuring my designs reach their goals effectively.
High mold accuracy extends mold service life.True
Accurate dimensions prevent excessive wear, ensuring longer mold lifespan.
Surface roughness has no impact on mold wear.False
Smooth surfaces reduce friction and wear, extending mold life.
How Does Surface Quality Impact Mold Wear and Tear?
Ever wondered how the smallest details create the biggest changes in mold strength?
Surface quality greatly affects mold wear and tear. It influences friction, material flow and surface interactions. A smooth surface decreases friction. This helps mold last longer. It also raises product quality. A smooth surface is important.
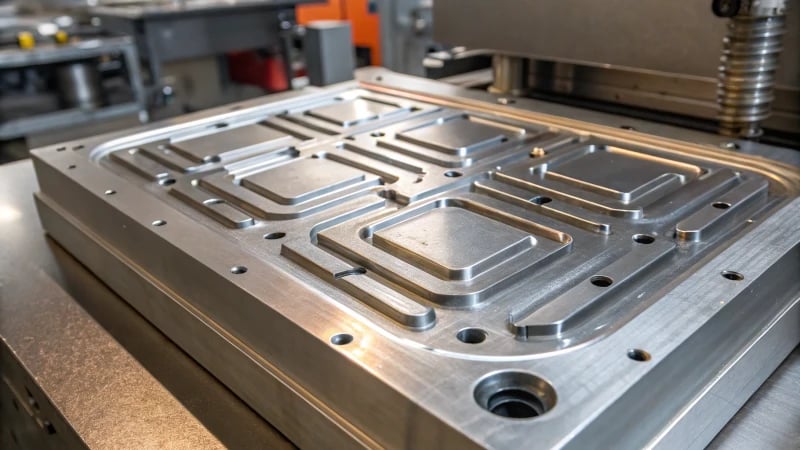
Role of Surface Roughness
I remember my team discussing how surface roughness impacts performance. A smoother surface3 lowers friction, much like smooth roads are gentle on car tires. Rough molds face more friction, leading to quicker wear. Polishing a mold to Ra0.1μm or less reduces wear by 30% – 50% compared to rough molds. This polishing not only extends mold life but also gives a better product finish.
Impact of Surface Integrity
Surface integrity resembles taking care of your skin. Microcracks and burns weaken durability, just like ignoring health affects our well-being. During molding, pressure makes microcracks grow, causing failures. Burns change material structure, leading to corrosion. Keeping surface integrity strong is vital to stop these problems.
Processing Accuracy: Dimensional and Positional
Processing accuracy felt like building furniture without directions – a small mistake causes imbalance. High dimensional accuracy meets design needs, avoiding uneven pressure that causes wear. Good positional accuracy, like flatness and coaxiality, keeps mold movements smooth.
Aspect | Influence on Mold Life |
---|---|
Dimensional Accuracy | Ensures even pressure distribution |
Positional Accuracy | Minimizes friction during movement |
For instance, coaxial guide pins stop deflection and uneven core-cavity interactions. Smooth interactions are crucial.
Influence of Processing Sequence
Once, I saw how processing sequence impacts a project. Correct sequence, like heat treatment before machining, improves surface quality. Heat treatments after roughing reduce stress and prevent bending.
Without proper sequence adherence, uneven allowances can cause excessive cutting forces affecting both dimensional accuracy and surface quality.
Special Processing Technologies
Techniques like Electrodischarge Machining (EDM) act like a precise scalpel for complex molds but may add flaws like metamorphic layers. On a project, we had to grind after EDM to remove these layers and extend mold life.
Employing techniques such as stress relief tempering after wire cutting helps eliminate microcracks and improve fatigue resistance.
For more on advanced mold processing4 methods, reading specialized books offers full guidance on improving mold durability.
High dimensional accuracy extends mold life.True
Accurate dimensions ensure uniform pressure distribution, reducing wear.
EDM does not affect mold surface quality.False
EDM creates a metamorphic layer needing removal to prevent defects.
Why is the processing sequence crucial for mold durability?
Picture the frustration when a mold breaks while you work. Knowing processing steps helps avoid this trouble. This knowledge saves both time and money.
The order of tasks is vital for mold strength. It helps shape parts accurately, keeps materials from bending and gives surfaces a better finish. Doing tasks in the correct order likely makes the mold last longer. It helps keep details precise and lessens damage over time.
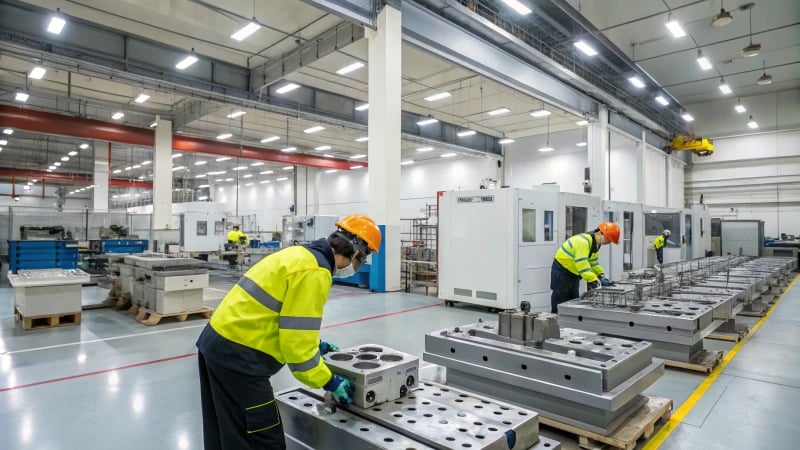
The Importance of Processing Order for Mold Lifespan
Processing order is crucial for mold lifespan, much like setting up dominos—if one piece is off, everything falls apart. A careful processing order balances rough and detailed work, spreading out the workload evenly. During rough work, most material is removed quickly, preparing everything for the fine details.
Stage | Importance |
---|---|
Roughing | Removes bulk material, sets up for finishing |
Finishing | Achieves precision, improves surface quality |
Heat Treatment | Enhances hardness, must be correctly timed |
Dimensional Accuracy: Imagine how important it is in furniture assembly—everything must fit exactly right. Parts must match design plans to keep molds accurate during injection molding. If the cavity’s dimensional accuracy5 is wrong, you may get too much wear in certain spots.
Position Accuracy and Surface Quality
Position accuracy is like having bike tires aligned properly—it makes everything run smoothly. Good position accuracy cuts down friction between mold pieces. For instance, keeping all parts lined up nicely stops uneven wear between the core and cavity, extending the mold’s life.
Surface quality is very important. Think of skating on rough ice versus smooth ice; a smoother surface cuts down resistance during molding. It also makes it easier to remove the finished piece. Methods like precision grinding6 really increase wear resistance by making surfaces smoother.
Timing of Heat Treatment
Timing is critical—something I first learned on a tough project! Heat treatments should follow rough processing to correct any warping. This helps keep molds precise and durable.
Mastering these steps allows experts to improve processes for longer-lasting molds. This cuts costs and probably keeps products consistent. For more on heat treatment benefits7, try delving deeper into resources.
Understanding the right processing order not only keeps the mold strong but also significantly increases its lifespan. This brings big benefits to manufacturing efficiency and quality.
Special Processing Methods
Methods like Electrodischarge Machining (EDM)8 tackle tough shapes but might leave unwanted layers needing removal for endurance. Also, wire cutting might cause microcracks that need care to avoid reduced fatigue resistance.
Summary Table:
Technology | Potential Issue | Solution |
---|---|---|
EDM | Metamorphic layer | Grinding/Polishing |
Wire Cutting | Microcracks | Stress relief tempering |
Experts in product design should know these factors when planning mold production strategies to achieve great durability and performance. More details on wire cutting treatments9 are available for those interested.
Knowing every part of the processing order is essential for optimizing mold lifespan in different manufacturing settings.
High dimensional accuracy ensures mold longevity.True
Accurate dimensions prevent uneven pressure, reducing wear and extending mold life.
EDM processing increases mold surface hardness.False
EDM creates a softer metamorphic layer, requiring post-treatment to ensure durability.
Can Special Processing Techniques Extend Mold Life?
Ever wondered if a secret exists to keep molds lasting longer in manufacturing?
Special methods like Electrodischarge Machining (EDM) and wire cutting extend mold life. They improve dimensions, surface look and how processes occur. These changes lower wear and tear. Mold service life becomes longer. Molds last longer.
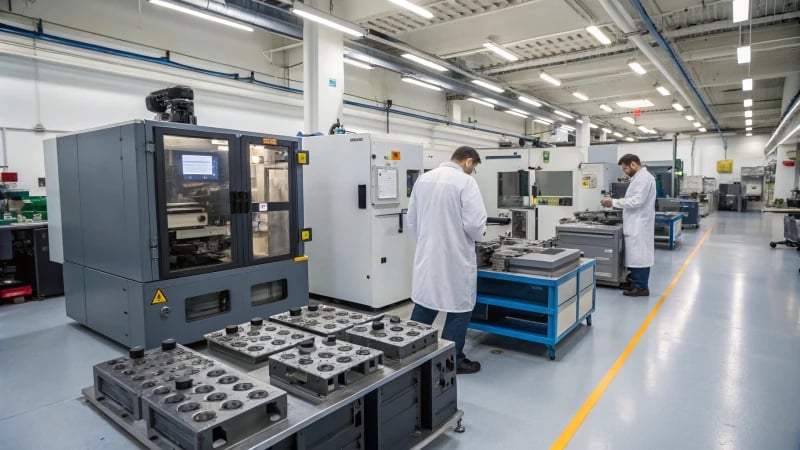
Influence of Processing Accuracy
At the start of my journey in mold design, I realized how very important precision is. Think of building a puzzle where each piece must fit just right. This is high dimensional accuracy10 in molds. It aligns every part exactly to create even wall thickness in products. This careful alignment stops unnecessary pressure, which then reduces local wear.
Dimensional and Positional Accuracy
I’ve discovered that reaching perfect positional accuracy11 is like tuning a fine musical instrument. Small details such as flatness and coaxiality matter a lot. For example, the coaxiality between a guide pin and its sleeve helps the mold move smoothly. This minimizes friction and keeps parts from clashing.
Surface Quality: Roughness and Integrity
I still remember how surface quality transformed my first project. Smoother surfaces lower resistance for plastic flow inside cavities, which makes demolding easy and cuts down on wear from friction. A mold surface refined to a roughness of Ra0.1μm can cut wear by up to 50%. This really extends mold life. This fact is crucial.
Surface Roughness Level | Wear Rate Reduction |
---|---|
High | Minimal |
Low (Ra0.1μm) | 30%-50% |
Keeping the surface intact is vital too. Avoiding small cracks and burns during processing is key as these can grow under pressure and can break the mold over time.
Processing Sequence Considerations
I was surprised by how much the order of operations matters. During roughing, most excess material is removed, setting the stage for precision finishing. Spreading the allowance properly is important to keep machining accuracy and surface quality.
Timing heat treatment is very important for mold life. Doing heat treatment after rough machining but before finishing helps remove internal stresses and fix any deformations.
Special Processing Techniques: EDM and Wire Cutting
Electrodischarge Machining (EDM) is useful for complex shapes; however, it leaves a layer that must be polished to keep mold precision.
Wire Cutting introduces layers and small cracks that lower fatigue resistance. Using techniques like stress relief tempering can ease these effects, boosting surface integrity.
Processing Technique | Post-Processing Requirement |
---|---|
EDM | Grinding or Polishing |
Wire Cutting | Stress Relief Tempering, Surface Treatment |
Careful use of these special techniques helps designers like me extend the life of molds12. We aim for better accuracy and quality to face the challenges of manufacturing environments.
High dimensional accuracy reduces mold wear.True
Accurate dimensions prevent uneven pressure, reducing local mold wear.
Surface roughness has no effect on mold lifespan.False
Lower roughness decreases friction, extending the mold's service life.
How Do Heat Treatment Processes Affect Mold Performance?
Picture changing a plain metal block into a mold that lasts for a long time. Heat treatment plays an important role in this process. However, how does this heat process truly affect how the mold works? Let’s explore the details.
Heat treatment processes improve mold performance by increasing hardness and toughness. These processes reduce wear and deformation, too. People use them after rough machining but before fine machining. Molds gain precision through this method. They also last longer. Very long, actually.
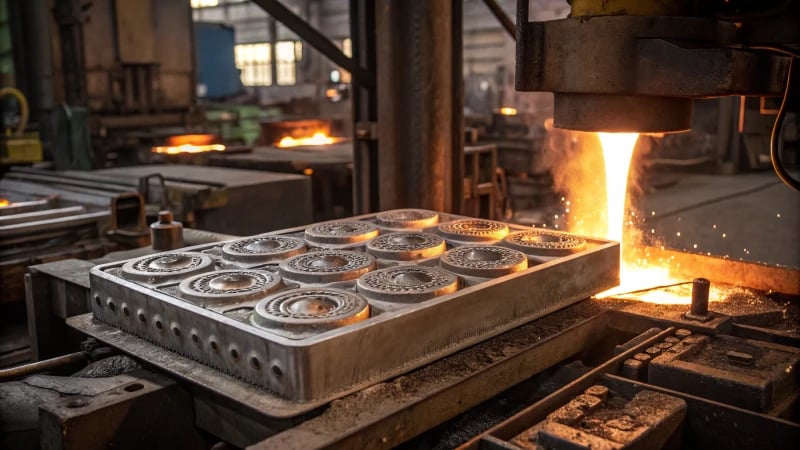
The Role of Hardness and Toughness
Imagine when everything in a project fits together just right. Heat treatment does this for molds. Adjusting hardness and toughness13 is like giving molds the endurance of a marathon runner. Temperature control and cooling speed shape these qualities. Very hard molds resist wear, while tough ones endure continuous impact. Important properties. Really important.
Sequencing and Accuracy
Timing is crucial. Proper sequencing of heat treatments is critical. Perform them after rough machining but before fine machining. This sequence removes stresses and allows corrections, ensuring high dimensional accuracy, like a perfectly synchronized clock.
Process Stage | Description |
---|---|
Rough Machining | Initial shaping with allowances for finishing adjustments. |
Heat Treatment | Alters material properties for improved durability. |
Fine Machining | Final adjustments to correct deformations and ensure accuracy. |
Mitigating Deformation and Cracking
Improper heat treatment can cause problems—huge problems like deformation and cracking that harm mold performance. However, by implementing appropriate heat treatment methods14, manufacturers can reduce these issues, extending mold life.
Surface treatments like tempering follow heat treatment to relieve internal stresses and add a protective layer, reducing microcracks—really protective.
Special Processing Techniques
Working with complex molds is challenging, like solving a tricky puzzle. Techniques such as electrodischarge machining (EDM)15 help despite creating surface defects that require further treatments to maintain mold accuracy.
In short, effective heat treatment shapes high-performance molds, ensuring they meet design needs while lasting long and working reliably in tough production settings.
High mold dimensional accuracy reduces local wear.True
Accurate dimensions ensure uniform pressure distribution, minimizing wear.
EDM leaves no impact on mold surface hardness.False
EDM creates a metamorphic layer that alters surface hardness.
Conclusion
Mold processing technology significantly influences mold lifespan through dimensional accuracy, surface quality, and proper sequencing, ensuring durability and efficiency in manufacturing processes.
-
Exploring this link provides an in-depth understanding of how dimensional accuracy influences the molding process, crucial for designers and engineers. ↩
-
This link offers insights into various factors impacting mold longevity, aiding in comprehensive mold design and maintenance strategies. ↩
-
Understanding how surface roughness impacts molding can lead to improved processes and longer-lasting molds. ↩
-
Explore cutting-edge methods in mold processing to enhance durability and efficiency. ↩
-
Explore how dimensional accuracy affects injection molding efficiency and product quality. ↩
-
Learn about how precision grinding enhances mold surface quality and longevity. ↩
-
Understand why correct timing of heat treatments is crucial for material durability. ↩
-
Discover how EDM can shape complex molds while understanding its limitations. ↩
-
Find ways to mitigate the negative effects of wire cutting on mold surfaces. ↩
-
Understanding dimensional accuracy is crucial for ensuring uniformity in product thickness, which reduces wear on molds. ↩
-
Learn how positional accuracy prevents friction and extends mold life by ensuring smooth operation. ↩
-
Explore various techniques to enhance mold lifespan, focusing on processing accuracy and surface quality. ↩
-
Understanding how heat treatment affects hardness and toughness can guide material selection for molds. ↩
-
Best practices in heat treatment help avoid deformation, enhancing mold accuracy and lifespan. ↩
-
Learning about EDM impacts can help refine post-processing treatments to maintain mold quality. ↩