Have you ever noticed the strain of increasing labor expenses in injection molding and thought about ways to handle them more effectively?
Optimize injection molding labor costs by automating processes, improving workflow efficiency, using skilled operators, minimizing downtime, and implementing regular maintenance.
These strategies set up the basics for saving money. Looking closer reveals even better ideas. It’s similar to when I began improving my work methods. The first changes were only the beginning. Seeing how these methods fit into your operations truly changes your efficiency and profits. Each strategy deserves a closer look.
Automation reduces labor costs in injection molding.True
Automated systems reduce manual operation, lowering labor costs.
Trained employees increase equipment downtime.False
Skilled operators reduce downtime by efficiently handling tasks.
- 1. How Does Automation Help Cut Down on Labor Costs?
- 2. How Can Employee Training Improve Production Efficiency?
- 3. Why Is Process Optimization Essential for Cost Reduction?
- 4. How Do Performance Incentives Affect Labor Costs?
- 5. How Can Intelligent Monitoring Systems Transform Your Operations?
- 6. Conclusion
How Does Automation Help Cut Down on Labor Costs?
Automation is not just a trendy term; it is the main way to change our work and life. It reduces costs and improves efficiency.
Automation lowers labor expenses. It simplifies manual work. It also increases efficiency. Resource use gets optimized with new technologies. Intelligent production systems play a role too. They are very useful. Skill training adds value. These methods are really important.
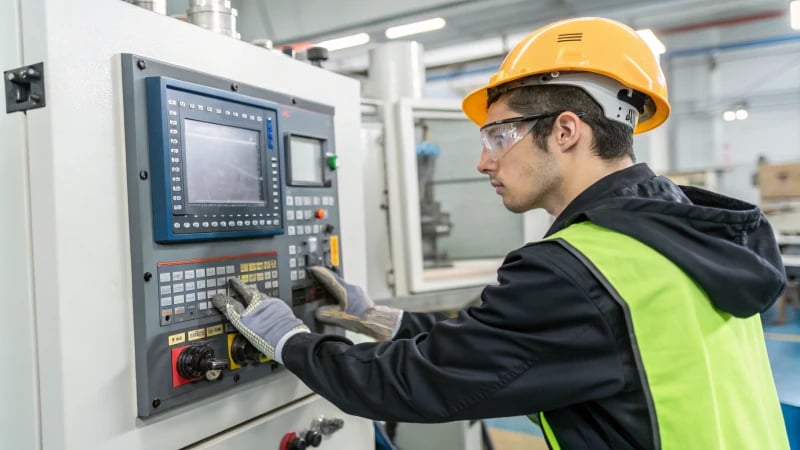
Intelligent Production Systems
Picture yourself stepping onto a production floor where machines almost operate on their own. This scene unfolded when we introduced automated injection molding machines. These machines, with automatic loaders and unloaders, let one worker manage several machines. It felt like watching an efficient dance. Output grew without needing more workers, reducing labor costs and improving production per worker with new equipment.
Consider the intelligent monitoring system next. Imagine relaxing with a coffee while the system watches every production detail. It sends an alert if something’s wrong, letting us act quickly. This automation reduced manual checks and made quality control much better.
Automation Feature | Benefit |
---|---|
Automated Machines | Reduces manual labor and increases efficiency |
Intelligent Monitoring | Improves quality control and reduces errors |
Employee Training and Skill Development
The human touch is important too. Automation means smarter machines, but it also means we work smarter. With professional skills training, our team learned to run complex machines and handle quality control confidently. Trained operators could change molds quickly, keeping production steady.
The multi-skill training followed. Handling both operations and basic maintenance uplifted everyone. We didn’t wait for special help; we fixed minor issues ourselves. This flexibility kept things running and reduced the need for more staff.
Process Optimization and Task Assignment
Improving production processes was like tidying a cluttered room. We reengineered and streamlined processes, removing unnecessary steps using efficient inspection methods, which relieved our inspectors significantly.
Assigning tasks based on employee skill levels optimizes workforce output. Complex tasks should go to experienced workers, while simpler ones can be handled by newer staff members.
Performance Incentive Systems
We set up a performance review system to give us a push. Rewards for hitting high production and quality standards made a big difference. Everyone aimed higher, with bonuses or promotions as motivation.
We also introduced a cost savings reward program where everyone became like mini-consultants, finding ways to cut costs and improve processes. The company saved money, and employees felt ownership and pride in their work.
Incentive Type | Impact on Labor Costs |
---|---|
Performance Appraisal | Motivates higher efficiency and quality |
Cost Savings Rewards | Encourages innovation and cost control |
Automation wasn’t just about cutting costs; it changed our work, empowered our team, and opened new doors.
Automation reduces labor costs per unit product.True
Automated systems increase efficiency, reducing manual labor needs.
Employee training increases equipment downtime.False
Training enhances skills, allowing faster problem-solving and reducing downtime.
How Can Employee Training Improve Production Efficiency?
Do you ever think about how training changes how well your team works? Training provides team members with the right skills. This helps work go smoother and increases how much work they complete.
Employee training increases production efficiency by improving skills, reducing downtime and fostering a culture of constant progress. It gives staff the power to handle equipment effectively. Workers solve small problems quickly. They adapt to new technologies easily.
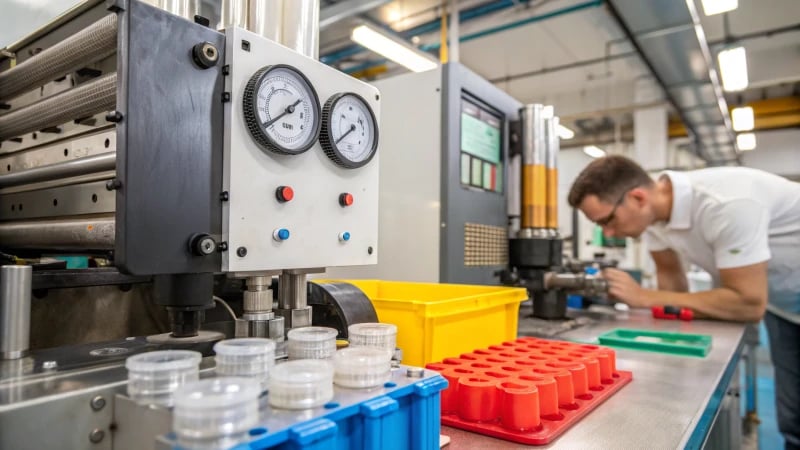
Building Skills for Better Productivity
Training gives workers the important skills needed for greater output. Look at injection molding as an example. Specialized skills training1 really cuts down machine downtime. Workers learn to quickly change molds, keeping production on schedule.
Table 1: Benefits of Specialized Skills Training
Training Focus | Impact on Efficiency |
---|---|
Mold Maintenance | Reduced downtime |
Quality Control | Enhanced product consistency |
Equipment Operation | Increased speed and accuracy |
In my first year, I saw a colleague improve and save time with focused training. Minutes saved in mold changes became hours saved every week. This showed how important skill improvement is.
Training for Multiple Skills and Flexibility
Employees with various skills add flexibility and improve production flow. When staff handle equipment and simple maintenance, they solve minor issues fast, keeping work running smoothly without waiting for specialists.
A co-worker once fixed small machine problems quicker than we could even call maintenance. During busy times, this was a very big help.
Working with Automation and Skilled Workers
Automation reduces physical work, but skilled employees must handle these machines well. Workers good with automated systems monitor and manage alerts effectively. Intelligent monitoring systems need operators to understand data and make quick changes.
Table 2: Integration of Training and Automation
Automation Feature | Training Requirement |
---|---|
Automatic Loading Devices | Basic operational knowledge |
Intelligent Monitoring | Data analysis skills |
Manipulators | Hands-on troubleshooting experience |
Thinking back, I see how providing employees with the right knowledge always improved efficiency and brought innovation.
Matching Work Through Training
Strategic task assignment uses employee skills wisely. Giving complex tasks to experienced workers and simpler ones to newcomers enhances contribution and keeps work efficient. This practice not only refines processes but also helps employees grow through reasonable work allocation2.
I recall getting tasks that suited my growing skills. It motivated me and kept me engaged, knowing that I was learning and contributing well.
Building a Culture of Ongoing Improvement
Training goes beyond just learning skills; it builds a culture of innovation and steady progress. Offering rewards for efficiency and new ideas encourages employees to use their training creatively, leading to important cost savings3 and better production outcomes.
Remembering these strategies, I recall vital lessons from training that boosted my work efficiency and opened many doors for growth.
Automation reduces labor costs in injection molding.True
Automated equipment decreases manual reliance, enhancing efficiency.
Employee training has no impact on production efficiency.False
Training improves skills, reducing downtime and boosting productivity.
Why Is Process Optimization Essential for Cost Reduction?
Do you ever feel like your factory methods could work better, helping you save time and money?
Process optimization holds great importance for reducing expenses. It organizes tasks better, lowers waste and improves efficiency. Upgraded equipment helps. Smart monitoring serves well. Employee skills might need improvement. Companies reduce labor expenses by doing this. They also increase output.
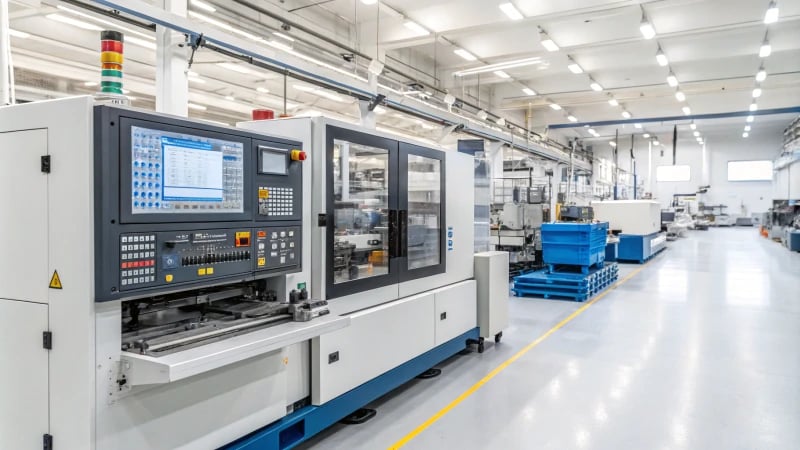
The Role of Technology in Process Optimization
The first time I watched an automated injection molding machine, it amazed me. One person controlled several machines because they loaded and unloaded by themselves. This automation changes everything. Fewer people need to work manually and it increases production efficiency per person. Intelligent monitoring systems4 adjust automatically in real-time to keep quality high. Fewer mistakes slip through because of this.
Equipment Upgrade Benefits | Description |
---|---|
Labor Efficiency | One operator can manage multiple machines, cutting labor costs. |
Quality Assurance | Reduces errors by automating quality checks and adjustments. |
Building Workforce Skills
In the past, people usually learned skills on the job. Today, formal training really helps. Skilled workers change molds quickly, which means machines don’t stop for long. Multi-skill training turns workers into versatile experts who solve small problems that would otherwise stop production.
- Skillful Workers: They change molds quickly, cutting down equipment idle time.
- Versatile Training: Workers manage both operations and fixes, raising productivity.
Improving Workflows
I once joined a project to rethink our process, breaking it down completely. I was surprised by the many unnecessary steps we found. We used better sampling methods for inspections which reduced the inspection work while keeping product quality high.
Optimization Strategy | Outcome |
---|---|
Process Reengineering | Removes redundant operations for smoother workflows. |
Work Allocation | Assigns tasks based on employee expertise to maximize efficiency. |
Inspiring Through Rewards
In my experience, a good performance incentive inspires a team. I’ve seen people work hard when they know there are bonuses or promotions available. A fair system that rewards efficiency and quality pushes everyone to do their best.
Cost Savings Reward Program5 shares the gains from cost control with those who achieve it.
By focusing on these strategies, I’ve seen businesses improve their efficiency with lower costs and much better profits, helping them stand out more in the market.
Automation reduces labor costs in injection molding.True
Automated systems decrease reliance on manual labor, cutting costs.
Intelligent monitoring systems increase production downtime.False
Monitoring systems prevent downtime by detecting issues early.
How Do Performance Incentives Affect Labor Costs?
Visualize trying to inspire your team using rewards, only to face surprise expenses. This situation resembles a Jenga game. One incorrect move might topple everything. It might just collapse.
Performance incentives affect labor costs by pushing employees to work harder, leading to better efficiency and reduced costs per unit. Careful management is crucial. Poorly handled incentives raise costs without boosting output.
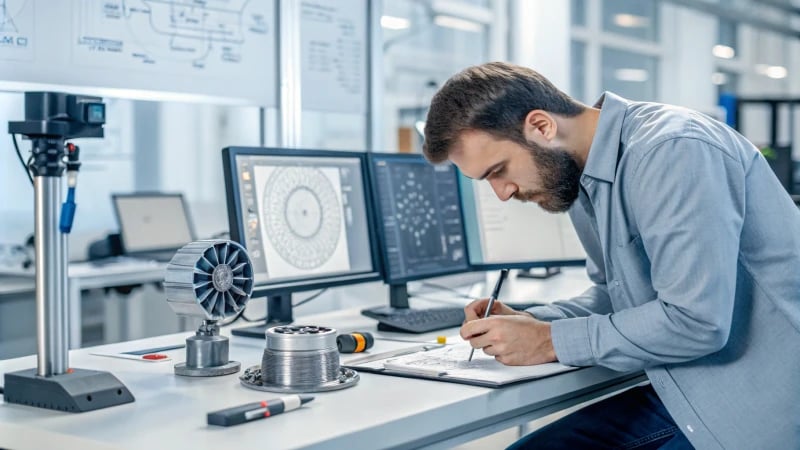
The Role of Performance Incentives in Labor Cost Management
I remember introducing performance incentives to my team. The concept was simple: reward top performers. Yet, it’s a careful balance. Poor design might lead to higher expenses with no benefit. A friend at a manufacturing firm set up a cost-saving reward system. Workers wanted to reduce waste and improve processes. Those who saved costs received rewards. Employees worked harder and the company reduced expenses.
Performance incentives are designed to motivate employees by rewarding them for meeting or exceeding certain targets. These incentives can take various forms, including bonuses, promotions, and cost-saving rewards. When structured effectively6, such incentives can align employee goals with organizational objectives, leading to improved efficiency and reduced labor costs.
Consider a scenario where a manufacturing company establishes a cost-saving reward program. Employees are encouraged to optimize production processes and reduce waste. Those who achieve significant cost savings receive a percentage of the savings as a reward. This not only motivates employees to think critically about their work processes but also directly impacts the company’s bottom line by lowering overall production costs.
Automation and Intelligent Production
Automation seemed like science fiction years ago. Now, it’s a normal part of industry. New automated systems allow one person to run several machines, reducing the need for manual work. Picture an intelligent system adjusting settings instantly – mistakes and guessing are problems of the past.
Incorporating automation into the production process can significantly reduce labor costs. For example, upgrading equipment with automated loading and unloading devices allows one operator to manage multiple machines simultaneously. This reduces the need for manual intervention, thereby decreasing labor costs per unit product.
Moreover, an intelligent monitoring system7 can further enhance efficiency by providing real-time data on production parameters. Such systems can automatically adjust settings to maintain quality, reducing the need for frequent manual inspections and minimizing errors.
Employee Training and Skill Improvement
Training changed our operations greatly. Skilled employees handled tasks like mold changes quickly, reducing downtime. Multi-skill training allowed them to fix small problems, keeping production smooth without needing experts.
Investing in employee training is another strategy that complements performance incentives. By offering professional skills training in areas like mold maintenance and quality control, employees become more proficient and efficient. Skilled operators can perform tasks like mold changes swiftly, reducing equipment downtime and indirectly lowering labor costs.
Additionally, multi-skill training empowers employees to handle minor maintenance issues themselves. This reduces reliance on specialized maintenance staff and ensures production continuity, further optimizing labor costs.
Training Type | Benefits |
---|---|
Professional Skills | Faster task completion, reduced downtime |
Multi-skill Training | Self-reliant workforce, reduced maintenance wait times |
Optimizing Production Process and Work Allocation
Analyzing and redesigning processes can reveal hidden problems. For example, online quality checks replaced traditional inspections, letting inspectors focus on important work.
Analyzing and reengineering production processes can eliminate inefficiencies. For instance, simplifying the product inspection process with online quality inspection equipment reduces inspector workload and enhances overall productivity.
Moreover, reasonable work allocation based on employee skills ensures that each individual contributes maximally to the production process. Assigning complex tasks to experienced employees while delegating simpler ones to newcomers optimizes both individual and team productivity, reducing labor costs across the board.
Crafting effective performance incentives needs careful thought using this approach with strategic automation8, employee training and process refinement; businesses really motivate their teams and control labor expenses wisely.
Automation reduces labor costs in injection molding.True
Automated equipment minimizes manual operations, lowering per unit labor costs.
Employee training does not affect production efficiency.False
Trained employees perform tasks faster, improving overall production efficiency.
How Can Intelligent Monitoring Systems Transform Your Operations?
Picture a digital assistant keeping your tasks organized. It predicts issues before they occur. This is the wonder of smart monitoring systems.
Smart monitoring systems transform operations with real-time data study, predictive repair and better efficiency. These systems automate jobs, reducing mistakes by people. Decisions get better, which ultimately cuts expenses. Productivity grows.
Improving Operational Efficiency with Smart Monitoring
Technology fascinates me. It takes boring tasks away, leaving us free to focus on important things. Smart monitoring systems work like a backstage team, keeping things running smoothly. They analyze huge amounts of data quickly. This speed lets us adjust things before problems grow big. In my experience, they change manufacturing floors by watching production details. Alerts come before small glitches turn into major issues.
Predictive Maintenance
A thrilling part of these systems is their ability to predict when something could go wrong. Imagine this: everything seems okay, but a machine is about to fail. Predictive maintenance stops such surprises. I remember avoiding an expensive shutdown because the system pointed out an issue in the data. Maintenance was scheduled just in time, saving stress and money.
Table: Benefits of Predictive Maintenance
Benefit | Description |
---|---|
Reduced Downtime | Prevents unexpected breakdowns |
Cost Savings | Minimizes emergency repair costs |
Extended Equipment Life | Maintains optimal operating conditions |
Real-Time Alerts and Quick Decisions
Real-time alerts help us stay in control by providing immediate understanding of the current situation. I saw their importance in fast-paced places like healthcare, where every second can be vital. Data shown on clear dashboards helps us decide quickly and wisely—it’s like a navigation tool guiding us away from troubles.
Lowering Human Mistakes
Mistakes happen, and when avoidable ones occur, it frustrates everyone involved. Smart systems automate monitoring tasks, significantly reducing human errors. For instance, in quality control processes, these systems detect defects that even the best inspectors might miss.
Automated inspection technologies9 keep product quality very high consistently, building trust and satisfaction with customers.
Automation and Smart Production
Automation changed everything for us by introducing robotic arms that lowered our need for manual work while increasing production efficiency too. I recall integrating a smart monitoring system that watched production metrics and changed parameters instantly—workloads became lighter and product quality improved.
Intelligent automation10 enhances per capita production efficiency by streamlining complex workflows.
Training Employees and Improving Skills
Advanced systems bring the need for new skills; training strengthens our team so they can handle minor issues independently, reducing downtime and boosting morale as well. I watched colleagues gain confidence with technology—they now manage equipment and lead innovations.
Encouraging skill training expands what we can do; operations run smoothly even when problems appear. Investing in team growth improves productivity while enriching career paths for everyone.
Automation reduces labor costs in injection molding.True
Automated equipment decreases manual labor, lowering costs per unit.
Intelligent monitoring increases manual inspection workload.False
It reduces manual inspections by automating parameter adjustments.
Conclusion
This article explores strategies to reduce labor costs in injection molding through automation, employee training, process optimization, and performance incentives, enhancing efficiency and productivity.
-
Exploring this link will provide insights into the specific benefits of professional skills training, such as reduced downtime and enhanced efficiency. ↩
-
Effective work allocation strategies are key to maximizing individual productivity by aligning tasks with skills. ↩
-
This explores how performance incentives can drive cost-saving innovations and improvements in production efficiency. ↩
-
Discover how intelligent monitoring systems improve production quality by real-time adjustments and error reduction. ↩
-
Learn how companies incentivize employees to reduce operational costs through innovative reward programs. ↩
-
Explore how well-structured incentives can align employee goals with company objectives, enhancing productivity. ↩
-
Discover how intelligent systems streamline production and reduce manual errors. ↩
-
Learn how automation reduces dependency on manual labor, lowering overall costs. ↩
-
Learn about the advantages of using automated inspection technologies in quality control processes. ↩
-
Discover how intelligent automation transforms manufacturing processes and boosts productivity. ↩