Did a project ever fail because of a troublesome short shot defect?
Short shot defects occur when plastic does not fully fill the mold in injection molding. Low pressure often causes this issue. Slow speed might be another reason. Sometimes, the plastic flows poorly. Mold design problems are also possible causes.
Finding out why these short shots happen has been a challenge in my work. I try very hard to reach a perfect balance between design and usefulness. Many factors affect these defects. Changing injection pressure probably helps. Rethinking mold design really matters. Every adjustment is important in our journey for quality and efficiency.
Low injection pressure causes short shot defects.True
Insufficient pressure prevents the plastic from filling the mold fully.
High mold temperature leads to short shots.False
High temperatures generally improve fluidity, reducing short shots.
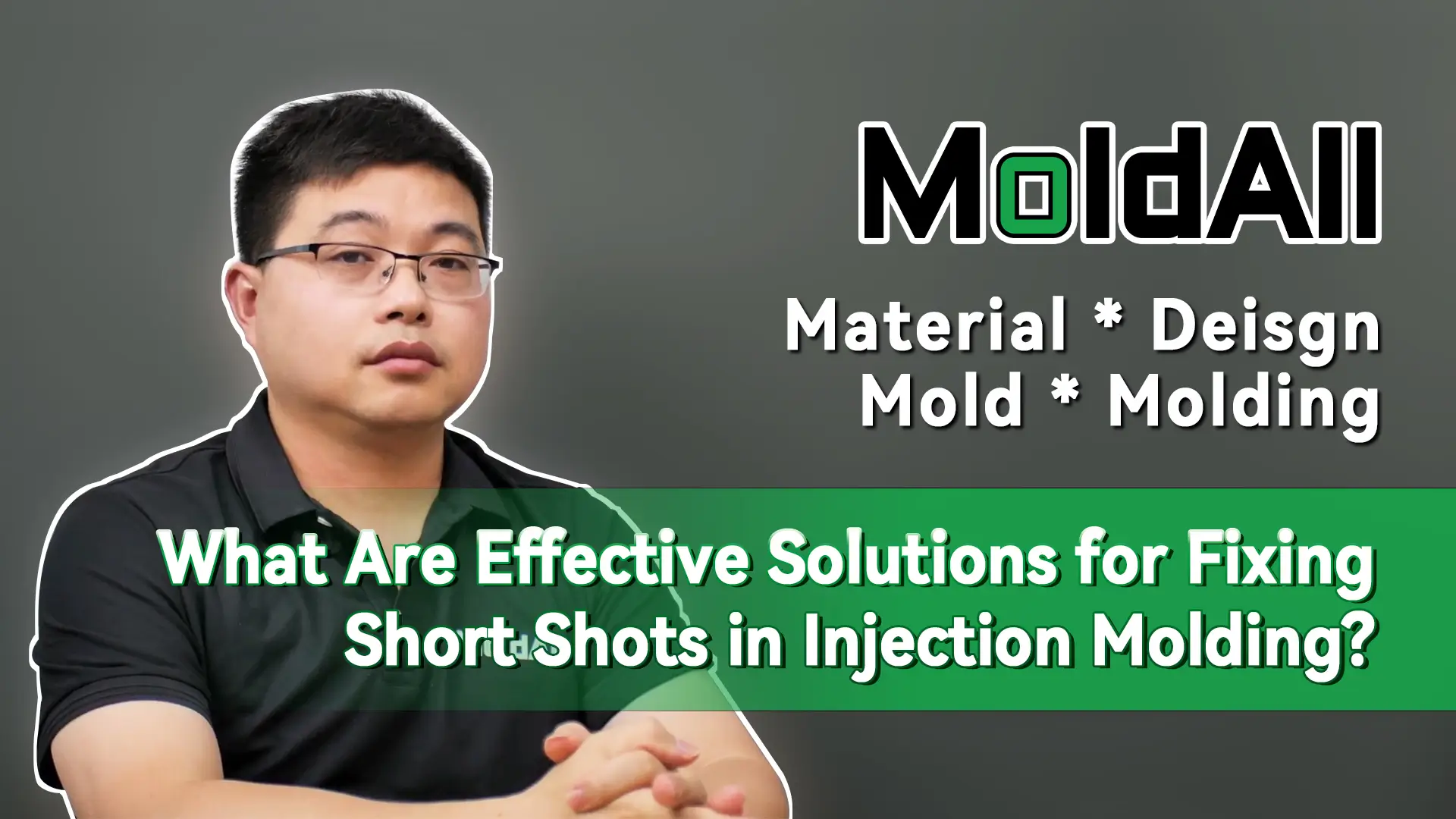
- 1. How Does Injection Pressure Influence Short Shots?
- 2. Why is Injection Speed Critical in Preventing Short Shots?
- 3. How Do Plastic Materials Influence Short Shot Defects?
- 4. How Does Mold Design Influence Short Shot Formation?
- 5. What are Effective Strategies to Mitigate Short Shot Defects?
- 6. Conclusion
How Does Injection Pressure Influence Short Shots?
Ever experienced a day when nothing seems to fit? In injection molding, injection pressure plays a big role so every part fits perfectly. Very important.
Injection pressure plays a critical role in injection molding. It helps fill the mold completely. Low or changing pressure might result in short shots. Short shots occur when the mold is not filled all the way. Product quality suffers because of this.
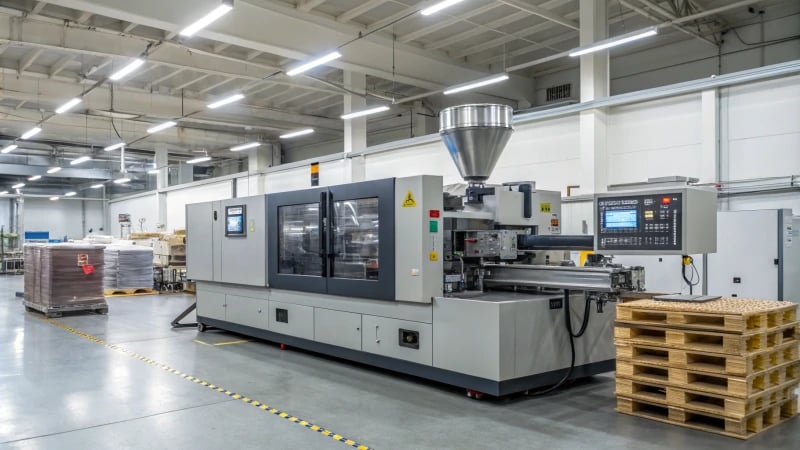
The Role of Injection Pressure
Injection pressure acts like the strong push needed to get toothpaste out of an almost empty tube. If the pressure is too low, the melt struggles against complex mold designs or thin walls, causing short shots. This can prevent the cavity from being fully filled.
Pressure Issue | Effect on Mold Filling |
---|---|
Too Low | Incomplete filling |
Unstable | Variable filling, short shots |
Challenges with Pressure Instability
Once, a problem with the hydraulic system caused me a lot of stress because it led to uneven melt movement. Pressure instability is like driving on a road that changes lanes suddenly. This often causes unpredictable filling in molds with many cavities. Some fill correctly, while others stay unfinished.
Impact of Injection Speed and Material
I discovered through experience that slow injection speed greatly affects thin-walled products. It’s similar to pouring honey through a straw; it cools and hardens before reaching the end. Materials with poor fluidity add to the problem. Imagine trying to run in mud; the melt does not flow well. Poor fluidity1 is especially problematic with certain engineering plastics.
Mold Design Considerations
- Gate Design: I once worked on a project where a tiny gate caused big issues. It’s like trying to pour soup through a pinhole. Poor gate size or positioning blocks melt flow.
- Runner System: Runners are highways for the melt; narrow or rough ones make the journey difficult and increase resistance.
- Exhaust Issues: Without proper vents, it’s like blocking all the exits in a busy room. Back pressure builds, stopping the melt from flowing smoothly.
- Temperature: Uneven temperatures are like mismatched shoes – one comfortable, one uncomfortable. Cooler areas decrease melt flow, which affects the final item.
Understanding these factors can enhance mold design and mitigate short shots through optimized injection pressure and process parameters. Mold design considerations2 are key for achieving consistent, high-quality products.
Low injection pressure causes short shots.True
Low pressure fails to overcome mold resistance, leading to incomplete filling.
Stable pressure guarantees no short shots.False
Even with stable pressure, factors like design or material can cause short shots.
Why is Injection Speed Critical in Preventing Short Shots?
Have you ever thought about how changing the injection speed might affect product quality? Small changes can have big effects. It’s essential to get this right. It’s very important.
Injection speed is key for stopping short shots. This speed lets the plastic melt fill the mold entirely before it cools. Slow injection risks empty spots, especially in thin areas where heat disappears fast.
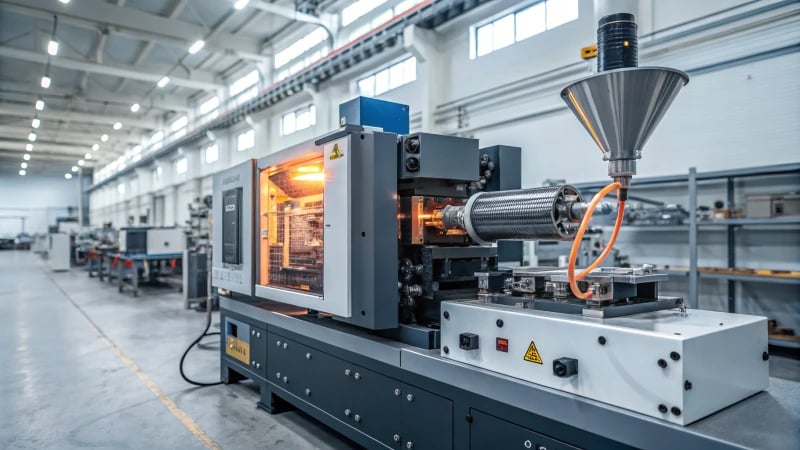
The Role of Injection Speed in Mold Filling
In my early days in the mold industry, I watched experts like Mike Tang deal with injection speed. It seemed like a dance; moving too slowly could mean the mold was not filled correctly. Injection speed decides how fast the plastic melt3 flows through the mold cavity. With a slow speed, the melt might harden before reaching all areas, especially in thin-walled designs where heat escapes quickly. Speed is vital.
Factors | Impact on Injection Speed |
---|---|
Injection Pressure | If pressure is too low, the melt won’t overcome cavity resistance. |
Mold Design | Complex shapes increase resistance, requiring faster speeds. |
Balancing Injection Speed and Pressure
Finding the right balance between speed and pressure is something I practiced for many hours. It’s similar to driving a car uphill. Too little pressure and you stop; too much and control might be lost. Pressure changes, perhaps from a hiccup in the hydraulic system, can cause uneven melt flow and unwanted short shots.
- Pressure Instability: Causes different melt speeds and possible short shots.
- Slow Injection Speed: Raises the chances of melt cooling too soon.
Material Characteristics Affecting Speed
After experimenting, I learned that different plastics have unique behaviors. High-viscosity materials are like stubborn old cars in the morning – they need extra effort to start moving. For these materials, higher speed is needed to keep the flow going before they cool.
- Poor Fluidity Materials: Need faster speeds to maintain flow before cooling.
- Damp or Contaminated Materials: Block flow and require speed changes.
Explore more about plastic materials4 and their effect on injection speed.
Mold Design Considerations
Designing a mold is like setting up a racetrack; it’s about creating a smooth flow without obstacles. A bad gate design or weak runner system acts like unexpected roadblocks, needing faster speeds to overcome them. Poor mold exhaust is another challenge; it’s like trying to breathe through a straw while running a marathon.
Mold Aspect | Effect on Injection Speed |
---|---|
Gate Design | Impacts initial melt entry speed. |
Runner System | Affects flow consistency and speed. |
For more on improving mold design to increase speed efficiency, visit mold optimization techniques5.
Slow injection speed causes short shots.True
A slow speed allows the melt to cool and solidify prematurely, causing short shots.
High-viscosity materials require slower injection speeds.False
High-viscosity materials need higher speeds to maintain flow before cooling.
How Do Plastic Materials Influence Short Shot Defects?
Do you struggle with short shot defects in your injection molding tasks? I have been in that situation, puzzled by why those annoying gaps always appear. These flaws can really disrupt your work.
Plastic affects short shot defects by reducing fluidity. Thick or dirty plastic has lower fluidity. This prevents the plastic from completely filling mold spaces. This causes defects.
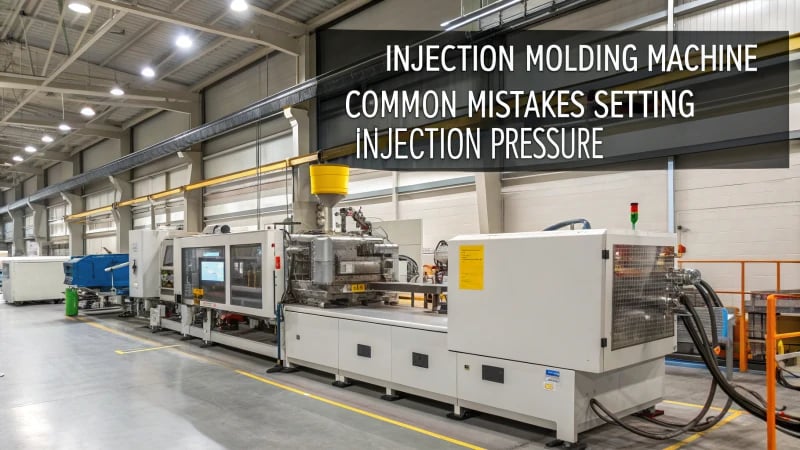
Exploring Plastic Materials
The choice of plastic affects the success of injection molding. Fluidity is a primary characteristic that dictates how well the molten plastic will flow into the mold.
-
High Viscosity Materials: High viscosity means resistance to flow, like honey in a small funnel. Some plastics, especially those reinforced with additives like glass fiber, have high viscosity. This complicates the process of filling molds completely. Temperature and pressure adjustments help enhance flow. For example, adjusting temperature6 can reduce viscosity, but too much heat can damage the material. It’s a delicate balance.
-
Moisture Content: Moisture vaporizing during molding hisses like steam. This experience showed me the need to dry materials first to avoid moisture problems and prevent steam-related issues7.
-
Contamination: A tiny dust speck can cause trouble. Keeping materials clean is vital as impurities disrupt fluidity and must be avoided.
Balancing Injection Pressure and Speed
Choosing the right pressure and speed is like tuning an instrument. Each setting counts based on the plastic material used.
Material Type | Recommended Pressure | Recommended Speed |
---|---|---|
High Viscosity | High | Slow |
Low Viscosity | Moderate | Fast |
-
Low Pressure & Speed: Using low pressure or slow speed with high-viscosity materials may lead to short fills as the material struggles to fill the entire mold before cooling.
-
Pressure Instability: Fluctuations in pressure can disrupt the filling process, particularly with complex molds or thin-walled designs. Consistent pressure control8 is essential for quality production.
Material Selection and Design Considerations
Selecting plastic isn’t just about color; understanding properties and mold fit is essential.
-
Mold Design Compatibility: Ensure that material must match mold design complexity and wall thickness. A design seemed perfect on paper but failed in reality due to bad material fit. Materials with poor flow should be matched with simpler designs or adjusted mold temperatures.
-
Exhaust Systems: Air needs a way to escape, like having an exit door. Proper exhaust systems are necessary to prevent air traps which worsen short fills. Ensuring that exhaust paths are clear and effective is key for all material types.
Getting these aspects right leads to better products by investigating your material choices and adjusting settings accordingly. Staying ahead of problems reduces flaws and probably improves quality in injection molding processes. This proactive approach can help mitigate defects and enhance product quality.
High viscosity plastics cause short shot defects.True
High viscosity materials resist flow, leading to incomplete mold filling.
Moisture in plastic pellets improves mold filling.False
Moisture vaporizes during molding, creating steam and obstructing flow.
How Does Mold Design Influence Short Shot Formation?
Ever experienced the annoying moment when your injection mold refuses to fill correctly? The problem usually lies in the mold design.
Mold design greatly influences how well the melt flows and how efficiently the cavity fills. Important parts are the gate design, the runner system and controlling the mold’s temperature. Paying attention to these factors is likely to reduce short shots.
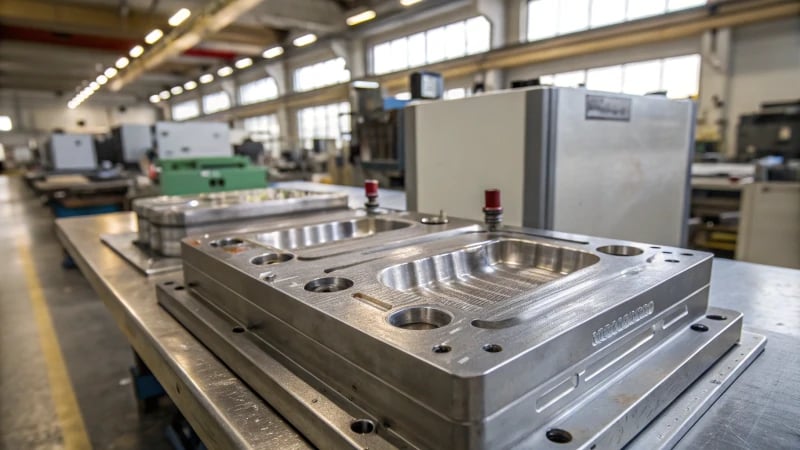
Gate Design
The gate acts like a welcoming team for the hot plastic. If it’s too small or in the wrong place, it blocks the flow. It’s like forcing a big bag through a narrow doorway. Using several gates can really help smooth the entry and stop those short shots we hate.
Consider a multi-gate approach9 where multiple gates are strategically positioned to optimize flow.
Runner System Efficiency
Runners are like highways leading the melt to where it should go. A wide, smooth highway allows easy travel. If it’s narrow or rough, traveling is like hitting every bump on a road trip, which slows down progress.
A detailed runner analysis10 often reveals these problems and speeds things up.
Runner Characteristics | Impact on Flow |
---|---|
Narrow Width | High Resistance |
Rough Surface | Increased Friction |
Mold Exhaust Mechanism
Venting is crucial because it lets air escape, like opening windows in a stuffy room. Air pockets can ruin your mold fill.
Implementing effective exhaust design strategies11 can alleviate this problem.
Mold Temperature Management
Keeping mold temperatures steady is key. Without this, you risk uneven filling and shrinking, which brings bad results. I found that using advanced temperature control systems keeps things consistent, like maintaining an even oven temperature when baking.
Using advanced temperature control systems12 ensures better quality and consistency in molded products.
These design choices are practical methods I use to stop short shots and improve quality in injection molding. These strategies work.
A small gate size can cause short shots in molding.True
Small gates restrict melt flow, leading to incomplete cavity filling.
Uneven mold temperatures have no effect on short shots.False
Uneven temperatures affect melt viscosity, causing inconsistent filling.
What are Effective Strategies to Mitigate Short Shot Defects?
Think about putting your whole heart into creating a product. The product then struggles in the end because of short shot flaws.
To fix short shot problems in injection molding, adjust the injection pressure, speed and mold design. Study the material qualities. Keep molds really clean and well-maintained. This is very important. Without this care, mold filling stays incomplete.
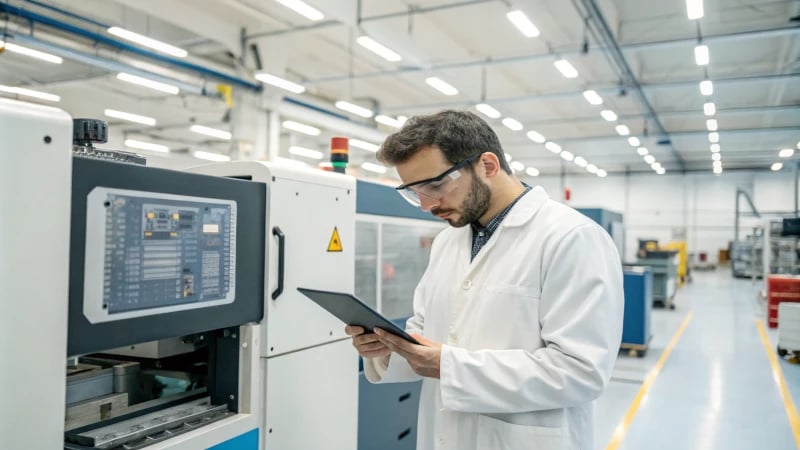
Injection Pressure Optimization
In the beginning of my work with injection molding, I quickly found out how important having the right pressure is. Picture trying to push a thick smoothie through a tiny straw. Low pressure feels like that to the plastic melt. It struggles to move through a complex mold without enough force. I learned this hard lesson when a batch came out only half-formed. A reliable pressure system13 is very important to prevent such problems.
Injection Speed Adjustments
I remember when I first saw a thin-walled product turn solid in the middle of the process. It was like watching an ice cream cone melt on a hot day. Setting the correct injection speed is really crucial. A careful balance between speed and quality is necessary and depends on the material used.
A table illustrating the impact of speed on different materials:
Material Type | Recommended Speed |
---|---|
High Viscosity | Moderate |
Low Viscosity | High |
Thin-Walled | Fast |
For high viscosity materials, a moderate speed works better. Low viscosity materials need a higher speed to stop early cooling. Really important!
Material Characteristics Analysis
Choosing the material is like picking the perfect ingredient for a dish you love. If you pick something like reinforced glass fiber plastics with poor fluidity, disappointment is likely. I once forgot to dry my materials well, which caused steam pockets and ruined the flow.
Always check for dirt and wetness in your materials as contamination or moisture hampers flow and should be carefully managed.
Mold Design Considerations
Think of mold design as the plan for your work. A wrongly sized mold gate14 or badly placed runner is like trying to push a river through a garden hose – not efficient.
Early on, I had to rethink my mold designs because the gates were too tight.
Proper exhaust systems and even temperature control across the mold help stop air getting trapped and uneven flow.
Exhaust and Temperature Control
- Ensure sufficient exhaust channels.
- Regularly inspect for blockages.
- Monitor temperature uniformity across the mold surface.
Fixing these methods – like changing machine settings, picking the right materials or redesigning molds – probably reduces short shot defects and increases production efficiency. It’s really about understanding each part’s role and how they work together in making a perfect product.
Optimizing injection pressure reduces short shot defects.True
Maintaining optimal pressure ensures complete mold filling, preventing defects.
High viscosity materials require high injection speed.False
High viscosity materials need moderate speed to ensure proper flow.
Conclusion
Short shot defects in plastic injection molding arise from low pressure, slow speed, poor fluidity, and mold design issues. Optimizing these factors enhances product quality and efficiency.
-
Discover how different materials’ fluidity impacts their ability to fill molds effectively. ↩
-
Learn about critical aspects of mold design that influence product quality and manufacturing efficiency. ↩
-
Understanding plastic melt properties can help optimize injection speed for better mold filling. ↩
-
Knowing material characteristics aids in adjusting speed to prevent short shots. ↩
-
Enhancing mold design can significantly improve injection efficiency and quality. ↩
-
Discover how temperature adjustments can enhance plastic flow by reducing viscosity, crucial for preventing short shot defects. ↩
-
Explore techniques to remove moisture from plastics before molding, preventing steam-related flow issues. ↩
-
Understand methods for ensuring stable pressure during molding, critical for high-quality outputs. ↩
-
Discovering optimal gate placement strategies can improve melt distribution and reduce short shots. ↩
-
Analyzing runner systems can uncover ways to enhance flow efficiency and prevent incomplete fills. ↩
-
Effective exhaust designs help prevent air pocket formation, ensuring better fill efficiency. ↩
-
Advanced systems maintain consistent mold temperatures, crucial for even filling and reduced defects. ↩
-
Understand how adjusting injection pressure can prevent incomplete mold filling. ↩
-
Explore how proper gate design facilitates better flow into the mold cavity. ↩