Injection molds achieve high precision due to the steel used. Steel plays a crucial role. This metal provides the necessary strength. Steel really helps in shaping products accurately. Different types of steel offer varying levels of hardness. Hardness influences durability. Many manufacturers choose steel because it lasts. It’s strong and reliable.
Steel’s hardness and toughness are crucial for precise injection molds. Hard steels resist wear. They keep mold dimensions stable. Tough steels stop fractures during high-pressure molding. This balance leads to better surface quality. It also results in long-lasting mold performance. Very long-lasting molds.
Years ago, I loved figuring out how my molds could last longer without losing precision. I studied steel properties deeply. Hardness and toughness in the right balance changed everything. H13 steel resists wear very well. This type helps gears keep their precise shapes. On the other hand, P20 steel has strength. This steel stops cracks from forming in complex designs, like phone cases. My designs improved with this knowledge. Material waste went down a lot. Time and money were saved for my company. I felt very proud watching my hard work succeed. It drove my passion for mold design even further.
High-hardness steel improves mold dimensional stability.True
No explanation available.
Poor toughness causes molds to deform under pressure.True
Molds with low toughness may deform, affecting product accuracy.
Why is Hardness Crucial for Mold Dimensional Stability?
Some molds last longer than others and keep their shape and accuracy. Hardness is the key.
Hardness in mold materials is important for dimensional stability. It helps resist pressure and wear during injection molding. This leads to accuracy and consistency. Steels such as H13 have high hardness. They play a crucial role in keeping cavity sizes precise. This is necessary for making accurate plastic parts.
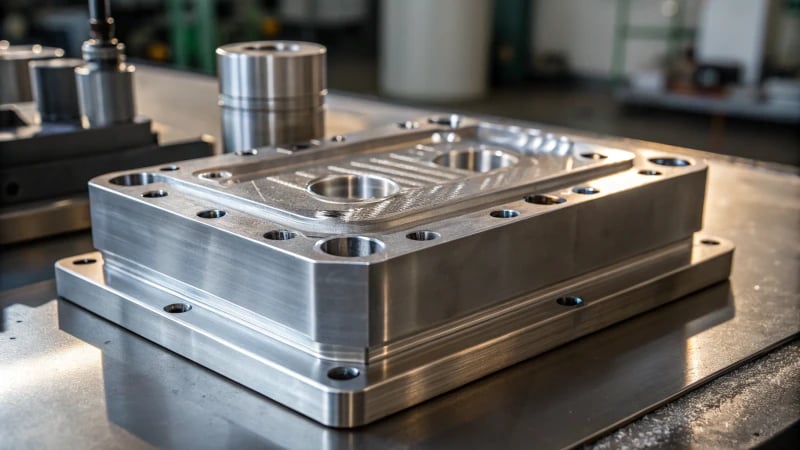
The Impact of Hardness on Injection Mold Precision
Dimensional Stability
I remember my first encounter with a mold that wasn’t ready for the job. It taught me the importance of selecting the correct material. Molds made from high-hardness steel, like H13 steel1, keep their shape even under the intense pressure of injection molding. I realized this during a project with precision gears – where even tiny errors could spell disaster. Imagine gears not fitting properly because the mold wore out too soon! H13 steel’s toughness (48-52HRC after treatment) keeps this from happening. It maintains the cavity size perfectly through endless production cycles.
Mold Steel Type | Hardness Range (HRC) | Application |
---|---|---|
H13 | 48-52 | Precision Gears |
S136 | High | Mirror Finishing |
Surface Quality
In one of my early projects, I faced a challenge with surface quality – it felt like trying to perfect a mirror finish on a foggy day. High-hardness materials like S136 steel2 simplify this task. I discovered the value of surface quality when a polished mold changed the product’s final look. Achieving a smooth finish is crucial, with S136 reaching a surface roughness of Ra 0.01-0.05μm after polishing. This ensures our plastic products appear sleek and precise.
Uniform Hardness for Consistent Dimensions
From experience, uniform hardness across a mold is a must for accurate dimensions. It’s like baking – if the heat in the oven isn’t even, some parts are raw while others are burnt. Similarly, controlled heat treatments keep the hardness consistent across the mold, reducing deviations to within ±1HRC.
Toughness vs. Hardness3
While hardness matters, I’ve learned not to forget toughness. It’s like building a house; strong bricks matter, but if the mortar can’t absorb shocks, the whole structure might fall apart. Toughness prevents molds from cracking or deforming under high pressure – a real lifesaver with complex structures or thin walls. For instance, P20 steel’s toughness has saved many molds from breaking under pressure.
In short, while focusing on hardness, understanding its relationship with other properties like toughness is key to improving injection mold design and achieving excellent results in plastic product manufacturing.
High-hardness steel improves mold dimensional stability.True
High-hardness steel resists wear, maintaining cavity size during molding.
Toughness in mold steel increases fracture risk.False
Good toughness prevents mold fractures under high stress conditions.
How Does Toughness Prevent Mold Fractures During Injection?
Have you ever wondered why some molds stay strong during injection molding while others break under stress? Toughness is the secret hero. It keeps molds whole. Toughness is key for perfect performance.
Mold steel’s toughness stops fractures during injection. Molds absorb stress and resist bending. This quality gives both strength and accuracy to complex plastic items. Mold integrity depends on it.
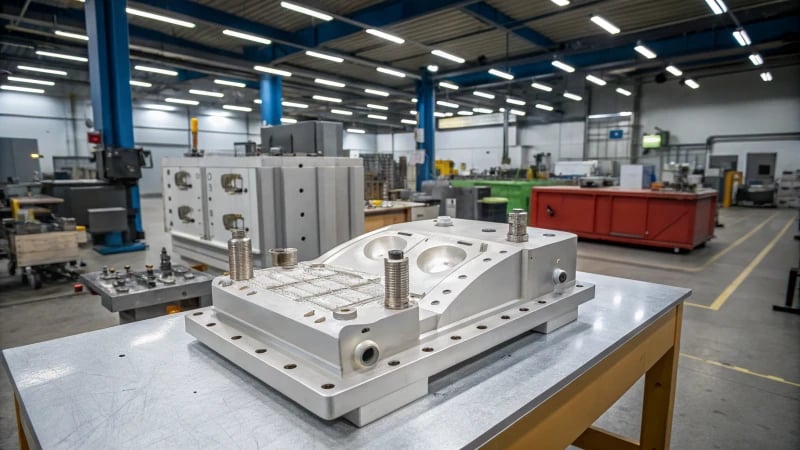
The Importance of Toughness in Mold Strength
Delving deeper into injection molding4 unveils how vital toughness truly is. Imagine creating a smartphone case mold. Those button holes have thin walls facing enormous stress during injection. When the mold lacks toughness, there is a risk of cracks, production could stop, and the mold might become useless.
Protection Against Fractures
Materials like P20 steel often act as saviors in this scenario. Their toughness works as a safety shield, stopping fractures even in complex designs. Consider using a table to compare tough materials5:
Material | Toughness | Use Case Example |
---|---|---|
P20 Steel | High | Smartphone Cases |
S136 Steel | Medium | Automotive Parts |
Resistance to Deformation
Deformation resistance also plays a significant role. During plastic injection into a mold, pressure becomes very intense. Tough steels retain their shape, ensuring each detail appears correct.
For bigger products, such as car bumpers, tough materials withstand high filling pressure. A lack of toughness could result in deformations affecting the product’s accuracy.
Stability of Size Through Uniform Hardness
Uniform hardness matters a lot too, not only toughness. High-hardness steel like H13 keeps its cavity size stable over many cycles – this reliability is excellent for precise parts like gears.
Through careful heat treatment, uniform hardness can be achieved, leading to consistent mold sizes. This precision helps in smooth operations without expensive delays or mistakes.
Knowing these factors aids in picking the right materials for lasting injection molds and enhances the longevity and performance6 of molds. Efficient production is possible without setbacks from mold cracks.
High-hardness steel improves mold dimensional stability.True
High-hardness steel resists wear, maintaining cavity size accuracy.
Toughness of mold steel is irrelevant to fracture prevention.False
Good toughness prevents cracks in stress-concentrated mold areas.
How Does Material Selection Affect Molded Products’ Surface Quality?
Picking the correct materials sets a strong base for a masterpiece. This step greatly improves the surface quality of molded products. It is very important.
Choosing the right materials matters a lot. High-hardness steels like H13 or S136 improve the surface quality of molded products. These steels resist wear very well. They maintain precision over time. This is very important. Durable materials result in better products. Let’s repeat that for clarity. Better materials result in better products.
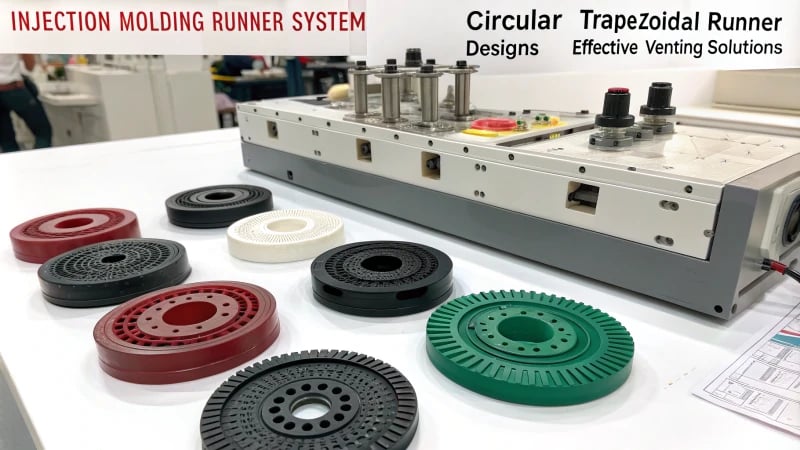
The Role of Hardness in Surface Quality
Imagine you need to create gears that fit perfectly, with only a tiny space for error, just 0.03mm. Choosing high-hardness materials like H13 steel, with hardness ratings of 48-52HRC, is essential for maintaining cavity stability in molds. This ensures that even under intense pressure and friction during injection molding, the mold cavity remains dimensionally stable, leading to high-precision products like gears with tight tolerance requirements.
For example, H13 steel prevents cavity size changes due to its resistance to erosion and filling pressure, ensuring consistent dimensional accuracy across multiple cycles. Additionally, uniform hardness7 in the mold material ensures dimensional consistency throughout the manufacturing process.
The Importance of Toughness
Consider a mobile phone shell with delicate button holes. Stress loves to gather in such areas. Mold toughness plays a vital role in preventing fractures and deformations during molding. Materials like P20 steel are known for their toughness, making them suitable for complex mold designs such as mobile phone shells that have stress-concentrated areas like button holes.
I remember a car bumper project; we picked P20 for its strength against huge pressures. Toughness prevents cracks and breaks, ensuring the longevity and accuracy of the mold. For instance, in producing car bumpers where fill pressures are high, tough materials8 resist deformation, maintaining shape integrity and meeting dimensional accuracy requirements.
Surface Processing Quality
Now, let’s discuss achieving a surface that shines like a mirror. Materials with higher hardness provide superior surface processing quality. For example, S136 steel allows for surface roughness levels to reach as low as 0.01-0.05μm after polishing. This results in smoother product surfaces since any imperfections on the mold surface can directly affect the final product’s appearance.
S136 steel is like an artist’s brush in our tools; its excellent hardness lets us polish the mold surface extremely smooth—ensuring each product from the mold looks impeccable—a flawless finish is very desirable.
A comparative analysis table below illustrates how different materials impact surface quality:
Material | Hardness (HRC) | Surface Roughness (μm) | Ideal Applications |
---|---|---|---|
H13 | 48-52 | 0.03 | Precision gears |
S136 | High | 0.01-0.05 | Mirror finishes |
P20 | Moderate | N/A | Complex molds |
Understanding these material properties assists me in picking the best fit for each project. By understanding the interplay between material properties like hardness and toughness, designers can better select materials that enhance both long-lasting quality and beautiful appearance in our molded items.
High-hardness mold steel improves dimensional stability.True
Hardness resists wear, maintaining cavity size accuracy during molding.
Tough mold materials are prone to deformation under stress.False
Toughness prevents deformation, ensuring mold integrity and accuracy.
Conclusion
Mold steel hardness and toughness are vital for injection mold precision, ensuring dimensional stability, surface quality, and resistance to fractures during high-pressure molding processes.
-
Discover how H13 steel’s properties make it ideal for high-precision mold applications. ↩
-
Learn why balancing hardness and toughness is critical in mold design. ↩
-
Explore key design principles that enhance mold accuracy and durability. ↩
-
Explore how toughness impacts the reliability and longevity of molds during injection. ↩
-
Understand different materials’ toughness levels and their specific applications in molding. ↩
-
Discover how toughness extends the lifespan and efficiency of injection molds. ↩
-
Learn why uniform hardness is crucial for ensuring consistent dimensions and surface quality in molds. ↩
-
Discover how tough materials enhance mold durability and accuracy during high-pressure applications. ↩